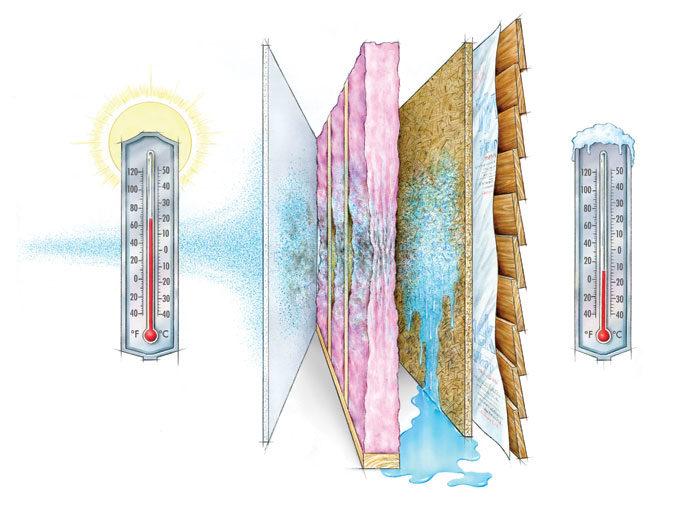
Image Credit: Don Mannes, Fine Homebuilding # 204
At the dawn of our current interest in building science, sheets of polyethylene were routinely stapled to interior framing before drywall was installed. The idea was to block the flow of water vapor into exterior walls. (Some builders tried to make their polyethylene seams airtight, so that the poly would do double duty — acting as an air barrier as well as a vapor barrier.)
Installing a vapor barrier (or more properly a vapor retarder) was considered cutting-edge.
But in time, builders began to see flaws in their approach. For one thing, it was virtually impossible not to damage or puncture the barrier during installation or after it was applied. The plastic sheeting was usually full of holes by the time the house was complete. As it turns out, these holes did not affect polyethylene’s performance as a vapor retarder — a ripped, torn vapor retarder works very well. However, these holes undermined the poly’s performance as an air barrier.
Since polyethylene reduces the ability of a wall to dry to the interior during the summer months, some builders began to worry the vapor barriers trapped moisture inside walls where it could do a lot of damage.
Thus began a muddying of the waters: when and where are vapor barriers a good idea?
Sandra Heiser wades into this debate with a Q&A post that’s the subject of this week’s Q&A Spotlight.
Leave the poly in, or take it out?
Heiser writes about a house near Buffalo, N.Y., that is ready for drywall. She describes the exterior wall assembly as follows: vinyl siding, 1 in. of rigid polyisocyanurate foam, 1 in. of sprayed closed-cell foam, fiberglass batts, and, finally, clear plastic.
“I’m thinking [the plastic] has to go,” she writes. “What are our options? Is it…
Weekly Newsletter
Get building science and energy efficiency advice, plus special offers, in your inbox.
This article is only available to GBA Prime Members
Sign up for a free trial and get instant access to this article as well as GBA’s complete library of premium articles and construction details.
Start Free TrialAlready a member? Log in
130 Comments
Renos
95 % of the homes built in the last twenty or even thirty years, at least here in western Canada, where built with stick frames, fiberglass bats, and poly on the inside to act as a vapor barrier and in a lot of cases, as the air barrier as well. They are still allowed to build this way which is a bit ridiculous considering our climate.
My question is, is there a safe way to add insulation to the exterior of these homes??
Vapor Barrier
This is a great article and in Minnesota builders are still required to use the vapor barrier unless the install a minimum of 2.5" of closed cell insulation. Our wall system we have been using for the last few years is the DOW SIS exterior structural insulated sheathing and a minimum of 3" of closed cell insulation. We use 2 x 6 walls 24" on center, but have had to learn all the extra backing required in order for siding, corner trim, etc having something to attach to.
wall construction
Just a couple of weeks ago we were being told that there is now evidence that during the air conditioning mode a house is subject to moisture problems on the outside face of the interior vapor barrier, especially if the house has wood siding.
Who are we to believe ?
Exterior Insulation
Mr. Riversong quotes Joe Lstiburek in support of his argument against exterior insulation. But Mr. Lstiburek, and the Building America approach that he and his colleagues helped develop, advocates just that. Here's a quote from the Building America Best Practices Series: Volume 5:
"Putting the vapor diffusion retarder roughly in the “middle” of the assembly by installing impermeable or semi-permeable insulating sheathing (such as unfaced, rigid, extruded polystyrene foam insulation) on the exterior of a frame cavity wall filled with permeable insulation. This is the system recommended by Building America teams."
This is the approach that we have adopted in our practice for wood frame construction. Air sealing at the sheathing plane allows the envelope to be pressure tested before insulation is installed. Exterior rigid foam is applied to a thickness that insures the sheathing remains above the dew point, based on climate. Wall cavities are filled with dense pack cellulose or similar semi-permeable insulation allowing drying to the interior. Exterior siding is applied over a vented rainscreen.
And of course interior humidity levels are managed with mechanical ventilation.
Response to Ken Ziegelbauer
Ken Ziegelbauer,
The advice given here at GBA has been consistent: in all but very cold climates (e.g., the Canadian prairie provinces, interior Alaska or Arctic Canada), interior polyethylene does more harm than good.
When GBA recommends the use of an interior vapor retarder, we are usually referring to kraft facing, MemBrain, or vapor-retarding paint.
vapor barriers
I should have qualified my resource. I did read in the last couple of weeks about support for more rigid insulation on the outside to offset the effect of the air conditioning season. I don't agree with that.
Response to Ken
Ken,
Well, you may not agree with it, but it's an excellent way to insulate a home. Thick exterior foam stops thermal bridging through studs, warms the wall cavity (and thereby prevents any condensation from forming in the wall cavity), and stops inward solar vapor drive during the summer.
What do you have against architects
I bristled at the last line in this article "As such, energy conservation has the potential to destroy more buildings than architects." There are lots of architects who care about this stuff, who are working to save buildings, and read Green Building Advisor.
Response to Lloyd
Lloyd,
Don't paint GBA with such a broad brush, Lloyd. You are quoting a summary by Scott Gibson, who is in turn quoting a GBA reader named Robert Riversong, who posted a comment on a GBA Web page in which he quoted Joseph Lstiburek, a well-known building scientist who delights in being provocative.
I tracked down the Lsitburek quote to its source -- a Web page where Robert Riversong probably picked it up. (If you are interested, here it is: http://www.joelstiburek.com/topten/wood.htm .)
This GBA page -- one of a series called Q&A Spotlight -- attempts to draw new readers into our Web site by summarizing a recent exchange of views on our Q&A page. The quoted statements are the opinions of the posters, not GBA.
By the way, Joe Lstiburek is married to an architect. When an architect recently accused him of architect-bashing, he responded, "You should hear what I say about engineers." (Joe is an engineer.)
ice dam caused leaking and interior ceiling damage
We live in SW Saskatchewan and our winters are harsh along with the occasional "chinook" which can drive the temperature to change 100 degrees in just a few hours {-50 to + 50}. We live in a reconstructed 1914 house with double studded framing {2x4 interior, 2x6 exterior staggered }. There is insulation in both walls as well as 1" styro on the exterior sheathing and a 1" layer of stucco and a vapor retardant paint. Our roof is metal and above the ceiling is 2x8 with 8" pink insol bats.
I think that the avalanche flashing caused the snow to build up and then turned to ice an began to creep up till it backed up under the edge flashing for our turret .
How can I repair this without serious roofing removal and reconstruction ? How can I prevent this from happening again. Do I remove the avalanche flashing... the eavestrough ? Do I need to add more insulation ? Venting ? motorized venting ?
Please help advise !
Response to Bradleyman
Bradleyman,
I'm not sure what "insol bats" are; I'm guessing you mean fiberglass batts. If that's what you've got, then your ceiling is insulated to about R-25 (if the insulation is very well installed). In Saskatchewan, you want R-60 insulation in your ceiling. Your ceiling is leaking a lot of heat.
