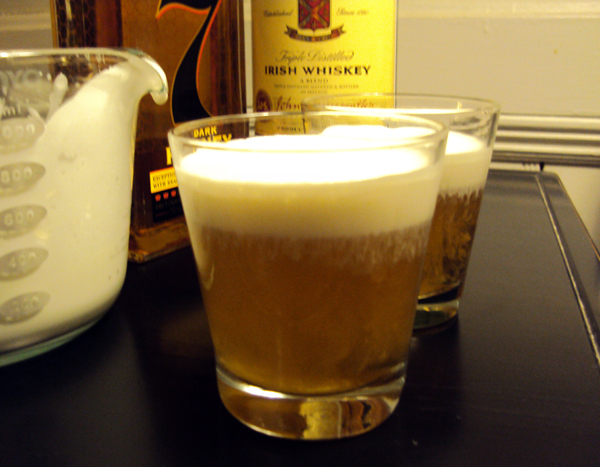
*1 1/2 oz. Irish Whiskey
*1 1/2 oz. Segrams Seven Dark Honey
Shake with ice, serve in a chilled glass, float thin layer of half whipped cream
*1 1/2 oz. Irish Whiskey
*1 1/2 oz. Segrams Seven Dark Honey
Shake with ice, serve in a chilled glass, float thin layer of half whipped cream
Image Credit: Inconvenient Truth Beddington Zero Energy Development is the UK’s largest mixed use sustainable community. It was designed to create a thriving community in which ordinary people could enjoy a high quality of life, while living within their fair share of the Earth’s resources.
Image Credit: BedZed Modern Beach House - Truro, MA from Zero Energy Design
Image Credit: Zero Energy Design Contours0 - One of Michelle Kaufman's Zero Series home models
Image Credit: Michelle Kaufman Studio BrightBuilt Barn - Our own Phil Kaplan's work.
Image Credit: Kaplan Thompson Architects
You can also subscribe to the Green Architects’ Lounge on iTunes. That way, you’ll never miss a show—and it’s free.
In part one of this episode, Phil and I chat about the mega trend that is Net Zero housing. We introduce the concept, and talk about why green architects all seem to be headed in this direction. And of course, we share a cocktail recipe, and of course we offend another culture / ethnicity with our terrible accents and cartoonish caricatures. (My apologies Brian O’Hanlon, I owe you a beer!)
Also, Jesse crawls out from under the crawlspace and returns to the podcast in his usual role as the intelligent yet often grumpy architect for the segment we call, “What’s bothering Jesse?” Today, it’s lumberyards.
In Part 1 of this episode, we discuss:
Phil and I would love to hear from you. If you have a great idea for an upcoming topic, want to leave general feedback, or want to share your favorite cocktail recipe, you can e-mail us at [email protected]. If you’d like to complain about our tangential ramblings, fragment sentences, or our general irreverence, you can email us at [email protected].
- What Does “net zero” mean?
- Why do we care?
- Who’s out there building this stuff?
- What’s up with lumberyards?!
Be sure to check back in for Parts 2 and 3, in which we talk about how you get to net zero and how the economics are actually starting to favor this approach.
Cheers!
TRANSCRIPT
Chris: Welcome to the Green Architect’s Lounge podcast. I’m your host, Chris Briley.
Phil: And I’m your host, Phil Kaplan. And today we’re going to talk about Net Zero: the challenge and fun of getting there.
Chris: It’s about time. We’ve been gearing up for this. We just did Passivhaus, and this is the next thing. Now that the energy demand is down low, maybe it’s possible to live on this planet, from an energy standpoint, consuming as much as you make. As in, you have net zero consumption, which is what the term means.
Phil: Essentially, it’s just producing as much energy as you consume over the course of a year. That “over the course of a year” is very important, because in wintertime in Maine we use a lot of energy, but in summertime in Maine we’re going to make a lot of energy. It has to be net zero, not zero across the board.
Chris: So are there renewables involved?
Phil: Absolutely. You have to do it with renewables. Before we dig into it, I want to hear about this tasty drink you made us.
Chris: This drink used to be called the Dubliner, but instead we’re calling this the Irish-American. It’s equal parts Jamison Irish whiskey and Seagram’s 7 Dark Honey. Put it in a cocktail shaker with ice, whip up some whipping cream and float it on top.
So let’s talk about green architecture.
Phil: Tell me again what net zero is? Producing as much as you consume over the course of the year. So why do we care?
Chris: Because we’re people that want to tread lightly on this planet.
