Image Credit: All photos: Kent Earle
Image Credit: All photos: Kent Earle Floor joists rest on steel beams that are set into recesses cast into foundation walls. The beams were lowered into place with a crane. At the foundation wall, joists are supported by metal hangers. In this scenario, joists are supported by framing members completely inside the building envelope, eliminating the potential for thermal bridging.
Editor’s note: Kent Earle and his wife, Darcie, write a blog called Blue Heron EcoHaus, documenting their journey “from urbanites to ruralites” and the construction of a superinsulated house on the Canadian prairies. Their previous blog on GBA was called Making an ICF Foundation. The blog below was originally published in June 2015. (A complete list of Kent Earle’s GBA blogs is provided in the “Related articles” sidebar below.)
We had always intended to use our well as our source of drinking water and domestic hot water use. It had simply made sense to us all along. It seemed to be the most sustainable and logical thing to do.
The only problem was that our water… well, it sucked.
It was very strange to think that our water would be so crappy. We live right on the river. It is our front yard. You’d think the water would be good. Our house is perched about 50 to 60 feet above the river, but our well is, bizarrely, 140 feet deep. (Interestingly, as for our neighbors, one could not find water on his land, another had to go down 250 feet, and a third only 20 feet. It’s so strange how in a two-mile radius everyone can have such different water tables, even with all of us are along the river).
We’d had our well water tested when we first bought the land to make sure it was potable. It was, but it really tasted bad. I was also worried because it had caused serious damage to our hot water element in the shop the year before — completely corroding it.
Treating the water is expensive
The only real option for treating the water was a process called whole-house reverse osmosis. This type of system is just one step under complete distillation of water in terms of intensity of water treatment. It is major. It takes a lot of equipment and processing, and is very expensive (in the range of $12,000 to $14,000 for the initial setup, not including the regular cost of filters). It basically demineralizes the water; demineralization is bad for pipes and potentially bad for us. It also wastes a ton of water. When everything was considered, the cost of treatment using a whole-house reverse osmosis system would have been $40,000 or so over 15 years.
The alternative was to have water delivered by truck. I had thought this was completely dumb at first — why would you do this if you had a well? But after further consideration, this seemed to be the only logical thing to do. And some simple cowboy math showed that paying for water delivery will be way more affordable than the well option — at an anticipated cost of $150 a month, buying water will cost a total of $27,000 over 15 years.
Even if we did not try to be conservative with our water use, this option is much more affordable then the reverse osmosis water treatment option.
Where will the tank go?
If we were going to be buying our water, we would need a tank. We were given two options:
1. Put a concrete water tank underground, or
2. Put a big water tank in your mechanical room.
The in-ground tank is good if you don’t have the space in your house, but due to trenching, the cost of the concrete tank itself and piping required, this option comes in at about $6,000.
Option 2 was a lot cheaper. The indoor tank is a heavy-duty poly plastic that costs about $1,000. I like saving money, so the latter seemed to be the better option.
I have to admit, though, that I did not have as much time to research this as I would have liked, because we had literally two days to decide. (I talked to our neighbor and a friend who both use the indoor tank and have no complaints, as well as some suppliers, the water delivery companies, and contractor who installs the in-ground tanks).
The foundation was done and the floor joists were being installed. (You can’t fit a 2,000-gallon tank through the front door; it must be installed on before the main floor joists are in).
Racing against the framers
At 1:00 p.m. on Monday, we finally decided that we were going to install the water tank in the mechanical room. We had gone to view our neighbor’s setup and talked to him about his experience. It all seemed good enough. But meanwhile, the crane had shown up that morning and lowered the giant steel beams into the walls of the foundation.
I had watched the crane go to work in awe, like a little kid — “Wo, a crane!” It was pretty awesome to see the crane towering over our trees and lowering the steel beam into the pockets that Taylor and Curtis had left when pouring the concrete a couple days earlier.
It was an impressive sight to see. The beams slid in so effortlessly. (See Image #2, below).
Within a few hours, the guys were hanging the joists and starting to the lay the floor. You’ll notice that the beams and all of joists are within the envelope of the foundation walls. This was intentional from an energy-efficiency point of view. There is no thermal bridging at all with this system. Oftentimes typical houses are built with the joists sitting on top of the concrete wall or on a ledger of the wall. Both of these are a bit more work then simply using hangers. And the former, requires excessive use of spray foam to seal.
