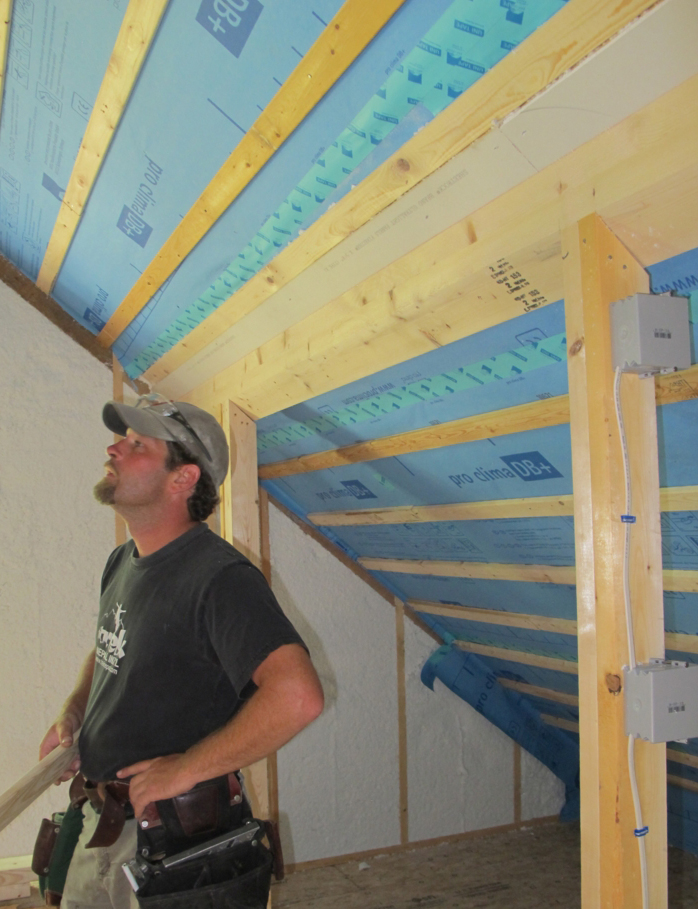
Image Credit: Photo #1: Alex Wilson
During the winter, when indoor air is usually warm and humid, most wall sheathing is cold. Under these conditions, we really don’t want water vapor to move from the interior of our homes toward the exterior. That’s why builders in the 1980s installed polyethylene on the interior side of walls.
During the summer, on the other hand, outdoor air can be warm and humid, while our drywall is often cooled by the air conditioning system. Under these conditions, we want to limit the movement of water vapor from the exterior toward the interior. We also want to allow any moisture in our walls to be able to move toward the interior of our homes, unimpeded by a vapor barrier, so that a damp wall assembly can dry out. That’s why an interior-side vapor barrier works against us during the summer.
There are two possible solutions to this dilemma. The first solution is to install an adequate thickness of continuous rigid foam on the exterior side of the wall sheathing. This foam layer prevents inward vapor drive during the summer, while also keeping the wall sheathing warm enough during to winter to avoid condensation or moisture accumulation.
In some types of wall and roof assemblies, it may be appropriate to consider a second solution: installing a “smart” vapor retarder — that is, a membrane with variable vapor permeance — on the interior side of the wall assembly.
The membrane’s vapor permeance rises and falls
When conditions are dry, a smart vapor retarder is relatively vapor-tight (in other words, it has a relatively low vapor permeance). When the air or the building materials adjacent to a smart vapor retarder get more humid, however, the membrane becomes more vapor-open — in other words, its vapor permeance increases. Under dry conditions, it…
Weekly Newsletter
Get building science and energy efficiency advice, plus special offers, in your inbox.
This article is only available to GBA Prime Members
Sign up for a free trial and get instant access to this article as well as GBA’s complete library of premium articles and construction details.
Start Free TrialAlready a member? Log in
34 Comments
Great quote
“This is an example of a wonderful tool perfectly analyzing the wrong problem."
One can learn a lot playing with WUFI, but there's also a lot one can't learn playing with WUFI.
Vapor Permeance Range
Martin - Great article. The line," That means that the vapor permeance range of DB+ is greater than that of Membrain…" isn't quite right ,if your numbers are correct. You list DB+ at 0.8-5.5 and Membrain at 1.0-10, making Membrain have a slightly greater range than DB+.
Response to Kevin Zorski
Kevin,
Thanks for catching my error. I have corrected the text.
