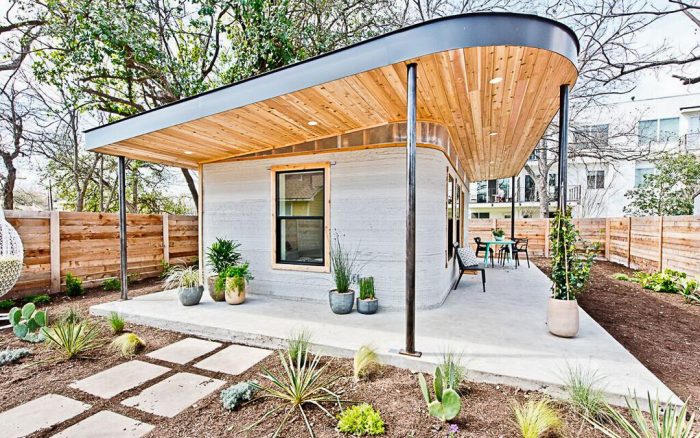
A Texas construction technology company says it has developed a 3D printer that will be used later this year to build a cluster of houses in an impoverished Latin American community as the experimental equipment graduates to real-world use.
The project will pair the Austin-based company ICON with a California nonprofit called New Story that has been building houses in the region for the last several years. ICON will roll out its Vulcan II printer for the project, an updated version of a printer that was unveiled last year in Austin where it printed a single-story house in a couple of days.
Since then, ICON has been tweaking the design and now says it can create the walls of a house in a day or less, according to an article posted by Fast Company. Wiring, plumbing, windows, doors, the roof, and other details all would be left for crews using conventional techniques. ICON regards 3D printing as the most promising technology for building affordable and durable housing in distressed areas.
In addition to taking on the Latin American project, ICON says it plans to ship Vulcan II printers to a small group of customers this year while it actively seeks orders for 2020. Fast Company didn’t offer details, and ICON declined in an email to answer any questions.
How the printing process works
According to information posted at ICON’s website, the gantry-style printer is capable of printing walls that are 8-1/2 ft. tall and up to 28 ft. wide (the length of the building is, in theory, unlimited). A computer-guided nozzle dispenses a 1-in.-tall, 2-in.-wide bead of a proprietary cement-based material that cures to form finished walls.
The printing material, called Lavacrete, is mixed and pumped from equipment housed in a trailer. The 3,000-lb. printer uses 2 gal. of water per minute and can lay between 5 in. and 7 in. of material per second. It requires a crew of four to six people to operate.
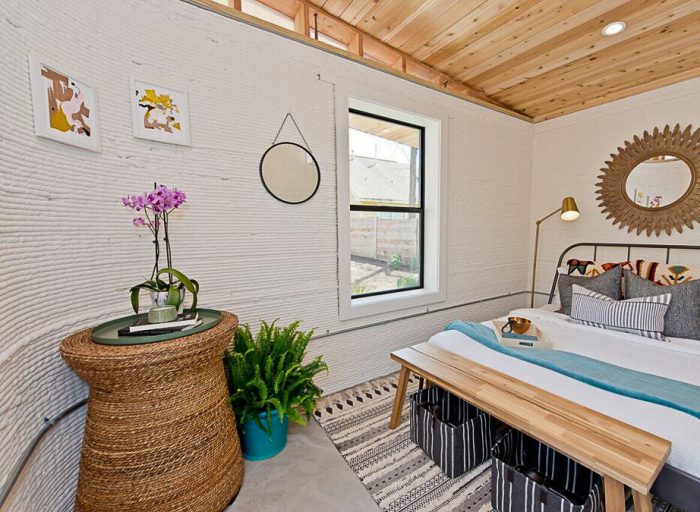
ICON says 3D printing has many advantages over conventional construction, including faster builds, near-zero waste, and less reliance on manual labor. Concrete is a well-understood and affordable material, the company adds, and printed walls combine structure, interior and exterior sheathing, a moisture barrier, and insulation into one.
Although the company says the high thermal mass of printed walls are advantages for comfort and energy efficiency, the R-value of a completed wall isn’t listed. Given the low thermal resistance of concrete in general, it’s not clear whether these printed houses would be suitable for anything other than very mild climates where freezing temperatures aren’t a concern. If additional insulation would be added for some climates, the company doesn’t explain how that would be done.
