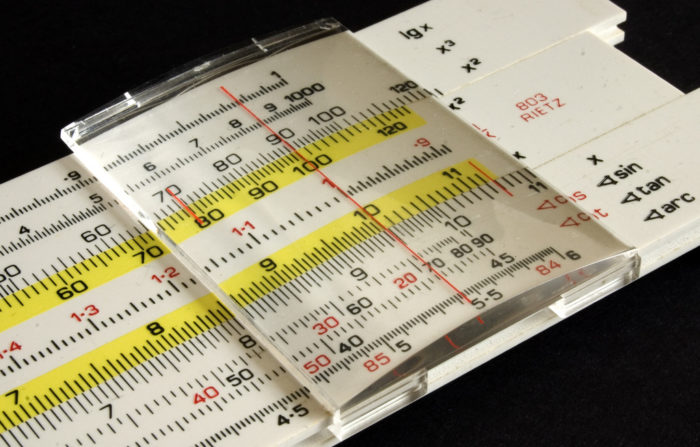
Image Credit: Dominic Alves
I’m going to devote the next several blogs to a discussion of heat-loss and heat-gain calculations. These calculations are the first step in the design of a home’s heating and cooling system.
In order to address this big topic in little bites, I’ll start by discussing heat-loss calculations. I’ll get around to heat-gain calculations and cooling equipment in a future blog.
Before digging in to the topic, however, it’s worth answering the question, “Why do I need to know how to perform these calculations?” If you are a homeowner or carpenter, you may not need to know anything about calculating heating loads. However, if you are a designer, architect, or builder, this knowledge will prove useful — even if you never perform the calculations yourself, but instead depend on computer software or consultants to perform the calculations.
Understanding the principles behind heat-loss calculations will help you understand how buildings work and how heating and cooling systems perform. With this knowledge, the quality of your dialogue with window suppliers, HVAC contractors, and engineers will definitely improve.
Outdoor design temperature
If you’re performing a heat-loss calculation to size heating equipment, you need to perform the calculation for the worst-case condition: namely, the coldest night of the year. (Because the coldest condition usually occurs at night, a heat-loss calculation does not consider solar gain through windows.) The temperature on that night is referred to as the outdoor design temperature. (To be precise, the outdoor design temperature is usually defined as the temperature that is equaled or exceeded for 97.5% of the time during the three coldest months of the year. Other sources define the outdoor design temperature as the temperature that is equaled or exceeded for 99% of the year. As it turns out, most homes will remain comfortable…
Weekly Newsletter
Get building science and energy efficiency advice, plus special offers, in your inbox.
This article is only available to GBA Prime Members
Sign up for a free trial and get instant access to this article as well as GBA’s complete library of premium articles and construction details.
Start Free TrialAlready a member? Log in
28 Comments
Sliding ruler
Good thread. I guess I need to turn off my computer, dust and oil my sliding ruler and get goin'...
I did notice that the design temperatures from ASHRAE Fundamentals differ considerably from ACCA MJ8 design temperatures. Do you know why?
design temperature vs "coldest"
I'm glad you somewhat distinguished between "the coldest night of the year" and 97.5% design temperatures, but I'd like to make the point much more emphatically. The purpose of the 97.5% design temperature is specifically to avoid specifying a system for record cold weather, which is rare and persists for only a few hours.
Response to Armando Cobo
Armando,
You're right -- you'll notice that design temperature tables from different sources don't always agree. Older design temperature tables are based on older weather data; as global temperatures have warmed over the last few decades, some design temperature tables have reflected these changes by raising design temperatures.
Microclimates can make a big difference in design temperatures, especially in mountainous states like Colorado. My temperatures at 1800 feet of elevation in Wheelock, Vermont, are considerably colder than the temperatures recorded in Burlington, Vermont, so you have to use a little common sense if you are building at a location that isn't listed in the design temperature tables.
Pay attention to your thermometer for a couple of decades, and use your own local knowledge as a common-sense reality check when choosing your design temperature.
Response to Curt Kinder
Curt,
Your point about the difference between the 97.5% design temperature and "the coldest night of the year" is an important one.
I adopted a shorthand phrase ("the coldest night of the year") to make my prose more readable, at some loss of technical accuracy -- so it is, indeed, worth repeating the point that you underlined.