Thanks for having a close
Thanks for having a close look at this. The solution still seems to be a combination of a wall that dries to the outside as well as an interior wall that allows for a certain amount of humidity in it , but evenly, and when it needs to . I can't help but feel that polyethylene makes us feel like were living in a bag!
Response to William Murray
William,
I'm not sure that I understand what you mean. But here's my take: From a moisture management perspective, it's hard to improve on a 2x6 wall with an adequate thickness of rigid foam on the exterior side of the wall sheathing.
Everything on the exterior side of the rigid foam dries to the exterior.
Everything on the interior side of the rigid foam dries to the interior.
The rigid foam prevents inward solar vapor drive during the summer.
The rigid foam keeps the wall sheathing warm enough during the winter to prevent condensation or moisture accumulation.
According to researchers who have monitored the moisture content of wall sheathing in a variety of wall types, this wall stays dryer than any other wall.
Martin, when you say above "rigid foam on the exterior side of the wall sheathing" what do you mean by wall sheathing? Is it the dry wall or is it the sheathing applied to the studs on the outside of the house (OSB,ply, celotex etc)?
It's the sheathing applied to the exterior side of the studs, such as OSB.
If readers post questions here...
I'll be on vacation until Saturday February 6, so I won't be answering questions between now and then. Feel free to post comments and questions here, though -- I'll address questions when I return.
In content and tone,
this is a surprising article. Subjects of such articles should be given the opportunity to comment - but we were not. We look forward providing clarifying information on our blog at http://www.foursevenfive.com. We also look forward to seeing everyone at Better Buildings by Design this week in Burlington. Please stop by our 475 booth and say hello.
Response to Ken Levenson
Ken,
Green Building Advisor is happy to provide you a forum for comment. You are most welcome to comment on this page, and provide any clarifying information you'd like. We welcome a dialog.
More data on vapor barriers.
I found that following interesting:
http://www.kuleuven.be/bwf/projects/annex41/protected/data/ORNL%20May%202005%20Prese%20A41-T2-US-05-1.pdf
It shows the polyamide vapor barriers (a.k.a. Membrain) opening up to 40 perms in very high humidity environments.
Redundancy
I really think this article is an argument for redundancy - rather than relying on one building component to serve the sole air barrier function, you have a redundant system as a back-up. In other words, you tape the sheathing, tape your weather resistant barrier, and you have an interior air barrier as well. I went crazy in the house we built and made sure that each stud bay was sealed from the others as well.
I think a secondary air barrier on top of the roof is good insurance if you are filling the ceiling rafters with dense pack cellulose. That happened to be the only place we used foam in the house - 2 layers of taped and staggered 1.5 inch polyiso (upstate SC - zone 3).
Response to Ken Levenson
Ken,
I'm grateful that you took the time to post your comments on GBA. This is an important dialog.
I'd like to start by emphasizing our points of agreement:
1. We both agree that monitoring building components -- especially, monitoring the moisture content of sheathing -- is a good idea. When builders and building scientists install monitoring equipment and share their data, everybody gains knowledge.
2. We agree that it's good that "475 recommends vented assemblies." That's an excellent recommendation.
We do have a significant disagreement, however. The disagreement concerns whether 475's recommendations for a "a safe (foam free) unvented roof" are, in fact, safe. Whether one calls these unvented assemblies safe or risky depends on judgment and a builder's appetite for risk.
Hoping to get a perspective on this question from three of the smartest experts in the industry, I interviewed Joseph Lstiburek, John Straube, and Marc Rosenbaum. Their verdict was unanimous: all three called unvented roofs insulated with cellulose between the rafters "risky."
I stand by my story. (After the article was published, John Straube sent me an email in which he called my story "very well done." Marc Rosenbaum also sent an email, noting, "nice job.")
That said, every builder has their own appetite for risk. I know for a fact that some owners and builders have been convinced by 475's arguments and have built this type of unvented roof. That's OK. Everyone's appetite for risk is different.
Response to Kohta Ueno
Kohta,
Thanks for your comments. The details you have provided on Chris Corson's roof clearly demonstrate that this is a code-compliant vented roof -- an assembly that includes the code-mandated ventilation gap above the top of the insulation layer. It's no surprise that this roof assembly has no moisture problems -- and it seems disingenuous to me that Ken Levenson is using this roof as an example of "exactly the assembly the GBA article is focused on."
