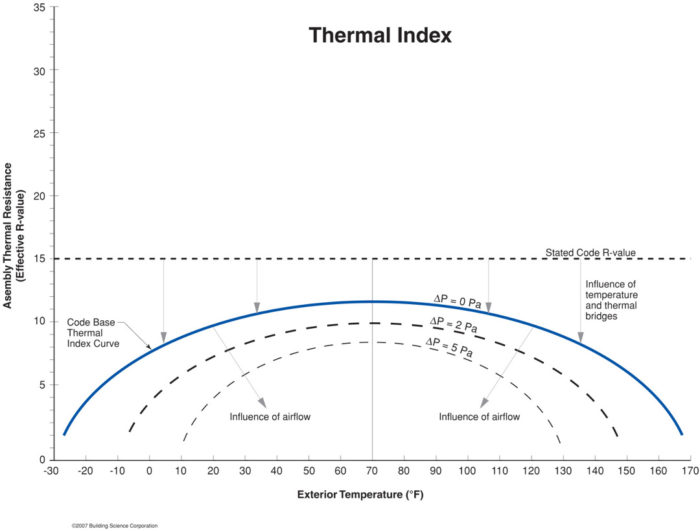
Image Credit: Building Science Corporation
R-value is the poor stepchild of building science metrics. Although it is often essential for builders, designers, and engineers to know a material’s R-value, this useful metric is regularly abused, derided, and ridiculed for its shortcomings. “R-value doesn’t measure assembly effects: thermal bridges, air movement, thermal mass, moisture content — all of which can all affect thermal properties,” explained Chris Schumacher, an engineer and researcher at Building Science Corporation, at a summer symposium in 2009. “R-value doesn’t do a good job describing the entire system.”
To R-value defenders, however, creating a list of things that R-value doesn’t measure is a trivial and pointless exercise. After all, a similar list can be developed for any metric or measurement device: for example, a thermometer doesn’t measure relative humidity or wind speed.
Even critics of R-value, including Schumacher, note that the metric has certain strengths. “R-value is widely accepted and FTC-regulated,” Schumacher noted at this year’s Building Science Symposium in Westford, Mass. “It is simple to measure. You can communicate it easily — it’s just one number.” On the other hand, Schumacher points out, “R-value implies that the thermal performance of a material is constant. But that is only true if the effective conductivity is constant, if there material has no temperature sensitivity, if the material has no airflow sensitivity, if there is no moisture adsorption, and if the material is homogenous.”
Did the developers of R-value make a mistake?
As I noted in an earlier blog, R-value (defined as the inverse of U-factor) was first proposed in 1945 by Everett Shuman, the director of Penn State’s Building Research Institute. Since 1979, the Federal Trade Commission has incorporated a definition of R-value into federal law. Insulation manufacturers and insulation installers must report R-values according to the FTC definition. The…
Weekly Newsletter
Get building science and energy efficiency advice, plus special offers, in your inbox.
This article is only available to GBA Prime Members
Sign up for a free trial and get instant access to this article as well as GBA’s complete library of premium articles and construction details.
Start Free TrialAlready a member? Log in
22 Comments
Fossil energy used per person
Fossil energy used per person per year and their sustainable energy used per year and finally the number of offspring they have and pets! LOL China limits offspring. When they raise their flag over the capitol we will too start to limit births which is the only true issue, no r value measured in complex ways.
Just sayin
Infiltration heat recovery
I can't say I agree with the second nugget but I do agree with 1 and 3. Infiltration degrades R-value in highly insulated walls and you need an air barrier on the inside and outside of the wall at extreme temperatures.
Heat recovery in assemblies and questioning the value of this
Martin, for further reading on your nugget # 2, check out this report my colleagues released 8 years ago about heat recovery in building envelopes.
http://epb.lbl.gov/publications/pub_index.html
If I recall correctly, this was a modeling exercise, but it should help illuminate the issue.