The way to prevent ice dams is:
1. Seal all air leaks between the heated interior and your attic, and
2. Improve your insulation layer.
When contractors can't perform these two tasks properly, they often recommend other measures to get rid of the leaking heat (for example, ventilation) or to prevent the ice dam from damaging your ceiling (for example, installing a rubber membrane under your roofing). But these two measures are signs of failure. They are only necessary for badly designed roofs.
My guess is the suggested work is more than you can handle, so you should probably hire a contractor to improve air tightness and insulation in your ceiling. Often, the best approach is to use spray polyurethane foam to address these problems.
Wall vapor barriers
I don't see a clear consensus on this issue. Except Builder beware! No win situation it looks like to me. Why isn't there a clear standard. Even code built will be wrong it seems. I had problems with a unfinished basement where we had kraft faced insulation installed on a walk out exterior wall. The inspector called it a fire hazard and had to cover it or remove it the owner wanted to finish it later (never did) so we removed the Kraft facing. over the winter the OSB frosted & melted till warping and mold were an issue. would driwall prevented this or simply covered up a problem?
Outsulation
I'm considering an exterior wall composed of stucco, double wall paper vented inferiorly, 2" of polyiso, plywood, 2x6 filled with fiberglass bat, and no poly to enhance inward drying. This appears to meet the recommendations of Dr. Joe and others. Two concerns - 1) the need for a second rainscreen at the outer face of the plywood, and 2) the effect of high humidity in the bathroom. Does a vented rainscreen not increase the risk of condensation on the plywood during the heating season? Will high-humidity areas in the house not cause longterm harm? (Zone 6 - Okanagan Valley in B.C., 3500 heating degree days, 5 foot overhang).
Response to Mike Blake
Mike Blake,
Unfortunately, there is no substitute for the need for builders to study a little bit of building science so they can keep up with these issues. You're right that building to minimum code standards isn't enough to stay out of trouble.
If you install fiberglass batts in an exterior wall of a walk-out basement, you're asking for trouble. Basements are often damp, which means that the interior air has a high relative humidity. Fiberglass does very little to slow the flow of air, so your warm, humid indoor air has easy access to the OSB sheathing. The predictable result is lots of condensation on the back of the OSB. (By the way, OSB is the most vulnerable available sheathing -- much more likely to turn to oatmeal when wet than other types of sheathing like plywood.)
Fiberglass batts are the worst available insulation. In some applications, like yours, they can lead to real trouble. Your problems could have been easily solved with an adequately thick layer of exterior rigid foam. Another way to stay out of trouble would have been to insulate your basement walls with closed-cell spray polyurethane foam.
By the way, your building inspector was absolutely correct when he informed you that it is illegal to leave kraft facing exposed. It's a fire hazard.
Response to Francois Theriault
Francois Theriault,
Your proposed wall assembly should work fine. You don't want a rainscreen air gap between your plywood and your exterior polyisocyanurate -- the air gap would undermine the value of the insulation and make your plywood cold. If the plywood ever gets wet, your wall is designed to allow the plywood to dry to the interior.
There are two ways to address high indoor relative humidity in the bathroom:
1. Paint your walls with vapor-retarding paint.
2. Install a bathroom exhaust fan and use it.
If you take those steps, everything should be fine.
perm ratings and condensation
As a straw bale home designer and builder I have found that straw bale wall systems with perm ratings around 10 perform quite well in the harsh New England climate. These wall assemblies rarely experience the condensation issues so commonly found with todays conventional building practices.
To follow up-The question is
To follow up-The question is about “Green” insulating products in R&D which claim to posses the same bulk moisture storage and water vapor dissipation properties that of a plastered straw bale wall system? I understand that straw bale construction is still a leap of faith for many green builders and I would like to know if there is a transitional insulating product that isn’t high in embodied energy, recyclable, user-friendly, minimized failure and above all is affordable.
Nonsense without accounting for climate
I live in the NorthEast USA. Almost every winter, we hit 30 below zero temperatures. This can go on for a week and then be followed by a week of above-freezing weather and substantial rain.
Few (if any) homes have central AC, and what AC is used amounts to one or two window units used a few days of the year. But the relative humidity for June to September will still be quite high - it's simply the climate we enjoy.
The Prairies actually have it better. It may be nominally cooler, but it is also much drier most of the year. In Maine, I'm not sure there even is a "dry" season.
There are many valid points in the above story and comments, but they all seem to be searching for some "magic pill" - the "one way" of building that will work everywhere (maybe even on the moon :-)
In Canada, they have been building "super-insulated" (by US standards) R2000 homes for 25+ years. You will note most of Canada's population lives within 100 miles of the US border, so it stands that most of these homes would be close to the northern USA.
Of course there were problems. First, builders don't like conforming to standards. Homeowners didn't like running HRVs all the time. But the principles of R2000 are still valid and applicable to similar climates (with adaptations for new technology).
That means never trapping moisture within an assembly, controlling human-produced moisture at or near source (with HRVs) and making sure liquid water has no ingress from the outside (above and below ground).
Personally, I am adverse to spray foam. As mentioned, new wood contains a lot of moisture. Spray foam creates such a hermetic seal that - unless it is encasing inorganic, moisture-free material - increases the chances of locking in that moisture (and any added from structural movement or design failure).
Time will tell.
Now what really makes sense . . .
from this point of view, is balloon construction. Air from a vented basement space rises up through the walls carrying moisture to the vented attic--we hope--with it.
exterior foam board insulation
is it a good idea to add foam board to the exterior sheeting to increase the total wall r value when residing and new windows
Response to Capn John
Capn John,
I hope your comment was tongue-in-cheek. It is certainly true that most attic moisture problems can be traced to a damp basement or crawl space -- and an inadvertent air leakage connection. Weatherization contractors see this problem all the time.
Needless to say, deliberately designing a house with such an air leakage connection would be a big mistake.
Response to Glen
Glen,
You asked, "Is it a good idea to add foam board to the exterior sheeting to increase the total wall R-value when residing and installing new windows?"
The answer is yes, as long as:
1. The rigid foam is thick enough to prevent condensation in the walls, and
2. The installer does a good job flashing windows and penetrations.
In most cases, such exterior foam retrofit jobs require the inclusion of a rainscreen gap between the foam and the siding.
What to do with plastic?
When I was in school my instructor said to put the plastic on the inside, but back then we used black board on the outside. From all the commets it seem to me that the zone is key to the problem. If it's 7-8ish then think plastic. As you go to warmer areas the progam has to change.
CONCRETE BLOCK WALLS
My house is in the Mid-Atlantic region and is constructed of concrete block walls with the brick front. As I have been remodeling, I have been lining the block walls with 1" rigid foam in the basement with the DOW fiberglas free batts inside metal stud walls. Is that a mistake? Additionally, I have a wood framed addition which I planned to remove the exterior siding and replace it with 1" rigid foam and Certainteed foam backed siding, and finish off with the 1" interior and dow battts. Any advice?
Response to Marc
Marc,
I haven't heard of "Dow fiberglass-free batts." What are they made of?
Increasing air flow in your personal steam shower
"The drying potential of an assembly decreases with the level of insulation and increases with the rate of air flow." * from the above article
I have been experimenting with air flow in my steam shower renovations. I have built a few mock ups and have nearly finalized my design. The design is simple - move air through the steam room to speed up the drying times. These designs are so sleek and contemporary today and a busy steam shower can be in a constant state of saturation if used by the entire family at multi times in the day.
By moving air through the steamer the rate at which it dries out is increased dramatically. With a quick squuegee a typical 4'x5' steamer dries out before you are ready to go to bed or out to work.
DOW Fiberglass Free Batts
Martin,
I am not sure. I trashed the packaging. They are sold at Lowe's and require no gloves, they don't itch and can be cut with scissors. There is a clear backing membrane if you will, that we left on against the inside of the house against the sheetrock. It states that it is not a source of food for mold and that mold cannot grow under any circumstances. It looks like blue jeans.
30 yr experience w/ poly
When we built our house in '78-'79 (eastern VA), we put poly on the interior walls even though some people were starting to recommend against it at the time. We have recently done some remodeling for a new fireplace, sliding glass door replacement, and repairs to rot from improperly flashed decking. In all cases we had to tear into the old wall structure. There was no sign of moisture damage or condensation due to the interior poly in any of the locations.
