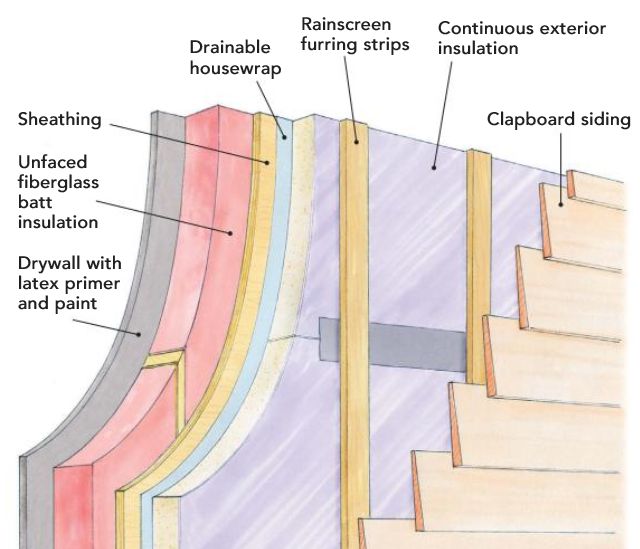
An architect recently told a friend of mine that he was designing a flash-and-batt wall with the spray foam insulation installed on the interior, and the batt insulation toward the exterior, “because that way the vapor barrier will be on the right side of the assembly.”
Anyone who wants to address this architect’s suggestion will need to unpack the assumptions behind his statement. For example, it’s worth discussing whether walls need vapor barriers. It’s also worth discussing why flash-and-batt walls almost always have the spray foam insulation near the exterior rather than the interior of the wall assembly.
To help people like this architect, my friend suggested that I write an entry-level article on wall design, starting from first principles.
Materials choices are wide
When designing a wall, builders can choose from a wide range of materials. Available insulation materials include rigid foam, spray foam, fiberglass batts, mineral wool, and cellulose. Sheathing options include OSB, plywood, gypsum sheathing, and Zip sheathing (with or without adhered polyisocyanurate insulation).
To put these materials together wisely, a designer needs to understand a few basic principles involving water entry, vapor transmission, and air leakage. Moreover, a designer needs to understand these principles well enough to sense which types of assemblies are risky and which are safe.
To point designers in the right direction, I’ve boiled my advice down to five principles.
#1: Airtightness is always good
Regardless of what type of wall you are building, strive for airtightness. The tighter the wall, the better it will perform.
If you can’t control air flow through your walls, it’s hard to maintain the interior conditions than most homeowners expect. Air leaks cause many problems: they increase heating and cooling costs, of course, but they can also lead to moisture problems. During the winter,…
Weekly Newsletter
Get building science and energy efficiency advice, plus special offers, in your inbox.
This article is only available to GBA Prime Members
Sign up for a free trial and get instant access to this article as well as GBA’s complete library of premium articles and construction details.
Start Free TrialAlready a member? Log in
53 Comments
Martin,
This is an excellent introduction and distillation of many articles on GBA. Thanks! I've always been confused about the case with continuous external insulation where the water resistive barrier is on the plane of the exterior side of the sheathing...between housewrap (or zip or whatever) and rigid foam. How can liquid water drain out? On your figure you specify a drainable housewrap, which makes sense to me. Is it necessary (as opposed to standard such as Tyvek)? Does Zip provide a sufficiently dimpled surface? Thank for.
Fred,
Q. "I've always been confused about the case with continuous external insulation where the water resistive barrier is on the plane of the exterior side of the sheathing, between housewrap (or Zip or whatever) and rigid foam."
A. You may want to read this article: "Where Does the Housewrap Go?"
Q. "How can liquid water drain out?"
A. Why do you expect liquid water to appear between rigid foam and your WRB? In the case of rain, some rain will get past the siding -- but that rain will drain down the exterior face of the rigid foam, aided by flashing and your rainscreen gap. It won't reach the WRB. If you are worried about the condensation of moisture migrating from the interior during the winter, the exterior rigid foam keeps the WRB warm enough during the winter to prevent this kind of condensation or moisture accumulation. So stop worrying. There won't be any liquid water on the exterior side of the WRB.
Q. "On your figure you specify a drainable housewrap, which makes sense to me."
A. I didn't draw the detail shown at the top of the page -- it comes from a Fine Homebuilding article -- but it is an excellent detail. If it makes sense to you, go ahead and use the detail as a guide.
