Zone 5 Retrofit (Chicago)
Hello,
In few weeks I will be replacing my siding and windows. House was build in the mid 70’s with single pane glass and aluminum siding. Brick on the west façade, but I will be replacing all of that with vinyl siding. At the same time I would like to add more insulation. House is a one story ranch. I have read most of your articles and I believe I have a solution with one unknown. Current wall assembly is a 2×4 framing, fiberboard insulation (that brown looking paper sheathing) probably #15 felt paper and aluminum siding. I also have aluminum foil faced batt insulation. Once I open up the walls from the outside I have to choices.
My prefer option would be to keep the fiberboard insulation panel (for cost reasons), remove any felt paper and wrap the house in Tyvek drainwrap. Then apply 1.5″ of EPS (great article on rigid foam thicknesses requirements) and my vinyl siding, preferably without any additional furring strips. However, that brings me back to my unknown. Does aluminum faced batt have any permeability so that the wall could dry to the inside of the building? I am afraid this wall will not dry properly if I sandwich cavity insulation and fiberboard between foil faced vapor barrier and the EPS.
Option two, is to remove, siding, fiberboard and aluminum faced batts, and start from scratch. If I go this route, what kind of vapor barriers can I install inside the cavity? Do I even need one at this point with outside insulation? Followed by unfaced batt (I know GBA recommends drilling out holes and blowing in the insulation but I feel it is counter productive putting up new sheathing just to make holes in again), 1/2″ OSB (I know plywood would be better but it is an additional cost), drainwrap, EPS and siding.
Last year while renovating the bathroom I found some mold behind drywall on the back face of the exterior fiberboard sheathing. It was around the shower enclosure, which makes me believe it was from a leaking shower. I would like to avid removing all od that fiberboard but I will perform additional investigation to make sure the mold wasn’t coming from the outside of the wall assembly.
Thank you.
GBA Detail Library
A collection of one thousand construction details organized by climate and house part
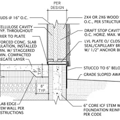
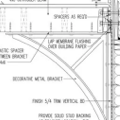
Replies
Foil facers are true vapor barriers, but as long as the air leakage to the interior is minimal and you have more than R5 on the exterior the risks of moisture accumulation are low.
Asphalted fiberboard is extremely tolerant of moisture highly vapor permeable, and good for about R1.5, to which you're adding an other R6- R6.5 of EPS. Type-II EPS without facers will still run about 1.5-2 perms @ 1.5", so with inherently backventilated siding such as vinyl or aluminum there is still a reasonable amount of drying capacity toward the exterior.
The most important detail to get right is proper lapping of the window flashing with the housewrap, since any bulk water that gets in would still take awhile to leave through 1.5-2 perm EPS.
I don't think you need to remove the existing fiberglass batts just because they are foil-faced batts. I'll expalin why in a minute, but before I do, I'll answer your second question.
Q. "If I remove the existing fiberglass batts, what kind of vapor barriers can I install inside the cavity?"
A. You don't really have to install any vapor barrier or vapor retarder on the interior side of your wall if you are installing exterior rigid foam. The principles behind foam-sheathed walls are explained in this article: Calculating the Minimum Thickness of Rigid Foam Sheathing.
Now to return to your original question: I'll cut-and-paste my stock answer below.
Many energy experts worry that it may not be a good idea to install exterior foam on a house with an interior vapor retarder. Although it would be better if the vapor retarder weren't there, the fact is that tens of thousands of Canadian homes with interior polyethylene have been retrofitted with exterior rigid foam, and there haven't been any reports of widespread problems. According to building scientist John Straube, all indications show that these retrofits are "not so risky as most people think. These homes will probably be fine."
That said, the installation of exterior foam is not advised on any home that has suffered wet-wall problems like leaking windows or condensation in stud cavities. If you plan to install exterior foam during a siding replacement job, keep an eye out for any signs of moisture problems when stripping the old siding from the walls. Investigate any water stains on housewrap or sheathing to determine whether the existing flashing was adequate.
If there is any sheathing rot, determine the cause -- the most common cause is a flashing problem, but condensation of interior moisture is not impossible -- and correct the problem if possible. If you are unsure of the source of the moisture, hire a home performance contractor to help you solve the mystery.
