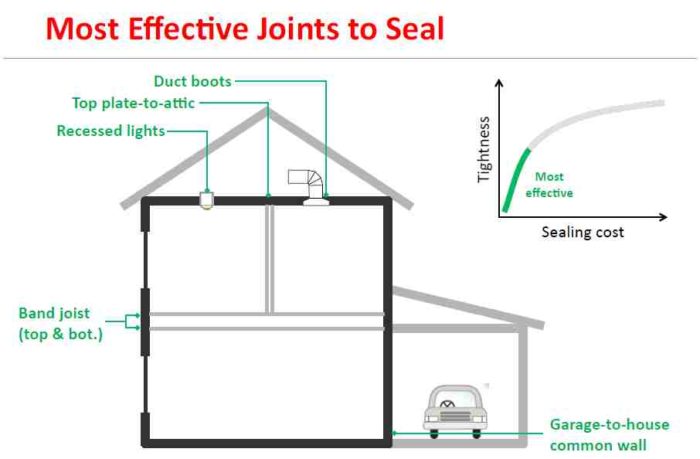
Image Credit: Graphics courtesy of Owens Corning
Most new homes are leaky. In the typical new home, significant volumes of air enter through cracks near the basement rim joists and exit through ceiling holes on the building’s top floor. These air leaks waste tremendous amount of energy.
In recent years, after years of prodding by building scientists, code officials have finally taken a few stabs at addressing air leakage. (For more information on recent code changes related to building airtightness, see New Air Sealing Requirements in the 2009 International Residential Code and An Overview of the 2012 Energy Code.)
Of course, some builders have focused on energy efficiency for years, and many of these builders own a blower door. If you have your own blower door, you have probably learned by trial and error which cracks matter most.
However, the vast majority of contractors build homes without any feedback from a blower door. If these builders want to improve the airtightness of the homes they build, they probably don’t know where to start.
Get the big holes first
The first step is to make sure that there aren’t any really big holes in your homes. (Joe Lstiburek calls these “the Joe-sized holes”; they’re the holes that are big enough for Joe to crawl through.) You may be thinking, “Can a house really have holes that big?” The answer, sadly, is “Yes, it really can.”
Let’s raise the bar just a little, and make a list of holes that are big enough for a cat to walk through. These include:
Once…
Weekly Newsletter
Get building science and energy efficiency advice, plus special offers, in your inbox.
This article is only available to GBA Prime Members
Sign up for a free trial and get instant access to this article as well as GBA’s complete library of premium articles and construction details.
Start Free TrialAlready a member? Log in
22 Comments
Can lights in sealed attic
If you are foaming the underside of a roof to create a sealed attic, are can lights okay? Would you still want to (a) substitute a different type of light fixture or (b) create an air seal around each fixture? I think I know the answer, but my brain is a bit overloaded with business sciences info.
Cold Climate Bias ?
Martin wrote: "the stack effect disproportionately depressurizes the lowest areas of a house and pressurizes the highest areas of a house."
Martin, how about in a Not-So-Cold Climate?
How about in an Air Conditioned House?
Aren't the highest areas often "depressurized" With Respect To Outside (WRTO)?
Edit to say:
The first paragraph of this article also suggests a Heated Home...
or a Cold Climate Perspective.
Response to Steven Knapp
Steven,
If you are installing spray foam on the underside of your roof sheathing, you need to make sure that the foam insulation is thick enough to at least meet minimum code requirements for R-value. This should be obvious; but, believe it or not, many spray foam contractors convince their customers that foam is such a miracle product that it's OK to install it in a layer that is too thin to meet minimum code requirements.
Once you've done that, you could install a recessed can light under the spray foam, as long as you meet the clearance requirements established by the recessed can manufacturer. Remember, though, that in many cases the rafters aren't deep enough to accommodate both a recessed can fixture and enough insulation to meet minimum code requirements.
If the spray foam contractor is conscientious, the spray foam will create an air barrier as well as an insulation layer. If you install a recessed can light on the interior side of the spray foam, you don't have to worry about air leaks through the recessed can.
Response to John Brooks
John,
Thanks for the reminder about my bias. Sometimes the need for a fluent writing style forces a writer to be less than complete from a technical standpoint. If a sentence is overloaded with caveats and prepositional phrases, it often becomes so leaden that it isn't worth reading.
Even Texans do experience winter, however, and most need to heat their homes for a few weeks every year.