Q. "Is it (drianable housewrap) necessary (as opposed to standard such as Tyvek)?"
A. Not in most cases, although if you are unwise enough to sandwich your sheathing between exterior rigid foam and closed-cell spray foam -- something I don't recommend -- you probably want drainable housewrap, especially if you specify OSB sheathing. For more information on this issue, see Joe Lstiburek's article, "Mind the Gap, Eh!"
Q. "Does Zip provide a sufficiently dimpled surface?"
A. Zip sheathing is smooth, not dimpled. But I don't understand your question -- "sufficiently dimpled" for what?
If there won't be any liquid water on the outside face of the WRB, then why bother installing a WRB? And, why do we spend so much time and effort integrating our flashings with it?
Peter,
Q. "If there won't be any liquid water on the outside face of the WRB, then why bother installing a WRB?"
A. A water-resistive barrier is required by code. But if you don't want to use housewrap as your WRB, you are free to use rigid foam as your WRB. For more information on this approach, see "Using Rigid Foam As a Water-Resistive Barrier."
Q. "Why do we spend so much time and effort integrating our flashings with it [the WRB]?"
A. The WRB is the last defense against water entry, and so it makes sense to integrate our flashing with our WRB. But you are free to use the rigid foam as your WRB, and to integrate your flashing with the rigid foam layer, if you prefer that approach.
Another approach that is perfectly acceptable, and which you may prefer, is to install housewrap on the exterior side of the rigid foam layer.
Still confused about double stud. (we do it with diagonal board sheathing usually) sheathing is cold and first condensing surface in a double stud assembly. I've heard about finding iced up cellulose in February from local builders.
Hi Robert.
I don't know if you're going to sort out that confusion. I haven't. Modeling double stud walls shows risks, some builders have reported problems, others, and in pretty cold climate, have been using double-stud walls for enough time to have monitored and remodeled them to feel confident that it is a durable assembly. Maybe all that adds up, at a minimum, to: proceed with caution. Of course, as with any other assembly, the devil is in the details--water management, air sealing, etc. I assume you have seen this: A Case for Double Stud Walls
I think what bothers me about double stud (and I have been doing them for 15 years or so) is that although it can be a very forgiving system and easy to understand, It relies on a well designed and functioning mechanical moisture management system and careful attention paid to interior humidity levels. So if the client has 50 big houseplants that they water every other day and a large gas stove and they don't use the hood. Or they turn off the HRV because of the noise....
Great points Robert.
Robert,
When sheathing is cold enough, it will ice up in winter -- as long as there is a path that allows interior moisture to reach the cold sheathing. One mechanism for moisture transfer is air leakage -- and to prevent that, attention to airtightness is essential (especially for the interior finish layer -- presumably, gypsum drywall in most cases). Another mechanism for moisture transfer is vapor diffusion -- which is why builders worried about moisture or frost accumulation on cold sheathing often specify a so-called "smart" vapor retarder, like MemBrain.
In one of my articles on this topic, "Two Views of Double-Stud Walls," I quoted builder Jesse Thompson, who said, "You can use taped CDX instead of Zip sheathing. Plywood is tougher than OSB. If you want, you can specify a modern WRB — maybe a product from 475. We now have lots of smart vapor retarders to choose from: Intello, Siga Majpell 5, CertainTeed MemBrain, or kraft paper. So you can do it this way: Strapping plus WRB plus taped CDX plus cellulose plus a smart vapor retarder plus GWB."
One final point: If the builders who found "iced up cellulose" made the discovery before the drywall was installed (as might be the case if damp-spray cellulose was installed), then the icing is no mystery. If drywall isn't yet installed, moisture accumulation or icing during the winter is a commonly observed phenomenon.
In the instance I am thinking about, there was a diffusion issue from three years of a slightly pressurized moist house with an HRV working at 10% or not at all. Airtightness was 1.1 Ach50 (mento exterior was primary air barrier) so I think there was just so much moisture being pumped into the walls through diffusion that it didn't get much chance to dry except where the sun hit. Basement walls (insulated) had wet against plastic which was against the concrete. This indicates to me that the house just never had a chance to dry. It probably would have been worse with OSB sheathing instead of boards.