Ultimately, I question what the utility of this research effort is. Do we expect very different responses to temperature and air flow between different materials and assemblies? Between poorly constructed and well-constructed assemblies, I imagine the answer is yes. But with assemblies of similar air flow resistance and R-value (as currently measured), the differences of thermal performance would be quite small (I imagine). Also, it seems to me that the moisture content of the assemblies would have a large impact on performance, given the rates of sorption and desorption at different temps/humidity levels. If one were attempting the sort of whole picture thermal analysis that is being proposed, then leaving out changes in performance due to moisture is a folly. Of course, this would just make things more expensive and difficult to accurately control.
So, what is the purpose of this? Are we trying to aid designers in better climate-responsive decision making? Are we trying to improve energy performance modeling/prediction? Honestly, this could be a case where more info just leaves the vast, vast majority of professionals scratching their heads as to how best to proceed.
Great article.
Messed up link
Whoops, that link doesn't work properly, for some reason. You can click on Infiltration, under Residential Buildings. Then scroll to the bottom. The paper is third from the bottom.
Response to Brennan Less
Brennan,
Thanks for your comments and the link. Here's a direct link to the article: "Heat Recovery in Building Envelopes"
We'll see whether your prediction -- that the BSC researchers using their double-guarded hot box may not end up with data that are truly useful to the building community -- comes true. I certainly understand why you might think that; like you, I have my doubts about the outcome of the project.
However, the researchers doing the work are top-notch engineers and scientists struggling with a tough challenge, and I wish them the best.
fascinating
Much appreciated blog.
I enjoy learning more about physics applied to building issues.
Why such high temps?
In Lstiburek's tests is 144deg used because of the potential for an attic to reach that temp?
Also, are we talking vapor permeable or impermeable interior air barrier. In Tahoe/Truckee area we are required to install a vapor retarder on the interior of walls. It is commonly done by the insulation contractor in a not-so-craftsmanlike way, but would be an air barrier if installed properly. I'm guessing the purpose is to stop a convection loop??
Regarding both side barriers:
Regarding both side barriers: see page 5 of Lstiburek's "understanding vapor barriers"
http://www.buildingscience.com/documents/digests/bsd-106-understanding-vapor-barriers/files/BSD-106_Understanding%20Vapor%20Barriers_r2011.pdf
Seems like a direct contradiction.
Now Im really confused!
Response to Sam Marsico
Sam,
You are confusing air barriers and vapor barriers. An air barrier stops air movement but not necessarily vapor movement. (For example, gypsum drywall is an air barrier but not a vapor barrier.)
A vapor barrier stops vapor diffusion but not necessarily air movement. (For example, vapor-retarder paint and the kraft facing on fiberglass are both vapor retarders but not air barriers.)
Lstiburek and other building scientists warn that in some types of wall assemblies, a double vapor barrier can be a problem. But a double air barrier is not a problem, as long as at least one side is vapor-permeable. (The Airtight Drywall Approach is one way to install a vapor-permeable air barrier.)
For more information, you might want to read these articles:
Questions and Answers About Air Barriers
Vapor Retarders and Vapor Barriers
Forget Vapor Diffusion — Stop the Air Leaks!
Another response to Sam Marsico
Sam,
Yes, attics can reach 144°F.
And you guessed correctly that the reason that some experts recommend that walls have both an interior and exterior air barrier is to prevent the exchange of air between the stud bays and either the exterior or the interior air -- especially when fibrous insulation might allow a convective loop to develop.
Convection loops. Years ago
Convection loops. Years ago Pop Science had an article explaining that double envelope homes once thought to set up a convective loop actually transferred energy via tiny eddies if I remember right. So whenever I see convection loops mentioned....
So should we say, "micro-eddy energy transfer phenomena?"
Good and bad loops
Convective loops between panes of glass or inside walls is to be avoided. A convective loop within a building envelope that is very airtight is desirable and will minimize stratification. I have found buildings built airtight with adequate insulation on all sides have close to even temperatures throughout. Open floor plans in multistory homes are the main beneficiary of the convective loop.
Martin, do we stand any
Martin, do we stand any chance of getting everyone to drop the term "vapor barrier?" We ought to replace it with "water vapor diffusion retarder" (WVDR) or something else that distinguishes better between transport by diffusion vs. convective flow.
Response to Dick Russell
Dick,
I don't think that we need any new terms. "Vapor retarder" and "vapor barrier" are clear in my mind.
