Mineral wool as insulation, outsulation, drainboard, rainscreen?

Hello,
I am building a multi use, residential, building.
It will be built into the side of a hill, with a south exposure walk out basement.
A main floor with 12′ walls, and a stick framed roof to provide for a second floor in the future.
It may eventually become a living quarters, but for now, is just a shop with no loft.
It is located in south central Ontario, I believe is climate zone 5 or 6.
We have cold winters, and humid summers.
The building will be heated in winter, and air conditioned in summer.
There will be a full basement. The main floor will be constructed of poured concrete on steel pan.
Both the basement, and main floor will each have in floor hydronic heating.
The walls are to be 2×6, the rafters will be stick framed 2×12.
The foundation is poured.
The roof will be steel sheet, and the siding reverse board and batten.
As the building will not be used on a daily basis, but I will need to keep it from freezing in the winter, I will have heat on all season. Cooling would only be done if the building is eventually used for habitation. But I would like to plan for that to happen, just encase it does….
Heat will come from hot water solar panels, and the rest of the south face of the roof will be covered with solar voltaic panels. I am hoping that I can insulate the building sufficiently to not have to use oil as backup heat.
I have been reading on here for a couple years now, about apples and turds, mineral wool in the attic, and many other very informative articles on building theories and designs, trussed walls, persist and remote, and eifs… However, for as many pros to each, there are just as many cons, and some very dedicated followers of each.
Perhaps I have my own biases now, but would like to stick to a few principles I think I have correct for my building climate zone, and intended use.
a. Insulation works better on the outside. Outside of the foundation wall, wall studs, and rafters. But it just makes sence to insulate those cavities, its cheap, and easy. SO both the cavity should be filled, and the exterior side of the wall covered with insulation as a thermal break.
b. Vapour barrier needs to be on the inside of the insulation. That may be on the out side of the studs if they are not filled with insulation. Although more difficult to do correctly considering all the penetrations such as electrical boxes, plumbing, lighting, etc. A vapour barrier just behind gypsum drywall is doable, and is code…
c. Roofs should be cold and ventilated. Using steel, or shingles, the roofing material should be kept cool with soffit to ridge ventilation.
SO, if I have these correct, here is what I would like to do.
Foundation:
– Coat with water resistant barrier, paint on or stick on.
– 2″ of Roxul drainboard = R8.6 from footing up to top of Main floor sill plate. Approx 24″ above grade..
– cement board fastened to 2×10 pressure treated sill plate to protect roxul drainboard from grade to siding, eventually covered with veneer stone, or stucco.. 2×10 sill plate will overhang foundation wall by 3″. The 2×6 wall will sit flush with inside edge of sill plate.Flashing put on top of 3″ overhanging sill plate will stick out far enough to cover top of veneer stone as well.
Main Walls: From Inside to out.
– 1/2″ gypsum drywall
– 6 mil Poly vapour barrier
– 2×6 stud wall with R-22 mineral wool batt insulation between studs
– 2″ of drainboard, or cavityrock mineral wool board insulation on exterior side of stud wall.
– Tar paper or Tyvek
– 2×4 horizontal strapping screwed through Roxul into studs.
– 1″ thick pine board reverse board and batten would equal 2″ thick siding attached to strapping.
Roof:
– 1/2″ gypsum drywall
– 6 mil poly
– 2×12 rafters on 16″ center (22′ length) with R-44 mineral wool batt insulation between rafters
– 1″ R-4 mineral wool board on top of rafters, or on bottom of rafters
– 2×4 horizontal strapping
– high rib steel. or standing seam steel roof.
That is my proposal.
My questions are:
1. Are there any flaws with this proposal as far as where the vapour barrier is? I was worried about summer time cooling, and getting condensation on the insulation side of the 6mil poly?
2. Is the extra 1″ of insulation required or useful on top or on bottom of the roof rafters?
3. Is there enough air flow under a high rib steel roof, or between the top of the 2×12 filled with 11″ of insulation and the 2×4 strapping for adequate soffit to ridge ventilation?
4. My main wall assembly has an overhang, past the foundation, of 4.5″ to the outside of the battens, the board would add another 1″ thickness to the wall. That would make it possible to increase the foundation insulation thickness to 3″ R12.9 and you would only see the sill flashing between the boards, in the reverse board and batten siding. Would it be worth it, to add another layer of drainboard to the foundation? My cost for that is only about $1000 more for the extra inch.
5. Is it possible to put 2×4 strapping over mineral wool board insulation that is 2″ thick, and still attach reverse board and batten siding to the studs safely?
6. The major problem is the sill plate has no thermal break, or insulation. I do not know how to insulate that area, and still provide a good attachment point for the cement board.
Sorry for the long post, but wanted to make sure I posted all the details.
I am digging the hole for the foundation the first week of June, so I need to figure this out soon.
