Unvented roof – I know. So wrong, but…

I’m building a tiny house on wheels with a simple shed roof. I have 2×6 rafters and am insulating with two layers of 2″ XPS which are carefully fitted, spray foamed (foam in a can) around joints and edges, then, once the spray foam has been trimmed level with the XPS, sealed with R-Guard Air Dam. Each of the two layers are treated like this, and the joints are offset. A third 1″ XPS layer is added and treated the same way, and a final 1″ XPS layer is then fitted to cover the ceiling crosswise to the rafters and routered out for the portion of the rafters which protrude from the nominally 5″ thick XPS sandwich. Thus, when seen from below, the insulated ceiling shows no rafters, only the blue of the final layer, with joints again sealed with R-Guard Air Dam.
Yes. A fortune in sealant, a lot of time and effort, and Bubba ain’t helping, but I hope this works to keep condensate from forming.
Comments please. Too much? Not enough?
Thanks, Doug
GBA Detail Library
A collection of one thousand construction details organized by climate and house part
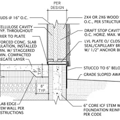
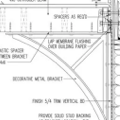
Replies
Polyiso will give you a little better performance for the same thickness of material, and you’d be able to easily tape seal the panels together to avoid all the canned foam detail work.
While I don’t see a problem with the use of XPS, you’re using it on both sides of your rafters so you’re sealing in the air space (no drying ability). Why not use some mineral wool batts between the rafters and then a conventional ceiling material? This would probably give you a bit higher ceiling too.
Bill
If I am understanding right, you are attempting a cut-and-cobble approach (that is, placing the foam in between the rafters). It will be both time consuming and difficult to detail, and mistakes in air sealing could lead to roof failure.
There are multiple ways to build an unvented roof. See Martin's article on the subject:
https://www.greenbuildingadvisor.com/article/how-to-build-an-insulated-cathedral-ceiling
He notes in the article:
"When it comes to cathedral ceilings, here’s the rule: the cut-and-cobble method can be used for vented cathedral ceilings, but not for unvented cathedral ceilings. (There have been several reports of moisture problems in unvented cut-and-cobble cathedral ceilings.)"
Unless there is some reason that you cannot use foam on top of the rafters, you should do so, using the thickness recommendations in the IRC (see: https://www.greenbuildingadvisor.com/article/calculating-the-minimum-thickness-of-rigid-foam-sheathing). By abiding by the minimum foam thickness, you will prevent condensation from forming in your assembly. Then you can simply fill the rafter bays with fluffy insulation.
Thank you both for your comments. The reason I am using cut & cobble is that there is a height restriction on my house (13'6" ground to top of the roof) - and the trailer deck plus floor insulation means that the top of my subfloor is at 2'. Then subtract another foot for finish flooring, rafters, roofing, ceiling and bit for latitude so I am sure to be in compliance with DOT requirements.
That gives me 10' 6" at the peak, less on the low side, to squeeze in a 6'4" ceiling height in the kitchen (code for tiny houses), and 6" or so of joists and flooring in the loft leaves a bit more than 3' 8" headroom in the high side of the loft. In a conventional site-built house, there are no such restrictions, so no reason to cut and cobble. I have read the article about failed cathedral ceilings, and do understand the issues. I'm hoping that the process I outlined will provide an airtight roof assembly that will not allow moisture to reach the underside of the roof sheathing, and that was really the essence of my question. Given that I do want to C&C, does what I am doing sound adequate.
As to polyiso, there is an article here by Martin, our energy nerd, pointing out that as the temperature drops, so does the R-value of polyiso. In fact, at 50 degrees and below, XPS outperforms polyiso. Also, although no foam is particularly green, I think that the blowing agents used in polyisocyanurate are especially nasty. Hence my choice of XPS.
Again, thanks for your comments.
Sounds like you have done your research. Still, I would not recommend the C&C approach here, if you can avoid it.
Is there any reason you are avoiding closed-cell spray foam as a solution? You can completely fill the rafter bays with foam and be done with the whole thing. Alternately, you can use the minimum recommended amounts from the article I linked then fill the remaining space with fluffy insulation. Two inches of spray foam will work in most climates, and that amount allows you apply the foam in one pass and easily use batts meant for 2x4 walls.
Edit: Also, have you considered using 2x4 rafters? Depending on the spans involved and the rafter spacing, it could be doable. The narrower rafters will allow you to add two inches of foam to the exterior without affecting your current footprint.
