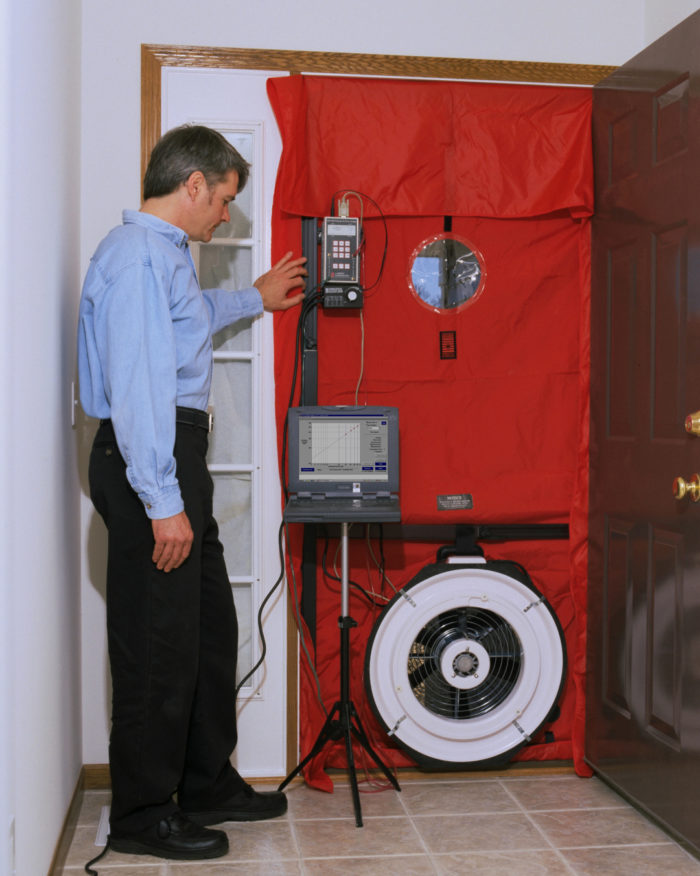
Image Credit: The Energy Conservatory
Leaky homes are hard to heat and hard to cool. The only way to know whether your home is leaky or tight is to measure its air leakage rate with a blower door. A blower door is a tool that depressurizes a house; this depressurization exaggerates the home’s air leaks, making the leaks easier to measure and locate.
An energy-efficient house must be as airtight as possible. Many older U.S. homes are so leaky that a third to a half of the home’s heat loss comes from air leaks.
There is no such thing as a house that is too tight. However, it’s also true that there is no such a thing as an airtight house. Every house leaks, and that’s why we perform blower-door tests — to measure a building’s leakage rate.
Who needs a blower door?
Blower-door testing is useful for both new construction and existing homes. By testing a new home, a builder:
- Can determine whether a certain airtightness target has been met;
- Can document airtightness levels needed to qualify for certain home labeling programs, including Energy Star and Passivhaus;
- Can do a better job calculating heat loss and heat gain the next time he or she builds a similar house;
- Can brag about the home’s airtightness to prospective homebuyers or drinking buddies.
If you’re building a new home, the best time to conduct a blower-door test is after the home is insulated but before the drywall is hung. If the test reveals major problems, the leaks will be easier to fix at that point than later on.
Testing existing homes
There are at least two reasons to conduct a blower-door test on an existing house: to determine how leaky it is, and to help locate and fix the leaks.
…
Weekly Newsletter
Get building science and energy efficiency advice, plus special offers, in your inbox.
This article is only available to GBA Prime Members
Sign up for a free trial and get instant access to this article as well as GBA’s complete library of premium articles and construction details.
Start Free TrialAlready a member? Log in
25 Comments
Natural ACH
Martin,
I'm glad you mentioned the variability and potential inaccuracies of the estimated natural air change number that are often offered by energy audit technicians. I just read an interesting study by the Energy Center of Wisconsin comparing different methods of assessing duct leakage in new homes. The blower door/duct blaster method tended to over estimate the leakage that was occurring under standard operating system pressures. My assumption would be that this is similarly the case with standard blower door tests. Air exchange will vary widely by micro climate. The "n" factors that are used attempt to account for this, but they necessarily fail to capture the micro climate. Here's a link to the study: http://www.ecw.org/resource_detail.php?resultid=361. Keep up the great posts.
