Basement renovation

I’m renovating my basement (1956 bungalow) and putting in an income suite. I’ve gutted the entire basement and am finalizing planning/material selection. I had plans drawn up by an Architect and am planning to do most of the work myself with the exception of some electrical and plumbing. I have found GBA to be extremely helpful with my planning, but still have some questions. I live in Edmonton, Canada which is Climate zone 7.
Insulation is where I’m at!
Unfortunately, due to the age of the home, insulation in my house in general is poor. There is no insulation or house wrap on the exterior of the foundation. I am fortunate not to have any water issues though! I’m planning on using 2″ of EPS on the exterior walls and then framing with 2×4 and using Roxul in the wall cavities. I’ll then spray foam the rim joist although I’ve discovered that my floor joists are almost fully embedded into the foundation. I’m not planning on using a vapour barrier, although I’ll likeyput one up for the inspector. For flooring, I don’t have a vapour barrier underneath my foundation floor, it’s just concrete. I’ll be laying 2″ EPS on the floor as well and covering with a layer of 5/8 TG plywood which I’ll frame my walls right on top of. It will then be finished with laminate flooring.
Questions:
-What is the best method for insulating the embedded floor joists?
-I’ve seen folks reference 2 layers of the 5/8″ plywood. Is this necessary given my application?
-Do i fasten the plywood down or keep it floating?
-Sorry in advance but…. Do I need a vapour barrier given my cold climate?
Thanks!
GBA Detail Library
A collection of one thousand construction details organized by climate and house part
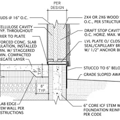
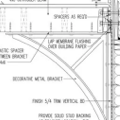
Replies
Ben,
Here are links to a few articles that you might want to read:
How to Insulate a Basement Wall
All About Basements
Fixing a Wet Basement
The last of these articles has advice for installing a horizontal layer of rigid foam on top of an existing slab, followed by a layer of OSB or plywood subflooring. (Scroll down to the section with the heading, "Insulating an existing basement slab.")
Q. "What is the best method for insulating the embedded floor joists?"
A. The best method for detailing embedded floor joists is to cut off the ends of the joists (which are vulnerable to rot) with a Sawzall or chainsaw, and to support the ends of the joists with new stud walls.
All other methods carry risks. The risk is higher in cold climates than warm climates; higher when the rim joist area is insulated than when it is uninsulated; higher when the indoor RH is high than when it is low; higher when the there is only a small distance between the exterior grade and the lowest wooden components of the building than when there is a large distance between the exterior grade and the lowest wooden components of the building; and is higher when there are bushes near the foundation than when sunlight and wind have free access to the exterior of the foundation.
Q. "I've seen folks reference 2 layers of the 5/8" plywood. Is this necessary given my application?"
A. No, it's not necessary. You can use one layer of 3/4" T&G plywood if you want, fastened through the rigid foam to the concrete slab with TapCons.
Q. "Do I fasten the plywood down or keep it floating?"
A. Either way. If it's floating, two layers of plywood help prevent "potato chip" curling.
Q. "Do I need a vapour barrier given my cold climate?"
A. I'm not sure what surface you are talking about. It's always a good idea to have a layer of polyethylene under your slab. If you think there isn't any polyethylene under your slab, you can install a layer of polyethylene on top of your slab, before you install a horizontal layer of rigid foam.
When it comes to walls, the rigid foam that you intend to install on the interior side of your basement walls is a vapor retarder. You don't want any polyethylene in your wall assembly.
With only 2" of EPS (~R8-R8.4) you would be a bit marginal dew point control on the above grade section for an R15 Roxul 2x4 wall in climate zone 7. The IRC calls out R10. See Table R702.7.1:
http://codes.iccsafe.org/app/book/content/2015-I-Codes/2015%20IRC%20HTML/Chapter%207.html
If it's air tight it won't be very risky to skip the interior vapor barriers, since below grade it would have plenty of dew point control. To satisify the inspectors and to lower the risk to nearly zero, a layer of 2-mil nylon (Certainteed MemBrain) in lieu of 4-6 mil polyethylene works.
Nylon is a variable permeance material sensitive to the relative humidity of the air next to it. When the EPS is cold enough to condense it lowers the RH of the entrained air next to the sheet nylon, and it becomes low permeance (much less than 1 US perm) , meeting Canadian code definitions of "vapour barrier". If the moisture levels in the stud cavity are high enough to support mold growth it becomes more vapor open than standard interior latex (3-5 perms), which allows it to dry toward the interior at a reasonable rate. By preventing rapid moisture accumulation and allowing faster dry times, the risk drops to near zero.
http://www.certainteed.com/resources/30-26-074.pdf
Thanks for the prompt responses folks!
Martin:
appreciate the detailed and timely response. A few follow up questions.
