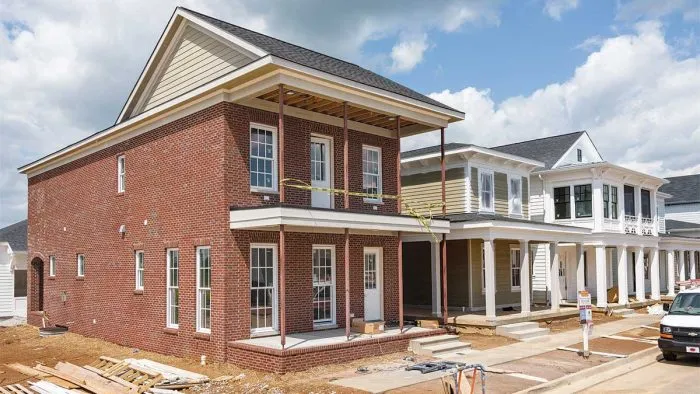
Two reports on more than 500 newly constructed homes in Canada confirm earlier studies showing that the selection of building materials dramatically affects the climate impact of residential construction, outweighing the importance of energy efficiency for decades after the house is built.
Results suggest that the choices builders and designers make about foundations, insulation, cladding, and other materials are far more important in lowering carbon emissions in the near term than the energy it will take to operate the houses. With scientists warning that sharp reductions in carbon emissions are essential in the coming decades, the research shows that choosing low-carbon materials can have a bigger impact on global warming and climate change than building net-zero energy houses.
Researchers looked at 537 as-built houses, in British Columbia and in the Toronto area, and analyzed the embodied carbon in materials used to construct them. Housing units represented a range of styles and sizes, as well as different levels of energy efficiency.
Chris Magwood of Builders for Climate Action, which helped carry out the research, said that the importance of embodied carbon has come into sharper focus in the last several years, but emissions related to the operation of the building are still significant.
“The overall message I keep wanting to bring, especially to municipalities who are thinking about this, is please don’t think of these two things as isolated metrics,” he said in a telephone call. “You can’t pursue one without thinking of the other, and vice versa. It isn’t always about energy efficiency and it isn’t always about materials. It’s always kind of a play between the two.”
Before anyone moves into a new house, the building is responsible for an average of between 30 and 40 tons of greenhouse gas emissions. Material carbon emissions for an all-electric new house will be greater than the operational emissions for about 60 years; material-related emissions for a new house heated with gas will outweigh its operational emissions for about 15 years, Magwood said.
The results mirror earlier work, including a 2021 report for Natural Resources Canada, that found embodied carbon in building materials (what is called Material Carbon Emissions or MCE in the reports) can outweigh operational carbon emissions (OCE) for as much as a century-and-a-half where the electrical grid is relatively clean. The findings are getting more attention as UN’s Intergovernmental Panel on Climate Change and others continue to warn of the looming climate crisis.
“The very short amount of time available to meet Canada’s emission reduction targets of 40‑45% below 2005 levels by 2030 requires us to consider all of the emission impacts from the housing sector and focus effort on those sources of emissions that have the greatest immediate impact on our remaining carbon budget,” the introduction to one of the two reports says.
The smaller of the two studies, which analyzed 34 homes in Nelson and nearby Castlegar, British Columbia, was prompted by concerns that some materials used to build high-performance houses might be responsible for high levels of greenhouse gas emissions. Houses insulated with lots of spray polyurethane foam, for example, used less energy for heating and cooling, but come with a high carbon price tag.
Researchers discovered that energy-efficient construction was not necessarily a predictor of carbon content. “There were high-efficiency buildings with low embodied carbon, and low-efficiency buildings with high embodied carbon,” Magwood said. “It was more that the materials you chose to make the building more efficient is the difference, not just being more energy efficient. You can have those levels of performance without driving up the embodied carbon, but you have to do it with the right suite of materials.”
Nor is there necessarily a direct connection between cost and carbon content. Choosing materials with a low-global-warming impact doesn’t necessarily cost builders or homeowners any more money. Materials with the greatest carbon impact are standard blends of concrete, cladding, and insulation. Low-carbon substitutions are available.
How the work was carried out
Researchers in Toronto called their study EMBARC, for Emissions of Materials Benchmark Assessment for Residential Construction. They examined as-built residential housing units—single detached, semi-detached, and townhouses—that are representative of 16,400 new homes built in the region annually. The research covered carbon emissions in the extraction and transportation of raw materials and processing them into building materials, called “cradle to gate” accounting.
Using standardized Environmental Product Declarations (EPDs) and a carbon estimating tool called BEAM, researchers looked at 59 sample house plans from eight developers to calculate total material carbon emissions for the 503 housing units.
Not everything that went into the new homes was counted. Researchers excluded mechanical systems, electrical and plumbing, as well as paint, millwork, and fixtures and appliances. In some cases, researchers didn’t have EPDs for the products. In others, there were no meaningful substitutions for the materials. In the case of paints and surface finishes, the materials didn’t meet a 25-year minimum lifespan. In all, excluded materials could represent just as much carbon as the materials that were counted.