The way we did it required a taller basement wall, but there is zero chance of air leakage, thermal bridging, or unusual heat loss with this approach.
Anyway, the carpenters were working fast. Crap, Darcie and I realized, we had to decide immediately whether or not we were going to have the water tank in the basement. The carpenters were going to be done the floor system the next day, which meant that the tank needed to go in the basement now.
I made some calls and found a manufacturer east of Saskatoon who sold large tanks. We hopped in the truck and made the 45-minute drive. We had debated briefly about what size of tank to get — essentially everyone we talked to told us to purchase the largest tank that would fit in the house. That meant we could get a tank with a capacity of 2,100 U.S. gallons — one that measured 88 inches by 88 inches. If you can’t picture that — well, it’s big.
We drove back to the land and within a couple hours were ready to haul the giant beast of a tank into the basement.
Without a crane, improvisation
Only problem was the crane was long gone, and there was a huge gorge — 11 feet deep and 6-feet wide — all around the perimeter of the house. The four of us put our heads together. We all agreed that it would have been a lot better to have done this when the crane was here.
The options were slim. The only possible way was to jimmy up a rickety makeshift bridge between the foundation and the ground using 2x10s and some leftover joists. We decided to push the tank off of the trailer (there was no way to carry it) and roll it to the side of the gorge. From there we wrapped two large ratchet straps around the top of the tank and lashed them to the back of my tractor.
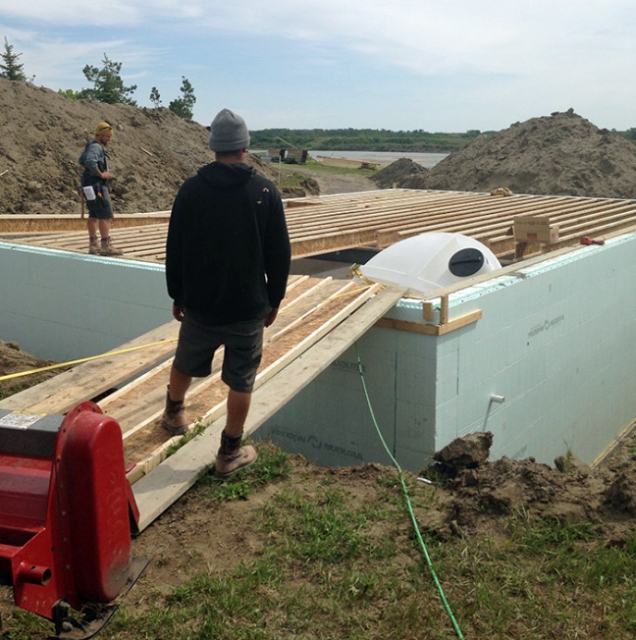
Now came the dangerous part: Taylor and Curtis pushed the tank onto the shoddily crafted bridge (one false step would mean certain death or at least dismemberment) while I slowly backed up the tractor, thereby keeping tension on the straps and allowing the guys to ease the tank across the “Bridge of No Return.” My wife cringed as she watched the bridge bow under the weight of the tank and guys.
Miraculously no one was killed. Not even a little bit.
Once we had the tank to the edge (Taylor had also built a small ramp on the inside of the foundation), I could simply back the tractor up and lower it down. That went well.
By the end of the day, the guys had the floor framed — pretty impressive. They’d poured the basement on Friday and the floor was framed and sheeted with subflooring by Wednesday. Time for a dance party.
We all grabbed a beer to celebrate, and as we were standing there, an eagle flew by carrying a fish. We were all in awe, and Curtis said, “And this is where you guys live?” It was awesome.
P.S. One more geek/nerd energy efficiency thing: They wrapped the house in the waterproofing seal, but also wrapped the membrane up to seal the seam between the foundation and the plywood wall sheathing, creating a complete seal around the entire basement. It is possible that a small amount of air leakage could occur through the plywood and the top of the joists and foundation wall. This simple trick tightens the house up even more.
Weekly Newsletter
Get building science and energy efficiency advice, plus special offers, in your inbox.
11 Comments
Osmosis was the only alternative solution?
TBH I'm amazed that a water softener with a charcoal filter couldn't get the job done. I grew up on hard well water that was treated with a softener but we didn't need to filter for taste.
Tank Weight
The full water tank weighs around 16,600 lbs, exerting somewhere round 400lbs psf on the substrate. Were any allowances made in the slab design for this large point load?
Deeper well?
