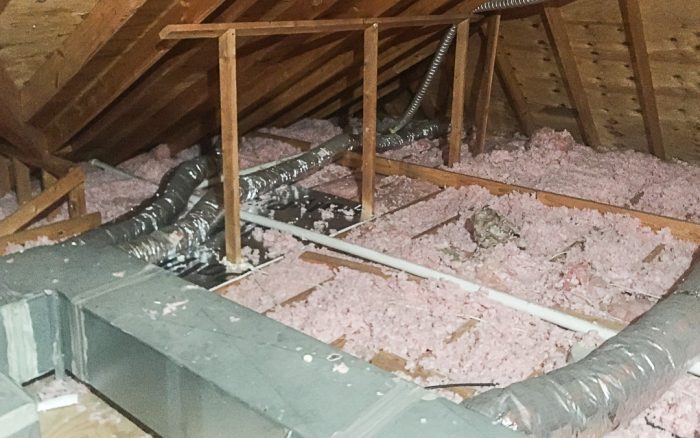
Not even the most powerful residential air conditioning unit on the market is enough to keep Ryan Welch’s Alabama home cool and comfortable.
With the HVAC equipment located in what sounds like an underinsulated attic, temperatures in the second-floor living area may not reach 72°F until 10 in the evening—only after the attic has cooled.
“Our attic has varying levels of insulation,” Welch writes in a Q&A post, “and the weak spots are under the attic floorboard, which has been nailed down, making it difficult to remove.” Parts of the attic floor are insulated to R-19, other areas to R-30 (Alabama is in Climate Zone 3, where the International Residential Code, or IRC, requires attic insulation rated at R-38).
Welch runs two powered attic ventilators constantly, with the AC set at 75° during the day. But the system simply can’t keep up.
Moving the HVAC equipment is not an option, Welch says. So, he is considering several other options: disconnecting the attic ventilators, adding more insulation to the attic floor, and spraying a layer of foam on the underside of the roof deck, which would create a conditioned attic.
What’s the best plan? Welch’s dilemma is where we begin this Q&A Spotlight.
Make it conditioned space
GBA Editor Brian Pontolilo suggests that if moving the HVAC equipment is truly impossible, Welch should make the attic part of the conditioned space. But he adds a caveat.
“Keep in mind that your insulation R-values are only part of the equation,” he writes, “and that air-sealing is likely a bigger issue, including around those [non-IC-rated] can lights that need to be isolated from your insulation asap.”
Pontolilo points Welch toward a GBA article on the issue (see the “Related Articles” sidebar for a link). The article says…
Weekly Newsletter
Get building science and energy efficiency advice, plus special offers, in your inbox.
This article is only available to GBA Prime Members
Sign up for a free trial and get instant access to this article as well as GBA’s complete library of premium articles and construction details.
Start Free TrialAlready a member? Log in
8 Comments
Trying to cool a house in Alabama to 72° sounds tough. Is there a humidity issue that could be addressed and allow a higher inside temperature to still be comfortable?
I'm interested if the equipment is performing properly. A refrig tech should be able to look at temps/pressures/amps to see if the equipment is actually giving you it's rated performance. I don't disagree about the air sealing or other measures, but it seems hard to believe that such an oversized system isn't more capable. It might even be freezing up the coil or something if the return air is restricted badly or the tx valve is malfunctioning.
Also, check to make sure your drains are properly trapped to prevent air from blowing out the condensate drains.
I have a house in Northern Arizona where outside daytime temps still climb to 95-100F in the summer. The house is ICF with a properly detailed SIP (R-40) roof. I set my 1 ton ductless mini split to 70F in the summer and it keeps my house in the 70F temp. In a 100% electric house (no gas). My monthly electrical bill is $50-$60 in both summer & winter.
The point of my comment is to show that even though there is a 30 degree temp difference between inside vs outside, it can be done efficiently $$. It all comes down proper insulation, air tightness and keeping the AC in a conditioned space. If the house is improperly built (leaky, low R-Value, AC ducts in unconditioned space), you will be battling high energy bills and living miserably inside for the life of the house.
When I lived in a code minimum home years before. The AC would never cool the house below 78F. This was with two 5-ton units. The AC air handler & ductwork was in the unconditioned attic. My monthly electrical bills were in the low $300 range during summer. I got sick of battling a losing battle so I sold the home and built an energy efficient home on my own.
Peter,
These numbers sound impressive for your new home and really, really awful for your prior home. Can you share the square (or cubic) footage of space for each to better contextualize the numbers you have provided already?
Antonio
New home is around 800 sqft with an attached garage. Older home was 3,000 sqft also with an attached garage. Older home was spec home with fiberglass insulation in a 2x4 wall and blown in fiberglass in attic (R-38).
In addition to the $300+ monthly electrical bill at the older home. It also had natural gas for heating/cooking/water heater. So I spent around $40-$130 per month in natural gas bills, in addition to my electrical bill.
The Phx home was featured in GBA Spotlight:
https://www.greenbuildingadvisor.com/article/why-are-houses-built-this-way
I have concerns, and solutions to the sentence "The air conditioner is probably too big". I manage a utility HVAC program in Phoenix AZ. While I don't assume to know the specific Cooling Degree Days for this particular home, I would assume that with the addition of Latent Cooling Capacity needed for Alabama's humidity, the sizing is probably not far off for a 2200 Sq. Ft. Home. 5 Tons for 2000 Sq. Ft. in Southern AZ is commonplace. In the world of cooling capacity Air Flow is King! You will want to be moving about 400cfm/Ton of capacity to (Possibly a little less depending on avg. humidity levels) You can DIY a test that will help you know where you are. Conduct a Total External Static Pressure (TESP) Test on this beast. Collect both the supply and return pressures separately and add them together (Ignoring the (-) sign) . (Any reasonable AC tech can also do this for you) You will want to make sure that a). The TESP does not exceed the MAX TESP listed on the data plate for the Air Handler Unit (AHU). Best guess from the picture, that limit will be 0.50iwc (Inches of Water Column). If you are running high pressures, the separate supply and return numbers will tell you where the bulk of the problem lies. Your return pressure should ideally be half or less of the TESP, (0.25iwc) and your supply pressure should be right about half of the TESP.(0.25iwc) You can then compare the TESP to the Blower Performance Chart for your specific AHU (Google will usually produce the specs) That will ultimately tell you how many CFM per Ton of capacity you are moving. All that said, you can also have an HVAC contractor run a "Manual J" Calculation for you. It is a modeling software that takes the homes characteristics (Building type, window type, insulation levels and orientation etc) into account and produce a report on how much capacity (how many tons of cooling) this home needs. If you want to go one step further, Manual S will tell you if your specific equipment is rated to handle that capacity. In my opinion, this AC system is not oversized, it is probably just starved for air. P.S. I have also been in the Home Performance industry for 25 years and manage our state utility program for that as well...So, of course, fix your air-barrier and insulation problems too!
Five tons for 2000 sqft? That’s a ton per 400 sqft. That’s either GROSSLY oversized, the home is extremely poorly built/sealed/insulated, has huge low quality west facing windows, or some combination.
Ryan,
My company is located in Decatur, AL and we will be happy to diagnose and fix your issues.
Todd Witt@ Synergy Home Performance
Log in or become a member to post a comment.
Sign up Log in