The Latin American project is a mystery
Fast Company writes that New Story was frustrated at the slow pace of reconstruction in Haiti after a major earthquake there in 2010. The nonprofit thought that rebuilding with conventional construction techniques would be too slow, so it began working with ICON on the development of the printer.
New Story originally said the printer would be used to make dozens of houses in rural El Salvador this year. The houses could be created in a single day for about $4000, much less than the $6500 that New Story was spending to build simple houses with concrete walls, according to an article published last year.
But a variety of factors, including access to land, permitting, and utilities, prompted the nonprofit to move operations to another part of Latin America. Where, exactly? New Story won’t say, because “intense interest that the technology generates could undermine completion of the project,” Fast Company reported.
New Story’s website says the houses will be between 600 sq. ft. and 800 sq. ft., and that in the future it would share the technology with other nonprofits and governments that are focused on providing housing for underserved families.
In an email, New Story declined to answer questions about the project.
Printing houses is becoming more common
Icon is by no means alone in developing the technology for printing full-scale houses. In an article posted at ALL3DP, an industry newsletter, Leo Greguric mentions four examples (including the Austin house produced by ICON). They range from a 410-sq.-ft. house built by a Russian company for $10,150 to an office building in Dubai that took 17 days to print at a cost of about $140,000.
The Chinese company WinSun says it built 10 small houses in just 24 hours in 2014, and later went on to fabricate a three-story villa that could be printed in a month at a cost of $160,000.
In 2014, a Minnesota man named Andrey Rudenko printed a small castle with a gantry-style printer he designed. Rudenko’s website shows a variety of buildings made with a printer, and he will sell you a printer of your own for as little as $300,000. It’s capable of printing a house measuring 10 meters by 15 meters (33 ft. by 49 ft.), according to his website.
Although it’s difficult to generalize about costs, Greguric writes, it’s possible to print a house for as little as $4000, a price that would include the roof.
“As time progresses, more and more companies will adopt 3D printed buildings,” he says. “This, combined with developing technologies, will bring prices down and quality up. And that’s great news if it means more access to safe, affordable shelter for those in need.”
Weekly Newsletter
Get building science and energy efficiency advice, plus special offers, in your inbox.
7 Comments
While I think there is a strong future for automation in the building industry, I see little sense in using this in developing countries at this time unless someone has some data to show why it makes sense. What they are printing is essentially equivalent to an uninsulated CMU structure. Automation solves problems of skilled labor shortage, which is the opposite of the problem in most developing countries. A couple people with some minor training could assemble the printed portion of the building shown in a day or so from CMU's. As everyone knows, walls go up quick.
Now a robot that installs insulation, electrical, plumbing, roofing, and windows would be a lot more interesting.
The real near term future for automated construction is in the commercial and infrastructure side where there is a real labor shortage and big rewards for increased construction rates.
I know nothing about the company, but it is going to be equipment like this: https://www.tybotllc.com/
Matt,
I agree. The last thing the Third World needs is a high-tech building method that further alienates them from their 0wn vernacular techniques and materials. The one thing these communities usually have is abundant labour, and not much work. Why not use a method that recognizes that?
Ted Talks is full of well-meaning architects all championing their own elegant solutions to Third World housing problems. None seem to have made any real difference. There are NGOs that have. I think Martin was involved with one. Those typically work with local communities, not impose their ideas from above.
I think this website did an article on this back in 2017 or maybe late 2016. I believe the context was that these 3D structures would serve as better temporary shelters in tropical climates after a natural disaster.
Has any testing or certification been done for the structures? If so, what bodies or engineering firms have released reports? I took a quick glance, but I do not see anything directly applicable in the 2018 IRC. It's an interesting concept, but if it's not allowed "by code" I can't see it taking off here. Though, if we're not the target market maybe that's not a concern.
For the moment populations in tropical climates are the target market.
I'm always interested in new ideas but based on the picture, the carpenters needed to frame that roof could have stood up a few panelized walls in half the time needed to print it. With less equipment on site, less carbon intensity and more r-value.
It automates the easiest part of the job and leaves the hard stuff to people. Because of electrical and plumbing, I honestly think more of a standardized, interlocking, already plumbed and wired panel system would likely be better.
The ease of doing a radius is kind of fun though.
Andy,
Completely agree. And while the radius is fun, in a house that small it really confines how you can layout furniture. I bet framing the curved clerestory window took as long as all of the rest of the project combined.
Log in or create an account to post a comment.
Sign up Log in