Contrary to Ken's assertion, I am not concerned with the performance of cellulose-insulated roof assemblies with a vent channel above the insulation. I am concerned about the performance of unvented roof assemblies insulated with cellulose or fiberglass.
The 475 blog has asserted that "while the ProPink Unvented Insulation System may provide a safe roof in zones 2B &3B, if we instead combine dense fiberglass insulation (batts or densepacked) with INTELLO smart vapor retarder and airtight membrane we can make safe and robust unvented roofs in climate zone 6!" [Emphasis added.]
Once the vent channel is eliminated, these roof assemblies become risky.
Response to Ken Levenson
Ken,
As I wrote before, I stand by my story. The story does not include misstatements.
Update on Kohta's comment
I was able to speak with Chris Corson yesterday, where Chris clarified that Kohta is actually mistaken about the assembly for which we were citing data - and that we were correct in our description. We will be adding back the comment regarding the presentation per our initial response based on Chris' confirmation.
Kohta, I kindly ask that you also confirm with Chris and update your comment accordingly. Thanks.
475's Response
475's response is now posted on our website http://www.foursevenfive.com. We ask that corrections be made to this article as our response warrants. Also the response is here (pls go to our website to get all the links):
A regular platform of building science debate is the GreenBuildingAdvisor (GBA) website. We’ve been contributors to GBA and engaged in debate there – always with a seriousness of purpose. So it was with great surprise and frustration that we read Smart Vapor Retarders for Walls and Roofs on GBA. No questions were asked of 475 in preparing the article. The article is full of strawman arguments, unsubstantiated claims, gratuitous personalization and bait & switch tactics.
Data
We have real-world experience and we have data. The Whitchurch Passive House Cottage, in Middlesex Vermont, built by Chris Miksic of Montpelier Construction with Passive House consulting by Indigo Ruth Davis and consulting by Bill Hulstrunk from National Fiber, for owner Greg Whitchurch, is one example of an unvented roof with INTELLO Plus inboard. The project was well suited up with data monitors during construction in 2014 – blogged by 475 here – and we’ve been getting updates. Greg’s readings from Feb 1st 2016, show moisture content at the outer roof sheathing of 8.1%.
Kohta Ueno, a Senior Associate at Building Science Corporation, did a presentation with Chris Corson of Ecocor, at NESEA BE15 – on the exactly the assembly the GBA article is focused on – with real world data: see slides 31-39 of the presentation here (pdf).
The 475 worldview is not divided between computer simulation and actual experience. 475 is committed to using all the tools at our disposal to lift the quality of building, through: writing and trainings, drawings, computer modeling, real-world experience and data collection.
The Vapor Curve
The vapor curve matters. Contrary to what the article would have readers believe, while many materials are vapor permeable the quality of the permeability curve is quite different from material to material. This difference matters. Vapor retarder paint is not close in performance to a smart vapor retarder. MemBrain has a less robust vapor curve than DB+, and a much less robust curve compared to INTELLO Plus.
We’ve careful laid out some of these differences in our blog post Why The Vapor Curve Matters. When Joe Lstiburek is quoted in the GBA article, that the limits of 25% to 35% interior RH in relation to smart membrane effectiveness, he is mistaken. INTELLO Plus works effectively at interior RH levels of 50%. Read the INTELLO Primer.
WUFI
GBA never asked to see the 475 WUFI Pro models. GBA doesn’t know what’s in the WUFI models. Yet the article has further expert opinion telling us what’s in and not in our WUFI models. Strange.
“The 475 Approach”
475 always takes a whole systems approach to making high performance assemblies. While every component is important, how they work together is even more important. As insulation levels grow and expectations of comfort and efficiency rise, assembly drying capacity and reserves are increasingly critical. Experience is a tool. WUFI is a tool. Detailing continuity and training are tools. Blower doors are tools. We use all the tools at our disposal.
Smart vapor retarder, especially INTELLO Plus, can significantly increase drying reserves of assemblies. But contrary to what the GBA article would have readers believe, the addition of INTELLO Plus is not the end of the answer, rather, it is the start. The details must be worked through and the job site execution done properly. Consequently a pencil hole will not endanger the system.
We’ve gained our customer’s trust because we are focused on their specific requirements and solutions. 475 is committed to helping build the highest quality, highest performance, most robust and environmentally sustainable buildings. We’re proud to be part of teams executing some of the most exciting and ground-breaking work across the US and Canada.
