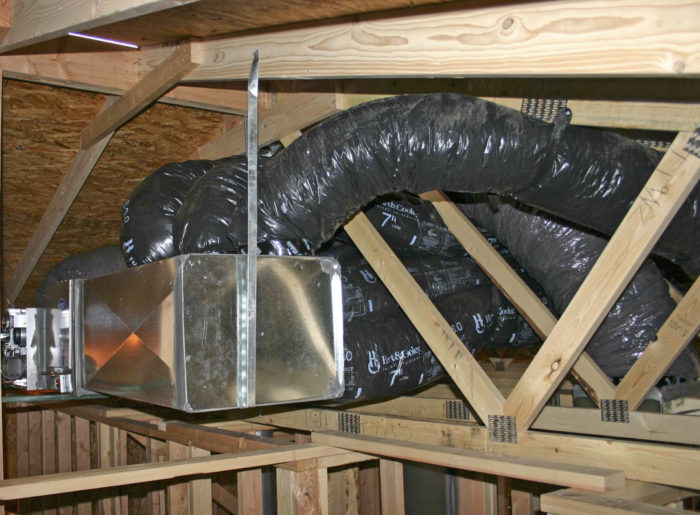
Image Credit: Image #1: Christopher Fuller - GBA
In last week’s blog, I discussed the practice of burying attic ducts in deep insulation. Since burying ducts is simply one of several ways to address the energy waste associated with the decision to locate ducts in a vented unconditioned attic, it’s worth taking a fresh look at all of the possible solutions to the attic duct problem.
Energy experts have been advising builders for at least thirty years that it’s a bad idea to locate ducts in vented unconditioned attics, yet the practice persists. Why? Building scientist Joe Lstiburek blames the problem on architects and builders, and he’s partly right. But it’s also fair to blame regulators, most of whom are too timid to approve code changes that would make the practice illegal.
According to NREL researchers David Roberts and Jon Winkler, moving the ducts from a vented attic to a new location inside the conditioned space will reduce electricity used for cooling by 15% to 20%, and will reduce the size of the needed air conditioning equipment by 0.5 to 1 ton.
In this article, I’ll look at a variety of solutions to the attic duct problem — a topic that I first tackled seven years ago in an article titled Keeping Ducts Indoors. The presumed reader is a designer or builder who wants to know the best way to avoid the energy penalties associated with attic ductwork.
In my 2011 article, I listed five possible solutions to this problem:
In this article, I’ll also discuss…
Weekly Newsletter
Get building science and energy efficiency advice, plus special offers, in your inbox.
This article is only available to GBA Prime Members
Sign up for a free trial and get instant access to this article as well as GBA’s complete library of premium articles and construction details.
Start Free TrialAlready a member? Log in
14 Comments
Why does the soffit or plenum approach require airtight ceilings? Is it so that the plenum/soffit doesn't become a channel that supplies air to a fire? or some other reason?
User 7073758,
First of all, can you tell us your name? (I'm Martin.)
There are several reasons why a ceiling should be airtight. The main reason has nothing to do with whether there is a soffit with ducts in it. Ceilings should be airtight because you don't want conditioned air from inside your house to leak into your attic or the great outdoors. (All of your building envelope should be airtight -- that means your ceiling, your walls, and your floor.)
If you have a soffit with ducts in it, and there is a small duct leak due to imperfect mastic at a duct seam, the entire soffit can become pressurized. If there are any tiny leaks in the home's thermal envelope -- for example, rim joist leaks or ceiling leaks -- the pressurized soffit will assure that lots of air escapes through a small hole in the thermal envelope. Everything needs to be airtight -- the parts of the soffit that represent the home's air barrier, as well as the duct seams.
To Martin Holladay and GBA readers: We recently completed a down-to-the-studs remodel of a 1950s era home in Massachusetts. This project highlighted another key factor: If you upgrade insulation for the entire house, the overall size of the HVAC / heating system can be reduced -- often significantly. Fewer duct runs may be needed, with smaller diameters and fewer registers. We wrapped this house with 2" thick XPS (carefully air sealed), sealed and filled all of the stud bays, and flash 'n batted the roof joist bays plus a final layer of polyiso foam board. Result? I ran ducts through all of the floor/ceiling joist bays, with just one supply/return per room. The furnace and HVAC condenser were 60% of the size the contractor recommended. (Yep, I did a Manual J and he did not.) In summary, upgrading insulation and air sealing in general is always a good idea -- that can help with other challenges, e.g. HVAC and heating systems. Plus you win-win-win with recurring heating / cooling costs every year, which keep going up-up-up.
