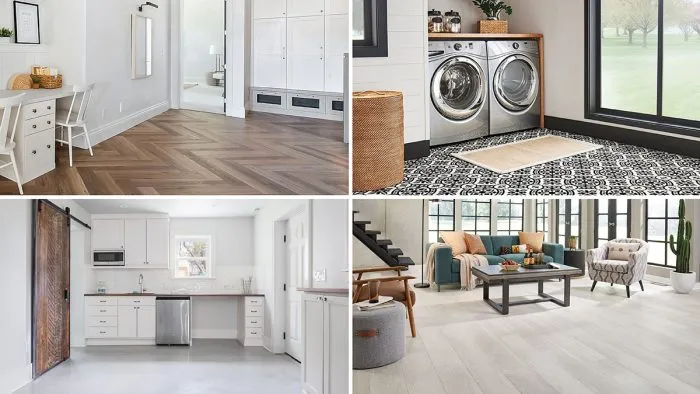
Finishing a basement is a popular and relatively inexpensive way to add living space to a home. But given that at least part of every basement is below grade, managing water is always a primary concern. A wet basement not only will destroy the flooring you choose (and other building materials as well), but it can also lead to mold growth and unhealthy air quality. Before any flooring options can be considered, all bulk-water issues need to be dealt with. For more on managing bulk water to establish a dry basement, check out the approaches to the site and foundation detailed in “Build a Risk-Free Finished Basement” in FHB #248.
This article is designed to help contractors and homeowners think about the most efficient ways to create comfortable, long-lasting basement floors while avoiding some common problems. It also explores different flooring products and subfloor methods. While the focus is basements, many of these tips and techniques apply to slab-on-grade applications as well.
Manage water vapor
Like bulk water, water vapor is a flooring destroyer. Persistent water vapor will cause laminate floors to delaminate, LVP planks to cup, wood floors to swell, and glue-down adhesives to fail; even tiles set in mortar will be prone to efflorescence staining if laid over a floor with high levels of water vapor. Water-vapor movement through concrete can be caused by several factors, the most common being the capillary effect. Without a barrier between the soil and the concrete slab, any moisture in the soil can be wicked up into the concrete and work its way to the surface of the slab.
In 2003, the International Residential Code (IRC) began to require a 6-mil polyethylene or approved vapor retarder under basement slabs to protect against moisture absorption. However, if you are installing flooring in an older…
Weekly Newsletter
Get building science and energy efficiency advice, plus special offers, in your inbox.
This article is only available to GBA Prime Members
Sign up for a free trial and get instant access to this article as well as GBA’s complete library of premium articles and construction details.
Start Free TrialAlready a member? Log in
8 Comments
I loathe the dimpled subfloor products. Mark writes, "The dimples in the high-density polyethylene are designed to prevent trapping moisture and to allow small spills to dry or work their way to a floor drain." The reason I loathe them is that they are marketed very differently; the marketing suggests that the dimpling allows air to circulate under the floor and allow the concrete to dry toward the interior. The marketing suggests that this is desirable when in fact it's the opposite of what you want, you want the moisture in the concrete to stay in the concrete.
For example, here's what the DriCore website says: "DRICORE® has been designed with Air Gap Technology that encourages air flow to help protect against moisture emitted from concrete floors, as well as small water leaks."
Contrary to what many people think, Dricore is not a vapor barrier. There is a version that will act as a vapor barrier but it needs to be tapped together firmly so the tongue and groove joints seal. So many points of failure.
Delta wrap and DMX one step seem like they would keep the moisture in the concrete and provide a small air barrier for a tiny bit of insulation or thermal break.
https://www.dorken.com/en/our-products/products/residential/delta-fl.php
https://dmx1step.com/
One option not written about here is how to finish a mech or storage basement room in an old house with an ugly or uneven slab finish while spending the least amount of money possible in order to redirect funds to the rooms that matter most. One method I've used many times successfully is to prime and self level the floor with a self cementitious leveling agent. Maipe makes one that CAN be used as a wearable surface but I've only used the brands that state that they can not be used as a final wear surface like "Custom Building Products LevelQuik RS" and "Sika SikaLevel" because they are always bigbox available and you need to be able to overbuy then return when self-leveling to prevent cold joints. I then paint the final surface w/ a Porch & Floor paint. This has given me a high-quality feeling floor that can easily stand up to typical shoes-off household traffic without a problem and the paint and self leveler seem to prevent moisture migration. If the slab was very wet then I might use a product like RedGard below the self leveler (but have not tried this yet). If the slab is very out of level, say 2 or 3 inches from one side of the room to the other, ceiling ht is already low and I don't want to spend a fortune on self leveler nor lose ceiling ht and having a perfectly level floor is not important then I have found that it's really easy to start the leveler placement at the high points (not filling from from the bottom) and using a rake to spread the self leveler to the lower points and into the corners so that the entire off-level slab gets a thin layer (varies from 1/8" to 3/8") of leveler to smooth out to the surface to a mirror like smoothness. This method has worked really well for me in the past.
If ceiling ht is already a concern without room for 1-2" of foam then I have found that finding the thickest natural cork underlayment that you can find (typically 1/4") makes for a not insignificant thermal break and provides slight bounce under foot that is welcome in a basement when you're expecting a hard cold slab. In this photo what you see is: 5/8" true-wood-core engineered wood veneer flooring (click-lock floating / not gluedown) over 1/4" cork underlayment (as thermal break & softner) over RedGard over self leveler over a 1965 concrete slab (no poly below).
Ric,
I'm not sure I'd describe cork underlayment's R-value of 1.1 as a "not insignificant thermal break". It is about twice what the slab itself yields, but that's not much.
If installing cork, is it still considered a wood?
If so, can it really go in place if foam? I'd imagine most basement floors would be concrete, foam (taped), plywood, flooring.
If you replace foam with cork, isn't that putting untreated wood directly in contact with the vapour source and lead to rot in the cork?
Hi, question about new houses? I redid my 100 year old basement and have brought it into modern building standards.
Bulk water is handled internally with dimpleboard on internal walls, connecting down to French drain, connected to sump pump out.
The French drain lives in 6 inches of glavel, followed by 4inch of type ix EPS (that wraps up and around the slab fully isolating it), followed by 10mil, followed by 4inch fiber reinforced slab.
On top of this kind of basement concrete slab, could you just drop down floating engineered wood flooring?
guillow,
Yes - with the understanding that if at some point y0u do experience moisture problems, the flooring is more likely to be damaged than the ones mentioned in the article.
Log in or become a member to post a comment.
Sign up Log in