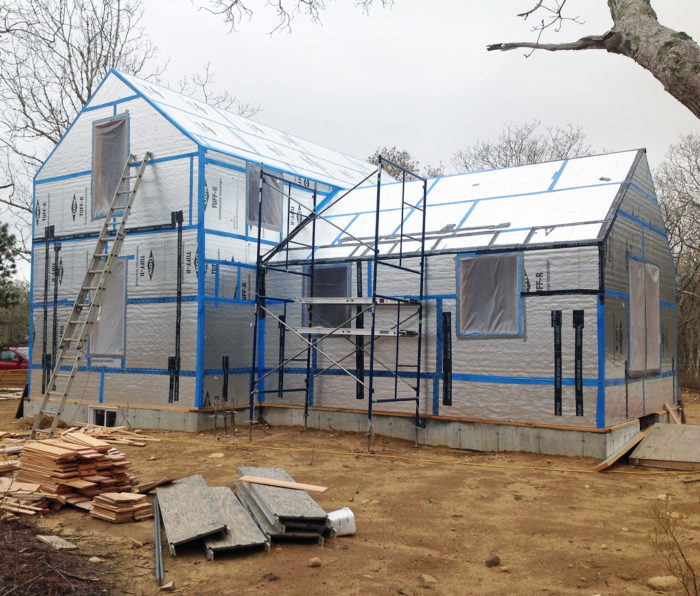
Image Credit: Marc Rosenbaum
The ability of insulation products to resist the flow of heat changes with temperature. Most insulation products — including fiberglass batts, extruded polystyrene (XPS), and expanded polystyrene (EPS) — perform better at low temperatures than high temperatures. At lower temperatures, there is less conduction, less convection, and less radiation — so insulation materials usually work better than they do at warmer temperatures.
However, one type of rigid foam, polyisocyanurate, doesn’t follow this pattern. At temperatures below 50°F, polyiso performs worse than it does at a mean temperature of 75°F.
Although many building scientists have known about this phenomenon for years, published data from recent testing by Chris Schumacher and John Straube — two researchers at Building Science Laboratories in Waterloo, Ontario — have sparked new questions about the performance of polyiso at cold temperatures. (See links to previous GBA reports on the topic in the “Related Articles” sidebar, below.)
There are two ways that polyiso can disappoint
Some people confuse the problem of polyiso’s poor cold-weather performance with a different problem — that of “thermal drift.” The phrase “thermal drift” refers to the gradual dissipation of gaseous blowing agents which are replaced by air as they exit the foam. This process takes several years.
Gaseous blowing agents are chosen for their thermal properties, so the escape of these gases causes the R-value of polyiso to decline. Polyiso manufacturers have faced decades of criticism from those who assert that thermal drift makes the R-value labels on polyiso unrealistic. Responding to these critics, polyiso manufacturers agreed in 2002 to adopt a new method of R-value testing, the “long-term thermal resistance” (LTTR) method. This testing method strives to come up with a more realistic R-value for polyiso — one that takes thermal drift into account. (For more on this issue, see Thermal Drift of Polyiso and XPS.)
Weekly Newsletter
Get building science and energy efficiency advice, plus special offers, in your inbox.
This article is only available to GBA Prime Members
Sign up for a free trial and get instant access to this article as well as GBA’s complete library of premium articles and construction details.
Start Free TrialAlready a member? Log in
27 Comments
Which brands...
...of closed cell polyurethane have switched over to using HFO1234yf ???
Also, in the National Roofing Contractors Association graphs showing polyiso performance at different outdoor temps, what is the temp at the conditioned space side of the foam?
Showing just the performance relative to outdoor temp is useless unless it's presumed that polyiso is 100% of the insulation.
And if that's the case those graphs are meaningless for trying to assess performance as insulating sheathing on the exterior of framed wall or roof with cavity insulation, since the average temp through the foam won't bet the same as if one side were maintained at single temp.
The range of performance between samples/vendors is impressive though, even if not all the relevant parameters are spelled out.
Response to Dana Dorsett
Dana,
Q. "Which brands of closed cell polyurethane have switched over to using HFO1234yf?"
A. [Edited answer] I'm not sure. Looking into it.
Q. "In the National Roofing Contractors Association graphs showing polyiso performance at different outdoor temperatures, what is the temperature at the conditioned space side of the foam?"
