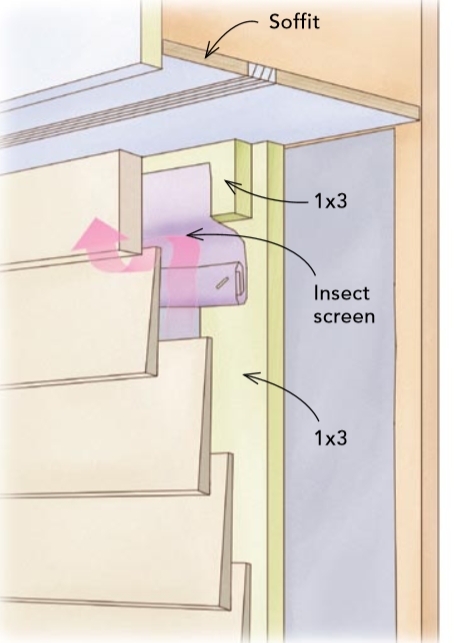
A vented rainscreen — an air gap behind the siding — has become a standard detail in many new houses. It helps remove moisture that works its way through the siding, and in the process helps siding last longer. It’s the “vented” part of this equation that has Gerald Pehl thinking.
“I’ve got an assembly design for a vented rainscreen, and it will be held continuous to the soffit spaces, which then vent through to the attic ridge vent via conventional vent chutes between the rafters,” Pehl says in a comment posted in the Q&A forum at GBA.
His question, and the start of this Q&A Spotlight, is whether this plan eliminates the need for additional soffit venting. Pehl’s building inspector has left the decision up to him.
Risks in the event of a fire
Malcolm Taylor suggests that connecting the rainscreen and attic ventilation might increase the drying potential of the wall assembly. He points out, however, that a rainscreen is typically 1/2 inch to 3/4 inch deep, a function of what material is used to create it, and that probably isn’t enough to make up the required area for soffit vents. Even if it did, he adds, that detail raises another issue: What happens in the event of a fire?
“Here in Canada,” Taylor writes, “we can’t connect the two to find out. The code precludes it because it creates a concealed air space from which fire can spread up into the roof assembly. Practically, I wonder how much difference there is from a fire spread point of view between a connected rainscreen, and one which is vented at the top with soffit vents immediately above. I’ll be interested to see what other posters think.”
GBA senior editor Martin Holladay notes fire…
Weekly Newsletter
Get building science and energy efficiency advice, plus special offers, in your inbox.
This article is only available to GBA Prime Members
Sign up for a free trial and get instant access to this article as well as GBA’s complete library of premium articles and construction details.
Start Free TrialAlready a member? Log in
23 Comments
Vented Cavity Depth
One aspect of the cavity depth discussion that often seems overlooked is the necessary depth of solid wood that is required for attachment of a variety of common siding materials. This is specific to when furring is being placed over rigid insulation and not directly over structural sheathing. Many siding materials require 1" embedment of fasteners at 16" o.c.. This also often precludes advanced framing techniques of 24"oc framing as well as the more shallow cavity depth. In summary, if you want a siding warranty, 5/4x wood furring is often required for proper siding attachment thus providing a 1" vented cavity.
I would also be interested to hear comments on the experience of using different types of siding attached to furring strips at 16" o.c. (or other). It seems obvious that stiffer siding is desirable so that the unsupported spans don't flex or be prone to bending with the occasional side loading. Are siding manufacturers who previously assumed attachment directly to sheathing now offering products specifically for the vented cavity installation? Aluminum better than vinyl? Composites even better in this aspect?
User...957,
I'm not aware of any manufacturer that has altered their products for installation on rain-screen furring, or of any problems using vinyl, or the various composites. Most have altered their installation guides to include mounting on furring, with the only noticeable possible impediment being the depth of solid material need to provide purchase for fasteners.
Many manufacturers have a special brochure or instruction manual for installing their products on furring strips.
For example, here are James Hardie's instructions: https://www.jameshardiepros.com/getattachment/f580da6b-a3b5-4962-8548-5671e761034a/19-jh-over-advanced-framing-or-continuous-insulation.pdf
At this point, a manufacturer who doesn't offer clear instructions for installing their products on battens over a rainscreen gap seems like they are falling behind the times.