As you can see, I do not want to use foam, anywhere I dont have to. I may use some spray foam under the sill flashing to fill the void it would leave so water drains away from the wall, but dont see needing it anywhere else.
By not using any foam, I have a vapour open assembly everywhere to the exterior. That I think should make the summer time cooling ok if some condensation happens on the insulation side of the poly vapour barrier.
What do you think?
Thanks for any advise.
GBA Detail Library
A collection of one thousand construction details organized by climate and house part
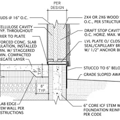
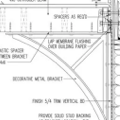
Replies
I'm doing a big job now where we used Drainboard. It's expensive and not much fun to work with. And it's actually 2-3/8" thick. We covered it with PT ply, which got covered with cedar 1x. We just buried the bottom, assuming the dirt will hold it in place well enough.
Not sure I understand entirely, but the 2x10 sounds like a thermal bridge.
Does your code actually say "vapor barrier" as w/ 6 mil poly, or does it say "vapor retarder of 1 perm or less", and people commonly use poly for that purpose?
Mr. Kolbert, I was unable to find a supplier that could get me the thicker Drainboard. The only product I could find, and need to order, was the 1" thick material in 4x6 sheets, about $10 each. I need about 60 sheets to cover my foundation, not a big barn really... I did not even think about using PT plywood. I have read that they actually use that for below grade insulated panels, as a foundation wall, so why not, It should last quite a while, especially if protected.
What are you covering the plywood with?
Yes the 2x10 is a big thermal bridge, I am not sure how else to deal with that transition. But that is the only bridge to deal with really. i was thinking I could use a 2x8 sill, and just put a 2" wide strip of 1.5" thick foam under the inner half of the 2x6 wall that would be overhanging the narrower sill plate... Hard to vision with words, i will work on posting a drawing tomorrow..
As for the Code Mr. Klingel, Our code has a section for Air Barriers OBC 9.25.3 and for Vapour Barriers OBC 9.25.4, and Vapour Barriers Used as Air Barriers.OBC 9.25.3.4
Here is a condensed version of what our says:
The MAXIMUM allowable vapor permeance of a wall assembly in Canada is noted as 60 ng/Pa.s.m2 (nanograms per Pascal second meter squared) almost identical to the requirement of the US Code.
The code also requires a Barrier to Air Leakage: to provide continuous barrier to air leakage from: a.) interior of the building into the wall, and b.) from the exterior inward, to prevent condensation in the wall space in the heating and cooling season respectively.
The code allows for Poly, only if it is made for use as a vapour barrier, and also allows the use of membrane type vapour barrier material, and also gypsum coatings, as long as they were made to be used a vapour retarders..
The code also says the barriers be installed sufficiently close to the warm side of insulation to prevent condensation, and will be used in all insulated walls, ceilings and floors.
Thanks for the questions..
For exterior insulation you should be using Roxul's RockBoard. On their site you will find it under Commercial. You should probably use the densest of their offerings since your siding will be heavy.
Put your building paper, or tyvek against your sheathing, the RockBoard on top of that. It will be fine. It sheds water, it does not need the building paper or tyvek air barrier over it. Plus you'll have no good way to fasten those sheets over insulation.
You should be calling Roxul for the same advice above - would be the best place to start before soliciting opinions here actually.
I would use Certainteed's Membrane vapor retarder in place of a straight barrier if you will be airconditioning and you have humid summers to boot. If you don't know what that is read up on it - its an adaptable membrane that will raise its permeability if moisture condenses on it during the summer vapor profile.
And you should consider an interior wiring chase to avoid putting holes in the membrane.
Here is my wall sketch.
The Roxul Rockboard has the same, 8lbs/ft3 density as the drainboard, and the drainboard is 2 tenths higher in R value per inch.. I have compared most of the Roxul board insulation products, and the drainboard seams to be the best of them all if you compare the same 1" thicknesses.
Comparing the products compressive ability is difficult, as Roxul states those numbers in two different forms.
Drainboard is listed at Compressive Resistance: ≥1.5” at 10% deformation 17 kPa (355 lbs/ft2)
RockBoard 80 is listed at Compressive Strength: At 10%: 743 psf (35.6 kPa)
I dont know how determine which of those is harder, they both have the same 8lb density...
I also do not know the price of the Rockboard.
I was in contact with a Roxul Sales Rep, last year. He advised me that the drain board was suitable for what I am proposing, and that he had actually used it on his own house in a similar fashion. However, he only used one 1" layer, and his siding was vynal. He gave me a list of local distributors, but none of them could, or would get me a price or order the products for me.
I will see if I can source locally the MemBrain type of Vapour barrier.
