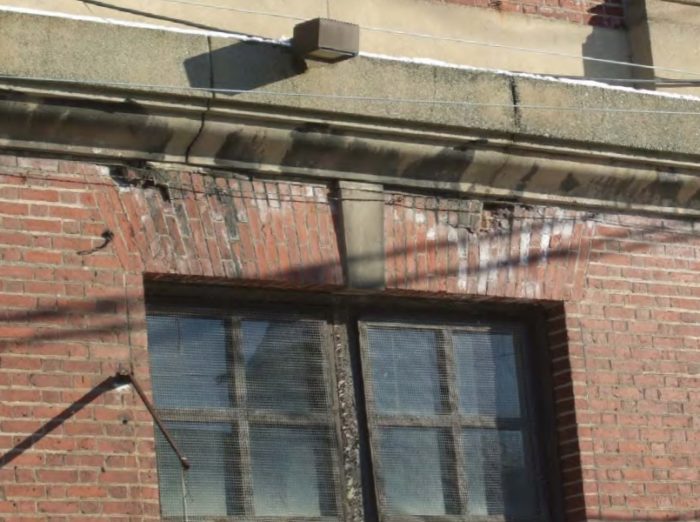
Image Credit: John Straube
UPDATED on March 18, 2019
Older buildings with load-bearing brick walls are common in many northern U.S. cities. While these thick (muti-wythe) brick walls were often plastered on the interior, they were rarely insulated.
Load-bearing brick walls are tricky to insulate. Here’s why: if you insulate the wall on the interior, you’ll make the bricks colder during the winter. As we know from the psychrometric chart, cold bricks are always wetter than warm bricks. Once the wall is insulated, the escaping heat that formerly passed through the bricks is no longer available to drive out the moisture. So your wet bricks stay wet for a long time. In some cases, repeated cycles of freezing and thawing can permanently damage the bricks, causing them to fall apart.
After I began researching and writing this article, I received an invitation to attend the Department of Energy’s Expert Meeting on Interior Insulation Retrofit of Mass Masonry Wall Assemblies, held on July 30, 2011 in Westford, Mass. (The meeting was sponsored by the Building America program.) The presenters at that meeting — John Straube, Henri Fennel, Terry Brennan, Bill Rose, Mark Bomberg, Christopher Schumacher, and Kohta Ueno — all contributed valuable information that helped with this article.
It’s possible to insulate a brick building on the interior
If insulating a brick wall on the interior can make the wall vulnerable to freeze/thaw damage, does that mean such walls should never be insulated? No. But builders who want to insulate an old brick wall should proceed cautiously.
There are no simple rules of thumb when it comes to assessing the vulnerability of an existing brick building to freeze/thaw damage. However, here are the most important points to remember:
Weekly Newsletter
Get building science and energy efficiency advice, plus special offers, in your inbox.
This article is only available to GBA Prime Members
Sign up for a free trial and get instant access to this article as well as GBA’s complete library of premium articles and construction details.
Start Free TrialAlready a member? Log in
172 Comments
fiberglass
"Clearly, fiberglass batts should never be used to insulate the interior of a brick wall."
is fiberglass so bad? Even when used with a good vapour check on the interior? It will allow the wall to dry to the inside, will closed-cell spray foam allow this?
Foam Injection
Denver's most respected home energy upgrading contractor has been injecting foam into brick walls for years. In a double wythe wall, you can sneak in an inch of foam for an R value of 6+.
Dennis Brachfeld of AAS reports no moisture problems (Denver is relatively dry) and much increased comfort. It's a very expensive procedure, even without building a new interior wall, so they rarely do an entire home, just the most uncomforable rooms.
In my own testing, I found that the "blue can" Great Stuff (low expansion) fills the wythe cavity much better than the cheaper, standard "red can" stuff.
Note: foam injection may cause worse problems even than insulation on the inner wall. That's because it plugs the cavity behind the exterior bricks. This cavity is traditionally relied on to help drain and dry the brick. So stay away from this method if you have rain in the day with freezing at night.
Response to James
James,
Q. "Is fiberglass so bad?"
A. Yes. It is almost impossible to make drywall so airtight that interior air will never contact the bricks and lead to condensation.
Q. "Even when used with a good vapour check on the interior?"
A. The problem has more to do with air leakage and air convection than vapor diffusion.
Q. "It will allow the wall to dry to the inside."
A. Precisely my point -- you don't want to allow vapor diffusion to occur between the warm, interior air and the cold bricks -- a vapor-open assembly is counterproductive.
Q. "Will closed-cell spray foam allow this?"
A. No, and that's a good thing.
fiberglass again
I ask because you don't advocate interior polyethylene barriers because that stops the wall drying to the inside, but you are advocating closed-cell foam which will also stop the wall drying to the inside. Am I misunderstanding something? I don't want to install the wrong material in my renovation. No one over here (UK) uses spray foam on bricks, most use closed-cell foam boards.
Also perhaps cellulose has worked (as mentioned in the article) as it has vapour resistivity between mineral wool and closed cell foam. (I'm using figures for resitivity from the following document http://www.viking-house.ie/download.html, pg 3 and 4). However, the cellulose manufacturer does not recommend cellulose on solid masonry walls.
By the way you might be interested in some of the projects on that site (eg the solar slab).
Response to James Brown
James,
You're right -- I don't advise the use of interior poly in most climates. However, interior poly makes sense in much of Canada and Alaska -- at least on the interior of wood-framed buildings.
Load-bearing brick walls differ in many ways from wood-framed buildings, however, as I try to make clear in the article. I don't think you should use any rules of thumb from wood-framed construction when insulating an existing building with load-bearing brick walls. In case you are wondering, I don't advocate the use of interior poly when insulating brick walls.
Rigid foam boards can be used to insulate the interior of a brick wall, as long as the seams between the sheets are carefully sealed with caulk, canned foam, or tape. All of the other advice in the article above would still need to be followed: deal with the rain, assess the bricks, consider the climate, and don't install too much insulation.
Cellulose insulation differs in two important ways from fiberglass batts: dense-packed cellulose does a much better job of limiting air infiltration than batts, and cellulose is hygroscopic. If you were to use fiberglass batts to insulate a cold brick wall, condensation could run down the brick wall and pool on the floor. If you install cellulose -- still an experimental method, and probably risky in cold climates -- the cellulose is able to absorb and store a certain amount of moisture that might otherwise condense against the cold bricks. If the wall assembly allows drying to occur at a faster rate than moisture accumulation -- something that can be determined by WUFI -- such walls can succeed. Perhaps.
fiberglass
thanks Martin. I've got a better grip on the issues now.
cellulose
I know cellulose is best applied damp with a blower machine but these can't be rented in the UK. Is it feasible to mix the cellulose with say, a paddle mixer in a big bucket, adding water and then apply it by hand, a bit like rendering/harling/plastering? This would be for filling the gaps between studs before drywalling over.
Response to James Brown
James,
I don't recommend your suggested technique, for a variety of reasons. The technique introduces too much water; you won't be able to fill all the gaps; and the density of the installed insulation will be too low.
Insulating the interior of a brick wall is tricky. You want a carefully air-sealed assembly. If you want to insulate with cellulose -- I method I don't recommend -- then I suggest you take John Straube's advice: "You need to install a fluid-applied membrane that is vapor-permeable but airtight on the interior surface of the bricks." This is not a method that is appropriate for do-it-yourselfers who spread gobs of insulation with their hands.
My advice is to hire an insulation contractor experienced at insulating brick walls.
Extending existing buildings
This article brings up a number of good points about insulating brick buildings to help extend their lifetimes. While it's true that the preferred method would be to insulate the exterior, there are a number of reasons that may be impossible - many times related to historic reasons such as for credit, zoning or funding. Insulating the interior as you've stated really comes down to "it depends" which is probably the best way to put it. A professional can be most helpful in determine whether the interior insulation is really the best thing for the brick building and if so, to what extent. In the end, the deciding factor should be the cost and life-cycle assessment for your options.
insulating brick house from outside with foam
As I understand it, your saying insulate from the inside, but not outside. I witnessed a foam company insulate from the outside by drilling holes in the gaps 16in on center, Does this, or could this not also fill up any rain plaine designed into the home? And I have not read in this blog anything about rain plaines being involved? Here in Seattle Washington.
Reply to Robert Haverlock
Robert,
All of the information in this article is about multi-wythe load-bearing brick walls. Such walls were commonly built in decades past; most such buildings in the U.S. are between 90 and 200 years old.
Your comment mentioned "rain planes." I assume that you are referring to the drainage gap in a brick veneer wall. Brick veneer walls are built completely differently from mult-wythe load-bearing walls. The typical brick veneer wall is non-structural. A single wythe of bricks is installed; between the brick veneer and the wall sheathing is a drainage gap that shouldn't be blocked or filled. Most brick veneer buidlings are actually wood-frame buildings; the wood-frame wall is the load-bearing wall.
If any insulation contractors are installing spray foam in the drainage gap of brick-veneer walls, they are making a mistake. These drainage gaps should not be filled.
cellulose
"you won't be able to fill all the gaps; and the density of the installed insulation will be too low"
It seems unlikely to me that the machine could apply the cellulose with more force than I could apply by pushing it on with a hawk and trowel (or similar, eg tamping it. Or, as you say, literally with your hands!) This is for a situation where you have yet to sheet over the stud walls. I'm not suggesting it would be possible to fill a cavity via holes by hand successfully.
"My advice is to hire an insulation contractor experienced at insulating brick walls"
Over here that would result in laminate foam board, or foam board in stud bays then drywalled over. This method has too many detailing requirements to leave to a contractor. I think the spray method ('liquid applied' as you referred to it) is great as it as it would ensure a full fill. My main reluctance to use sprayfoam is the risk it poses to joists / timbers embedded in the masonry. I feel cellulose may buffer the humidity and help move water away from the structural timbers to avoid them rotting.
Good Read
Very good read and even. We don't have to worry about many of these issues in my climate region but I thought the article, and follow up, was well done.
Silane Water Repellent?
Couldn't you minimize the amount of moisture penetration by using a silane/siloxane water repellent? That would allow the brick to dry to the exterior while preventing moisture intrusion.
Insulating between the wythes
Hello, very timely subject for me. I've got a double whythe, load bearing house and would like to place insulation between the whythes in the 2.5-3 inch gap. Preserve the exterior and avoid a complete interior remodeling job are the reasons. Plus fantastic thermal behavior in the summer with the added mass.
Location is dry and cold, 12 inches of precip/year, half in snow. 8000HDD. Absolutely no sign of moisture related deterioration anywhere in the house. The roof is steep and has gutters but the bricks are pretty soft. Interior is plaster directly on the brickj and the basement is dry.
So, I've looked at UF, Air Crete and low rise 2 part foam primarily because they can be injected in the mortar joints. Part of the difficulty is finding an applicater.
What would you recommend in terms of insulating the void? Can it be done safely and what type of insulation would you recommend.
Attached is a photo.
Thanks, Jim Baerg
Hi, curious if you ended up doing this project? I'm in a similar position and want to know the outcome. Thank you
Response to Eric Dymond
Eric,
In general, historic preservationists and most building scientists agree that, although silane/siloxane coatings may have their applications for specific problems, they should not be used as a general solution to try to improve the hygrothermal performance of all of the walls of an existing building. Their performance and longevity are questionable.
Response to Jim Baerg
Jim,
My advice to you is the same as the advice presented in the article: hire a consultant experienced in these issues, and have your bricks tested. (Although if you are unable to locate a contractor willing to do the work you propose, the entire issue may be moot.)
Lime wash as water repellent?
Eric asked above about silane/siloxane water repellent. While discussing this topic with a restoration mason, he mentioned lime wash, which is apparently suitable for old(er) load bearing masonry walls. Each lime wash application lasts only for a few years, but it is said to improve the hygrothermal performance of the wall. Any opinion on this option?
