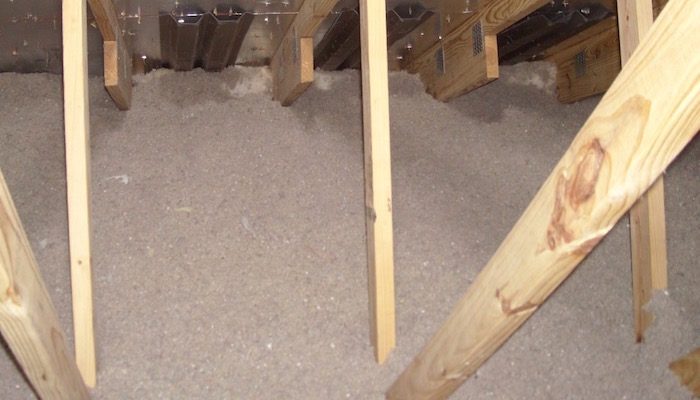
Image Credit: Energy Vanguard
Everyone knows about the impact of burning fossil fuels on global warming. Maybe not everyone believes it, but scientists first started focusing attention on increasing carbon dioxide levels way back in 1827. The impact of insulation on global warming, however, is relatively new.
About a decade ago, Professor L.D. Danny Harvey started looking at the effect of blowing agents released by the production and use of some foam insulation types. Then Alex Wilson picked it up in 2010.
At the 2016 North American Passive House Conference, I presented my views on this topic. I wrote about the first part of my talk in my last GBA article. Today, I cover the part about using David White’s global warming tool for insulation.
Background
In his calculations, Alex Wilson chose one scenario. He looked at the global warming impact for a house heated with a natural gas furnace. He chose a cold climate with 5,000 heating degree days (HDD), and he didn’t include cooling.
The resulting payback showed how long it would take to save enough energy to offset the global warming emissions from the embodied energy in the insulation and from the release of blowing agents with global warming potential (GWP). He looked at several different insulation types and a range of R-values.
The first part of my conference presentation covered what I see as the main flaw with his payback calculations. In the second part, I discussed David White’s spreadsheet tool for calculating the global warming impact of insulation. The nice thing about his calculator is that you can change a lot of the variables and see what the effects are.
I showed three scenarios in my conference presentation. I’ll put them in a different order here, beginning with the gas furnace. If you download the presentation file, you’ll find the two for heat pumps before the one for the furnace.
Gas furnace
The graph below shows the output from David White’s calculator for the gas furnace.
There’s a whole lot going on here, so let me first give you the lay of the land. This tool doesn’t calculate payback. Instead it calculates global warming impact, as measured by the kilograms of carbon dioxide emitted per square foot of wall area per year (kg CO2/sf/yr). That’s on the vertical axis. On the horizontal axis is the total R-value of the assembly. To the right of the graph, I posted a sidebar with the main inputs I used.
One important thing to note: I used version 1-2 of White’s tool. It doesn’t include cooling. PHIUS has version 1-3 on their website, and it has the ability to include cooling energy in the calculations.
Let’s dive into the results now. There are three curves on the graph. They show the global warming impact for cellulose (red), closed-cell spray polyurethane foam (green), and extruded polystyrene (blue). The calculator has a lot more options for insulation types, but I chose these three since they capture the important differences. Most of the others are similar to cellulose.
I chose a reference R-value of 14. That matches what Wilson did in his calculations and means that we already have a wall equivalent to 2×6 cavities insulated with cellulose. The whole-wall R-value of that assembly is about 14. On the graph above, the three curves all begin at R-14.
It’s what happens when add more insulation beyond the R-14 that gives you some guidance here. In this case, all three see their global warming impact drop as you go up from R-14. But cellulose has a different behavior than the other two. It just keeps dropping whereas the other two hit a minimum and then begin rising again.
For closed-cell spray polyurethane foam (ccSPF), that minimum occurs in the mid-R-30 region. As you add this insulation type, the global warming impact keeps getting better and better until you’ve added about R-20. That would be about 3 inches of ccSPF.
For extruded polystyrene (XPS), the minimum comes more quickly, at about R-19. Once you add about R-5 (or 1 inch) of XPS, the global warming impact begins to rise.
When I discussed using this tool with David White and others, most believed that if you’re going to use XPS or ccSPF, you shouldn’t go further than the minimum. I drew the yellow line on the graph, however, to show where the net effect of adding XPS or ccSPF goes from positive to negative. With XPS, you can add about another R-5 before your assembly becomes worse for global warming than if you hadn’t added any extra insulation at all. With ccSPF, it’s beyond R-60, which, at about 7 inches, is also beyond the point that most people would use this type of insulation.
Electric heat pump with “clean” electricity
Now let’s look at the results for a heat pump. First, here’s the scenario for a house that uses “clean” electricity.