Martin,The link you provided
Martin,
The link you provided in your article come from 1985 ASHRAE Fundamentals, where the design temps for DFW, TX are 22/100 and for ABQ, NM are 16/94. The design temps form MJ8 are 24/98 for DFW and 18/93 for ABQ. Clearly MJ8 shows DAL to be 2°F warmer in winter and 2°F cooler in summer. At the same time ABQ shows to be 2°F warmer in winter and 1°F cooler in summer.
I believe both Wrightsoft and Elite software use ACCA MJ8, which is used by most HVAC contractors. Since a two degree temperature difference can represent ½ ton more on the AC unit, I guess it could be important to know the correct design temperatures. Should ASHRAE update their tables or meet ACCA in a common ground? Any thoughts?
I’m including the ACCA MJ8 for other folks to check their design temps.
Response to Armando Cobo
Armando,
Thanks -- I appreciate the link to the Manual J design conditions document.
Bulbs
And I don't mean tulips. Dry bulb? Wet bulb? These terms have long been a puzzlement. Perhaps Martin will cover them in the next installment.
Response to Gordon Taylor
Gordon,
The temperatures referred to in this article are all dry bulb temperatures -- that is, the temperatures shown on an ordinary thermometer. (To determine a wet bulb temperature, you need a different type of thermometer -- one that has a dampened cloth surrounding the bulb at the bottom of the thermometer. This type of thermometer is called a "sling psychrometer," because it is designed to be slung in a circle to encourage the evaporation of the moisture held by the damp cloth.)
Fortunately, heat-loss calculations don't require consideration of wet bulb temperatures or psychrometrics.
If you're interested in learning more about psychrometrics, you can see my blog on the topic: Are Dew-Point Calculations Really Necessary?
You might also be interested in this helpful article: Dry Bulb, Wet Bulb and Dew Point Temperature.
Is it common for hvac contractors to do the load calculation?
I'm wondering if these calculations are often done by contractors. Energy Star V3 requires it on the Checklist at Section 2.18. Air flow tests are required in Section 9. I don't see why it's not required before installing any hvac equipment.
Maybe this will qualify as a near horror story.....
The house I bought about a year ago needed a new furnace. I requested a high efficiency gas furnace and that the ducts be inspected and serviced as necessary. A new 95% gas furnace installed and I was assured that the ducts were fine.
The furnace seemed to be installed ok, except for the fact that the whole house humidifier was not reconnected when they were done and that they left large gaps in the attic penetrations. That wasn't a huge deal to me but the supply ducts in the crawlspace are another story.
There is no way they were ever inspected. The galvanized rectangular duct, resting on the dirt floor, was completely rusted out. For some years, who knows how long, there was a flexible copper drain tube from the water softener resting on the galvanized steel. It was completely corroded to the point of having a puncture in the copper, so that water drained all over the duct. The ducts are insulated internally. I guess the black stuff all over the insulation is mold. Another section of round galvanized duct was completely disconnected.
So instead of heating with my super efficient furnace, when it gets below 45F I turn the electric oven on, open it, and let the ceiling fan run to disperse the heat. It seems that my 8 year old daughter has fewer asthma attacks that way. I'm glad I work 12 hours a day and that I have 50/50 custody of my daughter so neither of us are here that often. I'm also fortunate that the house is small, about 1000 sq ft, and fairly well insulated.
My guess is that most contractors know that very few homeowners are actually going to get in the crawlspace to check out their work, especially ones that are 90+ years old, like my grandparents, the previous owners of my house. Also, I guess that few homeowner's are going to ask to see their load calculations. I bought the house from my Mom and Aunt, who inherited it after their parents died.
I was going to attach some photos but the resolution is too high for the 2MB attachment limit. I'll see if I can resize them and post them later.
Response to David Martin
David,
Q. "Is it common for HVAC contractors to do the load calculation?"
A. No.
For example, my brother, who lives in Boston, recently contacted three HVAC contractors for bids on a new furnace. He asked them to perform a load calculation, and not a single one was able to do one. All three contractors suggested that he install a new furnace with a rating that was three times the design heat load for his house. (I performed the heat loss calculation for him when the contractors said they couldn't.)
For more information on this problem, see Saving Energy With Manual J and Manual D .
Understanding the fundamentals
Another great topic. Energy models would be much more accurate & meaningful if modelers truly understood heat loss calculations outside the "black box" of most modeling tools; I look forward to following this blog series.