Internal Insulation of Masonry Walls Measure Guideline
If anyone is interested in BSC's current document on the subject, our Building America-sponsored research report has recently been finalized:
RR-1105: Internal Insulation of Masonry Walls: Final Measure Guideline
http://www.buildingscience.com/documents/reports/rr-1105-internal-insulation-masonry-walls-final-measure-guideline/
Response to Kohta Ueno
Thanks, Kohta. I've added a link to the document in the "More Information" sidebar.
I know this article is a bit
I know this article is a bit old, but are these concerns basically limited to cold climates? I am down in New Orleans where it only freezes occasionally in the winter but we do have a ton of moisture (both bulk and vapor). Is this freeze/thaw concern really only a problem in the North with repeated and extended freezing / thawing cycles?
Response to Randy Starr
Randy,
Yes, these concerns are limited to cold climates. As building scientist Joe Lstiburek, who was quoted in the article, said, “It’s rare that we have to worry about freeze/thaw problems in places like New Jersey and New York City.”
None of the concerns mentioned in this article apply to buildings in New Orleans.
Awesome. Thanks.
Awesome. Thanks.
Philadelphia
Thank you for writing this article. My wife and I are currently looking to relocate to another home in Philadelphia, which of course, means old double-wythe construction! As we look I'll pay closer attention to the brick conditions on the exterior, particularly around chimneys and parapets. I found it interesting that you referenced Philadelphia as an area that wouldn't be a problem to insulate from the interior. I would still be a little wary of adding too much insulation, as there can be prolonged periods of wet winter weather, especially the last few years. Additionally, I disagree with the EIFS recommendation, as I believe it's an inferior product as well as a dangerous one. Here in Philadelphia there are a lot of contractors installing it, only to have it redone shortly after. Many times, it's the installation and flashing detailing, etc. I will personally be looking into mineral wool open joint rainscreen on the rear / side where the street presence isn't as important to the block conformity.
Any articles on insulating attic spaces? I know there are a lot of flat-roofed homes in the Northeast that are un-insulated in the tight void space between the roof and ceiling.
Response to Matthew Emerson
Matthew,
The best way to insulate a flat or low-slope roof is with a layer of rigid foam above the roof sheathing. That means that insulation upgrades are usually performed when it is time to install new roofing.
Following the question about a flat roof.
Will Roxul and a vapor barrier be a good solution for a flat roof (NYC area)? Will this method cause problems with the embedded wood joists in a load-bearing brick wall? I will not insulate the walls, only the ceiling and overlap the vapor barrier a few inches with the wall. Thanks in advance.
Eddy
Response to Eddy Trochez
Eddy,
In the response posted on this page immediately above your question, I wrote, "The best way to insulate a flat or low-slope roof is with a layer of rigid foam above the roof sheathing."
If you want to insulate below the sheathing, I recommend that you use closed-cell spray foam.
Roxul is a bad choice because it is air-permeable. It can allow warm, moist interior air to reach the cold roof sheathing, leading to condensation.
A polyethylene vapor barrier is not recommended for this application. It will not prevent air movement from the interior to the sheathing. It's impossible to install poly in a way that is totally airtight -- and in any case the trapped air would inevitably have moisture in it anyway.
Thanks Martin for the help.
Thanks Martin for the help. Some people are installing rigid foam bellow the sheeting and sealing the edges with foam or caulk. How do you feel about this approach?
Second response to Eddy Trochez
Eddy,
That approach -- sometimes called "cut and cobble" -- can work, but it has two disadvantages:
1. Obtaining an airtight installation (which is essential) is fussy, time-consuming work.
2. Even if the work is perfect, you still have thermal bridging through the rafters.
Thanks Martin
Martin,
I was doing some reading (your article here on GBA) regarding the possible health issues with spray foam. The situation definitely makes it more difficult for the DIYer, and the cost to hire a professional is sometimes astronomical for this type of job. What kind of advice would you give to somebody who wants to do it himself? Is it worth it? I'm convinced that spray foam is the way to go in my situation, but the thought of having lingering fumes and smells is very scary.
Third response to Eddy Trochez
Eddy,
Only you can make that decision. You have to weigh your expected energy savings against the expected cost of the work, and decide whether you feel comfortable using spray foam. It doesn't matter what I think -- only what you think.
The best approach is to combine new rigid foam on top of the roof sheathing with a re-roofing job.
Thanks Martin
If it wasn't for this site, I would've made a big mistake. Local contractors wanted to blow in insulation.
Question regarding the rigid foam.
Will I need a second layer of sheathing on top of the rigid foam? Can you point me to a good online resource on the subject?
Thanks a million,
Eddy
Fourth response to Eddy
Eddy,
No, you don't need any sheathing on top of the insulation. Here are two articles to help you:
How to Insulate a Low-Slope Roof
The Rundown on Low-Slope Roofing
Spalling
If old brick walls are patched and repointed with cement based mortar they spall. Spray foam insulation becomes extremely hard and impermeable (like a cement based mortar). if the spray foam is applied to the interior would it not cause the same spalling problem on the interior of the wall. would it be better to apply a rigid foam insulation board and then an inch of spray foam. Would you for see any problems with this method? I would be reluctant to spray directly onto the brick. This would be an R value of 12 or so. We are based in Toronto and our bricks appear in great condition (even in the chimney)
Response to Joanne Alfonsi
Joanne,
The problem you describe -- repointing an older brick building (most of which have lime-based mortar) with Portland-cement-based mortar -- is independent of the problem described in this article (insulating an older multiwythe brick wall on the interior). Obviously, there is more than one way to damage an older brick building. Choosing the wrong repointing mortar is one way to damage it. Insulating it incorrectly is another way.
I stand by the advice given in this article. If you want to insulate a brick wall on the interior, follow all the steps listed in this article before you proceed. If you are sure that it is safe to proceed, then closed-cell spray polyurethane foam (sprayed directly on the interior of the bricks) makes more sense than rigid foam.
Philly Double Wythe Detail
Hey all, just finalizing on a wall detail for my breezeway double wythe brick wall. I would add 2" polyiso foam board with reflective side showing, with a open joint rain screen system ( Hardie Panel,etc). My inside was my greatest concern. I have decided to frame 1.5" away from the interior brick, with 1 " spray foam sprayed directly on the brick, and then denim insulation in the 2x4 cavity 16"oc. And 3 mil plastic sheathing before 1/2" sheetrock. Any suggestions/advice would be appreciated, thx
Response to S. Tunji Turner
S. Tunji Turner,
My advice hasn't changed since I wrote the article. So: if you are leaving the exterior bricks exposed, the only insulation to consider is closed-cell spray polyurethane foam. And that should only be used if you feel confident about your exterior water management details and the quality of your bricks.
If you are willing to cover up the exterior bricks -- and it sounds like you are -- I would put all of the insulation on the exterior of the building. Two inches of polyiso is better than nothing, but I would aim for at least 4 inches of polyiso if I were you.
Response to martin
So you are suggesting 4" exterior with a rain screen , soffit box, water management. and then no foam on inside, just the denim insulation on the inside w/plastic.
Response to S. Tunji Turner
S. Tunji,
No denim insulation. No interior polyethylene. Otherwise, you've got it.
Brick walls in Arizona
Hi- I hope this blog is still active.
We live in a 1961 brick house in Tucson, AZ, without any insulation of the exterior brick walls. Brick is about 4-inch thick (yes, we basically live in a brick oven). We would like to insulate inside. I don't think we have to worry about the freeze/thaw problems, but not sure what materials do use. Some folks here that have experience say, fiberglass batts are just fine and less expensive. We also looked at the rigid foam-sheets.
Any advice?
Response to Anita B.
Anita,
In your climate, you can insulate the interior of your walls without worrying about freeze/thaw damage.
I don't recommend that you install fiberglass batts, for two reasons: (1) Fiberglass batts perform worse than all other insulation types, and (2) If they were insulated with fiberglass batts, your walls would be susceptible to inward solar vapor drive problems, especially if your house has air conditioning. (For more information on inward solar vapor drive, see When Sunshine Drives Moisture Into Walls.)
I advise you to install rigid foam insulation on the interior of your walls. Polyisocyanurate insulation is the most environmentally friendly type of rigid foam insulation, and it has the highest R-value per inch. Polyiso performs well, and it will prevent any problems from inward solar vapor drive.
Vermiculite
Excellent article!
I have an 180 yr old house with load bearing brick walls in the Philadelphia area. The bricks have an exterior layer of stucco which has been painted. The house roof has a 2 1/2' overhang which keeps the walls fairly dry. The foundation is also brick and this allows some moisture to wick up into the above grade brick. The interior plaster is applied to lath on top of 1" thick furring strips. the gap created by the furring stips is open from the basement to the attic. Would it be advisable to insulate and/or seal the top and bottom of this 1" gap? If so, would vermiculite be an option? It seems like the easiest material to flow down into that narrow space.
Response to Jeff Spiers
Jeff,
While some people have used vermiculite to insulate the type of gap you describe, I don't recommend the practice.
The main problem with vermiculite is that it does little to stop air flow. If your gap is open from the basement to the attic, the most critical step for you to perform is air sealing. Every single channel needs to be carefully sealed in the basement as well as the attic. Unless you are planning to demolish your interior plaster, this work will need to be performed in the basement and attic, using a two-component spray foam kit.
One inch of air-permeable vermiculite wouldn't provide much R-value anyway.
Since the exterior of your building has been stuccoed, the best way to insulate the building is with an exterior layer of rigid foam. The most economical way to do this would be to finish the exterior with EIFS (rigid foam plus synthetic stucco). If you call up a few local EIFS contractors, you should be able to get bids for the work.
If you prefer to do the work from the interior, I recommend that you follow the advice in the article, by installing spray polyurethane foam against the interior of your brick walls. That will require you to demolish the interior plaster.
Freeze/thaw concerns in DC?
The article and commentary have been so helpful for my current predicament. I bought a 100yr. old double wythe end-unit row house about four years ago that had been flipped. This past spring the house started to feel very humid. I started to notice mold in my closet (on an 2nd floor exterior, northern wall). After several consultations with an industrial hygienist, we started to discover more mold on the western and northern walls where the air was stagnate (behind pictures, closets, etc). We determined that the mold was caused by a vapor drive issue from the exterior brick. It was getting caught in middle of the wall and then condensing in the cooler months, not drying, and then providing the conditions for mold to grow inside the wall the spring/summer. The mold I saw behind my pictures was because the drywall was saturated with water. When they flipped the house, they applied drywall directly to the old plaster without a vapor barrier. In some cases there was also wallpaper attached to the plaster and then drywall over it....a recipe for disaster that I am now living out.
I have performed the mold remediation steps and am now left with very old plaster and in some areas just brick where the plaster has fallen off. My next task is to figure out how to rebuild in a manner that will prevent vapor drive to the inside AND reduce the risk of condensation inside the wall structure. While I've consulted with several structural engineers and performed lots of internet research (love building science articles), I'm still not confident of the best way to address the issue without causing unintended consequences.
The first step I am taking is to remove the remaining plaster and repoint the interior brick with Type N lime mortar and then apply a brick sealer on the interior. My current plan to finish the wall is to frame out the inside using 1.5" x 3.5" studs, leaving about an inch gap between the frame and the brick and the framing oriented like in the picture below (my current kitchen). From there, I wanted to hire a spray foam contractor to apply 2" of closed-cell spray foam insulation that would fill in the 1" gap behind the framing plus about an inch into the frame cavity. After that, I would reapply drywall. I think this would address both my vapor barrier and condensation concerns, but I am not sure how it would address the freeze/thaw concerns. I read it is not a concern in NYC, so I assume DC is fine to use this method. Do you see any red flags with my approach? This is not my area of expertise and I've found that different people have lots of different opinions. This is all really expensive and unexpected, so I only want to do this once, so am just looking for some validation that I am on the right track. Thank you so much!
