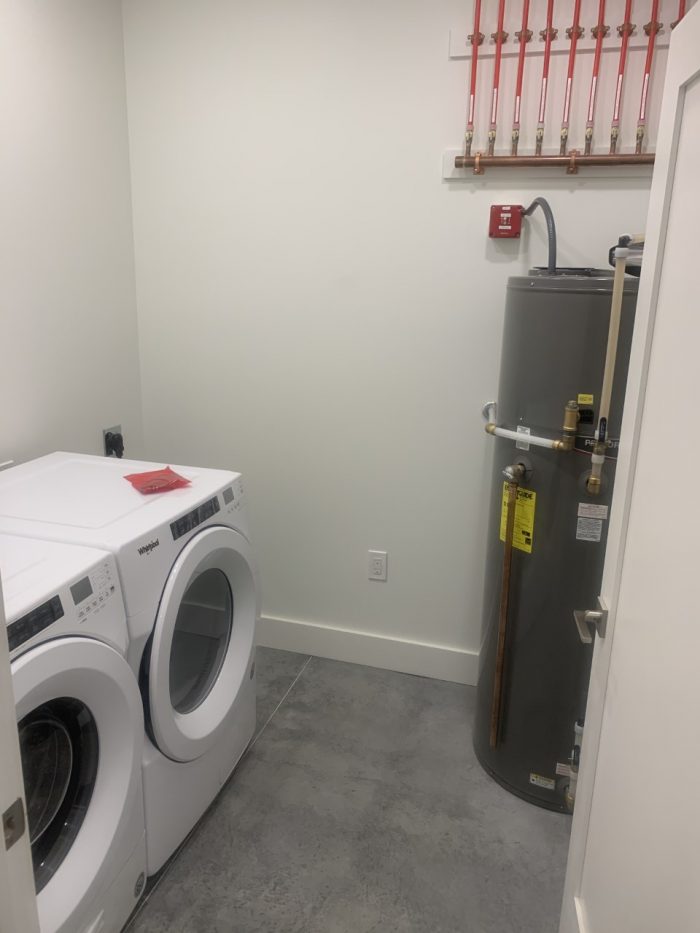
I installed my first heat pump water heater about eight years ago for a client whose roof was not appropriate for the solar hot water system I wanted to use. Since then I’ve installed many more heat pump water heaters and, as long-time GBA readers will not be surprised to hear, not a single solar hot water system. Having mostly killed the solar thermal market, heat pump water heaters continue to grow in popularity and by now most of the people I talk to are at least aware of the existence of this technology, even if they’ve never seen one or don’t quite understand how they work.
Basements are a good option, but not always available
Until recently, all of my installations had been in basements here in upstate New York. There are several obvious advantages to locating a heat pump water heater in a basement. The heat pump dehumidifies a normally damp space while it also makes efficient use of waste heat from a boiler or furnace during the heating season. During the non-heating season there’s enough air volume and ground source heat in the basement to keep the heat pump happy. And fluctuating basement temperatures don’t affect anyone’s comfort upstairs where the thermostat is.
There are occasionally disadvantages to a basement installation, but these are mainly a concern for the unlucky installer who might have to get a large, heavy tank down a rickety flight of stairs, through a narrow door, or in a worst case, might have to dig a hole in the floor with a pick and shovel and line the hole with EPDM rubber in order to get an extra two feet of headroom for a tall tank in a short space.
But where do we put a heat pump water heater when there’s no basement and no boiler? In new high-performance slab-on-grade homes, it’s hard to find an obvious place for a heat pump water heater.
Heat pump water heaters usually have minimum volume requirements, so they can’t be shoehorned into a cabinet the way electric resistance tanks can. And having a heat pump that scavenges heat from conditioned space seems potentially wrong-headed. In the summer not so much—it’s free cooling. But in the winter making hot water means robbing Peter to pay Paul: the house’s heating system (in this case an air source heat pump) will have to work harder because the water heater is pulling heat out of the air. If the COP of the heat pump water heater is 2.5, but it’s being supplied with heat by an air source minisplit, is the combined COP in the winter a little lower or a lot lower?
