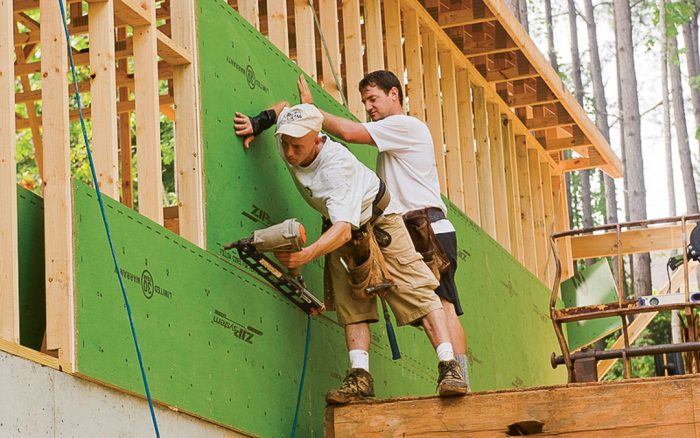
Wall assemblies that are both well insulated and free of long-term moisture problems are a frequent topic for the Q&A Spotlight. Hasn’t this subject been raked over enough in the past to answer just about every possible question?
Not according to Nat, a GBA reader and structural engineer who is planning his own house in Climate Zone 5. Even after poring through GBA and other websites, Nat finds himself uncertain about the planned wall assembly on his budget-conscious new home.
The house design is simple. A plain box with a gable roof and a full basement, roughly 1,100 square feet per floor. Nat wants to keep detailing as simple as possible. His plans for exterior walls include clapboard siding over a rainscreen, then Zip R-9 sheathing—a combination of OSB and polyisocyanurate insulation—and a 2×6 wall insulated with mineral wool batts in the stud cavities.
“Despite a lot of reading I’m finding a hard time getting full comfort with the Zip R-9,” Nat writes in a Q&A post. While the ratio of batt insulation to exterior rigid insulation appears safe, the insulation rather than the OSB becomes the condensing surface should moisture move through the assembly.
“I see plenty of drawbacks with the Zip-R and I know it’s probably not the best R for my money—but I really like how it seems to involve very little atypical detailing and very easy to make sure it’s well executed,” Nat says. “Is this a safe and reasonable assembly for my zone?”
That’s the key question here, but Nat’s initial post opens the door to other options, such as the pros and cons of an exterior layer of insulation over the sheathing. For more on those topics, use the link above to check the full text…
Weekly Newsletter
Get building science and energy efficiency advice, plus special offers, in your inbox.
This article is only available to GBA Prime Members
Sign up for a free trial and get instant access to this article as well as GBA’s complete library of premium articles and construction details.
Start Free TrialAlready a member? Log in
31 Comments
An article on creating SAFE wall assemblies uses a picture of someone being obviously UNSAFE in creating a wall assembly...
What's unsafe? Unless the drop is a lot higher than it looks no fall protection is required.
Seems to be!
The deck has a rotted joist, the framers wearing a wrist split, and the guy behind him more likely to push him off the deck accidentally than help in a meaningful way.
You guys do much framing?
- You have no way of evaluating whether what they are standing on is safe from the photo.
- It's two man sheathing crew. They both position the sheet, then one holds it in place while the other nails it off. That's h0w it's done.
- One guy has a wrist brace. Probably for carpal-tunnel, something that is pretty common among carpenters. If you looked around the site there is also probably someone with knee-brace, finger-splint, maybe some stitches. If you test the crew they also all will have some hearing loss. So what?
I'm left shaking my head that either of you would comment disparagingly on something you know so little about.
BTW, regardless of the height, any fall in that position carries the possibility that he discharges the nail gun into himself....google nail gun accidents to see the creative ways and places all you "experienced" framers have managed to "nail" the landing....
Framing nailers have safety noses. Unless he is walking around with the trigger permanently depressed, and modified to fire "bump" he can't shoot anything.