Robert,
You wrote, "Basement walls (insulated) had wet against plastic which was against the concrete." It sounds as if the builder used a method of insulation that isn't recommended. Installing polyethylene on the interior side of a basement wall is a bad idea, and GBA advises builders not to do it.
And if the polyethylene was getting wet, I'm guessing that the basement wall insulation was air-permeable -- something like fiberglass or mineral wool. Air-permeable insulation should never be used on the interior side of a basement wall unless there is an adequately thick layer of rigid foam or closed-cell spray foam between the concrete and the air-permeable insulation.
yes - I've seen mixed info over the years on plastic against the foundation wall instead of stopping it after it comes up from under the slab. 2" xps then a stud cavity filled with cellulose. (living space)
Iced up cellulose, wow!
Could it have been bulk exterior water? Was the ice most prevalent behind the boards or in line with the gaps between boards?
I suspect the more cautious among us (though not so cautious to avoid double studs altogether) would likely use an interior or 'mid-wall' smart vapor retarder and air barrier.
https://www.greenbuildingadvisor.com/article/the-return-of-the-vapor-diffusion-bogeyman
Wood will take on water according to relative humidity. This includes cellulose and the studs. The drying potential (ability to continue diffusing to the exterior) will limit the accumulation. An exterior vapor barrier would certainly be a no-no, and a rainscreen highly recommended. It seems to me number 1 (after bulk water elimination) is to limit interior moisture drives via air stopping and to some degree vapor retarding. Number 2 is allow adequate drying at exterior layer.
Sheathing is also cold in a flash and batt. Flash and batt is basically just a mid-wall air and vapor barrier, but we tend not to talk of it this way because its a 3 dimensional product as opposed to a sheet product. Bulk water can saturate the sheathing, but is less likely to enter a 'cavity' and sit there since that cavity space adjacent to the exterior is plump full of impenetrable foam.
One caveat re: thinking of flash & batt as a 'mid-wall air and vapor barrier': The flash coat of foam only provides that air and vapor barrier inside the stud cavities. Small gaps still exist between stacked framing members, under sill plates, etc, and these gaps are quite happy to let air and vapor whistle right through them.
While everybody on this site seems stuck on stud walls of some kind or other, I'd like to propose a wall structure that mostly eliminates the studs. The one proviso is that the house be a timberframe house that does not need the sheathing for rigidity. With a post and beam structure built on a slab approximately one foot inside of the perimeter of the slab, an ICF wall is built outside the timberframe. Instead of cement, fill the forms with cellulose. Attach the ICF forms to the timberframe with wood. 2x3's will stiffen the ICF wall,provide space for the electricals, and nailbase for the interior finish. Nailbase on both sides of the ICF forms means you can easily attach rainscreen and cladding on the outside of an airtight R40 plus wall. If only it was made with renewable locally sourced materials instead of plastic and styrofoam.
Nils,
Compared to ordinary wall approaches, your suggested wall is significantly more expensive and likely to frighten away most builders. (Builders are understandably conservative.) I see no advantages.
Nils,
"2x3's will stiffen the ICF wall, provide space for the electricals, and nailbase for the interior finish."
Why not just use 2"x4"s, provide whatever level of exterior insulation you want, eliminate the ICF and the timber frame?
How would you suggest attaching R30 to the exterior of a 2x4 supporting wall? Eight inch screws through furrings and six inches of EPS to find the 2x4's behind? Longer screws for mineral wool? Plus the time and expense of insulating between the studs with fibreglass or mineral wool. On the interior you would need Intello or similar, plus ideally two layers of furring for electricals and nailbase for gyprock. Oh sorry I forgot the sheathing outside the 2x4's and finally the rainscreen and the cladding. and don't forget all the tape, and detailing at joist ends. I've never done this but I imagine ICF forms full of cellulose to be more airtight than a double stud wall taped and wrapped inside and out with whatever. Would you even need to tape the ICF?
I'm looking to insulate without sawing all my majestic pines into 2by's. A timberframe means less time on the sawmill, but more craftsmanship.
All the options for insulation involve building stud walls that might as well be supporting walls. SIPS panels can also be supporting walls, and are even more expensive. The ceiling and walls can be filled with cellulose all in one operation. I think the time and effort saved would be worth the extra cost. My first cost estimate for ICF just came in. I'll know soon enough.