You've got the blowing agents backwards.
XPS has the blowing agents with the super high global warming potential
Polyiso and EPS are significantly better from a global warming perspective.
Depending on your priorities and/or tolerance for risk, here are two options you might also consider:
- Do a ventilated assembly. You could do the same cut-and-cobble approach, but leave a 1 1/2" air gap under the sheathing and include soffit and ridge vents. This will of course sacrifice some R-value.
- Use closed-cell spray-foam (ccSPF). Using a thickness of ccSPF appropriate to your climate zone, then insulating the rest of your rafter bays with fiberglass or mineral wool is significantly more foolproof than cut-and-cobble. This approach may be more expensive and harder to DIY. HFO-blown ccSPF is the stuff you want from a global warming perspective (Icynene ProSeal HFO is one example, but there are several on the market).
Aedi. Thank you. Let me talk to my structural guy about the 2x4 approach. WRT the use of fluffy pink, I live in the Mountains outside of Taos. Sub zero is not unheard of, and teens are quite common. Roxul is good, but a bit heavy, which is the last thing I want in the roof. I've been trying to figure out how to maximize my R-values, even at the cost of time and effort. Since it is DIY, and I am retired, time is "free". At least it's better than playing golf. :-)
Ah, I think I understand where you are coming from now. In your situation, I would not shy away from fiberglass. It is light, and while it has a slightly lower R-value per inch compared to foam, the difference it will make in your whole assembly when you factor in thermal bridging through the rafters is probably not worth it. Here's some calculations, assuming 16" rafter spacing:
-Your assembly, without the innermost 1" XPS layer, has whole assembly r-value of ~R19
-Full spray foam in the bays gets you ~R21.
-The "flash and batt" approach gets you ~R19.
-Straight fiberglass batts (Not allowed, demonstration only) is ~R17
-Using 2x4 rafters, adding 2" exterior XPS, and using fiberglass batts, gets you ~R22.
I omitted the innermost XPS layer from your assembly, as that can be added onto any of the methods above (though you'll need to use EPS in the assemblies I proposed to allow vapor transmission). To take into account that layer, simply add ~R5 to any of the assemblies.
As you can tell, the cut and cobble R-value benefits are practically non-existent at a whole-assembly level. That, and it's inherent riskiness and difficulty, makes it very hard to recommend.
Brendan - Oops. I do need to look into the XPS vs Polyiso. I don't really want to loose R-value - see my reply to Aedi. And thanks for the info regrding HFO blown foam. I'm in the boonies, so I'll have to see what is relatively available. But thank you.
Not all polyiso is the same regarding cold weather performance. Dow thermax actually increases in R value a little in food weather the same as fiberglass batts. It is more expensive than “regular” polyiso though.
Bill
Have you considered using SIPs (structural insulated panels)? These are factory assemblies of foam insulation and wood structure and might be a better option for you here, especially considering your needs for minimum depth and a well sealed assembly.
Bill
I don't think you can leave the bottom layer of foam exposed inside due to smoke/fire dangers. Definitely not in a conventional house.
Presumably you'll have some sort of heating source. Since it's a tiny house, it'll be easy to heat even with way below code insulation. I'd stick with 2x6 rafters, a 1 1/2 vent space and batts. Pay attention to air sealing. Cover with flexible membrane and wall finish. You'll still need to open the windows when the heat is on. No oil based foam needed. If you decide on foam, at least look for reclaimed foam.
Thanks for the additional comments. One problem is that this is a work in progress. Yes, I know. I should have done it differently from the start, but I'm rather stuck with the shell and unable to add insulation outside of it.
Based on your comments, what I am now considering is drilling 1" dia holes in the sidewalls between rafters and just below the roof sheathing, and then spacing the insulation 1 1/2 " down below sheathing, creating a 1 1/2" vent channel. The 6" metal roof flashing will cover the holes with 2" hanging below the bottom of the hole on the high side. I then would have 4" of room between the rafters for insulation, whether that is fluffy or rigid. And yes, if I want additional insulation at the cost of a small amount of headroom, I can add an inch or two of "continuous" rigid insulation below the rafters. I do worry that the 2 inches that the flashing hangs beyond the bottom of the hole will be insufficient, but I can always get, and easily install, 8" flashing for the high side.
Does this seem more reasonable? Thanks again for your thoughts.