I wrote an article in September about the carbon intensity of electricity by state. I posted an expanded version of the article that included carbon intensity by regional interconnect. The state data show a wider range than the regional data, varying from less than 0.1 kilograms of CO2 per kilowatt-hour produced up to about 0.95 kg CO2/kWh. In this analysis, I called the “clean” electricity that which had a carbon intensity of 0.1 kg CO2/kWh and the dirty electricity that with 0.95 kg CO2/kWh.
Clearly, the cleaner the electricity, the less you can affect affect global warming emissions by saving energy. In the graph above, notice how low the yellow line is. As the the three insulation curves diverge from the R-14 starting point, only the cellulose makes sense here. (Again, there are a lot of other insulation types that perform similarly to cellulose. I just haven’t shown them here.)
Electric heat pump with “dirty” electricity
With dirty electricity, the effectiveness of insulation is much better.
As in the previous two graphs, the cellulose curve keeps going down. The more you use, the more you decrease the global warming impact. With ccSPF and XPS, however, there’s a minimum and then a rise. For XPS, the sweet spot is at about R-25, so you could add about 2″ for another R-10. For ccSPF, the minimum is about R-40, so you could add 3 to 4 inches for another R-25 or so.
To stay below the yellow line, you’d want to limit XPS to about R-25, or 5″. You could go beyond R-60 total with ccSPF, but why would you want to? In my last article, I showed that unless you’re in a really severe climate, you could even achieve Passive House walls with R-50 or less.
Conclusions
This global warming calculator from David White is a useful tool. Rather than trying to calculate payback, it gives you the numbers for global warming impact. You can look at the curves for different insulation types and see where your sweet spot is. One thing I think would make it even better would be if it allowed you to look at the effect of an entire assembly instead of just individual insulation types with a reference R-value.
If you download my presentation slides, you’ll see these conclusions:
- Global warming impact isn’t as simple as it seemed
- Blanket condemnation of XPS and ccSPF based on payback are not warranted
- Avoid XPS
- Use ccSPF with other blowing agents (that is, blowing agents with a lower global warming potential)
- Use David White’s calculator for more refined guidance.
The big one there is in the middle: Avoid XPS. In terms of global warming impact due to the HFC-134a blowing agent, it’s the worst.
It’s also relatively easy to substitute another type of insulation for XPS. On walls, you can use mineral wool or polyisocyanurate. For slabs, you can use expanded polystyrene (EPS) or mineral wool. So just use something else.
Manufacturers are tight-lipped about what blowing agents they’re using these days. Some of the spray foam companies have switched over to the next generation blowing agents with much lower global warming potential. I don’t know of XPS manufacturers who have announced changes, but a rep from manufacturer did tell me they’re not using HFC-134a anymore. When I asked what they used, he said, “I can’t tell you that.”
In general, all insulation types can help mitigate the effects of climate change. Types with the bad blowing agents, however, have limits to their effectiveness. If you’re planning to use XPS or closed cell spray foam, the tool from David White can help you decide where to draw the line.
Allison Bailes of Decatur, Georgia, is a speaker, writer, building science consultant, and the author of the Energy Vanguard Blog. You can follow him on Twitter at @EnergyVanguard.
Weekly Newsletter
Get building science and energy efficiency advice, plus special offers, in your inbox.
10 Comments
Got it right
For anyone stumbling across this and wondering what to make of the multiple perspectives Allison has offered on this topic, I suggest ignoring the others and sticking with this one, which is both useful and correct.
The analysis here still makes it seem a little more complicated than it needs to be. Most of the discussion of the plots compares different R-values for a single insulation type, and considers how the R-value choice affects the impact. The results are then different with different assumptions about the heat source, as well as being different for different types of insulation. But the most important conclusion is to avoid the types of foam with high impact. That conclusion is consistent across all the plots and doesn't depend on the assumptions about the heat source. You can see that by looking at a single R-value and comparing across the different insulation types vertically rather than horizontally. For example, at R-40, the difference between cellulose and XPS is about 0.6, on any of the three plots. The benefit of avoiding XPS is consistent, regardless of what heating source you are using.
So it's easy to get to Allison's two key conclusions:
Avoid XPS
Use ccSPF with other blowing agents (that is, blowing agents with a lower global warming potential)
To elaborate on each of those a bit, avoiding XPS applies in North America through 2020, unless manufacturers announce they have phased out HFCs early. And on ccSPF, the only commercial product that I know of that has low GWP so far is Lapolla 4G, so for now, that bullet means use Lapolla 4G if you are going to use ccSPF.
Response to Charlie Sullivan
Charlie,
Thanks for your helpful and accurate summary -- both your conclusion concerning the diversity of tone and approach in Allison Bailes's many articles on this topic, and the summary of the key points for designers and builders to remember.
Energy consumed to produce rockwool
I downloaded the calculator and it looks to me like rockwool also performs quite well. I had thought that it was very energy intensive to produce. How accurate are the embodied energy portion of the calculations?
