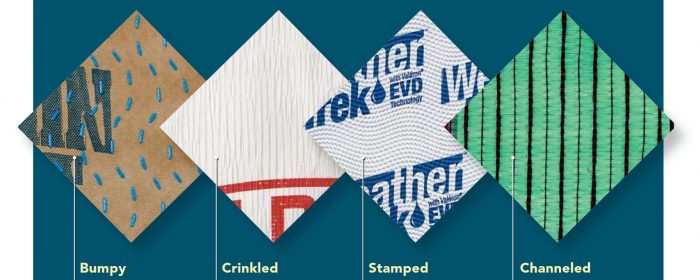
If you plan to install a layer of continuous rigid foam on the exterior side of your wall sheathing, where do you put the housewrap? There are many opinions on this issue, but the usual answer is that the housewrap can be installed either between the sheathing and the rigid foam, or on the exterior side of the rigid foam. Either approach can work, as long as the builder knows which layer will function as the home’s water-resistive barrier (WRB), and as long as the WRB is integrated with the window flashing, door flashing, and penetration flashing. (For more information on this issue, see “Where Does the Housewrap Go?”)
The first time that a builder sandwiches housewrap between his wall sheathing and a layer of rigid foam, he or she may feel uncomfortable. Among the questions we’ve received on this issue are the following: How can the housewrap work as a WRB when there is no clear drainage path for liquid water? Shouldn’t I be installing one of the wrinkled or bumpy housewraps in this location to facilitate drainage? (For more information on wrinkled housewraps, see the Fine Homebuilding article, “Are Drainable Housewraps Enough?”, or the GBA article, “All About Rainscreens.”)
Here’s the short answer: It’s perfectly OK to install a wrinkled housewrap in this location if you want to. But wrinkled housewrap may not be necessary.
When should you include a rainscreen gap?
To address the question of when wrinkled housewrap is nessesary, it’s helpful to step back and broaden the discussion somewhat—specifically, to establish when walls need a rainscreen gap. Before delving into rainscreens, though, I’d like to tip my hat to building scientist Joseph Lstiburek, on whose analysis I rely heavily. (For those who want to read what Lstiburek has to say…
Weekly Newsletter
Get building science and energy efficiency advice, plus special offers, in your inbox.
This article is only available to GBA Prime Members
Sign up for a free trial and get instant access to this article as well as GBA’s complete library of premium articles and construction details.
Start Free TrialAlready a member? Log in
29 Comments
Does the insulation values goes down with the type of "air space" created by a 3D WRB? Maybe some more than others?
Armando,
The answer to your question is in my article. In the next-to-the-last paragraph, I quote Joseph Lstiburek, who wrote: "But won’t the tiny gap cause a loss of thermal performance of the foam sheathing? Yes. How much? About 5 percent of the thermal performance of the foam sheathing (not the entire wall assembly) with the 1/8-inch gap, less with a smaller gap. With ‘crinkly’ stuff you loose next to nothing."
Translation: If you are installing R-5 foam, then the foam layer will act like R-4.75 foam if you include an 1/8" gap. With R-10 foam, the foam layer will act like R-9.5 foam. If you use "crinkly" (wrinkled) housewrap, there will be virtually no loss in thermal performance.
Sorry, my bad... I guess I missed it being in a hurry to get to Peter Yost's webinar this morning.
Great article, Martin!
In regards to your "bumpy OSB" reference, Zip sheathing is kind of bumpy as the felt layer is on the rough side of the OSB and has a subtle grid pattern. It's not much, but perhaps enough to matter. I might do an experiment to see if water will drain behind rigid foam when fastened through Zip sheathing.
I still wouldn't sandwich OSB between closed cell and rigid foam without a larger gap, but perhaps this could constitute a little extra drying for walls with air permeable cavity insulation and exterior rigid foam.
I'll report back soon.
Rick,
Matt Risinger already conducted that experiment. Here is a link to his video.
Spoiler alert: Zip sheathing is bumpy enough to allow drainage.
The timing of this article was perfect for me as I have been stressing about putting a crinkle wrap between the zip and the 2" XPS. Question though, with the zip fully taped is there any reason to tape the rigid foam also?
Question though, with the zip fully taped is there any reason to tape the rigid foam also?
We do both as part of our “belt and suspenders” approach. Are both scientifically necessary? Probably not, but if you do both you’ll never find out. It’s Short money.
Lee,
Bob's answer is a good one. Tape both layers if you are a belt-and-suspenders type. Otherwise, just tape the Zip sheathing.
Haha- thanks Martin!
Good to know! (Puts away saw, sheathing scrap, and utility knife ...)
