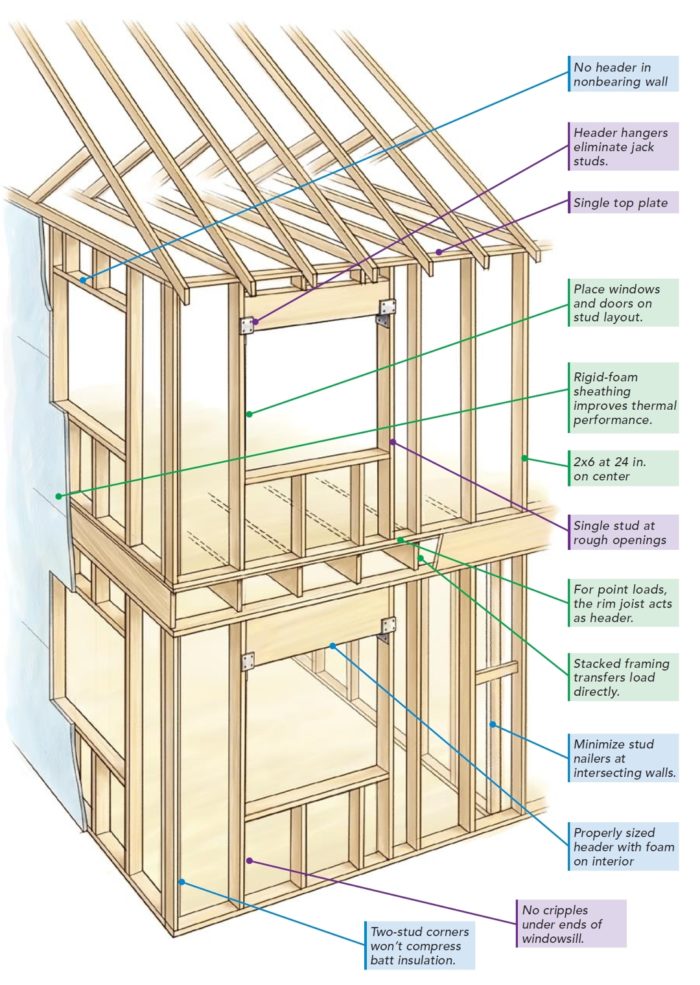
Image Credit: Fine Homebuilding
Advanced framing, also called optimum value engineering (OVE), is a framing system that aims to pare the amount of lumber used to frame buildings to the bare minimum. Advanced framing was developed in the 1960s by the Department of Housing and Urban Development as a way for builders to reduce costs.
In recent years, the decades-old framing system has been adopted by many green builders. These new advanced framing devotees are focused less on the cost-cutting aspects of the framing system than on its other virtues, including energy and materials savings.
How advanced framing saves lumber
If you want to adopt every principle of advanced framing, here’s what you need to do:
- Design your house with dimensions that fit a 2-ft. module.
- Switch from 16-in.-on-center framing to 24-in.-on-center framing for joists, studs, and rafters.
- Stack the wall, floor, and roof framing so that rafters, studs, and joists all line up.
- Switch from double top plates to single top plates joined with steel strapping or splice plates.
- Get rid of jack studs; instead, support headers with steel clips (Simpson HH header hangers).
- Omit headers on gable walls and other non-loadbearing walls, and make sure headers are right-sized.
- Switch from three-stud corners to two-stud corners with drywall clips.
- Use ladder blocking at partition intersections.
- In some cases, omit structural wall sheathing and substitute T-profile diagonal steel bracing.
Will your local code official balk?
Even though optimum value engineering has been around for decades, that doesn’t mean your local code official won’t raise his eyebrows. As one advanced framing guide puts it, these details “are likely to inspire questions from the building official.” So it’s best to discuss your plans with your local officials before you begin framing.
The International Residential Code (IRC) now recognizes some, but…
Weekly Newsletter
Get building science and energy efficiency advice, plus special offers, in your inbox.
This article is only available to GBA Prime Members
Sign up for a free trial and get instant access to this article as well as GBA’s complete library of premium articles and construction details.
Start Free TrialAlready a member? Log in
11 Comments
Good summary.
But I'd question #3 of your 'benefits' bullet points. Environmental priorities have changed since the 1970's. There's a good environmental case for using MORE lumber in construction rather than less. Lumber from sustainably managed plantations provides long-term carbon sequestration when used in construction.
OVE and kitchen cabinets
Backing for cabinets is a must with this system.
There are better ways to frame
To eliminate thermal bridging, you could also use interior rigid foam board (and rim joist details) or a Riversong Truss wall, both of which you fail to mention.
And the glossary definition of double stud wall is quite misleading: "Construction system in which two layers of studs are used to provide a thicker-than-normal wall system." It's not two layers of studs but two independent walls or two walls sharing common plates.
Also, the illustration of bracing options shows (correctly) that K-bracing against a window won't work with Advanced Framing, as it requires a stiffer window post to transfer the loads.
Few builders, including those most concerned about resource efficiency, ever adopted the OVE system because it does not make as strong a frame, it saves very little wood or labor, and it makes finishing details much more problematic.