Phil: The CO2 levels are why we’re bringing in net zero. We’re nearing almost 400 parts per million or so. We’re trying to get back to 350. Which is about where we were in the ’90s. We’ve been off the charts since then. We just have to kick it back a little bit.
Chris: We need to try to minimize our consumption. Oil is going to run out. Our kids are going to be dealing with the fact that cheap oil will be gone. Every house we design, if we did a good job and it’s still around when we’re dead and gone, will be renovated, with a different mechanical system than what we’re using now. Especially if the house is burning fossil fuel. There’s a chance that houses will still be burning electricity, but the electricity is going to be made differently.
Phil: It’s true. Let me get on my soapbox for just a minute. If you’re an architect and your client is paying you $10,000 or $20,000, and in five years that house is obsolete, you’re being irresponsible to your clients.
Chris: That’s right. The big vinyl-sided McMansions that are 5,000 square feet and use $5,000 worth of oil a year are going to be massive white elephants on the market. They’re going to get split up and renovated, and they’re going to be the slums.
Phil: Buildings worldwide account for 40% of our primary energy use, and 24% of all greenhouse gas emissions. Well, we’re responsible for buildings. People listening to this podcast — architects, builders, engineers, contractors, mechanical guys, and vendors — wWe can change the world right here. That’s why net zero matters.
Chris: You’re “first chair” in this podcast because you’ve summitted. You’ve done it. You’ve got your own net zero project.
Phil: Yeah. BrightBuilt Barn was our first net zero.
Chris: Phil is an awesome guy. It’s a charming little studio building that has a “light skirt” that lets you know when it’s consuming and when it’s saving. You’ve done this before, which is why you’re qualified to sit here. I’ve come close.
Phil: You have come close. The Redford house you did could be net zero. Chris did this really good-looking structure in Portland, Maine.
Chris: The goal was to be LEED Platinum. In town. It was on the market playing against everybody else in the worst housing climate ever. It sold in a month — proof that it can be done. It’s not net zero, but it could be, with a little work.
Phil: Net-zero-ready is in some ways just as good as net zero. You get everything ready and wait for the renewable prices to come down. That counts in my book.
Chris: That counts in my book. It’s kind of like where Passivhaus is going. It’s all about energy demand. Plugging in renewables isn’t part of the equation. We’re going to reduce that demand and whatever is left, we’re going to take care of on site, and that makes us net zero.
Phil: Michelle Kaufmann has a neat line called Zero Series homes. I’m going to step back slightly before we take a break. I gave a talk last year at the AIA convention at Custom Residential Architect Network in Austin. I met some great people. John Connell, who founded Yestermorrow, a cool guy, has done some wonderful modular low-energy stuff. Dale Mulfinger was there — he gave a nice talk. I had a chance to chat with Bill Aylor, one of the principles at Lake Flato. People are doing it. People from all over the country are getting involved with net zero.
Chris: Unlike Passivhaus. Instead of this being one-directional thing from Europe, net zero seems to be more amoebic — popping up everywhere at once.
Chris: I don’t know if you want to do it now, but it has been a while since Jesse vented with us. Since we’re on our own at GBA, do you want to bring him in?
Phil: I’d love to hear what he is going to say today. Sheila, let’s bring in Jesse.
Musical interlude
Chris: Welcome back, everybody. He hasn’t been with us in a long time: here’s Jesse Thompson of Kaplan Thompson Architects. How are you, Jesse?
Jesse: I’m all right.
Chris: Everyone’s missed you. So tell us, what has been bothering you?
Jesse: Lumberyards. I’m an architect, and I’ve been pretending to be a general contractor for a little while. It’s been sort of shocking how unbelievably amateurish and badly organized lumberyards are. They don’t have systems. There’s a guy on a phone. The way it seems to work with my salesman is that I call him up and if I’m lucky he’s there, but maybe not. If he’s not there he calls me back a little while later and I tell him what I want over the phone, and he seems to write it down and maybe it shows up. If I want to know how much something costs, I call him up and then maybe he gets back to me. Maybe he gets back to me in an hour, maybe six hours, or maybe a day. And then I learn what that thing costs. But if the thing is too expensive I have to find out how much another thing costs. Meanwhile I’ve burned off a day — I don’t know how long.
Chris: And you’re thinking, where is the website I can browse and choose it?