Nils,
Your complaint seems to be about studs. All your assembly does is substitute one rather novel form of exterior insulation for the more conventional one. Leaving aside whether it's easier or even possible to use ICFs that way, using the timber-frame and stud infill adds nothing (beyond expense and complication) to the assembly that load-bearing studs don't already bring. If you are going with timber framing, and have something against studs, why not choose an assembly that completely eliminates them and use SIPS?
Malcolm. With a sturdy well braced timberframe structure a stud wall is needed for the sole purpose of holding insulation, and doors and windows. As Martin said in another thread; a stud wall would make the timberframe superfluous. SIPS would also make the timberframe superfluous,and are very expensive. I'm aiming for Passive House or better levels of insulation because we are in a cold spot half an hours drive north of the Vermont border. Twice this past week the temperature has dipped below -30C. R40 walls don't seem excessive. I don't like the idea of hanging rainscreen and cladding off of long screws that might or might not hit the stud I'm aiming for. What kind of wind resistance would the cladding have and how much would the appropriate screws add to the budget? ICF forms are made to withstand tons of liquid cement so I think that with the 2x3 bracing fixed to the ICF wall and the timberframe, that the structural and insulation requirements are met in a wall that will be easy to construct and sturdy.
Nils,
A stud wall does make the timber frame structure redundant. But you still have stud walls, you are just calling them something else. That's the common dilemma both timber frame and and steel structure buildings face: Infilling between the load-bearing elements needs studs, which could have held up the building.
I worked with ICF forms last summer. On their own they have just enough strength to resist the outward pressure of a concrete pour. They rely entirely on the concrete for their rigidity, so the idea that they will be more robust and capable of supporting cladding if filled with cellulose than a wood framed wall doesn't make sense.
This is one of an string of very unorthodox assemblies you have suggested. I appreciate that Blue Sky thinking can shake up conventional approaches and may lead to something useful, but to be honest I don't think you have enough practical experience to evaluate them, and seem dismissive of any flaws that get pointed out. That may or may not end up being an approach that bears fruit for you.
Nils,
I'm not sure why you are talking about attaching R-30 rigid foam to the exterior side of your wall. What's your climate zone? In Zone 5, you could go with R-7.5 of rigid foam and 2x6 walls; in Zone 6, you could go with R-11.25 of rigid foam and 2x6 walls; in Zone 7 or 8, you could go with R-15 of rigid foam with 2x6 walls.
All of these suggested options use considerably thinner rigid foam than R-30 of rigid foam, and avoid the "long screw" problem that seems to irk you so much.
For more information on this issue, see "Combining Exterior Rigid Foam With Fluffy Insulation."
You wrote, "I imagine ICF forms full of cellulose to be more airtight than a double-stud wall taped and wrapped inside and out with whatever." Well, you might imagine that, but I doubt that you're right. ICF walls are airtight because of the concrete. If you omit the concrete, air can whistle through the seams -- and cellulose is also air-permeable.
An ICF wall without any concrete would also be tippy. It would be totally non-structural -- just a stack of lightweight blocks of EPS. If you want exterior EPS, just buy some EPS sheets and attach them to your sheathing the ordinary way.
Is timber-framing cheaper or easier than building a stud wall? No, but some people do it anyway, because it is satisfying and beautiful. Go ahead and build a timber-frame if you want -- but it's hardly a good approach for most homes.
Martin. A 2x6 wall R15 rigid foam will theoretically be R37; just shy of the minimum I'm aiming for. The long screws don't irk only me. Some engineers in BC are specifying an angle of 15 degrees upwards when installing long screws and three quarter inch plywood sheathing to counter the structural weakness.
The ICF forms I have seen looked to fit very tightly and there was no evidence of water leakage from the tons of liquid concrete poured into them.
As far as being tippy, I would comfortably turn my back to an ICF wall, but never would I let go of a stud wall until it was anchored and thoroughly braced.
A timber frame is not only beautiful and satisfying to make but stronger than a stud wall structure. When you have to saw all your lumber one eight by eight seems like less work than eight two by fours.
I really appreciate your well thought out and informative articles. I'm not sure if there are any I haven't read since I logged onto this site. The comments section has also proved invaluable. Enjoy your retirement.
Nils,
It's your house, and you should build it exactly the way you want to. You seem committed to your plan. Good luck.
