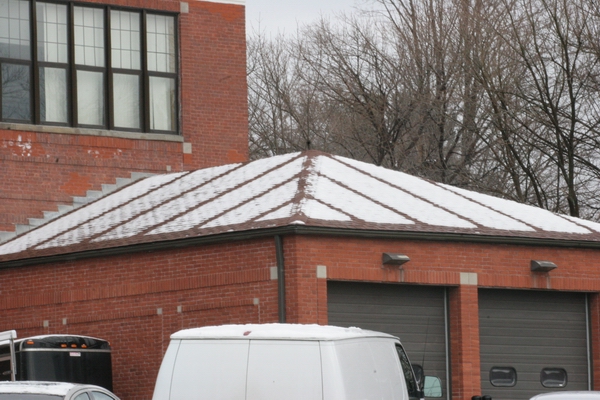
Image Credit: Dan Morrison
Everything is relative — especially when it comes to thermal bridging. Thermal bridging occurs wherever assembly components with low R-values relative to surrounding materials span from the inside to the outside of a building assembly. Thermal bridging takes place in wood-framed assemblies because, although wood is a pretty good insulator at about R-1 per inch, it is at least three times more thermally conductive than any cavity insulation, which start at about R-3.5 per inch.
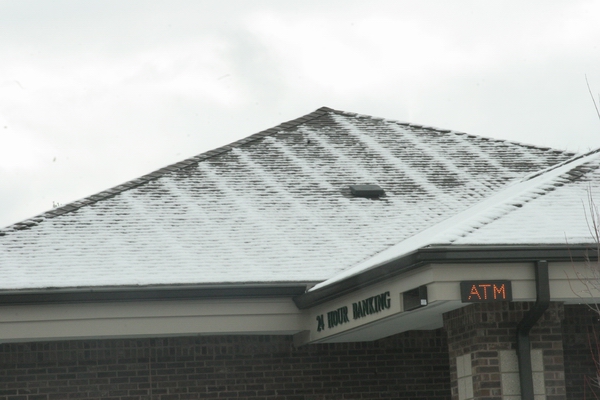
With steel framing at about R.04 per inch, it’s thermal bridging on a whole different scale. Steel framing typically reduces the in-cavity R-value by as much as 50%, while wood framing reduces in-cavity R-value by a bit less than 10%.
Wrapping a building envelope with exterior rigid insulation cuts off the thermal bridging. Rigid insulation as exterior sheathing is a great idea for wood-framed assemblies, imperative for steel. But as in all things hygrothermal, you get a double benefit when you reduce or eliminate thermal bridging — you save energy and reduce the potential for condensation, mold, and rot.
The main reason we put insulation in framing cavities is because there is space — it’s the easiest and least expensive place to put the stuff. But it is not the best place, in large part because of thermal bridging. In what Joe Lstiburek of Building Science Corporation calls the “perfect wall” (or roof), all of the insulation is on the exterior. This means that the building frame experiences nearly the same conditions as the occupants, a real recipe for happy, comfortable, and long-lived people and buildings.
To gauge the energy implications of framing type, spacing, and thermal bridging, try the ORNL Whole Wall R-value Calculator.
Weekly Newsletter
Get building science and energy efficiency advice, plus special offers, in your inbox.
10 Comments
Prevent Thermal Bridging While Maintaining 6-9/16" Jambs
March 18th, 2009
Being “Green” first and foremost starts with being energy efficient. There is no better way to insure that your building envelope conserves energy then to use closed cell spray foam insulation. With the highest R-Value rating at or around 6.8 per inch and achieving a vapor barrier at or around 2″ thickness, closed cell foam is simply the best performing insulation on the market and should be an integral part of your wall and attic designs. One wall design that is sure to become more popular utilizes 2×4 studs, 2″ foam board as a thermal break, 7/16 OSB or other structural sheeting using 3.5″ screws for fasteners. Then the 2×4 stud cavities are sprayed with 2″ of closed cell foam. The total wall thickness ends up to be 6-9/16″, standard for window and door jambs. The R-Value of this quiet and comfortable energy wall is 24! There are many other ways to utilize closed cell foam for your insulation that will not break your budget and will pay dividends in energy savings for the life of your home. We will discuss some more of them in the days to come.
Thefoamman
http://www.thefoamman.net
Is an R-24 wall noteworthy?
"The R-Value of this quiet and comfortable energy wall is 24!"
I'm no building scientist, Kevin, but if we agree that heat radiates, I don't see why we applaud an R-24 wall when building codes (read "minimum acceptable standards") call for R-30 and better in roofs and floors.
Shouldn't we be trying to create a balanced envelope?
heat radiates but mostly rises
"...when building codes (read "minimum acceptable standards") call for R-30 and better in roofs and floors." I know of no commercial bldg code that requires R-30 in walls and I;m in Wisconsin, where we get lots of cold weather. Code requires me to meet an overall envelope target, using Comcheck.
"Shouldn't we be trying to create a balanced envelope?" What do you mean by balance? Heat rises and the most bang for the buck is in roof insul., thus roof R-values should be higher.
Adding more R-value indiscriminately is foolish. Here's a real world example from a project on our drawing boards right now that demonstrates the law of diminishing returns. R-32 walls and R-60 were proposed. When the energy modeling was done they found that R-20 walls and R-30 roofs only cost $1,000.00 more per year. But the cost of the extra insul. to get to R-30 walls and R-60 roofs was $40K! That is a 40 year payback and just does not make sense.