Adding on to this discussion--Lorne Rickets of RDH recently gave a presentation (Exterior Insulation: A More Layered Understanding), which included their spray testing of walls with exterior insulation and open-joint cladding. Clips of the relevant slides below.
They had a slick rig to measure where the water ended up draining--off the exterior face of the cladding, the backside of the cladding, the face of the exterior insulation, and the water-resistive barrier behind the insulation.
Quick takeaway: no drained water measured getting through the insulation, to the water control layer. Basically, all of those layers shed the water before it gets further into the wall.
Of course, we must design the walls assuming water will get back there--entirely likely with penetrations and other details. But this is an elegant demonstration that the layering of this wall intrinsically limits how much water gets all the way back there.
Also: the research this is based on: https://www.rdh.com/wp-content/uploads/2017/10/RDH-BSL-Drainage-Balance-Spray-Rack-Report.pdf
Kohta,
Thanks for providing information on research that confirms the analysis in my article. I appreciate it.
Kohta,
Thanks for the link. Apart from the conclusions they draw, my big take-away is not to use an open-joint cladding.
Kohta or Martin - Occasionally we install taped sheathed walls with taped polyiso, a black WRB on top of the taped insulation, and open-joint cladding with Ipe or cedar board or Hardie (panel and board) siding, over 1x4 rainscreens, for a modern look. I assume this still ok, right?
Armando,
Malcolm Taylor's comment -- "my big take-away is not to use an open-joint cladding" -- is apparently a reaction to the researchers' obervations on how much water reaches the insulation layer when a wall with open-joint cladding is subjected to driving rain. The researchers wrote:
"There is a decrease in the total water collected when the joints are taped, and a further decrease for the vinyl siding, as more water was reflected from the higher percentage of cladding, and splashed over the collection trough onto the floor. This test result means that if the cladding is not a high-percentage open-jointed rainscreen, the amount of water actually coming into contact with the insulation layer in a wall assembly with a realistic driving rain is likely very small, assuming there are no gross deficiencies in construction."
Open-joint cladding obviously lets in the rain. It's an architectural conceit, chosen by a designer to satisfy a desire for a certain look. The open joints obviously undermine the principles of water management.
That said, if a client insists on having that fashionable look, the wall can be flashed in such a way that the water is managed. You just have to be very careful with your flashing and WRB installation.
The other issues with open-joint cladding have to do with finding a fastening method that prevents curling or warping, and the question of cladding durability.
I use a rain screen as a matter of course (that's a clever play on words).
On new construction, we pretty much always build double wall with dense pack cellulose. We try to remain as vapor open to the exterior as possible, so we want to make sure it can easily escape.
On renovations, especially in the historic district where we frequently work, it's usually not possible to increase the thickness of the assembly with a real rainscreen, so we try to use the crinkly or bumpy stuff there.
This is a super useful article. I was wondering about whether vapour barriers might be another reason to use a drainable WRB.
Here in Canada, interior vapour barriers (poly sheeting usually) are found in the vast majority of houses built since the early 80's and the code in most (maybe all?) provinces has requirements for vapour retarders. Building permit officials are so used to assemblies with poly that you just can't build any sort of wall without showing them where the vapour barrier is going to go.
I would think that the presence of an interior vapour barrier would be another occasion for the mandatory use of a drainable WRB. Like closed cell foam, the vapour barrier would prevent interior drying of the sheathing. Best solution would be to omit the vapour barrier but that's probably too costly (remove all the drywall or sheathing + cavity insulation?) and might not get through the building department - a problem for a new build as well.
Patrick,
If we're talking about houses with exterior rigid foam, the rigid foam slows down exterior drying to such an extent that wrinkled housewrap is irrelevant to the discussion of exterior drying rates.
I think your worries about interior polyethylene are unwarranted. To learn why, read this article: "Rethinking the Rules on Minimum Foam Thickness."
Thanks for the pointer to that article. I get the logic about how an interior vapor barrier actually reduces issues that could be caused by too thin foam. But what if everything isn't done perfectly...like say window leaks or some interior air sealing wasn't perfect? Then you've got moisture in walls and no way to get out. Seems risky.
I'm not sure I'm following you regarding the inability to dry outward with exterior foam. I thought that was the logic for including a wrinkled house wrap when you have exterior rigid foam and closed cell between the studs. Joe's "Mind the gap, Eh!" article seems to suggest that the wrinkled wrap provides just enough "hygric redistribution" to allow some drying to the exterior so that the OSB sheathing can dry in at least one direction. I don't see why this wouldn't also work with an interior vapour barrier.
Patrick,
Q. "What if everything isn't done perfect--like say window leaks or some interior air sealing wasn't perfect? Then you've got moisture in walls and no way to get out. Seems risky."
