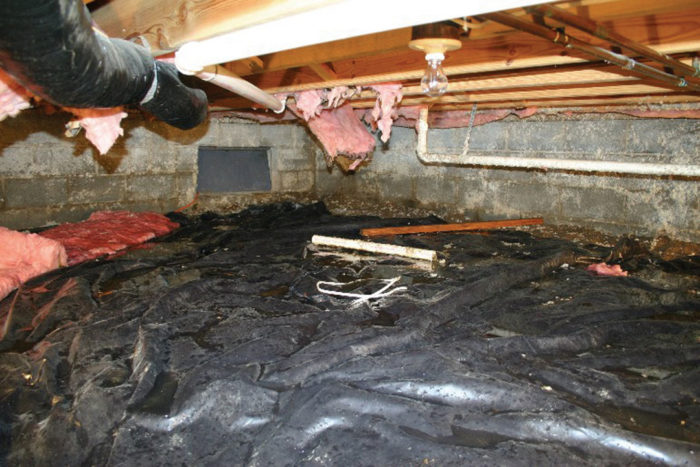
Image Credit: Aire Solutions
Residential foundations vary widely from one corner of the U.S. to another. Builders in some regions love basements, while builders in other regions swear by slabs on grade. Although most builders have a theory to explain these regional preferences, the main reason for these variations is habit, not logic. In areas of the country where basements are rare, there usually aren’t any technical barriers to building basements; and up north, where basements rule, it’s perfectly possible to build on a slab.
Slabs have several virtues: they are inexpensive and they keep all of a home’s living area above grade, away from dampness and mold. Basements also have their virtues: they keep plumbing pipes from freezing, provide a good place to install a furnace and run ductwork, and provide a useful area for storage.
Crawlspaces cost almost as much as a basement, with none of a basement’s advantages
Crawlspaces are more of a puzzle, and it’s hard to come up with a reason to like them. I’m sure that as soon as this blog is published, a builder from North Carolina will write in with an eloquent defense of the crawlspace. I don’t have a dog in this fight, however, so if you really want a crawlspace, go ahead and build one. Just be sure you get the details right.
If you’re perverse, and you want to build a damp, moldy, nasty crawlspace, just do two things: insulate the crawlspace ceiling with fiberglass batts, and vent the crawlspace to the exterior. If you live in the Southeast, within a few short years the fiberglass batts will begin to hang down at odd angles like drunken stalactites. Every summer, the open vents will introduce huge amounts of moisture into the crawlspace. You’ll end up…
Weekly Newsletter
Get building science and energy efficiency advice, plus special offers, in your inbox.
This article is only available to GBA Prime Members
Sign up for a free trial and get instant access to this article as well as GBA’s complete library of premium articles and construction details.
Start Free TrialAlready a member? Log in
124 Comments
NC crawl spaces
First crawl space justification from North Carolina- flood elevation requirements.
Second- high water table negates a basement,so a conditioned crawl is sometimes the only/best way to get the ducts in the thermal boundary in a multilevel house.
(you asked)
Another reason to do crawl space...
Great article, but I'll give another reason to do crawl space. Very expansive soils w/ high PVR.... most times you have to do a peer and beam foundation. Very common in TX.
Love/hate crawls
Almost no one has a basement here in NW WA, most are crawls, some are slabs. I will say one thing for crawls--if you want to remodel, access is easy compared to a slab. Folks with slabs need to plan on leaving the bathrooms and kitchens right where they are.
What's the detail for termite viewing? You want to insulate the interior of the perimeter walls, but you need to leave a 3" strip bare directly under the mudsill? Is this continuous around the entire house?
Response to David Meiland
David,
I guess (like me) you live north of the termite line. Aren't we lucky?
Termite inspection wreaks havoc with the continuity of a home's thermal envelope. Those insects are nasty little creatures -- another reason to live up north.
# 1 Best Use of Crawlspace
Storage space for large quantities of drywall mud
Just Kidding...
I do think slabs are better for Universal Design & "Aging in Place"
Personally anti-slab
I think I'll run a new cat6 to the office, or a dedicated electrical circuit, or a coax to a new t.v., or maybe I want a hose bib where the builder was too cheap to install one, and I absolutely need to run a gas line so I can get rid of the electric range... and a dozen more reasons off the top of my head.
I have refused to buy otherwise desirable houses because they needed updating, but were on a slab. All houses need updating, and needs are changing more quickly than ever.
All you slab-haters out there...
Basements!
Sealed Crawlspace Ventilation for Superinsulated House
Martin,
Thanks for the thorough blog.
For those of us who are unlucky enough to live with termites, this is a quandary . . .
For a sealed crawlspace, how would you meet the intention of the IRC ventilation requirement, given PH airtightness, minisplit heating / cooling, and HRV?
Do you know of any PH projects that use a sealed crawlspace, or are they all built on FPSF?
Response to Daniel Ernst
Daniel,
I know of one Passivhaus with a crawl space -- the Freas house in Olympia, Washington. The builders decided to insulate the floor joists above the crawl space with blown-in fiberglass, and to keep all of the mechanical equipment and ductwork upstairs.
Basements ;-)
Quotes taken from the book: "From The Ground Up," by John Cole and Charles Wing
"A full basement foundation is essentially a large and expensive concrete-lined well that we try to keep dry."
"It is difficult for me to comprehend how any harmonious relationship with the natural world of your site could lead you toward a full cellar. One does not follow the other."
"There are no two ways about it – I agree with Rex Roberts – the cellar is second-class space. It’s naturally dark and damp, and to achieve anywhere near the same livability as above-ground space, it will end up costing as much or more per square foot."
the fine print
Martin says: "Another option (for CS insulation): insulate the exterior of the foundation walls."
I add, referring back to our SE obsession with termites -- Be sure to check w/local code officials re: termite protection for insulation before going too far along with plans for exterior insulation. Many will not permit it under ANY circumstances even though some new product developments involving pesticides and sealed (in plastic) insulations offer promise for the future.
Termite inspection strips: fortunately, the Delta-T in zone 3 is significantly less extreme than elsewhere. I've lived in New England; and I've lived in GA; and I'll trade y'all some kudzu and termites any ol' time.
RE: slabs -- the latest in snob zoning. Several counties in this area won't accept slab on grade going forward. Slab construction will, in the futre in these counties, be required to be raised slabs. 18" above grade is "suggested."
Joe
Martin has it almost right...
There are way too many issues here to get into all of them with the limited time I have available, however, there is one that is way too important to leave out: The RIGHT way to do a closed crawlspace is to insulate the floor of the house the same way you otherwise would (R-30 fiberglass batts in our neck-of-the-woods), THEN insulate the crawlspace as needed to assure that the total UA from the crawlspace to the ground or ambient exterior is LESS than the UA from the house through the floor. This assures that the crawlspace will always remain above half of the difference between the outside and the inside, which in most climates will assure a dry crawlspace. This formula can be adjusted as needed for different climate zones. The big payoff is that when the delta-t through the floor is less than half what it would be with a vented crawlspace, the heat lost through that floor is half, usually resulting in a 7% to 15% reduction in total heating or cooling load on the house.
One other note, I NEVER allow air from the house to go into the crawlspace in my climate, it is way more moist than the outside air, and would CAUSE condensation. Make sure you know what the relative humidity and dew-point of your typical inside and outside air is, and design your mechanical ventilation accordingly. I use a small bath fan that operates on a humidistat to bring more cool, and therefore dry, air in from the outside. This is an exhaust-only fan, using passive leakage to supply make-up air, assuring that any radon or other undesirable elements are not forced into the living area, as they would with a positive pressure system. In a humid climate, you would want to bring the air in from the house, as Martin describes in his article. In more than twenty years of doing closed crawlspaces, I have yet to see the fan ever come on, it is only there for the code official...If you have done your calculations right, you will NEVER get condensation in a closed crawlspace.
Regarding insulating the outside of the walls, this is the best place for the insulation if you can protect it well enough. Try a sprayed-on polyurea coating, it is just like a heavy vinyl coating, and I don't think many termites or other bugs even could eat through it.
Ted: Where are you referring to when you refer to your climate?
Considering Martin doesn't
Considering Martin doesn't like the crawl space on principle he does a pretty good job of describing how to do it right, and kudos for pointing out the variations in regional conditions that affect performance. Echoing Hunter's comment, it's said here in the Carolina Piedmont with its high water table that either your basement will leak and be full of water or it won't leak and your house will float up out of the ground. If the slope is enough for a walkout, fine - in other conditions a nonventilated crawl space takes a lot of beating.
Response to Ted Clifton
Ted,
Concerning your two suggestions:
1. I don't doubt that your proposed insulation method -- insulating the floor above the crawl space as well as the crawl space walls -- results in a dry crawl space and good thermal performance. Many builders and homeowners will balk at the added expense of insulating twice to create a double thermal envelope, but for those who are willing to go that route, I'm sure your proposed insulation method will work. To me, the complicated solution just highlights the inherent disadvantages of crawl spaces.
2. In my article, I explained the two options listed in the International Residential Code for conditioning crawl spaces. One option is to install a fan that exhausts air from the crawl space along with a grille that provides makeup air from the house. Although you don't like that method, it is one of two code-mandated options, and it works in most climates. The question of how to condition a sealed crawl space is enormously contentious; suffice it to say that no method of crawl space conditioning is without drawbacks, and there are strong arguments on all sides of this issue. If you have a system that works well for you in your climate, and if your local building inspector approves of your method, then go for it. There are some risks to your approach -- the possibilities of poor indoor air quality or high radon being among them. But if you have satisfied yourself that your homes don't have these problems, you are good to go.
Again, these contentious issues remind me of why slabs on grade look good.
Martin,
Could you revisit this and explain how to seal off a porch that is included in my crawlspace? I was wondering how I would build a small wall to close that area off to outside air (cracks between floor boards on the porch). Hope you can help! I can take pics if needed tomorrow morning.