Diane in DC
Response to Diane McAvoy
Diane,
Your case raises many questions.
First of all, the climate in your location (Washington, DC) is mild enough that you really don't have to worry about freeze/thaw damage to your bricks. In general, it should be safe to insulate the interior of your walls with closed-cell spray polyurethane foam.
But your mold situation is unusual, and the actual mechanism is a little puzzling. I suspect that two factors may be at work here: the exterior of your bricks may be unusually wet -- which would be the case if your house had insufficient roof overhangs or some type of flashing problem -- and (perhaps) the interior finishes on the walls were vapor-impermeable. (The classic problem occurs with vinyl wallpaper, which is a disaster if used in an air-conditioned home in a humid climate.)
In your climate, an uninsulated brick wall doesn't usually grow mold. During the winter, the indoor air is usually dry, and the bricks are kept warm by your heating system. During the summer, if the house is air conditioned, the indoor air is dry, and any moisture in the bricks dries inward -- unless, of course, there is vinyl wallpaper to mess things up.
Without a site visit, I can't know what's going on at your house, of course, and you shouldn't take any action based on my speculation.
You shouldn't proceed with a remedy, in my opinion, until you fully understand the mechanism that created the mold. It's possible, for example, that your house has a wet basement or a wet crawlspace, and that the mold grew during the winter; this might have happened if all of the rooms of your house weren't heated.
Any remedies have to start with the basics. You need to do everything you can to keep rain off of your bricks, and that might require better roof overhangs. And you need to be sure that you don't have a wet foundation.
Thanks
Thank you for your comments, Martin. I will look into other factors that may have contributed to moisture accumulation in the wall besides just vapor drive-related moisture getting stuck and condensing in between the plaster and paper-backed drywall. I'll keep you posted. Best, Diane
Response to Diane McAvoy
Diane,
It's impossible for moisture to "get stuck and condense between plaster and paper-backed drywall." Paper-backed drywall is hygroscopic and vapor-permeable. When it gets wet, it dries rapidly to the interior of the house -- unless someone installed vinyl wallpaper, or unless someone glued a mirror to it.
We recently purchased a 2.5
We recently purchased a 2.5 story brick masonry home in Chicago that we plan to renovate. Upon demolition of the kitchen, I discovered moldy batt insulation between a plastic sheathing (the last renovator's vapor barrier form 1983?) After reading your article, and the ones on BSC this made sense. I raised the issue with my architect and asked how we should address and this was his response...
"We have typically installed a vapor barrier on the inside face of the masonry wall with 2" rigid foam insulation between wood or metal studs, and then we use a secondary vapor barrier on the inside face of the studs (between the studs and the gypsum board). Properly installed, this isolates the insulation and framing from condensation or water infiltration from either side of the interior wall assembly. Rigid foam is considerably more expensive than batt insulation (when calculated as dollars per R-Value) but I will investigate the cost of spray on insulation (I have pricing estimates from another project that I can reference). My concern is that spray on insulation will prevent the masonry wall from properly breathing thus trapping moisture in the wall and causing efflorescence and deterioration of the masonry."
1) Can you recommend any consultants in Chicago?
2) Is it time for a new architect?
Response to Colin Marshall
Colin,
Sandwiching insulation and studs between polyethylene doesn't work, because it's impossible to make the poly layers completely airtight, especially on a job site. (Even in a university lab, it would be a difficult challenge.) Changes in temperature and air pressure will cause a pumping action that leads to air exchange between the air trapped between the polyethylene layers and the air on the exterior or interior side of the sandwich assembly. When humid air enters the sandwich assembly, it can trap moisture between the poly layers. Later, when one side of the poly sandwich gets cold, water will condense on the poly and run down to the bottom of the sandwich, and will pool at the bottom plate.
Spray polyurethane foam insulation is the recommended insulation material to use on the interior of a multi-wythe brick wall -- subject to the caveats listed in this article.
The sentence, "My concern is that spray on insulation will prevent the masonry wall from properly breathing thus trapping moisture in the wall and causing efflorescence and deterioration of the masonry" doesn't make any sense. If the architect wants the brick wall to "breathe" to the interior, why is he suggesting the installation of polyethylene -- a layer that limits "breathing"? Clearly, a multi-wythe brick wall that is insulated on the interior will "breathe" (I would say, will dry) to the exterior, not the interior. There are still risks, of course, especially in freezing climates. These risks are explained in the article.
If you want to hire a consultant, the consultant doesn't have to live in Chicago. It's hard to beat the consultants at the Building Science Corporation in Somerville, Mass., or at Building Science Consulting in Waterloo, Ontario.
Only you can decide whether it's time for a new architect. It sounds like your current architect will need a little hand-holding or guidance because of an incomplete knowledge of building science. Unfortunately, that's not unusual -- so switching architects may not help.
mortar and paint
In my local many of the buildings are over 100 years old and were constructed with a very soft brick and limestone mortar with no portland cement. My understanding is that because the combination of soft brick and self-healing mortar allows for resiliency in freeze-thaw cycles.
When I observe buildings with damage to the brick it is often caused by either direct water/drainage issues or re-pointing with hard portland based mortars.
Is soft brick and limestone mortar more resilient to being insulated on the interior?
How does exterior painting affect the insulation scenario?
Confused and uncertain!
In the UK, spray foam is very rarely ever mentioned yet given the large number of old houses with 9" walls there is a lot of opportunity and much of what you read is conflicting or not well thought through. The simple fact seems to be ask 3 experts and you get three different opinions and each is convinced he is right. I have a 220 year old brick barn with solid 18" lower walls and 13" upper walls, no damp proof course. The weather here is fairly benign with around 22" rain per year and temperatures rarely move outside of a -5 to +25 range with a median around 15 degrees centigrade. Timber joist ends sit directly in the walls bedded in using the same lime mortar that the walls are built with. I have read many many many articles, spoken to a lot of 'experts' and suppliers and have yet to get a consistent picture of what should be done. Some advocate a woodfibre board or a silicate board essentially glued to the wall to provide a vapour open insulation only some 50mm thick so that enough heat leaks through to keep the inside face of the wall above freezing. Others say seal it all up with a PIR type vapour proof board - but the air will still leak through the woodworm holes and old buidings are impossible to seal adequately. So my thinking is to go the vapour open route in conjunction with a central ventilation system to keep dry air moving around inside and allow any excess moisture to evaporate out of the wall into the house and when the sun shines and the wind blows, the outside will dry naturally. The real dilemna here is that I am not sure that I can do nothing e.g. leave the walls uninsulated (even though that's what the conservation people would like) as the heat loss is so high we would need to round in ski-suits in winter in order to keep heating bills down.
Hi, curious what you ending up with?
Response to Iain Whyte
Iain,
I sympathize, but I'm sorry to say that I cannot deviate from my advice. It's unwise to try to invent new ways to insulate this type of building, especially if there are embedded beams or joists.
Of course, the best way to insulate this type of building is on the exterior, with a layer of exterior rigid foam protected by synthetic stucco (EIFS), or mineral wool panels and synthetic stucco.
Good luck.
Brownstone
We are renovating a circa turn of the century Brooklyn brownstone. The only walls we were considered insulating were the front and back brick walls. There are no joists or beams embedded into these two exterior walls. They are about 17 feet across. My question is, if the facade is covered by a layer of brownstone, does the brownstone provide any insulation or water protection to the bricks behind?
The back wall is painted white from the outside. Looks like it has been repainted many times. There are no leaks or issues I can detect on the inside of the walls. We have them currently exposed after demolition. We have not discussed the type of insulation with our contractor. After reading your article I am prepared to tell him to go with closed-cell foam. I will note, we have not had a specific brick consultant come out, but we have had several engineers look at the place who said nothing about insulation concerns.
Oh, and another question. Is insulating the cellar brick walls an issue at all? They are mostly, though not completely, underground.
Response to Jason Cuve
Jason,
The easy question first: I don't think you'll have any problems resulting from insulating the cellar walls, although it's always possible that you'll see some spalling or freeze/thaw damage of some of the above-grade exterior bricks (if there are any).
When it comes to brownstone, I'm going to have to plead ignorance. I suggest you consult local experts familiar with brownstone. If you can't find a local expert, you could work with the Building Science Corporation.
Triple Wythe Wall Question
I have a home with load-bearing clay brick basement walls that is constructed withe three wythes: the two on the outside abut each other and the third inside wythe follows a 1.5" air gap. All three are held together with tie bricks. Question: Does the air gap mean that the inside wythe is "warm" and the outer two are "cold". After following along with this article and the many comments, the temperature of the wall seems to be key in determining what materials can be placed directly against the brick.
Response to Rich Steenwyk
Rich,
Q. "Does the air gap mean that the inside wythe is 'warm' and the outer two are 'cold'?"
A. During the winter, the innermost whythe of a multi-wythe brick wall will always be warmer than the outermost whythe, regardless of whether the wall has an air gap.
The air gap will provide some R-value, of course, especially if air leakage through the wall has been controlled (and you probably can't make that assumption). Under ideal circumstances, the R-value of the air gap probably falls in the range of R-1 to R-2.
In winter, the temperature of the bricks will be colder on the exterior of the wall than on the interior of the wall; and will be colder near the top of the wall than near the bottom of the wall.
No portion of this wall can be considered well insulated.
Most building experts would probably note that, in most circumstances and in most climates, it's probably safe to install 2 inches of closed-cell spray polyurethane foam on the interior of this basement wall. However, the rigid foam will lower the wall's drying potential, and this change can lead to an increase in the moisture content of the sill beam resting on the brick wall. If the above-grade portion of the wall is relatively high (more than 8 inches), and is well ventilated (exposed to sunshine and not shaded by vegetation), the risk of rotting your sill beams is lowered. If conditions indicate that your sill is at risk, it may be advisable to jack up the house about 1/2 inch so that you can insert a capillary break (metal flashing or rubber roofing) between the top of the brick wall and the sill beam.
Here is a link to a relevant article that deals with stone foundation walls (rather than brick foundation walls): Rubble Foundations. While the walls discussed in this article differ from yours, some of the advice in the article is still relevant to your case.
Philly rowhouse needs to be insulated
Now my head is spinning enough to lift right off of my body.
All that I want to do is reduce my heating and cooling loads. It seemed simple...insulate. But then there's vapor control and condensation and now brick concerns.
Let me see if I understand; cellulose is out, fiberglass is out, spray foam may be ok, vapor barrier is out, vapor permeable is ok, foam boards may be ok, air movement is bad, fluid applied permeable membranes may be necessary.
Some or all of what I just said may be partly or completely right or wrong. That's where I'm at.
There is a parapet wall 3' high in the front of the house that appears to have suffered no damage in 70 years.
This house is a rowhouse. Just the 19' wide front and back walls are exposed. It's 70yo (1945) and has a block and brick interior wythe and a brick face. The walls were furred with 3/4 stock and then covered in plasterboard and plaster.
The plaster and plasterboard are fully stripped as is the ceiling below the flat roof. I was going to 2x4 stud the walls and insulate with Roxul or fiberglass but now I'm not sure what to do. How do I get a definitive answer specific to my house and climate?
Ed
Response to Edward Lampe
Edward,
Q. "I was going to 2x4 stud the walls and insulate with Roxul or fiberglass but now I'm not sure what to do."
A. My article is fairly clear on this point: you don't want to insulate this type of building with an air-permeable insulation like Roxul or fiberglass.
Q. "How do I get a definitive answer specific to my house and climate?"
A. I suggest that you take the advice provided in my article. If you don't have the confidence to reach any conclusions based on the recommendations in my article and a thorough inspection of the building, you should invest a few thousand dollars and hire a consultant from the Buildling Science Corporation to help you. The investment in consulting fees will be less than the cost of repairing your building if you make a major insulation error.
Philly rowhouse II
Thank you for your reply.
I've taken the time to do reread your article and others like it.
