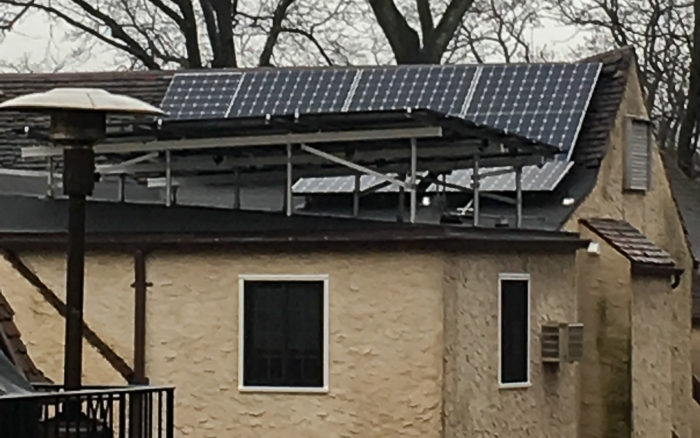
This Q&A Spotlight begins with a confession of sorts from Ryan Lewis, who thinks he may have botched an insulation job.
“Let’s suppose you screw up insulating a flat roof from the exterior in Climate Zone 4A,” he begins in a post at the Q&A forum.
The code minimum for attic insulation in this climate zone is R-49. Lewis’ roofing contractor has added 1 1/2 inches of polyisocyanurate foam insulation on top of the roof deck, which Lewis assumes will perform at its nominal R-value of 9.75.
If he adds enough fluffy insulation between the rafters to get the total roof R-value to 49, Lewis runs the risk of creating moisture problems on the underside of the roof deck. Why? The roof sheathing will be cold, cold enough to become a condensing surface for moisture working its way through the cavity insulation. (For more information on this issue, see “How to Install Rigid Foam On Top of Roof Sheathing” and “Combining Exterior Rigid Foam With Fluffy Insulation.”)
If the layer of foam is too thin, can’t he simply add more to keep the roof sheathing above the dew point? Not now. The roof is loaded with solar panels. In order to add more foam, Lewis would have to remove the panels and the racks as well as the roofing.
What Lewis wants to know now is the maximum amount of fluffy insulation he can install between the rafters below the roof deck without incurring moisture related problems.
Balancing interior and exterior insulation levels
The issue is the proportion of interior to exterior insulation. In Climate Zone 4A, the International Residential Code prescribes R-15 to the exterior, and a total R-value of 49, writes Dana Dorsett. About 30% of the total R-value should be to the exterior of the…
Weekly Newsletter
Get building science and energy efficiency advice, plus special offers, in your inbox.
This article is only available to GBA Prime Members
Sign up for a free trial and get instant access to this article as well as GBA’s complete library of premium articles and construction details.
Start Free TrialAlready a member? Log in
5 Comments
The roof color matters less for the part that is shaded by the solar panels. The solar panel shading will reduce the roof temperature on sunny days, when that heat will help (a little) with drying, but will also reduce the night sky cooling on cold nights when moisture might accumulate. I'd be hard pressed to estimate which of those factors matters more.
Situations like this make me wonder about the feasibility of making a fully sealed cavity with vapor barriers on both sides, and with replaceable desiccant cartridges accessible from ports in the drywall. Wireless hygrometers would monitor the situation and warn before you need to replace the desiccant cartridge or if there was a roof leak. Usually when I wonder that, I conclude that that system would work great for the first two years, while there were in fact no roof leaks, and then it would be forgotten by the homeowners, and be out of service by the time it was needed. But it's a fun thought experiment.
I’m flattered to be written about, I don’t think it’s clear from the original post, which is my fault— this wasn’t a “mistake” in so much as that it just simply wasn’t possible to meet code on the exterior without replacing the entire roof on the house — a proposition that was out of the question for our budget. However, no matter the context, I found this conversation about what to do enlightening.
It's been discussed here before but why do we assume the presence of moisture (in vapor form) against the roof deck? Is it the presumption that the air barrier or is installation is inherently fallible? The presumption that there are numerous penetrations? Ignoring the legitimate concern of moisture content of new building materials, what's the source of the moisture? Why not address the source?
Keith,
Blower door tests on houses air-sealed with a great amount of diligence by experienced builders, still show substantial leakage - and that is when the building is new, un-modified, and also doesn't take into account other methods of vapour-transfer like diffusion, transpiration, or bulk-water intrusion. If we could entirely eliminate the movement of moisture thr0ugh assemblies, building would be a lot easier.
>...why do we assume the presence of moisture (in vapor form) against the roof deck?
There is water vapor in ALL air, and air barriers aren't vapor impermeable (nor should there be). When the roof deck temperature falls below the dew point of the entrained air in the cavity insulation it draws moisture from the cavity air into the roof deck. Even with a perfectly air sealed vapor retarder in place to control the rate of transfer, some amount of moisture will diffuse through the vapor retarder to the colder parts of the assembly.
Making it all very vapor tight as well as air tight has risks too, making the assembly less resilient by slowing all drying paths to a glacier's pace crawl.
In cool/cold climates the wintertime indoor dew point average are usually 35F or higher, and the roof deck temperatures average well below that for weeks/months on end. So in an unvented roof assembly it's good to slow down that moisture diffusion to limit the peak moisture, but still have it sufficiently vapor open to dry toward the interior. Most roofing materials are VERY low permeance, and nothing drys to the exterior through rain / snow /dew wetted roofing.
Log in or become a member to post a comment.
Sign up Log in