We struggled with these questions on a recent Passive House project, and my boss Josh Edmonds suggested we try something unorthodox: putting the water heater in the laundry room upstairs instead of downstairs in the relatively small mechanical room. After nearly a year of experience, it turns out this arrangement works well. And if the occupants are willing to modify behavior a bit, it works really well.
Laundry closet install is an efficiency win
In a small laundry room of 70 square feet, standby losses from the clothes dryer, in this case a heat pump condensing unit, can significantly raise the room temperature. We’ve seen 10°F or more with the heat pump dryer running and the door closed. The heat pump water heater on the other hand, can lower the temperature in this space by 10°F or so. It’s worth noting here that water heater COP goes up with room temperature, so the heat pump water heater already has a higher efficiency than if it were located in a 50°F basement.
The picture gets even gets better when hot water demand—showers and baths for example—coincides with clothes drying. Then the COP on the water heater really maxes out, the room temperature stays balanced, excess moisture in the air is removed by the heat pump’s evaporator, and there’s little to no transfer of heating or cooling load to the minisplit.
Interestingly enough, as I was Googling to see if I could figure out how to calculate the COP implications of a heat pump water heater operating in conditioned space during the winter when it’s basically shifting its load onto the minisplit, I found an article in Home Energy by Ian Shapiro of TAITEM Engineering exploring this exact question. It’s well worth reading if you are interested in the technical details.
Shapiro has a couple of interesting conclusions. During winter the efficiency picture for the heat pump water heater in a space conditioned by a minisplit turns out to be roughly similar to the basement scenario once you factor in the higher ambient temperature in conditioned space. It’s basically operating as a two-stage heat pump.
Using Shapiro’s formula and applying rough numbers for our scenario with an air source minisplit operating in heating mode but without standby dryer losses, we calculate an adjusted COP for the hot water heater of above 2.0—or a respectable 200% efficiency. But if we shift load and scavenge standby heat from the dryer, the COP rises significantly, to between 4 and 5. Those are the kind of numbers we really like to see.
Some installation details
We have since built two other houses with a similar arrangement, and so far occupants are happy and efficiencies look good. We are careful to set expectations ahead of time by emphasizing that heat pump water heaters are about as noisy as refrigerators and by designing with that in mind so that if possible the laundry/mechanical room does not communicate noise to a bedroom, for example.
Manufacturer guidelines vary, but all heat pump water heaters have minimum volume requirements for air. One option we tried in our most recent project is to combine the mechanicals and laundry in one space. Normally this space might be a bit too small for the HP water heater’s volume requirement, but because we left the mechanical room ceiling open to the truss service cavity above, the heat pump has access to a much larger volume of air. And some new models can also be ducted, so that supply and return are potentially in separate rooms. In that case the water heater itself can be located in a much smaller space.
One last lesson we’ve learned the hard way: the mechanical room is critically important real estate and it should have enough space to house bulky equipment and allow easy installation and service. Usually this comprises the electrical panel, the ERV/HRV, the well pressure pump, possibly water filtration, condensate, and maybe even the water heater, distribution manifold, and washer and dryer. Mapping out appliance footprints, duct paths, pipes, etc. ahead of time pays big dividends later.
-Norm Farwell specializes in energy efficient mechanical systems at Simple Integrity in Cooperstown, NY. Photos courtesy of the author.
Weekly Newsletter
Get building science and energy efficiency advice, plus special offers, in your inbox.
31 Comments
Good article.
It would be interesting to see some data on various ducted configurations.
I'm thinking of a basement install, but considering ducting either the supply or return to a unused upstairs floor register (abandoned from the decommissioned furnace and ductwork configuration).
My thought is that it might be better to pull in warmer upstairs air (heated by a woodstove in deep cold, and a mini split in shoulder seasons), rather than cool down my already cool basement.
Or perhaps duct the discharge upstairs to encourage air movement between the basement and mainfloor and avoid over-cooling it.
This may reduce the de-humidification though, since the warmer upstairs air may not drop below the dewpoint.
You can put a SanCo2 in a closet. Or, anywhere else inside for that matter. The stainless steel tank will last a lifetime and the space requirement is small since the storage temperature is typically 150F. That puts the mixed temp yield of even the little 43 gallon tank in the 80's. Recovering that tank at .5 gpm can serve a small family. The same can be applied with the 80 gallon tank. 150F storage pushes the mix stored volume up to the 120's and ready to fill a big tub.