Another use for the blower door
I have ran this by a few folks, Gary Nelson included, why not use the blower door as a pre-drywall diagnostic tool. This probably would apply more to climates where a vapor barrier is used. When the insulation is in and the vapor barrier is in place, slightly pressurize the house and introduce theatrical fog into the living space and watch where it goes. You could mark those areas with a Sharpie and seal them before the drywall is in place. You could also see the leaks through the exterior sheathing and seal them up before the siding goes on. Gary said they have a fogger and use it for commercial testing, I think it may have value in residential. It's hard to find and seal air leaks once the drywall is hung.
When to conduct a blower-door test
Doug,
If you read the article again, you'll notice that I wrote, "If you’re building a new home, the best time to conduct a blower-door test is after the home is insulated but before the drywall is hung. If the test reveals major problems, the leaks will be easier to fix at that point than later on." So I agree that it's usually best to use the blower-door before the drywallers arrive.
One possible exception: homes built with the Airtight Drywall Approach; for those homes, it may be desirable to hold off on the test until after the drywall is hung.
Finally, I agree with you about the usefulness of theatrical fog machines. The last paragraph of the article includes a link to an earlier blog, "Pinpointing Leaks With a Fog Machine."
Onward through the fog
You are way ahead of me Martin, I should have read closer. Once a builder gets on to building airtight, there really should not be many leaks, but we all miss things. The fogger would be a great tool to use when breaking in a new insulating and airsealimg crew. This would also be the time to depressurize very slightly and IR camera the house to spot insulation voids.
The problem with volume & home made blower doors...
Great, thorough article, Martin! It's not the sexiest building science topic out there, but it's certainly an important one.
Now, about those ways of reporting air leakage, you mention cfm50 and ACH50. The former is great if you're in the business and have tested a lot of houses. You get a feel for the numbers after a while, but you still need to factor in the size of the house. That's where ACH50 comes in, and it's a flawed measure, in my opinion, because it's based on the volume of the house, not the surface area of the building envelope.
Leaks don't happen throughout the volume, though, so dividing the cfm50 by volume doesn't give you a fair way of comparing houses of different sizes. As houses grow, the volume usually increases faster than the surface area, so using ACH50 (or ACHnat) is biased toward larger houses. For many houses, the range isn't big enough to worry about, but when you're comparing a 1000 square foot Habitat for Humanity house to a 10,000 sf McMansion, the difference is significant.
A much better way to report infiltration is with the Envelope Leakage Ratio (ELR), developed by Southface in Atlanta for its EarthCraft House program. Since the leaks come through the envelope, not the volume, the ELR is simply the cfm50 divided by the square footage of the building envelope. With this measure there's no bias in favor of bigger houses because you're normalizing to the correct quantity.
Also, a couple of other measures, described in the Energy Conservatory's Blower Door manual, are the Effective Leakage Area (ELA) and the Equivalent Leakage Area (EqLA). They're attempts at extrapolating the size of the hole in the envelope based on the blower door results. A very rough estimate is that for every 1000 cfm50, there's about one square foot of leakage area in the envelope.
Finally, I just found out this week about a website with instructions for making your own blower door that can measure the leakage using a fan, a variable speed controller, a manometer, and an anemometer. I haven't tried it, but it looks like it probably gives decent results. Here's the URL:
http://www.nlcpr.com/Pressuretesting.php
Allison A. Bailes III, PhD
Energy Vanguard
Response to Allison Bailes
Allison,
Thanks for all the great information and the useful link.
When I was editor of Energy Design Update,, I tried to untangle all the various metrics used to report blower-door results. This is what I wrote on the topic in the August 2005 issue of EDU:
A typical blower-door test measures infiltration airflow at a pressure difference of 50 Pascals. The airflow is usually reported in cfm @ 50 Pa (CFM50 or cfm50).
To calculate air changes per hour at 50 Pa (ACH @ 50 Pa or ACH50), multiply cfm50 by 60 minutes per hour and divide the product by the building volume, including the basement, measured in cubic feet.
Equivalent leak area (EqLA) is the area of a theoretical sharp-edged hole in the building envelope that would leak as much as all of the building’s actual holes at a pressure difference of 10 Pa. EqLA (in square inches) approximately equals cfm50 divided by 10.