A. I'm looking into that now. I'll post the information when I learn it.
Per John Straube....
John Straube states:
"The latest solution from Honeywell is the company's new low-GWP product called HFO 1234yf. This is the gas used in some brands of closed-cell spray polyurethane foam."
Can he name even one brand using it, or is that conjecture on his part?
Response to Dana Dorsett
Dana,
Sorry. I'm guilty of a hasty misreading of your question. My brain read "polyiso." I'll look into it.
Temperature question
Dana,
As you probably know, the Federal R-Value Rule requires that insulation manufacturers test insulation materials at an average temperature of 75°F according to the ASTM C518 procedure. ASTM C518 permits testing at a range of temperatures from 20°F to 120°F. David Yarbrough explained, "An average temperature of 75°F can be achieved by the hot plate at 100°F and the cold plate at 50°F -- a commonly used set of conditions. An average of 75°F can also be achieved by hot plate at 90°F and cold plate at 60°F. There are an infinite number of combinations that average to 75°F."
Is this test method satisfactory? Not really. Manufacturers are not required to report the temperatures at which they test their insulation materials, as long as they follow the Federal R-Value Rule and ASTM C518.
I just emailed John Straube with this question: “In the National Roofing Contractors Association graphs showing polyiso performance at different outdoor temperatures, what is the temperature at the conditioned space side of the foam?” Straube responded, "It varies. They [the people performing the test] don't have interior and exterior, just hot and cold. They likely choose a 50 F° difference, but the hot and cold side [temperatures] chosen to generate the mean they reported [varies]."
But the graph doesn't present the mean temp, it's outdoor temp.
Straube suggests:
"It varies. They [the people performing the test] don't have interior and exterior, just hot and cold. They likely choose a 50 F° difference, but the hot and cold side [temperatures] chosen to generate the mean they reported [varies]."
The axis on the graph reads "Outdoor Temperature", not "Mean Temperature".
BTW: My prior understanding was that for labeling purposes per the FTC insulation had to be tested under ASTM C518 at a 75F mean temp at a nominal 30F delta-T (90F hot side, 60F cool side). ASTM C518 doesn't specify any delta-T or the mean temp, but you can't just pick & choose when labeling the performance. ( That 30F nominal delta may have been a minimum, not a nominal. I haven't read the regs in quite awhile, I could be getting fuzzy on that.)
Testing I care about.
First off, thank you for this, it filled in some gaps in my knowledge of this issue, and I have been considering this as a factor on some projects lately.
More than anything though, this made me wonder why insulation is tested the way that it is. It seems to me to be tested under a condition that nobody cares about. I certainly don't (unless someone can explain why I should). So scrap the details of ASTM C518, etc., I want to know what its heat flow is with 68F on one side and 0F on the other. While we're at it let's do one for the folks down south at 75F and 100F. Those are numbers I care about. I realize that I'm over simplifying here but for the sake of conversation humor me. When is anybody counting on build insulation to perform at a mean temperature of 75? At 75F I have my windows open.
Maybe we should be pushing for different testing standards and let that force the hand of manufacturers.
Response to Andy Kosick
Andy,
One of the main aims of the Thermal Metric Project undertaken by the Building Science Corporation was to address the issues that bug you. Some data from that project have been published, but unfortunately researchers have released no information on the brand names of the tested polyiso samples. One of the reasons that brand names have mostly been kept secret is that much of the funding for the testing came from insulation manufacturers.
The Thermal Metric Project has been discussed in several GBA articles, including these:
A Bold Attempt to Slay R-Value
Air Leakage Degrades the Thermal Performance of Walls
The main political reason that it's hard to redefine R-value is that any change in the definition would create winners and losers. The losers all have lobbyists.
Your proposed changes are intriguing but open to challenge. For example, many cold-climate builders would note that there are relatively few hours per year when the outdoor temperature is at 0°F or colder. This is the argument used by those who favor the European method of measuring window U-factor (based on an outdoor temperature of 32°F) over the North American method of measuring window U-factor (based on an outdoor temperature of 0°F). For more information on this controversy, see Presumptive European Superiority Syndrome.
Many hot-climate builders, on the other hand, will note that roofing temperatures above 100°F are quite common, so your proposed hot-climate testing protocol should be changed to reflect a higher outdoor temperature.
