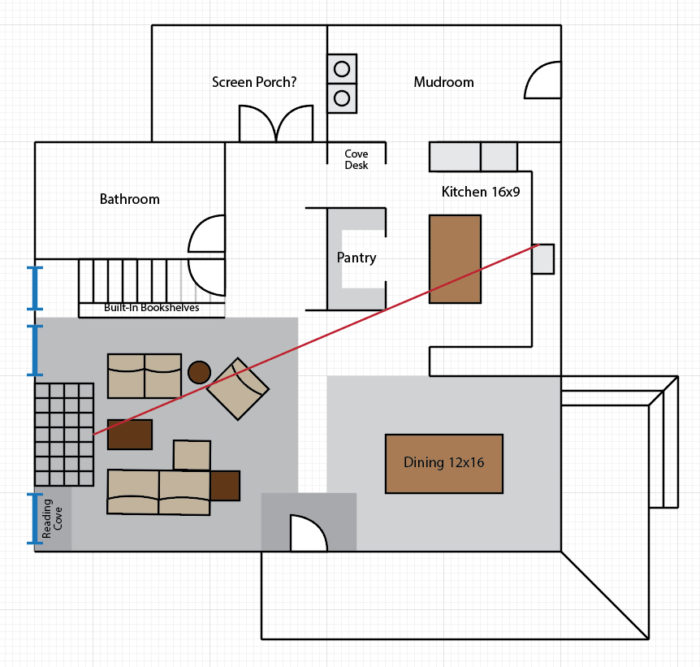
Image Credit: Mike Sterner
Too big, too complicated, too expensive — all problems in Mike Sterner’s current home, and exactly what he’d like to correct in the new house he’s planning in northern Wisconsin.
Writing in a Q&A post, Sterner lays out his basic plan for a “pretty good house that finds that happy place between great energy efficiency and economy.”
The site is vacant farmland with a south-facing slope. Sterner’s woodlot has lots of pine and oak he intends to mill for use in his new house.
“I would prefer to stay away from anything too ‘techy’ and have a fairly simple approach to the build,” Sterner says. “It is also my preference that we use materials that are earth and human friendly, with a proven track record. We’re looking at a simple saltbox farmhouse with a single gable, a big covered porch on the east and south, and a shed roof on the back as a rear entry.”
The second floor will have a shed dormer, although Sterner is open to the suggestion of building a full second story it it would be a “vastly better approach” for ventilation and insulation.
His current stumbling block is choosing a construction method for the building envelope.
“I go back and forth between 2×6 framing with a 4-inch rigid foam wrap and a double-stud wall with blown cellulose in both cases,” Sterner says. “I don’t really want to use rigid foam because it is kind of nasty and a hassle to install siding over, but at the same time I am concerned about the double-stud wall cold sheathing and moisture problems. The double-stud wall seems to have questions to me, based on the articles I am reading here.”
He also wonders whether…
Weekly Newsletter
Get building science and energy efficiency advice, plus special offers, in your inbox.
This article is only available to GBA Prime Members
Sign up for a free trial and get instant access to this article as well as GBA’s complete library of premium articles and construction details.
Start Free TrialAlready a member? Log in
10 Comments
board sheating
In my area, which is also Peter Yost's area, builders are enjoying using locally milled pine boards as sheathing in conjunction with double stud walls. Correct me if I'm wrong but I think the board sheathing mitigates the moisture issue with fat walls. I second what Martin said about dormers. I try to avoid them as an architect because of air sealing but mostly because they cost more.
Response to Robert Swinburne
Robert,
You're right: Because board sheathing is vapor-permeable, it allows moisture in the wall system to dry outward rapidly.
GBA often advises builders to consider the advantages of board sheathing. In one of my articles on double-stud walls, How Risky Is Cold OSB Wall Sheathing?, I wrote, "If you’re worried about the durability of your sheathing, choose plywood, DensGlass Gold, or diagonal board sheathing over OSB."
In another one of my articles, Wall Sheathing Options, I wrote, "Diagonal board sheathing has a lot of advantages for green builders: it’s usually produced locally; it’s strong; it’s vapor-permeable; it resists rot better than OSB; it holds nails well."
I would emphasize that
I would emphasize that exterior Roxul and exterior foam are significantly different in terms of moisture movement. The former can dry well in both directions.
Exterior foam
Good day Mike!
Come on down to Appleton if you want to see what 9" of used foam looks like to wrap an old 2x4 wall. It can be very inexpensive when found in large amounts on craigs list in our area. Just look for me on the web under FASCG.com. If new, I'd go with cellulose myself as proven in AK.
More on board sheathing
Board sheathing needn't be diagonal, if you add diagonal bracing. In a normal stud wall, that would need to be "let in" bracing, but in a double wall,.the bracing can sit in the space between the two walls, without being let in. How much labor that saves depends on the geometry skills of your carpenter.
Air tightness with board sheathing depends on another layer, such as house wrap. That is unlikely to be as good an air barrier as.taped sheet goods, unless you go with peel and stick WRB or liquid applied.
Cutting foam
If you lean toward natural earth friendly materials, you might not like it if your contractor cuts it in your yard with a table saw or circular saw and spews foam dust all around. The fire retardant chemicals are persistent bioaccumulative toxins. Cutting with a knife is much clearer, though EPS still tends to shed beads that will blow around the site. That, and the blowing agents in xps, make me think that polyiso. Is the best choice, at least for virgin foam.
But also, in your search for a combination of a builder and a method, I suggest checking that a builder who would use foam is ok with avoiding using saws on it outdoors if you want to avoid that site contamination.
ZIP System R-Sheathing
Where does this system fall into the mix? I am in the planning stages now and have found it hard to find builders and contractors who have experience and/or would be willing to take on a job using these methods. I also debated weather to use the double stud wall method or exterior foam over sheathing. I decided on the latter. So the first plan was to use two 2" layer with staggered seams. Then when discussing this with contractors the issue of three trips around the house became an issue compared to one with the ZIP R system. I am still in the early planning stage and haven't gotten to the cost estimates between the different methods of wall construction but have just made general considerations. Any thoughts or comments would be greatly appreciated. Thanks for all the great info on GBA.
Response to ADK Creator
ADK,
Zip-R sheathing is a perfectly acceptable way to add a continuous layer of exterior rigid foam to your walls. To read more about Zip-R sheathing, as well as a variety of other similar products, see Nailbase Panels for Walls.
The main caveat is that you have to choose the correct thickness of Zip-R sheathing. The product you select must have an R-value that is high enough to keep the interior surface of the sheathing above the dew point during the winter. For more information on the minimum required R-values (which vary by climate zone), see Calculating the Minimum Thickness of Rigid Foam Sheathing.
EIFS
EIFS seems like having your cake and eating it too: liquid-applied waterproof/airtight membrane (with taped joints); drainage plane; as much foam on the exterior as you care to pay for; and any number of finish details to choose from. Put the windows in the plane of the sheathing for airtightness and simplicity.
No complicated details, warm sheathing, great insulation.
And everything done by one subcontractor, quickly and efficiently.
Double Stud Wall v. Exterior Foam
Our experiences sends us in the camp of double stud wall with a 3-1/2" interior space. Outer wall and interior space blown with dense pack cellulose. Vapor barrier applied to the outer face of the inner wall. Inner wall filled with Roxul. Also, walk out basement built with ICF walls works great .... put as much finished space downstairs as you want ........ warm and try with sub-slab insulation and VB. Click on to http://rcmzeroenergy.com/ROSE-Cottage-Project/project-overview.html to see an example using the above.
Log in or become a member to post a comment.
Sign up Log in