-Are there any DIY links you're aware of that detail this process of cutting off the ends of the joists?Do you actually need to physically remove them from the foundation? Mine are set in about 8 inches so full removal would be quite the process. My new load bearing wall would be against 2" of the EPS, so there would be about 2 inches between the old joist ends and the new top plate for the load bearing wall. Would I simply continue up the wall with rigid foam and then fill the rim joists (with or without the old joist ends?) with spray foam?
-I don't know for sure that I don't have poly underneath my slab, but given the age of my house, I'm fairly certain it's not there. I'll add the player of poly just to be sure. The previous owner had put down a low pile carpet that I had pulled up. As a result there is some glued on carpet mat. It's maybe a mil or two thick and varies in different places in the basement. It's slowly disintegrating with foot traffic in the basement. Do I need to remove this first or can I throw the poly right over top of it?
-My basement floor also isn't level. Should I use a self leveling agent on the slab or simply level the plywood? Or even level the rigid foam? I'm thinking shims?
D Dorsett:
Thanks, most of what you said was a little over my head, but I'll grab some of that Certainteed MemBrain you mention.Seems like a good alternative to the poly. I'll check with my Building inspector to be sure.
Thanks!
Ben,
Q. "Are there any DIY links you're aware of that detail this process of cutting off the ends of the joists?"
A. I'm not aware of any such article. However, one of my GBA articles discusses a variety of ways to address embedded joists. Here is the link: Insulating Old Brick Buildings.
Q. "Do you actually need to physically remove them from the foundation?"
A. No. The embedded part of the joist is abandoned in the wall. Once abandoned, it can sit there or rot, without threatening the rest of the joist.
Q. "My new load bearing wall would be against 2 inches of the EPS, so there would be about 2 inches between the old joist ends and the new top plate for the load bearing wall. Would I simply continue up the wall with rigid foam and then fill the rim joists (with or without the old joist ends?) with spray foam?"
A. Yes, the procedure you describe would work.
Q. "There is some glued-on carpet mat. It's maybe a mil or two thick and varies in different places in the basement. It's slowly disintegrating with foot traffic in the basement. Do I need to remove this first or can I throw the poly right over top of it?"
A. No need to remove it. Put the polyethylene on top.
Q. "My basement floor also isn't level. Should I use a self leveling agent on the slab or simply level the plywood? Or even level the rigid foam? I'm thinking shims?"
A. Either approach can work, but the self-leveling agent sounds a lot easier than shimming either the plywood or the rigid foam.
Thanks Martin,
I'll give it a go and see how cutting off the joists works. Leaving the joists in place makes this job very doable. I'll just cut them off then cover them in spray foam with the rest of the rim joist.
I was planning on completing the subfloor (with EPS under 3/4" T&G) and then framing over top. Now that I'm going to have load bearing walls at each end of the house, should I have the sill plate directly on the slab? I'm worried about compression of the EPS given the load of the wall. If so, then is there any way to insulate or create a thermal break so as not to create a thermal bridge?
Also, I'm trying to figure out if it's worth it to add more than 2" of rigid foam along the exterior walls? Does EPS have a diminished R-value return when you add more thickness or is it linear? For example if the R value is 4 for 1" is 2" R8, 3" = R12, ect? In your opinion are the energy saving substantial enough to warrant more than 2" considering I'm adding the Roxul as well?
Thanks!
-Ben
Ben,
Q. "Now that I'm going to have load bearing walls at each end of the house, should I have the sill plate directly on the slab?"
A. Yes. Make sure the bottom plate of the wall is pressure-treated.
Q. "Is there any way to insulate or create a thermal break so as not to create a thermal bridge?"
A. The thermal bridge is minor. Don't worry about it. Put EPS everywhere except where the bottom plate of the wall rests on the slab. In theory, if your slab is thin, it might not be able to support a load-bearing wall. An engineer might recommend cutting the concrete slab and pouring a wide, thick footing under the bearing wall. Necessary? If this detail worries you, consult an engineer.
Q. "I'm trying to figure out if it's worth it to add more than 2 inches of rigid foam along the exterior walls. Does EPS have a diminished R-value return when you add more thickness or is it linear? For example if the R value is 4 for 1 inch, is 2 inches R-8, 3 inches = R-12, etc.?"
A. Yes. Doubling the thickness doubles the R-value. Tripling the thickness triples the R-value. Every time you double the R-value, you cut the rate of heat flow in half. That said, the energy savings per year diminishes as the R-value increases. The first 2 inches saves more dollars per year in energy costs than the second 2 inches.
Q. "In your opinion, are the energy saving substantial enough to warrant more than 2 inches considering I'm adding the Roxul as well?"
A. In Zone 7, you want to install a total R-value on your basement wall of at least R-15. In your climate zone, a conservative approach calls for at least 43% of the wall's total R-value to come from the rigid foam layer, with a maximum of 57% of the wall's total R-value coming from the fluffy (air-permeable) insulation. For more information on this issue, see Combining Exterior Rigid Foam With Fluffy Insulation.