Greenhouse gas emissions are expressed as kilograms of CO2 equivalent (kg CO2e) per unit of a material, such as cubic meter or square meter. The BEAM calculator accounts for carbon storage in certain agricultural or forest products, but it does not credit carbon storage for virgin forest products like lumber because of “important and unresolved concerns” with current accounting methods. Those include the carbon released from soil during logging operations, carbon released from roots and mill waste, and the carbon storage that is lost when a tree is cut down.
To sort out the results, researchers not only looked at total carbon emissions (MCE) but also at the Material Carbon Intensity (MCI), which is total carbon emissions divided by the floor area of the building. This allowed researchers to compare the carbon content of houses of different sizes.
Researchers also proposed another metric, Carbon Use Intensity, which combines material carbon emissions and operational carbon emissions. The Toronto report says consideration of both is “critical to understanding a more complete scenario of emissions arising from new homes.”
What researchers found
In the Toronto study, the lowest MCE was 9.5 tons of CO2 for a single home while the highest was 827.1 tons of CO2e. The 503 homes averaged 40 tons of CO2e each. When those numbers are extrapolated across the greater Toronto area, the total MCE for new homes is 840,000 tons, the equivalent emissions of more than 183,000 cars.
Nearly three-quarters of total material carbon emissions could be traced to just three things: concrete (33%), insulation (26%), and cladding (13%), the report said. But there is quite a wide range of carbon content in available products. For example, the global warming potential of concrete samples ranges from a low of 124 kilograms of CO2 equivalent per cubic meter to a high of 610 kgCO2/m3, depending on the proportion of slag and fly ash and the type of cement used in the mix.
“While mix design offers opportunities for emissions reductions,” the report says, “it is possible for new homes to be designed to use less concrete by minimizing below-grade construction and/or substituting materials such as treated wood foundations. Home built above grade using pier or pin foundations can eliminate concrete use altogether.”
Insulation is the next largest contributor, but here also the global warming potential covered a wide range. By far the biggest carbon villain is extruded polystyrene (XPS) board with 83 times the embodied carbon as fiberglass batts (newer versions of XPS have a much lower global warming potential because of changes in the blowing agent used to manufacture it). Aerogel batts and closed-cell spray foam ranked second and third on the list after XPS, respectively. But some types of insulation have negative MCE values, including hemp fiber batts, cellulose, wood-fiber batts, hempcrete, wood-fiber board, and straw bales. Straw bales have 10 times the carbon-storing capacity as hemp fiber. (Only two carbon-storing insulation types were found in houses in this study, cellulose and wood-fiber board.)

Insulation poses special challenges for building designers. As the authors note, one strategy for lowering total material carbon emissions in new homes is to use less material. “But with increasing (and important) demands for improvements in home energy efficiency to reduce operational emissions, new homes will likely be using more insulation, not less. So as we push to improve energy performance we risk driving the significant MCE from insulation even higher.”
Insulation with lower emissions also may have lower R-values, so designers need to plan on more of it to get the same thermal performance in a house. That’s true for most types of conventional insulation—foam board, spray foam, mineral wool, and fiberglass. But for carbon-storing insulation, the more you use, the more carbon that can be stored.
Cladding was the third-most carbon-intensive material used in the study houses. Brick was far and away the worst offender, with a carbon content nearly 10 times that of vinyl, and it was used on all but one of the houses sampled in the study.
At the moment, there aren’t any commercially available cladding options that store significant amounts of carbon. But researchers noted that one U.S. manufacturer, CalStar Brick makes a brick product with one-tenth the carbon content of typical bricks.

What material substitutions can do
Using the BEAM calculator, researchers also estimated the impact of substituting low-carbon materials for those with high embodied carbon. They studied two possible families of materials. The first is “best available materials,” those readily available in the Toronto market that meet current code requirements. That might include using cellulose batts instead of mineral wool or fiberglass batts, using engineered-wood cladding instead of brick, or switching to a low-carbon concrete mix.
A second option was to specify “best possible materials.” These include materials that are commercially available in other markets, and are code compliant elsewhere, but not necessarily possible substitutions now in the Toronto area. This step up might include materials such as straw-based insulation, interior walls made of compressed straw board, a type of drywall made from compressed recycled drink boxes, and linoleum and cork flooring.
When “best available” materials were specified for the house with the lowest carbon intensity, carbon emissions dropped by 51%. When “best possible” materials were run through the calculator, carbon emissions dropped by 145%.
It’s interesting to note that the home in the Toronto study with the lowest MCI was a townhouse from a large developer, who researchers presumed “did not intend to achieve a low MCI score when it was designed or built,” meaning that this level of performance “could therefore be considered an easily achievable minimum target for conventional and cost-competitive buildings.”
If all new homes in the Toronto area matched that performance, it would reduce carbon emissions by as much as 465,000 tons, the report says, the same as removing about 100,000 cars from the road.
What about cost? In a competitive building environment already beset with supply chain issues, high inflation, and rising mortgage rates, can builders afford to make some of these changes in the interests of climate concerns? This is how the authors of the Toronto report addressed that issue:
“Though it was outside the scope of this report to comment accurately on the cost implications of material substitutions, correspondence with several regional concrete suppliers indicated that a low-carbon concrete mix substitution would not have any notable cost implications.”