Pushing and Push Back
475 recommends vented assemblies. See our blog post A high performance roof should be vented – how to do this properly.
The genesis for developing a safe (foam free) unvented roof came not from marketing research but in working with professionals on flat roof Passive House projects of high insulation levels, where vented roofs would not be effective. (See two in-depth 475 blog posts on this subject here, and here.) This is the case of the Whitchurch project in Vermont.
The other impetus for thinking about making a safe (foam free) unvented roof, was in hearing of home retrofits dominated by the application of toxic spray foam, where installers were looking for a safer viable alternative – like this leading insulation contractor in Massachusetts.
We don’t push products. We do push for more predictably energy efficient buildings, and a less toxic environment. Our North Stars are Passive House and Greenpeace. Both are where some of the the most interesting and meaningful work is getting done on the planet.
Is It About Foam?
We think the spray foam industry’s dominance in construction is a clear victory of chemical giant marketing over good science. (See our blog series Foam Fails.) And we understand foam isn’t going away – some of our products are foam. Our motto is Less is Best.
Onward
475 has big ambitions to help move the enormous US construction industry toward truly sustainable high performance. 475 is happy to challenge convention where we think it falls short, and engage in informed debate. Let’s make better buildings.
correcting
Kohta and Martin,
See my #17 comment below.
Clarifying what's going on here...
Both Kohta Ueno and Chris Corson have promised to post comments here when they get a chance. Until that happens, I'll share what I know. I just got off the phone with Chris Corson. Evidently Kohta's image is an accurate representation of the roof that he monitored. It's a code-compliant vented roof, and it has no moisture problems.
At the conference Ken Levenson mentioned (the 2015 NESEA conference, BuildingEnergy 15), Chris Corson was a co-presenter with Kohta, and Chris reported on data from a different house -- one with an unvented roof assembly. Chris's monitoring shows that his unvented roof assembly is also performing well, with no evidence of moisture problems.
I'm grateful to Kohta and Chris for their monitoring work and their willingness to share data. As I noted in Comment #12, "When builders and building scientists install monitoring equipment and share their data, everybody gains knowledge."
I stand by my assertion that the issue here is a builder's appetite for risk. Unvented roofs insulated with fiberglass or cellulose do not comply with building code requirements, and several building experts -- including John Straube, Joe Lstiburek, and Marc Rosenbaum -- have labeled this approach "risky." It's good to gather and share data on these homes.
Builders are free, of course, to evaluate the data and estimate the risk associated with this type of unvented roof -- and then to choose the specifications for their next roof based on these evaluations and estimates.
Yea, I couldn't agree more with Ken... What are you doing Martin? Talk about attitude. Didn't consult anyone at 475 before blasting them in this article? Not only is that rude, but it makes you personally look bad and your entire organization. Shame.
Araya,
I've known Ken Levenson for years, and in fact have had the pleasure of inviting him into my home in Vermont for a visit. I've called him up on the phone numerous times to get information on his company and to discuss building science issues. We're far from strangers.
The information in this article is accurate. The article is intended to provide a counterpoint to information that Ken Levenson's company was posting on the company's website -- information that was counter to the consensus view expressed by building scientists like Joe Lstiburek, John Straube, and Marc Rosenbaum. In fact, I interviewed those three experts for this article.
I felt no need to offer Ken Levenson "an opportunity to comment" on the article before publication, since the entire intent of the article is to correct ill-advised opinions published by 475 High Performance Building Supply. Like all GBA readers, Ken Levenson has the opportunity to post comments to any GBA article he chooses to respond to; and in fact, Ken Levenson did so in this case.
I stand by the article. Research conducted since this article was published further confirms my expressed conclusions. The new data undermine the validity of Ken Levenson's advice. For more information on the new data, see "Filling Rafter Bays With Fluffy Insulation."
Thanks for your comments Martin. My frustration is with the way this was approached and to read from ken in his initial comment that
"A regular platform of building science debate is the GreenBuildingAdvisor (GBA) website. We’ve been contributors to GBA and engaged in debate there – always with a seriousness of purpose. So it was with great surprise and frustration that we read Smart Vapor Retarders for Walls and Roofs on GBA. No questions were asked of 475 in preparing the article. The article is full of strawman arguments, unsubstantiated claims, gratuitous personalization and bait & switch tactics."