It sounds very worth it, if it actually does what they claim.. Smart plastic? Really? I guess I would like to know if anyone has done independent testing of the product, before I rely on it. The extra cost is not the concern, but if it does not perform as it claims, you could end up with a big mouldy problem.
I agree the problem with the interior vapour barrier is all the penetrations. I am considering doing the electrical in EMT steel conduit on the interior side of the finished wall. I may use a sheet steel in place of drywall as well. It will give it an industrial looking style.
It is a barn/ shop after all, for now at least.
I did a google sketch of the wall.
I will try to post it here.
Thanks again for the advice.
Some properties of the DrainBoard and the RockBoard may be the same, but they are manufactured for a different purpose. The thicker RockBoard is a dual-density configuration with a denser batt on the surface to resist local crushing from fasteners, and your battens.
Your configuration is similar to my USA New Wall - http://blog.lamidesign.com/search/label/USA%20New%20Wall
With all the effort you are going to for the walls you should be placing at least 4-8" of foam under the entire slab.
R Hunt,
Your response to John Klingel's question confirms my understanding -- namely that your code does not require an interior vapor barrier. Instead, the code requires an interior vapor retarder -- big difference.
I would skip the poly, and instead use vapor retarder paint on the gypsum wallboard.
I wish I could agree Martin, but relying on your painted GWB for a vapor retarder still means it will be full of holes for electrical devices. I don't see that wall having a tight air-barrier in that config.
Note he is not showing sheathing on his wall system. I'm not sure if that is an omission, or his plan to build a strapped wall rather than a sheathed wall. But without a solid back up to mount tyvek over I don't think the tyvek will create a reliable air-barrier. He also mentions the option of using building paper which is definitely not a tight air-barrier. So his vapor retarder in this configuration needs to also be his air-barrier if the house is to be tight. I don't think you can achieve that with drywall punctured by electrical devices, and it will be prone to letting moist interior air into the wall cavity in winter. Furthermore if the air-barrier will not be the tyvek on the outside of the wall cavity insulation, then for the summer vapor profile its even more important that he has something that will allow drying to the inside during summer - because the wall will be more open to the exterior and more likely to allow moist summer air into the cavity where it can condense. I think the variable permeability plastic retarder is the best solution here because it will move to permeability levels higher than a paint retarder.
I'm sure there must be other manufacturers of material like the Membrane besides Certainteed. In fact I doubt they make this - likely they are distributing a european product in north america.
Gregory,
I never said that R Hunt should omit an air barrier!
Of course every house needs an air barrier, and there is no need whatsoever to use polyethylene as an air barrier. Many people create tight air barriers using the Airtight Drywall Approach, which requires the use of airtight electrical boxes.
If you want to learn more about the difference between an air barrier and a vapor retarder, see:
Vapor Retarders and Vapor Barriers
Air Barrier or Vapor Barrier? - Building Science Podcast
Forget Vapor Diffusion — Stop the Air Leaks!
Questions and Answers About Air Barriers
Airtight Drywall
Martin - I know the difference. I was simply reacting to your comment above which did not include advice about Airtight Drywall Approach, nor airtight electrical boxes. It read as a suggestion to use a coat of vapor retarder paint, which would leave that wall without an air-barrier.
Again, I'm saying if his wall does not establish an tight air barrier at the exterior, which it does not seem to by his description, then his vapor retarder should be serving also as his air barrier. And I'm saying that this configuration leaves him vulnerable to summer vapor profile condensation, in which case a variable permeability membrane is better than vapor retarder paint (and air tight drywall).
I never suggested poly. You've mis-read my posts.
Gregory,
I'm sorry for mis-reading your recommendations; I see that you recommend something like MemBrain rather than poly. You're right that MemBrain would work.
But I still disagree with your statement, "So his vapor retarder in this configuration needs to also be his air-barrier if the house is to be tight."
You are right - you can still have two separate elements for the two functions, but even you are not suggesting that. Unless you want to consider airtight drywall with vapor retarder paint two separate elements.
Gregory,
We're going around in circles a bit here; I'm not sure why. When I suggested a vapor-retarder paint, you challenged my recommendation: "Relying on your painted GWB for a vapor retarder still means it will be full of holes for electrical devices. I don't see that wall having a tight air-barrier in that config."
Anyway, addressing air leakage at electrical boxes should be routine for all energy-conscious builders; it is certainly routine for anyone using the Airtight Drywall Approach. Moreover, good air-leakage detailing is also necessary if someone follows your recommendation to use MemBrain as the air barrier.
So, we're both right. It's possible to create an air barrier at the interior, using either MemBrain or drywall. In either case, remember to address air leaks at electrical outlets.
I never suggested ignoring air leaks. So I hope we can agree that either approach works, and we both believe in airtightness.