SIPS need far more consideration than they get.
There's a general view on this site that SIPS should be avoided, apparently because of failures in certain SIPS structures under certain conditions. But the causes for those failures and the solutions for them are very well understood and the solutions are straightforward to implement.
Just like any structural system, even conventional 2x framing, detail the assembly poorly and there will be problems. Conventional walls have problems when openings aren't flashed properly. How many hundreds of thousands of homes across the USA have seen damage from that? EIFS were a disaster when they first appeared but are reasonably reliable now.
Design and build a SIPS house right and you'll have a tight, highly insulated wall.
I would opt for an EPS foam and upgrade from OSB to plywood if the budget allows. OSB doesn't generally hold tape as well. XPS, and to a lesser extent PUR and Polyiso, are more damaging to the environment and lose enough of their insulation value over time that they aren't much better than EPS after 10 years.
This page is a good summary of SIPS:
https://www.wbdg.org/resources/structural-insulated-panels-sips
This page has a bunch of documents you can download that describe best practices and detailing:
https://www.sips.org/publications/for-design-professionals/view/19/download
Martin,
The more I read about the situation elsewhere the luckier I feel to be in BC. Here is a list of government sponsored seminars on Building Science available to us:
https://mytrainingbc.ca/buildingsmart/
Malcolm,
Looks like a good use of government funding!
Of course, the building industry in British Columbia had to experience the leaky condo crisis of the 1990s (with an estimated $4 billion in repair costs) to wake up the local community of builders, architects, and government leaders to the need for building science solutions...
It caused a lot of hardship, but proved great kick in the pants for everyone in the industry.
Malcolm,
When I got interested in superinsulation in the early 1980's virtually all of the information I used was coming out of Canada. You were way ahead on the construction and diagnostic front.
Doug,
It's always had great government backing here. When I was working in Ottawa and had a building science question you could call up the NRC and they would get an expert in the relevant field to call you back and discuss it. Pre-internet that advice was like g9ld.
Martin, thanks for this article. It is very timely for discussions I’m having with my architect and general contractor now. I do have a couple questions.
I’m interpreting principle #2 as an argument for not building vapor open wall systems at the expense of air sealing or protecting sheathing against wetting from condensation. It is possible to achieve all of those objectives though, correct?
My particular project is in coastal Delaware, zone 4A. My understanding is that in zone 4A I’m safe to use any thickness of continuous exterior insulation. Taking into account the possibility of hurricanes in our area, my preferred wall would probably be from outside in: fiber cement clapboards; 1x4 furring to establish a ventilated rain screen; 1.5 inches foam; plywood or OSB sheathing; 2x6 stud walls 16 in o.c. A WRB would be in there somewhere dependent on whether my GC prefers to install the windows as innies or outies. My reading from the Building Science Corp website is that 1 inch of unfaced polyiso has a permeance of 2.7-4.4, so I presume 1.5 inches of unfaced polyiso would be a Class III vapor retarder.
Question 1: In the scenario above, wouldn’t a wall using unfaced polyiso perform as well as one using foil-faced polyiso—in the words of the last paragraph of that principle “exceptionally well”—and still result in an assembly open to vapor flow in either direction?
Foil faced polyiso would seem to provide protection against inward solar vapor drive, but the summary paragraphs describe this problem as rare. I believe this problem is further mitigated by the use of a ventilated rain screen.
Question 2: How should I weigh the benefit of creating a wall assembly that can dry to either side (by using unfaced poliso or EPS) against the benefit of preventing inward solar vapor drive (by using foil-faced polyiso)?
Thanks in advance.
John,
Q. "I’m interpreting principle #2 as an argument for not building vapor open wall systems at the expense of air sealing or protecting sheathing against wetting from condensation. It is possible to achieve all of those objectives though, correct?"
A. Correct.
Q. "Wouldn’t a wall using unfaced polyiso perform as well as one using foil-faced polyiso — in the words of the last paragraph of that principle 'exceptionally well' — and still result in an assembly open to vapor flow in either direction?"
A. Yes.
Q. "How should I weigh the benefit of creating a wall assembly that can dry to either side (by using unfaced polyiso or EPS) against the benefit of preventing inward solar vapor drive (by using foil-faced polyiso)?"