K. Dodson,
If your crawlspace lacks a wall on one side, you would (ideally) install all of the missing components of that wall: a concrete footing, followed by either a concrete block wall or a framed wall that extends all the way to the joist above. This wall should be as airtight as possible. Once complete, it should be insulated.
For more ideas, see this article: "Crawl Spaces vs. Skirts."
Slabs on grade are cut into
Slabs on grade are cut into and modified all the time. Hilti makes all the tools to do the job dust free. We also use large barn fans and gas powered water equipped diamond saws. Actually just did a cut Friday to add a floor drain. Two crew and one hour done. I like cutting through floors to make improvements or changes to bath and kitchen plumbing and do so often as by far the best way to do the work efficiently. Last year we redid a dental office changing much of the plumbing layout. The slab was cut, work done and slab patched the first day, done. I just did the plumbing, but loved learning how easy a slab can be to work through given the right tools and techniques.
Great article Martin, much needed info. And I second the idea of building slabs raised to deal with water.
crawlspace w/ no crawl no space
We're working on a deep energy retrofit and have two conditions I'd like to describe and ask if anyone sees any redflags.
We are in cold climate zone 6.
Condition 1-
On a 14' extension to an existing home we are pondering a sealed crawlspace completely filled with insulation (i.e. no air space). Footings are located below frost line (42") and a 8" concrete block stem wall is insulated to the exterior to match the retrofit of the existing basement. 12" I-Joists sit on a sill on the new stem wall and tie back to the rim joist of the existing basement. Ground is excavated to only 2" below the new I-joist flooring. Continuous 6mil poly covers the ground and up the sides of the basement and stem walls and rigid EPS insulation is laid on the poly. I-joists laid and cover with Inusl-Web then dens packed w/ cellulose insulation. Floor sheathing is next covered by a self leveling compound that will function as the air barrier. Any red flags? If this were a cold climate wall the vapor retarder would be on the wrong side but the vapor drive dynamic down into towards the ground must be different then between conditioned spaces and outside air.
Condition 2-
The existing structure had been added onto in the past. This former addition sits on an uninsulated slab on grade - may have been a former attached garage slab. This slab is 14" below the main level floor plane. For the retrofit we are proposing hanging a floor above the slab to time out with the main level. On the existing slab we would (similar to condition 1) lay a 6 mil poly vapor barrier, lay EPS insulation and between the floor joists dense pac the cavities with cellulose. Same issues as Condition 1 but here we have much less financial flexibility to move to a typical sealed crawlspace or basement if this proposal draws redflags.
Slabs Rule except with Expensive Land
Some neighborhoods may have such expensive land (say $60/foot and up) that the economics dictate that you should build a basement. If you don't, someone will eventually buy that home and scrape it off so they can have a basement. It's one of the few things that you just can't retrofit. Some neighborhoods also have zoning codes that limit the height to one story or 1.5 stories. Basements make sense there too.
Otherwise, thickened edge slabs are better:
1. Energy detailing is easier.
2. Slabs add some thermal mass to the main floor, which reduces diurnal temperature variation.
3. The most durable flooring of all is concrete. It's also the most economical of all. Stain it and seal it, and you're good. (Mine is 6 years old and I can't believe it looks like the day we did it. Hardwood usually shows some wear areas in that time.) And it's still trendy as a finished floor.
4. If you can build a 3rd floor, the house footprint can be smaller, which makes the yard bigger.
5. The 3rd floor of a slab house costs less per square foot and is worth more than a basement.
Response to J Chesnut
J,
I see a contradiction in your description. You say you are proposing "a sealed crawlspace completely filled with insulation," but you also say that you will use "I-joists ... with Inusl-Web then dense packed w/ cellulose insulation."
So, I don't get it. Do you want to fill the space below the Insul-Web with cellulose, or just the space above the Insul-Web -- that is, the joist bays? If you're just filling the joist bays, then you're not building "a sealed crawlspace completely filled with insulation," because there will be an air space below the Insul-Web. But if you are completely filling the crawl space with insulation, why bother with the Insul-Web?
clarification
Martin,
Thanks for your response.
The idea in both conditions is to completely fill the space between the I-Joists and the space below the I-Joists with insulation. The space inbetween the I-Joists with cellulose, the space below with rigid board insulation. The space below the flooring joists would be minimal ~1.5" -2.5". In order to gain some extra R-value and have a material less susceptible to moisture damage seemed like a good idea to try to fill the space below the I-Joists with rigid EPS. So the rigid foam would sit tight or slightly below the bottom of the I-Joists and the dens-pacing of cellulose would happen from above the floor joists. Insul-web would be used to contain the cellulose insulation as it was being installed from above and then later covered by the floor sheathing.
I think these conditions could be well detailed and executed in the field. With the rigid insulation below the I-joists it seems like the I-joist themselves will stay warm and not become a surface for "condensation". What I can't wrap my head around is if something in the floor assembly were to become wet for whatever reason how can we know if there is sufficient drying potential in the up direction back to the interior finished space?
Living on a slab
My house is on a slab, and I can tell you, it is significantly cooler inside than the ambient temp outdoors in zone 5a. The only way it could be a "thermal" mass is with in-slab radiant. Otherwise, it is a "cooling" mass.
Response to Shane Clafin
Shane,
Thermal mass works during the summer as well as the winter. On hot summer days, interior thermal mass will prevent the indoor air temperature from rising as quickly as it otherwise would. Similarly, during the winter, on very cold days the interior thermal mass will prevent the indoor air temperature from dropping as quickly as it otherwise would.
An insulated concrete slab does not require in-floor radiant tubing to work as thermal mass.
If you are unsatisfied with the performance of your floor, it's worth asking: did you remember to install continuous horizontal insulation under your slab? If so, how much did you install?
Second response to J Chesnut
J,
Okay, now I understand your proposed plan.
I say, "Don't do it."
If you want to use wood framing, you need enough of a crawl space under the framing to inspect the joists -- that is, enough room for a small adult to crawl in without spelunking equipment.
If you don't have enough room to crawl, you need to pour a slab. Fill the area with gravel (compacting as you go with a plate compactor) until you reach the level where you still have enough room for a layer of rigid foam insulation and a 4-inch slab.
But it looks good on paper ;
But it looks good on paper ; )
Thanks for the feedback. Figured there had to be a reason I haven't heard of anyone doing this.
Back to the drawing board.
In South Jersey we have to many crawlspaces
I have commented before on this issue. I have a passion for conditioning crawlspaces. As Martin said the first thing my crews do when they are working a retrofit is clean the floor. I do the vapor barrier a little bit different, i use 8 mil/12 mil/16 mil scrim reenforced vapor barrier. The mil difference for me is how bad the earth is in each crawl. Some dirt floors have a lot of fill dirt with to many rocks to remove (so I go with 16 mil and a before than I might even lay some poly to pad a path to crawl to appliances (sometimes I may double up on vapor barrier). I good scrim vapor barrier will make a world of difference with overlapped seams of 12 inches, buttered with muck or (what I use) number 15 white vapor mastic by RCD. The vapor barrier is always installed 12 inches over the ground level (always unless the dirt is as high as the band joist & yes I have seen it). Once the vapor barrier is installed depending on budget I drop the thermal barrier down the walls with either polyisocyanurate sheathing typically 2 inch (R-12) or Thermex sheathing (use nothing but Thermex sheathing when there are gas fired appliances in a crawl) (R-14) . I havent been able to use anything thicker than 2 inches due to budget numbers but will post one day when I install 3 to 4 inch poly iso. I have used 2 part spray foam (high density/closed cell/1.75 P.C.F., many names same game). We always make sure the nad joist is either sprayed with 2 part or we seal all infiltration/exfiltration points with 1 part spray foam (we only use 16 pounders with a bottem load gun). Once the band joist is done we cover it with glass wool batts. All seams of the poly iso are taped with UL181 tape and than painted with number 8 gray mastic.
last but not least we install a supply vent (when possible) and a return vent. the air change is enough to make the crawl a wonderful place to dwell (if your into that kind of thing) and really, really makes a huge difference in the winter months.
As for vented crawlspaces what I have my crews do is cut around them when installing the polly iso than I have them make a removable plug for the vents. This makes the vents useful if there is ever a flood in the home or a pipe leak. Pop off the plugs let the crawl dryout and place the plug back in.
I have had nothing but rave reveiws from my customers from our work in crawlspaces and those reviews are what make me stand by my methods.
I am always willing to discuss these methods with anyone who wants to! Yes I do consider myself as the green mad wizard!! I hope my feedback is of value to our community! thanks for reading.
Frank A. Bovio
Thanks Frank, this was helpful (still years later).
South Florida coastal stilt homes
Slabs vs. basements vs. crawl space....did we forget stilt homes? We live near the coast in South Florida in a stilt house that's about 4 feet above the ground (actually sand) due to flood requirements. This style allows for storage space, saves on fill and if built higher....garage parking underneath. Ours has no insulation under the floor or any walls. Completely open. Coastal breezes keep the space cool and airy with no signs of moisture but I'm always wondering if I should insulate the floor ....but how. Spray foam seems to be a good option but don't know the effects of salt air and humidity when the foam is exposed to the elements.
permits and conditioned crawlspace
Has anyone ever had a building official require a pe mit for a conditioned crawlspace based on the assertion that you are adding new "conditioned" space to the existing home? Here in California a building owner is required to pull a Title-24 permit, that is perform Title-24 energy documentation showing that the addtiion conforms with the state's T-24 energy requirements, for additions. SMUD, the utility I work for, supported a just completed a project with Habitat for Humanity where we "sealed" and insulated a 18" crawlspace - (it was nasty), and lo and behold the city official required them to pull the Title-24 permit because it was an addtion. Has this happened to anyone else in the country? Thanks for your comments.
floor register in unconditioned crawl space?