40 Year Payback vs IRR
What is the IRR (internal rate of return) of the added cost of insulation. That is calculate the incremental costs vs the incremental savings over the next 10 or 15 years. If IRR is greater than cost of capital it makes financial sense to insulate more. Can you calculate those numbers?
heat rising and payback
Hey guys -
I know this may seem like a technicality, but heat does not rise, hot air does. We mostly put more insulation above us rather than alongside of us because it is generally cheaper to put more in attics than walls. In a well-designed and airtight building, stratification of air can be slight enough that heat loss through ceilings is just about the same as through walls.
On payback: I am sure that you both had read enough of Martin's blogs to get his perspective insulation payback, but I pretty much agree with Marc Rosenbaum's assessment of payback: https://www.greenbuildingadvisor.com/blogs/dept/green-building-blog/blog-review-thriving-low-carbon. I think that when building structures that should last for more than one hundred years, simple or even net preset value payback calculations are just not up to the task.
"Wrapping a building envelope
"Wrapping a building envelope with exterior rigid insulation cuts off the thermal bridging."
What minimum thickness is needed to cut off the thermal bridging?
stopping heat flow
Hey Stewart -
You can't stop heat flow, just slow it down. Adequate R-value to significantly reduce heat flow is a function of the temperature difference the assembly is experiencing (and its duration). A rule of thumb we used to use when I was at Building Science Corporation was 1/4-inch of rigid foam (let's say R-5 per inch) per 1000 heating degree days. Just a rule of thumb, but still useful.
Peter
Response to Stewart A.
Stewart,
In addition to reducing the rate of heat flow through framing members, exterior foam sheathing performs another important function: it keeps the wall cavity warm enough to prevent condensation or moisture accumulation. To achieve that goal, the foam must meet certain minimum R-value requirements. To learn more about these calculations, see Calculating the Minimum Thickness of Rigid Foam Sheathing.
Forest through the trees
This is a great academic discussion, but what’s the real point? To me it’s the living experience the house provides. What’s the cost (upfront and recurring) and what’s the comfort level? What’s the impact to the homeowner, community and environment?
Calculating the thermal resistance of wall system is pretty straight forward (high school math). Many web sites address this, but resistances in series simply add while those in parallel add by the inverses or reciprocals (Rtot= 1/(1/R1 + 1/R2).
To be more clear, I’ll talk about R values of the individual components and the overall effective R value of the wall system (studs, fiberglass, windows, outlet boxes, etc). BTW, my calculations seem to agree with those of the link provided, but our assumptions are likely different.
Consider a 12 foot long (8 feet high) piece of wall with 2x6 wood construction filled with fiberglass. The overall R value is around 11. That may sound paltry, but to put it in perspective, our colonial and Victorian forefathers were dealing with R 1 or less in their houses. WWII vets were living in brand new houses with R values around 3 or 4?
First, let’s assume that the wall is pretty air tight, or fiberglass won’t do you much good. Second, I’m ignoring the effects of drywall, sheathing and exterior cladding, which will simply an R1 or so to all my numbers. The wall is about 15% wood for the studs and plates, so you calculate the thermal shunting (bridging) that the wood (R5.5) does to the fiberglass (R19) to give you and overall wall system R value of R13.9. The thermal bridging of the wood studs degrades the filled space’s R value by about 33%.
If you add a window (R3) at 6% of the wall surface area, then the wall system falls to R11.3
Adding some light switches and outlet boxes (1% of the wall area) and stuffing the insulation behind the boxes (R11?) degrades the wall system to R11.2.
If you chose, instead to cut the fiberglass completely around the boxes, then your wall system is also R11.2 (Assumes and R5.5 for the dead air space of the boxes.) (It actually lowers the calculated R value about 0.02, if you believe these simple calculations are that accurate in a real application.)
Say 5% of the wall has wrinkled fiberglass with an effective R10, then the wall system would be around R10.9
So by calculation you can show that the thermal bridging of the studs is a big hit on the overall R value and the appeal of external foam panels is evident.
The calculations also show that sloppy fiberglass installation degrades your R value by a few tenths to maybe ½ of a unit. Of course adding an extra window or extra wood can have a similar effect and if the fiberglass installation is really poor, then these numbers will be worse.
But the real question is how significant is this? How much does this cost the homeowner in extra heating/cooling costs and comfort level? How much does it cost the builder to mitigate this “problem”? How much more money would a build pay to increase this R value? If you’re dealing with studs and fiberglass or something similar, would you be better off paying the insulation installer more money to be more persnickety or simply buying a more efficient heating unit? Is this the true weak link in the thermal envelope? I don’t have these answers but those are what we should be seeking.
These numbers need to be next entered into a model of an entire house. Then this information might add some insight to heating/cooling costs and comfort levels. Dollar values can be assigned and real cost benefit analyses can start to be done. With an entire house, a dynamic model is much more useful than static. Ultimately you’d like to compare these theoretical numbers with real world results to further refine (or understand the limitations of) the model.
Response to Gerard Celentano
Gerard,
You are far from the first person to raise these questions, which were all tackled and answered by the superinsulation pioneers of the early 1980s.
In cold-climate regions, building walls in a way that addresses thermal bridging makes good economic sense. The usual solutions are double-stud walls or exterior rigid foam.
In Florida or Texas, the returns on investments that address thermal bridging are less certain than in Minnesota and Maine.
Log in or create an account to post a comment.
Sign up Log in