Response to Anonymous
Anonymous,
Your situation is typical. Like you, I built my house with interior poly, and subsequent renovation work has not revealed any problems. Most houses with interior poly are not experiencing problems.
The worst-case situation for interior poly involves air-conditioned houses with stucco, manufactured stone, or brick veneer over a vapor-permeable sheathing (without exterior foam). Those houses usually have serious problems.
Of course, new-home builders can't be reassured by the fact that 90% of homes with interior poly are performing well. If they were to choose a construction method that resulted in 10% failure, they would soon be out of business.
Response to Marc
Marc,
It sounds as if you have been installing Dow SafeTouch batts, which are manufactured from polyethylene terephthalate fibers. According to my research, the plastic facing is a vapor barrier.
http://www.dowsafetouch.com/na/en/faq/index.htm
You wrote, "I have been lining the block walls with 1" rigid foam in the basement with the DOW fiberglass-free batts inside metal stud walls. Is that a mistake?"
My guess -- yes, it's probably a mistake. You don't want a vapor barrier in that location. Moreover, I'm not sure whether polyethylene terephthalate fibers behave better or worse than fiberglass when used in a damp location like a basement. I wouldn't recommend fiberglass for basement walls.
According to the Dow Web site (see above link), "SAFETOUCH™ Insulation should not be used in the exterior walls of Types I, II, III or IV construction, per the International Building Code. It is important to understand the building code that is being enforced in the location of building design to ensure compliance. If foam plastics are used in the wall constructions, then the exterior walls are required to meet the requirements of Section 2603.5 of the IBC. Specifically, SAFETOUCH™ Insulation has not been tested per Section 2603.5.5 (NFPA 285 Test) of the IBC in an exterior wall system that includes foam plastics and is therefore not approved in this application."
Although the Dow Web site is terribly written -- wake up, Dow! Give us the facts! -- it seems that they are admitting that their batts are not vapor-permeable enough to comply with the requirements of the IBC for Types I, II, III or IV construction. If anyone from Dow is reading this, feel free to tell us all what your Web site really means.
I would suggest that you use only rigid foam or closed-cell spray polyurethane foam on a basement wall.
rigid foam insulation
does anyone have a opinion on using 1"ridgid blue foam sheets to cover the underside of a floor with or with out fiberglass batts. there is a 4' crawl space that has 2"extruded foam on exterior walls. the house is in Montana, very little humidity and winter temps that get to zero and below quite ofter during dec. and jan.
Response to Vi
Vi,
Sealed conditioned crawl spaces make more sense than unconditioned crawl spaces. If you have insulation on your crawl space walls, and if your crawl space has no vents, then you should remove all insulation from the joist bays above the crawl space.
Be sure that you have a ground cover (heavy polyethylene) on your crawl space floor. You probably want to add more rigid foam to your crawl space walls.
vi
additional info on the above ?. the floor joist are 11" boise casscade manufactured joists, the sub floor is OSB. the foam would be attached the the bottom of the floor joists, encapsulating the entire bottom with the seams taped. if i use fiberglass batts they would be staped to the bottom of the sub floor with the vapor barrier up toward the sub floor. the purpose would to be to increase the r value of the floor and derease the use of fossil fuels during the cold months. any insight would be great. thanks
vents
we have exterior vents that we close and seal during the winter months, also we do have poly on the raw dirt floor.
Response to Vi
Vi,
Your vents should be permanently sealed. Insulate your crawl space walls, not your joist bays. You want a conditioned crawl space.
thank you.
thank you.
Vapor barriers
i did not see any mention of open and closed-cell foam in walls, etc. This does same things but I believe to a greater degree. Why wasn't it mentioned?
Response to Gotchaa
Gotchaa,
What your point? I'm not sure what you are driving at.
Walls that include open-cell spray foam or closed-cell foam still need to be analyzed from a hygrothermal perspective to be sure that the wall assembly is able to dry. Just because you use spray foam doesn't mean you can ignore a moisture analysis.
Open-cell foam is quite vapor permeable, and several builders have had wet-wall and wet-ceiling problems in homes insulated with open-cell spray foam. The usual cause of these problems: high indoor relative humidity, and no vapor retarder on the interior side of the foam. In a cold climate, this combination spells trouble.
Closed-cell spray foam is an effective vapor retarder.
Humid South
Remember that this problem is reversed in the humid south. In Baton Rouge today there will be high humidity and probably a 95-98 temp. Water vapor from the outside can condense in wall because of the sheetrock side is cool from the air conditioning. This is a particular problem where the ceiling vent for the air handler is blowing cooled air on an exterior wall, which may cool down dramatically.
Shower/Steam Room on Outside Corner of House
Timely discussion. I think I am convinced no poly on interior of walls (house is in DC area).
So for remodel will use "Modified" GBA Wall = latex paint/drywall/2*8 studs & unfaced fiberglass (can't afford 2lb foam)/0.5" Ply Sheathing/1.5-2" Closed Cell Foam (taped & sealed as best I can)/0.75" RainScreen/Cementitious Siding -- So question is: for shower/steam room on outside wall do I omit outside foam and use air/bulk water barrier (kills wall R value)? Or what? House is very small so using false wall(s) is not optimum. Moving the room to be all interior is possible but $$. Any way to vent stud cavities that has some chance of working?
Reflective Heat Barrier
I've seen pitched, reflective foil barrier for exterior walls and attics. Any experience and recommendations for or against this stuff?
Renovation of older home
I am adding insulation to an existing brick/block home in Cincinnati - in most cases I have added 1 1/2" rigid foam directly on the block. In a few cases I have installed stud walls with kraft faced fiberglass batting. I'm wondering if there is the potential for water problems as a result, particularly with the fiberglass batt construction....any comments?
Response to Sam
Sam,
You wrote that you plan to install "1.5 - 2 in. Closed Cell Foam (taped & sealed as best I can)" on the exterior side of the plywood sheathing. Do you mean rigid foam board (like XPS or polyiso)?
In the vicinity of the steam room, I would suggest one of two approaches:
1. You could switch to 1.5 in. or 2 in. of EPS foam -- slightly more permeable XPS or polyiso -- and include MemBrain on the interior.
2. You could use any type of rigid foam on the exterior, but instead of using fiberglass in the steam room, you could use spray polyurethane foam between the studs (for example, one or two portable Handi-Packs).
Response to Anonymous
Anonymous,
You asked a question about radiant barriers. Here's what the GBA encyclopedia has to say on the issue:
"Radiant barriers are shiny sheets of material—aluminum foil, for example—with a low-e (low emissivity) surface. When an air space has a low-e material on one or both sides, the R-value of the air space or building assembly increases.
"The effect of a radiant barrier on a building assembly's R-value may be significant or insignificant, depending on whether the assembly is well insulated or poorly insulated. Radiant barriers do not significantly benefit well-insulated assemblies. A poorly insulated assembly, however, will benefit from a radiant barrier. That's why radiant barriers make the most sense when installed in an uninsulated steel warehouse; they make the least sense when incorporated into residential walls or roofs, as these assemblies are already required by code to be insulated.
"Radiant barrier products can be foil-faced kraft paper, foil-faced polyethylene film, or foil facings on rigid insulation or wood-fiber sheathing. No paints — not even aluminized paints — qualify as radiant barriers. If the radiant surface is touching another material, it won't work; an air space is required on at least one side of a radiant barrier in order for it to function as designed. Otherwise, it functions as a conductor.
"If radiant barriers are installed horizontally with an air space above—for example, on an attic floor—their usefulness rapidly deteriorates due to dust accumulation.
"Radiant barriers have no R-value. However, if installed adjacent to an air space, they can help raise the R-value of the air space."
Read more here: Insulation Choices.
Response to Pat
Pat,
Of the two methods you've been using, the installation of rigid foam is far preferable to the steel studs with fiberglass batts.
I don't think your walls will have any moisture problems (as long as there were no moisture problems before you started insulating). But when you install fiberglass batts between steel studs, you have almost no insulating value whatsoever. The heat is so easily transmitted through the steel studs (which act like thermal bridges) that the fiberglass batts might as well not be there at all.