Martin - in the instructions above for "Creating an Unvented Crawl Space" one of the steps listed is "Install a floor register in the floor above to allow air to flow between the living area and the sealed crawl space below." Can you please clarify why you need air flow between the living space and crawl space, if the crawl space is supposed to be 1) unvented, 2) unconditioned, and 3) the walls are insulated with rigid foam and there is a poly vapor barrier?? Thanks!
Unvented crawl space over sold
First let me say, if constructed as outlined here, an unvented crawl space works, however, I believe they are over sold. Do they work, yes, do they require very specific attention to detail that is common to the construction trades today, not even close.
My parents live in update NY with part of the house with a full basement and another on a vented crawl space, which has slab below with uninsulated cmu walls. The crawl space is insulated with 10-12" of fiberglass batts on the underside of the floor and has two vents. This crawl space was built in the early 70s and never, I repeat, never have there been any moisture problems. Yes, the slab likely retards the moisture flow from the ground to the space, but this house was not built to any Fine Homebuilding standard.
I now live in Houston (i.e. hot and humid) on a raised floor house on "drilled" piers, which as noted here has other some advantages and is commong practice in "expansive" soils. This is obvisouly not common practice in the Northeast. I have 4" of spray foam on the underside, no slab below, with perimeter lattice all the way around the house so there is plenty of air movement. Periodically I inspect the crawl space particularly during the summer and have no issues, in fact, it is actually pleasant (as much as that is possible) during the hot/humid summers.
Obviously different regions require different solutions, but I believe the amount effort to truely seal a crawl space and maintain it (I have to run an exhaust fan, come on) in most situations (except for extremely cold climate, ducts in the space) is over sold. For my money, build the perimeter however you want (cmu, cast-in-place, etc), provide adequate venting (i.e. exceed code) and use closed-cell spray foam on the underside, call it a day.
As far as termites are concerned, remember they need a food source + water, remove one and no termites. What typically is installed down here is a terminte shield which is essentially a sheet metal cap which contrary to most people's understanding, is not a barrier but an obstacle that they have to build around. Since they have to build around it, their "tunnels" would be visible from a periodic inspection of the foundation.
Response to Erica Downs
Erica,
Q. "Can you please clarify why you need air flow between the living space and crawl space?"
A. As stated in the article, the requirement for a floor grille to provide air flow between the living space above and the crawl space below is a code requirement found in the 2006 IRC, section R408.3. If you choose Option 1, and install an exhaust fan in the crawl space, the grille is the source of conditioned makeup air from the crawl space. If you choose Option 2, and install a supply register in the crawl space, the grille allows the air in the slightly pressurized crawl space to flow to the house above, at a slow rate, thereby mixing the crawl space air with the home's conditioned air.
Some builders have had good success with sealed crawl spaces that lack an exhaust fan, a supply register, or a grille connecting the crawl with the living space above. Omitting conditioning sometimes works and sometimes doesn't. In all cases, however, it would be a violation of the 2006 IRC.
Good Crawl Space Articles
For anyone interested in more information on building sealed crawl spaces, my usual go-to articles for explaining the process come from The Journal of Light Construction:
Building a Sealed Crawlspace (Jeff Tooley, October 2003) for new construction
Fixing a Wet Crawlspace (Jeff Tooley, August 2004) for retrofits
Yes, they're JLC articles, not Taunton. Shh! ;)
Tooley had a good point on having a "sacrificial" layer of polyethylene during construction, to account for tears and debris from construction, and some advice on drying framing before sealing it all up.
Also, if you are ever working with contractors who are new to unvented/sealed crawl spaces, be sure they have some of the basic information in hand. I once dealt with a contractor where the plans were "thrown over the fence" to him. He built a polythylene ground cover (read: a plastic "bathtub") inside the foundation before the building was dried in (read: a plastic bathtub open to the sky). He was later surprised and angry when he built an OSB box 3 feet above pools of standing water (read: his first floor framing) and got mold on it. Yes, to me, this was an [eyeroll]--"You did **what?!**" situation. But if folks are used to building things one way, they might not visual the consequences of changing their procedures.
Response to Kohta Ueno
Kohta,
Thanks for recommending the two JLC articles. I agree with you -- these are great articles -- and I'm happy to second your recommendation. For anyone who wants to read them, here are the links:
Building a Sealed Crawlspace.
Fixing a Wet Crawlspace.
I have no problem recommending articles from the Journal of LIght Construction. It's a great magazine -- I worked there for years.
In case readers missed it, more links to useful articles and Web sites can be found in the sidebar near the top of this page. The sidebar is titled "More information"; it appears near the article's 4th paragraph.
conditioned crawl space
Here in Michigan crawl spaces are normal, our approach is sealed-conditioned. Usually a single heat run 6" is normal. Sometimes a vented door to existing basement space. We have trained the local inspectors to accept this, as they still think in terms of outside vents of old. We only use ICF's for foundation walls, so insulation is complete to below grade. Sealed vapor barrier, sometimes radon vents, as needed by testing. Add a SIP floor above and you have a bone dry and warm crawl space.
Getting around the code issues with sealed crawl spaces
For many years before the building codes recognized closed crawl spaces, we were constructing them as "basements with no habitable space". There is still no code requiring a basement to be heated, or to be provided with ventilation from the living space above.
With the installation of an exhaust fan, and no deliberate opening to the living space, radon issues would be negated, because the crawl space would be in negative pressure. The living space above should be fitted with a balanced air handling system, creating a slight positive pressure, especially if there is an attached garage. The garage should also be in constant negative pressure. House positive, garage and crawl space negative. Simple.
Response to Chris Harris
Chris,
I would monitor the conditions in the crawl space during the summer to see if any signs of dampness develop. If necessary, you can install a small stand-alone dehumidifier at a cost of about $300. I would adjust the controls so that the dehumidifier runs as little as possible -- just enough to control the moisture.
Sealed crawl space w/out air conditioning
I work on Cape Cod, which is very humid almost the entire year. We also build a lot of houses (fewer today than five years ago) without central air conditioning.
I am a proponent of sealed crawlspaces, but how do you handle the situation when you cannot deliver "conditioned" air to the crawlspace during non-heating periods?
Response to Martin Holladay
Thanks Martin,
So you would still be of the opinion to go w/ a sealed crawlspace, provide ventilation as described by code and the article and then use a standalone unit to handle excess moisture during warmer months?
Second response to Chris
Chris,
The building code tells you how the house must be built; however, the building code doesn't tell you how to operate the house.
The IRC lists two options for conditioning a crawl space, which I called Option 1 and Option 2. In your case, I would go with Option 2: "Option 2 requires that the crawl space have a forced-air register delivering 1 cfm for each 50 square feet of crawl space area."
The code does not require a house to have air conditioning. Just because there is a register in your crawl space, doesn't mean that it will be operating in the summer. The dehumidifier is an optional way to keep the crawl space dry if observations or measurements show it to be necessary.
Of course, you should check with your local building official before assuming that my recommendations make sense.
I guess my assumption is that
I guess my assumption is that if you are creating a "conditioned" crawlspace, the time of primary benefit of being conditioned is during the most humid months, presumably when you would typically be running an air conditioner (in most parts of the country for at least some amount of time).
I was just was wondering if you would still realize the full benefits of a sealed crawlspace if there was never a chance of introducing truly conditioned air during those most humid months. Or if you are just trading one way of adding humid air to the space for another (i.e. if all of the windows are open from June to Oct., you are introducing outside air to the crawlspace regardless of "sealed" or "unsealed".
I understand there certainly are other benefits of moving the thermal envelope to the building envelope rather than floor plane, better overall air sealing, etc. but was just curious when air conditioning is not a factor. It sounds like you would recommend a sealed space in this case and I guess I have talked myself into it as well.
Thanks for your help.
ThermoCon insulation in a crawl space?
Is ThermoCon a suitable material for insulating the inside walls of an unvented crawl space?
We are building a house around a previously unheated cabin that sits above a fairly shallow crawl space. Moisture has not been a problem in the 20+ years we've owned the cabin, but now we will be heating not just the old cabin but the crawl space as well. The crawl space walls have a rough surface of rock and mortar, and the floor is dirt (with occasional tree stumps and boulders).
Working room is tight in places, and a sprayed insulation would be much easier to apply than building a Thermax layer over the walls and into the rim joists.
Because I don't want to use a sprayed polyurethane, an insulation contractor has suggested ThermoCon instead. The ThermoCon website does not mention crawl spaces as a recommended use for ThermoCon, but overall the website is not that informative either.
Response to Dennis Cornhill
Dennis,
Your question is best directed at a technical representative from ThermoCon. Their telephone number in Houston is 800-979-4914.
A few comments to update
The IRC has always called them "Closed" crawl spaces, and I consider it to be the better and more accurate term. A "Sealed" space would be as tight as a balloon - neither possible nor desirable. Here in NC the 2009 IRC the Closed Crawl Spaces section is R409. R409.5 has five options for Space Moisture Control: 1. Dehumidifier, 2.Supply Air, 3. House Air, 4. Exhaust Fans, 5. Conditioned Space.
I've been functioning as a consultant re existing crawl spaces for a number of years and my approach for most spaces is to use a 6-mil plastic vapor retarder. It has all the perm you need. If there is equipment in the space I install a four foot wide piece of 16 mil from the crawl space door to the equipment and along the front of it. If there is already insulation in the floor structure I touch it up as necessary. If not, I install interior foundation insulation - I like R-10 rock wool panels - leaving the required three inch termite inspection gap. (I'm also a certified termite inspector, and 3" is much more than necessary, but I do the 3" for liability reasons.) If the Wood Moisture Content of the floor structure is less than 12% at the time of installation, that's it. If the WMC is 12% or above, to dry out the space I install a $200 dehumidifier gravity drained to the exterior or to a condensate pump. In either case I provide the client with a Temperature- Relative Humidity monitoring system with a master in the house and up to three remotes in the crawl space (less that $50). I tell my clients to keep an eye on the master monitor and if the Rh in the crawlspace exceeds 65% with any regularity I follow up by either installing a de-hu if there isn't one, or if there is I go back and find out what went wrong. 90% of the time, once the space is dried out no further action is necessary. Monthly calls to new clients and my annual inspections for the first several years. reassure the clients and keep things under control. That's it. Relatively simple and modest in price - and it works.