Engineered wood siding costs between $7 and $12 per square foot, while brick cladding costs from $9 to $28 per square foot. Cellulose insulation was less expensive than the as-built choices in the study houses, although installation costs vary.
“On the whole,” the report says, “it is encouraging that the most impactful substitutions on emissions do not appear to have significant negative cost implications and could potentially cost less.”
Studies confirm earlier modeling
The relationship of operational carbon to material carbon emissions is complicated. Where the electric grid is very clean—in, say, a region where renewables make up a good portion of the power generation—it can take more than a century for operational carbon to catch up with the immediate impact of material selection. But as the grid gets dirtier, the gap narrows.
That’s the case in northern Saskatchewan, where the grid basically runs on coal and winter temperatures are really cold. There, addressing energy efficiency has a much bigger impact because the climate is harsh and power generators are using a very dirty fuel. It might be as little as 10 or 15 years before operational carbon equals the upfront carbon penalty of the building materials.
According to Magwood, the two studies confirm earlier work that was based solely on modeling. Critics could grouse that computer models can be made to produce whatever results researchers wanted. “What about real houses?,” they would ask.
“These are the real houses,” Magwood said, “and this is what it actually looks like on the ground today.”
These studies also are useful in establishing baseline carbon levels in new construction that could be used by municipal officials as a starting point for carbon reductions written into building codes. The average per-house carbon content in these recently studied homes fell in a fairly narrow range, somewhere between 150 and 190 kilograms of carbon equivalent per square meter, according to Magwood.
One house in Nelson came in at 72 kg CO2e/m2, while a number of homes in Toronto measured around 115 or 116, suggesting builders are making low-carbon buildings even when they’re not specifically trying to do.
“They were just making the product, not even intending to make a low-carbon building,” he said, “and they’re already 30-40% under the average, so those kinds of numbers should be really achievable. It shouldn’t be a big lift to say 115 kg is a cap. The whole industry could move and make a pretty big reduction, and not even be challenging business as normal.”
Scott Gibson is a contributing writer at GBA and Fine Homebuilding magazine.
Weekly Newsletter
Get building science and energy efficiency advice, plus special offers, in your inbox.
6 Comments
I think it ought to be noted, that although brick has very high embodied carbon, that it is typically a very long lasting and durable cladding, usually having a life span of well over 100 years with minimal maintenance needed. There are few other cladding materials that can compare with that regard. (not to mention the aesthetic considerations)
I would like to see a graph similar to figure 11 of other common claddings as a reference as to how many times they can be replaced before they meet the CO2 emissions of bricks.
> Material carbon emissions for an all-electric new house will be greater than the operational emissions for about 60 years; material-related emissions for a new house heated with gas will outweigh its operational emissions for about 15 years, Magwood said.
The way this is worded (probably not intentionally), it makes the all-electric new house sound like a worse option from an emissions perspective, but it's the opposite.
The operational emissions of an all electric house are so much lower than a gas heated house that the overall emissions end up being dominated in the near term by the embodied emissions. This is especially the case in areas with cleaner electrical grids like the Toronto where the study took place, where the electricity is 96% zero carbon.
All electric is still far better from an overall emissions perspective. After all, for a new code-built home, other than the heating/cooking systems, you wouldn't build it very differently if it were electric vs gas. The only thing in the electric home that would have significantly higher GWP would be the heat pump refrigerants, but that should pale in comparison to the emissions impact of the building materials themselves.
It's analogous to EV vs ICE cars. EV lifetime emissions will be dominated by their manufacturing emissions, but overall lifetime emissions are far lower than a similarly sized ICE vehicle.
By all means, we should minimize and negate embodied carbon in building materials, but where possible that should be in addition to, not in place of, electrification.
It is always funny for me to see conversations about embodied carbon that don't focus on eliminating most if not all of the concrete from residential construction. There is such resistance and folks often sound like it is an idea that is exotic and weird and more suited for gadflies and ex hippies living in the woods. And yet up and down the Atlantic and Gulf Coasts hundreds of thousands of homes have been built on driven timber pilings with little or no concrete (unless they include a pad for a garage). Many are multi million dollar mansions. Many have been around for 50-60 years, some longer, having withstood hurricanes and nor'easters. I don't see why this technique cannot be used in many places where the ground does not have a lot of bedrock near the surface.
These homes are difficult to air seal and therefore not terribly energy efficient. Added height (ie. beach house) can obviously cause problems for entry/exit. Can't be used in expansive clay or rocky soils due to problems associated with shifting foundation. Termites.
Termites are the real deal in the northeast. They will literally turn wood to dust, I have even seen them eat through plastic sheeting.
See this article and the discussion after it. It's quite feasible. Steel piles don't have the termite issue, and air sealing is also a solvable problem--it's a lot like building a wall and we succeed in air sealing walls.
https://www.greenbuildingadvisor.com/article/all-about-helical-piles
Log in or create an account to post a comment.
Sign up Log in