Response to David Martin & Martin Holladay
On existing homes with pre-existing heating systems needing replacement, it's usually more accurate to use fuel use & burner-efficiency of the previous system against base-65F heating degree days over a mid-winter billing period, or a "K-factor" on an oil bill.
To determine the heating degree days over the billing period find a weather station near you on degreedays.net and download a spread sheet spanning the dates, sum the dates of the bill, and divide by the fuel use.
With fuel use per heating degree day it's simple arithmetic to convert that to the BTU output of the burner per heating degree-HOUR. Multiply that constant by the difference between the 65F and the heating design temp, and that's the whole-house load that needs to be provided by the heating system.
EG: Say a house used 238 therms of gas between January 15 and February 13 per the billing, and the degreedays.net total for the billing period came to 1251 heating degree days. That's ~0.19 therms/HDD, or 19000BTU/HDD. In an 82% furnace that's (19000 x 0.82=) 15,580BTU/HDD. With 24 hours in a day that's (15580/24=) 650BTU per heating degree hour.
If the 99th percentile heating design temp is +7F, that's (65-7=) 58 heating degrees, and the whole house load is about (58 x 650=) 37,700 BTU/hr.
A "K-factor" stamped on oil bills is HDD per gallon. There are 138,000BTU/ gallon, so 1/(K x 138000) = source-fuel BTU/HDD, the rest of the arithmetic flows the same as in the example. (Oil burners are typically ~85% efficient when new.)
One can quibble about the numbers being skewed by setback thermostat savings, boiler oversizing factors, burner degradation with age, or fuel used by hot water heating & cooking, solar gains offsetting fuel, etc., but in anything but a superinsulated passive solar house, all those are going to be a single-digit percentage error factor, whereas Manual-J methods are usually well into double-digits for error.
Oversizing the equipment by 15% on a fuel-use calc isn't an efficiency or comfort disaster, even with high-mass boilers, but it tells you just how ridiculously oversized most heating systems are for their actual loads. Oversizing by 15% from Manual-J can sometimes be on the edge not meeting the AFUE tested numbers for cast-iron boilers.
This approach tells you nothing about the condition of the house, or where the heat was being lost or how to improve the situation. It's not an energy use model, it's an in-situ measurement of the energy use, not how it's leaving. The rest of the story is better told by DOE2/BeOpt type modeling than a straight-ahead Manual-J or IBR heat loss calculation methods.
Response to Dana Dorsett
Dana,
The purpose of this series is to introduce readers to the principles behind heat-loss calculations. I am not recommending that readers use the old pencil-and-paper I=B=R calculation method that will be discussed here.
Thanks for sharing your tip about using historical fuel-use data to size a replacement furnace for an existing house. It's a useful method; of course, that method can't be used for sizing a furnace for a new home.
The limitations are understood...
Clearly historical use methods can't be applied to new homes, nor can it properly balance room-to-room heating/cooling load balance issues, but it cuts to the chase on sizing replacement units when dealing with contractors unwilling or unable to run a Manual-J (which would be most of them, in my experience.)
On a new home (or addition) a room-by-room heat loss calc is essential, yet still relatively rarely done except where mandated by law (as in California, under Title 24.) Oversizing hot air furnaces by a factor of 3 is more of a comfort issue than an efficiency issue, but with high-mass boilers or air-source heat pumps it's an efficiency disaster.
Response to several
Another wrinkle is the difference between 97.5% and 99% design temperatures. The 1 % condition is obviously more incusive but may lead to oversizing. Man J has safety factors built in, so resist the urge to add yet more.
It would have to be an awfully big house for a 2 degree delta to add a half ton of cooling load. Cooling loads are driven more by window solar gain, internal heat sorces and air infiltration than outdoor air temperatures. In a related vein, wall insulation R values are relatively inconsequential to cooling loads. Play with a load calc to prove it to yourself.
The comments about microclimates and elevations are well made. It is inappropriate to use temperature history from a nearby airport to model conditions in a nearby wooded suburban setting. Conversely urban heat island conditions must be considered. Nearby water bodies (at least until they freeze over) act to cap temperature swings.
