Vented Attic and Roof Plus Exterior Insulation

The basic question is as follows “Is it possible to do a vented attic +roof assembly with exterior insulation?” but it has a series of internal questions built into it…Thank you for everyone’s input.
This question comes after reading a lot of the material on this site – it has been very helpful but I am still stumped on this item. They began brewing in my mind as I was thinking about how to make my home progressively more efficient as I make periodic improvements to it. In particular, the following line of thinking began after I read these articles (https://www.greenbuildingadvisor.com/article/five-cathedral-ceilings-that-work & https://www.greenbuildingadvisor.com/article/a-new-look-at-conditioned-attics) and about how I could accomplish this at my home.
My Current Condition:
I have a small 1350 sqft home with a 2*4 framed roof built in the early 1960s in SF Bay Area; the home currently has gable exhaust vents, soffit/fascia intake vents (pictures attached) and it is currently insulated with loose blown-in insulation about 6-8″ thick and has no baffles at the intakes. My current HVAC ducting is in this hot attic.
My Immediate Goal:
My roof is due for replacement and I wanted to retrofit the roof and attic with roofline insulation and exterior roof insulation when I redo it. The goal is to bring the HVAC into the conditioned envelope for now. Ideally, I would like to do the work myself as much as possible – not sure if this is realistic. I am no expert at this kind of work, but I am willing to put the work in and I have friends and family who have done work like this before and are willing to help me.
My Long Term Goal:
I would ideally like to get my home to generate all the power it needs from the PV system (the home is south-southwest facing with the majority of rooflines facing to the E/SE/S/SW/W) with almost no solar obstructions (trees, other homes, etc. To accomplish this goal, I plan to get PV on the roof, Battery storage systems, replace gas appliances with electric/heat-pump systems (water heater, cooktop, heater, etc), aggressively insulate and air tighten the home over time, encapsulate and insulate the crawl space, and add a fresh air ventilation system.
My Current “Main” Concern:
As indicated by the title query, I am uncertain on whether exterior insulation can be applied to a vented roof using the venting setup detailed below as I have never seen it done or seen it detailed anywhere before. The driver for this concern is the distance from a future ridge vent to the initial framing and vent baffles after we account for the entire roof assembly thickness.
My “Plan” for the Venting and the Roof:
The plan on venting is as follows. I would closeup my existing gable exhausts and shift to a ridge-vent system (seismic/shear needs permitting) with baffles running on the underside of the roof running from existing intakes to the ridge peak, with dense blown-in insulation applied to the underside of the baffles on the interior and with 5/8th drywall on the underside of the roof rafter framing. If needed I would consider extending the roof rafters by sistering on 2*2 or even a 2*4 if possible (seismic/live load/dead load) permitting. I would also replace the existing attic access, with a new insulated dropdown door, and also add some subfloor to the attic floor to the ceiling joists to use the now insulated attic for some limited storage and to place an HRV or ERV in the future. I will be seeking guidance on the structural items prior to moving forward with any modifications.
I would like to work with the soffit/facia venting setup I currently have due to cost and complexity issues. Is this possible, or am I working with an irrational expectation/assumption? In the future, I plan to replace my windows & doors and also add mineral wool insulation to the exterior walls, followed by either stucco or some form of horizontal siding – when I do this, I would add a continuous boxed soffit intake as seen on more modern-built homes and recommended in the details I have seen for vented roof assemblies.
If exterior insulation is possible, then the plan for the exterior insulation is to repair and replace existing roof sheathing as needed, apply a fluid-applied or peel-n-stick WRB (exact spec is TBD and I am open to recommendations), then install 1-2 layers of mineral fiber insulation (1.5/2/3/4 inches total depending on structural feedback), tape the exterior layer seams (again, haven’t seen mineral wool taped so not sure this is possible – open to input), followed by an air gap using either 1*2 or 1*3 furring strips (undecided on right furring to use) with a continuous bug screen (can be removed when boxed soffit is built), and finally another roof sheathing layer, with a traditional tar paper + shingle roof on top. I was initially considering a standing seam roof, but I couldn’t justify the added roofing costs to myself (is this true, or a false assumption?).
An Alternate “Plan”:
I could also shift to an unvented roof assembly as detailed in the article above and other sources (Fine Homebuilding and ProTrade Craft articles and videos), but I am not certain I have the skills to make this switch on my own and would probably need to hire a contractor to perform this work as most schemes I have seen would require the roof system to be reframed. I am also concerned about having an unvented roof given the sun exposure my roof has; my understanding is that the roofing material takes a beating when done with an unvented roof. Also, my understanding is that when you switch to an unvented roof, you need to tackle the exterior walls at the same time – if so I would also need to wait a few more years before doing this project so I could save the additional cost of this larger scope change.