Jesse: Yeah, I kind of know why they do it. There’s a salesman and he’s trying to sell me things and he probably gets a commission off how much he sells. But it’s crazy. It’s so crazy. Especially because I have to think that most small-time contractors order everything at night and they’re doing their costing at night. They’d love to know how much a 2 x 4 is today. Why can’t you enter your discount code, and find out what your price is online? This sounds simple — this sounds like 1994 Internet.
Chris: You didn’t wear you’re “I’m an architect” T-shirt?
Jesse: There’s no question my orders are small and they don’t care about me. But they shouldn’t have to. If you want to give me a 5% discount, that’s great, but let me know how much things cost. The possible number of errors is mind-boggling. I e-mail the guy, but I’m still at the mercy of how much he cares about me to find out how much things costs. So I’m the small guy, and I don’t get great service. But what about big-timers doing three to five houses at once? Does it work the same way for them? Is everything so expensive because it’s too hard to figure out how much everything costs? I’d like to think that in San Jose, California, there are all these fancy Internet lumberyards, but I don’t know. As an architect I’ve spent my career listening to people complain that architects don’t know what things cost. It turns out contractors don’t know either. It’s too hard to find out, because the lumberyards don’t want them to know. I shouldn’t have to ask what a 2×4 costs. Make it easy for us.
Phil: Good stuff.
Chris: Yeah, thanks for dropping by. Always a pleasure.
Weekly Newsletter
Get building science and energy efficiency advice, plus special offers, in your inbox.
7 Comments
Net Zero Energy Homes Part 1 - Slapstick Comedy
BFD! No one said you couldn't attain NZE. So what??
Now show us how to make it affordable for the couple with 2 kids still trying to get by on $30K/year..!!??
To Tom
Two kids on $30k/yr is tight to say the least. I'm going to reread your comment as something like, "Hey guys, why don't you do a podcast on making green affordable?! Like, what are your top ten tricks or strategies?! I'm looking for bang for the buck, not pie in the sky!"
Great idea, Tom! We'll put that on the list and make it happen.
Chris Briley, Architect
It would be great to hear
It would be great to hear about how much green you recommend to clients who aren't interested in green for it's own sake, and how you justify it. How efficient can you make a home without adding more than 10% to the cost?
Hi all
I'm just playing catch up here. I've been off the green building radar and out of the radius of all things construction for the last three months, as I was busy doing some dissertation work into forms of contracts and so forth. I'm looking at some Design Build texts from the north American side of Atlantic. It all has to be translated back into European-speak however, though, because of your difference in approach to cost planning, tendering, contractor involvement etc. I think over in North America, you may have an ecosystem of 'Design Builders' already. Something which is only just starting from scratch on this side of the Atlantic - like so much of the procurement systems for construction from America, there is a twenty or thirty year lag, over here. But eventually, we get there.
I'm downloading the latest couple of Net Zero energy podcasts now.
One interesting researcher, whose work you might find interesting is that of Victoria Stodden. I haven't had time yet to take a look at GBA's series of articles on Wolfgang and whatever the latest debacle there is, in the area of energy building simulation. But there is a much, much wider conversation happening at the moment in relation to climate simulation, and scientific method. Ms. Stodden spoke at the iSchool in Berkeley and you can listen to the podcast here, and also download the slides.
http://www.ischool.berkeley.edu/newsandevents/events/20100505deanslec
I also recommend this short Wired magazine article by editor Chris Anderson from a few years ago. It was referenced in one of Ms. Stodden's slide collections. It is a short summary, for those who may not be able to listen to the podcast above.
http://www.wired.com/science/discoveries/magazine/16-07/pb_theory#
I took another look into latest BIM software this summer, and the various computers that people are running the stuff on these days. A lot has changed since I did heavy computer aided design lifting with a computer - and I needed to bring myself back up to speed. Running a new multi-core desktop these days, between doing dissertation work - and may get back into some proper architectural work again in next few years.
One thing I will say though about all of this. If one has a sweet tooth for fancy technology and digital tools, it is very hard to keep a focus on the construction, design and management side of the equation at the same time. I had pencilled in a couple of things for the recent few months, to accomplish. To look at some recent detailing for green buildings, and articles I had on file about construction methods. It never happened. Once my focus changed towards 'nuts and bolts' high tech matters, all appetite to stay focussed on better building details etc, just vanished.
I subscribed to a Bonnie Biafore Microsoft Project online course, and her latest book on the software. That is coming into the Design Build contract management study now in a big way. Although, I'm still a distant ways from attaining any competence in the tool. Ms. Biafore has a long, long career is digital tools, going back to the earliest computer aided design days of GDS. I am sure, she would be an interesting person to interview at some stage, for GBA web site, on general construction management tips and techniques.