Martin, I don't think we disagree on something fundamental as air-tightness. I just don't think that in the context of this poster's question we can assume we are speaking with an "energy-conscious builder" or somebody for whom the Airtight Drywall Approach is routine. I'm not challenging you - just responding to your post at face value.
We are not going in circles - I just disagree with your advice. I feel that with the exterior of the proposed wall being not so tight, that the summer vapor profile could result in condensation in the cavity. And with a strategy that relies on Airtight Drywall Approach that condensation might be against the bare paper on the back of the drywall. So, no, I don't think that is a good way to go here unless there is a decent air barrier at the outside of the wall.
Thanks for the info guys.
Re. Drainboard VS Cavity Rock Dual Density.. The Drainboard has a density of 8. All other mineral wool products have a lower density, the dual density product is 6 on one side, and 4 on the other.
Even tho they market one product for one purpose, the specs indicate that the higher density material is better suited for my application.
Not trying to be argumentative, It just looks like the Drainboard is the most dense product.
I will try to contact another Roxul Rep, and get the skinny from the horses mouth.
They are reluctant to give out info if asked what should I use.... I need to ask them technical questions, like which product would perform best if compressed. They can not tell me to use a product in my application, because it has not be tested to death and approved by the legal depart to do so. But thats just my Opinion.
It think they have a great product, that should be better utilized, in place of foam
I am the builder. This is not my profession, but it is not my first time either.
I would like to think I am an Energy-conscious home owner. Nobody wants High utility bills. I have spent the last ten years, renovating a 100 year old double brick home. I know first hand, that sealing up and insulating your building is much cheaper, than paying the gas bill every month.......
I was aware that you can use airtight Drywall construction methods for a vapor barrier. I think I am capable of constructing that as well. As I am the builder, and I do not have to move into this building any time. I am not in a hurry, so I can make time to do things right, as long as I know how.. Thats why I posted on here, I want to do RIGHT... the first time.
I just do not like foam, so I do not want to use it if I do not have to, and I am willing to pay a bit more for that option. Just not twice as much....
I am also concerned about the summer vapor profile. However, my AC only runs one or two hours a day, once or twice a week in July and august. I mostly use my AC as a de-humidifier. That being said, even tho it is only used a few times a year, by me, the next guy might like to live in fridge all summer.. I am not planning on moving anytime, but I am building this structure for the next generation as well as my kids...
I think we all agree that a Vapor barrier should be on the inside of the wall, be it MemBrain, or drywall paint with appropriate electrical boxes ect.
If I can source a smart vapor barrier, I will use it on the inside of my studs, however, I do not want vapor condensing on the outer side of the MemBrain if I use that product, during the cooling season, as short as it is.
But with a "not so tight" exterior wall that I am proposing, wont any condensation that does form on the membrain be able to dry to the outside?
Do you think my wall assembly is not air tight enough without the exterior sheeting?
Would a layer of tar paper in place of exterior wall sheeting do the same job as plywood (air barrier wise), or create problems?
All electrical will be done in EMT so its on the inside of the wall covering.
Thanks again for the thoughts,
Also, Gregory, you mentioned 4-8" of foam under my basement floor.
That may be a topic for another post, but I was thinking that because I am using solar panels to heat the water that will heat the basement and main floor, would I not be better to have the soil beneath the floor work with the concrete as a heat sink, that gets hot during the sunny day, and releases the heat over the night? I am well above the water table, so I dont have to worry about water scavenging my heat away.. I certainly am not adverse to using foam in that area, as there really is not another viable option...
R Hunt,
I suggest you read some of the articles I linked to in my response of 05/31/2011 at 09:58.
I disagree with your statement: "I think we all agree that a vapor barrier should be on the inside of the wall, be it MemBrain, or drywall paint with appropriate electrical boxes etc." No, you don't want a vapor barrier -- you want a vapor retarder.
You asked, "Would a layer of tar paper in place of exterior wall sheeting do the same job as plywood (air barrier wise)?"
The answer is No. Asphalt felt (tar paper) cannot be used as an air barrier.
Gregory,
You wrote, "And with a strategy that relies on Airtight Drywall Approach that condensation might be against the bare paper on the back of the drywall." I disagree.
If you don't include poly in your wall, it's impossible for solar-driven exterior moisture to condense on the back of the drywall. Drywall is vapor permeable; the paper facing on drywall is VERY vapor permeable. What happens is that the drywall absorbs moisture and the drywall dries to the interior. Since this occurs during the air conditioning season, the interior of the house is dryer than the exterior, and drying to the interior works well.
No poly, no condensation.
R Hunt - I think you will find the density of the Rockboard is sufficient for your application. Using the denser drainboard will only cost more for no more insulation value. Also applying one 2" layer of RockBoard will take less labor than 2 layers of 1". Also note that I don't believe the 2" RockBoard comes in the dual density configuration.