Many thanks for the feedback and link to installation instructions. I'm in Edmonton and could not find any supplier of perforated J channel, but finally found Coravent SV-5 at Convoy Supply.
Diagram doesn't seem to make sense.
I also notice that the "Rainscreen Vented at Top" doesn't really make any sense. Doesn't the horizontal 1x3 at the top, block any ventilation from happening since the screen is basically wrapping the 1x3?
“[Deleted]”
Response to Jeff Stetter
Jeff,
The siding is fastened to the furring strips. The horizontal 1x3 at the top of the wall is nailed on the exterior side of the furring strips -- not in the same plane, but proud of the furring strips. This horizontal 1x3 brings the horizontal frieze board to a plane that is well proud of the siding -- the horizontal 1x3 packs out the frieze board. The result is a gap between the bottom of the frieze board (probably a 5/4x4 or a 5/4x6) and the siding. This gap is the vent for the top of the rainscreen cavity.
Ice damming concerns
My concern for venting into the soffit would be in a cold snowy climate. I think there is a potential issue for the wall acting as a solar air heater and then sending all that air directly to the underside of the roof. Thus starting a cycle of snow melt and freezing that could lead to ice damming.
I would say this is even a concern with having the soffit intake vent near the wall rain-screen vent if they were separated. I always suggest moving the soffit vent as far away from the wall as possible.
I would be interested to here others opinions.
Even greater separation from
Even greater separation from wall heat would be achieved with vents under the eave shingles (eg, SmartVent) and none in the soffit. This also allows extending some insulation into the overhangs.
https://buildingscience.com/documents/insights/bsi-046-dam-ice-dam
rain screen direct to the attic
I am building a house with a 1.5" rain screen, clad with Hardie Panel (the 4x10 sheets, not lap siding). Before reading this article, I was actually considering having the soffit abut on the siding such that the rain screen basically connects directly to the attic space. I gather this is a stupid idea? I'm in southwest Ontario, moderately cold winters, humid summers but not particularly rainy.
Trevor
Our code here in BC has a section devoted to rain screens which prohibits connecting the two. I don't know if the Ontario code has adopted the same standards. You need to look at the requirements for fire-stops between assemblies in concealed spaces to see if it is allowed.
Response to Trevor Lambert (Comment #6)
Trevor,
Q. "I was actually considering having the soffit abut on the siding such that the rainscreen basically connects directly to the attic space. I gather this is a stupid idea?"
A. The point of this article is to discuss the pros and cons of the approach you mention. GBA readers can consider the arguments of the experts interviewed for the article and can draw their own conclusions.
Personally, I think it makes more sense to vent the rainscreen gap at the top of the wall rather than direct the air into the soffit or the attic. But I think that in the vast majority of cases, connecting the rainscreen gap to the attic doesn't cause any problems.
Lstiburek Ice Dam Warning - Snow Prone Regions
Joe Lstiburek's advice on solar radiation with dark claddings altered the construction methodology in our home. (Figure 9 in the link that Jon R. posted.) Like Trevor above, we knew we were going to utilize Hardie panels with a rain screen assembly.
It's a passive solar SIP home and our original plan was to truncate the roof SIPs at the wall edges. Soffit vents in field built overhangs would have then ventilated the cold roof. Joe's advice changed that direction.
Our wall assembly was built with Cor-A-Vent strips beneath the Hardie panels. Those strips were placed at the future batten locations so as to minimize nail marks. Cor-A-Vent top and bottom provide air flow. (In hindsight I do like the screen detail as shown at the top of this article somewhat better than what we did. It provides less hidden surface area for boring insects to get into the blocking behind the top frieze board.)
Our roof SIPs extend past the wall edges to the gutter line. Our cold roof above was ventilated at fascia edge, more Cor-A-Vent.
Under the category of "it's anecdotal data", here are some south wall temp pictures I captured midday yesterday. It was 82 degrees outside. (They display here bottom to top.)
Sorry to comment on an old
Sorry to comment on an old article, but I have a question that doesn't seem to be addressed by the article. What about venting the rainscreen into the eave if the attic is unvented? There are vents in the soffit but the attic is sealed. Would there be a problem venting the rainscreen into the soffit in this application?
Response to E247
E247,
An unvented attic is like an upside-down wine bottle. If you connect something to the mouth of an upside-down wine bottle, it isn't vented. It's sealed at the top.