I haven't addressed the matter of water control or drainage - critical factors to be properly controlled to be successful. Martin did that very well in his original article. However, if at all possible, I want a gravity drain from the space. Around here the time when you may need the drain the most may be when you don't have any electricity, and battery back-ups for the sump pump have a limited charge.
A couple of asides. First, I trained with Jeff Tooley (son of the esteemed John Tooley - Building Scientist extraordinaire) for a week 11 years ago, and he really knows this topic well from a lot of hands-on experience. Read his previously mentioned articles. Second, in the 1968 NC Building Code in the back of the book there are several drawings that show how to properly do a closed insulated crawlspace! Who knew? Must have really messed with the 99.9% of the builders that were so sure that all crawlspaces had to be ventilated, and the more the better!
I will finish with this; You MUST recognize that except for doing your best to keep the water away from the crawlspace to begin with, there are no absolutes in the closing of a crawlspace. Every one is different particularly with regard to their geographic location. With a bow to Marcus Pollio: That crawlspace that would be fine in Albany, Georgia, would not be appropriate for Albany, New York, nor for Albany, California.
ThermoCon insulation in a crawl space?
I spoke to several people about the use of ThermoCon in a crawl space and got a range of opinions from "certainly" to "doubtful."
So in the end because we were not sure that ThermoCon would last for the long term in a crawl space, we insulated the rim joists and the foundation walls with 2" of XPS covered by 1.5" of Thermax instead. It was a tedious job working in a confined space, but the result looks good and will hopefully be an effective insulator for the long term.
cost effectiveness of insulating crawlspace walls
I am amazed to read, in the cited North Carolina study, that insulating the crawlspace walls provides only an additional 3% of energy savings (18% versus 15%) over encapsulating/sealing the crawlspace but using fiberglass insulation in the floor joists. I am convinced that I should encapsulate my existing crawlspace, but I'm not sure if it's worth the added expense to insulate the walls (for my 1700 sq-ft house, the cost is $3900 versus $1850). Probably not worth it for the 3%. But it's hard to believe that moving the HVAC ductwork into the conditioned envelope would not yield far greater savings. Even ignoring the ductwork effect, the square footage of the crawlspace walls is about half that of the floor.
Response to John Eyles
John,
There are many benefits to sealing a crawl space other than energy savings. However, if you are chiefly motivated by energy savings, then you are right to hesitate. Anyone who expects a huge saving from sealing a crawl space and insulating the crawl space walls is likely to be disappointed.
Not mainly energy savings
Martin, thanks. I have expressed myself poorly. I am chiefly motivated by the moisture issue. I intend to encapsulate the crawlspace, no matter what. But as long as I'm having the work done, I'm tempted to go ahead and insulate the block walls also. I don't think it makes much difference whether I do that, or just leave the floor batts, as far as moisture control. So it becomes a question of whether the potential energy savings is worth the approx $2K added cost to insulate the walls with 1.5" Thermax. If the savings is only another 3%, probably not; but as I say, that figure seems to conservative to me. I suppose a big part of the calculation is how you factor in the floor of the crawlspace (which would be unfeasible for me to insulate at this point). I'm thinking it helps in the summer (since the dirt is pretty cool) but hurts some in the winter - but I'm heating with free and plentiful wood then anyhow.
Wet crawl space on unheated cabin
Martin,
I was just linked to this discussion and find it very helpful - thanks, I just wish I had seen this 20 years ago.
I have a "rework" project facing me. Years ago I designed and built a cabin in Northern MN, and put it on a crawl space, (it would have been pillers). I built it in the (I believe) prevaling fashion back then; footing at 48+ inches, 7 course block wall, backfill wall, poly on fill, passive vents in wall, and glass in floor joists.
Turns out it is a good way to grow mold.
So, my plan is to dig it out, vaper barrier and rat slab, insolate the inside of the block walls, seal, maybe add active vent out, passive makeup air.
But the cabin is unheated most of the time,
any thoughts or red flags for this plan?
Dan
Response to Dan Lindberg
Dan,
I think your plan is fine. Just use common sense: monitor conditions in the crawl space to be sure it isn't too humid. As long as it stays dry, you don't have to worry.
If it seems damp, you have to start analyzing where the moisture is coming from to figure out how to address the issue. But since that hasn't happened yet, I wouldn't worry yet.
Cabin con't
Well, there is plenty of mold growing now, and I suspect that the mosture is/was coming in through the vents, as the fill is/has been very dry anytime I've gone down there.
But, my question is should I remove the insolation in the floor joints, and/or do I insolate the rat slab? The concern is freezing of the foundation during winter when it is unheated.
Dan
the article said:
Install a
the article said:
Install a durable vapor barrier — for example, a 20-mil pool liner or Tu-Tuf poly — over the floor and extending up the crawl space walls, to within 3 inches of the top of the wall. Leave a 3-inch-wide termite inspection strip at the top of the wall.
i thought never ever put poly on basement/crawlspace walls..?
Response to Dan Lindberg
Dan,
Q. "Should I remove the insulation in the floor joints?"
A. Yes. If you have fiberglass batts between your floor joists, and if your crawl space shows signs of mold, you should remove the batts and throw them away (assuming, of course, that you are sealing the crawl space vents and insulating the crawl space walls).
Q. "Do I insulate the rat slab?"
A. The payback for rat-slab insulation is going to take much longer than for the wall insulation. Most crawl space retrofits don't include insulation under the rat slab.
[Editor's note: Comments continue on Page 2. Click the "page 2" tab to read more comments.]
Response to Erik Olofsson
Erik,
Q. "I thought never ever put poly on basement/crawlspace walls..?"
A. Good catch! It would be more accurate to say: "Never install polyethylene on a basement or crawl space wall in conjunction with fiberglass batts. Especially, never install polyethylene on the interior side of a stud wall built on the interior side of your concrete or masonry basement or crawl space wall."
Thermax for Unvented Crawl Space
From
From Dow: Installation Procedures for Thermax or Styrofoam brand Rigid Insulation - Closed Crawl Space
(For closed crawl spaces)
Response to Brian Higgins
Brian,
Thanks for the link.
Ok I would like to update pictures of my conditioned crawl space
Years ago I added pictures to this very article, I have certainly improved with time..
I would like to share some newer photos, this recipe has been very successful for me and I do an extremely large number of crawl spaces every year in conjunction to other HP measures....
I can only use low rez pix due to size limitations so I can only show so much...
Please only do the floors of the living space when near a body of water or extremely high water tables!!!
Questions on Unventing My Crawl Space
Hi Martin -
I realize that the above posts are old, but I have a few questions that are related to the post and would greatly appreciate any insight you can give.
I live in Wilmington, Delaware, and have a crawl space (approximately 8' x 8') that has a concrete floor that is above grade. As far as I can tell, there has never been any moisture problems in the crawlspace (I purchased the house about 3 years ago and I don’t know if the previous owners ever had any problems, but the fiberglass insulation is still in good shape, it doesn’t smell musty, and I have been in it on multiple occasions and it has always been dry).
There are two vents to the outside that I would like to close. I would also like to insulate the block walls with rigid insulation. I'm looking at the Thermax insulation mentioned by Brian above. The installation manual that Brian provided a link for says to install a 6 mil poly liner on the walls between the blocks and the insulation and on the ground. However, the installation manual (and most of what I have read about unventing a crawl space elsewhere) assumes a crawl space with a dirt floor. Is it any different for a crawl space with a concrete floor that is above grade (I don't know if there is a vapor barrier underneath the concrete floor)? Should I put down a vapor barrier over the concrete floor? What about between the walls and the insulation?
The crawlspace opening is approximately 3' x 2' and is located in my heated basement (the crawlspace is an addition). If I leave the crawlspace opening open, is there still a need to vent to the room above?
I have tubing for radiant heat that runs in between the joists in the crawl space, along with aluminum heat transfer plates, a reflective barrier, and fiberglass insulation. Most of what I have read on conditioning a crawl space says to remove fiberglass insulation in between the joists. Given that the crawl space opening is located in the basement and I would leave that open, can I leave the fiberglass insulation between the joists?
Thanks in advance for any help.
Response to Paul Loughman
Paul,
Q. "Should I put down a vapor barrier over the concrete floor? What about between the walls and the insulation?"
A. If you don't currently have a moisture problem in your crawl space, there is no need to install polyethylene on top of the concrete. It can also be omitted from the walls. (The rigid foam that you plan to install is already a vapor barrier, so poly on the walls would be redundant.)
Q. "If I leave the crawlspace opening open, is there still a need to vent to the room above?"
A. No.
Q. "Can I leave the fiberglass insulation between the joists?"
A. Not only can you -- you should. The fiberglass batts are an important component of your radiant floor heating system, so the batts should not be removed.
Thanks Martin!