A. That would be risky. I never said that the wall you described wasn't risky. But in the case you are talking about, the main problem would be the defective window flashing, not the interior polyethylene.
Q. "Joe's 'Mind the gap, Eh!' article seems to suggest that the wrinkled wrap provides just enough hygric redistribution to allow some drying to the exterior so that the OSB sheathing can dry in at least one direction."
A. You're basically right--although the issue of hygric redistribution is a little more complicated than the way you stated it. Removing concentrated moisture and redistributing it so that the moisture is "averaged out" over a larger area is often all you need to do to avoid OSB rot. I'm not going to pretend that I understand all of the physics involved--but suffice it to say that wall performance improvements occur even if the water never makes it all the way to the exterior. I agree with you that wrinkled housewrap can't hurt, and might help somewhat, in the case you're talking about.
We've used bumpy houseware as a last ditch drainage material in the event of water (which, I agree, is highly unlikely). We use it specifically when we're applying wood shingles, where we apply the rain screen strapping horizontally. We also use rough pine strapping in these cases which let's water pass anyway through the saw kerf gaps. I believe that there is enough air getting through the shingles to keep everything dry, while the multiple layers of shingles help keep water out.
I'm confused where to put the WRB.
I'm building a tiny 11m^2 cabin in a climate similar to US Zone 3 (think: Atlanta, but with seasonal high winds) and the exterior wall will be 24mm plywood + 2 layers of 65mm foam (130mm total) + horizontal furring strips + vertical metal siding panels.
Here's the metal siding website: https://www.nichiha.co.jp/center-siding-roof/centerSiding.html
Metal siding install guide: https://www.nichiha.co.jp/pro/pdf/tech/metal/metal_1908_02.pdf
(page 35 shows the detail for vertical install which specifies horizontal furring -- I guess this is OK?)
On the interior will be exposed studs with no insulation -- no real reason, except I like the look, convenience, and less to worry about. The roof will also be 24mm plywood deck with rigid foam on top and a 30cm fake soffit (like in this video: https://www.youtube.com/watch?v=9GIrSF26SjA -- unless you know a better method) and sheet metal for the top layer.
Metal roof: https://www.tsukiboshi-shoji.co.jp/product.php?s=97
I will be doing outie-style for the windows (probably a Dudley box unless you can convince me otherwise).
So based on what I've read here, on Joe Lstiburek's site, in the REMOTE guide, etc I'm still a bit confused about the WRB. I'm inclined to use the foam as the WRB (since it's 2 layer total 130mm thick) and not use Tyvek anywhere, but then I'm confused about how to tie the WRB of the roof foam to the WRB of the wall foam.
Do I just put a roof-grade peel and stick membrane starting ~30cm from the top the wall and lap it all the way up to the top of the roof, on top of the foam, and then below that there's nothing between the foam and the plywood roof deck? It seems like the obvious answer but I haven't come across any discussion or diagrams of this. Then I would assume I'd put the furring for the the sheet metal roofing directly on top of the membrane.
Edit later: I guess the other option for the WRB would be putting the roof membrane on top of the plywood deck and extending it out over the top of the wall foam, then putting the roof foam on top of that. But then on the roof I've got the WRB under the foam, and on the wall the WRB is the outside surface of the foam itself. Is that okay to have the roof and wall WRB on different planes relative to where the insulation is?
Any thoughts?
Thanks,
Ben
Ben,
Q. "Do I just put a roof-grade peel and stick membrane starting ~30cm from the top the wall and lap it all the way up to the top of the roof, on top of the foam, and then below that there's nothing between the foam and the plywood roof deck?"
A. Yes, that will work. Or the peel-and-stick can go directly above the roof sheathing (the plywood) -- that's often done when the roof has exterior rigid foam. The peel-and-stick is the air barrier -- and the best location for the air barrier on this type of roof assembly is between the plywood sheathing and the exterior foam. If you go this route, the peel-and-stick can be integrated with a water-resistive barrier (housewrap) installed on the walls -- and in that case the water-resistive barrier would be between the wall sheathing and the exterior foam as well.
For more information on this type of roof assembly, see "How to Install Rigid Foam On Top of Roof Sheathing." You may also want to read these two relevant articles:
"Airtight Wall and Roof Sheathing"
"Getting Insulation Out of Your Walls and Ceilings"
Thanks for replying so quickly.
> If you go this route, the peel-and-stick can be integrated with a water-resistive barrier (housewrap) installed on the walls -- and in that case the water-resistive barrier would be between the wall sheathing and the exterior foam as well.