Since the heat pump unit is sitting outside, there is no noise or taking heat from the homes interior. The life expectancy is nearly double and the wear parts are outside which means that worry of a tank failure from flipping from heat pump to ER to heat pump to ER and stirring the tank is no longer a danger in a finished room like that laundry room.
Not trying to poke holes, but point out that there are better tools to consider.
How does the SanCo2 compare in COP and price to a standard HPWH?
EDIT:
Found this technical info doc: https://www.sandenwaterheater.com/sanden/assets/File/Sanden_sanc02_technical-info_10-2017_4.pdf
Chart on page 13 shows that for 150 F output temp, the COP varies from about 4.8 at 70 F ambient temp to 3.0 at 23 F to 1.6 at -13 F.
I also just remembered the SanCo2 is a monobloc unit, so it's going to need freeze protection anywhere that has temperatures below freezing. That's not a drop-in replacement for an indoor HPWH.
Yep. Thats it. Price depends on location. In Pacific Northwest NEEA rebate area, the wholesale to trade is about $3600. Consumer rebates after installation are $250-$500. Other areas trade price might be $3800 or so
Ok, thanks. I hadn't seen any prices.
If you have a crawlspace, digging out a small area for a hpwh may be well worth it to save on living space, noise, and comfort issues and even provide some dehumidification.
This might be slightly off-topic, but it does relate to the effect of the heat pump on the space in which it's installed.
In our 150-year-old Maine home, we have a somewhat damp basement. It's only an issue in the summer, and during July and August, we run an electric dehumidifier, which is a huge energy consumer.
We currently obtain domestic hot water from a wall-hung propane-fired condensing boiler, which also heats the home. Due to venting requirements and they layout of the home, the physical location of the boiler is not ideal for DHW - there are very long runs to the bath and kitchen fixtures, and it takes forever to get hot water at the point of use.
Yes, there are many potential solutions here - addressing basement moisture, buying a more efficient dehumidifier, installing a hot water circulating pump, etc, etc. But what's stuck in my mind is a heat pump hot water heater. It could be located close to the kitchen and bath fixtures, which would provide very short plumbing runs, and it would also serve to dehumidify the basement.
For summer, this sounds great.
For winter, I'm not sure. The basement is already cold enough to keep beer at a drinkable temperature for at least 8 months of the year. Compared to the oil-fired boiler that was there years ago, the wall hung boiler contributes almost no waste heat to the basement. I wonder whether it will be too cold with a heat pump - for comfort, or for efficiency of the unit. There are no doubt many variables, but that leads to my question:
Why not feed the water heater from the DHW output of the boiler?
That way, in summer, we could bypass the boiler's DHW function, and let the heat pump carry the entire DHW load. In winter, if we found the heat pump chilled the basement too much, we could engage the boiler's DHW function again, and have it feed pre-heated water to the the water heater. The heat pump would only run to maintain the temperature in the tank, not to recover from usage, so it's chilling effect would in theory be reduced, but we'd still have a reservoir of hot water close to the kitchen and bath fixtures.
Is this a good idea? Bad? Crazy? Am I making incorrect assumptions? Invalid conclusions? Your feedback is welcome!
If your boiler is a flow-through (tankless) boiler that uses a flow sensor to activate, this seems like it would work. You would have to remember to manually turn off the DHW feature of the boiler in spring/summer, and back on in the fall. That's not too tough. I would insulate the pipe between the boiler and HPWH really well. Maybe your cellar will stay at beer temp all year with this setup. That would be a good thing.
In a new build, the ability to plan for and properly duct a HPWH makes them a lot easier and more flexible to integrate. Once ducting is considered the tank can be put just about anywhere, and warm air can be drawn and cool air supplied to areas that make sense. This can increase COP, reduce noise concerns, and even increase comfort in the house if you consider the year round dehumidification.
Ever since I first heard of HPWH a few years ago I've been trying to make sense of where to install one. When I first heard of them, we lived in a house with an unheated detached garage and a finished daylight basement that included an oil furnace and the family room. In the winter the furnace did not put out any stray heat for a HPWH to scavenge since this was living space. And if it did, how was that any better than having a water heater that used oil or gas? And though winter temps were seldom below freezing, they seldom averaged much above 45' in the garage. That didn't seem like a very efficient option for a HPWH.