Because the indoor-to-outdoor delta-T in Texas isn't as large during the summer as the delta-T in Vermont during the winter -- or even, for that matter, as the delta-T in Texas on a cold winter day -- the "reverse stack effect" attributable to air conditioning is less pronounced than the stack effect that occurs during the heating season. In fact, infiltration and exfiltration locations are just as likely to be influenced by wind, exhaust fans, or HVAC blower operation as they are to be influenced by the "reverse stack effect" in Texas during the summer.
That said, I plead guilty to occasional eruptions of cold-climate bias.
The stack effect does indeed work in both directions.
Just because it's a cooling dominated climate doesn't invalidate the importance of both high & low leakage points, unless you can somehow demonstrate that cold air leaking out the foundation sill sucking hot outdoor air (or worse- ATTIC air) into the top of the house isn't a comfort or energy use problem.
Near the shore in San Diego maybe it doesn't matter too much, but anyplace with more significant heating or cooling loads stack effect pressures really do matter.
But let's get over the climate-bias paranoia, eh? For all but US climate zone 1 locations heating season stack effect infiltration exceeds cooling season stack effects. Even if peak cooling loads may be higher than the heating loads, the seasonal average delta-T drivers of stack effect (air conditioned or not), are greater for during the heating season. Cooling loads are dominated by solar gain, whereas stack effect is driven by air temperature deltas. The effect of infiltration rates on heating & cooling loads are also a function of air temperature deltas. Even in TX and most of FL there's a bigger net effect and energy use from stack effect infiltration during the heating season than the cooling season. (Only down in Brownsville TX is it close to a wash, with roughly equal heating/cooling season stack effect infiltration.) A heating-season bias is appropriate when addressing this issue, more so than with other issues.
If you live in Miami or Hawaii you can pretty much ignore the heating-season stack effect discussion, but it's valid for the rest of the US.
I might catch Hades from some other Pros...
Bear with me a couple minutes while I argue for the evil spray foam guys:
If I'm starting out with an existing home with attic ductwork, I'd rather have an air tight code minimum (here R19) foam job than R 30-40-60 anything of loose fluffy stuff.
Sure, the engineer in me would rather have R38 or better spray foam, but the payback on the 'second' R19 is vanishingly small, on the order of a century.
In fact, given the unit costs of spray foam, there is probably a valid case to be made for dropping BELOW code minimum insulation levels, IF the project is PROVEN air tight.
The positive effects derived from minimizing duct losses and attic air leaks, reducing stack effect and latent gain overwhelm, at least in my area, losses associated with reduced R-Value.
Can lights seal the deal - houses with lots of them derive the most benefit from retrofitted foam.
No one likes to give up so much as a scintilla of R value, but economic reality suggests a blended solution of moderate R-Value and heavy air sealing, at least down to 2-3ACH50.
I repeat that the foam job must be proven as air tight as reasonably possible - a loose foam job can do more harm than good by limiting sensible load while leaving latent load. No good comes of that, occupants are unhappy, and foam's reputation suffers. Therefore we don't participate in a foam project if we aren't engaged to control quality.
Do these results depend on where the air barrier is located?
I'm probably not fully understanding this, but isn't the location of the designed air barrier important to prioritizing what needs to be sealed? e.g. I'm going with the REMOTE approach with air barrier on the outside face of the sheathing, including over a flat roof.
Doesn't that make anything on those surfaces critical for air sealing, e.g. Vertical seams (identified in the research as low priority) in the plywood should be sealed because the plywood is covering everything, including the band joists (high priority).
Related to this, how important is the drywall in this case?
Of is the research identifying weak points, but you can address in different ways? including redundant layers, e.g. caulking band joist and exterior air barrier?
Response to Curt Kinder
Curt,
I understand your point. Spray foam has certain advantages, including the potential for greatly improving airtightness. I suggest that we should be aiming to achieve airtightness as well as (at least) code-minimum R-values.
Spray foam contractors whine, "But spray foam is so expensive that it is hard to compete with cellulose!" True. But that might be a good argument in favor of cellulose.
In your area, where HVAC contractors mysteriously put their ductwork and air handlers outdoors (in the attic), you have an additional problem. If you are building an unvented conditioned attic, you have fewer options for insulation. But if spray foam is too expensive, you can choose to use rigid foam above the roof sheathing, or a combination of rigid foam and air-permeable insulation, or a combination of spray foam and air-permeable insulation.
Response to Jerry Chwang
Jerry,
Q. "Do these results depend on where the air barrier is located?"
A. As far as I understand it, the Owens Corning researchers were looking at typical American construction techniques. They were assuming that builders are just beginning to consider air sealing, for the first time in their careers.