These problems can't be solved easily, because no matter what testing temperatures you choose, someone will be dissatisfied.
"The graph reports outdoor temperature"
Dana,
Thanks for your comments. I am awaiting more information from John Straube and Chris Schumacher on the graph reporting NRCA data.
Andy
Unless the polyiso is the ONLY insulation in the assembly, only one side (or perhaps none) will be at either the interior or exterior design temperature. (Under the roofing it will be both above and below the outdoor design temps, due to solar gain and night-sky radiation.)
The performance at the mean temp through the foam layer is a more useful metric, since it doesn't vary rapidly with delta-T. It's performance at +25F on one side and 5F on the other (mean temp +15F, delta-T of 20F) isn't very different than with +20F on one side, and +10F on the other (mean temp of +15F, delta-T of 10F) or 30F on one side, 0F on the other. But if it's centered around +30F it can be pretty different than when centered around +15F.
That's what makes the graphs showing only outdoor temp sort of useless. The mean temp performance (at any realistic delta-T) would be something you could actually design around. But with only the outdoor temp you can't. At +15F on one side it's performance will likely be very different between a warm-side time of +30F, as compared to what it would do with the warm side at 70F or 90F.
simplifying...
what I think Dana was saying, why don't they pick a *fixed delta* for
all this testing, with an easily discernible average, and just slide
the endpoints up and down together as needed?? That might yield a
far more uniform set of numbers. I'd be interested in seeing what
*that* curve looks like across different brands/blowing-agents.
_H*
Response to Martin and Dana
Yes, my proposed changes are absolutely open to challenge. Dana, you're right of course about the location of the foam in the building assembly (no more pulling numbers out of the air at 11pm for me). I think the point I was trying to make is that the conditions under which the insulation is going to be expected to perform should be the conditions that it is tested under.
Also, I can see using average winter/summer temperatures to determine the testing conditions, this making the most sense for overall performance in something like energy modeling software, but there is a strong argument to be made for testing at temperature extremes. After all, it's at the extremes that R-value is counted on the most, with heat pumps being sized within a hair's breadth and sheathing needing to be kept above dew point temperatures.
An explanation of the graph displayed here
It’s unfortunate that the graph shown in this article is the one that we have to talk about. It looks like the graph was lifted from the Thermal Metric presentation that I made at the 2012 Summer Camp. That graph is misleading without the accompanying verbal explanation (which I think we skimmed across at summer camp).
To my knowledge NRCA has only ever tested using the “standard” conditions described in ASTM documents: Mean temperatures of 25, 40, 75, and 110 F, all with temperature differences of 50 F between the hot and cold plates. The attached table (top image, below) summarizes the temperatures used in the tests.
Also attached (second image, below) is the original version of that graph. Notice the bottom axis and label are different! The graph summarizes the data (from testing at those 4 mean temperatures) that NRCA presented at the 2010 roofing conference.
Now, mean temperatures really confuse people. "What does mean mean? Is it an average over time? No? Oh it’s an average temperature across the wall.”
“How do we use these numbers to design our buildings? We don’t typically have buildings that operate at a mean temperature of 25 F with a cold side at 0 F and a hot side at 50 F.”
Back at the 2012 summer camp, someone (might have been Joe Lstiburek) asked, “What would the equivalent outdoor temperatures be?” So, we extrapolated the test temperatures to get “Equivalent Outdoor Temps.” For example, if you assume the indoor temperature is 72 F, and you have a mean temperature of 25 F. To get that mean temperature in a wall, the outdoor temperature would have to be 72-2x(72-25)=-22F. (See the table reproduced as the bottom image, below.)
You can use this approach with materials that have “normal,” near straight line R-value vs. Temperature relationships. This approach doesn’t work for materials like polyiso. I didn’t like THAT graph when we made it; I’m hating it now. At summer camp, I hope I prefaced the slide with something like “the data are developed at standard mean temperatures but we’re making a leap to extrapolate them to outdoor temperatures here.”
Almost immediately after summer camp I moved beyond the ASTM standard test temperatures and developed my “In service” test temperatures -- In service temperature test with room temperature on one side and outdoor temperatures on the other. Those were the ones we used for Info Sheet 502. I believe that was published / posted somewhere late 2013.
