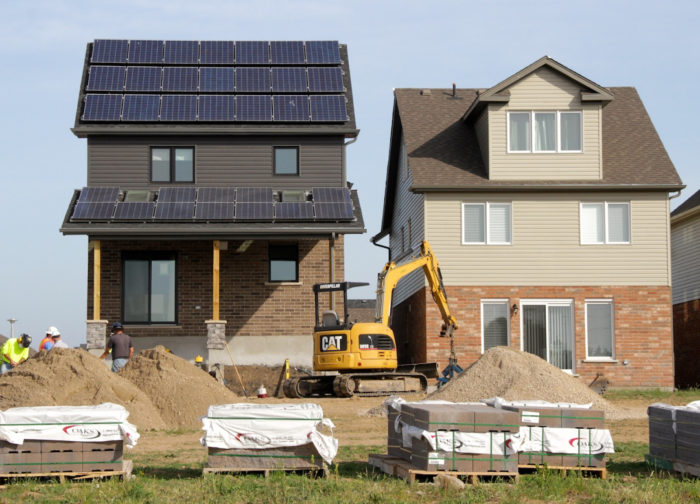
Image Credit: buildABILITY Corporation
In Canada, private and public interests are working on a common problem: How to build net-zero energy housing that average homebuyers can afford.
Asked by officials in the government’s ecoEnergy Innovation Initiative for some new ideas on how to encourage energy efficient building, a company called buildABILITY Corp. put together a program in which five separate builders were invited to tackle the net-zero problem in whatever way they chose. As a result, single-family homes and condominiums are going up in five cities in four provinces as builders work with their own consultants to produce affordable net-zero energy houses in their respective markets.
Natural Resources Canada chipped in $2 million from the national $278 million ecoEnergy program. (All costs in this article are in Canadian dollars.)
Owens Corning Canada provided insulation products for free, and builders themselves came up with in-kind contributions that equaled the government’s ante, says buildABILITY president Michael Lio. The net-zero houses, all of which must be completed by next March, will be sold privately after the government double-checks to make sure they really will produce as much energy as they use.
The larger goal of the Owens Corning Net Zero Housing Community Project is to help production builders figure out how net-zero building practices can become part of their regular repertoires.
“We’ve been talking about it for a long time,” Lio said recently. “There have been lots of net-zero buildings that have been constructed both in the U.S. and in Canada, but there haven’t been many activities that focused on production builders, and even fewer on affordability. So at the heart of this project is to work with large production tract builders to bring them to net-zero and have them change net-zero so it’s more affordable for their customers, to simplify it and drop it into their assembly-line processes.”
Builders find common ground
Builders are working independently. There’s no central agency directing their work, and there’s no common script they have to follow. Even so, Lio says, builders have settled on very similar approaches. “The technologies are off the shelf,” he says, “very accessible.”
Some of the common building characteristics:
- Grid-tied photovoltaic systems for on-site renewable energy, with arrays averaging about 10 kilowatts.
- Exterior walls with R-values between 38 and 44. Wood-framed walls have cavity insulation of fiberglass batts and an exterior wrap of extruded polystyrene rigid insulation between 2 and 3 inches thick.
- Airtightness, measured with a blower door, of 1.5 air changes per hour, or lower, at a pressure difference of 50 pascals.
- Triple-pane windows.
- Although some builders have chosen small-output furnaces, many others are using cold-climate air-source heat pumps.
- Heat pump water heaters.
- Interior polyethylene vapor barriers.
- Attics insulated with batts or blown in fiberglass to a range of R-50 to R-70. Roof framing consists of raised-heel trusses that allow extra insulation above perimeter walls.
Lio says the units have fairly small heating loads (most of the projects are located in Climate Zone 6). Half the 10 kW output of the PV arrays are on average used for base electric loads, Lio says, with one quarter devoted to space heating and the balance to domestic hot water.
Builders will sell the houses at market rates, Lio says, but because of program restraints they won’t be allowed to make a profit on building components that contribute to net-zero operation.
Construction costs are similar
A total of 26 housing units are underway, ranging from one-bedroom condos to single-family houses. Floor areas run from 750 to 3,000 square feet. They’re being constructed in Laval, Quebec; the Ottawa suburb of Kanata; Calgary, Alberta; Halifax, Nova Scotia; and Guelph, Ontario, just to the west of Toronto. Lio says land prices vary widely, but construction costs are similar across the country. Single-family houses will probably be listed in the $500,000 range.
The incremental cost of getting to net-zero on a single-family is looking like $60,000 to $80,000, Lio says, a 12% to 16% premium over the cost of a conventional house. Lio says it’s too soon to know whether Canadian homebuyers will be willing to pay it.