David Martin asks if HVAC subs do load calcs...as of 15 March the 2010 building code took effect in my area, mandating load calculations for system changeouts. This is eating into the margins of the low bid hacks and rewarding those of us who do perform them. If one goes to the trouble of performing a proper load calc, it is a small extra step to add in a blower door test which acts to firm up some uncertainty in the load calc.
Response to curt kinder
"The comments about microclimates and elevations are well made. It is inappropriate to use temperature history from a nearby airport to model conditions in a nearby wooded suburban setting. Conversely urban heat island conditions must be considered. Nearby water bodies (at least until they freeze over) act to cap temperature swings."
The ACCA Manual-J design temps are usually from local airport weather history, whereas degreeday.net or wunderground.com data can be clipped from a range of nearby weatherstations for working the fuel/HDD numbers. I've yet to meet the heating pro who uses factors in proximity a local lake into a heat load calc. Shading shading is primarily a heat gain/cooling load factor, not a heating load factor. Cooling loads are inherently more difficult to assess without understanding the occupancy duty cycle & plug loads- lots of room for error.
Still, using nearby airport weather data (rather than a more local weather station) rarely inserts an egregious error into the heating load numbers for single-family moderate density development the way it might in high-density or high rise urban centers.
If there's a significant elevation delta between the local site and the weather station/airport, using a crude 3F/1000' adiabatic temperature delta model is good enough. Even a 5F delta in the estimated vs. absolute design temp, is still only a single digit percentage error for locations in US climate zones 5 & higher.
The "small extra step" of a blower door test can nearly double the cost of a straightforward heat load calc. In even a moderately tight house the higher precision is not likely to be worth the extra expense unless the client is already committed to retrofit air sealing or hitting a particular BTU/hr or cfm number, which is beyond the scope of most furnace/boiler replacements. On energy use reduction retrofits of a broader nature, or high-R buildings where infiltration rates can dominate the heat load, sure- verification is important.
Back to Design Temperatures
Sorry to take us back, and this may not be the right forum, but since you were talking about design temperatures: I have been trying to get ACCA to change the design temps for Tucson, AZ for some time. We are apparently one of few building departments that require the submittal of a manual J, and we review it. Using a high cooling design temp is one way that contractors game the calculations to increase tonnage of the AC.
The ACCA Design temps come from Appendix D of the International Plumbing Code??? I have no idea when this was last updated and it is a 2.5% temperature...apparently a standard no longer used.. ASHRAE design temps were updated in 2010 and ASHRAE now uses the 1% temperature of 103.6, at least in the table that I recieved from a local mechanical engineer that I called on for assistance. Then, I asked the local weather service to research the 1% temperature and the result was 108 (regardles of the date range of the dataset). From 102 to 108 will make a difference and how do I review a manual J for proper design when the basic design criteria can not even be established?
Response to Rich
The 2011 updated design temps for ACCA Manual-J lives here:
http://www.energystar.gov/ia/partners/bldrs_lenders_raters/downloads/Outdoor_Design_Conditions_508.pdf
Note that the 99th percentile heating temps some areas are less than 1 degree different from other source's 97.5th percentile numbers, but the 99th percentile cooling temp listed for Tucson is 103F, not very different from the ASHRAE 103.6F design temp.
UA Calculation and Temps
Martin, I also have been doing heat loss calculations for decades,(since 1978), and teaching students to do this for the last 20 years. I think this is very important, for them to get a gut feeling for the various contribution of different building components to the overall UA. However, I differ from your and the standard ASHRAE approach in that I think one should not bring in either Design delta T's or HDD until first having done all the UA's (in Btu/hrF). I think it is most valuable to stop and look at the different UA contributions from areas such a Abovegrade basement walls, vs. Belowgrade basement, vs Windows, vs. Infiltration, etc. One can learn a lot by doing many of these, and it is very quick to do by hand once you have the building geometry. Then you get a feeling for what parts of the building are the big contributors.
After having made a complete UA table for all Transmission and Infiltration Loads, then one can go ahead and quickly either calculate Design Loads or Seasonal Loads, using the UA. While many people think that this is the old way to do things, and that computer programs would be the better way, Michael Blasnick's work (as you recently pointed out) shows the opposite.
My students do many of these hand UA calculations every year, on existing buildings close to our campus, and by comparing results among different building types and conditions we get to where we can just do a quick walk through of a building, and with some basic R value info make a very good guess at the overall building UA. It's amazing how much you learn by doing hundreds of these over the years.