The problem with the in-service temperature test data is that the results are only valid for the thickness tested and the precise temperatures tested. In 2014 I moved beyond those to try to get a REAL R-value/in vs Temperature (i.e. a k vs T curve) that you could use to calculate the R-value and performance of any assembly under any conditions. We’ve mostly worked that method out, and hope to publish it at an ASTM Symposium.
When you see any of my data that says “convergent,” it was developed with that method. Now, our graphs will typically have an x-axis label that says “mean temperature” when the data was derived using the standard (ASTM) test temperatures; or they’ll have an x-axis label that says simply “temperature” when they use our convergent method.
John and I have tried not to overwhelm the average practitioners with all of this technical crap but I think it is important for you to have some knowledge of it for context.
.
Response to Chris Schumacher
Chris,
Thanks very much for taking the time to provide such a thorough explanation; it is very helpful.
During my phone conversation with John Straube -- the interview presented here -- John referred to the NRCA data, and sent me an email that included the graph he was referring to. I reproduced the graph which he sent me.
I'm grateful to both of you for your work and for your explanations.
Response to Dana Dorsett's question about HFO1234yf
Dana,
Today I got an email from John Straube, responding to the question, "Which brands of closed-cell spray polyurethane foam now use HFO1234yf as a blowing agent?"
Straube answered, "I am pretty sure none are yet marketed. They are trying this out in the field with preferred contractors to test out the real world issues, if any, with the product. There has been lots of lab testing so we know it works there. Why don't you contact Mary Bogdan from Honeywell and ask what the status is? She can give you definitive information."
I have emailed Mary Bogdan and will share any information she provides when she answers.
Thanks Chris, Martin!
I s'pose they should have labeled that axis for what is was: "Extrapolated equivalent outdoor temp, at an indoor temp of 72F", which would give it the proper context. That begs other questions ("Extrapolated how, from what?") but the fuller explanation with the other graph.
Clearly the mean temp and delta-T on the polyiso layer changes when it's being used as insulating sheathing on a framed wall with cavity insulation, but knowing the mean temp performance even at a big delta-T is better than nothing.
With 2" of polyiso a 2x6/R20 house when it's 0F outside and 68-72F inside the delta-T across the polyiso is WELL under 50F, and it has a mean temp somewhere around +10F. Performance at mean temp of +10F the performance with the cold side is 0F and the warm side is ~20F (a 20F delta-T) could be substantially different from when the cold side is -15F, and the warm side 35F, as the the standardized 50F delta-T case. The mean models for this type of application are prone to large errors from building design point of view unless the tested delta-Ts are more realistic for the application.
Even if the polyiso sheathing were fully half of the total center-cavity R, the only realistic data points would be at outdoor temps in the (70F - 50F - 50F= ) -30F range so that you get pretty much the full 50F delta-T across the polyiso with the other 50F across the cavity fill of roughly equal R. Everywhere else you'd never see anything even close to a 50F delta-T. The only places in the US that might see average mid-winter outdoor temps of -30F would be at altitude, in the interior of Alaska, say at a cabin at 5000' up in the Brooks Range or something. The mean temp performance curves at 20F or 30F delta-Ts would be more relevant for typical insulating sheathing applications in US zones 4-7, and given the nonlinearity of the performance with temp it really does matter.
More on HFO1234yf
I just received an email from Jeannine Sohayda, a marketing rep for Honeywell.
She wrote, "I am responding to a question you sent to Mary Bogdan. We are not aware of any spray foam manufacturers / systems houses in North America using HFO-1234yf as a blowing agent in spray polyurethane foam."
I guess that's the answer then.
I'd think moving to a greener blowing agent COULD be a marketing coup, assuming the market for closed cell foam actually cared.
It may be that just as with other blowing agent changes, it won't happen until it's required by regulation. Potent HFC greenhouse gases are more tightly regulated in Europe than in the US, but we may get there eventually.
On the polyiso nonlinearity front, you can't really model the nonlinear aspects of it using mean temp with a large delta-T, since that would presume that the changes are fairly linear, and they are clearly NOT. Breaking it down across mean temp with much smaller temperature differences would be necessary to see what it's doing with reasonable resolution, since it's more likely to be sorta-linear across a 20F difference than across 50F, looking at the mean-temp performance curves at using a 50F delta. The performance of polyiso clearly changes dramatically and non-linearly over a range of 50F within some temperature ranges that matter.