I guess my confusion is if it's OK to use a membrane applied to the plywood roof deck as the WRB on the roof (_under_ the horizontal foam), but then have it lap _over_ the outer surface of the vertical foam which would serve as the wall WRB, thus not needing any Tyvek type product... AND then being able to flash the outie windows using Joe L's guidelines which assume the foam is the WRB?
Based on the many hours of reading and understanding the concepts here on GBA and on Joe L's GSC site, I think it'll be fine... I'm just wondering if I'm overlooking something because I haven't seen any exact details or illustrations which show this kind of hybrid approach on a new build that will have outie windows.
Thanks again. I appreciate your input.
Ben
Ben,
Q. "Is its OK to use a membrane applied to the plywood roof deck as the WRB on the roof?"
A. There is no such thing as a WRB on a roof. Your roof assembly needs an air barrier -- and that might be the peel-and-stick, if you want to use it -- and it needs roofing underlayment (which is required by code). The roofing underlayment is usually a different material from the air barrier, but these two requirements are sometimes fulfilled with a single material (like a peel-and-stick membrane or synthetic roofing underlayment with taped seams).
Q. "Is it OK to use a membrane applied to the plywood roof deck ... (_under_ the horizontal foam), but then have it lap _over_ the outer surface of the vertical foam which would serve as the wall WRB, thus not needing any Tyvek type product?"
A. Yes.
Q. "AND then being able to flash the outie windows using Joe L's guidelines which assume the foam is the WRB?"
A. Yes. More information here: "Using Rigid Foam As a Water-Resistive Barrier."
Thanks again. Your many articles and consistent replies to reader questions are so helpful.
In the case of the last example mentioned (Lstiburek's dimpled housewrap between OSB and exterior foam), how should the housewrap be detailed as it nears the ground? In my case this situation applies where my OSB sheathing meets my sill on grade. I am using Obdyke Hydroflash LA to liquid flash the base of the OSB sheathing to the foundation joint. I'll be using bumpy Obdyke Hydrogap wrap (not the adhesive backed). Shall I integrate the wrap into the liquid applied base flashing? I am planning to liquid flash the wrap to the side of the extended 2x buck I've made for my outie window placement. My initial though is to leave the wrap loose as typical (not affixed in any way at the base) However, since there shouldn't be any bulk water in there (between the OSB and wrap), it also doesn't seem too risky to integrate it. Perhaps the main risk is splash off the ground in heavy rain, or snow piling up against the house. So maybe I've answered my question (leaving it loose at the bottom), but I'd still appreciate any feedback on this detail.
Aaron,
Can you explain what you mean by this sentence: "In my case this situation applies where my OSB sheathing meets my sill on grade." If you are talking about your pressure-treated mudsill, my first question is, "Is that pressure-treated mudsill really at the same level as grade?"
Ideally, you want there to be at least 8 vertical inches -- more is better -- between grade and the first wooden components of your house.
Martin, yes, I have proper grading (or will have - see explanation below) as you mention and the pressure treated sill is 8" above it on the slab-on-grade foundation. This actually brings up a previous problem in that this wasn't the case - the grading was against the framing (when I bought the house). So now I'm in the process of digging out, adding 2" of xps against the foundation going 2' down and then 2' out as a "frost wing/in-ground eave" (https://www.greenbuildingadvisor.com/article/an-underground-roof)and then will backfill and grade appropriately. I will install 2" of polyiso to meet the xps, above grade of course. Initially, I had planned to install the housewrap over the top of the foam since I'm installing windows in the outie method with 2x extensions. But because I'm using OSB sheathing I was concerned after reading Lstiburek's "Mind the Gap" article. I am in a very dry climate (Wyoming) so the assembly should be drying to the inside (r-23 mineral wool) easily. However, the last component that may complicate this is that I'm adding structural 7/16 OSB over pre-existing 3/8 painted t1-11 OSB for shear strength. My concern is that this might interfere with drying to the inside, therefore demanding the bumpy housewrap between the OSB and polyiso. So my concern now is trapping moisture in the outer layer of OSB should I put the foam directly against it. Other than ripping off the 3/8 t1-11 and completely starting from scratch with the sheathing, the bumpy housewrap seems to fit the bill. I am following the external insulation method as detailed here: https://basc.pnnl.gov/resource-guides/exterior-insulation-existing-foundation-walls. So my question really is "where does the bottom of the housewrap go?' specifically as it pertains to integrating above-grade with below-grade outsulation.
Process photo showing structural OSB added to pre-existing non-stamped 3/8" t1-11 OSB. The grading will be excavated in order to install xps and polyiso layers as detailed in the pnnl.gov resource. This window will be replaced and 2x buck extensions will be added to meet foam/furring profile.
Log in or become a member to post a comment.
Sign up Log in