If you ask the typical American framer, "Where is the air barrier?" he will have one of two answers. He will either say, "What's an air barrier?" or "You mean the housewrap?"
The houses that the Owens Corning researchers looked at had no air barrier. Before they began their iterative process of air sealing various cracks, the homes leaked. There were cracks between the sheathing panels. There were cracks near the windows and doors. The ceilings and rim joists leaked in many, many areas. The drywall layer slowed down, but did not stop, these leaks.
For those who have been paying attention to air sealing for decades, it may seem surprising to learn that the average American home builder doesn't know where his air barrier is located. But the sad fact is, he doesn't.
Q. "I'm going with the REMOTE approach. ... Doesn't that make anything on those surfaces critical for air sealing, e.g. vertical seams ... in the plywood?"
A. Yes. That is why David Wolf wrote that “it best to try to seal all the joints, if you can. The sealing of all joints/openings is important, although some are more important than others.”
Q. "How important is the drywall in this case?"
A. If you are building a REMOTE or PERSIST house, the air barrier is created at the exterior wall sheathing, which means that it is on the interior side of the insulation. In such a house, there is no need to create a second air barrier at the drywall layer.
Q. "Can you address [air sealing] in different ways? including redundant layers, e.g. caulking band joist and exterior air barrier?"
A. Of course. That is why I wrote, "If you are a Passivhaus builder aiming to achieve 0.6 ach50, ... every conceivable crack in the home’s thermal barrier needs to be sealed. In some cases, Passivhaus builders use a redundant approach — for example, using both caulk and a gasket."
plaster value
Martin
If painter's caulk provides some value in stopping air flow does blueboard finished with thin coat plaster provide any value in sealing the wallboard?
Response to John Roy
Roy,
Plaster is a good air barrier (equivalent to taped drywall). As with drywall, air leakage won't occur in the center of a plaster wall. Likely air leakage points occur at electrical boxes, penetrations, window rough openings, door rough openings, under bottom plates, and between the top plate and the blueboard.
These areas need to be sealed in the same way they would if you were following the Airtight Drywall Approach.
Attic kneewalls
I would think attic kneewalls would make the "biggest bang for the buck" list - like garage walls, they often have something other than standard OSB sheathing on the exterior side and can leak quite a bit.
Can Lights
Martin,
Can lighting is a necessity in many homes, esthetically and practically. My house has a dozen of them in kitchen and living room. I read, perhaps in GBA, that each can leaks 4 CFM and I don't doubt that. Plus my cans are not IC-rated so the attic insulation is pulled back at the housings. The advent of LED and the rapidly dropping cost of same offers solutions on a few levels. I bought Eco-Smart Cree-technology LED can inserts (dimmable) on sale at my local big box store. My original intention was to install air tight baffles at about $8 each but stumbled onto to the LED's instead. Last time I checked they were $50 each but price has dropped by half. We love them. Higher quality light than incandescent spots and only 10w each (versus 65). The old leaky cans were (I hope) an easy solution. I stuck on some white foam rubber 3/8"w x 3/16"thk weather strip on the perimeter of the baffle to seal the ceiling joint. Rubber foam is more pliable than vinyl and compresses better on this low pressure joint. I want to thank GBA for getting me on this mission. I have sealed my attic hatch with weather strip and found a massive 1/2 inch gap around the stove vent duct penetration. It was so bad there were dust tracks on the cabinet door joint. Dust/dirt tracks are a good indicator, which I learned from my AC tech. How did I miss that all of these years? Sealed it with expanding foam. Also found many leaks in skylight joints. Will be hitting crawlspace and attic to seal plumbing and electric leaks before winter. Looking forward to propane savings this winter.
Response to Richard James
Richard,
I'm glad that you are making progress in your air sealing efforts. Keep up the good work.
According to some observers, can lights may be aesthetically pleasing. Others, including me, recoil in horror when they see one. So your statement that "Can lighting is a necessity in many homes, esthetically and practically" seems indefensible to me. A more accurate statement would be that "some homeowners find can lights to be attractive." There is no accounting for taste. It's your house.
Just be aware of the energy penalty you are paying for you aesthetic preference.
For more information on can lights, see Recessed Can Lights.
Can lights
Martin, No choice in my house, they were already there sucking $$ propane heated air up info the attic. I'll rephrase, the Eco-Smart inserts are more attractive than the originals. The kitchen group brings light to all corners, they are great. The LED's dipserse light far better than the uncandescents. I could do without the living room sets. Rarely use them. Great site, glad I found it. Never would have learned about "stack effect". My wife thinks I've gone nuts since I retired. Attic fanatic. Idle minds...