Martin, I don't know why you expect the wall cavity to dry to the inside when you've proposed to place a vapor retarder paint on the drywall. No matter how permeable the drywall is the vapor retarder paint will limit the transpiration - that is why it is there after all.
We understand that some drying will occur through the vapor retarder, but in the configuration of this wall the rate of drying to the interior is much lower than the rate that new moisture will enter the wall cavity from the exterior. The permeability of the exterior layers - especially since there is no OSB - is much higher than the GWB+vapor retarder paint. Any moisture that condenses in this wall will not dry out because it will be replaced by more moisture from the exterior faster than the drying rate. This does not happen only with "poly" - a polyester vapor barrier is just an extreme of the imbalance.
In order for a wall to dry the way you describe the permeability of the interior side of the cavity has to be equal, or at least close to the exterior side. OSB could help since its permeability is not that high, but here we are talking about building paper, or tyvek with out the back up of sheathing, so compounding the fact that the drying rate is slower than the "wetting" rate, we have the possibility of outside air driven into the wall by pressure differential because there is no tight barrier at the exterior.
This is just not a wall for a drywall solution.
Gregory,
Sorry, but I stand by my earlier post. There will be no condensation. It is technically impossible -- the gypsum wallboard is hygroscopic.
And yes -- the wallboard will dry to the interior, in spite of the paint. Vapor retarder paint is not a vapor barrier -- that's why I recommend its use.
Martin, I'm not saying it will condense in the drywall. If you ran a vapor profile of the wall the dew point will be inside the insulation, very close to the drywall, not in the GWB. If condensation occurs it will be in the insulation close to the GWB and wetting is likely to occur at the paper surface, the most vulnerable item to mold growth in the wall.
Your paint on retarder will be about around .5 perm. Your building paper and tyvek are going to be 10x that and more plus outside air driven in under pressure. As fast as moisture can dry to the interior it will be replaced by more moisture from the outside, no matter what you recommend and what you stand by.
R Hunts wall as he has listed it would be fine for cold climate, no air-conditioning. Cooling thrown in, he should use something like Membrane. Drywall based vapor retarder in this case is bad advice.
Gregory,
Sorry, I stand by my statement. Condensation will not occur in the fiberglass batt -- that is a rare phenomenon indeed, almost never seen -- nor at the back of the drywall, for the reasons I have stated. What happens is the wallboard absorbs moisture, which dries to the interior.
Martin, and when the drywall is saturated and will absorb no more, and will not dry faster than moisture that is present, then where does the moisture go? I understand the principles you are standing on, and for a tighter wall it would suffice. For a wall that is so much more open to the outside than the inside it will not behave as you expect. You really have not spoken to the specifics of the proposed wall.
Greg, drywall doesn't "saturate" with atmospheric conditions. Have you ever seen saturated drywall in your area?
At some level, you have to not overthink the analysis and look around you. There are thousand upon thousands of houses built throughout the mid-Atlantic region for decades with housewrap, plywood exterior sheathing (or even spaced boards, more vapor open!), fiberglass and drywall (no poly), and they just aren't dissolving into goo.
Add a layer of poly and you've got a big risk of a mold infested disaster once you turn on the air conditioning, but the wall you're claiming is a high risk wall is out there in multitudes and surviving just fine.
No Jesse, that is not the wall we are discussing here.
Granted the multitude of the installed base includes a kraft paper based vapor retarder, and although most of it is poorly installed it does provide some level of vapor retarder. But even if it did not work at all, and the drywall was exposed, the exterior has a layer of OSB with a perm rating in the range of a vapor retarder, and a layer of housewrap which even when poorly installed does provide some degree of air sealing.
The wall in question here has no OSB, is proposed with building paper, or housewrap installed without a sheathing layer below (which I believe will not be a tight installation.) There is no air sealing at the exterior here which means ambient air can get into the wall, and there is no low perm OSB sheathing. R Hunt explains it is going into a humid summer climate, with air conditioning. These are flags raised. If you change any of those factors the situation greatly improves. Use OSB. You're fine. Get a good air barrier at the exterior. Big help. Not a humid climate. Great. Don't have air conditioning. Perfect.
But as it is its physically impossible for the GWB with vapor retarder paint to dry the wall cavity faster than new moisture can enter this particular wall. The end result is the same as having poly - it may take a bit longer but its a race that the drywall will eventually lose. That is not over-thinking. These are basic principles.
So what are we discussing here? Is this a barn or a house?
Is there sheathing on this building or not? What keeps it from falling over if no sheathing?
R. Hunt
Last year, like you, I considered using Roxul DrainBoard and other products as external insulation. I asked Roxul some technical questions and received a prompt response from Iain Stuart, the Technical Solutions Coordinator. The company office number is (800) 265-6878
One of the sales reps is Susan Martin. Her Cell phone is 905-467-5224.