If you want the advantages of top-side venting -- namely, air flow and ventilation drying -- you need to vent to the exterior, not to an unvented attic.
I understand that the attic
I understand that the attic is unvented. I was only asking if the vents in the soffit could be used at the top vent for the wall's rainscreen.
For example, if the roof assembly was similar to the picture below where the attic is unvented. If soffit vents were installed and the rainscreen for the wall was vented into the soffit, would there be any issues (so air could enter the bottom of the wall assembly, go into the eave and then exit through the vents in the soffit)
Response to E247
E247,
As long as local codes permit, there is no reason that your rainscreen gap couldn't be vented into the soffit area.
If the soffit is ventilated -- that is, if your soffit material allows air flow -- the air movement through the rainscreen gap would be possible with this approach.
It would be nice if someone point me to section details (that I can't seem to find again in GBA, I've seen it somewhere) of the bottom of the rainscreen assembly with best practices for integrating the WRB, exterior mineral insulation, furring strips, and drip edge above foundation. My question here may already be answered in that discussion as to whether or not a drip edge metal flashing should be shingled in with the WRB, or be placed on top of the furring strips and be a drip edge for the cladding. My initial thought was that the former would conceal the bottom edge of the whole assembly (which includes Cor-A-Vent between furring strips), and channel any water originating from either WRB or rainscreen cavity.
My project on Martha's Vineyard will have two wide sliding door assemblies on the first floor, one 16' wide, the other 12. The height of the rain screen below the doors is only 12". For a variety of detailing issues, I'm finding it difficult to provide a vent gap at the top of this portion of the rainscreeen. From reading this discussion, it sound's like, given the short height of the affected portion of the rainscreen, omitting top venting below the door sill will have a negligible effect on performance. Am I correct?
Hugh,
All residential buildings here in Coastal BC have to include rain-screens. Very few are top-vented, and in what is a quite demanding climate, they seem to work fine without it.
This has been helpful thanks everyone. SwitchgrassFarmer and spaulson, I like the discussion of ice damming and solar gain. Also good point Jeff about fastener embedment.
Here in heating mostly dominant -not too soggy- southern new England, I follow the light on this one and treat facades according to their orientation as I do with coatings on glazing packages and eve shadow lines. East and west faces are more of a summer overheating liability than a winter gain benefit and rainscreen cavities there should be vented at the top and bottom - might as well do the north face the same as the north face has a higher mold liability. The south side should be closed at the top as it stands to benefit more from solar gain in the winter and is less of an overheating liability.
Though I do like the simplicity of the unified roof wall drainage cavity (also for weeping the
secondary water barrier), I am compelled by the seemingly small risk of ice damming. Further we wouldn't want the solar gain from the siding to be used to melt snow that could otherwise be adding to insulation value - although this is admittedly a bit of a mute point if the roof cavity is indeed ventilated. Am I going to have to fabric a ridge assemblies allowing top ventilation to be toggleable in spring and fall? Short of such a toggle, cavities could be integrated between the north roof and wall and separately top and bottom vented at the south roof and top closed at the south wall. All of this assuming a sound conditioned air barrier and east west ridge orientation.
Does anyone have any further insight into other benefits of the relative stagnation of top closed cavities? In particular I am curious as regards potential benefits of limiting the flow of spores and pollen that might support mold growth.
Regarding the firring, in addition to Jeff's point about fastening depth in assemblies with continuous rigid exterior insulation, particularly in such assemblies with increased insulation depth, greater care is needed to maintain the consistency of the siding plane as the thickness of the firring decrease and becomes less resistant to variation in insulation compressibility while fastening. I've been using 1.5" rainscreen which also gives me more flexibility in finessing stability of floating corner trim.
By the way, can manufacturers please stamp sloped grooves into the sides of firring so that -when installed properly- intruded water flows away from the structure?
cheers
Hello,
I'm putting together an assembly for a remodel in climate zone 2A. The cladding is going to be stucco. I will use a rainscreen such as slicker max which takes care of the draining but I still haven't found a good solution to make it a fully vented rain screen assembly. I found a new system called HydroDry from Amico (https://amicoglobal.com/hydrodry-system/). It looks pretty promising but no contractor in my area has heard of it. Does anyone here have experience with it? I'd love to get first hand information on this system.
thank you
Log in or become a member to post a comment.
Sign up Log in