I have looked over the brickwork and feel secure that it is robust and unlikely to suffer a freeze-thaw issue. The 3' tall parapet wall appears identical to all other brickwork.
If I have concluded correctly, good insulation practices would be either closed cell spray foam applied directly to the inside of the masonry wall with a less expensive infill, a flash and batt approach.
Or, coating the wall with a fluid WRB and then adhering rigid foam board, polyiso, on top of that. The wall is wavy by up to 1/2" so the flash and batt seems ideal.
And for both, positioning the studs off of the masonry wall as much as is feasible and creating a well executed air barrier.
My question now is, for a flash and batt, what is the minimum thickness for the flash as far as both reducing the chance of condensation on the flash and providing proper vapor permeance? I know I read it somewhere amongst all of my research but now can't locate it.
And would the batt be faced or unfaced?
Thanks again, this article has prevented me from making a serious and costly mistake.
Ed
Response to Edward Lampe
Edward,
Once again, I'm going to stick with the advice in my article. Your attempt to come up with new approaches is risky.
If you have determined that your bricks are suitable for insulation on the interior, you can install between 2 and 3 inches of closed-cell spray foam against the bricks.
I do not recommend that you install a water-resistive barrier on the interior side of your bricks.
I do not recommend that you try to insulate your bricks with rigid foam.
I do not recommend that you attempt a flash-and-batt insulation job.
Philly RowHouse manual and insulation
Hi,
My home is a 1909 Philly row home with brick construction. My walls appear to be an inside run of cement brick with more expensive traditional brick for the exterior run. There appeared to be some settling, but no mortar problems or crumbling bricks.
I'm in the middle of a kitchen remodel which is the back end of the row home. The room has two exterior walls. The whole room was gutted.
Your site suggests that Philly is ok in terms of freeze thaw. One of my walls is protected by a cantilevered second floor from rain, the other looks onto my neighbors wall with a span of about 8 feet, so some rain exposure, but not terrible and really wind dependent.
Philly has a RowHouse Manual. They suggest keeping an air space between the interior of the brick and the insulation, then a vapor barrier attached to the studs between studs and drywall. If their recommendations are correct, this will lend itself perfectly to foam boards.
Can you offer your perspective on Philadelphia's advice?
blown fiberglass
I understand fiberglass can be blown in to achieve a higher density and lower air permeability rate than cellulose. Wouldn't this make it a less risky alternative to cellulose?
Response to James Brown
James,
It's hard to generalize about the density and air-permeability of blown-in insulations. Either cellulose or fiberglass can be installed at a high density or a low density; much depends on the skill of the installer.
Cellulose and fiberglass behave differently. Cellulose is hygroscopic, while fiberglass is hydrophobic. In other words, cellulose does a better job than fiberglass of redistributing moisture from one damp location. Because of this, it's dangerous to assume that fiberglass will behave the same as cellulose.
This article describes the use of cellulose by Chris Benedict to insulate old brick buildings in New York City. The technique makes some experts nervous; in general, spray foam is probably less risky. If you want to experiment with blown-in fiberglass for this application, you are entering unknown territory. Considering the consequences of failure, I don't advise experimentation.
Response to J. Sip (Comment #61)
J. Sip,
You wrote, "Philly has a RowHouse Manual. They suggest keeping an air space between the interior of the brick and the insulation, then a vapor barrier attached to the studs between studs and drywall. If their recommendations are correct, this will lend itself perfectly to foam boards. Can you offer your perspective on Philadelphia's advice?"
I'm going to stick with the recommendations given in this article, even for Philadelphia. If you leave an air space between the interior of the brick and the insulation, you can have convective loops that lower the effectiveness of the insulation. Moreover, interior vapor barriers (presumably, the manual is recommending polyethylene) can cause problems, especially in air conditioned buildings.
Another Old Philly Row -
Martin,
Thanks for all the great info. I'm wondering what you think about the pictures of the major renovation we will be undertaking on a Circa 1900 house in Philadelphia. House is mid-row so only the front and back along with a breezeway of ~1200 SF are exposed. I will be keeping the original front facade so the plan there will be to do 3" of closed cell spray. The sides and back are currently stucco over brick.
Will applying EIFS be possible without first repairing and cleaning the entire stucco surface? Is 4" of EIFS possible to get the required R- value in Philly?
Does EIFS make more sense then just doing rigid foam with another cladding like hardie board?
Is there an argument to re-coat the existing stucco with additional cement based stucco and just do spray foam on the interior for the purpose strengthening the wall assembly?
Thanks
Hot-humid climate walls
Martin, I'm looking at insulating a circa 1900 single story building with 12" brick bearing walls and flat roof. A recent Building Science Corp. article on insulating brick bearing walls says that insulating on the interior with cellulose if OK in a hot/humid climate - brick should have a fluid applied >10 perm air/water barrier coating on the inside face of the brick. Can you suggest some readily available products that fit the bill? Are any of them products that could be installed by a DIY'er? Roller application? What would you recommend if there is an intact/sound interior plaster finish directly applied to the brick? Can the plaster stay? In the BSC article - it also suggests installing an exterior polymer cement parging on the exterior of the brick (or stucco). Do you have any products/manufacturers for the polymer coating? Location is South Georgia. Thanks.
Response to Mike S (Comment #65)
Mike,
The best person to answer most of your questions is an EIFS contractor. If you can find an EIFS contractor to do the work you want and stand behind it, you are all set.
How thick should the insulation be for an EIFS job on a retrofit? That depends on your local code -- most codes don't have minimum R-values for retrofit work -- your budget, and the physical limitations of the EIFS system that your contractor uses.
If you can't find an EIFS contractor that you feel comfortable with, the other option -- exterior foam, furring strips, and fiber-cement siding -- is also possible. As with any construction decision, you have to weigh the costs and the hassle factor with the advantages and disadvantages of each approach.
Response to Roman Stankus (Comment #66)
Roman,
Q. "The brick should have a fluid applied >10 perm air/water barrier coating on the inside face of the brick. Can you suggest some readily available products that fit the bill?"
A. Products include StoGuard, W. R. Grace's Perm-A-Barrier VP, Henry Company's Air Bloc 31, DuPont's Fluid Applied WB System, and Tremco's Enviro-Dri. For more information on these products, see Housewrap in a Can: Liquid-Applied WRBs.
Q. "Are any of them products that could be installed by a DIY'er? Roller application?"
A. Yes and yes. Talk to the manufacturer of the product you want to use before proceeding.
Q. "Can the plaster stay?"
A. Probably not, but I'm not an expert on these products. Again, talk to a technical representative for the product you are considering.
Q. "Do you have any products/manufacturers for the polymer coating?"
A. No, I'm afraid not. You'll have to start with some online research.
does a painted exterior make a difference
I have a residential home built in '17, double wythe exterior walls that i want to insulate. The plan so far is to fur out all exterior walls with stick framing. Plan to foam the floor joist in the vented attic, exterior walls and attic.
The plan also includes painting the home, my question is if the exterior of the home is painted does this eliminate the concern about freeze/thaw?
Response to Mark Herndon
Q. "If the exterior of the home is painted, does this eliminate the concern about freeze/thaw?"
A. No.
First of all, paint is temporary, so it can't be depended on as a long-term protection against a threat that is capable of destroying your building.
Second, most brick experts advise against the use of exterior paint or coatings, because paint and coatings interfere with the ability of damp bricks to dry to the exterior.
Finally, you didn't tell us your climate zone, so it's hard to provide advice.
4A
The exterior has been painted before, thus the exterior paint question. I understand it is not a long term solution, but if this home is to be insulated with closed cell, will repainting and maintaining the exterior address some of those concerns?
I also understand I may be concerned over something i dont need to be if this freeze/thaw issue is not going to affect my home in TN.
Response to Mark Herndon
Mark,
In your climate, your plan will work. Closed-cell spray foam is a good way to insulate this type of house, and your climate is mild enough that you don't have to worry about freeze/thaw damage.
If I were you, I would let the old paint flake off so you could see the real bricks underneath. But I don't think it matters one way or another whether a brick house in your climate has paint -- except that you will be faced with a regular maintenance headache due to the need for periodic repainting.
Never make a mistake to
Never make a mistake to underestimate the nature of brick differing in quality. Not all of them would behave in a similar fashion. Don’t take a chance if you have some precious structure at stake. No doubt about it, a professional would take the responsibility and they also have appropriate equipments, tools and tests to figure out good bricks from bad.
Save the bricks and timbers, then worry about insulation
I just purchased an antique brick cape located in central Vermont. It has survived in good condition for at least 150 years with 2-wythe brick exterior walls and a thin layer of plaster/mortar for insulation. There are 24’ wood timbers that connect the brick walls. They appear to be in good shape, too.
Is there some minimalist approach we can take to insulate the brick exterior walls so that we stop some of the heat loss without endangering the bricks and timbers? We were planning to add interior studs and drywall. Would that air space, without any insulation, stop some heat loss without endangering the bricks and timbers? Would 1” of spray foam applied to the interior bricks be thin enough to avoid any negative consequences?
I’m not so worried about minimizing my heating bills as I am about ruining my antique bricks (or damaging the timbers). I will address any drainage issues come spring, but the house is being renovated now.
Response to John Semple
John,
The answers to your questions can be found in my article. Adding interior insulation will make the bricks colder and wetter than they would otherwise be, raising the possibility of damage. To assess the risk, you have to assess the quality of the bricks and their exposure to exterior moisture. When in doubt, hire an experienced consultant to help you.
Adding exterior insulation is far less risky, of course.
Type of mortar is critical to performance
Since adding exterior insulation might not be allowed by local preservation codes, thus making interior insulation the only option, it should be considered that the material of the mortar or the presence of inappropriate cement mortar repairs is an important distinction relevant to this question.
In historic buildings, mortar in a brick wall assembly is the sacrificial material. It makes up about 20% of the surface area of the wall. A lime based mortar has an absorptive property that allows it to pull liquid out of masonry units. Absorbed water in the mortar will evaporate. Absorbed water in historic mortar triggers a self-healing process where water dissolves calcium in the binder and transports it to voids thereby healing microscopic cracks. After about 75 years, lime based mortar degrades to the point that it needs to be repointed with new mortar. The mortar fulfills its role as the sacrificial material in the wall assembly.
http://www.limes.us/wp-content/uploads/2013/04/APTI-ComparativeLabEval.pdf
Modern cement based mortars do not absorb water or self heal like lime based mortars. Cement mortars are more resilient than historic brick. Historic brick repointed with modern cement mortars retains more water, is subject to greater stresses from freeze/thaw cycles and becomes the sacrificial material. Instead of replacing mortar every lifetime, bricks have to be replaced instead.
Adding interior insulation to a historic brick wall repointed with cement mortar will be more likely to spall brick than adding interior insulation to a historic brick wall repointed with lime based mortar.
Unusual brick house
I am hoping to revive this old article. I have a brick house from 1852 but it is a timber framed building with a brick exterior skin and brick nogging between the timber framing. I am not sure how the skin is attached to the building or if the courses of exterior brick are somehow attached to the nogging. The interior walls were originally either plaster and lathe or tongue and groove panelling, I think. That's all gone now and has been replaced with drywall before I bought the place. Has anyone every seen construction like this? I wonder if the insulation concepts in this article would apply to my house.
Response to Michael Jordan
Michael,
From your description, I would say that the principles discussed in this article apply to your building.
Why not rigid foam
Martin, I'm not clear why you don't believe rigid foam on the interior side of above grade brick is acceptable? Is it because it won't form to the brick pattern, thus leaving air/water channels?
FWIW, this is for the DC/MD region, all above grade buildings, typically vintage 1895-1950.
We'd like to avoid framing out walls to minimize floorspace intrusion. Understanding that it's not ideal, our thinking is continuous ~R8 insulation, air sealing and improving flashing is still a significant improvement. Thanks.