Vapor retarders and vapor barriers are intended to lower vapor diffusion rates. Air barriers are intended to stop or reduce the flow of air. It's really not that complicated.
The confusion arose in the 1980s, when a lot of builders started calling 6-mil polyethylene a "vapor barrier." Of course, 6-mil poly is a vapor barrier -- but it is also an air barrier. The fact that poly can perform both functions confused builders.
R-value
The single biggest factor responsible for superior energy efficiency in a home is its shape. Shape makes all the difference in the world. As mentioned before of all possible geometric forms the pyramid has the least amount of exposed exterior surface area per square foot of heated or conditioned floor space. Heat loss or gain is a direct mathematical function of surface area.
A common term used in construction today is "R" value when talking about insulation in the roof or walls. This is a very misleading term and is often misunderstood. It is supposed to indicate the relative energy efficiency of a material in stopping the flow of heat through a wall or roof. The coefficient of heat loss, which is a small decimal point number describing the heat flow in BTU’s per hour per inch of thickness, is the "U" factor and the reciprocal of that decimal number, or 1 divided by the U factor, is called the "R" factor, which is a whole number. The larger the "R" value then the better the home’s efficiency, right? Well, not exactly! Insulation’s "R" value is only one small part of the formula used in calculating a building’s total heat loss or heat gain. A claim of any percentage amount of comparative energy efficiency is quite misleading as well. A humorous but true old adage says that "figures can lie and liars can figure" should suffice to remind us that we should examine the whole picture when it comes to claims of energy efficiency. A truer statement that actually proves any buildings energy efficiency is the actual energy bill history paid by the homeowner. Those are the numbers that actually count. An analogy for instance: in the automobile industry would be to say that, this vehicle gets 15% better gas mileage than a comparable sized auto.
It seems much clearer, when we can measure miles per gallon, and judge for ourselves the relative efficiency of any particular vehicle.
A building’s exterior surface area measured in square feet multiplied times the material’s "U" factor and the design temperature difference between the interior and exterior surfaces (Delta T) will yield an overall heat loss in BTU’s per hour. A perfect vacuum within the exterior shell of a structure would lose zero BTU’s to the outside environment. If a building leaks air like a sieve through all the joints, doors and windows it would lose all of its heat energy in a very short time. The point being that the shape of the building and the air tightness of it are much more important in determining energy efficiency than simply the "R" rating of the insulation.
R-value continued
The lower total outside surface area results in greater heating and cooling savings. The following comparisons between a pyramid, a dome, and a box show the efficiency rating as a percentage of exterior surface square footage to the amount of interior floor space enclosed. A one to one ratio would be 100%; a 2:1 ratio would be 50% efficient. Therefore, a higher percent of efficiency is better in this comparison. Look at the numbers that compare three approximately same sized geometric forms that have similar ground footprints.
A comparison of the Pyramid Home to the Geodesic Dome Home and the Standard Box Home
A PYRAMID HOME
32 ft. x 32 ft. pyramid (footprint of 1024 sq. ft.)
1553 sq. ft. total floor area (first floor & second floor)
1663.3 sq. ft. total outside surface area
The ratio of floor area to surface area = 1553/1663.3 = 93.4% efficient
A DOME HOME
35 ft. diameter dome (footprint of 962 sq. ft.)
1661.5 sq. ft total floor area (two floors)
1990 sq. ft. total outside surface area
The ratio of floor area to surface area = 1661.5/1990 = 83.5% efficient
A BOX HOME
23 ft. x 50 ft. box (footprint of 1161.5 sq. ft.)
1150 sq. ft. total floor area
2337.5 sq. ft. total outside surface area (14.8% more area than a dome)
The ratio of floor area to surface area = 1150/2337.5 = 49.2% efficient
This comparison shows that a pyramid is almost twice as efficient as a box and more than a dome when comparing exterior surface area to interior living space. Isn't this by far the most important consideration?
The percentage advantage here, along with the pyramid's perfect heat-flow shape, can save 75% of your monthly heating and cooling costs.
Air infiltration heat recovery
Air infiltration heat recovery through has been studied, in both theory and in tests. See Timusk J, "Performance Evaluation of the Dynamic Wall House", 1987, University of Toronto, as well as many papers by Calridge DE, such as "The energy impact of infiltration through an insulated wall" 1992. My thought is that despite possible heat recovery through a wall, it's still preferable to restrict air movement through the building assembly as much as possible and introduce mechanical heat recovery for minimal required ventilation.