Thanks for the quick response. Very helpful.
crawl space
I recently bought a cabin in north Georgia on a hillside. It was built with foam covered blocks filled with concrete right up to the roof trusses. Part of the basement has a concrete floor but the part under the road side of the house has a dirt floor. As it is built on the hillside, the basement part is very high and there is a load bearing wall also constructed with the foam blocks filled with concrete between it and the dirt floor crawlspace section. There is no vapor barrier on the dirt. No insulation under the floors in either section. The home inspector recommended adding 6 mil plastic on the dirt floor. The walls throughout of course are lined with foam. There doesn't appear to be any moisture problems. The space is unvented to the outside. The wood floor above the crawlspace (mere inches at one end and fifteen feet at the other) doesn't seem to be suffering from moisture either (no warping). It has been this way since 1999 with no apparent ill effects. As I said the home is built on a steep hillside so gravity takes care of most water I'd think. I was planning on spraying foam up under the wood subfloor in the dirt floor section but now not sure what to do based on what I'm reading here. Termites are another concern as the builder put rock siding over the foam to below grade all around. No way to look for tunnels. I was planning to treat for termites as a precaution. Any advice appreciated.
Response to Dwayne Keith
Dwayne,
It sounds as if your home has ICF walls. (ICF stands for "insulated concrete forms.")
As I explained in my article -- you did read the article, right? -- and as your home inspector wisely advised, you should install 6-mil polyethylene over the dirt floor. My article give more details on how the polyethylene should be installed.
If your crawlspace is sealed (unvented), there is no reason to install spray foam insulation on the crawl space ceiling (between the floor joists above).
crawl space
Thanks your reply. I did read it but with the ICF construction I wasn't sure how that changes things for me. Not sure how I would adequately attach plastic up the sides of the walls to the foam. Might have to use boards anchored into the concrete behind the foam which would be lots of fun. I think I'll try taping directly to the foam first and see if it holds. The ground in that space slopes so severely, just putting down the plastic will be a real treat. Thanks again.
SF Bay Area
Oh man, I recognize every one of these crawlspaces. I live in the San Francisco Bay Area and nearly every house I've ever inspected has a ventilated crawlspace. Should I seal my crawlspace here too?
Response to J. Bu
J. Bu,
Every house needs a good air barrier and a good thermal barrier. In San Francisco, the climate is dry enough (and mild enough) that a ventilated crawl space can work. So can a sealed, unventilated crawl space.
If you want to keep your ventilated crawl space, you need to verify that you have a good insulation layer on the crawl space ceiling, and that the crawl space ceiling is well sealed (without any air leaks).
questions for Martin - sub-rat slab insulation & termite barrier
In reading the Pretty Good House blog entries, I see R10 insulation recommended for sub-slab insulation, but I noticed in comment #50 that you say the payback for insulating under a rat slab is much longer than for wall insulation. Is there a fundamental difference in the thermal effect of insulating under a slab-on-grade floor vs. insulating under a rat slab in a conditioned crawl space?
For new construction in climate zone 4, do you think R-10 insulation under a rat slab is overkill if the above ground portion of the house is insulated to R-25? I know intuition is often wrong, but it's hard to think of paying so much attention to insulating the rest of the house and then omitting it on the bottom side.
Also, I'd like to avoid the 3" termite inspection window thermal bridge at the top of the block crawl space wall. If a metal termite barrier extended past the inside edge of the rigid foam that insulates the inside of the crawl space wall, wouldn't that create a situation where the termites would have to crawl around the barrier, thus being visible?
Response to Timothy Godshall
Timothy,
My guess is that if you used energy modeling software to determine how much energy savings you would get in Climate Zone 4 by installing R-10 insulation under the rat slab in your crawl space, you would get a very long payback period indeed. (In other words, the annual savings would be low.) However, I don't want to discourage your from doing the modeling. Go right ahead and do it.
Many people include energy measures at the time of new construction even when the energy measures aren't very cost-effective. If you can afford the insulation, and you want to install it, by all means install it.
The reason that it makes more sense to insulate above-grade walls than a crawl space rat slab is that the soil under the slab is warmer in winter than the outdoor air.
Concerning your question about the termite inspection strip ("I'd like to avoid the 3-inch termite inspection window thermal bridge at the top of the block crawl space wall"), I'm not an expert in termite details -- and in any case my opinion would be irrelevant. The only opinion that matters is the opinion of your local building inspector. So ask your inspector.
response to Martin
Thanks, Martin, for your response. I'm still not clear on one point: Wouldn't you lose about the same amount of heat through a rat slab in a conditioned crawl space as you would through a slab-on-grade floor? If so, why is it recommended to put foam under a slab-on-grade, but not cost-effective for a rat slab?
Response to Timothy Godshall
Timothy,
Q. "Wouldn't you lose about the same amount of heat through a rat slab in a conditioned crawl space as you would through a slab-on-grade floor?"
A. No. In winter, the temperature of the soil is coldest near the surface, and is warmer at lower levels. Basement slabs are often 7 feet below grade; at that level, the soil can be relatively warm, which is why most Climate Zone 4 builders don't bother to install horizontal rigid foam under basement slabs.
A slab-on-grade foundation is actually above grade, not on grade -- because the grade at the perimeter of the foundation has to slope away from the house. At this level, soil temperatures are colder than they are 7 feet below grade, so insulation makes more sense.
That said, most Climate Zone 4 builders only install vertical insulation at the perimeter of a slab on grade, and skip the horizontal insulation under the slab.
A rat slab on a crawl space floor is usually (but not always) below grade, so in winter it encounters soil temperatures that are warmer than a slab on grade, but not as warm as a basement slab that is 7 feet below grade.
Don't insulate the crawlspace ceiling! No don't do it!
No, no no! Don't insulate the crawlspace ceiling! That's a mistake. You are much better off to insulate and seal the crawl space skirting (walls) and then seal the dirt floor with poly (plastic sheeting), to keep dirt and moisture out of the crawl space, then lay foil faced bubble pack on top of the ground, to stop radiant heat loss and also to slow moisture transferral. Then, you can run a dehumidiifer in the crawl space for a week or so, and voila, no more ground moisture entering the house and you've turned the entire airspace of the crawl space into a still air insulation with radiant barrier. This keeps the floor joists of the house dry, and also all the water pipes and drains in the crawl space are nicely kept warm. I have an article about how we encapsulated our crawl space at http://www.jennyruthyasi.com and it's working great.
Insulating Crawl Space
I have a question regarding insulating my unvented crawl space. My house sits on a partial basement and partial crawl space. The basement portion is finished and sealed/insulated from the crawl space; however the living/dining rooms above the crawl are uninsulated and the floor tends to get pretty cold in the winter months. The crawl space has a vapor barrier down on the floor and up the foundation walls and is actually quite dry, surprisingly (I live in the Portland, Oregon). I would like to insultate with R-30 between the joists, but am unsure if I should use faced or unfaced insulation rolls. The likelihood of moisture transfer from the house into the crawl space seems unlikely, which would make using unfaced insulation fine, but I would like to get some other opinions on the matter. Any other useful things to think about are much appreciated.
Thanks!!
How easy to get to your crawl space?
Ryan,
It is far easier to insulate the perimeter than between the floor joists. The area is smaller and you can do a better job. Laying on your back trying to keep the insulation between the joists and out of your eyes is a serious pain and won't last as well as insulating the walls of the crawlspace.
Response to Ryan Suarez
Ryan,
Lucy gave you good advice. The best place to install insulation in an unvented crawl space is on the interior side of the crawl space walls.
If the floor above the crawl space is cold, don't neglect the possibility that you may have air leaks. Air sealing can make a huge difference in comfort. The usual problem areas are between the top of your foundation wall and your subfloor.
Finally, if you can't be dissuaded from installing insulation between your floor joists, you should read this article before you do the work: How to Insulate a Cold Floor.
New York City crawl space
Hi and thank you for your article!
I would really appreciate some help on insulating my crawl space. I just want to be 100% sure before I proceed and blow all the money :-)
My house is on a slope, lower than the street. The crawl space is in the front of the house, next to the street, at the lowest angle of the slope. The previous owner finsihed the entire asement just with drywall over the foundation (cinder blocks) and as far as I can tell there is no musty smell or great humidity level. I am thinking of insulating the crawl space wall as it doesn't have any insulation/drywall. There is no venting, it is basically a storage space with doors that i can periodically keep open to circulate air in.The ceiling of the crawl space is my living room floor (hardwood). There are fiberglass batts in the ceilinf of the crawl space and drywall.The floor of the crawl space is already done, it is raised at waist height with what appears to be a concrete slab on top. I have no idea what is underneath that.
I am a newbie diy: can i keep the fiberglass in the ceiling? Also, can i use something else other than sprayed foam for the cinderblocks in the foundation before i installing the drywall?
Thank you in advance for your help!
Response to Tenci
Tenci,
Q. "Can i keep the fiberglass in the ceiling?"
A. You can if you want. If it is moldy or deteriorating, however, I would remove it and dispose of it.
Q. "Can I use something else other than sprayed foam for the cinderblocks in the foundation before installing the drywall?"
A. If the walls are smooth, you can insulate them with rigid foam. Crawl space walls are insulated the same way as basement walls. Here is a link to an article with more information on insulating crawl space walls and basement walls: How to Insulate a Basement Wall
Thank you Martin!
Thank you Martin!
heated crawl space
Any thoughts on putting some baseboard radiators in an unvented crawlspace and keeping it warm enough down there to keep the first floor toasty?
Response to Bob Butera
Bob,
Here in Vermont, some people heat their crawl spaces to keep their pipes from freezing. But this approach is only necessary if your crawl space is grossly defective -- riddled with air leaks. If you do a normal job of air sealing, your crawl space won't freeze. So the answer is, you don't need heat in a crawl space.
If you want to "keep the first floor toasty," then you should install your baseboard radiators on your first floor. If you install them in your crawl space, a lot of the heat is wasted -- the heaters warm the dirt on your crawl space floor, and much of the heat escapes to the outdoors through your crawl space walls. That is wasteful (and expensive).
To vent or not in SW CO
Hello,
I have been researching this topic and reading all the various articles from GBA, BuildingScience, ORNL etc. and still feel either will work well in my scenario and climate.
A crawl space is 50% the cost of a foundation, so that topic is decided for a remote cabin.