For more information, see Steel Studs.
Best Insulation for new home constuction in Galveston, Tx
We are building a new home in Galveston. The exterior is vinyl siding over 5/8 inch plywood with 2x4 studs and with interior sheetrock. We are trying to achieve the best R factor as possible and not have the problems of mold, mildew, inner wall rot and other related problems. The a/c -heater heat pump will be seer rated 16.
Response to Bill T
Bill T,
There really is no upper limit on the possible R-value of your wall. Most builders or homeowners don't strive for the "best possible" R-value; they usually stop at a point that seems economically reasonable.
Obviously, the minimum R-value of a wall is determined by your local building code. Many energy experts advise builders to install twice the code minimum R-value, if that amount of insulation is affordable.
For some reason, you've decided to install vinyl siding over plywood over 2x4 studs. This construction is incompatible with your desire for a high-R-value wall.
Ideally, your wall would be sheathed with exterior rigid foam -- as thick as you can afford. Exterior rigid foam greatly reduces thermal bridging through wall framing.
If you are absolutely set on vinyl siding over plywood sheathing over 2x4 studs, the highest R-value wall would include closed-cell spray polyurethane foam between your studs, and then as much interior rigid foam over your studs as you can afford.
Exterior Walls
In my experience, in humid Florida, it seems that the best mindset to have when trying to determine the materials to use for an exterior wall assembly that keeps dry is to have no vapor retarder at all but rather a vapor barrier or two. For example, typical Florida homes are constructed with CMU on the first floor and wood sheathing on the second floor and above. On the first floor we typically will install stucco or cemplank over a permeable house wrap which is attached to the block. On the inside of the wall we'll install rigid iso board, furring strips and drywall or furring strips then permeable foil wrap followed by drywall. On the second floor again we'll install stucco or cemplank over top of a house wrap which is fastened to the plywood with insulation installed between the studs then the drywall over top of the studs...no vapor barrier. The idea in both of these instances is succumbing to the fact that there will be moisture in the walls, no matter what, and dealing with it. Don't stop it. Let it flow to the outside when it's cold or to the inside when it's hot...and dry out. I can recall back in 2004 when Hurricane Charlie came to town that so many homes suffered from moisture problems from the driving rain, not because of water getting through the vapor barriers but rather hitting the vapor barrier, traveling down the walls and having no place to weep out (improper flashing is a whole other topic).
hot AND cold
What about here in the Midwest where the temps are -20 to 40 during the cold months and we also have high humidity with temps around 100 for weeks during the summer? Most of this has seemed to tilt towards "this works in warm climates" and "this works in cold climates" ....?
Sounds like you don't want a vapor barrier on either side in that case? Permeable house wrap on the outside, and kraft paper on interior batts? Assuming 2x4 walls, OSB/plywood sheathing and hardiboard/engiineered wood/vinyl on the exterior -- that's what you typically see for framing in a new-construction neighborhood.
Does this mean that for really decent insulation you should have 2x6 exterior walls in this setup?
Perhaps with open-cell insulation instead of fibreglas?
Two walls
I wish to consider the insulation of two walls. Location Upstate New York. Winters to 0 F, summers to 95 F. Baseboard heat.
1. Old house built as follows from inside out - plaster / lathe, 2x5 studs, brick mortared between studs (Insulation? thermal mass?), clapboard siding. (No sheathing) I wish to discard the siding and install plywood sheathing, foil-faced polysio foam and vinyl siding. I have been told to put the polyiso under the plywood since the reflection will cause problems with the siding. I intend to leave the brick in place. What is the correct order of insulation, what other layers should I consider and what other suggestions would you have.
2. New house wall consideration. Same climate. Radiant floor heat. Desire to have envelope of externally-insulated masonry thermal mass. Interior wall structure to be 8" thick Azar Dry-Stack Block containing electrical and plumbing runs subsequently filled with grout. Next would be 3-4'' foam sprayed in place. Exterior to be covered with stucco over metal lathe attached to Azar wall with ties through foam. Comments as to practicality, unmentioned layers, potential problems would be welcomed.
Hybrid insulation?
I used to have serious doubts about the "hybrid" insulation strategies touted by the DIY spray foam companies, especially from a moisture viewpoint. After reading this board, I think they may be on to something (besides making their product seem more economical). The use of closed-cell foam against the sheathing (and inch or two) and filling the rest of the bay with either unfaced fiberglass or open cell foam is consistent with putting the vapor barrier in the middle of the assembly and allowing drying to both sides. The wall would be: vapor retarder primer, drywall, fiberglass or open cell foam, closed cell foam, sheathing, housewrap, optional rainscreen, siding. Any thoughts?
vapour barrier
I have known that VB's are a waste of time for several years. I live in Vancouver Canada. It rarely gets below freezing and we see a lot of precipitation. Why do we spend so much time trying to keep moisture on the inside of a house to the outside when all the moisture is on the exterior of the house? I have torn open a lot of walls in my years with insulation and no VB. I have never seen rot in those walls caused by interior moisture sources...only damage from precipitation, poor flashing etc. When are the engineers/building codes going to change?
Response to Midwesterner
Midwesterner,
There really is no substitute for building science knowledge; each wall has to be studied and considered based on its merits. There is no simple rule like "houses in the Midwest shouldn't have a vapor retarder." If these issues puzzle you, I strongly suggest that you buy and read Joseph Lstiburek's Builder's Guide to Mixed Humid Climates.
The wall you describe -- 2x4 studs covered with OSB sheathing -- performs very poorly. Your suggested improvement -- a wall with 2x6s -- is barely better. There are many types of walls that perform much better. For starters, I would suggest adding 2 inches of rigid foam sheathing on the exterior of your walls.
Response to Mike Hoyt
Mike Hoyt,
1. Put the polyiso on the exterior side of the plywood sheathing. Then install vertical 1x3 or 1x4 strapping over the polyiso, screwed through the foam to the studs. Don't worry -- the foil won't damage the vinyl siding.
2. Your proposed new-construction wall will probably perform well, although it sounds like a very expensive way to build a wall. I don't believe there is any advantage whatsoever to thermal mass in your climate. The only detail you mention that I'm unsure about is the plan to anchor the metal lath through the foam to the Azar wall; I don't have enough experience to suggest a good detail for those fasteners.
Hybrid insulation question
Dear Anonymous,
Flash-and-batt insulation (or hybrid insulation) can work well, as long as the layer of closed-cell spray foam is thick enough to avoid condensation problems in your climate. (Thick is better than thin.)
Read more here:
https://www.greenbuildingadvisor.com/community/forum/gba-pro-help/13791/spray-foam-and-batt-insulation
https://www.greenbuildingadvisor.com/community/forum/energy-efficiency-and-durability/12175/hybrid-insulation-techniques
Response to Anonymous from Vancouver
Anonymous from Vancouver,
As I'm sure you know, the changes you seek are already happening.
The "leaky condo" crisis in Vancouver led to significant building code changes in your area; now rainscreen gaps are required between the siding and the sheathing for most Vancouver buildings. Rainscreen techniques are intended to address the most common problem with walls -- wetting from the exterior.
Traditional
We're in Northern Alabama and have an extremely wide range of weather. The temperature can swing from 10º below zero to 115º above, with rainfall that matches London and Seattle. Chasing the dewpoint location in a wall assembly is a definite challenge.
I think we have used every combination conceivable, and have come full circle to an old-school solution:
3/4" Plywood sheething, #30 asphalt felt half-lapped and flashed to roofing standards, kraft-faced batts, and drywall. And then stop. We don't even use OSB because of its moisture impermeability.
The key here is to take the savings in high-tech materials and simply frame a much thicker wall, with thicker batts, and slow down the speed of the dewpoint shift. Moisture then has the opportunity to disapate as vapor rather than condense on the in-wall surfaces. R-values, sound, wall depth for window trim visuals are just a bonus. Run the numbers; you can build a offset double-stud wall this way cheaper than any single wall combination using foam.
Flash and Batt - BAD!!