Responser to Jason Holstine
Jason,
Q. "Is it because it won't form to the brick pattern, thus leaving air/water channels?"
A. Yes.
Your climate is relatively mild, so the risk of freeze/thaw damage is low. The use of rigid foam in your climate may work, especially if the perimeter of each piece of rigid foam is carefully air-sealed with canned spray foam. It's your building; you have to assess the risk/benefit equation. Closed-cell spray foam would be a better choice.
some recent work by a British
some recent work by a British preservation agency suggests that ivy in the proper circumstances actually protects brick, by mitigating freeze thaw cycles. The surface temperature of brick behind ivy remained far more constant. They had specific recommendations for how to tuckpoint to discourage rootlet penetration.
I can't find the article at this point, but wonder if anyone had seen it, had any thoughts on this, or would care to venture whether American climate zones might be so distinct as to make the study unuseful in this hemisphere?
Response to Ryan
Ryan,
I'd be interested in reading the paper if anyone has a link.
Two comments: In cold climates, ivy loses its leaves in winter, so it's hard to imagine that it can provide much of an insulating blanket -- especially when the temperature drops to 0°F. So I'm guessing that research based on British ivy during British winters probably won't apply to the colder areas of the U.S.
.
response to Martin on ivy
For some reason, the spam filter blocked my answer, probably because it had links. Bottom line is that if you use a search engine for english heritage ivy and brick, you'll find the report I was talking about. Though once I rediscovered it, I skimmed it and noticed that more of the research was on limestone walls than on brick.
The other thing is that if you search for english ivy united states climate zone, you'll find pages that suggest english ivy is evergreen through most of the US. I live in Chicago, and English ivy should be evergreen here.
Here are some links
Ivy links:
A news story: Why ivy creeping up the walls of your home could actually protect the building thanks to 'thermal shield'
The paper: Ivy on Walls (2010).
A relevant excerpt from the paper: "Looking in more detail at the differences in the aspect, degree of exposure and thickness of ivy cover at each site helps to explain some of the variation in strength of the ‘thermal blanketing’ effect of ivy. The wall studied at Worcester College, Oxford is south facing with high exposure to light throughout most of the day (no nearby shading) and has a relatively thick cover of ivy (c. 45 cm). The thick ivy here has been proved to provide an excellent way of reducing excessive heating under these conditions. In contrast, the wall studied at the Abbey Inn, Byland has a relatively thin cover of ivy (c. 20cm), is east facing and exposed tohigh levels of light (no local shading) and in an area prone to very cold winter conditions. Even this thin cover of ivy has been proven to prevent extremes of cooling in this cold climate – and prevented freezing within the winter months (see Chapter 4, Figure 4). Smaller, but significant, impacts on diurnal temperature cycling were recorded at the south-facing Ramsey site, which has some shading from nearby walls and trees and a thin (c 24 cm) cover of ivy. Even the very thin and patchy cover of ivy at the Nailsea site (< 10cm thick) has been demonstrated to have a significant effect on daily temperature cycling at a west-facing site which is quite heavily shaded all round by other trees. The other sites studied within Oxford showed similar trends."
New construction window installation
We've gutted the plaster and lathe in the kitchen and the back bedroom we're converting to a bathroom in our 2-wythe brick row house in Pittsburgh. We'll most likely insulate with 3" of closed cell spray foam with the studs held out 1" from the wall per your recommendation.
However, we're uncertain about the window installation. Should we use masonry clips, install new PT bucking and use a nailing flange or use some other method?
We're replacing original double hung windows with weight pockets. So, the interior M.O. is several inches larger on each side than the M.O. on the outside edge of the outer wythe.
I'd appreciate any references to detailed measures or methods for lining and framing around the M.O. and installation.
Most of the contractors I've spoken to so far don't believe in using spray foam on windows or in the need for pan flashing. So, I'm still searching for someone who believes air sealing and providing a draining plane are as important as I do.
Thank you for your time and consideration.
Response to Sharon Slovenec
Sharon,
You should start by watching GBA's 4-part video series on replacing a window in a brick house. Here is the link to Video #1 in the series: Video: Replacement Window in an Old Brick House (1 of 4).
The video shows the use of an insert replacement window. If you have no remaining frame in your opening, you would instead buy a new flangeless window, and you would follow the installation instructions provided by the window manufacturer. (Window manufacturers sell windows designed to be installed in brick buildings.)
dimpel board with spray foam
We are currently renovating a 130 year old solid brick building (double wythe) in Toronto and had originally planned to use 2" of 2 lb closed cell spray foam sprayed to interior of brick walls with 2x4" framing located 1" off the wall so that we can spray between studs and brick walls.
After we had started with the renovation the scope got extended quite a bit. We had to replace some of the bricks and repointed some areas using lime mortar. We are going to replace all eaves, downspouts and flashing, ensuring that we will have proper drip edges and water management everywhere. So far all this seems to be in line with your recommendation on how to insulate old buildings.
However after having read an article from Dr. Kim Pressnail (refer to link below) we consider providing an air space between the brick wall and the spray foam insulation to avoid damage caused by moisture trapped in the inner layer of the brick.
We would like to entertain the idea of using dimple board to create the air space. Staple dimple board on to the brick wall, have the 2x4" framing 1" offset and install spray foam onto the dimple board and in space between studs and dimple board. How do you feel about this approach?
https://www.greenbuildingadvisor.com/sites/default/files/Solid%20Masonry%20Interior%20Insulation_retrofit%20w-drainage%20mat.pdf
Response to Claudia Fader
Claudia,
I think that you should stick to Plan A -- without the dimple board.
I am aware of Dr. Pressnail's work; I have heard him speak and have written an article about his research. Here is a link to the article: Nuggets From the 2015 Westford Symposium. (Scroll down to the bold heading that reads, "Insulating old buildings with structural brick walls.")
I think that a fair characterization of Pressnail's work is to call it experimental. Pressnail is still at the data collection and assessment phase. Until Pressnail knows more, and confirms the validity of his approach, it's best to stick with a tried-and-true approach.
Pressnail's method depends on drilling ventilation holes through the brick. There is always a risk of condensation problems when you have an air space adjacent to cold bricks.
Purchasing an Old Brick Home in Vermont
We are considering purchasing an old brick home in Vermont, built in 1826. The current owners have updated it with insulation and spray foam in the basement. Would anyone know of a good home inspector in Vermont who specializes in inspecting brick homes and is well versed in these insulation matters?
Response to Timothy Lawlor
Timothy,
You can't beat the consultants at the Building Science Corporation. Here's the contact info:
Building Science Corporation
70 Main St.
Westford, MA 01886
978-589-5100
http://buildingscience.com/contact
Their consultants travel frequently, to locations across the U.S. and Canada. Vermont would be considered close.
BSC Contact
Thanks very much for the information, Martin. I will contact them soonest.
See below for a case where
See below for a case where spalling was occurring and it stopped with better air sealing and negative building pressure.
Natatorium Building Enclosure Deterioration Due to Moisture Migration
Google: 2075-5309/2/4/534/pdf
Leaving air gap with rigid insulation?
Hi Martin,
Super informative article! Hope it's still open for discussion...
We have walls of double and triple wythe exterior loading-bearing brick wall in New York City, a fully detached brick house. We removed the plaster and lath which were attached to 3/4" thick strips of wood nailed directly to the brick.
What do you think of attaching 2" rigid foam board to the wood strips, leaving a 3/4" air gap between foam board and the brick? I figure this air gap was part of the original design and its worked for 100 years. This would seem to allow the brick to keep 3/4" air gap to still "breathe" since the insulation would not be mounted directly on it. What do you think of this approach? An architect suggested filling in between those wood strips with 3/4" thick rigid foam too, but we were wondering if leaving it empty would help let things "breathe" as it was designed.
We know you advise spray foam in the best option for insulating exterior brick (if you can't insulate the outside of the wall), but we just can't afford the spray foam cost.
Please let us know what you think- thank you again for sharing such a helpful article!
AJ
Response to AJ (Comment #93)
AJ,
Q. "What do you think of attaching 2 inch rigid foam board to the wood strips, leaving a 3/4 inch air gap between foam board and the brick?"
A. I stand by the advice given in my article -- namely, to use closed-cell spray foam, but only if the site assessment for moisture issues and the assessement of brick quality are encouraging.
The problem with your suggested method is that the rigid foam insulation will make the interior surface of the bricks much colder than previously. Now that the interior face of the brickwork is cold, the surface will be susceptible to condensation or even frost formation. If you leave an air gap, you leave open the possibility that air currents will carry warm, moist interior air into contact with the cold bricks.
You don't want that type of condensation. That's why you need closed-cell spray foam -- to preclude the possibility of air movement in this critical area.
One more thought...
Thanks for the quick reply, Martin.
I definitely get the preferred option is spray foam and we wish we could afford that.
But the cost won't allow, so if spray foam wasn't an option, would you stick rigid foam right onto the brick or leave the 3/4" air gap?
I.e. what's your next favorite option?
And yes, I know you may not like both options, but just imagine spray foam wasn't invented yet :)
Thank you!
Second response to AJ
AJ,
As my article points out, the consequences of bad details in this case are quite serious: your building can start deteriorating, and can literally begin falling apart.
You're not going to get me to alter my advice, I'm afraid.
Advice received!
Last question: does the situation change any if the exterior of the brick is covered in stucco already?
We just have one 40' long wall that was stucco'ed over the brick outside so wondering if this wall can be treated any differently to avoid using spray foam.
Third response to AJ
AJ,
I don't have enough experience with stucco over brick in cold climates to answer your question. But I'll provide general advice to GBA readers in your position: If you are willing to consider the application of exterior stucco, by far the best solution to your problem is to install exterior insulation between the bricks and the stucco.
When this approach is taken with synthetic stucco, it is called EIFS (exterior insulation and finish system). It's too bad that you didn't call up an EIFS contractor instead of a stucco contractor.
Exterior insulation is always preferable to interior insulation for this type of building.
Correcting poor insulation construction in a double wythe home
Martin,
Thank you for writing such a thorough article. I am a first time homeowner of a double wythe brick home in Washington DC. The home was built in 1900 and extensively renovated by a company that sold me the house in 2016. The house was gutted down to the point of them installing new joists.
Due to some issues that I have noticed, I am seriously concerned that parts of the renovation were not done correctly. First, they constructed the interior walls with a furring strip adhered to the brick, followed by 1/2 inch foam board, a layer of a plastic vapor barrier, then drywall. There is no air gap. As a result, in the hot humid period of the year, water condenses on the vapor barrier and runs down the inside of the walls. I discovered this issue when water leaked out of an outlet and I cut open a section of the wall to investigate. In addition to threatening the integrity of the building, I am worried it poses a serious fire hazard to have outlets exposed to water in this way. As far as I can tell, this issue only occurs on one side of the house, which faces an alley way and is fully exposed to the elements. I think this is because this exposure results in the largest temperature differential between the inside and outside.
The house is painted, and there is some paint cracking and there is limited spalling.
At this point I am seeking confirmation that this was the incorrect way for the house to be insulated. I think that there is a long path forward for me that includes get an expert to assess the exterior brick as well as getting someone to rip down the drywall and insulation on at least the wall that is experiencing the problems, letting the wall dry out, and then reinsulating and installing drywall.
I would love any input or advice you can provide.
Thanks,
Patrick
need clarification
If I understand the stackup correctly you have:
great outdoors | double wythe brick | furring + air | 0.5" foam | polyethylene sheeting | drywall ???
If yes, you must have about 1.75" between the interior paint and the brick, and shallow 1.25-1.5" deep electrical boxes(?)
[Editor's note: This thread has additional comments on Page 3. Click the number 3 below to continue reading.]
Response to Patrick May (Comment #99)
Patrick,
Your walls are probably experiencing inward solar vapor drive. For more on this phenomenon, see this article: "When Sunshine Drives Moisture Into Walls."
If my guess is correct, that means that the wall with the problem is not facing north.