Let it go.
Looking closer at the stock photo, in the background a handmade wall bracket can be seen. While this may not be against OSHA reg, it's not best practice either-steel wall brackets and staging exist and can be quickly assembled.
I've seen a few people forget they're shooting ply nails when building outriggers to install sheathing etc, only to have it collapse when the first OSHA plank gets slapped down on it.
Great discussion!
Looks like a platform built for a skylifts hooks.
Good catch. I couldn't figure out what that was in the background.
It is an elevated mobile work platform..Osha regs require railing on that platform and a harness on the worker. Ignoring that, he is overextended beyond his balance point (his toes are extended way over the edge of the mobile platform - your toes are a major part of sustaining your balance) with a heavy object in his hand only contributing to the out of balance situation. It is obviously unsafe, the only question is how unsafe it is based on the fall height.
At approximately 11:00 a.m. on February 16, 2013, Employee #1, a 33-year-old male with Slone Builders Inc., was performing residential framing activities. Employee #1 was working in the garage area framing up a wall with a pneumatic nail gun equipped with a contact (bump) trigger. The nail gun appeared to misfire/double-tap which caused the employee to lose his balance and the nail gun to come in contact with his face. This caused an unintended discharge of the nail gun. The nail passed through the employee's eye socket and into his brain. Emergency Medical Services transported Employee #1 to the hospital where he later died from his injuries.
A quick read of Scott Gibson bio doesn't mention of any trades experience. He's in publishing.?
there s typos also.. Is this real?
Come on with this smoke screen, enough
Seems to be about 10 people that keep this website propped up.
Junk status. Can Scott Gibson pull a 16" layout?
James,
This is a website dedicated to information on energy efficiency through high performance building techniques, with a large library of useful articles, blogs and related news.
The reason I commented on But Why and your posts on safety was that they are sideshows. Over the years But Why has sporadically posted comments that invariably mock green initiatives or alternate energy. I can't remember him ever contributing constructively to any of the discussions around high performance building, and I'm at a loss to understand why he comes to GBA. You now seem to be happily embarking on the same path.
Scott Gibson is a journalist. So was Martin. Maybe Scott can't pull a layout. I don't know - and it doesn't matter. So far I don't see any indication you have any useful knowledge about building assemblies for high performance houses. If you are here to learn, great. If you have something to contribute, better still. Otherwise, are you sure you want to stick around?
> I would not be worried about interior vapor making its way through the insulation to the OSB
People only taping the exterior of SIPs used to think similarly, with sometimes disastrous results. Turns out that moisture flow at the joints (where the OSB/tape IS the "condensing surface of interest") matters. Think about the amount of moisture diffusing through a large area of Class III on the interior and then concentrating in the small cold tape area. Or air flowing from the interior, dumping moisture in the cold joint and then either continuing through a leak or returning to the interior. Zip-R is not hygrothermically equivalent to taped OSB with exterior foam. I'd take additional steps to control the amount of moisture coming from the interior (eg, interior side air sealing and a Class II vapor retarder). But who knows if it will be enough. Summary: don't use 1D mid-panel analysis alone to declare an assembly safe.
> R7.5, still meeting code
Except that it doesn't meet the code requirement for "over" the wall. Zip-R foam is inside the wall.
Huber could pay BSC to instrument/measure houses built with a mix of Zip-R and other common wall assemblies. I find it odd that they haven't. And that they don't publish full perm vs %RH information (a sorption isotherm does not indicate permeability).
This should be useful to people looking for a simple pass/fail (although I wouldn't use it for the unusual Zip-R).
https://www.appliedbuildingtech.com/fsc/calculator
"Turns out that moisture flow at the joints (where the OSB/tape IS the "condensing surface of interest") matters". I've been wondering this same thing but have not found an answer. It seems that there is an inherit flaw where warm moist air from the interior can go through the air permeable batts, goes between the polyiso sheets at the joints, and then hits the back side of the tape used to seal those joints, which is a cold surface and condenses onto the tape/OSB. Does Huber say anything about this? How would would one air seal the back side of the polyiso, spray foam? That seems problematic as the joints cross behind studs. If you need to spray foam the joints it also seems to make the tape redundant.