First of all, I want to name the convention you described in this article. It's called flash and batt insulation. This is where someone comes in and sprays 1" of closed cell spray foam to the outside of the wall and the fills the cavity with fiberglass to get a better R-value. The problem is the vapor barrier (1" of closed cell) is on the outside of the wall. This still allows moisture latent air to pass through the fiberglass cooling as it runs through the fiberglass and then it condenses on the foam. Just so we're all clear, you can't build in upstate NY without 2" of closed cell or 3" of open cell. South of Washington. DC you can do flash and batt, but north of it, I would say NO Way!!
Who says the codes are right? I've seen to many codes where the intent is good, but it's flawed in all circumstances. Much like this one, which is requiring a vapor barrier to the warm side. So, I would say you have a significant decision to make. Consider tearing out the fiberglass and putting foam (open or closed cell) in the cavity to basically fill the cavity with an air impermeable material. That being said, it doesn't need to be filled, but it does need to cover all surfaces of the studs and be at least 2-3" thick at minimum.
Response to Jim Coler
Jim,
1. I disagree with your definition of "flash and batt." You wrote, "This is where someone comes in and sprays 1 inch of closed cell spray foam to the outside of the wall and the fills the cavity with fiberglass." In fact, the definition does not specify the thickness of the closed-cell foam. Done right, the method require a climate-specific thickness of foam -- not just 1 inch.
2. I disagree with your one-word assessment of the system (Flash and batt -- BAD!). The flash and batt system can work well, as long as the spray foam is thick enough.
3. Here's what Joe Lstiburek has to say about the flash-and-batt system: “The only way you can get into trouble is if the foam isn’t thick enough in a cold climate,” says Lstiburek. “To be safe, use about 1 inch in climate zone 5, or 1 ½ inch in climate zone 6, or 2 inches in climate zone 7.” Lstiburek points out that plywood-sheathed walls allow better drying to the exterior than OSB-sheathed walls. “It’s not a problem on plywood or gypsum sheathing, which are more vapor-open than OSB,” said Lstiburek. “OSB is the only sheathing of consequence if the spray foam is too thin in a cold climate.”
vapor/condensation entrapment
Looking at polyfoam blocks that one installs rebar inside and then pours concrete in center. Planning to use vinyl siding on outside, and inside of blocks will be 2 x 6 with fiberglass insulation, finished with gyprock. Question is ...should I not put plastic vapor barrier under the gyprock?
vapor/condensation entrapment
Sorry ,I should have added " area is Nova Scotia,Canada" Similar to upper n/e coast of US, with ocean near.
insulating a garage ceiling
I've been trying to figure out what to do with my garage ceiling for weeks now and today I received this article in my email - very timely but doesn't really give me a definitive answer. I'm in eastern Ontario where we get very cold winters and hot summers. My garage is 34'x23' with 11' ceilings. Only a very small portion is attached to the house. The builder finished the ceiling with drywall but put no vapour barrier or insulation in the attic - which has a huge peaked roof and great air circulation. Any suggestions on how to insulate the ceiling without taking down all that drywall - from reading this article I was hoping I could just paint the drywall with a vapour retarding paint and then use some blown in insulation or I thought of putting rigid foam insulation between the trusses and then blowing in insulation on top off that - any suggestions? I plan on heating the garage with natural gas and keeping it about 5degrees above freezing and just turning it up a little bit when I work on my car.
"Ideally, building assemblies
"Ideally, building assemblies should be designed to dry to both the interior and exterior. In heating climates, the primary drying potential is to the exterior."
I think this is talking about the diffusion open walls that Europeans have been building for decades. What do you experts think about that type of assembly? I wonder though, just as in windows, a good window that is good for chicago is not good for new orleans, I would think climates matter a great deal in this thermalhydro discussion of wall assemblies.
Response to EJC
EJC,
To rephrase your question: You are building an ICF wall in Nova Scotia. You intend to frame up the interior of the ICF wall with 2x6s and insulate between the 2x6s with fiberglass batts. You're asking whether you need polyethylene under your gypsum drywall.
No, you don't need polyethylene in that location. You're not going to have any cold surfaces on in your wall assembly where condensation can occur.
However, I understand that Canadian building inspectors often insist on poly. If your building inspector insists on poly, you have two choices. Either install the poly, because your wall is pretty safe, or install MemBrain, which will allow your 2x6 stud bays to dry to the interior in the unlikely even that the wall ever gets wet.
Response to garage ceiling question
Dear Anonymous,
Go ahead with your plan -- you'll be fine. Paint your ceiling with vapor-retarding paint and blow as much cellulose or blown-in fiberglass insulation as you can afford above the drywall ceiling.
Response to Roger Lin
Roger,
Q. What do you think about diffusion-open European walls?
A. I think they perform very well. In most European cold-climate residential walls, the interior of the wall is less vapor-permeable than the exterior of the wall. (Many European Passivhaus builders install OSB, which is a vapor retarder, on the interior side of a framed wall.) Since homes in northern Europe almost never have air conditioning, these walls perform well.
Q. Does climate matter when analyzing the hygrothermal performance of a wall assembly?
A. Absolutely!
Older house
Our's is an 1850's farmhouse in eastern Ontario, just north of Lake Ontario. Construction is coursed rubblestone/lime mortar walls varying from 26" thick at ground level to 18" at the gable end peak. The original interior finish was plaster on lath, however roof failures long before we bought it left a lot of the plaster moldy or on the floors. With a new steel roof complete, we tore out all the plaster and lath, leaving just the interior stone face, the dooks and the furring strips in place. We built the furring strips out to give sufficient room for 4-5" of closed cell spray foam. The second floor ceiling was covered with poly, which was sprayed into the foam at the perimiter. The attic is now R60 cellulose. We applied the drywall directly to the furring strips with no poly on the walls.
Our thinking was that the stone walls, with diligent repointing using lime mortar, would look after its own moisture balance. They have for 160 years. Interior moisture from baths and kitchen is vented externally. Heat is forced air
Given everyone's opinions, we're not sure if we have chosen a sound method.
Response to Jim
Jim,
Your house will be fine. It sounds like you did a good job.
Response to Anonymous from Vancouver by Martin Holladay, GBA Adv
Yes the rain screen has greatly improved the situation, but my point is that the vapour barrier is a waste of time and money. I'm not sure if it's true but I've been told that Seattle (same climate) doesn't have a vapour barrier requirement.
Edge conditions in superinsulated wall
My wife and I are building a superinsulated, sealed house in Vermont, ventilated with an HRV. Our current plan is to build with 2x6" studs, insulate the stud cavity with dense-pack cellulose, use zip system boards for sheathing, and then put 6" of polyiso on the outside, and then attach vertical strapping to provide a cavity for moisture to fall down, and attach either cedar or fiber-cement clapboard siding to that.
We went with this design in order to keep all the wood in the wall above the dew point, and we largely succeeded, but in the thermal model, we run into a problem right at the base of the wall, above the sill, where the temperature of the wood dips well below the dew point due to the thermal bridging effect of the frost wall.
Because I have no previous experience with this type of wall insulation, I don't know how serious this situation is. Clearly there's a real potential to get condensation in this area, but the question is, is the fact that it's such a small area a mitigating factor? Is it the case that as the wall warms and cools, depending on the outside temperature, the moisture will tend to migrate out, drying the condensation before it leads to rot? Or do we need to go with a different foundation design? The lot isn't flat, so we can't go with a plain slab on grade--we need that frost wall.
Response to Ted
Ted,
I imagine that you're overthinking the situation, but it's hard to be sure without a clearer understanding of your design.
You're talking about "the base of the wall, above the sill." Do you mean the rim joist? The bottom plate?
It's always possible to adjust your insulation to make your framing warmer. If you need insulation on the exterior of your concrete foundation, that can be done with XPS or spray foam. If you need insulation on the exterior of your mud sill or rim joist, that can be done with XPS, EPS, polyiso, or spray foam.
I'm almost certainly
I'm almost certainly overthinking the situation. :')
We hadn't planned on keeping the frost wall warm because it's quite tall, and we have substantial insulation under the slab. So the cold area we're talking about is probably 4" high at the outside of the stud wall, tapering off to 3" high at the inside of the stud wall--so it includes the sill and the bottoms of the studs. The studs are being connected directly to the sill, rather than framing the stud wall before standing it up on the sill, so as to minimize the thermal bridging through the framing from the frost wall at that point. This was a compromise to avoid having to have a thick insulating baseboard with all the complexity that would bring. The insulating baseboard would actually make the wood colder, so it doesn't address the potential moisture issue.