Canadian researchers are developing a wall energy rating (WER)
Like the researchers at Building Science Corporation, a group of Canadian researchers has been using a guarded hot box to develop a new way of rating the thermal performance of wall assemblies.
The researchers (Hakim Elmahdy, Wahid Maref, Mike Swinton, Hamed Saber,and Rock Glazer) hope to develop a metric that they dub the wall energy rating (WER). For more information, see Development of Energy Ratings for Insulated Wall Assemblies.
[Thanks to André Fauteux for pointing out the existence of this paper.]
ORNL standards
For 20 years, I have been following the standards for insulation in floors, walls and ceilings from Oak Ridge National Labs. I have built homes that use less than 1/8 chord of wood per year, or just a few gallons of propane for heat. No cooling is required here in Flagstaff, AZ. This is far below the average natural gas cost of $250 in January.
I never worried about the issue of true representation of insulation value. Just follow the recommendations! Let's not get too geeky about sustainable building. We know what works, just do it.
R-Value thoughts of Dennis Hayes
Dennis, your thoughts on the shape of a home and how this affects the total surface area is one I've considered before as well.
Personally I'd like to see you do the calculations again and make the homes more comparable - almost identical. As a realtor, I can say that 1,600 SF living area in southwest Florida is a size desired by many and a good starting point. Here virtually all homes are single story but I can see that that wouldn't work efficiently with a dome or pyramid. So stick with two-story homes but also for the box home. Calculate the ceiling height at 8' and add one foot for the second-story floor thickness. Make the outside walls one foot thick. The box home should also be a cube, not a rectangle, to make it more similar to the other two homes. Consider the box-home roof to be flat with the insulation on the attic floor. Please report the surface areas of the second floors in the dome and pyramid homes.
As I have come to realize through the years of my researching green building, rarely is it good to make a major decision based on one issue. This is no exception. This whole discussion is, in my opinion, mainly theoretical. Most people would probably not choose a dome or pyramid shape for their home. Sloped interior walls become almost useless for the way most people use them: hanging pictures and decorations, cabinets and book shelves. The curved walls in a dome would not work well with furnishings that are based on walls being straight. Neither domes nor pyramids fit in well with most neighborhoods. Most home owners would not want to live in a home that doesn't fit in with the neighboring homes and some neighbors would certainly find it unacceptable.
So, even though a dome or pyramid might be more efficient mathematically, for most people there are other issues involved that would be more important to them than energy efficiency. That brings us back to finding a good compromise. With your thoughts in mind, I would say, choose the smallest home that works for you and then make it as close to square as possible. Eliminate all windows on the east and west walls, if possible, because they bring in a huge amount of heat in the summer and often don't provide much heat gain in the winter. Now build the home with the highest affordable energy efficiency.
R-value and wall systems
Great information. However, I think there is more to talk about. Our 09 energy code still allows us to use a 2x6 wall with R-21 fiberglass. The builders I work with think this an inferior wall system when we're trying to achieve ACH numbers around one. On top of that, we are interested in finding a wall system that evaluates not just thermal performance but dew point, material savings, total embodied energy, thermal short, usable square footage savings, total cost, industry acceptance, sustainability, installation performance/failure rate, air infiltration performance, adaptability to other climate zones, time savings, and insulation diminishing returns.
Some sort of point system covering the above criteria would help us and our state in finding a suitable wall system for future building standards.
Response to Anders Lewendal
Anders,
I agree with you that a 2x6 wall with fiberglass batts makes a lousy wall system. If your point is that the current code is poorly written and not very stringent, you'll get no argument from me.
Until someone invents a new metric, we'll need to find a way to write our building codes in a way that defines wall performance in a different way from just saying, "Look at the label on the insulation package from the lumberyard." The next version of Energy Star is trying to do that; there are other ways that the code could be written.
Code writing isn't rocket science; it's just a type of technical writing (something I do for a living). Up until recently, it's been done quite poorly.
Log in or become a member to post a comment.
Sign up Log in