“His structural engineer insists on a site inspection of Zip-R panels.”
Let’s worst case if you do pay the structural engineer to inspect and they decide all 120 nails in most panels we over driven.
What is the remedy? Could an engineer risk recommending add more nails between the ones there now you have nails 1.5 inches on center in compromised OSB. Would that wall now be an become an untested system with the engineer being proficiently responsible for any problem?
Or will he play it safe and recommend pulling 128 nails from each panel and replace them all.
Walta
Malcolm, the stock photo is bogus. That helper aught to be put on clean up. I can eat a sheet of zip for breakfast by myself.
You have no evidence to discredit me either.
Good day!
I don't understand the worry about condensation getting through the polyiso to the OSB sheathing when this same surface touches all the studs directly?!
Steve,
The studs touch the foam on the warm side - hopefully warm en0ugh that the foam doesn't become the first condensing surface. Any moisture that gets to the OSB will find that sheathing close to the same temperature as the outside.
Malcolm, Peter Yost's comment in the article is that the polyiso interior would be the first surface, where condensation will occur. I worry a lot less about the OSB than the condensation inside the stud cavity against the structural framing.
Peter seems to be saying that in a wall with permeable insulation, the foam is going t0 be the first condensing surface no matter what. I'm struggling with that. What if there was 24" of foam? Would the interior of it still be the first condensing surface?
My (possibly flawed) understanding is that the first condensing surface is the first/coldest/least permeable surface. It's the combination of features that does it. Most of the time, you can guess what that surface is going to be, but as Joe L has pointed out, since it varies based on so many properties, you could be wrong.
Take the case of a Zip-R wall with drywall, fluffy insulation, Zip-R, perhaps a permeable housewrap because you don't trust Zip sheathing, a rain screen, and siding (Whew!). The polyiso insulation in the Zip-R is the least permeable material in the stack, at just shy of 1 perm. The interior surface of the Zip-R also floats near the dewpoint of the interior air at the design conditions for the house in question. Together, these features make the surface of the polyiso the "first condensing surface." So your answer is, yes, even with 24" of foam, the interior surface would be the first condensing surface - with that much foam, you would never get any condensation but that doesn't matter.
I share Jon R's concern about the taped seams, but I do point out that there are significant differences between this wall and a SIP roof. First, walls and roofs see much different air pressure drives. Stack effect makes roofs always see positive pressure from the interior. Walls are more variable and closer to the neutral pressure plane. Also, with early SIP construction, there was generally no attempt made to control air leakage at the interior. I think that, for the purposes of this discussion, we've pretty much agreed that an interior air barrier is a good idea. I think that interior air sealing is always a good idea. Finally, a lot of the SIP failures also had other stresses that can be managed. Some of them were in very cold climates, not CZ5. Some of them were also associated with high internal RH, and Scott mentions that as a risk factor in his article. High interior RH can be a problem for nearly any wall or roof system.
After all the discussion, I'm still not backing away from my first impression. For the OP's conditions, his wall should be safe. He's comfortable with the structural and installation details, and his climate zone is not that harsh. If he takes the further step of installing a smart membrane as an interior air barrier, that makes the wall a bit safer. As long as he reads his framers the riot act about nailing the Zip, he should be fine.
Malcolm: it really is better to use Joe L's term “condensing surface of interest”. Locations that reach condensing temp but don't accumulate moisture are not "of interest". Accumulation is avoided if a) moisture is blocked from getting there and/or b) moisture gets there but keeps on moving outwards (ie, drying >= wetting or flow-through).
