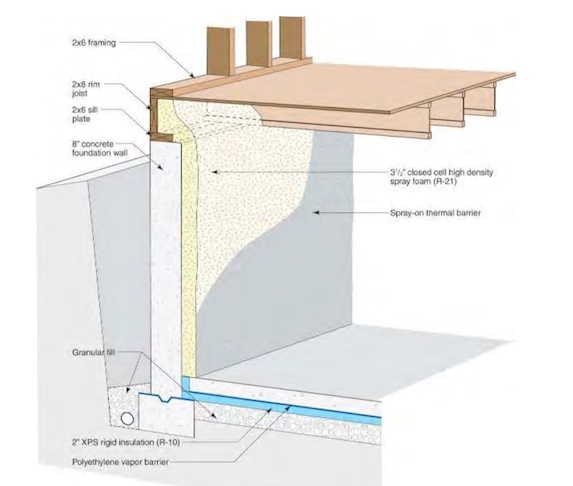
Dave Feldman is building a new house near Boston, Massachusetts, that will have a walkout basement with a tile floor. His goal is to have the floor comfortably warm in this Climate Zone 5 locale even in the dead of winter.
Feldman plans to insulate the basement walls with closed-cell spray polyurethane foam. For insulation below the slab, Feldman is considering two types of rigid foam insulation—expanded polystyrene (EPS) and extruded polystyrene (XPS)—as well as closed-cell spray polyurethane foam.
He’s uncertain whether to insulate the slab with 2 inches of foam (which he estimates at R-10 to R-14) or invest in 4 inches of foam and double the R-value.
“I don’t want to waste materials if there’s not a useful impact,” he writes in a post in the Q&A forum, “but [I] also don’t want to skimp on something that’s pretty much impossible to change once the house is up.”
His request for feedback is where we begin this Q&A Spotlight.
Please, skip the spray foam
The spray foam that Feldman has in mind is Demilec’s Heatlok HFO High Lift, which uses a hydrofluoro-olefin (HFO) blowing agent developed by Honeywell. HFOs have a much lower global warming potential than conventional blowing agents, but in Dana Dorsett’s view, spray foam is still a poor insulation choice.
“Why?” he asks. “That is some of the lousiest bang/buck going, and one of the least green methods of insulating a framed wall possible, despite using HFO blowing agents. Expensive (financially & environmentally) closed cell foam between framing is a waste.”
Dorsett directs Feldman to this article from Fine Homebuilding magazine explaining the basis for his conclusions while suggesting that dense-packed cellulose is the best choice for cavity insulation.
“Save the foam budget for…
Weekly Newsletter
Get building science and energy efficiency advice, plus special offers, in your inbox.
This article is only available to GBA Prime Members
Sign up for a free trial and get instant access to this article as well as GBA’s complete library of premium articles and construction details.
Start Free TrialAlready a member? Log in
14 Comments
Do you have a thermal break detailed under the door sill at the walkout basement entrance?
My basement slab is insulated with two inches of foam, and it's actually pretty great. The floor never feels cold even even it's -30 outside.
Care was taken to ensure no thermal bridging between the slab and the footing. It's completely floating on and between foam.
When its -30 outside your basement slab is sitting on 40 - 50 degree soil. When its 100+ outside, you basement slab is sitting on 40-50 degree soil. (assuming you are in the Northern portion of the US). Soil temp below the frost line is ALMOST completely agnostic of the outside temperature conditions.
Unless it's a walkout basement
The best way to insulate a basement slab is before its poured............
A couple interesting notes i found since the exchange:
To get the lally columns on the footing directly we’re having to frame the house, place the columns, cut in the insulation around the columns then pour the floor after the house is built. Engineer and architect wanted to ensure the point loads were on the footings instead of the slab in eps.
This does make it more complicated than an open pour so wanted to mention and share that.
David,
Why not just put block-outs around there the columns are going on the footing and pour the slab? That's what we do.
The pads are 3x3 each. Do you block the whole pad and insulate/pour around the columns later? It’s 2” eps and 5” slab.
No we just block out enough space for the base of the column, much as you do for plumbing at tubs. Pour the slab, attach the column in the usual sequence of framing, and fill the void with canned foam.
This is a detail I've been wondering about for awhile. I assume you don't bother dropping insulation down and under the footing, do you? The only uninsulated portion being directly beneath the column.
I've wondered if there's much value to including mid-span footings in the envelope. Many people do that? My gut tells me it's a pretty minimal energy penalty not to, and some engineers /coders may get squimish with the foam there. (I'm talking foam beneath footing, none in between slab and footing, small vertical leg connecting.)
Tyler,
The equation may be different in cold climates, but here in the PNW I don't worry much about the loss from uninsulated footings. With high compressive strength foam it isn't a structural problem to run it under footngs, but it's something I temperamentally just couldn't bring myself to do.
Curious if anyone will be monitoring this article, but will ask the question anyway.
I am about to run 4" of EPS foam under two new construction builds outside of Boston. I will of course follow the detail of carrying the foam up the foundation wall slightly (and over the footings) to ensure a thermal break from slab to wall.
My two questions are;
1 - I spoke in detail yesterday with one of the leading EPS manufactures in the Northeast and they insisted that your poly vapor barrier should go UNDER their EPS foam on top of the stone base. The logic was that although minimal, the EPS still has a water absorption rate of 3-4%. Every detail for sub slab insulation on GBA and other places always has the vapor barrier runnning over the subslab insulation directly between insulation and concrete slab. So what's the right way, the GBA way or the manufacturer recommendation?
2 - The garage for these homes is attached on the front of the house and has the master and a common bath/hallway above it. The garages will not be heated and the ceiling of the garage will of course be insulated. Is it wasteful to also insulate under the garage slab? Would a lesser 2" EPS foam make sense?
Regarding the poly vapor barrier placement: My understanding is that it belongs on top of the foam for several reasons:
1. You always want the vapor barrier on the warm side, and unless you're building an ice rink, your basement is going to be the warm side. See this video by Joe Lstiburek: https://www.youtube.com/watch?v=MwfpWA4HoNY
2. During the pour, you need to prevent individual pieces of foam from floating up and ruining the slab. Taping the foam can prevent this, but it's simpler to put the poly on top.
3. When constructing things, if you get caught with rain before the pour, you be stuck with water on top of the foam and under the poly. Not a good thing even if it's a small amount, but it's a nightmare if it's a large amount.
4. The poly barrier right beneath the slab serves as a flat slip sheet and it will help prevent cracking while the slab is drying.
“[Deleted]”
Log in or become a member to post a comment.
Sign up Log in