Effective leak area (ELA) is the area of a theoretical hole (with rounded edges) in the building envelope that would leak as much as all of the building’s actual holes at a pressure difference of 4 Pa. ELA (in square inches) approximately equals cfm50 divided by 18.
Specific leakage area (SLA) is calculated by dividing ELA by the conditioned floor area; it is usually reported in square inches of leakage per square foot of conditioned floor area. California Title 24 defines SLA differently: SLA is 10,000 times the ELA (in square feet) divided by the conditioned floor area in square feet. The California SLA approximately equals cfm50 multiplied by 3.812, divided by the conditioned floor area.
Normalized leakage (NL), defined by ASHRAE Standard 119, is a dimensionless number calculated by dividing ELA by the conditioned floor area, multiplied by a correction factor that varies with the height of the building. For most buildings, normalized leakage can be approximated by dividing ACH50 by 20.
“Natural infiltration” (ACHnat) varies greatly by season and by climate. It is not the same as normalized leakage, although its value may be similar. Rules of thumb for calculating ACHnat vary by climate. In Minnesota, ACHnat equals approximately ACH50 divided by 17, while in Florida, ACHnat equals approximately ACH50 divided by 30.
Several “leakage ratios” have been proposed. According to one definition, the leakage ratio equals EqLA (in square inches) divided by 1% of the total envelope surface area. The Minneapolis Leakage Ratio equals cfm50 divided by the area of the above-grade envelope in square feet.
Commercial buildings
I recently performed a final air leakage test of a commercial project of 182,000 CF, and came up with an ACH50 of 0.16. (Tightest by far of any I have tested and I have been at it since 1990) I was wondering if anybody could help determine the ELA, ELR and EqLA?
Formulas for ELA, ELR, and EqLA
Allan,
You will find the formulas for ELA and EqLA in my posted comment of Feb. 2.
ELA (in square inches) approximately equals cfm50 divided by 18.
EqLA (in square inches) approximately equals cfm50 divided by 10.
According to Allison Bailes, the ELR is simply the cfm50 divided by the square footage of the building envelope.
Martin,
I know the rules of
Martin,
I know the rules of thumb you stated on Feb 2. I was just curious on the actual calculation as TECTITE program values for ELA and EqLA differ from the cfm50 divided by (10 -18) by over 10%. Guess it is close enough as a mentor once told me: " it is better to be approximatively right than precisely wrong"
What about the properties of the envelope?
The Envelope Leakage Ratio (aka the >Minneapolis Leakage Ratio, apparently) seems like the most solid way of those listed in this thread of reporting the leakiness of a building. The surface area of the envelope has to be a part of the formula, seems to me. There are numerous other factors that some insist should also be considered (climate, wind speed outdoors, stack effect from height of bldg, etc), and of those the one that seems undermentioned and important is the properties of the building envelope. Is it fair to use the same metric for a masonry building with 10 percent fenestration openings and almost no wall penetrations for pipes and conduits, versus a wood-framed building with 30 percent fenestration openings and numerous penetrations? The leakiness of various building types should be compared to other buildings of the same type, not to buildings of different types. The metric should say "your building is tight compared to other masonry buildings with few openings and penetrations. Your building is leaky compared to other wood-framed homes with a generous number of windows and doors". This asks more of the evaluator, of course. But if there was a table that listed types of construction and assigned a numerical factor to each, it doesn't seem like it would be so difficult to add factors that would let us judge a building's leakiness in a more realistic and fair way.
Disclaimer: I have three days' experience with blower-door testing, and am just starting to learn how this all works and what the data means. All I offer is fresh eyes.
blower door test
very good info getting ready to take bpi i test in june trying to get a couple of test under my belt , but this info is the greatest also looking for some employment oppertunities if any resources please contanct at ernestjoyner41@ hotmail.com, plesently in weaterization course.being sponsered by eac of long island
Blower door testing
Hi, I have been using a blower door for about 2 years now and have done about 300 homes. I am BPI certified, however I don't agree on using the basement volume for determining the air leakage of the home if the basement is unconditioned as most are. If the basement is unconditioned, we don't want to heat it and a good sealing door should be installed between the two spaces. If the idea is to determine how much leakage is taking place, the volume of the conditioned space should be used, and even that has some problems. There is a big difference between testing for leakage and indoor air quality concerns. I think all new basements should be insulated and sealed and then viewed as conditioned space as this would take out the question as to weather the basement is conditioned or unconditioned or both. When I cannot figure out if the basement should be included, I do the test both ways.