I agree with your analysis: This wall was not insulated correctly.
Correcting poor insulation construction in a double wythe home
Martin,
The wall is north east facing, so doesn't see constant sun throughout the day, but I think the combination of high ambient heat, some direct sunlight, and high humidity all contribute to it being enough heat and moisture to cause a problem. The description of solar vapor drive in the article you linked seems exactly like what I am experiencing. I think a variety of factors including shading from neighboring buildings and a thicker front to the house have kept the issue from presenting problems in other areas. Regardless, in addressing it I suppose we will need to cut holes at the base of all of the walls and inspect for condensation. Worst case scenario, we would have to replace all drywall on all exterior facing walls, which is a daunting and expensive task.
I will have to get an expert to come and look at it themselves to confirm our suspicions. I wonder if I would have legal recourse like the home owners who bought houses from Zaring Homes and then had to have them retrofitted?
Thanks again for writing the article and taking the time to respond!
Patrick
Hey again Martin,
I spoke with you a few comments back on June 13th.
After your advice, we are now considering doing 2" of closed cell spray foam for the interior of our 3-wythe thick exterior walls.
One thing that wasn't mentioned is that the exterior of the brick is covered in what looks to be either thorocoat or perhaps just white paint- some areas more coated than others. And one wall is covered in stucco. All of this was applied long ago.
Is there any risk to spray foaming inside with those types of coatings on the outside? Will water get trapped inside? This is New York City climate we are working with.
Thank you in advance for any thoughts on this!
AJ
AJ,
Q. "Is there any risk to spray foaming inside with those types of coatings on the outside? Will water get trapped inside?"
A. I don't think the exterior coatings will make a difference, but there are lots of factors at play here, the most important of which is the water-management detailing (flashings and overhangs) protecting your walls. If you have any doubts, it's best to talk to an experienced consultant specializing in brick buildings.
Thanks for your reply, Martin.
One other thing to consider which may affect your thoughts on all this is that the spray foaming is only being done on the first floor apartment of a fully detached brick 3 story, multiple apartment building. The top two apartments/floors will keep their plaster/lathe on .75" furring strips which is what we removed from the entire ground floor apartment walls. Does that change your approach any if the insulating is only being done on the ground floor?
Thank you again!
AJ,
I'm going to once again repeat the advice in my article (and in my last comment): Talk to an experienced consultant.
I don't give advice over the Internet on installing interior insulation on old brick buildings. The downside -- destroying the building -- is too serious.
Understood :)
Anyone you would recommend in New York City with that type of expertise?
Thank you!
AJ,
Call the experts at Building Science Corporation. Here is the link:
https://buildingscience.com/contact
They are headquartered in Massachusetts, but (a) they travel, and (b) they may be able to recommend someone in NYC.
Hi again Martin,
So we are trying to make the budget work to take your advice and insulate our exterior brick in Brooklyn NY with 2" of spray foam.
The plan is to set our wood studs 1/2" off the brick and foam 2" thick, encapsulating about 1.5" of the wood stud itself in foam as well as 1/2" of foam between stud and brick. This leaves 2" of the wood stud exposed to run electrical through where needed. It also allows us to keep as much width as possible in our narrow rooms as opposed to setting our studs out free and clear of the 2" of foam.
How does that plan sound?
Thank you again for your help.
AJ,
Using 2 inches of closed-cell spray foam (not open-cell spray foam) can work, but only if you have first evaluated the exterior of the building for water management issues, and only if you have evaluated the quality of the bricks, as described in my article.
Yes bricks and water management have been evaluated.
Does that layout sound right though-- outdoors//3 wythes of bricks//2" closed cell foam with wood stud 1/2" off brick, allowing for 1/2" continuous behind studs.
Or is is necessary to leave more than 1/2" between brick and stud?
We're just trying to keep as much room width as possible in a narrow set of rooms.
AJ,
Q. "Does that layout sound right, though -- outdoors // 3 wythes of bricks // 2 inches closed-cell foam with wood stud 1/2 inch off brick, allowing for 1/2 inch continuous behind studs?"
A. That will work, as long as the spray foam contractor is conscientious about getting the spray foam behind the studs. Of course, either 3/4 inch or 1 inch would be a little better -- with more margin of safety for installation errors.
Hi, I have been researching and reading about this subject from multiple articles.
Here is our specific condition:
1-we are renovating a portion of an existing multi-bay service garage into an apartment.
(2) parallel walls / front and rear are cmu and need to be insulated. The other two walls will divide the overall garage form storage areas (unconditioned) from the conditioned apartment space.
2-the garage is in NJ and is built with a single wythe 8" cmu wall with single span roof wood beams inbeded into the top of the wall (building is single story) - cmu is unfinished / un-painted on both the exterior and interior and is generally in good condition.
3-as part of the renovation we need to insulate the (2) exterior walls with r-21 to meet code.
4-a new wood 2x4 wall have been built on the inside of the existing cmu wall for insulation and electrical - project has not yet been insulated - hence my question / research. There is a 1 1/2" airspace between studs and inside face of the cmu wall - someone previously installed 1 1/2" thick wood furing on the interior face of the cmu - they have not been removed.
5- we have learned that our original plan to insulate with r-21 batt insulation is not a good idea.
questions:
1- We now plan to insulate with closed cell spray foam directly onto the cmu wall.
we have read that the spray foam / insulation on the interior should be of highest permeability possible - is this true? - the recommendation is for 2" ( or i am figuring the amount required for the insulation to act as a vapor barrier)
- should we be only spraying the min. amount possible to achieve the vapor barrier and maintain the highest permeablilty possible? or is it ok to increase the amount of spray foam so that we achieve the r-21 with only spray foam - this would be our preferred method.
(The spray foam would be installed directly onto the cmu wall into the 1 1/2" gap between cmu and stud wall and into the bays of the wood stud wall)
The alternative would be to install 2" of spray foam and achieve the balance of the r-value with unfaced batt insulation. Is this recommended ?
2- do the furring strips attached to the wall need to be removed - they are not pressure treated - the GC does not want to remove them although I think they should be?
3- The wood roof beams going into the cmu wall - based on our conditions do we need to do anything. We do have the new 2x4 wall that would act as a bearing wall if the ends of the beams did see any rotting.
4- Should we be doing anything to the exterior surface of the cmu wall - the GC has recommended that the exterior should be painted - I am not so sure?
Thank you in advance.
John,
CMUs are not as susceptible to freeze/thaw damage as bricks.
1. Closed-cell spray foam is preferable to open-cell spray foam in this application. The spray foam layer doesn't have to be vapor-permeable, because CMUs can easily dry toward the exterior. In any case, CMUs aren't (generally) damaged by moisture.
2. You need to strive to meet or exceed minimum R-value requirements for walls in your climate zone. If you're in New Jersey, you are in Zone 4 or 5. You should aim for R-20 or better -- meaning a minimum of 3 inches of closed-cell spray foam. Or, as you suggested, you can go with the flash-and-batt approach -- 2 inches of closed-cell spray foam plus fiberglass batts.
3. Leaving the furring strips where they are is OK.
4. You can paint the exterior if you want. That will improve the appearance of the building and reduce the amount of rain absorbed by the CMUs, so it's probably a good idea.
Hello,
This was a great article and I believe it addressed some of my questions. However, I'm wondering if I could get some additional information. I live in Derry, PA.....about 35 miles east of Pittsburgh. Based on a bit of research at my local historical society, I believe my home was built sometime between 1820-1840.....Though I am still in the process of confirming the exact date. The 2 story house is constructed on what appears to be a large piece of shale stone (So I believe that is my footer). The foundation is hand chiseled sandstone and the home is a double brick construction (Common Bond Masonry I believe). From what I read, the bricks were hand fired somewhere on the property, and the mortar was lime based. (It is very soft, much softer than a typical portland cement). The house contains no insulation. The interior brick walls are coated with plaster directly on the brick and painted with a latex based paint. Overall the bricks are in good condition. There is no spalling or crumbling damage. The exterior needs some pointing in a few places, but overall, there are no major issues.
My questions are: Can I insulate the interior with rigid foam board without damaging the exterior bricks and causing interior moisture issues. If so, how would I do that? I am open to having a consultant come look at my home. Do you have any recommendations as to whom I can contact in the Pittsburgh area to perform an assessment? I resolved all of my water and moisture issues in the basement and will be putting on a new metal standing seam roof this summer. Along with that, I will be insulating the attic. I am trying to make my home a bit more energy efficient and warmer in the winter time. I appreciate any information you can provide. Thanks again.
Pat
Pat,
Q. "Can I insulate the interior with rigid foam board without damaging the exterior bricks and causing interior moisture issues?"
A. No. As my article noted, the only two safe approaches (if you want to insulate on the interior) are (a) no insulation, or (b) closed-cell spray foam if approved by a consultant.
Q. "I am open to having a consultant come look at my home. Do you have any recommendations as to whom I can contact in the Pittsburgh area to perform an assessment?"
A. Contact Building Science Corporation in Westford, Mass. (978-589-5100). They will either help your or refer you to someone who can help.
Hi Martin,
The Dept of Energy put out a whole report and guide to insulating brick with rigid foam here:
https://www1.eere.energy.gov/buildings/publications/pdfs/building_america/measure_guide_rigid_foam.pdf
I assume you disagree but was wondering what is your opinion of their report?
Thanks for your thoughts.
Hi abcc,
I have an old home built in 1900, I'm renovating my kitchen and found zero insulation. So I was going to do as everyone does, frame, batts, vapour barrier and drywall.
I feel this technique is simply so ingrained in our mentality we wouldn't think twice about doing it. I did a whole host of researching around this topic as to give me home the best treatment it deserves since its far older than me and will probably be standing well past my death.
I returned the insulation based on information here and in the links to the meeting Martin attended. The conclusion I came up with is just not to insulate, the building has been doing just fine for 118 years without insulation. I did however apply some gap filler foam to any holes in the mortar to prevent drafts.
You should also evaluate why you are insulating the first place, typically its simply to reduce energy costs. Most of the conclusions I have found point towards other envelope issues that produce a bigger "bang for your buck" like upgrading windows, doors or a more efficient furnace as examples.
As for rigid insulation, I suppose this could work but it is still removing warm air from the interior layer. On top of that rigid insulation in general sucks because it doesn't prevent drafts(gaps between panels, the base and the top edges) which is the bigger culprit with heating.
Edit: I guess I should also add that I evaluated spray foam but was hesitant because I would permanently alter the building envelope and simply didn't want to risk that. The best solution would be to clad the outside in siding to prevent moisture from getting to the brick in the first place but alas the brick is a nicer look than siding (IMO).
ABCC,
The DOE report you linked to is valuable. It lists several caveats to anyone who is considering insulating a brick wall on the interior with rigid foam, including (a) the need to manage exterior bulk water to limit brick wetting, and (b) the fact that this technique can only be used when the interior brick surface is smooth, not lumpy, and (c) the importance of ensuring that the rigid foam is installed in an airtight manner -- a point that is particularly difficult when one is faced with partition intersections and floor joists. In short, it's tough to do well -- and even the DOE report notes that when "closed-cell polyurethane foam is sprayed directly on to the brick masonry," that approach is "the most effective, though costly, method for insulating the interior of brick walls. "
Really informative article. Thanks for writing it! Also, impressive effort responding to comments over the years.
I'm in the midst of a historic renovation of a 3 story mixed-use brick building in Centre County, Pennsyvlvania.
In one section of the building I've already erected 2x4 framing over the existing plaster. I was going to use blown-in insulation but will most likely change course. I read in the comments that you advise first removing plaster and lath before applying closed-cell insulation. Could spray foam be successfully applied directly to the original plaster wall?
Also, how critical is it to apply the closed-cell foam behind the studs? Some of the framing, as it currently is, is in direct contact with the plaster wall. Should I redo the framing to allow for a gap or will leaving the framing as is suffice?