Jon,
That's helpful correction. I'd add to your list of things the stop accumulation that the material is sufficiently warm. That's why the drywall wouldn't accumulate moisture, even if it was backed by an impermeable vapour-barrier.
To bring this to bear on Steve's posts:
- If the inner-surface of the foam isn't below the dew p0int of the moist air in the cavity, it wouldn't accumulate surface moisture or wet the studs that are in contact with it.
- If it is close to the dew point, it as both Peter E. and Jon stress, reducing the moisture that gets to the foam with inner air and vapour-barriers so that the drying exceeds wetting becomes much more important. Otherwise as Steve fears, there could be damage to the framing members.
- Because the exterior OSB is protected by the low-perm foam, the amount of moisture it accumulates from the interior can be dissipated by the drying to the outside afforded by a rain-screen cavity.
Fair?
I wonder if this is a time when an air-tight but vapor open tape definitively adds insurance? I know that would be odd to pair a non-zip tape with a zip product...
The seams are the weak points and also the precise location where drying potential matters, and also the point where a low perm product is applied. In theory, the backside of the tape could be considered the first relevant condensing surface.
Tyler,
You are on the right track. If the tape is more vapor-open than some other part of the stackup, then condensation on the backside of the tape would be unlikely, regardless of its temperature. This would alleviate some of Jon's concerns. However, the use of a non-Zip product would void Huber's warranty, at least for that detail. That may or may not be a big concern.
I would think that, if Huber had any evidence of this sort of condensation causing problems, they would address the issue, either through the use of more vapor-open tape, sealing the insulation edges, or other methods. It seems that Huber has some pretty smart engineers working for them and that they are planning on being around for the long haul.
> If the tape is more vapor-open than some other part of the stackup.
Like a diffusion port. But you need to do a 3D analysis. For example, say there is moisture diffusing in from 32 sq ft of 10 perm drywall. But with 1/8" joints, that same area has only 1.5 sq ft of exposed Zip tape. Not enough drying, even if the tape were 50 perms (does Huber even provide a tape perm spec?).
Zip-R may work well, maybe even without a Class II and interior side air sealing. But IMO, there is a real lack of good data and analysis proving this.
Good day all,
I’ve enjoyed the insight thus far.
Rhetorical question:
Wouldn’t dense packing the cavities with cellulose be a nice pairing with this system, providing some mitigation for changes in the interior RH? I believe I have read a good GBA article illustrating this potential benefit. To be clear, we are in the Pac NW Zone 4, so, our vapor and temperatures dynamics are a bit easier to manage.
Additionally, I realize that dense packing to 3.5 lbs/cu ft may provide some air slowing, and not air sealing, but our blower door test results always improve when we test again after insulating. This, plus cellulose’s sorption properties, could, perhaps, provide a little extra confidence with regard to the condensation surface at the seams.
And it’s made from recycled newsprint; not too bad.
Good luck with your project.
Agreed, cellulose provides hygric buffering/redistribution and this is beneficial when condensation occurs inside the wall. Either at the joints or mid-panel (continuous foam reduces but usually doesn't eliminate reaching the dew point).
The other extreme would be moisture condensing on Zip-R and not being absorbed by the polyiso or hydrophobic mineral wool. I expect that this leads to water on the base plate and more accumulation in the OSB at the joints.
Is this a risky assembly from the standpoint of insect intrusion? If carpenter ants like damp foam, and moisture condenses on the polyiso, then seemingly this would create an ideal environment. I wonder over 10 or 20 years whether enough damage could occur to the foam to create areas of loose fasteners where the sheathing isn't tightly sandwiched to the studs anymore.
Michael,
My experience is that carpenter ants like foam period, not just the damp stuff. So I'd suggest the question is whether the foam in the assembly is susceptible to insect intrusion, not whether the moisture content makes it vulnerable.
https://www.greenbuildingadvisor.com/article/if-ants-like-rigid-foam-should-we-stop-using-it
Log in or become a member to post a comment.
Sign up Log in