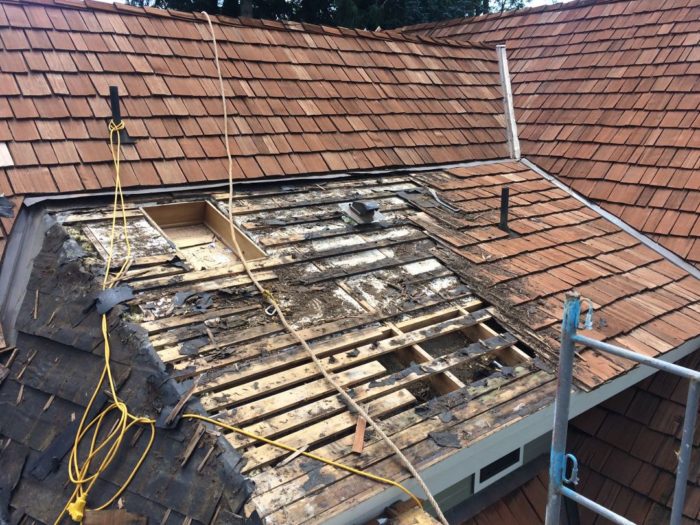
Image Credit: Chuck Kramer
Chuck Kramer’s home in Enumclaw, Washington, was built in the 1980s with unvented cathedral ceilings, insulated with cut-and-cobble rigid foam insulation and roofed with cedar shakes. A small section of the roof is showing signs of water damage, and now Kramer is trying to find a way of repairing the problem area without tearing into the rest of the roof.
As Kramer explains in a Q&A post at Green Building Advisor, the trouble seems to be in an area measuring about 150 square feet. This part of the roof, with a slope of 4-in-12, is surrounded by two other roof areas with a 12-in-12 pitch.
From inside to outside, the roof assembly consists of 2×6 tongue-and-groove boards, 15-pound asphalt felt, 2×6 rafters, 1×4 skip sheathing, and cedar shakes interwoven with strips of 15-pound asphalt felt. The rafter cavities are insulated with two 2-inch-thick layers of foil-faced polyisocyanurate foam insulation and 1 inch of Styrofoam beadboard.
“Most of the roof is 12/12 pitch,” he writes. “A small section above two bathrooms is 4/12, with two 12/12 pitches joining two sides with valleys. In that section, a skylight was cut in after initial construction, maybe in the late ’80s… The 1x4s [the skip sheathing] and a small part of the tops of the rafters are damaged by rot, particularly badly around the skylight.”
Kramer doesn’t see how he can increase the thickness of the low-slope portion of the roof without affecting the steeper parts of the roof. His proposed fix is to pull off the 1×4 skip sheathing, add a 1/2-inch layer of OSB with a peel-and-stick membrane, then a layer of 30-pound felt, and metal roofing. The 5,000 square feet of 12-in-12 roofing will not be affected.
Inside, he’s improved the bathroom fan capacity and covered the tongue-and-groove ceiling with drywall.
“In the long run,…
Weekly Newsletter
Get building science and energy efficiency advice, plus special offers, in your inbox.
This article is only available to GBA Prime Members
Sign up for a free trial and get instant access to this article as well as GBA’s complete library of premium articles and construction details.
Start Free TrialAlready a member? Log in
10 Comments
Oddball question?
With no specific response to the photos, is there ever a case for continuing insulation all the way out to end of overhangs, beyond the conditioned envelope? As an extension to the initial question, should one ever consider insulating a porch roof--especially when that roof extends from over the conditioned space?
One can certainly stop roof
One can certainly stop roof air ex-filtration by reducing building pressure. Cost effectiveness is up for debate.
Response to Antonio Oliver (Comment #1)
Antonio,
Q. "With no specific response to the photos, is there ever a case for continuing insulation all the way out to end of overhangs, beyond the conditioned envelope?"
A. Yes, of course there is (assuming we are talking about rigid foam installed above the roof sheathing). Even though there is no need for insulation over roof overhangs, you'll still need some type of shim or material to make the surface co-planar. If you need 2 inches or 4 inches of material over the roof overhangs for this purpose -- to match the thickness of rigid foam on the main area of the roof -- the cheapest way to proceed (considering both labor and materials) is usually to just extend the same type of rigid foam you're using for the rest of the roof.
Q. "Should one ever consider insulating a porch roof--especially when that roof extends from over the conditioned space?"
A. The same analysis applies. For a small porch, extending the rigid foam may be the easiest way to proceed. If it's a large porch, it may make sense to raise the height of the porch rafters, or to add 2x4 sleepers of some kind, over the porch instead of shimming with rigid foam.
SIP panel roof
GBA has covered rot in SIP roofs and lessons-learned: moisture will get into the assembly. This may not have the top sheathing of a SIP, but close enough to consider the side-effects. Might want to consider treating similarly with vapor relief at the upper end. Otherwise, the 2x's might see similar fate. The work also appears to be above a bathroom (more moisture than normal); upsized bath fan might help a little.
overhang insulation
Some say that the sun warms the walls and this heat rises to the overhang area and causes ice dams.
https://buildingscience.com/documents/insights/bsi-046-dam-ice-dam
Response to Jon R
Jon,
Good point. In case GBA readers missed Jon's point -- which he didn't make explicitly -- here it is: insulating a roof overhang on the south side of a house can limit potential ice dams caused by solar heat gain on the south-facing siding.
I thought COLD eves create ice dams... (5, 6)
My understanding is that the snow melts on the warm roof and runs down to the cold eves. Warm eves should be a way to stop this, as evidenced by folks installing heating cable on their eves...
NOT a SIP! (response to 4)
Isn't the issue with SIP roofs the fact that they leak at the joints if those are not well-sealed? The owner, here, is attempting to create a jointless SIP (well, IP) and that seems like the perfect solution.
My only question here is using tape for sealing to the insulation. This SHOULD work, at least with foil-faced isocyanurate, but I'd prefer something like Grace Ice and Water Shield, especially for making the air-tight tie to the other sections of roof when those are eventually modified.
Response to Skip Harris (Comment #7)
Skip,
If you want to prevent ice dams, the best approach is to design a roof system that results in uniformly cold roofing -- from the eaves to the ridge. The colder the roofing, the better the roof system will resist ice dams.
Installing heating cables at the eaves to melt accumulating ice is a band-aid approach that wastes energy. GBA has never advocated the use of heating cables at eaves to address ice dams.
If solar heat gain (on the siding) is warming the eaves, the heat can melt snow sitting on the roof. In some cases, the liquid water resulting from this snow melting process can freeze in the evening, setting the scene for ice damming problems. One way to address this type of solar heat gain is to insulate the roof overhang, to separate the hot soffit from the roofing above.
Response to Skip Harris (Comment #8)
Skip,
You are right that this house does not have a SIP roof, and that the problems encountered here differ in important ways from problems with leaky SIP roofs.
That said, there is a basic lesson here: Any time a builder attempts to seal a crack with canned spray foam -- whether the crack is between two adjacent SIPs, or whether the crack is between rigid foam and a rafter in a cut-and-cobble installation -- it's worth remembering that air leakage is still possible. Canned spray foam in this type of seam is not a long-term solution in a roof system.
Log in or become a member to post a comment.
Sign up Log in