I tried some of these techniques in the 80's, but soon enough discovered a far superior framing system which was a modification of the Larsen Truss, and is now known as the Riversong Truss - a framing system which allows almost unlimited thermal insulation with almost no thermal bridging and - depending on how it's braced and whether it's sheathed - can require no more lumber than a conventionally-framed house.
Riversong Truss
and here
Another Advantage
"Because the thermal benefits of advanced framing are relatively minor"
While this may be true comparing a standard 2x4 wall to a 2x4 wall with advanced framing techniques; we have found that by incorporating some advanced framing techniques it allows us to upgrade our wall from a 2x4 @ 16"OC to a 2x6 @ 24"OC without much of a cost upgrade allowing us to increase the amount of insulation in the wall cavity. When looking at it this way, the thermal benefits are a bit more compelling.
Still not sold on the single top plate though - have an architect down here that insist on it - seems like a lot of work for not much benefit and not worth the loss of structural integrity especially if you have a thermal break with exterior foam anyway.
As always - nice article and good summary.
Hurrricane style OVE
We've done a few adaptations here for hurricane issues (those darn flying trees)
1- push the headers up to the (double) top plates and cripple down to the window head so the trees hit the header at the ceiling level hopefully stopping at the top plate and keeping most of the water out of the house
2- structural sheathing stops 8' down from the top plate on 9' walls and 1/2" PT ply or OSB runs down to the mud sill, tying the mud sill to the studs and spans the rim joist tying the upper top plate of the first floor to the second floor studs, helping keep the plates on the floors during heavy wind loads. (They can be sucked off the floor on the downwind side of the home during a hurricane.)
3- solid block w/ 2X stock on the exterior of the upper top plate between the rafters stacked on the sheathing to help distribute the impact of trees to the sheathing and encouraging the rafter tails to break at the plate to help keep water out of the house after a tree strike.
4- block the ridge solid between the trusses, If vented just hold the blocking down on either side as shown in the attached drawing for the ridge vent, if spray foam, block solid and tie both planes of roof sheathing together at the peak.
5- not related to falling trees, but rather than using header clips on first floor move the header to the rim joist and cripple over the windows and doors.
6- use attached (pencil) framing compilation drawing as gift wrap for shelter nerd friends.
2x6 Advanced Framing
I agree with Danny Kelly. Using some of the advance framing techniques with 2x6 allows for increased insulation in the wall and helps meet the energy code. I would have thouht the article would have dealt with 2x6 since it is the most common stud size used in advanced framing.
The author might want to mention that there are code limitations on 2x4 advanced framing. IRC Table R602.3(5) limits two-by-four advance framing to supporting a ceiling/roof assembly only (no second story) .
The IRC also limits let-in bracing to 16" on center stud spacing (Table R602.10.2). Check the catalogue regarding the suggestion to replace structural sheathing with "t-profile diagonal steel bracing". Last I checked, Simpson metal t-bracing was also limited to 16" on center framing.
Response to Tom Kositzky
Tom,
Thanks very much for the further information on code requirements; much appreciated.
Of course, 2x6 wall framing allows more insulation than 2x4 wall framing. Where I live in Vermont, 2x6 studs have been standard for 30 years, so I sometimes forget that some framers still use 2x4 studs.
In any case, many framers use 2x6 studs without adopting Advanced Framing methods.
The idea that less is more has worked for me.
I too have evolved my own style of framing to achieve higher whole R values via my framing techniques.
The way I see it, is 5% savings times multiple changes adds up. Passive House standards are 90% better than code which just means they did 18 5% improvements possibly. Doable for all of us someday soon.
Lipstick on a Pig
It's great to see stick framers finally stepping into the 21st century and get on board with making a serious attempt to build energy efficient structures but trying to adapt outdated building method isn't anything different that putting lipstick on a pig and comes at a significantly higher cost than building with modern systems that achieve energy efficiency at a lesser expense and in a much shorter period of time.
Structural Insulated Panels have come of their time and can give builders a wood frame system with a short learning curve that is far cheaper to build with than Advanced Framing.
Jim Crowley - E-Building Systems
advanced framing etc
As a new residential sustainable designer I have researched and studied advanced framing. A great site to look at is http://www.buildingscience.com. The site is very informative. 24 oc. framing has been around for 100's of years under different names. I for one believe in trying new techniques. Everything has a price. Double walls are a huge upfront expense and a waste lumber and other materials.
The majority of builders can continue to build their cookie cutter style colonials where all the windows face North because that is the front of the house: Waste materials so they can have their super insulated houses that are full of toxins which compromise the health of the inhabitants. All for what?
I for one will never follow their train of thought. Working with people who have a passion for sustainability (not just energy efficiency) is key. It all comes down to designing a home around solar gain and the site. Followed by using innovative materials and construction methods that are sustainable and non toxic.
Healthy Living Starts at Home...Naturally
Response to Maria Hars
Maria,
Although you wrote, "24 oc. framing has been around for 100's of years under different names," the use of balloon framing with small timbers was rare until the 1880s -- although some say a decade or two earlier, beginning in Chicago. Before that time, timber framing predominated.
If I take your suggestion of "hundreds of years" literally -- perhaps 200 years? -- then you imply that builders in 1811 were framing with skinny studs spaced 24 inches on center. Few historians would agree with you.
Log in or become a member to post a comment.
Sign up Log in