Redundency VS Perfection
Not a builder, just grew up with them - went on to become an architect, jury is still out on that.
What I experienced growing up, and helping out, builders, to this day when pros help me out on my DIY farmhouse rebuild, is that SPEED is the name of the game.
Given the need for speed, more on that below, and the generally low QC on low bid (most) jobs where day workers outnumber permanent staff, language issues exist, etc. (see below), I can't help but believe the only solution to air / moisture barriers is redundency, perferably different trades. Say seal sheathing seams and tape house wrap along with airtight drywall AND a list of must seals as noted in the article.
Site mockups help, it provides a "training sample" for day workers and bridges the language gap,. After framing pick a strip top to bottom, have GC build it out, maybe without all the siding.
The need for speed: Can't fault builders for working fast. Lots of builders with good references, so it boils down to price
The need for quality: NYC is putting quality back in construction. Large buildings report yrly energy use, result, . Much publicized BA "LEED Platinum" building is actually a energy hog. The tenants are being blamed, long story and the jury is still out. None the less, the architect, engineers, buidler, and developer have all lost credibility, and no doubt customers, due to the under performance of the building. NYC is also requring certified inspections of at least 10% of all energy related materials and assemblies.
Response to Russell Higgins
Russell,
You raise an important point: if builders work fast, they may not care about air sealing. That's true.
There is a simple remedy to this problem: put an airtightness goal in the specifications, and hold the GC accountable for reaching the target. If everyone on the job site knows that the job will be tested with a blower door, and if payment depends on hitting the airtightness spec, workers will pay attention to airtightness.
Air Tightness
Layperson here and very interested. I remember the cheap energy days when a house was supposed to "breathe", I grew up in one of those ice boxes. The envelope deficiencies I am finding in my house, built in 2000, are significant. Custom built, the original owner was there every day. What are they getting away with in spec built subdivisions? My house met code at the time, or should have, so the fault is with the code and the inspection process. It needs to be updated (blower door test) and enforced. The average person has no clue, we have to rely on the builders and a sensible regulatory process. This is not rocket science. $500 extra in materials/workmanship in 2000 would saved thousands in heating and air conditioning. Multiply that by millions of homes and do the math.
Can we quantify "Cost per hole"
We have sealed our house at all the "available" joints and holes. There are lots of holes that are not available because we have no attic access. None of the holes in top plates to feed electric wires are sealed within the walls. I have found two while renovating a closet and they are .75 inch holes for each wire. I am contemplating trying to open up some of the walls to seal some of these, but is it worth the effort? The wall by the distribution panel may be worth the effort, but my wife is tired of the cleanup after each attempt.
Response to Roger Williams
Roger,
Here in New England, we have a lot of skilled weatherization workers who know how to perform blower-door-directed air sealing in existing homes. Unfortunately, these skilled workers may be lacking in other areas.
When there is evidence of "thermal bypass" leaks through interior partitions -- often due to electrical penetrations that are hard to access, as you describe -- these workers often install dense-packed cellulose in the stud bays of the interior partitions. The cellulose in this case is not working as an insulation; it is working to limit the flow of air through all those holes in the plates.
Leaks! Air Sealing!
We live in a 100 year old foursquare: two stories plus basement and attic. Major chimney effect potential. We've had blower tests, blown cellulose into the balloon frame exterior walls, packed cellulose between the joists in the attic floor after sealing all holes and cracks we could find, rebuilt double hung sash windows to tighten up the rails and seal the edges. Put a nice dent in the air exchange, but not enough, and having a hard time finding the rest of the leaks.
Reading this article, it hit me: the exhaust fan in the upstairs bathroom! Nice, expensive Broan, vented through the attic directly to the roof, with a vent cap with a flap valve. Run a blower test and the flap is sucked shut. No problem detected. But live life normally and convection pushes that danged little flap open all winter!
Is there such a thing as a powered vent cap that will open only when the exhaust fan is turned on?
Response to Robert Nachtrieb
Robert,
Q. "Is there such a thing as a powered vent cap that will open only when the exhaust fan is turned on?"
A. No -- not as far as I know. However, some bath exhaust fans have better backflow dampers than others. I suggest that you post a question on GBA's Q&A page asking GBA readers to suggest the best bath fan in this regard.
Log in or become a member to post a comment.
Sign up Log in