Two more notes: (1) This house was built shortly after WW2, probably by the returning GI who bought the land. He built it with 'radiating' joists, generally centered around the chimney. This made it much easier to run ducts from a central 'engine room' in the basement. Architects and builders should consider this. Provide a path for ducts; it won't cost much more. (2) I know that Mr. Holladay is opposed to foam board for good reasons. That said, and with remodels in particular, foam board is often the best / only solution. We are not working with deep walls, and customers have thinner wallets. Fortunately, Owens Corning responded to pressure and picked a new 'blowing agent' in 2012 that sharply reduced the GWP (Global Warming Potential) for Foamular XPS. OC also created a complete environmental report for this product -- which covers materials, manufacturing, transportation, etc. costs. So kudos to experts like Mr. Halladay; your critiques changed corporate behavior. (And polyiso is better when cold temps are not a issue.)
I hope this is helpful,
Mark
Mark,
Congratulations on your house. I'm glad to hear of your success story.
While Owens Corning XPS may have a blowing agent that is less harmful to the ozone layer than the blowing agents used 30 years ago, before the Montreal Protocol kicked in, I don't think that Owens Corning has yet address the problem of the global warming potential of the blowing agent used in their XPS. If it's advertised as having an R-value of R-5 per inch, it's the bad stuff.
In general, I'm not against the use of rigid foam. I just steer green builders toward EPS or polyiso, rather than XPS. For more information on this issue, see "Choosing Rigid Foam."
We have insulated 5 or 6 attics in the following manor:
Rafter vents
Fiberglass or Roxul between the rafters
2” R-Max Polyiso with a white vinyl faced finish, all seams and screw heads taped with R-Max white tape.
The 2” R-Max is not cheap but the home owners love the white sterile looking environment of their attic and no longer fear going up there to store things or change the filter on their air handler.
We buy the R-Max and special screws and washers from IDI which has several locations around New England.
I like this system better than spray foam as it requires no special equipment like a spray rig, can be installed by our employees and is easy to remove and put back if some kind of repair is needed in the future as opposed to a hatchet to chop out the closed cell foam.
It looks a lot nicer than spray foam.
It creates a thermal break across the rafters that closed cell job does not, unless you spray really deep and therefore costly.
Its labor intensive but still comes in less costly than closed cell equivalent, least in my area with our own labor it does (Norwalk CT).
As a remodeling contractor I like it because it is something my guys can do, keeping us on site while the subs are doing their work in the main house below, or on the day when we are waiting for the building inspector to show up....or not show up even when they are scheduled.....any body else have this experience with building inspectors?
Judson,
Rmax makes at least six kinds of polyiso for residential use, so any GBA readers interested in your approach have to be careful. As far as I know, only one of these products -- Rmax Thermasheath XP -- can be left exposed. (Building codes usually require rigid foam to be protected by 1/2-inch gypsum wallboard, which acts as a so-called "thermal barrier" to protect the rigid foam from the risk of fire.)
Rmax Thermasheath XP has a special facing that has passed tests that allow it to remain exposed when installed on an interior surface.
Martin-
The Rmax Thermasheath XP is what we have been using because it can be left exposed and with the white vinyl side facing out it gives a fairly good finished look.
- Jud
Dear Martin: I agree that polyiso foam board is the best solution for all INDOOR insulation, where the temperatures are above 40 degrees and there (should be) no threat of water infiltration. For EXTERNAL applications, however, XPS or EPS are the best options. (1) Polyiso insulation performance drops along with the temperature (e.g. on external applications where winter temperatures are a key concern), and (2) Polyiso absorbs water and moisture like a sponge; XPS and EPS do not. Should anyone install polyiso foam board under a concrete slab? Of course not. The same applies to external 'wrap the house' and external roof applications with polyiso.
For the total environmental impact of Owens Corning XPS see: https://dcpd6wotaa0mb.cloudfront.net/mdms/dms/Shared/10018928/10018928-EPD-Transparency-Brief---FOAMULAR-Insulation.pdf?v=1551285771000
Note: I have no affiliation with Owens Corning, except as a retail / pro customer. I have received no renumeration from Owens Corning. I also recommend polyiso for internal applications, so this post is not based on bias.