There are certainly ways that we could bring that wood up above the dew point, but there aren't any cheap ways to do it. So that's why I'm wondering how serious the situation is--do we need to solve this problem, or is it a non-issue?
Response to Ted's second post
Ted,
Now I have a better understanding of your planned detail. You do, indeed, have a thermal bridge at the top of your concrete foundation.
Insulating under your slab is not enough. If you are building a superinsulated home that includes 6 inches of exterior polyiso on your walls, you are obviously making a substantial investment, and you show all the signs of someone who wants to do it right.
If I were building the house, I would install vertical insulation (as much as you can afford -- 2 inches of XPS would be OK, although 4 inches would be better) on the exterior of your frost wall, all the way down to the footing. And I would be sure to have an airtight and waterproof detail where the top of the foundation insulation meets the 6 inches of polyiso.
Okay, thanks for answering
Okay, thanks for answering this. This article was very timely--we are right at the point of trying to finalize our wall design.
100 year old uninsulated home
We moved a 1899 home to a new location to be used as a museum. Built a perimeter vent free foundation and used it as a plenum for the furnace. Left the original siding and framing but vented each stud bay up into and out of the attic. Then applied 2" rigid foam, poly, and 1/2" cdx to interior walls.
Attic has blown in insulation. In the mild coastal climate of N CA this is working beyond my expectations.
Each building and climate must be approached for its unique problems and solutions. It's not a cookie cutter remedy.
Re: Older house
Thanks fo the encouragement Martin.
There is one area of our old house where moisture control is incomplete and we have the chance to do the "right thing", whatever that is. We're talking about the basement or "pit". The house was not built with a basement. The foundation is a perimeter rubble trench (no mortar) 35'x25' and 4' deep. The silty soil level within the perimiter is about 6" below the logs that act as main floor joists and is about 30' above the water table as guaged by 2 unused dug wells nearby.
It appears that in the 1970's the owners wanted central forced air heating. They cut a hole in the main floor beneath the staircase to the second floor, which is in the centre of the house. They excavated until they had a pit about 10'x10' and 7' deep, then installed the furnace, water heater and oil tank. They just ran the ductwork and water pipes in the gap below the logs/joists. The heat generated by the furnace during the winter makes it the warmest place in the house. During the summer it is cool but never damp. We have never had visible moisture in the basement. The logs/joists and underside of the 5/4" pine flooring are dry and sound
Should we be doing anything about insulation and/or moisture control? If so, what?
Response to Jim's second post
Jim,
Of course it's hard to fully assess your crawl space without a site visit. If I understand correctly, you have a crawl space that varies in height, down to a minimum of 6 inches. In the center of the crawl space is a 7-foot-deep pit for the furnace. You don't say whether this pit has concrete walls or dirt walls.
If the stone perimeter wall has no mortar, it must leak a tremendous amount of air. The right way to address such a crawl space would be to excavate the soil until there is at least 3 feet of clearance between the soil level and the underside of your floor joists. Then the interior stonework could be parged with mortar or fiber-reinforced mortar. Ideally, the interior side of the foundation walls would then be insulated with closed-cell spray polyurethane foam.
All ductwork seams should be sealed with mastic.
SIP Panels
Ii have 8" SIP panels spanning 30' on a12:12 pitch, as the roof structure on a northern Michigan, Lake Huron fronting home. As you might expect we have a lot of wind blown rain, high humidity, and more weather related environmental changes per day than many areas see in a month. I've seen temps vary 70 degrees in a day - -10 to 60. Not quite the Chinook another writer mentioned, but darn close.
My question is, how do I protect the OSB skins on my SIP panels. The cores are expanded PS (EPS) bead foam, not extruded PS (XPS) as Styrofoam is. EPS has much more porosity and I'm worried about the moisture getting trapped within and rotting the skins, at which point I no longer have a "structural panel", just a collasped one and a collapsed roof.
Anyone have any thoughts on what if any membrane I should use under the shingles on the top side, or under the drywall on the inside, I'm appreciative.
Response to RJC
You definitely want a vapor-permeable roofing underlayment. I think #30 asphalt felt works just fine.
The cluster of SIP problems in Juneau, Alaska was traced to air leaks at the seams, not diffusion. Be very careful with your air sealing measures -- I recommend a belt & suspenders method involving spray foam and interior tape for all seams.
Normal water-management details should handle the wind-driven rain. As with any OSB-sheathed house, I strongly recommend that siding should be installed with a rainscreen.
question for Pat
Pat, what are you putting over that 1 1/2" rigid foam and how are you securing it.
1850's super insulated rigid foam
Hi, In my 1850's Federal House in central Maine, I removed the occasionally wet cellulose which was only half filled in the walls. I have insulated the lower level with 4 inches of recycled black covered polyiso rigid foam board and have put it right against the old wood board interior sheathing boards. I foamed in all the cracks. Now I am building new offset 2x4 interior walls to reduce thermal bridging. Then I intend to fill the bays with 4 more inches of polysio rigid foam. Then plasterboard on the inside.
But I am still concerned about thermal bridging and uping the insulation. So I was wondering about adding more rigid foam, like 3 inches to the exterior of the house, over a typar sheeting which would be next to the old wood sheathing. Then add spacers between the exterior foam and the siding. But from what I read, putting solid foam on both exterior and interior might keep the moisture inside the 2 layers.
I know the one layer of rigid foam is not fully airtight as last winter I only had one interior 4 inch layer of solid foam and during very cold weather, I heard popping and cracking as the wood strunk and the foam unstuck itself from the wood. I could then feel air coming in slightly at spots.
Ideas?
Thanks!
Closed cell polyurethane foam
I have a lake cabin with a 2 x 6 t&g cedar ceiling. It was time to re roof. I wanted insulation (there was none), but I didn't want to lose the rustic look. so I built up the roof from the outside. I basically laid a 2 x 4 stud wall 16 o.c. on the roof and had 3 inches of closed cell polyeurothane sprayed in between the studs. I put OSB on top. Used ice and water guard on the whole roof, then shingled. No roof vent. I think it's called a "hot" roof.
This approach seemed to make sense to me. I used to get gigantic roof to ground icicles. No more.
I'm interested in other opinions on this.
Flash and Batt - Bad!!
Martin,
My one word answer was for the upstate NY area and all areas North of Wash DC. IN the southern climates, it makes total sense! I agree with you about the thickness, but what I've typically seen is 1" and then fill it with batt insualtion and this is in upsate NY! this doesn't work as you mentioned Joe Lstiburek states. You need to have enough thickness to prevent condensation! But what is the cost associated with this? Why pay to have two crews in two different operations come and install two layers of different insulation material? Could it be just to appease the fiberglass companies and make them happy since their sales are down by 40-60% last year? That's the only reason why I see many insulation companies going in this direction. The cost to install 2" of closed cell insulation or 3-4" of open cell insulation is much less than that of 1" of closed cell and fill it with fiberglass and it's all done in one operation!! So, from a time standpoint and fro a cost standpoint, why wouldn't you just go with open cell and call it done?
Now to pick on Joe a little bit - Who determined how these climate zones were set? Did you know that they have the same Heating Degree Days (HDD) for different climate zones? It's also cold in some climate zone 5 areas than it is in climate zone 6. This doesn't seem to make sense if they only used HDDs to determine it! SO, Joe's 1" in climate 5, 1.5" in climate 6 and 2" in climate 7 doesn't make any sense when you start to look at it in terms of HDD!
Response to Aurora04444
Aurora04444,
In general, it's not a good idea to sandwich wood components between two layers of rigid foam.
If you choose to do it anyway, use the most permeable available rigid foam (EPS) for your exterior layer. Cover the exterior EPS with rainscreen strapping and do an impeccable flashing job, to minimize the chance of water entry from the exterior and to maximize the chance of drying to the exterior.