Here's the question, for a zone 6, high rockies cabin we are planning to have radiant floor heat + wood stove. The radiant floor will be a closed glycol based system which allows us to leave it on while not using the cabin, it's 5 hrs from home and nothing worse than a frozen cabin on a friday night in January.
I like the idea of closed but only see budget and value in having a fan exhausting to the exterior with a grill on first floor to meet code, 2006 IRC for us. I entertained HRV's but seems overkill, maybe when it's a full time deal.
Then insulate interior foundation walls to R13, 20 mil poly and then a radiant barrier under the joist to keep the floor heating heading north.
Otherwise vented and move insulation between joist but keep the poly in place and well sealed to walls.
Given our climate, high rockies and dry but a fun mud season. It seems vented work equally well in the dry, arid west.
Thoughts?
Thanks,
Todd
Response to Todd Day
Todd,
You wrote, "A crawl space is 50% the cost of a foundation." But a crawl space is a foundation. Perhaps you meant that a crawl space is 50% of the cost of a basement?
Your proposal to insulate the crawl space walls to R-13 in your climate zone won't meet minimum code requirements. According to the 2012 IRC, you need a minimum of R-15 insulation (if you use a continuous layer of rigid foam, as you should) or R-19 insulation (if you use fluffy insulation between studs, which would be a stupid idea even if it is code-legal).
Your proposal to install just a radiant barrier under the floor assembly that includes PEX tubing for a radiant floor heating system is insufficient. If you have this type of under-floor heating system, you need real insulation, not just a radiant barrier, between your joists. (In addition, you need to insulate your crawl space walls, in my opinion, because vented crawl spaces don't make any sense.)
One of the main reasons that you don't want a vented crawl space for your cabin in the Rocky Mountains is that you don't want your plumbing pipes to freeze. If you leave open vents during the winter, you can arrive to find your pipes frozen. Seal up your crawl space -- you won't regret it.
Response to Martin Holladay
Thanks Martin. You're correct, I meant basement vs. crawl space. My county in CO is under 2006 IRC hence the R13. That said, I'm a firm believer in more is better in terms of insulation if done right.
I would only do rigid or spray on insulation in the crawl space, too many issues as you noted.
Your suggestion for continuous rigid insulation under the floor joist for the radiant system in terms of heat loss is what I was after in a closed crawl design.
It seemed off to insulate there and at the foundation stem wall, I haven't come across that detail but most exclude the notion of heating assembly as part of the equation.
It looks like the R19 can be continuous R15 lets say on the foundation wall interior and then R4 or better for the underfloor assembly per the IRC 2012.
I think we will be going for a closed crawl space with exhaust fan out crawl space and floor/wall vents to draw continuously from heated space. Maybe future consideration for an HRV but not on day 1.
My primary reason is for air quality and energy efficiency, the plumbing will be set up for draining and shut off while away. I don't want to take any chances something going bump with the radiant heat system.
Thanks for your input and the tremendous insight GBA provides.
Regards,
Todd
Unvented crawl space in NJ
Hi Martin. Fantastic article. I live in central NJ and have a vented crawl space connected to an unconditioned, unfinished basement and am considering sealing the 2 vents to create an unvented crawl space. The crawl space is not sealed from the basement, air can flow between the two areas via the rafters. The crawl space has an on grade concrete slab floor and I've never had any issues with moisture or water, it is bone dry. I do have a dehumidifier running in the basement. The humidity in the basement is currently 45% and in the crawl space it is 48%. If I seal the crawl space vents, would I need to run conditioned air into the crawl space considering the basement is unconditioned? Would the dehumidifier be enough?
Thank you,
Jim.
Response to Jim Mig
Jim,
Q. "If I seal the crawl space vents, would I need to run conditioned air into the crawl space considering the basement is unconditioned?"
A. No.
Q. "Would the dehumidifier be enough?"
A. Probably.
Crawl space - vapor barrier and Thermax
Another great article as I grapple with a poorly constructed addition in a house I just bought. Previous owners built addition with a dirt floor crawl space OVER the perimeter foundation drain for the main house. To solve the problem when they figured out there was too much moisture, they put in a sump pump to pump water out of the hole, installed vents (4" circles) at ever possible spot, put up fiberglass insulation on the ceiling, covered it with plastic, put plastic on the dirt (not taped), and hoped it would work. It didn't. Think lots of mice, wet fiberglass, and nasty smells. Oh, of course dry rot. If only I had read this article a few months ago I might have understood what I was buying....
Our plan is to not repeat their mistakes and to have it be an unvented crawl space. We've taken the following steps so far: 1) installed a new perimeter foundation drain for the entire house and addition that actually drains to daylight, (and imagine that - the drain pipe is actually located below the footing !); 2) put tuff n dri and warm n dri around the exposed foundation for water control and insulation; 3) closed off all the crawl space vents; 4) removed the insulation, plastic vapor barrier, and dry rot wood; 5) and installed new subfloor in the room above.
To insulate the crawl space, I purchased 2.5 inch Thermax (from Green Insulation Group in Worcester) and have been installing it on the interior walls of the crawl space about one inch down from the top of the foundation sill to about 2 inches off the floor. The sill joists will be sprayfoamed to seal the top of the thermax and complete the continuous vapor barrier and insulation. On the dirt surface, I plan to put 2" of XPS, taped at the joints, and have it extend under the Thermax. I figured the XPS would help the room a stay warmer a little and it was pretty cheap as it was reclaimed. I will have a floor register to allow air into the crawl space from the conditioned room above, with a continuous operated fan exhausting the crawl space to the outside.
I have a 20 mil plastic vapor barrier to install, and my question revolves around how to integrate it with the Thermax. Can I simply have it run up a few inches on the Thermax and tape it there or is there a need for it to be installed directly to the concrete foundation? I assume that the Thermax is serving as a vapor barrier - it is adhered to the concrete with construction adhesive and fastened with 1x4 strapping, and taped at all joints, and the bottom exposed edge nearest the dirt floor is taped as well, so moisture infiltration to the Thermax seems unlilkely.
Thanks for clarifying this aspect. Brian in southeastern NH
Response to Brian Hart
Brian,
Your use of brand names had be confused for a while, but I figured it out. (If any other GBA readers are confused, "Tuff-N-Dri" is a brand of dampproofing compound, and "Warm-N-Dri" is a brand of semi-rigid fiberglass insulation panels designed for insulating the exterior of foundation walls while allowing drainage.)
Ideally, the 20 mil plastic that you want to install on the dirt floor would have been installed before you installed the interior wall insulation. However, since it's too late to do it that way, I don't think you'll have any problems if you tape the 20-mil plastic to the Thermax with high quality tape.
What about a crawlspace with no crawlspace and no slab...
...and no joists? J chestnut mentioned a method of building "no-crawlspace" that still had joists. Martin said this wasn't possible because the joists would have to be inspected by a small person. But what about eliminating the slab altogether, as discussed in this JLC article: http://www.jlconline.com/how-to/foundations/a-basement-floor-without-concrete_o ???
I knw there are structural issues with this, but it may be worth exploring, as there seems to be much teeth gnashing about cold slabs, and much hand-wringing about damp moldy crawlspaces. Maybe wood floors are the answer? Anyone care to chime in on the structural implications of this method?
Dead link
The second link to the Home Energy article is dead, but the first one works.
Response to Michael Bluejay
Michael,
Thanks for letting us know. I have fixed the broken link.
If I run 10-15-20 mil poly
If I run 10-15-20 mil poly under the rat slab and run it 4-6" up the stem walls, then put taped (or otherwise sealed-to-the-poly) Thermax board on the walls, wouldn't the Thermax eliminate the need to run the poly vapor barrier the rest of the way up the wall? Idle question, I suppose; the additional poly is a minor expense, I just dislike the duplication of work.
Yes, I know code requires it so I should be asking my building official (and I will) but is there a good reason I'm missing?
Response to Rob Hunter
Rob,
Q. "Wouldn't the Thermax eliminate the need to run the poly vapor barrier the rest of the way up the wall?"
A. Yes. If you have interior rigid foam, you don't need to run the polyethylene all the way up the wall.
Martin, great article! Thanks for helping me understand the crawl space venting and code issues.
One other reason to do a crawl space vs. a basement is it requires half the resource to build. Half the raw materials, half the carbon, half the stress on the planet. Just a thought.
Cheers, Shawn
All,
It's wonderful how these older articles have such relevance. Would that I had known about GBA 8 years ago when we built a 3' x 12' x 20' crawlspace without a sump pump in the slab, much less a sloped floor. It was warm and dry when they cast the foundation and we didn't realize that a shallow swale led springtime meltwater and heavy rain right past the foundation (and into it at times)
We can't ignore things any longer:
1. Gutters are going in as much as I hate cleaning them
2. Regrade the settled soil outside
3. Sump pump is going to be cut into the slab
4. Underground electrical lines will be cut and sealed and moved above ground
5. Moisture barrier going in
6. Adding in-house fan and exterior vent per articles and comments
unclear about insulation, the slab appears uninsulated inside or out.
Scott,
Thanks for sharing your story. Do you have any questions?
I'm a builder of custom homes. When we do crawl spaces, we always treat them like basements and create conditioned space, insulated thermax walls, xps foam under slabs with concrete floors. Our hvac sub recommends (regardless if full bsmt, crawl, or otherwise, to leave the forced air furnace fan "on" all the time. He says it's better for the system and to have continuous air flow.
My question is, even if the furnace fan is always on, would it be optimal to install an open floor vent (maybe more than one) between crawl and main floor to promote more circulation? Seems it would be no different than a open stairway between floors. Moreover, if the home (such as a seasonal cottage) does not have A/C, the air exchange between floors with the open vent(s) would help remove humidity from the crawl. Thoughts?
