How risky is closed-cell foam on both sides of exterior sheathing?

I am about to start a complete renovation on a 200 year old cape style farm house in CT, zone 5. The two areas I am looking to address are the exterior walls, and an unvented roof assembly for second floor living space.
First the walls. The walls are roughly 4″ deep stud cavities. My thought was to cut and cobble staggered layers of 2″ and 1.5″ Glass Mat faced Polyiso (1.2 Perms at 1″ of thickness) tight to the sheathing, leaving a small space behind the sheetrock. I would also like to address thermal bridging in the future when I re-side the house. If the siding is stripped, and 1″ or 1.5″ XPS is added to the outside of the house with new construction flanged windows installed to the exterior of the XPS with a sill pan and proper tape sealing around the windows and a rain screen, how significant is the risk to the sheathing? I could add another layer of polyiso over the studs inside the house instead of on the exterior, but that involves relocating radiators, and I just plain like the idea of foam on the outside of the house to help smooth out the unevenness of the walls for the siding.
For the unvented attic roof, I have approximately 4.5″ of rafter depth. For that, I was considering the cut and cobble approach with the same material, except 2 staggered layers of 2″ Polyiso tight to the sheathing, then a 3rd layer of 2″ applied directly to the face of the rafters. Alternatively, I am considering filling the rafter cavities with 2# closed cell spray with a layer of 2″ polyiso applied to the face of the rafters, but I am concerned about the weight of the spray foam in this scenario. Thank you.
John
GBA Detail Library
A collection of one thousand construction details organized by climate and house part
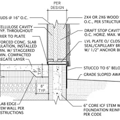
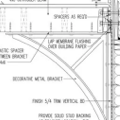
Replies
John,
When you get around to installing rigid foam on the exterior of your walls, specify EPS or polyiso, not XPS. Green builders avoid the use of XPS because XPS is manufactured with a blowing agent that has a high global warming potential. For more information on this issue, see Choosing Rigid Foam.
If there is a high likelihood that you will implement your plan to install exterior rigid foam at some point, I urge you to choose a vapor-permeable insulation to install between the studs rather than the cut-and-cobble method. One possibility is to install open-cell spray foam between the studs. For more information on this issue, see the following two articles:
Calculating the Minimum Thickness of Rigid Foam Sheathing
How to Design a Wall
For the roof, you definitely don't want to use the cut-and-cobble approach unless you can include a ventilation channel between the uppermost layer of insulation and the underside of the roof sheathing. The approach you are considering is risky. By far the best approach is to install rigid foam on the exterior side of your roof sheathing.
For more information on this issue, see these four articles:
Cut-and-Cobble Insulation
Insulating a Cape Cod House
How to Build an Insulated Cathedral Ceiling
How to Install Rigid Foam On Top of Roof Sheathing
Thanks, that was what I was afraid of. I am certain I will find some rotted sheathing, so for those areas, can I staple tar paper or WRB to the affected areas of sheathing before the open cell spray foam to uncouple it for future replacement?
Regarding the roof, the house is timber framed with purlins half way up the roof. There is no possibility for venting. Would padding the rafters with 2X's to increase the depth and using closed cell spray foam only between the rafters be advisable?
Alternatively, if I can justify a new roof, 4" of polyiso above the sheathing, open cell spray foam between the rafters and Membrain under the sheetrock? Thanks again.
John
In CT there are multiple nearby vendors trading in reclaimed rigid foam board at very cheap pricing. Some advertise here:
https://newhaven.craigslist.org/search/sss?query=rigid+insulation
https://hartford.craigslist.org/search/sss?query=rigid+insulation
https://newlondon.craigslist.org/search/sss?query=rigid+insulation
In zone 5 with a full 4" cavity depth you'll need at least 1.25" of exterior foam for dew point control, 1.5-2" would be even better.
Does this 200 year old house have a separate sheathing layer, or is the siding attached directly to the studs? If sheathed it's probably wide-plank pine, and if the siding has been updated in the past 10 decades there is probably some sort of kraft or rosin paper, or asphalted felt between the plank sheathing and siding (?).
If yes, the better way to go would be to put a 1" shot of closed cell spray polyurethane on the cavity side of the planking, and fill the rest with blown cellulose or fiberglass (or carefully fitted rock wool or high density R15 fiberglass).
The additional R value of cut'n'cobbled foam does very little for "whole wall-R", and the air sealing reliability of cut'n'cobble over time is fairly poor, whereas with an inch or more of spray foam air tightness reliability is quite good. At 1" most closed cell foam is between 0.8-1.5 perms, which is fairly ideal, since it's sufficiently permeable to allow seasonal drying toward the interior, but not so permeable that it loads up the sheathing with moisture over the winter. With 1" of closed cell foam (R6-R7) and a worst case of 3.5" of high-density rock wool (R15) there is sufficient foam-R for dew point control at the foam/fiber interface in your climate. Then anything you put on the exterior later won't really matter, as long as the window flashing details are right- the sheathing will stay dry.
At the roof deck you can do the same thing, but on roofs at least 40% of the total R needs to be closed cell foam for adequate dew point control in a zone 5A climate.
John,
Q. "I am certain I will find some rotted [wall] sheathing, so for those areas, can I staple tar paper or WRB to the affected areas of sheathing before the open-cell spray foam to uncouple it for future replacement?"
A. Yes, but if the amount of rotted wall sheathing is significant, it would be far better to replace the rotten sheathing (obviously, from the exterior) before insulating the cavities.
Q. "Would padding the rafters with 2X's to increase the depth and using closed cell spray foam only between the rafters be advisable?"
A. The answer depends on whether your roof has skip sheathing or solid sheathing, and whether there is visible roofing (like slate) peeking between the skip sheathing (if any).
If the roof has solid sheathing, you can create an unvented roof assembly with closed-cell spray foam on the underside of the roof sheathing.
Q. "Alternatively, if I can justify a new roof, [how about] 4 inches of polyiso above the sheathing, open-cell spray foam between the rafters and MemBrain under the sheetrock?"
A. That would work. For more information, see this article: Combining Exterior Rigid Foam With Fluffy Insulation.
Thanks everyone for the replies. The house does have wide plank sheathing, and I don't believe the siding is original. I know several sections have been redone and have tyvek behind them. About half of the sills have been replaced with PT, but no membrane between that and the foundation ( I am fixing this), so while updating has been done, the quality is questionable. I had considered the flash and batt method for the walls with open cell foam and roxul, but the idea of 1" of closed cell is intriguing.
As for the amount of rotted wall sheathing... I am hoping for minimal amounts as so much of the sill has been replaced, but I wont know until I start ripping. The roof has skip sheathing with plywood above that and asphalt shingles, so I am hoping that both insulation methods I was considering above are still valid for creating an unvented roof assembly.
Martin, from the articles you listed, I get the impression you don't much care for insulating Capes! I agree. My current house (1950's Cape) I turned into a colonial, and the 200 year old farmhouse we are moving into, the 4' knee wall is the exterior wall, so at least I have that going for me!
Thanks again.
John
Flash & batt with open cell air seals but it's very vapor permeable, takes at least a couple of inches to air seal, and has too lumpy a surface to not leave voids when working with batts (though it's fine with blown insulation.)
Batts are designed for particular stud spacings and dimensions, and can require a LOT of detail trimming/sculpting to get a good fit with antique buildings of odd dimensions & spacing, but blown insulation always fills the available space, no matter how what the depth & width spacing of the cavity is.