You might also try contacting Roxul Customer Service at [email protected] or 1-800-265-6878.
You mentioned you are located in South Central Ontario. Have you considered using Durisol Blocks for your foundation? These ICF blocks are made of recycled wood chips and contain Roxul insulation inserts. There is more insulation outside the concrete than on the inside, so the wall would perform better than most ICFs. If you wanted to add Roxul Drainboard to beef up the R value, you could screw directly into the Durisol block to anchor the insulation. Durisol Inc. is based in Hamilton, so they may not be far from you. I believe the name of their Technical Rep is Vipur Achuria.
You have asked about sheathing in the wall. I agree with the experts who suggested adding sheathing for structural strength. You could try plywood or Densglass. The latter is more permeable.
I'm not an expert, but my research reveals it is better to conserve heat by installing insulation below the slab. This is more energy efficient than using the soil as a heat sink. However, if you install an insulated sand box with radiant piping, similar to Thorsten Chlupp's SunRise house, this would be an effective plan. Good luck.
-Jim
R. Hunt,
In your roof configuration, you should install an air barrier such as Typar or Tyvek below the steel roof. Condensation can form on the underside of the steel. The air barrier will drain any moisture to the eaves. This prevents the insulation from getting damp.
Your horizontal strapping could act as a dam in this drainage plan. If you shimmed the strapping a tiny bit, the moisture would drain more freely.
- Jim
Jesse. This is a barn/shop for now.. It may one day become a house... Never the less.. I am putting extra money into it, as I will need to keep its contents from freezing. There will be wood working equipment in the basement, and lumber and equipment storage in the upstairs, as well as a couple vehicles... Thats why I have a concrete main floor thats 12" thick.
I want to heat with hydronic in floor heat, with hot water solar panels, and passive solar. So a well insulated building is a must.
I can put sheeting on the wall, if thats the way to do it. The Engineer says its not required, because I am strapping it with 2x4 for the reverse board and batten. BUT,, if it serves a double purpose, I will put it in.
Poly here can mean two things Polyester is the exterior Tyvek wrap, but is Polyethylene, and is a "Barrier". When I use the term poly, here that usually means vapor barrier.
Gregory's post #27 I think is bang on...
As stated before, I am required to have a retarder, and Membrain is accepted by our building code. Here is our Government report on Membrain, has some good installation drawings as well. http://www.certainteed.com/resources/MemBrain_13278_e.pdf
And as my building inspector will probably require a film a something, poly, plastic, membrain or paint, on the interior side of my wall, I will likely go with the membrain product. IF I can find it, the suppliers here dont seam to be carring it
However: I do not agree that water or water vapor will be continuously driven into my "open wall" due to a lack of Weather Resistant Barrier on the outside, as OSB sheeting would provide... The wall cavity will be air sealed, with the vapor retarder on the inside. That will make my wall a pressure equalized or vented rain screen, kinda... If the air pressure outside is higher than inside, there will be air movement into the building. AND there will be moisture laden air movement into the wall assembly, thereby saturating the wall cavity with moisture vapor, but only until the pressure is equalized. The moisture that does get in as far as the interior vapor retarder, be it poly, or painted GWB, will certainly condense on that product during the summer cooling season if the temp at the retarder, is at the dew point.
I dont think with that much insulation, the dew point will rarely be that far in my wall. Am I wrong?
My summer temps, are rarely over 87F but the humidity is generally high, 60% or more.
There will always be cracks and holes in every building, that is impossible to completely account for, even with the most meticulous builder. So, that is why I think an "open wall" is a better choice than one with a foam vapor barrier on the outside, and a plastic, or paint barrier on the inside.
The use of Tyvek, and other house wraps was intended to block the passage of bulk water, driven by capillary or wind, or hygroscopic pressure, into the wall given the poor design and installation of some sidings. Felt or tar paper was used before we had the plastic stuff... But was for the same purpose.
I have replaced that layer with an insulating WRB roxul board insulation.
Martin, if I may quote you from another forum " Like MemBrain, asphalt felt is a "smart vapor retarder" -- cheaper, too."
I think my climate is much like northern Vermont, we both get lake effect moisture.
Did you mean to say, asphalt felt, could be used in place of the poly, or membrain and placed on the inside of the wall, just before GWB?
Jim. Thanks for the advice.... I will call the Roxul reps you listed. I am very near the Roxul Plant in Milton On. I went there and picked up a piece of Drain board, I am going to mock up a small wall, see how it is to screw through....
I can also get a relatively inexpensive foam board locally, it is the cut outs from insulated steel doors when people order one with a window. I will get that to put down under my basement slab.
Do you not think there will be sufficient air flow under the steel roof, to dry any condensation that may form? The steel roof should always be the same temp as the surrounding air, as there is no insulation directly in contact with it, and a free flow of air from the sill to the ridge... On a cold morning the sun shining on it will heat it up faster than the air, but that should create a convection current under the steel that will help dry it out... Just my thoughts on that?? If I was sheeting it, I would put on the peel and stick Ice a water shield the whole way up..