So, all the information I've been finding online has been vague or confusing to me about a conditioned crawl space until I found your site but I still have some questions. I live in zone 4, north west Tennessee and my main concern is insulating the crawl space walls. They are cinder block and the bottom block will have that damp look after a decent rain and I may get a 1/4" amount of standing water in a few spots along the sides of the crawl space(2 -3 feet long by a foot wide) that soaks into the ground fairly quick, 1 -2 days after rain stops but the cinder block only dries out if there is no rain for several days. So my issue arrises when installing 2" XPS(pink stuff) on the walls and covering it with the vapor barrier(polyethylene 12mil) since the XPS needs to have a thermal barrier. Will I be trapping that moister between the cinder blocks and the XPS? I've tried to get the fire retarder foil faced Thermax, R-max thermasheath but I only need 10 sheets and the minimum they will sell is 25 sheets. I'm also planning on 2" XPS in rim bays along with using R-15 Roxul for added R-value and its thermal barrier qualities. Also I have read that a stand alone dehumidifier(aprilaire,santafe) qualifies as exhaust/conditioned air flow to meet codes conditions for #1 or #2. Thanks
Kevin,
There are several possible solutions to your problem. The best solution would be to provide drainage -- a perforated pipe (installed in a trench filled with crushed stone) near the damp wall. This perforated pipe can drain to daylight, if possible, or can drain to a sump equipped with a sump pump.
Alternatively, you could simply raise the floor of your crawl space by adding sand or crushed stone to the floor. This may not be too difficult -- especially if the maximum depth of standing water is only 1/4 inch.
If your concrete blocks are occasionally damp, that's no big deal. Water won't damage concrete blocks. You can cover damp concrete or damp concrete blocks with rigid foam without any fears.
I was thinking about the crushed stone idea. What about covering the XPS with the vapor barrier? I was also going to add a drain on the outside in the near future but it's not in the budget right now. I was also going to seal the outside of the block, above grade with a clear sealer. Thanks for the quick response
Kevin,
Q. "I was also going to add a drain on the outside in the near future but it's not in the budget right now."
A. The drain doesn't have to be on the exterior of the wall; it can be on the interior of the wall.
Q. "What about covering the XPS with the vapor barrier?"
A. Polyethylene on the wall is optional; all you really need on the wall is rigid foam or closed-cell spray foam. However, green builders avoid the use of XPS, which is manufactured with a blowing agent that has a high global warming potential. Either EPS or polyiso is preferable to XPS. For more information, see "Choosing Rigid Foam."
My question about the vapor barrier over the rigid board was to provide a thermal barrier to meet code let alone would that trap moisture between the board and concrete block. I can't leave rigid foam board exposed and I can't afford to have someone spray foam but that will also need a thermal barrier paint on it to meet code
Kevin,
A thermal barrier and a vapor barrier are not the same. When you wrote "vapor barrier," I assumed you were referring to a layer of polyethylene (plastic sheeting) -- the typical material used for a vapor barrier in a crawlspace.
Building codes require a thermal barrier to protect rigid foam or spray foam from fire -- and the typical material used for this purpose is 1/2-inch gypsum drywall. For more information on thermal barriers, see "Thermal Barriers and Ignition Barriers for Spray Foam."
Your local code official may or may not require a thermal barrier to cover rigid foam in your crawlspace; local interpretation of this code requirement varies widely. To learn about your local requirements, call your local building department.
So code calls for a thermal barrier over rigid foam board if crawl space is used for storage. I guess I'm not using the right words to explain the answer I'm looking for. I'm not going to build a 2x4 or 1x1 wall frame to attach gypsum in a 3' tall crawl space to cover the rigid foam board. I can avoid using it for storage if it will ease the install to meet code but I found out after purchasing a vapor barrier for the walls that they need to be insulated to meet code. I'm wondering if it is OK to cover the rigid foam board with the vapor barrier,( unless that will trap moisture) or should I just trash it and only install rigid foam board on the walls. I know some rigid foam board that is faced is considered a vapor retarder but I have no access to that product. Local stores have 1/2"-1" but they don't meet the R-10 required and I don't want to put two layers up unless that's my only option. I know your GREEN but I can only get XPS in the R-value required for code. Where does everyone get EPS then, I've tried but I have to buy 3 times what I need. There's a 1-1/2" polyiso by johns manville that's faced I can get but its only R-9.3. Sorry to sound angry but I've been searching for this answer for over a month now, seems like only contractors can get the supplies needed to do this job.
EPS is common but hard to find. But it's used commercially, so we buy EPS from a commercial roofing outlet. (Beacon Sales in our area; they also own ABC roofing and are a national company.) R value: R4/inch, less than half the cost of other foams, and lowest GWF of the foams.
Kevin,
Q. "So code calls for a thermal barrier over rigid foam board if crawl space is used for storage."
A. Yes, but you should check with your local code authority to see how the code is interpreted in your jurisdiction.
Q. "I'm not going to build a 2x4 or 1x1 wall frame to attach gypsum in a 3' tall crawl space to cover the rigid foam board."
A. If you decide to install drywall, you don't necessarily need 2x4s. You can either glue the drywall to the rigid foam, or you can attach the drywall mechanically to the concrete using long Tapcon fasteners through the foam.
Q. "I'm wondering if it is OK to cover the rigid foam board with the vapor barrier (unless that will trap moisture) or should I just trash it and only install rigid foam board on the walls?"
A. Most rigid foam is already a vapor retarder or a vapor barrier. If you purchased a polyethylene vapor barrier, you can install it over the rigid foam board if you want -- but installing it is optional.
Q. "I know you're GREEN but I can only get XPS in the R-value required for code. Where does everyone get EPS then? I've tried but I have to buy 3 times what I need."
A. The availability of EPS varies regionally. In some parts of the country, it's easy to buy. In other areas, it isn't necessarily as easy to find. If you tell us your location, a GBA reader might be able to suggest sources.
I'm in Clarksville Tennessee. It's nice to hear that the vapor barrier over the board is not an issue. I guess I was after my options. A- best, B-OK, C-will work. I see online post from other home builders showing vapor barrier on wall then rigid board on top of that, just rigid board and adding frame wall(or like you said directly to board) with gypsum or vapor barrier over the foam board. If it's added protection I want to use the vapor barrier and if I put it on the walls first I can take my time installing the rigid foam board over the vapor barrier. I have checked the code and it requires a thermal barrier but I will ask the inspector over the phone how they interpret it. I guess I can always add it later if I decide I really need the crawl space for storage
Kevin,
You might want to contact Drew Foam, a manufacturer of EPS. Here is the contact info:
Drew Foam of Tennessee
3050 Barry Drive
Portland, TN 37148
(800) 643-1206
Although the company many not sell EPS to you directly, they may be able to identify a local distributor of their EPS products.
I am looking at buying a house in Yellowknife, Northwest Territories, Canada, imminently. It was built in the mid 70s, but had Larsen trusses and an impressive amount of insulation added to the exterior of the original building at a later time. The walls are about 18 inches thick. Pretty cool!
Unfortunately, it has a damp and air leaky crawl space below it. I could smell the mustiness upon entry. The current owners had the wood stove running and the upstairs windows open, and there was a clear draw of air coming up through the vent registers from the crawl space. The downstairs floor also felt very cold. The floor joists are insulated with fiberglass, which doesn't appear to be moldy...yet. The crawl space foundation walls are insulated with 2 inch foam board on the concrete in some places, but there are gaps. It is a dirt floor with no vapour barrier. The forced air furnace ducting runs through the crawl space, but there are no heating vent registers in the crawl space. There are no vents to the outside of the foundation walls in the crawl space.
Should I buy this house, my plan is to insulate the uninsulated areas of the foundation walls. Then fill in the seams and maybe insulate the rim joists with closed cell spray foam. I will vapour barrier seal the floor. I was thinking about going with both option #1 and option #2, which you mention here. Installing an exhaust fan, but also adding more direct heat down there with some vent registers (there aren't any currently). My reasoning is to get as much air flow as possible through there, by creating a mostly negative pressure environment from the exhaust fan, but also adding additional heat to warm the floors. Is there any reason why I couldn't do both at the same time?
With the fixes which I am proposing (option #1 and 2 in combination), the crawl space would be fluctuating between positive and negative air pressure. Could the negative air pressure from the exhaust fan alone be enough to warm the floors, without the additional vent registers? My goals are to warm the floors, get rid of that awful crawl space air, and reduce any risk of pipes freezing.
Seth,
Q. "Could the negative air pressure from the exhaust fan alone be enough to warm the floors, without the additional vent registers?"
A. Yes. However, I'm not sure what you mean by "warm the floors." The main purposes of the exhaust fan are (a) to encourage a little air movement that helps address high humidity, and (b) to keep the air temperature in the crawl space above freezing.
If you have an exhaust fan, properly sized, and one or two openings in the floor to allow makeup air to enter the crawl space from the house above, everything will work. Remember, though, that in Yellowknife you will need impeccable air sealing everywhere for your house to perform well. Every part of your home's thermal envelope needs air sealing attention. Frozen pipes can happen, and when they do, the reason is always air leakage.
Thanks for your reply Martin. By "warm the floors", I mean make them feel warmer to the touch than they seem to feel otherwise. I may not be able to control air sealing everywhere, but I think that I can address the leakiest place, which seems to clearly be the crawl space, where the rim joists meet the concrete foundation walls.
Would you consider it unwise to go with option #2 at the same time? I suppose that I could go with option #1 first and assess the results.
if you live in an area without termite risks, any reason not to run the vapor barrier all the way up under the sill plate and use that to secure it to the stem wall instead of installing a separate batten 3" below it?
Carson,
There are lots of opinions on this issue. When I wrote this article, including polyethylene on this type of retrofit insulation job was standard practice. But if you're installing rigid foam or closed-cell spray foam on the interior side of your crawl space wall, it's possible to omit the polyethylene. The rigid foam or closed-cell spray foam is an adequate vapor retarder.