I'm just saying, I personally think this could have been approached in a much better way, that didn't make you personally or GBA look bad. Glad it's settled now though. Take care.
Isn't this all water under the bridge? This exchange was five years ago.
The comment you are replying to is calm, careful, and factual, and emphasizes being open minded and paying attention to both data and experts. In reply, you complain about "attitude", call it "blasting" and "rude" and conclude that shame is warranted? I'm having trouble understanding the basis for your comment.
Having trouble? I think you could find clarity by re reading the comments section here. Specifically, comment #15 by ken. Regardless of how Martin feels about all of this, or if he's friends with Ken or not, this blog post calls out a well known reputable company and saying that he disagrees with their advice publically. That's totally fine to disagree, obviously, I just really don't appreciate the way it was approached and Ken also clearly points that out - how the approach could have been done in a much better way and done more respectfully as seen in the public eye. First contacting 475 to seek clarification before making this kind of blog post would have been a great idea and a way to show respect to 475, ken points out, that was not done. Ken clearly points that out in his reply to this thread. I'm not sure what you're confused about? I just think this could have been approached in a much better way in 475's interest.
Araya,
You may be right that this article did not serve the interests of 475. However, I was aiming to serve the interests of GBA readers rather than the interests of 475.
Clarification on Chris Corson's Roof
This comment is superseded by information below; left here for reference.
I just want to make sure we're not talking past each other on this discussion, by making sure everybody understood all the layers of Chris Corson's roof (the one pointed out with low MCs). See the figure below, but to break it down, from exterior to interior:
Galvalume Roofing
2x4 24" o.c. (laterally across roof)
1x3 strapping 24" o.c. (vertically up roof
Proclima Solitex Plus (38 perms)
16" TJIs @ 24" o.c., with dense pack cellulose
OSB sheathing (air barrier)
2x10 24" o.c., with dense pack cellulose
1x3 interior strapping (laterally across 2x10s)
Interior GWB
This is, no doubt, a seriously beautiful, moisture safe roof with boatloads of outward drying. It relies on a system of battens and counterbattens to create a ventilated cavity. Ventilation through this cavity bypasses the low permeance roofing materials (metal roofing in this case). I was not surprised that Chris had consistently nice and low moisture contents--the small amount of moisture that got into the system (air leakage or diffusion through the OSB air barrier) could zip right out through the 38 perm exterior membrane.
However, this isn't how the construction industry is building unvented roofs, as much as we would like them to. Instead, the assemblies typically involve an exterior made of asphalt shingles, roofing felt/paper, and structural sheathing (OSB or plywood)--a "sandwich" that has essentially no outward drying. This is why the folks cited above consider relying on an interior membrane (in combination with fibrous insulation) to be a risky strategy.
This is part of the reason for BSC's research on diffusion vents--assuming this limited outward drying roof assembly, the diffusion vent will allow some minimal vapor diffusion drying at the ridge (where moisture accumulates). Doing this in combination with interior air and vapor control is probably a very workable solution--we are pushing research on this now. But for now--here is information on the work to date.
BSI-088: Venting Vapor
http://buildingscience.com/documents/insights/bsi-088-venting-vapor
BA-1409: Field Testing Unvented Roofs with Asphalt Shingles in Cold and Hot-Humid Climates
http://buildingscience.com/documents/building-america-reports/ba-1409-field-testing-unvented-roofs-asphalt-shingles-cold-and
BA-1511: Field Testing of an Unvented Roof with Fibrous Insulation, Tiles, and Vapor Diffusion Venting
http://buildingscience.com/documents/building-america-reports/ba-1511-field-testing-unvented-roof-fibrous-insulation-tiles-and
More Information from Chris Corson
I corresponded with Chris, and he verified the construction of his monitored hot (unvented) roof assembly--he mentioned two assemblies, and provided the image below:
Roof 1:
GWB
1x3 battens
Intello plus
16 in dense packed I joist
5/8 ZIP
EPDM
Floating Ipe deck tiles with built in drainage plane
Roof 2:
GWB
Intello plus
14 " dense packed I joist
3/4 AdvanTech
Grace Ice and Water HT
Standing seam galvalume roof nailed through the sheathing
He points out that he prefers the vented roof assembly discussed above--but sometimes he gets backed into a corner by circumstances.