If your sheathing is dry and sound, I don't think you need to worry about adding exterior foam. Adding a rainscreen gap will certainly go a long way toward avoiding future moisture problems. Of course, it's important to be meticulous with your details when you are installing your new WRB and window flashing. It's also important to keep your interior relative humidity within reasonable levels during the winter. Never use a humidifier.
To summarize, here are four caveats:
1. Be sure that your foam is thick enough to keep the wall sheathing above the dew point in winter. Read more on this topic here: Calculating the Minimum Thickness of Rigid Foam Sheathing.
2. When the siding is being removed, inspect the existing sheathing carefully for any signs of water intrusion, and correct any flashing or housewrap problems.
3. Install rainscreen strapping so that there is a ventilated gap between the new exterior foam and the siding.
4. Keep your interior humidity under control during the winter; if the interior humidity gets too high, operate your ventilation fan more frequently.
-- Martin Holladay
Thank you Dana and Martin for you inputs. Humidity during winter is never na issue (always below 40%) it is the summer humidity that is forcing me to use the dehumidifier. On a humid day it can reach access of 60%. Probably leaking old windows and doors and poor insulation between wall plate and foundation because I could feel cold draft air (during winter) around baseboards.
Martin you said "If your sheathing is dry and sound, I don't think you need to worry about adding exterior foam". I believe adding adequate amount of exterior insulation (R-5 in my case) and taping all the joints would help me with the overall R value of the wall plus any air leakage I might have. Corners of my interior walls are always cold, especially where brick meets the siding. Continues insulation makes sense to me, or am I wrong?
-Lucas
I think Martin meant "If your sheathing is dry and sound, I don't think you need to worry about adding exterior foam [causing moisture issues]". But hopefully Martin can clarify ;)
Adding continuous insulation is almost always a great idea.
It would probably be a good idea to post a detail showing how you plan to manage the flashing, insulation, and WRB at windows to get some feedback once you are at that point in the design process.
Lucas,
Brendan is right about my intended meaning. Exterior rigid foam will work fine. You don't have to worry about moisture issues if you install the rigid foam.
-- Martin Holladay
Brenden,
As far as the window flashing goes, I read few other articles by Martin. (This website provides infinite resources). Which brought me to my original conclusion that I would like to stay with a max. of R-5 (which is the minimum requirement where I live) and no furring strips. By doing so, I am only adding 1.5" of additional thickness to my assembly, and still doing a conventional window flushing (WRB over existing sheathing, followed by 1.5" EPS). However, I will consider putting the WRB on the outside of the foam if it makes more sense to bring that over the edge of EPS into a window opening.
"There are five possible approaches:
Install the windows as outies, with the window flanges on the exterior side of the rigid foam, and simply nail or screw the window flanges to the sheathing and framing using long fasteners through the foam. This approach requires neither a window buck nor a “picture frame,” but the approach only works if you are installing 1 1/2 inch or less of rigid foam and if the siding — for example, vinyl siding — does not require vertical furring strips. (If you are installing 2 inches of rigid foam, you can still get away without the plywood buck — but you’ll need to fasten the windows with masonry clips, not the window flanges.) For more information on this approach, see Nailing Window Flanges Through Foam."
Martin - I read your original comment too fast. Thank you for clarifying it.
You're really underestimating the Rvalues: 1.5" of Type-II EPS is about R6.4, and 1.5" of Type-I EPS would be about R5.8.
I'm not sure where you're getting the "...max. of R5..."
The fiberboard sheathing is moisture tolerant and adds another ~R1.3 for half-inch, ~R2 for 3/4", so you're looking at a minimum of R7.1 to as much as R8.4 on the exterior side of the batt insulation, which should be plenty.
The IRC minimum prescriptive of R5 is for plywood or OSB sheathing, which are FAR more susceptible to moisture than asphalted fiberboard, and it presumes the only interior side vapor retarder is latex pain (3-5 perms), not foil facers (0.05 perms). If the interior walls are reasonably air tight there should be no appreciable moisture accumulation in the fiberboard sheathing over a winter, but even if there were the fiberboard can easily handle 5x as much moisture as plywood. What's more, the fiberboard runs about 5 perms when bone-dry, 15 perms under more humid conditions, compared to plywood's ~5 perms when at a moisture content high enough to support mold. The high vapor permeance of the EPS relative to the low-perm foil facers on the batts would allow the assembly to dry through to the exterior even in winter.
So it's really a matter of making sure there are no chronic bulk-water leaks from the exterior getting by the flashing & foam.