A. If you have a ventilated rainscreen gap, you don't have to worry about inward solar vapor drive. To address another aspect of your analysis: I can't think of any benefit to using unfaced polyiso or EPS compared to foil-faced polyiso -- any of those types of rigid foam will work just fine. If you choose to install foil-faced polyiso -- and I'm not saying you need to -- any moisture on the exterior side of the rigid foam dries outward, and any moisture on the interior side of the rigid foam dries inward. And, unless you make gross flashing errors or air sealing errors, there isn't any reason to imagine that there will be moisture buildup anywhere.
One more thing I didn't think of earlier--if we choose to install windows as innies and end up with the WRB inside of the foam, would using foil-faced polyiso then be preferable from a water shedding perspective or would there be no functional difference between using foil-faced or unfaced polyiso? Thanks again.
John,
Foil-faced polyiso would certainly do a better job of shedding water than unfaced polyiso (or, more accurately, polyiso with a vapor-permeable facing -- since as far as I know, all types of polyiso have some type of facing). That said, I'm not sure that the difference would actually matter.
Martin - Again, many thanks for taking the time to share knowledge on this. You and all of the other regular contributors make this a valuable site for those of us that are interested in learning.
I'm designing a remodel of our 24'x48' 1860 stone house and want to reduce the perpetual cold caused by the exterior walls. Since the no-stucco 18" walls allow air through at some spots, I'm thinking the first step is a layer of closed-cell foam on the interior walls. I'll re-frame interior walls next to the foam to eliminate bridging through the studs.
Does this sound like a reasonable plan? If so, how thin of a layer of foam is effective (for cost efficiency)? How do the rules for interior R-value change, when the exterior surface is 18" of stone?
Thanks for any comments.
What climate zone are you in? In many climates, the necessary R-value inside would not be changed by the 18" of stone.
R-5 in Allentown, PA. Sorry for neglecting this in my question.
Mike,
If your primary concern is air leakage, one inch of spray foam (either open-cell spray foam or closed-cell spray foam) will create an air barrier. (For more information on this issue, see "Air Leakage Through Spray Polyurethane Foam.")
That said, if you are going to the trouble of hiring a spray foam contractor to come to your house and spray the walls, you might as well get a thicker layer -- as thick as you can afford.
Your 18-inch-thick stone wall has a very low R-value -- about R-1 or at most R-1.5. For all intents and purposes, it's close to zero. If you're aiming for an R-20 wall, you'd want about 5 inches of open-cell spray foam or 3 inches of closed-cell spray foam.
Code requirements are R13 + and R3.8 continuous layer of insulation, or R20 total without the requirement for a continuous layer. If you use a "flash and batt" approach, at least 27% of the insulation should be in the spray foam or other non-permeable layer. So for R-20 total, that would be R-5.4, which would easily be met with 1" of closed cell spray foam.
If you go with spray foam, I recommend asking for the new low-global-warming-potential "HFO" blowing agent instead of the current standard "HFC" blowing agent that has a global warming impact more than 1000X worse than CO2. Also make sure you have a reputable spray foam contractor who will make sure that the surface is adequately warm before spraying it (which might mean a long wait until those thick stone walls are warm enough!) and who will give you in writing their policy for what happens if the foam doesn't cure properly and your house becomes unlivable. That's rare, but it does happen.
While spray foam is the standard approach, I would consider using foil-faced polyiso foam boards and taping the seams and edges with high quality tape in order to avoid the risk of bad foam, to allow proceeding sooner, and perhaps reduce cost.
You might post a question in the Q&A section to get more opinions--I don't have first-hand experience with stone buildings so you shouldn't put too much weight on my comments.
Charlie,
Thanks for your advice about the risks of interior foam and how to minimize them.
My preference for closed-cell was to stop air leakage where it occurs. Due to the irregular stone surface, foam boards would create a cold air space (~1.5"). But, maybe this is insignificant. I don't know...
Yes, that space is a concern; how much of a concern is hard to know. The concern would be that cold outside air circulates through that air space, making it colder than the inside surface of the stone. One way to think about it is that that doesn't really matter, because on average, the stone temperature is the same as the outdoor temperature. Another way to think about it is that the stone stays at the average temperature over a few days, and never dips to as low or as high a temperature as the air, so even though the total heating energy needed is the same with either configuration, the peak heating need is less, making it easier to heat with a smaller heating system, and making a heat pump (if you use that) run more efficiently. And in mild weather, you extend the time that you don't need heating or cooling.