Mark Hays
Mark,
Polyiso is routinely used on the exterior of walls and roofs, where it is unlikely to get soaked. You're correct, of course, that polyiso shouldn't be used under slabs; EPS would be the best choice there.
It's true that the insulating performance of polyiso decreases in cold weather; however, that fact doesn't mean that green builders shouldn't use polyiso. For more information, see "Cold-Weather Performance of Polyisocyanurate."
XPS should be avoided by green builders because the blowing agent has a high global warming potential. For more information on this issue, see these articles:
"Choosing Rigid Foam"
"Calculating the Global Warming Impact of Insulation"
The Owens Corning document on Foamular, a brand of XPS, that you linked to, uses misleading examples in its environmental assessment of blowing agent releases. After providing the theoretical justification for its analysis of the effect of blowing agent releases, the document notes, "When properly installed, due to the savings it affords in an otherwise non-insulated building, the energy resource impact from the life cycle of insulation has a payback period of 0.7 to 1.2 years." In other words, it compares the energy use by steel-stud or cinderblock buildings that are uninsulated -- an illegal option -- with the energy use of a building using only Foamular. In the real world, that's rarely the way Foamular is used; it is usually used to wrap a building that has at least some fluffy insulation between the studs -- which changes everything in the calculations, to the detriment of Foamular.
Dear Martin: I agree that the >1,000 GWP of the blowing agent used by Owens Corning is a significant downside for Foamular. Apparently Owens Corning is responding to the pressure brought by you and others; they published a report highlighting a planned transition to a low GWP blowing agent for XPS factories in the USA and Asia., apparently scheduled for January 2021. I contacted Owens Corning to see if this initiative is still on track, and will let you know if they respond. You may want to contact them as well.
The water absroption problem with polyiso foam board is significant for external applications.. If polyiso foam board is very carefully sealed -- and unexpected water leaks never occur -- it works well. If any water is absorbed by the polyiso, however, this significantly decreases insulation performance and can encourage rot in adjoining sheathing and framing. There are many penetrations and flashing details in roofing applications, for example, where mistakes can occur. This makes polyiso a better solution for interior locations, where water leaks are less common and temperatures are higher.
Hopefully Owens Corning will join companies in Europe that have switched to low GWP blowing agents.
Dear Martin: Here is a copy of the reply I just received from a tech program manager at Owens Corning:
Chase Boudreaux
Technical Program Leader
"Today OC foam products GWP is approximately 750. Competitors products are around 1300. In Canada we are on track to launch products with a GWP < 150. In the US it’s more complicated but we are prepared to meet whatever rule or law set forth by the EPA or states."
Needless to say, it is disappointing that OC has the technology to significantly reduce the GWP in their Foamular blowing agent -- but is choosing not to make the switch in the US market. This could be an opportunity for action at the state level, e.g. in California and Massachusetts -- where there is more recognition of Global Warming. Action by two significant states would probably tip the balance for OC.
Mark,
Like you, I find it disappointing that U.S. manufacturers of XPS use a blowing agent with a much higher global warming potential (GWP) than European manufacturers of XPS. I've heard that U.S. manufacturers are worried that the more environmentally friendly blowing agent results in rigid foam with a somewhat lower R-value per inch than XPS manufactured with the environmentally destructive blowing agent.
Because XPS manufacturers are worried about loss of market share, the climate is being put at greater risk.
For green builders in the U.S., though, the choice is simple: specify EPS or polyiso, not XPS.
By far the two best solutions are to 1. create a conditioned unvented attic, or 2. use a ductless minisplit system. All the other solutions would result in awkward construction and maintenance. I especially cringe at the option to bury the ducts in insulation. That would make it extremely difficult to do future home re-wiring, plumbing, duct work etc. if you have to dig inside the insulation to figure out where wires are going and to lay new wires etc.
ddbear,
I'm not sure the good options are as circumscribed as that. Equipment can be located in crawlspaces, mechanical rooms or basements. Ducts can run in plenum trusses, bulkheads, dropped ceilings, service cavities, or if it works with the architecture can be left exposed.
I think we can learn a lot from Industrial and commercial buildings, which have a huge head start in how to efficiently handle mechanical systems, using a variety of strategies and locations.
Log in or become a member to post a comment.
Sign up Log in