All the best, BOH.
-
Worst Irish accent ever
For reference purposes, I think that honour of worst Irish accent ever, must go to Bob Cringely (author of some great books about Silicon Valley and its pioneers), in his interview with famous book publisher, Tim O'Reilly. You can listen to it, at the start of the fifth podcast on the PBS Nerd TV archives here. When some of us Irish guys have too much whiskey some times, we play the start of this podcast, and it never fails to have us in stitches. Bob Cringely is a super guy though, and I guess, to know him is to love him.
http://www.pbs.org/cringely/nerdtv/shows/
Self Build Projects
I scribbled this blog entry on the subject of cooling design in computer systems during the summer months. I think it may convey some of the wishful thinking that self-build computer nerds such as myself may do, when comparing the components I have at my disposal, to the integration that is possible inside of a large vendor such as Apple.
http://designcomment.blogspot.com/2011/07/cooling-design.html
Again, it raises a question, if an integrated company should be able to deliver a high performance home, with a decent profit margin, a lot easier than self-designed, self-built providers do?
On Lumber Yards
I listened to this podcast yesterday evening. On the subject of the lumber yards, by amazing chance I got to using internet quite a bit on my mobile phone this past summer, and did order quite a few spare parts, components and what not, as part of my new multi-core computer self-build I carried out. I just found the mobile phone very handy to let the orders out, once I had made up my mind. That is, I had many orders pre-set up using a full computer system - in the queue - and waiting my instruction via the mobile phone. All I had to do using the mobile phone was press a few buttons, and the chosen orders would go into processing with the web vendor. I found the system very efficient I must say. I could envisage a day shortly, when the construction industry operates like this. I mean, a self-build computer system is pretty modular at this stage. But still, there are decisions that hang in the balance until pretty late in the process. I could envisage a day shortly, when much of the ordering is pre-set up by someone using a BIM software, linked to suppliers, and the man on site, merely hits the order on his mobile device when it is time for the delivery to site.
I think, that was the most useful thing about the mobile phone ordering system. I could stagger the payments and also the times, when I was ready to receive new shipments of parts. That is, I didn't get a whole lot of stuff together, and figure out something wasn't compatible. I ordered the basics first. Got an idea of how it was working, and then made other choices based on the initial order of components I had received, and how they worked out.
Obviously, self-building a modular type computer system is different from building a once-off architectural project. I scribbled down a long 'rant' about mobile phones and procurement for the construction industry, which I may get around to cleaning up at some stage, and present here at GBA in the form of a comment. It was one of the professors in my building school here locally, who did a class last year about procurement systems. He showed us a couple of systems, whereby a contractor can 'lock in' prices for materials and supplies for an entire year. Of course, that locks you in to a specific channel for getting your goods too. But the thing it avoided he said, was the dreaded foreman on site, with the paper ordering book. It is basically a check book. You may have several foreman running around projects, and they are all paper based with no information much about what is being ordered, what is being paid for. It is very hard to understand cashflows and material flows on projects, when that is the case. At least with the other systems he showed us, the Contractor is able to manage their in-goings and out-goings better.
I think that building high performance green homes, may share commonalities with building high performance computer systems. You tend to jump around suppliers a lot, in order to receive best bang for the buck, and best of breed components. You know the way, the project doesn't quite fit the budget and you have to perform some re-configuration, to make it work. If an existing construction materials supplier set themselves up, such that, they added a new supply channel for the harder-to-source, specialist, higher performance components, then economics might do it's thing, and become efficient after a while. I remember trying to procure a good chassis enclosure to self-build a high performance computer system a decade ago. The market was full of awful stuff that flooded the market. The good chassis to build a computer was a rare item. Good power supplies hadn't been invented yet. At lot of anxiety and a lot of compromising took place. We used to saw holes bigger with hack saws, and replace fans with better fans, to try and make it work. Some crazy stuff went on.
But ten years on, the bargaining power has now swung the other direction, and the computer self-builder (even a small one like myself), has an awesome choice of products, and awesome efficiency in prompt delivery, online ordering etc, etc. You can get everything you need at an awesomely lower price point too. Which means you have more budget free, for things that really matter. My recent self-build, was the first self-build computer I did in a decade. It was all working out so flawlessly, I felt like asking, what's the catch here. It couldn't be this easy.
Log in or create an account to post a comment.
Sign up Log in