Now we're building a new house in a different state (colder climate) and will use mini-splits for heat. So if you put a HPWH in conditioned space, it's essentially stealing its heat from the minisplit. But even though it is one HP stealing heat from another, I guess we're saying that is still more efficient overall than electric resistance heating elements. You just need to make sure that your minisplit heating the space where the HPWH is located can supply enough energy for both the space and the water.
So if the HPWH removes humidity, where does the condensation go?
Lastly there's the cost trade-off which depends on your hot water consumption and energy rates. A $3000 price tag seems like a long payback period. On the other hand I see some units for barely over $1000. I guess I'll have to check into this more seriously.
If you have a new all-electric build, a HPWH is probably a good option. Remember, if you had a cold spell and were concerned about the main heat pump's ability to handle the heating load, you can always switch the HPWH to Electric mode. To me this approach doesn't seem too different than relying on electric resistance heating to help heat pumps cope with cold spells.
Condensation requires a condensate drain. 365 day dehumidification; the more you shower, the more humidity you generate, the more the water heater runs and moisture it pulls from the air.
Some whole home dehumidifiers cost more than the cheaper HPWH's, though they'd likely be more effective at strict dehumidification (with an added heat penalty).
A very timely article for me, thank you! I'm currently selecting equipment for new construction in Zone 4C (Seattle) and evaluating HPWH placement options.
Is it actually a "win" in the conditioned laundry room? During the cooling season that makes sense, but it would be the same "win" in any conditioned space, right? In the winter, all that additional heat from the heat pump dryer would otherwise circulate within a tight house and reduce the load on the heating system, wouldn't it? So the total additional load on the air heating system would be roughly the same, since the HPWH would be "robbing" the heating system of the would-be benefit from the heat pump dryer.
I keep coming back to the same conclusion with HPWHs: In a tight house, it doesn't matter where you put them inside the thermal envelope. The recommendation in cold climates is to put it in a semi-conditioned or unconditioned space, but I can't figure out how that's any better than in a conditioned space with a high-efficiency heating system.
It's true that Btus from a localized source of heat in a low load house get distributed because it's sort of a closed system. So dryer BTUs aren't lost. But not all BTUs are equal as far as the HPWH goes.
The "win" is that the HPWH works more efficiently at higher ambient temperature. So it does matter where it's located in terms of its efficiency. If the dryer raises the temperature in a small laundry/mechanicals room by 10 degrees, then that raises the efficiency of the water heater. If those Btus are at the other end of the house, then the water heater won't see them and will have a somewhat lower efficiency.
So the basic argument is to put the water heater, which reduces temperature and humidity, next to another appliance that outputs those same things. There's also opportunity to concentrate plumbing and electrical infrastructure and the fact that these appliances are all a bit noisy, so if you put them in a small room together you can close the door and have peace and quiet.
Hope that's helpful.
Increasing the efficiency of the HPWH via waste heat from the HP dryer would require that the two are working at the same time. If consistently coordinating showers with dryer use is possible, this is a plausible consideration. If not, it's not, and the HPWH will only have regular room temperature air to pull heat from, and less if the laundry room door is left closed and the room cools down during operation.
As long as the two run within a couple hours of each other and the room door is closed, there will be a benefit. The heat won't move to or from the room that rapidly. I don't even have a closeable door to my utility room, and it is cooler than the rest of the house in the winter.
Interesting point. I wonder if, on average, residual dryer heat in the room from a closed door would benefit the HPWH more than the door left open and the room staying closer to the temperature of the house?
Maybe a good case for adding some thermal mass to and/or insulating the room and leaving the door closed?
I've attached the floor plans of someone wants to have it a shot !
I've been thinking about this for a while. All electric new build. I was going to put the instant HW heater in the laundry because how small those units are and can be wall mounted. But then realized the electrical loads it draws. Storage solution makes more sense so it's Heat pump time. But those are so big so I don't know if that would fit in my laundry room. So I wonder if basement makes sense. Or ducted some how. But then the distance to points of use will be much longer, and that'll end up wasting a lot of hot water in the pipes. So I'm still very torn. Location is CO climate zone 5. Can be hot enough to need air con in summer for 2 months (especially with the solar gain of those windows) and then below zero in the winter once in a while.
