CLT replaces a concrete slab

I’m soliciting input for a potential project in southern Arizona. The client has approached me about exorbitant costs related to concrete slabs. Although I specialize in SIPs and CLT, I’ve often considered the use of CLT in an “at grade” situation. I appreciate that this could not be considered as viable in most building areas due to ground water and rainfall. However, the desert of Arizona is certainly an area for consideration. I don’t have a firm detail. However, I can easily envision a thick aggregate base, flowable fill, membrane barriers, and edge protection that would warrant a good chance of delivering on long term durability. I have a US based CLT supplier ready to go and with their version of a carbon-sequestering wood slab. However, I thought this forum would be a good place to have a discussion about any historical use, successes and failures as well as possible details, roadblocks and theories related to this concept. I invite your comments as I wade into the process of developing a plan and associated details.
My base size building is 16 X 48. and the 3 ply CLTs are 8′ x 16′. Everything is on the table. If you have an opinion, I’d welcome it.
acobbÂ
WV
GBA Detail Library
A collection of one thousand construction details organized by climate and house part
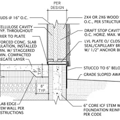
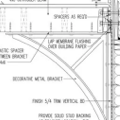
Replies
acobb,
I don't know much about CLTs. Is the main advantage of going that route over say sleepers and plywood, or two layers of plywood, that the CTL base could take the loads from above without needing stem-walls or pads?
The stiffness of a CLT system is such that it can span in all directions and a level site could afford the opportunity to lay a 4" slab of wood that requires no stem wall or other support. The biggest hurdle is moisture vs. wood.
In the size described above, I would allocate about one hour to lay and connect that sized CLT floor. Hence it's very fast and allows you to start with wood as opposed to concrete.
To me it sounds very promising.
Have you considered this type of system: https://www.greenbuildingadvisor.com/article/minimizing-concrete-in-a-slab-on-grade-home? In the comments, Josh Salinger shared a concept using CLT but he now uses a system more similar to the one in the article: https://www.greenbuildingadvisor.com/article/the-concrete-free-floating-plywood-slab-assembly.
I'm familiar with these types of systems and have used floating floors many times. Currently installing 23K SF of this system in Virginia. However, it's over a concrete pedestal pour with parking underneath. The project is a passive Haus build and I replaced the specified SIP floor with a foam and layered OSB floor for substantially less.
The CLT proposed slab would / could eliminate the perimeter stem wall as it really isn't needed from an engineering perspective as long as we stay single story.
Ah, thanks for the additional info. I think it could work; the key would be to keep the CLT dry, or else it will warp. Easier in a desert than in a wet environment but I'd still want redundancy in the waterproofing: a capillary break (crushed stone or expanded glass aggregate), a bulletproof polyethylene vapor retarder (15-20 mils) and coat the bottom of the CLT with whatever finish you're using on top.
For code compliance, you'll probably need something around the perimeter; as far as I know, the only truly "floating" slabs allowed in the IRC are for unconditioned buildings under 600 sf. What do your local codes say about foundation depth?
Could horizontal CLTs be supported just above ground level by helical screws aka technoposts?
stoltzberg,
Those low spaces under houses are always trouble.
- Inaccessible for repairs or maintenance, but not for pests and debris.
- You need more insulation under the CLT, but also because of the gap, it needs to be protected by cladding.
- Plumbing and waste lines, which if the CLT were on the ground could be buried, now somehow have to be protected.
Malcolm, I agree that narrow spaces are a problem as any builder who's had to squeeze into a narrow crawl space knows.
All your points are spot on.
Having used helical piles, I know the cost and the benefits. I don't see them as an option in this discussion. The idea is simply to replace the specified concrete slab with a CLT wood slab and how to detail it for best possible durability. Can it be done? Has it been done?
"Has it been done?" I'm hoping that's where you come in... A good test would be a small accessory building.
The devil is in the details. It's the perimeter I'd be interested to see sections through.
So I'm trying to figure this through, I'm basically thinking out loud here.
The CLT is a slab of wood, 16'x8'x4". One alternative would be a pre-cast slab of concrete of the same dimensions. The CLT:
* weighs about 40% as much
* is a nicer surface for attaching other pieces of wood to.
The concrete slab:
* won't rot, shrink or warp
* Is heavy enough to provide uplift protection
* Is probably quite a bit cheaper
* Produces significant greenhouse gases in its production
Am I missing anything?
Another alternative would be a 12" thick panel made from I-joists and OSB, or similar. The CLT is:
* Self-supporting on gravel
The joist panel:
* Has room for mechanicals
* Has room for insulation
* Requires some sort of foundation
* Is probably cheaper
Note that both competing panels could be easily fabricated on site.
I think the CLT could be used with a stem wall perimeter foundation. The engineered thickness of the CLT can span 16 ft easy with no support beam in the center. This leaves an 18" crawl space under the house with no obstructing beams. The stem walls would then carry the wall & roof loads. This seems to be the easiest way to make it fit the current code without experimental construction.
Tim