For most homes, there wouldn't be a problem if you ran polyethylene all the way up to the mudsill. The only exception would be an older home without any capillary break between the foundation and the mudsill -- in which case an argument could be made for leaving the mudsill exposed to the air to allow a little bit of inward drying. This is a complicated issue, however, and I wouldn't overthink it or worry too much no matter how you decide this question.
Martin, I was following the fhb article which shows the vapor barrier going up the stem wall. There was no vapor retarder applied between the footers and stem wall and the foam is also polyiso, not rated for ground contact, and I’ve read on here should be protected in this sort of application? I’ve found that the thick vapor barrier when installed has a lot of creases, and leaves a rather large gap between the foam and wall. I’m planning on foaming around them, but see gaps of nearly an inch in places. Is this a concern? Should I backtrack and tell them to remove the poly from the wall? How is the poly air sealed to the stem wall if not going up to the sill? Siga wigluv is expensive and likely would have to be special ordered.
an update for those with similar questions: According to Martin, following the poly up the wall as the original article is no longer recommended and to instead affix foam directly to the wall. The poly won't hurt anything if it's against the concrete, but can be fussy to install behind foam as outlined in my earlier comment.
I live in CT and have been in my house, built in the 60s, for over a decade. Consistent with what this article describe, we are seeing signs of mold growth on the insulation that is under the floor in the crawlspace. Our crawlspace has concrete ground floor and walls. I'm taking away from this article that closing up the vents is far better than to keep it vented. Different contractors recommended two options, both remove the old insulation:
1. Install rigid foam on the crawlspace walls instead of under flooring, close the vents. Add dehumidifier.
2. Replace insulation under flooring with new insulation, close the vents, and add dehumidifier.
Option 2 is a lot more affordable. Do you have any recommendation on which option is superior in moisture control and reduce summer heat from entering our home? if I go with Option 2, will it make the dehumidifier work harder? I don't need a "bentley" when a "corolla" will do, but also don't want to end up penny-wise and pound-foolish. Any advice would be appreciated.
By the way, although we don't have HVAC system, we've decided to move forward with a closed-cell spray foam project for our attic because we ran into a severe mold/moisture issue. We might've gone with a bently in this case... :)
Aimee,
Of the two options, Option #1 (installing insulation on your crawlspace walls) is preferred, especially in states east of the Rocky Mountains (like Connecticut). It's hard to predict whether a dehumidifier will work differently with the two different scenarios. In all cases, you need to address moisture entry issues and you need to perform air sealing work in your crawlspace if you want to reduce dehumidifier run-time (and if you want to solve your mold problem).
The fact that you have severe mold and moisture issues in your attic is concerning. My guess is that there are major air leaks in your home, including hidden air passages connecting your damp crawlspace with your damp attic. You need to get diagnostic work from a home performance contractor with a blower door--someone who understands air leakage issues and hidden air pathways in homes.
Thank you Martin. We do have an energy audit scheduled to do the diagnostic work. Since we have to do work in both our attic and crawlspace to control moisture, we're thinking of spacing the work out (span of 6-8 months) from a financials reason. Do you have recommendation on:
1. Sequence of work (crawlspace or attic first?). I'm leaning towards crawlspace due to the stack effect now that we're getting into the warmer weather.
2. If we started the work in the crawlspace (rigid foam and spray foam air gaps) , and waited 3-4 months before addressing the attic, how might this affect the attic? I'm thinking it would not accelerate the growth of mold in the attic.
Aimee,
Your plan to start with work in the crawlspace makes sense. Performing that work won't make the attic worse.
When the diagnostic work is being done, ask the specialists whether they can find any chases (for example, a plumbing chase, a chimney chase, or a duct chase) connecting the crawlspace to the attic. Any such chases need to be carefully air sealed to prevent air flow between these two spaces.
I’m in the process of repairing/upgrading the encapsulation of the crawlspace for my home in Winnipeg and have come up against a question I can’t find a solid answer to. I hope someone here can point me in the right direction. I want to replace the vapour barrier on the dirt/ground since its all torn up. That’s a given, and actually fairly straightforward. At the same time I want to insulate the walls and header of the crawlspace to improve the energy efficiency of the house and warm up the floor assembly a little. That’s where things get complicated.
See the attached photo for reference, but here's a description. I’ve got concrete foundation walls with a wood structured basement floor. The basement floor is made up of TJI I-joists supported by a ledger with I-joist blocking at the end of the joist bays. The ledger is bolted directly to the foundation wall without any spacers. There is about a foot of space between the ledger and the dirt floor. The original 6mil poly vapour barrier covers the ground and wraps up the walls, going between the ledger and the concrete. The poly continues up the side of the concrete foundation until it comes out between the basement subfloor and the basement wall framing.
Here’s my worry. If I insulate the ledger and blocking with rigid foam or spray foam (strongly leaning toward new HFO spray foam), am I trapping it between two vapour barriers? Is that a problem in this case? I know a double vapour barrier is bad when designing typical wall assemblies and is a situation best avoided. Does the same apply here?
I considered cutting slits in the existing VB behind the blocking in an attempt to eliminate the cold-side VB. But I think that will just make things worse since then the moisture from the soil on the other side of the concrete will migrate inward to the framing. Even though the framing won’t be touching the concrete, the foundation will always be damp from the exterior side, and the moisture will dampen the small airspace behind the blocking, and the blocking and ledger will absorb that moisture and rot.
I’m pretty certain I don’t want to insulate without creating a new VB on the warm side. If I just add rockwool on the inside of the VB, I’d for sure have condensation issues on the old VB since it would be up against the cold concrete.
So which way do I go? Do I keep the existing VB intact, or cut it? Am I damned either way and there is no safe method to insulate? Am I paranoid and I should just spray foam over the whole thing and move on to the next challenge? I’d really prefer to not be ripping it all out in 15 years to replace the ledger and sister the joists.
Al Windsor,
It isn't clear to me whether you are talking about new construction or an existing house. (If it's an existing house, how do you gain access to a one-foot-high crawl space under your wooden floor?)
I'm not familiar with the type of construction you're talking about -- what you describe as "a wood structured basement floor." But your description is clear enough. (You forgot to attach a photo, by the way.)
My own rule is never to create a crawl space that is too low for human access. A one-foot-high crawl space isn't recommended, since access for maintenance is impossible.
You wrote, "I’m pretty certain I don’t want to insulate without creating a new VB [vapor barrier?] on the warm side," and this sentence indicates a typically Canadian obsession with interior vapor barriers -- a simplistic approach. If your vapor retarder has R-value, as is the case with both rigid foam and closed-cell spray foam, then these Canadian rules based on polyethylene become irrelevant.
If you can provide a few more details -- for example, whether this is new construction or an existing house, and more information on whether you have access to this crawl space -- then GBA readers may be able to provide useful advice.
Hello Martin,
Thank you for responding to my question. I'll try to answer all your questions, but please fire away if there are still needed details.
It is an existing home, built in 2002. The crawlspace is about 18 inches from dirt to joist at the perimeter, and about 48 inches in the middle. The vast majority of the area has more than 36 inches of clearance. The access to the crawlspace is through a 30" x 30" hatch in the floor of the utility room.
I'm sorry, I tried to attach a photo to my first post, but it did not work. I've tried again here, hopefully I'll have success this time. I've also tried to attach a diagram of the structure. For reference, the basement floor sheathing is about 50-54 inches below grade.
My comment "I’m pretty certain I don’t want to insulate without creating a new VB [vapor barrier?] on the warm side," was in direct reference to simply adding batt insulation on the warm side of the existing vapour barrier. I should have been more clear.
I guess my question boils down to: How do I safely and effectively insulate the wall and headers without creating a moisture trap or other issues for the structure? Any advice would be appreciated. Thank you.
Al,
Q. "If I insulate the ledger and blocking with rigid foam or spray foam (strongly leaning toward new HFO spray foam), am I trapping it between two vapour barriers?"
A. As long as the ledger and blocking are dry on the day you insulate, I wouldn't worry. For more information on this issue, see "Sandwiching Roof Sheathing Between Two Impermeable Layers." (Although the link will take you to an article on roof sheathing, not crawlspace ledgers, the issues are similar.)
Q. "How do I safely and effectively insulate the wall and headers without creating a moisture trap or other issues for the structure?"
A. Either closed-cell spray foam or any type of rigid foam will work. I wouldn't worry if I were you. For background information on how you might analyze these issues, see "Worries About Trapping Moisture."
I know this is an old thread, but hoping to get some guidance. I'm building a 2 story home in a hot dry climate (southern CA - climate zone 3a) which is also in a flood zone. The finished floor elevation needs to be at least 4 ft above the highest adjacent grade, with an adequate # of flood vents. In my case this is anywhere from 4-6 ft above the natural grade throughout the house. A slab doesn't make sense given the height. The crawlspace will obviously be relatively spacious but a full basement is not an option, given the flood zone. I know GBA contributors all strongly recommend a conditioned, unvented crawlspace, but i also have high methane levels under the house and a conditioned crawlspace would require a complicated and expensive methane mitigation plan which would be cost prohibitive. I plan to put all my mechanicals in my unvented/conditioned attic, so no duct work will run in the crawlspace either.
I am wondering what is the best way to insulate and air seal the floor (above the crawlspace). I read lots if indirect references to how tricky that is, but don't fully understand why. Can i just spray closed cell foam under the floor between the joists? Would a combination of closed cell foam and fiberglass batts (cheaper) be reasonable? Or would rigid foam under the joists be preferable? Appreciate any suggestions.
Oren,
In those circumstances you may want to consider building on piers.
Oren,
In your situation, an unconditioned vented crawl space makes sense.
Here is a link to an article that explains how you can insulate your floor: "Insulating a Wood-Framed Floor Assembly."
Log in or become a member to post a comment.
Sign up Log in