Bernard,
Nice set of plans. Nice architecture and good comprehensive working drawings.
Bernard - The garage is usually the most obvious choice since it's a buffered temperature and you don't have to worry about ducting or cold air exhaust. But you're right it's longer runs to the top floor. But I've seen worse. You could consider an on-demand recirc system, but since it requires user interaction those are not for everyone.
Did you see Albert's comment about the Sanden above? More expensive but a kick-ass unit. You could probably fit the tank in the utility room(?) It's a split system with just water lines between outdoor unit & tank. Makes very hot water, heat pump only, very efficient, works in below-zero temps.
Bernard - Nice plans!
My vote would be to supply and exhaust to the large Great Room area from the floor that separates the kitchen and bedroom above. All those large West-facing windows will certainly add some heat to that side of the house. If the supply and exhaust are kept a few feet apart they shouldn't interfere with each other.
You can put the HPWH in the Utility room and run the ductwork through the ceiling in the pantry (box it in) to get it over far enough to run Westbound through the floor joists to the Great Room. It will take up more room than a wall mounted on-demand unit, but I'm not sure you have a much more sensible location.
You could locate it in the Crawl Space and run ducts through the main floor, but ducts leading out of the conditioned space are generally a bad idea. Also, not sure I like the unfinished crawl space with sliding barn door access. That space should be kept as airtight as possible, with insulated above-grade walls if the budget allows.
I try to limit plumbing runs and ducts as much as possible with this build, hence the mini splits and wanting to put the WH in the center of the house etc. And I wonder if such long ducting may reduce the efficiency of the WH. One thought I have is to put the WH in the laundry room (assuming I can still make it fit), and vent or supply directly to the upstairs where it stands - directly above would be the common open area upstairs, so I can just put a vent on the floor. That area does not get the south and west windows like the greatroom but I would assume its still the hotter part of the house just because its upstairs. This way my ducting will be just a few feet from the WH to the ceiling of the laundry room, and then a vent directly above in the floor.
If I want to vent/supply to the greatroom, I feel that putting the WH in the garage might make more sense (since the garage is directly below the greatroom. Again, then I can put a vent on the floot etc. But this means more holes in my air envelope. And more distance to points of use (more wasted water and time) But putting the large WH in the garage would make the laundry room a much more pleasant space. Maybe thats worth the sacrifice in water/energy efficiency. Its really pick your poison!!
concerning the crawl space - its actually EVENTUALLY going to be a finished space - later down the road. zoning wont let me finish it (max sqft limit etc) so the barn door is just for show. It will be finished into either a guest suite/ADU kind of space or a movie theater/man cave etc. So there will be a 6' wide sliding patio door behind the barn door.
Ah, good plan for the crawl space!
The Rheem HPWH can have up to 340' of ridgid 8" ducting attached (less with bends etc.). Details on pg. 12 of the manual:
https://rmc-cdn.s3.amazonaws.com/media/uploads/iat/sites/36/2020/04/AP21681-UseAndCare.pdf
This is for the newly announced Gen 5 version. I would think the current models are similar.
Ducting straight up to the rec room area might be a good idea if you think ducts to the Great Room might not be possible. I'd be curious what others think?
Ducting the intake & exhaust of a unit like the Rheem is pretty easy if you have an agreeable layout and plan ahead. It works well and avoids all the cold air/warm air challenges.
That said, if you're going for air tightness it's really not a great choice since it's basically a hole to the outside. Hard to beat the Sanden if budget allows.
To All,
Since this question was the original impetus for me to attempt analysis, I am re-posting from Lance's single question about the newest hybrid from Rheem. Lance - I read the link for the manual and still do not see any CFM or W.C. values that assure/support being able to go over 40' with rigid duct. Another oddity is the circuit sizing chart on page 10. The unit has a 2.25Kw and a 4.5Kw element and a compressor in the heat pump all asking for electricity. Already above the top limit charted.
With a unit that could demand 6.75Kw by elements alone, plus whatever the compressor will pull, I am inferring a fairly complex program that distributes load. Selecting when an element is operating independently of the compressor or not at all. Interesting that such a complex controller can't share the actual usage time and energy output of the heat pump function.