It would be great to find some data from tests of doing it either way, monitoring the temperature of the inside surface of the stone with sprayfoam, or the space between the stone and the insulation with foam boards, and comparing those results.
It's possible that some other approach could be used on the inside surface of the stone to create an air barrier more closely coupled to the stone, in addition to the taped foam layer air barrier--either a peel and stick air barrier membrane or a fluid applied product, maybe with some mortar first to smooth and level the surface, but at that point you are doing an experimental and complicated process instead of the better proven spray foam approach. Does your schedule allow waiting for the stone to warm up before foaming it?
The traditional approach for wall surface is stucco, which is on some inside walls of this house. If the outside of the house was still in stucco (removed decades ago), I wouldn't have the air blowing in.
I'll wait until the sun warms things up and go with an inch of closed-cell. I'm not sure how I'll confirm the quality of the installer, so I'll use the warming time to figure that out.
Posted comment on FHB but this seems more active...
I see many people installing ~1" EPS (~R4) onto a 2x6 batt wall in a zone 6 climate (Ontario). It seems like the comment you make about the "tried-and-true approach — for example, a 2×4 wall with a continuous layer of exterior rigid foam" can lead to a lot of high risk walls as it can easily be taken without the context of " it needs to be thick enough to ensure that the first condensing surface is above the dew point during most of the winter". Adding 2" (~R8) of EPS or 3" (~R12) which would be required to do this based on Zone 6 Table N1102.5. This starts to become both cost prohibitive, as well as complicated to build (multiple layers). I just wanted to point this out, as I feel like I see a lot of builders thinking they are OK with 1" of EPS in zone 6, when this seems like it could be very risky. Would this be a valid concern? or is the risk not that high?
The marketing push to use Zip-R sheathing is going to exacerbate this.
benshep,
Walls with 1" of exterior foam have become very common in Ontario. With good air-sealing and an interior vapour-barrier appear to work just fine. They are of course not as safe as walls with the recommended ratio of interior insulation and exterior foam, but experience seems to show they can't be classed as risky.
https://www.greenbuildingadvisor.com/article/rethinking-the-rules-on-minimum-foam-thickness
Fantastic, feels like that article was written for me! I do think I would try to avoid it myself, but makes sense why it can work now. Tricky part is that I am sure some of these builders are leaving out the interior poly due to the overwhelming dialogue against it. That helped clear it up for me though.
benshep,
I'm with you. I'd still stick to the recommended ratios. Building any risk into a wall makes it so much less forgiving if something goes wrong.
My own house built in 1978 in Minneapolis has 4 mil interior poly, 2x4 with R-11 fiberglass and R-5 Styrofoam exterior sheathing. Like new inside of those walls whenever I have changed windows or the like.
Doug
I'm in zone 6 (New Hampshire) and we're currently building with 2x6 walls with Zip R9 sheathing. It was my understanding that this assembly would be on the risky side if the cavities were filled with R21 to R23 fluffy stuff (blown cellulose or blown FG). Since I have pretty much decided I need CCSF on my roof assembly, I was thinking about just having them flash the walls with 2" of closed cell to move the "first condensing surface" inward, and just skip batts altogether. Does that make sense at all? Any reason that could be interpreted to NOT meet code? (there's no building inspection here).
Jim,
From a building science perspective (and a code perspective), your idea will work fine.
From a green perspective, your plan isn't great. Green builders usually try to avoid using closed-cell spray foam because most brands of closed-cell spray foam use blowing agents that have a very high global warming potential.
Thanks Martin. Alternately, assuming the Zip R9, would using a R19, faced batt or other fluffy cavity fill be appropriate, relying on drying to the interior, if moisture were to enter? I suppose a smart vapor retarder would also fit the bill, as mentioned in the article linked by Malcolm, above.
Jim,
Q. "Assuming the Zip R9, would using a R19, faced batt or other fluffy cavity fill be appropriate?"
A. No, not according to the usual rules. In Zone 6, a minimum of 36% of the wall's total R-value should be provided by the rigid foam layer -- and you are proposing an assembly that has only 32% of the R-value from the rigid foam layer. More information here: "Combining Exterior Rigid Foam with Fluffy Insulation."
Log in or become a member to post a comment.
Sign up Log in