Shed roof framing options

So I came up with some cost estimates just for the framing members of a cathedral shed roof. If I could do it all over again I’d likely just go the gable attic with cellulose on the attic floor, but too late for that, so it goes.
Following prices do not include anything more then rafter material.
Framed in 2×12= ~$1000
14″ TJI= ~$2,100
18″ Parallel Chord Truss= ~5,000
With the 2×12 and TJI I’d have more cost and time into the rafter tail detail, but probably end up with a better look. At the same time the sistered on rafter tail would take up even more insulation space. With the economy of the 2×12 I could put the extra money into a layer of foam above the roof, and fill the rafter bays with fluff, this would give a very insulate roof. I do have some reservations about sealed roofs.
Parallel chord gives a nice depth for insulation and saves a little time on rafter tails. Price also includes lifting them up onto the roof. Pretty pricey though.
I am trying to attain an above code performing roof, but have limited funds. Having missed the simple approach of a well insulated, vented attic. What do you suppose is the best option?
Spray foam is not really an option as it is cost prohibitive, plus it’s pretty nasty.
Any comments/suggestions appreciated. Especially from builders who have built with the above options.
Thanks
GBA Detail Library
A collection of one thousand construction details organized by climate and house part
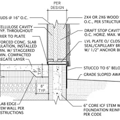
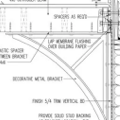
Replies
Joe,
Parallel chord trusses usually start to make sense then the spans are over twenty feet, or you want a cavity depth in the 2 foot range. An 18"deep truss will cost almost the same as one twice as deep, as from the manufacturer's perspective they involve comparable amounts of work and hardware, and not much more material.
If you're shooting for better than code, and you can afford 2x12 with fluff + enough rigid foam above the roof deck as appropriate for your climate zone, that's probably the best performing assembly.
If you can hit your R-value target in a vented assembly, then the TJI allows a little more space for venting and fluff than the 2x12 does. The flanges on the I-joist seem like good supports for your vent baffle.
The truss doesn't seem worth the upcharge unless vented fluff in the truss ends up being cheaper than 2x12 + foam for the same R-value.
Joe,
TIJ are easier to build with as they are much lighter especially when working overhead. Rafter tail details are about the same amount of work.
I'm surprised about the lumber cost, here TIJ is cheaper especially when talking about long spans. Might want to check with the lumber yard, you could be asking for a non standard series thus the extra cost.
With the I joist, you get a better performing roof as the joist web is thinner and you get much less thermal briding than with a 2x12.
If you are going with 2x12, the cheaper setup is to go with vented roof and add a layer of interior rigid insulation to get up to R49 and drywall over it. This is significantly less labor and material cost as you don't need such a thick layer of rigid foam plus you save the extra layer of sheathing. I've done a similar assembly, pretty straight forward to build just have to get extra long drywall screws.
I think the bottom line is, go with the assembly that your contractor is more comfortable building. The material cost difference is less of an issue.
I will be building it, with the help of other skilled carpenters.
Is the interior layer of foam not problematic? Why is this option not suggested more here on GBA?
I think the cost of 2x12 + foam is comparable to the truss package, surprisingly maybe less. The slope is lower, so maybe this could be a good option. For some reason I have reservations about unvented assembles. Everyone vents lower slope in my 4C coastal area, doesn't seem to be a problem like it is talked about here.
Thanks for all the feedback
Joe,
The interior foam option still needs to be vented. Vented low slope roofs generally work provided its not shotgunned with pot lights and you have a decent interior air barrier (either taped foam or drywall).
I think the reason it seems more problematic, is that only problems show up in forums, people with a vented low slope without issues won't be posting about it.
For foam, roofing polyiso is the cheapest around here, if you can get your hands on reclaimed stuff even better.
Important detail not to overlook is connecting the wall air barrier to the roof air barrier.
Martin seems adamant that venting anything 2/12 and under is not right. But there are many very reputable builders and architects who see it as a non issue in my area. A little confusing to say the least.
That said, for a cathedral ceiling, it's really hard to get anything better than code without foam unless you have a giant cavity to fill somehow, which gets expensive.
Even if you had 1 inch continuous foam on the underside of rafters seems like it would be a big performance boost. Where would the roof to wall air barrier be? Would this not be the sheetrock joint?
Joe,
You wrote, "Martin seems adamant that venting anything 2/12 and under is not right."
I never said that. A 2-in-12 roof is a low-slope roof. Just because it is a low-slope roof, doesn't mean that you can't insulate it. However, you can't use a conventional 1-inch high vent channel above fluffy insulation for this type of roof assembly, because the slope is too shallow for the requisite air flow. You either need a very generous height of air (a mini-attic) above the insulation, along with cupolas for ventilation, or you need an unvented solution.
For more information on several ways to insulate a low-slope roof, see "Insulating Low-Slope Residential Roofs."
You wrote, "There are many very reputable builders and architects who see it as a non-issue in my area." I'm not sure what "it" is, but your comment raises the question: Where is your area? In other words, what's your geographical location or climate zone?
A particularly dry part of climate 4C, northwest of Seattle
Joe,
An un-vented low slope with either spray foam or exterior rigid will always work.
Vented sometimes fails. Usually the problem is interior air leaks.
As I look around my neighborhood I see a lot of 100 year old flat roofs that are either edge vented, un-vented or the occasional mushroom vent. They do work until somebody puts them full of pot lights.
Typically the easiest wall air barrier is your exterior plywood/osb. You'll need to somehow bring this in and tie it into either your ceiling rigid foam or ceiling drywall.
Exterior sheathing to ceiling detail (you can also use wide flashing tape instead of the plywood piece):
https://s3.amazonaws.com/finehomebuilding.s3.tauntoncloud.com/app/uploads/2016/04/09112812/021242090-wall-to-roof-transition_xlg.jpg
Or if you want to go with air tight drywall on your walls (way more work and easy to mess up):
https://www.buildingscience.com/documents/information-sheets/air-barriers-airtight-drywall-approach
P.S. Getting your air barrier right is worth more in energy savings then extra insulation, don't skimp. Also don't go overboard, decent taping over all the plywood joints and window/door flanges is all you need.
Hi Joe -
There are always three potential driving forces for air flow: stack effect, wind, and fans or mechanically-driven air flow.
I am pretty sure that roof pitch makes a big difference in how stack effect-driven air flow gets expressed in vented roofs (I am actually testing this currently; see https://www.greenbuildingadvisor.com/article/wingnut-testing-soffit-ridge-roof-venting). And roof venting product manufacturers I have been talking to think that stack effect is a weak driver compared to wind.
If that is true, then air flow in vented roofs depends quite a bit on how windy it is at your site and the height of your roof off the ground, because wind speeds changes quite a bit with height.
In low slope roofs, it seems entirely possible that if you are ok with the energy penalty, you should be able to actively pull air through your roof assembly, but any flaws in the roof air barrier can mean that the resulting air flow introduces as much moisture as it was intended to solve.
While I am still working on proving this or at least better understanding roof venting, I think venting with less than a 3:12 pitch may be introducing less drying potential than it's worth.
Peter
Thanks Peter,
I have watched the demos, very interesting