Thanks again to all for the discussion...
My excavator moves on site today.. :)
R Hunt,
No, I don't think it's a good idea to install asphalt felt on the interior of your building, under the drywall.
My advice remains unchanged: if your building inspector insists on a vapor retarder, either vapor-retarder paint or MemBrain will work.
Horizontal 2x4s installed for reverse board-and-batten siding will not provide any racking resistance. To brace your walls, plywood or OSB is a good idea. The exterior sheathing can also become your air barrier, if you tape the seams of the sheathing and detail the edges properly.
ALso,, I looked at the Durisol product, and there is even a house being built down by the bayfront in Hamilton using the blocks,, they do not look very good, IMO.. Dry stacked and filled with concrete, the insulation only fills a small portion of the wall. Also the quoted priceon them, was much more than what I am proposing...
I also got a price on Foam type ICF foundation, (altho I disagree with having the insulation on the inside of a heated foundation),, and the price was still more than having a local guy pour the foundation, and me add the roxul to the exterior later...
To All:
For those having trouble getting any customer service out of Roxul, another mfg. of rock wool batts and boards is "Thermafiber", out of Indiana. They make a 'Rain Barrier' board that has a silicone coating, adding to rock wool's inherent water resistant properties, and a 'Versa Board' that has higher density choices. With the green building market and those trying to move away from foam, one would think that Roxul would be more willing to cater to residential and not primarily commercial building.
Also, I've done some cost comparisons between 2" boards in $/SF/R10. XPS blue board: 1.03; Foil polyiso: 0.78; Thermafiber Rain Barrier: 0.84; Roxul Drain Board: 0.90. Local prices will likely vary some.
Michael,
Thanks for the reminder. For interested readers, here are some more links:
VersaBoard
RainBarrier
R Hunt
My brother has been a roofer for about 35 years. Much of my knowledge comes from his expertise. About ten years ago, when he did a steel roof , the client wanted to pay as little as possible. The customer insisted that the air barrrier be eliminated below the steel. A few months after the job was completed, the customer complained about moisture dripping into his attic. He felt the cause was a poor roof job. My brother went to the house and checked out everything. After some discussions, he realized that whenever there was condensation on the roof, there were leaks. Condensation formed on both the top and the bottom sides of the roof. Therefore, moisture dripped into the attic.
Air barrier is relatively cheap and it provides good insurance. Experience has taught me to put my faith in redundancy.
Jim
Michael, those prices seem to be in line with what I have in my area as well...
I spoke with the Tech guy from roxul today. He confirmed that all the board products would work for the above grade, exterior wall I am proposing, however it is not something they endorse as a system, for liability reasons....But he knows first hand of projects that used mineral wool board under strapping for siding.
The Drain board is the most dense product, and he said that it would perform equally well in my above grade wall compared to the other product lines they make..
However, they have very little call to manufacture drainboard thicker than 1". So any thicker will be very difficult to find. The other products are more widely used in thicker dimensions, and are more easily obtained, but still not on a consumer/home owner level.
The Problem is not with Roxul,, It is the distributors, and retailers, and the general building community.. I think in time, more consumers will educate themselves and request the "greener" building products be used, then the availability and price will improve.
I had one retailer tell me he wont carry roxul, as it wont compress enough, and he would have to allocate more storage space for stock compared to the pink......
Jim.,., Experience is king. I will incorporate a water barrier into my roof assembly.
The mineral wool board will shed the water, but only to the end of the panel, then the water would drain down into the rafter insulation.
Therefor, I will put on a layer of waterproof, vapor permeable barrier over the rafters, then add 1" of mineral wool, then my strapping.
Martin, your blog "Calculating the Global Warming Impact of Insulation" you mention the use of Mineral wool insulation under a concrete floor. Is there any further information on this?
Certainly I am not pushing the Roxul brand, here,, ThermaFiber looks to be a very similar product. I would use them, except I am within a hours drive of the Roxul Plant in Milton Ontario, so buying local makes the most sense, to me...
Thanks again to everyone for the great information...
I will try to gather all the info, and come up with a revised schedule, for my foam free wall... and post a summary.
R Hunt,
The use of mineral wool insulation under concrete slabs is still experimental. I would leave that detail to the labs and test homes for the time being.
so how are you going to install the roxul?
the thermafiber site has a doc on how they install the product to the sides of office and commercial buildings, and they all indicate a z ledge or other thermal bridge be used
the drainboard obviously can't fall off in the ground with all the dirt up against it.
not sure how you fasten thick dimension to a standard wood stud wall
I'll chime in on the mineral board supply.