Thanks again for all of the high-quality content you create!
Eric
Eric,
Q. "I read in the comments that you advise first removing plaster and lath before applying closed-cell insulation. Could spray foam be successfully applied directly to the original plaster wall?"
A. No. You don't want to leave an air gap between interior insulation and the brick wall. If there is such an air gap, you run the risk of allowing warm, humid interior air to contact the cold bricks. If that happens, you'll end up with condensation on the interior of the bricks, increasing the risk of (a) interior puddles, and (b) freeze/thaw damage to the bricks.
Q. "How critical is it to apply the closed-cell foam behind the studs? Some of the framing, as it currently is, is in direct contact with the plaster wall. [I think you meant to write "brick wall."] Should I redo the framing to allow for a gap or will leaving the framing as is suffice?"
A. If the studs are touching the brick wall, you should remove the studs and re-frame the wall with an air gap that allows you to install spray foam between the framing and the bricks. Again, you want to avoid the possibility of hidden air pathways that allow moisture accumulation. Remember, the downside to doing it wrong is freeze/thaw damage that destroys your building.
Remember that you need to be sure that the studs aren't structural before you remove any studs. It can sometimes be hard to tell, when examining an old building, whether you're looking at a multi-wythe brick wall that is structural or a wood-framed wall faced with brick veneer.
I have a single story duplex in Klamath County Oregon, it is single wythe structural brick, the eaves are protrude out far enough that the bricks almost never get wet. Whoever built the building back in the 1960's directly attached 2x4s turned on their side (so 1.5" furring out from the wall) to the brick then insulated with fiberglass with aluminium facing between the 2x4s. Then drywall over top of the 2x4s. I've noticed mold and moisture damaged drywall issues all over the place, and after reading this article it seems like that was the worst decision they could have made. Would it be safe to just remove the insulation and put drywall back over the 2x4s?
Thanks you,
J.H.,
If you remove the insulation, you will probably reduce the chance of condensation and mold, because the interior surface of the bricks will be warmer.
Mind you, the energy use consequences of simply removing the R5-ish fiberglass insulation would be pretty significant in Klamath county. Installing an inch of HFO blown closed cell foam would put an air tight vapor retarder and R7-ish insulation where the fiberglass once stood, with no mold risk to the drywall.
An inch of closed cell foam between 2x4 furring would still be well below IRC code min in zone 4C Klamath County OR, but way higher performance than uninsulated brick. Installing 3.5" of EPS on the exterior of the brick would meet code with the fiberglass stripped out, 2.5" of exterior EPS would meet code performance if the 1.5" of fiberglass & drywall was left in place, which would also warm up the interior face of the brick.
Martin, Thank you for your quick reply and for still being here 8 years after your original article!
That's what I was thinking, I've been trying to read up on this subject and had a real tough time finding any information on relevant to my specific situation. It seems like the best solution would be to insulate the building from the outside, from the inside is a crap shoot, and they made some pretty bad decisions when they built this place. My plan is to remove exterior wall fiberglass insulation, replace the old windows, put in a bigger bathroom fan, and ask the tenants to run a dehumidifier. Hopefully replacing the old drafty windows and doors will be a decent trade off for removing the insulation energy wise.
>"Hopefully replacing the old drafty windows and doors will be a decent trade off for removing the insulation "
It's not even close! Reducing the wall performance by about 75-80% can't be made up for by improving window performance by 2-3x.
The uninsulated house will be hotter in summer, colder/clammier in winter, and you may not even have enough heating source to fully heat the place (though at 1960s era oversizing factors you probably do.)
Unless you're planning on insulating from the exterior some time soon, you're going through the trouble and expense of gutting and replacing the drywall, replacing the shot fiberglass with an inch of closed cell foam at something between $1.00-1.50 per square foot is going to be "worth it".
Dana,
That's a good point, I guess I should just suck it up and put in some spray foam if I'm opening up the walls.
Hello Martin,
Excellent article! The base first principles presented here demistify much confusion about this topic, and given the strengthening retrofit economy, will become more prominent to the building industry in the coming years.
I have one question regarding an answer you gave in February 2019: "You don't want to leave an air gap between interior insulation and the brick wall. If there is such an air gap, you run the risk of allowing warm, humid interior air to contact the cold bricks. If that happens, you'll end up with condensation on the interior of the bricks, increasing the risk of (a) interior puddles, and (b) freeze/thaw damage to the bricks."
The building in my case is located in Toronto, consists of uninsulated 3-wythe brick walls and is being converted to residential. I am looking to use 2" closed-cell spray-foam insulation in steel studs placed along the exterior walls, but I am looking to install two layers of 1/2" mortairvents between the interior surface of the brick wall and the insulation layer. This is to allow reversability and maintenance in the future - removing sprayfoam directly from brick is very difficult.
If drilled air vent / weeper holes are provided at the floor at 16" intervals through the exterior brick wall, do you believe that the equalization of air pressure accross the brick wall and allowance of drainage would be adequate to address any moisture or condensate build-up within this cavity while still allowing enough interior heat to reduce the risk of freeze-thaw damage?
Eric,
I had no idea what "1/2-inch Mortairvents" meant, so I looked it up. It appears that Mortairvent is a brand name for a three-dimensional plastic drainage mat.
If you can be sure that you have a perfect air barrier on the interior side of the Mortairvent, and if you install air vents through the brick to introduce exterior air into the cavity you are about to create, then you will reduce the risk of condensation. But why introduce the risk in the first place? A simple layer of Tyvek or Typar is all you need to assure reversability.
Perhaps this is a bit off point, but it seems at least somewhat relevant. I'm working on two old brick homes with somewhat different issues, so I' explain separately:
Home A - Originally built in the 1880s, it is a three wythe brick 1-1/2 story cottage, it was extended upward to become a 2-1/2 story around 1910. It was renovated around 2000 with the addition of furring strips polyisocyanurate panels and drywall. There have been no interior or exterior issues - I think. However, the exterior brick is very soft and is slowly deteriorating. My question is this - is it advisable to apply a water repellant or sealant to the exterior? Something like silane or siloxane?
Home B - Originally built in the 1880s (more substantial than Home A) of a dark red hard brick - three wythes on the first floor, two on the second. It is about to be renovated. The consultant has recommended 2x4 framing held 1" from the exterior wall and 3"-3.5" of closed-cell foam. My question is the same as with Home A - would you advise coating the exterior of the brick with silane or siloxane?
If yes for either case, would you care to discuss the relative advantages/disadvantages of these two products?
Hi Martin, I have a 1890’s brick two-story duplex in KC my husband & I have been renovating over the last couple years. We have successfully tuckpointed the front of the building. The sides & back we would like to insulate the exterior walls. Could we insulate using the methods described in your article using closed-cell spray foam instead of the rigid boards?
Thanks,
Jake
Jake,
Yes, you can. I know of two owner/builders who have done this: Cador Price-Jones and Peter Yost. You can read about their projects in these two articles:
Cador Price-Jones project: "Brand New Appearance and Performance for An Older Duplex"
Peter Yost project: "Deep Energy Makeover: One Step At A Time"
In both of these projects, contractors retrofitted a layer of closed-cell spray foam on the exterior side of the existing walls. (See photos below; click on a photo to enlarge it.) If you go this route, you'll need to install vertical furring strips or studs, using some type of stand-offs, to the existing wall before the spray foam is installed. These furring strips or studs are used to make it possible to install the new siding.
Incredible! Would we need to seal the brick or install some sort of moisture barrier prior to installing the furring strips and spray foam or could we simply spray foam onto the brick directly?
Jake,
Closed-cell spray foam is a vapor barrier, air barrier, and water barrier. You can spray the foam directly against the bricks. But you need to carefully consider the window and flashing details (as well as the siding attachment details) before you undertake this type of project.
“[Deleted]”
Dan,
I don't think this article is relevant. The article discusses brick buildings with multi-wythe load-bearing brick walls. Unless I misunderstand you, you have a wood-framed building with brick veneer.
You description of the basement walls is unclear. I don't know, for example, what you mean by "the exterior of the wood framing" and the "interior framing." Are these studs? Perhaps you can describe the layers of your basement walls, from the outside to the inside (or vice versa if you prefer).
“[Deleted]”
“[Deleted]”
Dan,
I have rotated your photo and posted it below.
I think you have a wood-framed house with brick veneer that lacks adequate flashing at the base of the brick veneer, and also lacks an adequate water-resistive barrier (WRB). These are tough problems to solve, although a skilled mason could perform some of the necessary fixes. The fact that your house has already suffered moisture entry problems and rot is not encouraging.
Here is a link to a relevant article: "Flashing Brick Veneer."
Good luck -- addressing these issues won't be cheap.
“[Deleted]”
Hi Martin,
Thanks for the article. I've spent an enormous amount of time looking for information on proper practices of insulating an old brick building.
After reading your article I believe my best option is to leave the exteriors walls un-insulated.
I would like to share my current project with you and see if you agree with me.
My wife and I purchased a 1910 brick 2 - flat in the city of Chicago 2 years ago.
Our first maintenance investment was partial tuckpointing on the upper front face of the building.
We had a leak that was forming whenever it rained near a window and the exterior tuckpointing fixed the problem.
2 years later we are working on remodeling the top unit and decided to remove the plaster walls and replace them with drywall ( the plaster was in terrible condition).
We're working one room at a time and the pictures attached are what we discovered above our ceiling at the exterior wall.
It appears all of the mortar eroded. The pictures also include the walls below the ceiling which are not in the worst of shape.
I took a sample of the mortar to our local masonry supplier and they determined it was a lime mortar.
I used the lime mortar they had available to repair the section above the ceiling.
I would love to add cellulose spray foam in the wall cavity's but it's too expensive for our budget, and secondly I'm concerned that any insulating may cause additional brick deterioration.
Any comments or suggestions would be greatly appreciated.
Thanks
Dan W
Here's a picture of the tuckpointing I had done above the ceiling.
-Dan W
Dan,
I'm not an expert in brick restoration or old lime mortars, so I don't have any comments. Good luck with your project.
Thanks Martin.
I was just curious of your opinion regarding insulating my brick building based on the condition of the interior brick.
After reading your article, I think I'm going to leave it as is without insulation.
Thanks again,
Dan W
We've purchased an 1837 built (front 2/3rds) former schoolhouse and Grange (back 1/3rd added 1936) in the Federal style. It is a two story, structural brick building. Interior is lathe and plaster with about a 1 inch air gap from the brick. The roof has about a one foot overhang.
The brick is in remarkably good shape in both the original section and the addition.
As we are planning to use this as a residence, the change of use from assembly hall requires bringing it up to code. Insulation is a part of that.
As it is an historic building, we do not want to do exterior insulation.
We are looking for an expert to test the brick and recommend a best course of action.
The building is in Worcester county in Massachusetts.
Clavallie,
Contact the Building Science Corporation -- a company with knowledgeable consultants who understand old brick.
Building Science Corporation
70 Main St.
Westford, MA 01886
978-589-5100
http://www.buildingscience.com
I'm in a 1950's solid brick house in Toronto - double whythe walls - brick exterior and concrete block interior. Interior side of the concrete blocks is parged (?)...and then this silver backing tacked on (tar paper?) - joints are not taped. Joists are pocketed into the concrete block.
Plaster was in poor condition (age, not moisture), so tore it all down and was planning to insulate with (contractor recommended) closed cell spray foam and then drywall - but after reading this article and several others, I'm now leaning towards leaving it uninsulated due to the moisture issue.
Plan is to install wood framed walls and then drywall over it. With closed cell foam I wouldn't need a vapour barrier, but if I leave it uninsulated, do I? I'm also seeing advice to NOT use polyethylene vapour barrier under the drywall either on a solid brick exterior wall?
What is the purpose of this tar paper? I think it prudent to take down the tar paper (?) to inspect and repair damage to the cement blocks, cracks, etc. Would I then use something like Tyvek (or Home Slicker with Typar to maintain an air gap against the parging) to replace it? (or do I even need to replace it - I haven't even seen it on other photos of brick walls?)