Second Point: I am surprised there is so much interest in historical weather data for Design Temps and HDD. Based on local HDD data I have for my area, going back 38 years, we have roughly 20% lower HDD in the last 10 years than we did in 25 years ago. My guess is that the Design temps are also about 8 or 10F higher now than then. Significant climate change has already happened here, and it would be a mistake for us to use the old values.
Response to Peter Temple
Peter,
Thanks for your comments.
In tomorrow's blog (Part 2 of this series), I'll discuss how to calculate heat loss at the design temperature using U-factors of the various building assemblies.
Estimating Leakiness
This article mentions that the location of leaks makes a big difference in the overall leakiness of the envelope. I'm wondering, on an older home (50+ years) that has been professionally air sealed in the most problematic areas (attic penetrations, top plates, rim joists, soffits, etc.) what is the best guess for how leaky the home is by today's standards? Would it likely be "medium" by ASHRAE's definition?
The reason I ask is, I'm trying to get an accurate cooling load calc, and I'm not sure what amount of air leakage to estimate. For my 55-year-old, 2000 sq-ft colonial, the ACH50 was improved from 10.4 to 7.0... from what I understand, 7 is still very leaky by today's standards. However, with the sealing work done in the critical upper and lower areas of the home, would the air changes per hour be much lower under realistic conditions? For what it's worth, before the improvement I noticed that smells would dissipate in maybe an hour, but now we need to run a ventilation fan or smells can stick around for hours! (We had a cat that didn't like to bury his business)
Response to Nathan Efrusy
Nathan,
If you are using the I=B=R method from 1975 discussed in this blog, you can probably define your house as "tight." (The old definition from the 1960s and early 70s noted that tight homes have weatherstripping on the doors and windows.)
Note that the I=B=R method isn't very accurate, especially when it comes to assumptions about air leakage.
If you use a more sophisticated (more recently developed) software program -- one that allows you to input your blower-door results -- you should, of course, use the known results (7.0 ach50) as an input.
Estimating Leakiness (followup)
Hi Martin, thanks for clarifying. I had imagined that the Manual J software that the HVAC guy uses had something similar to the I=B=R method (but by modern standards) for determining air leakage, since most people will not know their ACH50 for existing homes. But if it's good software, it probably has the option to input it directly.
Another related question... if we input 7.0 ACH50, is it likely to overestimate the infiltration load? For example, if all the holes in the envelope are in the neutral pressure plane (i.e. not in attic / basement), would the house perform similarly to say, an average 4.0 ACH50 home where the holes are more spread out? I would certainly input 7.0 regardless, but if it's likely to overestimate infiltration, then I'll keep that in mind with the results.
Thanks!
Response to Nathan Efrusy
Nathan,
If the software was properly validated -- a big if, but validation should be a normal part of energy modeling software development -- then you should input your blower-door result and assume that the software model provides good results.
It's not at all unusual for a blower door test to accompany air sealing work, so a very large percentage -- probably a majority -- of homes that have been blower-door tested have also undergone some air sealing work. Therefore, validation of any type of software that depends on inputting blower door results would involve data from homes like yours.
A variable output air
A variable output air conditioner will help significantly with Manual J inaccuracies.
Link is broken
The link to "the design temperatures for ACCA's Manual J are posted here" is broken. This appears to be the updated file:
https://www.energystar.gov/ia/partners/bldrs_lenders_raters/downloads/County%20Level%20Design%20Temperature%20Reference%20Guide%20-%202015-06-24.pdf
Response to User-6803041
Thanks. I have corrected the link.
Hi Martin,
Thank you for your posts - I am learning a lot by reading them! I'm new to residential HVAC consulting and have a very systematic approach to system sizing and selection, which includes a MJ heat load analysis. There are a lot of computer programs that take into consideration orientation of the house, thermodynamics, R-values, sq. footage of glass, Appliances., and etc. I am currently using is Rheem's Design Star (and I really like it). You can plug in any address and it uses a national database to populate the sq. footage of the house. Afterwards, you need to have a conversation with the homeowner to finish populating the necessary information to complete the heat load. With that said, would you recommend or suggest a specific program or software which would provide accurate results? Thanks in advance for your feedback!
Log in or become a member to post a comment.
Sign up Log in