Response to Johnny X
Johnny X,
You didn't mention your climate. Your roof is better than nothing, but it has a very low R-value.
Your 3 inches of closed-cell spray polyurethane foam provides between R-19 and R-20. Such a roof does not meet minimum code requirements anywhere in the U.S. Even in Florida, the code says you need at least R-30 in your roof. In Climate Zone 6, 7, or 8, you need at least R-49.
Response to Jim Coler
Jim,
In general, heating degree days (HDD) increase as your climate zone number increases. Of course there are micro-climates within each climate zone, so that there are areas within each zone that vary. If a national climate zone map attempted to adequately account for micro-climates, the map would be far too complicated to implement.
Joe Lstiburek and his crew at the Building Science Corp. have been involved with research studies and field studies from Florida to Canada. Members of his team, bolstered by millions of dollars of DOE money funneled through the Building America program, have run countless WUFI simulations and verified the results of these simulations by field studies and field measurements.
Joe Lstiburek's recommendations for climate-specific foam thickness are the best we've got.
House must breathe
I have been intrigued by this entire topic now for more or less 25 or so years. At one time the flavor of the day was R2000 building codes in Canada, thus I certified etc.
The drive of course was the huge rise in fuel costs and everywhere you turned new approaches showed up to save energy costs.
What drove me crazy was the theory presented of how lousy buildings were in past generations, the focus was on air infiltration, energy loss and everything in between. The reason I was truly confused is that in reno job I did on an old building even going back to the early 1900 I never once saw rot problems in walls, not from condensation. Yes from poor water runoff but not from condensation.
I realized why, all of these houses were built to completely breath, ironically not by design; it just was as fuel was cheap. You simply pushed out more than came in.
I have visited with a project that was done 25 years ago when rigid foam with polymer modified concrete was toweled over. This was the beginning and no allowance was given to water evaporation or trickle out effect that you find say in brick construction. At this job the sheathing is all rotting out behind the foam.
Today, much has been learned from the solid no breath approach to rigid foam construction. Before the foam is attached to the wafer board, a spun nylon screen is attached to allow for condensation or water infiltration to run down to the base and out weeping points.
Regardless of much care you take to prevent punctures in the internal poly, questions such as where the framing lumber breath does and what happens as soon as the home owner moves in and starts popping holes for pictures etc.
I am convinced that an outside wall must be treated the same as an attic, if it cannot breath and expel moisture in 25 years it comes down.
Response to Mel
Mel,
Your description of wall failures from early EIFS installations is, of course, correct. "Barrier EIFS" installations failed by the hundreds; "water-managed" EIFS installations are performing well.
At the end of your post, you have provided an argument in favor of rainscreen siding applications, which make a lot of sense.
I live in a New York City row
I live in a New York City row house with mildly sloping flat roof. Temperatures range from single digits in winter to upper 90's, with high humidity. After I moved in I discovered that the space between top floor ceiling and roof was not insulated or ventilated, with appreciable heat loss in winter, and difficulty cooling adequately in summer because of heat gain (ceiling was actually hot to the touch.) Ice dams were not an issue. I installed fiberglass rolls with vapor barrier face down, then had insulation contractor cut holes in roof to blow in cellulose and leave ventilation stacks. It worked great.
A friend recently renovated a similar house and ran a/c ducts through the same unventilated and uninsulated space. He told me that he had condensation problem leading to mold on top floor ceiling. He ripped out ceiling, had ducts insulated (I don't know if duct insulation had vapor barrier) and the problem recurred. My first impulse was to recommend what I had done, i.e. insulating the space and ventilating it, as well as vapor barrier paint on ceiling ), but now I'm not so sure. Advice?
Response to William Etra
William Etra,
If condensation is occurring on the exterior of air conditioning ducts, they don't have enough insulation -- or else they were wrapped in the wrong kind of insulation.
A.C. duct insulation must either be vapor-impermeable (for example, closed-cell spray polyurethane foam) or must be covered on the outside by a vapor barrier. Most insulated flex duct includes fiberglass insulation surrounded by a polyethylene vapor barrier.
There are a variety of remedies. If insulated flex duct was used, then it should be replaced with ductwork with insulation of a higher R-value. If your friend did his own insulating, I suspect he used the wrong type of insulation.
If the existing ductwork is galvanized steel, then it's certainly possible to insulate the ducts with closed-cell spray polyurethane foam. This isn't cheap, but it's a high quality job.
Don't be tempted to cover the existing mess with more fiberglass insulation or cellulose insulation. These vapor-permeable insulations won't prevent the migration of warm, humid attic air through the insulation to the cold ductwork, where moisture will condense.
Basement walls in Maryland
I am planning on finishing my basement. I plan to put 2" of either Expanded Polystyrene (EPS) or Extruded Polystyrene (XPS) against the block walls, then frame (2x4), then drywall. I was also looking to put 1" of either EPS or XPS on the floor, then plywood, then carpet. Three questions - 1) Is this a good approach for the walls and floor in Maryland? 2) Should I drylock (or equivalent vapor retardant paint) the block walls and concrete foor first? To me, this seems to defeat the capability to dry inward or outward. 3) R values aside, which is better for this application EPS or XPS.
SIP panel concerns
Thanks for the reply Martin. I read the article on the Alaskan SIP panel failures when Joe wrote it and I'm taping all my seams before drywall. The roof is conventional shingles over roofing felt with Ice and Water on the edges. Thus far no issues, but I get nervous since I can't really tell if anything is happening, and until this coming winter, the SIP panel space hasn't been heated. This will be the first year we are actually living in the new construction side.
Response to Mike
Mike,
The minimum IRC requirement for basement wall insulation in your climate zone (Zone 4) is R-10, so if you are set on only 2 inches, it has to be XPS, not EPS.
Either foam will work, as long as it is thick enough. The blowing agents used in EPS are more climate friendly. Since the R-value per inch is lower, though, you'll need at least 3 inches of EPS.
You don't need to install waterproofing or paint on the block walls as long as they are dry and your basement has no moisture problems. If you have moisture problems, however, these must be addressed before you insulate.
Your plan for the floor is okay, as long as there are no moisture problems. I don't like to see carpet in a basement, but it's your house. The rigid foam should keep the plywood warm enough to avoid the type of condensation problems that typically lead to moldy carpet.
2nd Question-Basement walls in Maryland
Martin,
Thanks for the response. How about 2 inches of EPS against the wall, framing, and unfaced pink fiberglass insulation between the 2x4 framing, then drywall? Also, instead of carpet, do you recommend tile directly over the concrete slab?
Response to Mike
Mike,
1. I don't like to see any fiberglass batts on basement walls. If you want more than 2 inches of foam, just make your foam a little thicker.
2. The idea of insulating the floor is a good one, and the carpet will work. I was just expressing my own preferences when I said I don't like to see carpet in a basement. If you can keep it dry and clean, the carpet will work. You can also install any kind of tile you want -- but in either case the floor insulation is a good idea.
Question for Martin
You Said
Of course, new-home builders can't be reassured by the fact that 90% of homes with interior poly are performing well. If they were to choose a construction method that resulted in 10% failure, they would soon be out of business.
Is there really a failure rate of 10% in properly done classic vapor barriers in northern climates?
Response to Mark Klein
Mark,
No, I haven't seen any data on the percentage of homes with polyethylene that have problems due to the polyethylene. (Nor did I ever claim that 10% of homes have problems; I was discussing a hypothetical situation about an unspecified measure that results in a 10% failure rate.)
I suspect that few cold-climate homes have had problems. Many of the reported failures are in air-conditioned homes in mixed climates.
Concealed spaces
A question regarding my home in Minnesota, where we have very cold and dry winters -40F and very hot and humid summers +95F. The home is a 1919 bungalow (story and 1/2) home where significant portions of the upper floor ceilings are sloped, the construction is plaster on wood lath, full 2x4 rafter, spaced wood board sheathing, and roofing felts and asphalt shingles. There is a small attic area at the peak of the roof where we have flat ceilings on the upper floor.