Modeling limitations
Thanks Allison, this is interesting and helpful. But it seems like the utility of this model is limited by several factors unfortunately:
*Manufacturers won't talk about what blowing agents are in their products.
*The model doesn't deal with the air sealing value of certain kinds of insulation--DP cellulose, spray PU, for example.
*The performance of foam degrades over time as blowing agents escape.
It's too bad that with so much at stake we still don't have the tools we need to help us make good decisions.
Response to Ethan T
If you compare rockwool to cellulose, and look only at the energy used to produce it, it requires much more energy. But that energy is small compared to the energy involved in heating the house, so it doesn't show up much in the results. I'm not sure how accurately it's modeled in that calculator, but it's not very critical to model it accurately, because it's a small effect overall.
The reason we care about the GWP of blowing agents is not out of a nit-picky desire to keep track of everything. It's because they are disproportionate--they are surprisingly large.
Response to Bennett Sandler
Although manufacturers are reluctant to talk about blowing agents, we can figure out most of what we need to know from what they do say ... and you can bet that when one of them finally has a product with truly low GWP, they will proclaim it loud and clear. And furthermore, it's not like we have any tricky tradeoff decisions to make. XPS is simply a lot worse than the alternatives.
So even though none of this changes the fact that XPS is a bad choice, here's what we do know:
The XPS industry association says that the GWP of the blowing agents their members use range from 740 to 1340.
Owens Corning says their top secret blowing agent recipe has 70% lower GWP than the pre-2009 blowing agent.
The pre-2009 blowing agent was HCFC-142b, which had GWP 2310.
740 is 68% lower than 2310, so presumably Owens Corning is rounding that up to 70%, and they are the manufacturer that the industry association is referring to at that end of the scale. The other end, 1340, matches HFC-134a, which is apparently what Dow and others use.
So if you do use XPS, it would be only half as bad to use pink foam as it is to use blue foam, but neither is a good choice and neither is green.
If you go with EPS or fluffy insulation, the degradation over time issue goes away, and there are lots of options for air sealing including tape and open-cell spray foam.
The bottom line is that we do have enough information to make good decisions.
Modeling limitations 2
Charlie, thank you for the details. However it would be useful, for example, to be able to compare a flash and batt against cellulose in an attic when the flash buys 5% on air sealing; or 5" of foam in a cathedral retrofit versus DP cellulose versus conventional fiberglass, when the fiberglass is going to leak 10% more than either of the first two--that sort of thing.
On a big picture level I find it odd that we have dozens of incredibly sophisticated programs available to simulate everything in buildings from thermal bridging to acoustical dynamics and that allow us to ask and answer very arcane questions in great detail, but for this most basic consideration--which insulation material makes energy sense in what situation--we have only a crude approximation to tell us "cellulose good, XPS bad." And this is not meant as a criticism of David White's work; clearly we should be grateful that he got us this far.
The dirty vs clean electricity needs an asterisk
Over the lifecycle of the insulation the carbon footprint of the grid is going to change, in most cased DRAMATICALLY toward cleaner.
Time of day and time of year when the heat pump is being used also varies, which is difficult to model without more real-time data, but that data is now becoming available: http://explorer.watttime.org/
But somewhere near that fuzzy bottom line is what is dead obvious from even the crudest lipstick-on-mirror math model:
1: The less polymer used per (very long term) R, and...
2: ...the least impact blowing agents that are used ....
...are key to reducing the lifecycle footprint of the materials.
On both of these factors water blown half pound density open cell foam has by far the least impact of any foam insulation product currently in common use.
Among some as yet unstated takeaways:
*Don't use plastic insulation except where it's needed (or dramatically less expensive than lower impact alternatives
*Independently of the blowing agent used, don't use ANY ccSPF where open cell foam can achieve the same desired result (air tightness, R value). The special cases still exist where the low vapor permeance is an asset, but those are typically in retrofits- it can usually be worked around in new construction.
*Reclaimed / re-used rigid foam is lower impact than any spray foam, lower than any virgin stock insulation product, or recycled feedstock cellulose.
Also note: Cellulose usually gets a pass due to the fact that it is largely made out of reclaimed/recycled material. The modelers typically only factor in the carbon & energy of the reprocessing and transportation, but this isn't necessarily always going to be legitimate. The energy, water use, and carbon footprint of manufacturing the original newsprint is pretty substantial. If making cellulose insulation as virgin-stock product from the original paper making feedstocks it may not look quite as rosy next to fiberglass or rock wool as it currently does. Cellulose fiber may simply grow on trees, but paper doesn't, exactly. But even when including all papermaking impacts it's still likely to come in much lower impact than any foam, including open cell polyurethane.
Dana - +1 on the WattTime link!
Thank you!
I suggest that anyone buying
I suggest that anyone buying reclaimed XPS is, to some extent, encouraging additional production and use of XPS.
Log in or create an account to post a comment.
Sign up Log in