Does anyone in the area have a deep enough well that this problem could have been avoided? I just had a 400' deep well installed for less than $6000.
Would a rain water collection system, coupled with filters, have worked? I can't imagine paying for trucked water. On the other hand, you could just drink beer.
400 lbs per square foot is nuthin' for a slab (@ Malcolm Taylor)
400 lbs per square foot ( /144 ) is 2.8 psi. A 2000 lb car parked on a garage slab is delivering much more concentrated pressures than that, and strangely, it doesn't break the slab.
The dynamic load of 200 lbs. Czech doing a polka would be delivering even more stress to the slab than the car, and at least an order of magnitude more than the tank.
Dana,
That's an interesting way to look at it, but is at variance with how residential codes approach loading. The bearing capacity of the soil below would have to be a minimum of 2500 psf, and presumably the foam underneath would easily carry 400 lbs/ft too? However you can't bring down any point loads onto a slab without thickening it or providing a pad underneath. Residential slabs are presumed to be capable of carrying around 40 lbs/psf live loads, not ten times that amount.
Residential Treatment Options
Chris M - If they bumped the budget up an order of magnitude or so, a lot more treatment options start opening up. There are a lot of things that a charcoal filter won't take out; if you have to deal with something that's not handled by one of the common, standard residential filters then it's straight to reverse osmosis because the alternative is tens of thousands of dollars (at least) of lab work & design to identify the appropriate treatment (which still isn't guaranteed not to be reverse osmosis).
About a year ago, my previously excellent tasting well water picked up an astringent (dry mouth-feel) quality to it. Charcoal filters didn't affect it, and a few hundred $ on water tests eliminated all the standard suspects. At that point... you're stuck. I tried and failed to find any alternative (even cost-ineffective ones) to 5 gallon bottle delivery or reverse osmosis (which would remove all the delicious chalk and leave us with even less appealing water). Luckily, just when I had given up hope and resigned to my fate, our water returned to its former glory.
Water options
Tim C., is correct. We had our water tested by four separate testing agencies, including a lab at the local University. I would have to go back and look at the exact details of what all of the particles were, but the major one was sodium - and there was an absolute tonne of it…. something in the range of 50x more than the allowable limit. So it wasn't that our water was hard, but that it was extremely soft. It tasted like a brine bath and left terrible salt stains on anything it touched.
So with this particularly bad substance typical treatment options are essentially useless (we also had tannins and other particles that weren't great, but on their own could have been managed). We were only left with distillation or whole house RO, which have their own set of issues and very high price tags (with no guarantee that they will do their job for very long - we were given quotes of a 5 year warranty… when spending $15,000 on something as important as your drinking water, that simply was not reassuring).
Stephen, we did consider getting someone in to look at a deeper well. No one has gone deeper than 250' deep. I might wait to see what other people do when they settle out here though. And to be honest, we are very happy with the hauled water that we've been using for the last 6 months since moving into the house. We're using less water then we'd thought so our cost is only $100/month to have clean, tasty and treated water delivered to our (we paid $90/month when we lived in the city).
Slab loads
The water tank is in the corner of the basement in the mechanical room. Our basement is on a structural slab with pilings (piers). I think I woke up one night in a cold swear worrying about those loads on the slab, but was reassured by the structural engineer that there would be no issues. Mind you, my neighbour has a smaller tank of 1300 gallons in his standard slab basement and has had no issues in over 16 years.
Kent,
I figured you must have thought about it as your foundation was engineered. No harm in having water storage on hand even if you did have the well functioning. Don't want to jump ahead if you deal with it in later blogs, but have you considered more storage to collect roof water for irrigation, or do you just tap into the river?
Irrigation and rain water
Malcolm -
Yes, we have three rain barrels currently that collect rain water from the very large metal roof. We use this water for our chickens and for watering plants inside and outside the house. For irrigation, we have a pump at the river with drip lines to our trees. I'll be trenching over a water line from the pump to the garden this summer with shunting at certain spots so that we can water around the house as needed (although we are using drought resistance natural prairie grasses, so hopefully the grass irrigation will only be needed to help it germinate when we seed it later this year).
To Kent Earle
Kent,
Have you read the recent article by Bronwyn Barry, in which she make suggestions for reducing the amount of energy used by your home? There are comments below the article as well. Here is the link: A Lesson From the Kranichstein Passive House.
Log in or create an account to post a comment.
Sign up Log in