The data he logged is shown in the other image. The roof is showing nice low wintertime MCs at the outermost (sheathing) sensor--peaking at 10-14%, or a very safe range.
He explains the circumstances of the ~20% MC spike in the first summer of operation, at the innermost sensor:
[KU editorializing] and of course the inward solar/temperature gradient--i.e., any stored moisture is blown out of the outer sheathing, and pushed inward.
Just to clarify--I don't think that anyone's saying that unvented roofs with a variable-permeance interior membrane can't work. It's clear that awesome practitioners like Chris... or other PassivHaus folks... or other folks who can pull off 1 ACH 50 regularly are likely to make this type of assembly work, assuming interior RHs don't get out of control. But I'd definitely be concerned releasing this assembly on the general construction market... i.e., the folks who are complaining about that newfangled code-required blower door 7 ACH 50 test. :)
Response to Kohta Ueno
Kohta,
Thanks very much for the further details. I agree with your assessment that Chris is an "awesome practitioner." He makes careful density calculations, figuring out the weight of the cellulose and the volume being filled, to ensure that enough cellulose is installed. He is also aware that very deep cavities (as are found in some double-stud walls) require cellulose to be installed at 4 pounds per cubic foot instead of 3 pounds per cubic foot. He often insulates wall and floor assemblies as panels that are manufactured indoors (in a manufacturing facility) before being transported to the job site. Finally, his quality control process includes the use of infrared cameras and opening up assemblies to check whether settling has occurred.
Chris Corson is unusual, and practices that work for Chris probably can't be generalized. Just this week, a homeowner posted a question on GBA, noting that he has had three cellulose insulation contractors visit his house, and only one of the three contractors knew what "dense-packing" is. The contractor who said he could dense pack a cathedral ceiling told the homeowner that flimsy polystyrene ventilation baffles are just fine -- they'll be able to resist the pressure of dense packing. This level of knowledge is, sadly, typical in much of the U.S.
How would the suggested substitute of rockwool on the roof deck work instead of foam when rockwool is vapor permeable and the foam boards are not?
David,
It's possible to install a continuous layer of semi-rigid mineral wool on the exterior side of roof sheathing, in the same way that rigid foam is sometimes installed in the same location. For most types of roofing, the vapor permeance of this continuous insulation is irrelevant, because there is no outward drying for most roof assemblies. (Asphalt shingles and metal roofing are vapor barriers, so these types of roofing prevent outward drying.)
If you are planning to install a vapor-permeable roofing like cedar shingles or concrete roofing tiles, then it's possible to design a roof assembly to dry to the exterior. But there are risks to this approach. If your roof assembly depends on outward drying to avoid moisture problems, then the roof assembly will fail if a future owner replaces the existing cedar shingles with a vapor-impermeable roofing material like asphalt shingles.
We are trying to finalize our deck over conditioned space assembly (low-slope unvented roof) where we will have a continuous layer of exterior insulation but not sufficient space to achieve the requisite exterior insulation “ratio rules” to completely avoid the risk of condensation for Climate Zone 6.
As shown in the enclosed drawing, our plan was to install tapered exterior insulation over our Advantech sheathing and install rockwool batts (r46) beneath the sheathing. We would apply a Zip protection board and EPDM over the exterior insulation. Because we’re using tapered insulation to achieve the desired pitch of the roof, a portion of the exterior insulation will only be 1 1/2″ thick (and up to 6 1/2″ thick). The exterior insulation on the low side of the roof will be far less than what is required to achieve the “ratio rules” for our climate.
We were considering have been considering the following options in order to modestly adapt our plans and yet lower the risk of condensation, but have concerns with both approaches. What are your thoughts?
1) Install rigid above AND closed-cell foam beneath the sheathing? That prevents warm interior air from getting trapped next to the sheathing but would also mean that we have no way for the system to dry out if there is a leak since we have EPDM on top of the rigid foam.
2) Install rigid above AND rockwool batts beneath the sheathing, with a smart vapor retarder on the interior side of the batts to limit vapor drive but still permit the wall to dry out on the interior side. If we go with this approach, what installation details/considerations must we be mindful of to ensure we’re using the membrane effectively?
Aspen,
Option 1 is the way to go. To reduce your worries about sandwiching the sheathing between rigid foam and closed-cell spray foam, read this article: "Sandwiching Roof Sheathing Between Two Impermeable Layers."
Thank you!
Log in or become a member to post a comment.
Sign up Log in