For instance, if the performance drops to say, R3.5/inch at a mean temp of 20F at a 50F delta-T, it could easily be that the foam that's colder than 15F could be performing at less than R1/inch and the part over 30F of it could be performing at R6-7/inch, and near 20F it could be running R5/inch. But there's no way to tell without breaking it down into smaller ranges to know where the sharp knees in the curves are. Using a 50F delta-T makes it all blurry using a single number for the very large range.
Correction to chart
In the first chart, the line labeled "0.417" should be "0.174".
Response to Michael Bluejay
Michael,
Thanks. It's been fixed. GBA appreciates your correction.
Interesting if polyiso doesn't preform well in cold weather and also more easily absorbs water why would Huber choose polyiso over EPS for their Zip R sheathing. Maybe someone else already does? Are there other sheathing products similar to Zip R that use EPS? I know Atlas makes their sheathing with EPS but its on the outside and requires a specific nail gun.
Interesting article. One comment about determining the R-value of polyiso boards at different indoor/outdoor temperatures. If the manufacturers of polyiso just provided a curve of the their materials thermal conductivity vs temperature (ITS actual temperature, not indoor/outdoor), you could (in theory) then determine the effective R-value at any board thickness and indoor/outdoor temperature combination. If you assumed 1-D heat flow, you could probably calculate it using a speadsheet. A finite element code could do it more accurately and in 2D or 3D. The point is that you don't actually have to construct a wall and run a bunch of test to get this information (which would be expensive).
Patrick,
Your comment raises many questions, including this obvious one: How does a manufacturer determine thermal conductivity at a certain temperature without performing testing that includes both (a) a temperature difference across the insulation and (b) measurable heat flow? Heat flow does not occur without a temperature difference.
Leaving that question aside, I agree with your basic point: If insulation manufacturers released data on insulation performance at different temperatures, builders and designers would be better served.
Martin,
There are number of ways to measure thermal conductivity, depending on the material. The one I'm familiar with sandwiches the test material between layers of a "reference" material of known thermal conductivity. A temperature difference is placed across the stack and the temperature at each interface is measured. Because the thermal conductivity of the reference material is known, you can then calculate the thermal conductivity of the unknown material based on the temperature drop across it. With a material whose thermal conductivity varies with temperature, it would be important to keep the test layer thin so the temperature drop across it is relatively small (maybe a few degrees). If you then assume the thermal conductivity varies linearly with temperature over that small temperature drop (a reasonable assumption) then what is measured is the thermal conductivity of the test material at the average temperature. The point though is that this can all be done in a lab under highly controlled conditions with reasonably good accuracy. The data could then be used in simulations to predict board performance under a variety of "real world" conditions.
Patrick,
Of course thermal conductivity is measured in a lab under controlled conditions. One of the most common methods is ASTM C518, "Standard Test Method for Steady-State Thermal Transmission Properties by Means of the Heat Flow Meter Apparatus." (For more information, see "Understanding R-Value.")
Clearly, you agree with my assessment that determining thermal conductivity requires a test that includes a temperature difference across the insulation. (You confirmed that when you wrote that your proposed test requires "a temperature difference ... across the stack.")
That makes more sense that your original comment, which suggested that manufactures provide "a curve of the their materials thermal conductivity vs temperature (its actual temperature, not indoor/outdoor)." You can't have thermal conductivity at "an actual temperature, not indoor/outdoor" -- you always need a temperature difference across the insulation being tested.
Martin,
Yes I agree, to determine the thermal conductivity of a material you need to measure the temperature drop across it (along with other info). But thermal conductivity itself is a material property which, for most materials, varies somewhat with temperature. So at a given temperature a piece of polyiso will have a definite thermal conductivity value, and you can create a graph of that vs temperature (its bulk temperature, not temperature drop). If you don't believe me, google thermal conductivity vs temperature for copper or aluminum or some other material, and you'll see graphs where its plotted vs absolute temperature (°K) or maybe Celsius (°C) .
Patrick,
I believe you, and am quite familiar with the concept. Thanks for your comments.
Log in or become a member to post a comment.
Sign up Log in