This opacity is partly what lead me to try and calculate how much energy I would be harvesting and from where. My question re-post below.
I have come to question just how useful HPWHs might be in my local environment. Here in the south west, humidity is generally lower overall than most of the country. So low that "swamp coolers" are a frequent choice to cool homes here. Since swamp coolers do exactly the opposite of what A/C- HPWHs do, I decided to try and quanitfy what level of energy is available in lower humidity parts of the country.
Initially, I got lost in charts and formulas for long forgotten physics that didn't quite seem related to HPWHs, which are simple air conditioners with one coil stuck in a tank of water. An house A/C reference about condensate and the BTUs required to return air moisture back to water seemed to provide a more relevant start point. I may be very wrong, but here goes.
The A/C reference stated you need to remove 1060 BTU from a pound of water vapor to return it to liquid water at 52F. This is higher than the 970 BTUs needed to make 1lb of 212F water into steam, and back again, and for some reason this value doesn't mesh with the additional 160F drop from the 212F water in physics experiments. But I have used the 1060 BTU figure in the following thoughts.
The sensible heat available in air appears to be trivial compared to the latent heat in the humidity. The physics books say 1/4 BTU per F degree per lb for perfectly dry air. Likely not relevant to the real world. The latent heat of the water vapor per pound is substantial, as seen by the 1060 BTU value per lb of water condensed. What is not very substantial seems to be the total weight of water in a fixed volume of air, ie. the air inside a typical home in the southwest, as well as low ACH northern homes with balanced humidity.
Like A/C units for homes, the air passed through a HPWH will only give up part of its sensible or latent energy, so I am looking at the extracted water weight in a fixed volume of air to help judge available energy. The numbers I am coming up with indicate either, I am completely misunderstanding the physics involved or HPWH COPs will be very poor in low humidity environments.
Reading the chart correctly (always a chance I am not) then air at 70F and 50% humidity has water weight of 0.0079 lbs. per lb of air or roughly 1/8 of an ounce. A pound of air is 14 cu ft on the psychrometric chart, so to gather up 1 lb of water will take 128 times 1/8 oz. to get to 1 lb. That means 128 x 14 = 1792 cu ft of air holding 1 lb. And the pound of water is available only if you can desiccate the air to perfectly dry. Not very practical.
An 1800 sf home on slab with 8' ceilings has ~14,400 cu ft of volume available. For experimental purposes, no leaks. This is only 8x the volume holding 1 lb of water, so if one desiccated the whole house and harvested the energy of 8 lbs of water, you only have 8480 BTUs. Enough to raise about 11 gallons of water by 90F. Even throwing in double the recovered energy doesn't quite compensate for turning your home into the Atacama Desert. (And cold too, if the warning about dropping a room 15F on page 6 is taken into account)
It appears that warm moist air from an unlimited exterior source and vented back out through a HPWH is a much more viable option. Am I correct in thinking that the COP of HPWHs in places like a Florida garage will outperform my location by a huge margin? Where is all the magical heat in a 700 cu ft. room minimum specified for many HPWHs? Is the specific heat value of the entire mass of the house the secret sauce? The resident's body heat?
While HPWHs seem to be working satisfactorily for many in northern locations, the constant question of where to put them seems disconnected from the physics. The moisture to be found in a laundry would appear to have limited BTU value even if every ounce of water vapor from the wet clothes is captured. Sort of like getting one cookie then back to melba toast. Venting HPWHs within the confines of a low ACH structure poses a subset of problems and questions. Even attempting to duct in outside air in good months may be problematic.
Searching ducting for HPWHs has yielded little quantifiable information. Rheem offers duct adapters from 5" to 8", but no clear CFM or W.C. info. It is hard to imagine the CFM is very high in such quiet units, nor having much push to them. Given the losses inherent in ducting air from any source, I remain suspicious about ducting HPWHs more than a few feet. (new info not withstanding)
Does anyone out there have hard numbers that quantify the useful and available BTUs successfully being captured by HPWHs? Do Kill-a-watt meters work on them? I suspect that measuring condensate production will only reveal part of the energy capture, but I am not seeing a good physics description for the source of the purported efficiency gains being claimed by manufacturers.
Where have I missed the BTU bonanza?