Final question - in a couple of areas under windows where I have forced air registers, the paint has continually peeled off - it could be due to water infiltration from the windows (now replaced), but had thought it was may be from the air blowing on the wall leading to some sort of moisture issue in that particular area. The plaster wasn't soft or anything - just peeling paint.
Thanks.,
Tim,
Bricks and concrete block are often dampened by rain, so the foil or asphalt felt layer -- whatever it is -- was installed as a type of water-resistive barrier (WRB) to separate the damp masonry from the interior materials. The presence of this product makes sense. If your remove it, you should substitute something else -- asphalt felt or housewrap would probably work.
I can't diagnose your peeling paint problem without a site visit. It could be water entry, or there could be another cause. Figuring out what's going on is detective work. Ask questions and make observations. Is the paint peeling on the ground floor or the upper floor? How wide is your roof overhang? Do the bricks look wet after a hard rain? Where are the bricks most wet? Do the windows have good sills that drip clear of the bricks? And so on.
Thank you.
With respect to using asphalt felt or housewrap to replace what is there, should it be "tight" to the irregular surface of the masonry or would a wrap with built in plastic mesh to give a 1/2" air gap against the masonry be better?
I presume I should NOT use polyethylene vapour barrier anywhere (i.e. under the drywall)?
Tim,
I'm not sure whether the built-in plastic mesh would be worth the added expense -- after all, the masonry is rough, and there will inevitably be gaps between the WRB and the masonry.
If the building will be air-conditioned, you don't want an interior polyethylene vapor barrier. But you do want to pay attention to airtightness.
Hello Martin,
We have a 1909 brick two-flat in Chicago that was converted into a single family home in the 90s by the previous owner. I believe the structure has 3 wythes. The masonry is in good condition now, but that is after a moderate tuckpointing project last year. Small parts of the parapet walls required attention as part of that
We are doing a major home renovation this summer. Insulation was not originally part of the scope of the project, but our GC noted upon drywall demolition that there are only 2 layers of 3/4" insulation and that it is of very poor quality. He said that for all intents and purposes, we do not have insulation. He said that one possibility is to move the walls in to allow for 4" of high-quality insulation, as would be done on a new construction home. But our house is not new construction and I am not sure he has a lot of experience with turn-of-the-century brick structures.
We do not love his solution for several reasons (loss of interior space, effect on window jamb lengths for windows already ordered, costs, and concerns about freeze/thaw issues that I have seen in your article).
We are not interested in exterior insulation for aesthetic reasons.
Do you think that altering the current insulation system makes sense?
Could removing the existing insulation and replacing it with higher quality spray foam insulation makes sense as a middle ground?
Best regards and thank you,
Daniel
Daniel,
Q. "Do you think that altering the current insulation system makes sense?"
A. You haven't provided enough information for us to answer that question. All you told us was "there are only 2 layers of 3/4 inch insulation and that it is of very poor quality." You didn't tell us what type of insulation -- whether rigid foam, mineral wool, or something else. Obviously, if the insulation is poor quality, that's not desirable -- but we don't know what that means. Is it poorly installed? Deteriorated? Mouse-infested? Or something else?
Q. "Could removing the existing insulation and replacing it with higher quality spray foam insulation makes sense as a middle ground?"
A. Perhaps, but you have to evaluate the quality of the bricks and the exposure of the bricks to exterior water before you decide whether you can do that -- as explained in my article.
Hello Martin,
I was incorrect in parts of what I said above. We have one layer of rigid foam insulation with an r-value of 5.6. My architect just informed me that Chicago code requires a minimum r-value of 17 for our mass brick structure. It seems as if there is no way around removing what is currently there, installing 2x4's and spraying closed-cell spray foam insulation directly on the interior brick to achieve this r-rating.
Would you say that is correct, along with trying to manage the amount of water that hits our masonry walls?
Also, this is just for the majority of our first floor that is getting opened up as part of this project. The rest of the house (basement, second floor, and parts of the first floor) would remain as is. Any risks with uneven insulation among different parts of the house?
TL:DR - do partially cast-in joists have the same risks and issues that are highlighted in the "embedded beams and joists" section?
I have a 2-story solid brick house with a finished half-story attic (knee walls). It's a poured concrete foundation with partially cast-in floor joists. Since they're only partially cast-in, there is a void between the foundation and the floor. I was considering caulking around the joist, spraying expansion foam (not insulation) into the void, and attaching 2" of EPS to foundation wall (from the floor to the top of the foundation - the void would be air sealed but not insulated). I wouldn't do anything to the concrete floor.
Three questions:
1. Do partially cast-in joists carry the same risk of rot as full cast-in joists?
2. From an energy efficiency standpoint, would the setup significantly increase the temperature of the basement or r would the uninsulated void and floor make the insulation ineffective?
3. Would attaching a 2x4 stud wall with mineral wool batts to the EPS change your answers to #1 or 2?
Andrew,
1. This is another of those " it depends" answers. How much moisture the joists take on from the surrounding concrete, and how much rot results from that are very site specific. In some climates and in some situations the joists will be fine, even in very old buildings.
2 and 3. If the joists have survived without incurring any damage, that is probably due to two things: That air was able to circulate around them allowing them to dry, and that the lack of insulation kept them and the concrete foundation wall warm, also aiding drying. The dilemma you face is whether by insulating and sealing you upset this equilibrium and allow the conditions (cold and damp) that will cause the ends of the joists to start rotting.
Unfortunately, while I feel fairly confident describing the issues in play, I'm not at all sure what to recommend as a solution. Maybe others who have dealt with this can weigh in.
As additional context, I'm near Toronto and the foundation and joists seem to be in good condition.
Thanks for this article, Martin. Having recently bought our first home, a 97 year old brick bungalow in Toronto, I have been devouring as much information as I can on retrofit options. This article is among the most useful I have found.
I’m wondering if there’s any change in your advice when it comes to brick foundation walls. For the above-grade parts, I imagine the same advice applies, but our brick walls extend below grade as well. With proper exterior waterproofing, can these also be spray foamed from the inside? Or is there a better approach?
Property setbacks and a driveway that is just barely wide enough to fit our car make exterior foundation insulation problematic for us.
Kamal,
For information on insulating a basement, I suggest you read these articles:
"Dealing with Basement Water from the Inside"
"Three Ways to Insulate a Basement Wall"
I'm not in favor of covering the exterior side of bricks with waterproofing compound. It's better to allow the brick walls to dry to the exterior. Using closed-cell spray foam to insulate the interior side of a brick basement wall makes sense.
Thanks. However, I’m unsure what drying to the outside would look like below grade. Wouldn’t the bricks absorb water from the soil, and if closed-cell spray foam prevented drying to the air in the basement, they would simply stay wet?
Kamal,
I was thinking of the above-grade portion of your brick foundation wall. You're right that the below-grade portion can (and should) be waterproofed on the exterior, if you have access to the below-grade portion of the wall.
I forgot to say thank you for the replies! Very helpful.
Thank you Martin and team for your hard work. GBA has been a life saver.
I am in a 110 year old brick home in Toronto Canada.
There is no room on the side to do any external insulation (property line and walkway for neighbours).
Inside is lath and plaster, and given the configuration of the home (stairs), it would be very difficult to insulate from the inside.
One option that has been proposed is using Airkrete to fill from inside and outside (holes in brick and holes in plaster), 1 inch on each side. Giving roughly R8 (realistically R6). This product has good reviews by folks who have done it in Toronto from a value perspective.
Given this is the only realistic option, and given the R value is low enough that some heat will get to the bricks, any concerns or considerations? Or am I better off just leaving things as is?
The brick overall is in good shape, except for the parapets and unheated portion of the attic. I have redone the parapets due to deteriorating bricks (flashed them with metal, the constant exposure to snow/ice without heat is a problem) and will add siding to the portion that is a part of the unheated attic.
The remaining brick that is a part of the envelope is in very good shape.
I have already insulated the roof (attic and flat both outside and inside thanks to GBA), windows and air sealed elsewhere.
Your perspective on this option or any alternatives would be much appreciated.
Hesmasi,
I don't have any experience with Air Krete, which has a mixed reputation. The product is usually injected into voids in walls.
1. Does your wall have voids?
2. Perhaps the voids you are thinking about are between the laths? Please describe the depth and location of these voids.
3. You wrote "1 inch on each side" -- presumably, you mean on each side of the brick wall. What does this mean?
Thanks for the response.
1. Yes it has voids.
2. Two voids:
A. Between the double brick wall (this gets accessed from the outside by injecting through mortars)
B. Between the lath and the brick (space created by studs)
3. Yes 1" between the two brick walls, and 1" between the Lath and Brick wall (inside).
Installer: https://www.brandinsulation.com/walls/
More detailed view: https://www.youtube.com/watch?v=KLo8MXRpsdQ
Hesmasi,
I don't have enough experience with Air Krete to answer your question. But filling an existing void will definitely change the moisture transfer performance of your old brick walls. Wind-driven rain, for example, might conceivably travel farther into the wall (to the inner wythe) if the void is filled. This is speculation on my part, however.
Your suggested insulation method is not an approach recommended by experts.
Thanks for your response.
It's challenging insulating these old structures while not impacting the bricks performance. Especially when I don't have room on the outside.
Why do you say the rain travels farther into the wall? Is it because it's not drying as quickly due to the insulation? or lack of air pocket (which is now filled with air krete)?
we're insulating a century building that has double brick with air gap. Location is Toronto (zone 5 going on 4). Even though the interior brick would presumably be dry, my client had the interior bricks tested to ensure they weren't susceptible to freeze/thaw damage. I prefer to design walls so that they can dry out, meaning that any vapour that enters on the inside can freely escape on the outside and vice versa. For this reason, I am considering open cell spray foam (ocSPF) up against the brick. We'll provide 4" of foam to ensure a good air barrier. My thought is that, without moisture transmission via air leakage, the moisture that does travel through to the brick will not be sufficient to create a condensation issue. Plus, the intimate contact of foam to brick would presumably prevent condensate from forming, or at least trap it until it can dry. With the above considerations, is ocSPF still an ill-advised strategy?
Rob,
I stand by the advice provided in my article. You don't want to use open-cell spray foam, since open-cell spray foam allows moisture to move from the warm interior to the cold bricks via vapor diffusion. Adding moisture to the bricks in the winter raises the risk of freeze/thaw damage to the bricks.
If your consultant determines that your bricks are dense enough to allow for some interior insulation, your best choice for interior insulation is closed-cell spray foam. This type of spray foam does a much better job of stopping vapor flow from the warm interior to the cold bricks.
Hi Martin,
Thanks for all of the helpful information. After reading your article and many of the responses, I am curious:
When using closed cell insulation directly on old double wythe masonry, wouldn't vapor still be trapped inside the brick and be susceptible to freeze/ thaw since the center of the warm side of the wall will still be closest to the interior?
Lodsn,
The purpose of the closed-cell foam is to prevent outward vapor drive during the winter. You don't want interior moisture (the moisture contained in the warm interior air) to accumulate in the cold brickwork over the winter. Closed-cell foam is a vapor barrier -- the foam prevents the outward vapor drive. (Note that when the brick wall is uninsulated, the bricks aren't particularly cold in winter -- they are warm. Uninsulated brick walls have bricks that are generally warm enough to limit moisture accumulation in the bricks from outward vapor drive.)
All brick walls are exposed to a certain amount of wind-driven rain. As long as the bricks aren't painted, this type of moisture usually evaporates harmlessly to the exterior during dry weather or warm weather.
If an old brick building has uninsulated walls, the bricks stay warm -- and warm bricks are dryer that cold bricks. The bricks are more at risk if they stay cold all year, so interior insulation must be approached cautiously.
Log in or become a member to post a comment.
Sign up Log in