“I think that as a full-on market initiative, we’re really early,” Lio says. “I suspect there will be some homebuyers who have an eye on innovation, who want to be the very first to adopt a particular technology and will certainly buy these houses.
“We’ve seen dramatic shifts in the pricing on some of these systems, particularly on-site generation, and as some of these systems become even more affordable and builders start to adopt the technology in volume, then it would be appropriate to have a conversation about what the market would bear. Right now, it’s conjecture. Prices are high, numbers are low, and it’s really unfair to talk about would someone be willing to dish out $80,000.”
Building on a Canadian tradition
Canada has a long history of high-performance building and introduced its R-2000 program in the early 1980s. As Lio points out, standards typically become more demanding as time passes.
“The R-2000 is in many regards the springboard for these net-zero houses,” he says. “R-2000 is an energy standard but it doesn’t include on-site generation. These net-zero houses not only demonstrate the new type of energy efficiency that’s embedded in the R-2000 standard but it takes that next leap and embeds on no-site renewables.
“That’s the real difference,” he adds. “It’s a continuum. We’ve been at it for a long time and we’ve made lot of mistakes along the way, but it’s pretty obvious that there’s this continuum and these programs that are voluntary eventually become the stuff of code minimums.”
Weekly Newsletter
Get building science and energy efficiency advice, plus special offers, in your inbox.
14 Comments
Wall R value
"Exterior walls with R-values between 38 and 44. Wood-framed walls have cavity insulation of fiberglass batts and an exterior wrap of extruded polystyrene rigid insulation between 2 and 3 inches thick."
How does a fiberglass batt plus 2-3 inches of XPS yield between 38 and 44?
Response to Reid Baldwin
Reid,
Your question has several possible answers.
Let's do the math: An R-38 wall with R-15 of exterior foam has R-23 of insulation that is not foam. If the wall is framed with 2x6s, then you can put R-20 of fluffy insulation between the studs. The rest of the insulation (R-3) would need to come from insulated siding (insulated vinyl, for example) or some combination of interior finish materials and air films. Otherwise, the walls would need to be framed with 2x8s.
An R-44 wall with R-15 exterior foam has R-29 of insulation that is not foam. If the wall is framed with 2x8s, there is enough room for R-26 or R-27 of fluffy insulation between the studs. The rest of the insulation (R-2 or R-3) would need to come from insulated siding or some combination of interior finish materials and air films.
In Climate Zone 6, where most of the projects are located, at least 36% of a wall's R-value needs to come from exterior rigid foam (if exterior rigid foam is being used). So R-15 exterior foam will work for a wall with a total R-value of R-41.6. If you are aiming for R-44, the R-15 foam becomes marginal.
I can't think of any easy way to make these walls work with R-10 exterior rigid foam unless spray foam insulation is installed between the studs.
There is one other possibility: these Canadian builders are using polyiso, and are assuming that 2 inches of polyiso has an R-value of R-12, and that 3 inches of polyiso has an R-value of R-18. That's what the labels say, so I could understand the assumption -- but polyiso doesn't perform well at cold temperatures, so it's not a good choice for exterior rigid foam in Canada.
Are the costs referenced in $US or $CAN?
Are the costs referenced in $US or $CAN?
Wall R value
Thanks for the response Martin.
I was thinking in terms of whole wall R values, but they are probably reporting nominal R values. Your analysis shows that the nominal R values could at least approach what is stated.
Since they are using interior polyethylene vapor barriers in combination with exterior XPS foam, I suspect they are not reading GBA.
Response to Reid Baldwin
Reid,
I agree with you completely on the issue of exterior rigid foam plus interior polyethylene. Even if those Canadian designers don't want to subscribe to GBA because of the high cost (in US dollars) of subscribing, they could learn a lot from our free articles.
Et si quelques-un de nos amis canadiens veulent poser des questions en français -- c'est possible aussi. Nous répondrons.
Costs
John,
Costs are in Canadian dollars.
Did someone say "Free Cotton Candy"?
Years of consistent funding for building energy conservation since the 1970's by both GOP and Dems has fostered an incredibly rich discussion south of the 49th. I'm jealous and the Yanks should be proud of this achievement; pragmatism over partisan dogma - something the Cons here can't get past.
The GBA is the result of vision (FHB) and meticulously curated content that people might love to hate, but in the end usually presents both sides of technical divides with articles on building science and pragmatic construction techniques.