I think you're thinking about it all wrong. The dehumidification is a side effect. The main way a HPWH captures heat is by lowering the temperature of the air.
I remember reading the compressor is around 4200 BTU/h, but I can't remember where to find that info, and I can't remember if that input or output. But think of it as a 4200 BTU/h air conditioner. It will run for a few hours after a shower until it has accumulated enough BTUs to heat up all the cold water drawn into the tank.
If you leave it on heat pump only mode, which you should if you care about efficiency and don't need faster recovery, the resistance elements will never turn on. No complex algorithm needed.
The BTUs recovered from moisture will be minimal. HPWHs aren't good dehumidifiers, because they aren't meant to be. A dehumidifier will make the coil relatively cold to maximize condensation. A HPWH will keep the coil relatively warm (but colder than the ambient air) to maximize efficiency. If the coil temperature is above the dew point you won't get any condensate. And there is a minimum temperature. Most of them are rated to work down to around 35-37F, which suggest they are probably keeping the coil above freezing because they don't want to deal with defrosting. So if the coil never goes below freezing, your house won't reach Atacama desert levels of dryness.
As far as where the heat comes from, it's the same as if you were running a 4200BTU/h air conditioner. It's going to cool the space. In the summer it will take some load off your AC or make the temperature a little more comfortable. In the winter your heat will run a little longer. In the spring and fall you might need to run your heat a little when you wouldn't otherwise. Or maybe there's enough heat in the ground around your basement to regulate the temperature.
It might be ideal to duct it to outside when the outside temperature is anywhere from the minimum temperature for the heat pump up to where you want to turn on your AC. When it's warmer than that you might as well take advantage of free cooling. When it's colder your central heat feeding the heat pump is almost certainly more efficient than using the resistance heating elements. But we're not talking about a lot of heat relative to the entire house, so it's not too bad to have it use indoor air year round.
Ducting a HPWH outside in cold weather is actually counter-productive. Every unit of air exhausted from the heat pump must be replaced through infiltration, un-balancing a ventilation system, or some combination of the two. If that incoming air is cold enough, it might even be colder than the exhaust from the HPWH.
On the topic of dehumidification I think you're right-on. Heat pumps get their high efficiencies from keeping evaporator and condenser coil temperatures closer together than farther apart. I've read tons of reviews from HPWH owners, and one in particular was very interesting; the owner observed that as soon as the relative humidity in his basement dropped below about 50% in the fall his Rheem HPWH stopped generating condensate. This is an indication that, as you pointed out, the evaporator coil just doesn't get that cold and is optimized to extract sensible heat rather than latent heat.
On an air conditioner that's called the Sensible Heat Ratio (SHR) and determines how much dehumidification you get as part of your cooling. Uber-efficient minisplits tend to have very high (low?) SHR and do very little dehumidifying, using a relatively warm coil and moving large quantities of air through it quickly. Set them to "dry" mode and the coil temp drops, the airflow drops, the cooling efficiency drops, but the "Pints Per Day" dehumidification goes up.
A friend of mine just installed a Rheem HPWH and I can't wait to have a look at it. He's thrilled so far with the efficiency, and he LOVES the app that lets him track how it's working. I'm interested mainly in how much noise it makes, since I will be ducting it into the living space of the South-facing living space of the house if I decide to use one and don't want it to be audible.
I'm assuming you can do balanced venting with a dedicated intake and exhaust, so the outside air is going through the heat pump but not mixing with the conditioned air in the building. I would probably also add dampers to allow switching between inside and outside air depending on the season.
We are currently building a new house and will have a HPWH in the basement mechanical room. The mechanical room shares a wall with the basement 3/4 bath. We're putting a shower in there for the occasional house guest and dog bath, but it will be used very sparingly. Would it make sense to vent that bathroom into the mechanical room rather than up and outside - thinking that the HPHW could make use of the limited warm/moist air and save a wall penetration.
I can think of several issues with that plan. For example the HPWH won't dehumidify the air enough, so you could have moisture issues, and unless the mechanical room has a vent to outside it's going to be under positive pressure from the fan, so humid bathroom air will leak into the rest of the basement. The short answer is the bathroom fan should vent outside.
Log in or create an account to post a comment.
Sign up Log in