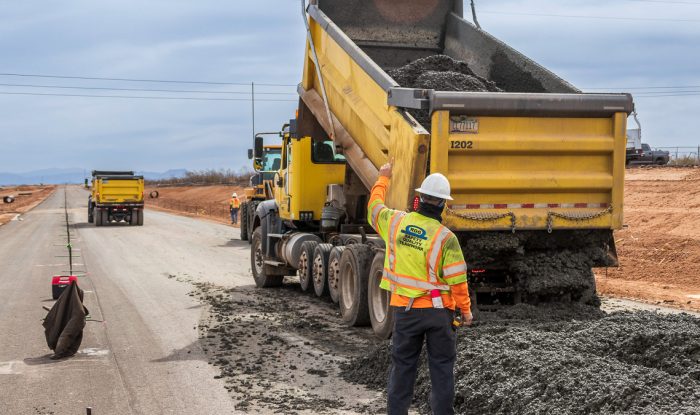
When it comes to the Inflation Reduction Act, we shouldn’t sully good intentions, nor should we pave the road with them, literally.
Last March, the Federal Emergency Management Agency (FEMA) announced it will provide additional funds to states, tribes, territories, and local communities that rebuild using low-carbon construction and building materials in the wake of natural disasters. The IRA authorizes FEMA to foot the bill on “eligible” low-carbon materials, through 2026, via the agency’s grant programs, even when the low carbon options are costlier than the standard ones. The eligible materials in question are concrete, steel, asphalt, and glass with a reduced Global Warming Potential (GWP) compared to industry averages in North America. So far so good.
Climate resiliency is now part and parcel of FEMA’s broader mission, and this comes not a moment too soon. Within the last ten years, six were the costliest in terms of cumulative climate disaster events since the agency began recording such numbers in 1980. (The years 2021 and 2022 rank #4 and #3, respectively, each surmounting $150 billion.) Peruse the various tentacles of fact sheets, press releases, and FAQs interrelated to the IRA and you will inevitably stumble upon language about “whole community resilience” and advancing a “clean energy economy.”
Quality of materials
There is some bite to FEMA’s new policy. The agency has backdoor access to the federal government’s enormous annual purchasing capacity of $650 billion. And thanks to the Biden-Harris Administration’s Federal Buy Clean Initiative, there’s newfound incentive to procure U.S.-made, low-carbon construction materials. The question is whether that bite has teeth. And that might all come down to the efficacy of low-carbon materials.
“The stronger your concrete is, the longer it’s going to last,” says Chris Bennett, owner of Bennett Build, a Portland, Oregon-based consultancy focused on sustainable concrete…
Weekly Newsletter
Get building science and energy efficiency advice, plus special offers, in your inbox.
This article is only available to GBA Prime Members
Sign up for a free trial and get instant access to this article as well as GBA’s complete library of premium articles and construction details.
Start Free TrialAlready a member? Log in
0 Comments
Log in or become a member to post a comment.
Sign up Log in