ELA = EfLA?
I have always seen ELA (this article) referred to as EfLA by the blower door manufacturers.
I know this article is older, but I have seen a few references to other standards recently including ASTM and USACE (for example: http://www.aikencolon.com/Retrotec-Blower-Door-Systems_c_1074.html). Are these newer standards?
Abbreviation of "effective leak area"
Brian,
The standard abbreviation for "effective leak area" is ELA, as you can discover with a few Google searches. For example, you will see the same abbreviation I used (ELA) if you do a word search for "effective leak area" in any of the following documents:
http://www.fsec.ucf.edu/en/publications/html/FSEC-PF-195-90/
http://www.sips.org/content/technical/index.cfm?PageId=160
http://www.whitegatehomes.com/heafaq.html
http://www.advancedgreenproducts.com/SIP%20Technical%20Info.htm
ELA vs EqLA
Martin,
Thanks for the list of different leakage area calculations. I am having a hard time figuring out the best one to use when I am in a home with a client. They seem to be trying to calculate the same thing, but have different methods of doing it and will always have different results. Do you have any suggestions on which to use and why?
Response to Evan langhorst
Evan,
Of course you can use any metric you want, but I don't think that either equivalent leak area or effective leak area is particularly useful.
Obviously, air changes per hour at 50 Pascals (ach50) is a commonly used metric. I tend to side with Allison Bailes, however, who argues that the best metric is cfm50 per square foot of building envelope. For more information on Bailes' logic, see How Much Air Leakage in Your Home Is Too Much?
Question on Interpreting Building Leakage Test Results
So if my results were 3658 CFM50, 12.91 ACH50, and 1.8291 CFM50/fl2 floor area, how bad is that? Something I can fix as a DIY, or should I hire a professional?
How bad
Pretty bad.
I'd hire an energy auditor to help me figure out where the big leaks are. Then you can decide what you can do yourself, which may be quite a bit.
Is this an old house? Where are you located?
Re: How Bad
It is an older home (c1906) that we gutted to the studs and redid back in 2010. I don't have a problem doing the work as long as I know what to do. I am in Northwest Missouri
Box fan?
Out of curiosity, why wouldn't a box fan work? A cheap one will move 2500 cfm. Would such a fan bog down under pressure?
Response to Jennifer Gruenke
Jennifer,
A blower door fan is rated at 6,300 cfm, so your box fan isn't quite powerful enough. That said, you can get meaningful results with two or three box fans. The trick, of course, is that they need to be installed in a window or door opening, and the installation needs to be relatively airtight. But people have done what you suggest, with box fans and duct tape.
You won't get a calibrated reading as you would with a blower door, but you can use a few box fans for the equivalent of blower-door-directed air sealing.
Response to Martin Holladay
Interesting. Thanks.
Here is another version of a DIY blower door kit: https://www.builditsolar.com/Projects/Conservation/BlowerDoor/BlowerDoor.htm
I like the idea of having time to seal leaks and to have the opportunity to run multiple tests without paying per test. As we all know from health care co-pays - we're less likely to go through with follow-up testing when each on costs $250.
Hi. I'm a fairly new energy auditor so disclaimer right up front! I realize this is an older article so thinking may have changed since this was written. For envelope air leakage testing, specifically new construction code compliance, I do NOT include the basement in the building volume unless it meets a few criteria... the biggest being whether or not it is "conditioned" space. So for an existing home, I would think the reasoning should be the same... DON'T include a non-conditioned basement in the cubic volume for the ACH50 calc. Thoughts?
GBSHV,
Traditionally, the volume of the house included the basement because the basement walls and basement floor are part of the home's thermal envelope. You can't ignore air leakage through cracks in the basement walls and floor. If that traditional assumption has changed, and blower door operators are being been instructed differently these days, that's news to me.
Log in or become a member to post a comment.
Sign up Log in