Many Canadian contractors still don't know how to dense pack cellulose properly and you can see from the article above that we eat free cotton candy without question like a polite Canadian! It's quite possible that some of the builders and some of the designers involved in the NetZero projects above have never heard of the Pretty Good House or GBA for that matter. In the last decade, Canadians have slipped back to the 1990s and we're a fragmented group spread over a vast area of land.
It is for this reason, I'd like to call upon GBA to help Canadians see the light and let's start by designating Scott Gibson as an Honourary Canadian.
poly and exterior insulating sheathing
The question of whether low perm insulating sheathings cause moisture problems has been recently addressed in a comprehensive study by the National Research Council of Canada's Code Centre. Dr. Hamid Saber has shown that the sheathing's R-value is the key factor that influences interstitial moisture and not its permeability. (Look for a possible code change that relaxes the current rules). The wall assemblies for these net zero homes meet the outboard/inboard ratio requirements of the Code's in each of their four provinces. Tens of thousands of houses have been built across Canada with exterior insulating sheathings (XPS) and poly without consequence.
Response to Michael Lio
Michael,
Thanks for the information; I appreciate it. Searching for more info, I figured out that Dr. Saber's first name is Hamed, not Hamid. I found one relevant web page:
http://www.nrc-cnrc.gc.ca/ci-ic/article/v18n2-10
If anyone has a link to a report on Dr. Hamed Saber's study, please share it.
Found a paper by Hamed Saber
Here is a link to one of Hamed Saber's papers -- but it's one that makes no mention of polyethylene:
"Risk of Condensation and Mould Growth in Wood-Frame Wall Systems with Different Exterior Insulations."
Dr. Saber wrote, "The results showed that decreasing the air leakage rate resulted in lower risk of condensation and mould growth. The values for the overall average mould index of walls configured with structural sheathing are lower than that of walls configured without structural sheathing. St John’s appears to have the most severe climate in comparison to the other three locations investigated (Ottawa, Edmonton, and Vancouver); the greatest values of the overall average mould index of the wall configurations amongst the four locations occurred in this location."
It wasn't about polyethylene (response to Martin, #10)
The point of that paper was to study what happens if they adjust the required maximum vapor permeance was relax from about 1 US perm to about 5 US perms. Ergo, no mention of polyethylene, which is two orders of magnitude more vapor tight than 5 perms, which is basically the difference between a minimalist Class-II vapor retarder and standard latex paint. It's spelled out in the first paragraph of the Abstract:
"The work originated from a Code Change Request “CCR-802” in which it was suggested that the Water Vapour Permeance (WVP) limit be raised from 60 to 300 ng/(Pa•s•m²) while leaving the limit for air leakage of building envelope materials unchanged at 0.1 L/(s•m²) at a pressure difference of 75 Pa. "
One US perm= 57.2 ng/(Pa•s•m²), so 300 ng/(Pa•s•m²) would be 5.24 US perms- roughly the vapor permeance of a single layer of interior latex primer.
What the paper reports is that with only 5 perms on the interior, a 2x6 R19 wall with no exterior foam has significantly higher mold risk than the same wall with R4 foam on the exterior in a number of climate zones. (We kinda knew this, but they quantified it.)
Even though Canadian code only requires a minimal class-II vapor retarder as the interior side vapor barrier, 4 or 6 mil polyethylene is cheap & ubiquitous, and has become the industry standard despite being an order of magnitude tighter (for both good and ill.) 2-mil nylon meets code as long as the air next to the sheet is reasonably dry (and becomes more vapor open at high humidity, a desirable feature) but it costs twice as much as 6 mil poly.
Response to Dana Dorsett
Dana,
My reference to polyethylene was in response to Michael Lio's comment that "Tens of thousands of houses have been built across Canada with exterior insulating sheathings (XPS) and poly without consequence."
I agree with Lio's statement, but I wonder whether Dr. Hamed Saber has looked into the question of the riskiness of walls with exterior rigid foam and interior polyethylene. Michael Lio implied that Saber had conducted research on that issue, but I haven't yet found a link to a paper that directly addresses the issue.
Interior polyethylene
I have yet to ever see a problem here in Climate zone 6 with interior poly and exterior rigid insulation. Never not once! I have taken apart lots of these wall assemblies years later and have never seen any issue of mold or significant condensation.
In theory the double vapor barrier sounds scary enough but in real life in cold climates I am not so convinced!
flashing
Kye,
The usual argument about double vapor barriers is that if water leaks in somehow (e.g. a bad flashing job), it will accumulate without any way to dry. Perhaps Canadians do a better job of flashing things well than Americans do.
Log in or create an account to post a comment.
Sign up Log in