I have tried to be nice and polite – wasn’t able to satisfy the “brief” requirement; my apologies for the lengthy post. I look forward to your responses.
GBA Detail Library
A collection of one thousand construction details organized by climate and house part
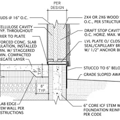
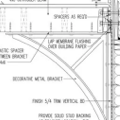
Replies
“Is it possible to do a vented attic +roof assembly with exterior insulation?” If that's your core question, I would say the answer is no. With exterior insulation, you are moving the thermal boundary from the attic ceiling to the roof sheathing. Everything under the sheathing becomes part of the homes "conditioned space."
If you have flat ceilings over the attic, the most economical approach would be to add more air permeable insulation (blown cellulose). However, you would first want to tackle air sealing the attic floor.
You also asked if work on the walls had to be done at the same time as the roof/attic. Again, the answer is no.
But if you have ducts in the attic and also want to use that space for an ERV system, converting the attic to an unvented, conditioned space makes a lot of sense. You could do this using the flash and batt method (a flash of closed cell foam to the underside of the sheathing with the balance of the R-value provided by air permeable insulation).
That said, let's see if one of the experts will chime in.
San Fransisco is IECC climate zone 3. In that climate it only takes R5 (minimum) on the exterior to protect the roof deck from interior moisture drives. More is better, of course.
The IRC code minimum for zone 3 attics is R38 if the insulation is between rafters or joists, or U0.030 (= R33 "whole assembly R" factoring in the thermal bridging, the R values of the roof deck & air films, etc.). If one used 3" roofing polyiso (R17.4) under a 5/8" OSB nailer deck or a 3.5" polyiso nailbase panel (R18) and R15 rock wool batts between the 2x4 rafters you'd be only R33-ish at center cavity, well below the IRC code minimum on an R value basis, but due to the thermal break of the continuous foam over the rafters it'll still make it on a U-factor basis. The edges could be protecte by a 1x4 facia board.
https://up.codes/viewer/nevada/irc-2018/chapter/11/re-energy-efficiency#N1102.1.2
https://up.codes/viewer/nevada/irc-2018/chapter/11/re-energy-efficiency#N1102.1.4
https://www.hunterpanels.com/docman-categories/product-documents/hpanels/flat-products/39-h-shield-flat-polyiso/file
https://www.hunterpanels.com/product-documents/hpanels/speciality-products/108-h-shield-nb/file
It's "worth it" to install PERFORATED aluminized fabric type radiant barrier (~5 perms) stapled to the underside of the rafters to keep earthquakes from shaking the batts back out- it doesn't need the full gypsum board treatment. The continuous radiant barrier next to the interior side air film adds another ~R1 to the whole-assembly performance. Do NOT use UN-perforated foil, aluminized fabric or bubble pack type radiant barrier, since those are all true VAPOR barriers as well. The material cost of perforated RB is about $90-100 per 1000 square feet, usually sold in 4' x 250' rolls. In your installation it doesn't need to be perfect, as long as there is R5+ above the roof deck.
With the roof deck insulated the gable vents should be sealed off and the gable ends air sealed & insulated. Again, perforated RB is fine to use to keep unfaced rock wool batts in place during tremors.
It's safe to leave the insulation on the attic floor, or remove it (your call), but it's R value can't be applied for meeting code R-value requirements.
My understanding is that the IRC has higher performance standards for roofs in your local climate than CA Title 24 demands, but you also get extra credit for radiant barriers.
If you can find a local source for RECLAIMED roofing polyiso the stuff will be dirt-cheap compared to nailbase panels or virgin stock foam + OSB nailer deck. From a performance modeling point of view de-rate it to R5/inch due to age, but from a code compliance point of view it can still be treated as R5.7/inch (or whatever it might be labeled, if the R-value happens to be printed on the paper or fiberglass facer.) Run this search every week or so and you're likely to come up with something by the end of the summer:
https://sfbay.craigslist.org/d/for-sale/search/sss?query=rigid%20insulation
These people in Sparks NV advertising in your area will sell you 23 sheets of 3" x 4' x 8' factory-seconds roofing foam for $750 + shipping, which is probably $25-28 per sheet after shipping, or about half the cost of perfect no-blemishes good.
https://sfbay.craigslist.org/eby/mad/d/sparks-polyiso-insulation-many-sizes/7327959698.html
If doing it with 3" sheet foam + OSB/plywood nailer deck, follow the same fastener schedule & specs for nailbase panels, for 3.5" nailbase, but stagger the seams of nailer deck with those of the foam for better air & water tightness over time. See:
https://www.hunterpanels.com/docman-categories/product-documents/hpanels/speciality-products/1388-h-shield-nb-application-guide/file