I recently scoured Virginia and surrounding states for Roxul's Rockboard 80 product. I couldn't find anybody that stocked their rigid board products. I'm still waiting to hear back from one distributor as to whether or not they can special order for me. The prospects are not good.
Thermafiber's Versaboard 80 has very similar specs as Rockboard 80. I did find a Virginia distributor that was willing to supply this, but their minimum order quantity was 4,800 sq. ft. I was told that 4,800 sq. ft. was their minimum lot size at the manufacturing plant (meaning it would be produced "just in time" against my purchase order). Cost was ~ $0.80 / sq. ft. for their 2" thick unfaced product.
The Thermafiber rep. said that they "typically do not recommend their products for below grade applications." I found this interesting since the Roxul Drainboard is designed to be buried below grade, as an exterior foundation wall insulation . . .
Martin - If it's okay to use Drainboard against a foundation wall, do you see any problems using it below a crawlspace "rat slab" (one that is not structural in any sense, only 2" thick)?
Daniel,
Q. "If it's okay to use Drainboard against a foundation wall, do you see any problems using it below a crawlspace "rat slab" (one that is not structural in any sense, only 2" thick)?"
A. I might do that on my own house -- it seems like it should work. But I can't really recommend it, since:
(a) I've never done it, and
(b) I have no idea what the mineral wool will look like (or how thick it will be) after being compressed by concrete for 10 years.
Lots of builders experiment -- I've done things on my own house that I've never seen anyone recommend -- but if you are building for a client, I recommend using techniques that are tried and true.
R Hunt.
Your original question has inspired some excellent follow up. Will you blog about your build? If not, when your project is finished, could you post about the good, bad and ugly? What worked, what didn't, so we can learn from your lessons. Thanks Jim
R Hunt.
A couple of years ago, I found Jesse and Darcy Lackman's blog about their Energy Efficient house project. They posted a picture of their method of reducing the thermal bridging in the roof. They cut rigid board insulation into strips and attached the insulation to the rafters. Then they insulated the cavity with batt insulation. Cutting the rigid board into strips saved on their costs.
They didn't post any comments about this solution, but they did include a picture at this link. http://www.wrtc.com/rvsrchjl/house/jfoam.jpg
This method could be an energy efficient compromise for you. If you use a circular saw to cut the insulation, it would be wise to attach a vacuum to the saw. The tiny chips of insulation pick up a static charge which makes them cling to everything, including dogs and cats. If you cut the board outside, the wind blows the light pieces everywhere. The vacuum makes the clean up easier.
Jim
.
Hey, just wondering why you wouldn't use the entire sheet? just to save costs?
It certainly does take care of the thermal bridge..
I am not sure how to blog... but I will take pics along the way, and will post my results at least after the build. But likely sooner, as I am sure I will come across something I will need some advice on...
My hole is dug, just waiting for the concrete guy to do his magic.
R Hunt.
There are several reasons to take the time to cut the XPS into strips. As your question indicates, the first is cost. XPS costs quite a bit more than Roxul and even more than fiberglass or cellulose. The main benefit of the XPS would be to reduce the thermal bridging while supporting the roof deck.
As an example of the economic benefits of using the strips, assume the insulated area of one half of your the roof is 32 feet long and the insulated slope is 16 feet. That's 512 Square feet. If you used full size 2 ft by 8 ft sheets, you would need 32 pieces. In Eastern Ontario, 1.5 inch XPS is about $18.00 CDN per sheet. If you cut the insulation into 1.5 inch wide strips and allowed 1/8 inch for the saw kerf, you would get about 14.75 pieces per sheet. Assuming the rafters are 24 Inches OC, you would use about 2.3 sheets for the bridging strips on half the roof. This saves the cost of 29+ sheets of XPS. The roof would be cheaper to insulate.
In recent months, I've read many blogs and Q & As on the GBA. site. I've learned that, if a vapour barrier (retarder) is installed near the inside of the building envelope, the exterior planes of the building must be permeable to allow the wall (roof) to dry to the outside. XPS has a low permeability. I would be concerned about creating a double vapour barrier by adding full sheets. Using the strips of XPS provides insulation and drying ability.
A recent blog addressed the issue of the Global Warming Potential (GWP) of the blowing agents in XPS. Cutting the strips is a compromise. Good insulation, reduced GWP.
Like you, I'm learning. I hope this helps.
-Jim
Hello Jim. That does make a lot of sence.
I am meeting with a steel roof saleswoman this week, and will discuss these ideas.
I will post my process for sure..
In the meantime, i finished digging my hole today, Just waiting for the foundation contractor to do his magic,, Severe thunderstorms tonight and the rest of the week will likely postpone my wall for a week or two tho..
Hi R Hunt,
I'm planning on a very similar wall to yours only retrofitting to Roxul
I'd be interested on the design you settled on - especially the foundation details.