A recent remodeling added closed cell spray foam to the attic, such as it was, to maximize the R-value of our 4" cavity. This was continued up to the peak of the roof creating a hot roof. The question is about the remaining concealed space, roughly 3 feet high by 28 feet long that runs along the roof ridge which is not ventilated to either the inside of the house or the outside. Does this area need ventilation? There was some concern that the spray foam in this space needed a fire barrier but there is also significant air space in here.
Response to Esteban
Esteban,
If I understand correctly, your house has a hot roof, with spray polyurethane foam spayed on the underside of the roof sheathing, all the way to the roof peak.
No, you don't need to ventilate the conditioned attic. Conditioned attics should not be ventilated.
The basic problem with your roof has nothing to do with ventilation; it has to do with R-value. You have chosen to insulate your roof to only R-26. The minimum R-value for roofs in Minnesota is R-49, so your roof has only half the insulation required by code.
Response to Martin
This is the interesting dilemma of owning a house that was built pre-code. We have vastly improved the performance of the roof/attic/insulation system and yet we cannot attain the code minimum. I should add that where is was possible in this "center attic" the insulation is thicker as there is physically more space for it and it likely does attain R49 where physically possible.
I really think the basic problem with my roof is that it can't physically meet code due to the 4 inch cavity and the dormers on the roof that preclude essentially building a new roof on top of it. The vast improvement that was made will allow this house to see 100 years and many more. As you know, the R value return decreases the more that is added such that the first few inches of insulation provide the most value. What we addressed was a more serious condition of air infiltration and heat loss.
So what I have chosen to do is to focus on what was physically attainable for an old house. Perhaps someday the Building Code will reflect the need to address existing construction differently than new in addition to going beyond R values to address air infiltration.
Thanks for your quick feed back!
Response to Esteban's second post
Esteban,
I certainly understand the limitations of working in an older house.
The next time you need to replace your roofing, consider adding rigid foam above the existing roof sheathing. If you do that, you'll be able to bring the R-value of your roof up to the minimum code requirement.
back again
Martin,
Indeed we considered rigid foam on top, but the dormers became an issue as the roof wraps around them. If we were to increase the roof thickness, we would have gotten into window replacement, among other cans of worms that didn't seem prudent to get into given our situation. Perhaps this decision will make more sense in the future.
Vapor / air barrier issues.
Surely, there has been a myriad of testing 2x4 / 2x6 homes across North America, and we still don't know the right answers. Look at asbestos...decades went by before anyone realized how dangerous it really was. We need testing to be more thorough to keep all of us safe, also, to protect our investments. What advantage would we have if we chose to follow the construction practices by masons, whereas, there would be a half an inch of air space between interior and exterior wall cavities. Would this hinder or help us?? I'm sure the cost of building a home would be inflated, but, could it work???
Response to James
James,
You are describing a rainscreen (a ventilated air gap between the exterior cladding and the wall sheathing). Of course it's a good idea. Builders all over the world have been doing it routinely on all kinds of buildings for years.
So, your proposal is not a new idea.
fiberglass insulation
Adding to the trouble: Last year I demolished a building and needed an "environmental report" to satisfy the city that there wasn't an asbestos or other hazardous material issue on the 60 year old Cape Cod style home. For $1,000 a few young engineers (mid 20's) and the supervisor (mid 40's)show up and take samples of the sheet rock, compound, brick, mortar, flooring etc. in search of things that would be considered dangerous and must be "mitigated" before demolition. I asked the guys what they felt was the next environmental hazard for lawyers to sue over and to be "mitigated" in the future and they all bust out simultaneously "FIBERGLASS INSULATION" and chuckled perversely. Obviously when all the asbestos and lead is cleaned there has to be another big bad boogieman so now we know what to expect. I don't think I could build using that material based on that survey, but I would like to know what else other environmentalists (who we know have mega-influence politically) have to say...By the way- the house had no insulation, no vapor barrier, poor flashing and substantial rot everywhere.
sheathing wet under eps
Great discussion here. I think I might have a problem. It is raining hard here today (BC coast) and I know that the sheathing under one wall of my project is now wet under 1.5" of eps. Do I need to pull the eps to allow the sheathing to dry before I install house wrap? Many thanks!
Increasing vapor intrusion
I'm a buliding Science expert from Alaska, so I have a different perspective. Osmotic pressure forces water through the wall from the inside most of our year, so a vapor retarder makes a lot of sense. I'd say if your climate is 5,500 HDD (heating degree days) then you should have an interior vapor barrier. If you are going to use exterior insulation, avoid closed cell, high-perm products like polyiso, any closed-cell foams, or foams with a "face"-that is, an aluminum or plastic layer on the foam. Usually the best outside insulation is a layer of cellulose in a non-load-bearing stand-off wall configuration with drainage plane and bulk water management built-in.
Re: sheathing wet under eps
If the EPS has a plastic or foil face that's in contact with the sheathing, you may have a problem. 1.5" of EPS has a perm rating of about 2, so its not by any means a vapor barrier--with a pressure difference of 1 in. Hg, two grains of water per square foot per hour is drying from the sheathing, which is pretty good--it should be dry soon. If, on the other hand, that EPS has a plastic coating, that will slow to about .08 grains/ft2/hr, thus the OSB will never dry. Tear EPS coatings off when used on the outside; if you installed the EPS with the "face" on, you'll want to tear it off. Sucks, but so does rotten, wiggly sheathing.
Thanks Garrison. My sheathing
Thanks Garrison. My sheathing is .5'" ply, not osb, and yes the eps has foil on one side and plastic film on the other. What do you think?
Response to MJB
MJB,
If your house is under construction, the obvious question is, what's on the interior side of the plywood sheathing? If your stud bays are empty, the plywood can dry to the inside.
Response to Anonymous from Vancouver
Anonymous from Vancouver has incorrectly identified the weather in Vancouver, BC. It has nothing to do with the days of frost (although we get weeks of below 0 weather of late), it has everything to do with the dew cycles, and Vancouver has some of the highest dew cycles in the country.
Yes you can get rid of the VB, but this has traditionally also been used as an Air Barrier. The reason the old homes do not have a problem is because a LOT of air flows through the wall assembly and dries things out. This is great for building integrity but sucks for energy use. You can build a wall that is both energy efficient AND able to self dry if you find a designer that is knowledgeable in calculating dew points and vapour permissibility.
Sean Wiens - SENWI House Inspections.
Response to Sean Wiens
Sean Wiens,
There are several simple options that are safer than interior poly.
The Airtight Drywall Approach can be used as an interior air barrier.
MemBrain can be used instead of interior poly.
Response to Martin re removal of poly
Hi Martin,
I totally agree. I was just pointing out that just getting rid of the ploy alone is not the solution. I have met several people in Vancouver that state they slit the poly after the building inspector leaves. I find this appalling and irresponsible. These are people that do not understand the need for an AIR barrier and make no other accommodations to provide an air barrier once they slit the poly.
As a side note, I am planning a reno next year in which I would have a mixture of old and new construction. I am planning on taking everything down to the studs (internal and external). My goal is to end up as close as possible to a Passive Home (limited heating requirements)
I was thinking of the following wall cavity make up starting from the exterior- can you provide a critique
- cladding (mixture of cedar siding, cementisious siding/wall shingles, other)
- Batton providing rains screen gap
- Tyvek or Typar (still trying to decide on which is best). This will be sealed by means of a blower door fan test and will be the AIR barrier
- 1" - 2" of EPS foam (want it to be vapour permeable so wall breathes outward
- plywood or ship-lap (will reuse ship-lap where possible)
- will fur out existing 2"x4" wall to a 2"x6" thickness
- either will fill cavities completely with closed cell spray foam (if I can afford it) or put at lest 3.5" to act as a vapour barrier/retarder and then balance with Roxul insulation (if all spray foam, would ensure inside face of stud was unsprayed to allow wood to dry to interior)
- NO poly
- drywall with latex paint to allow inward drying
I could also put a 2" layer of XPS between the studs and the outside sheathing if recommended and stay with just the 2" x 4" wall. The way I see it, this allows the wood elements in teh wall to breath to the inside or the outside depending on their location, removes ALL air flow through the wall assembly (which should eliminate most water vapour issues) and as long as the interior humidity is managed with mechanical ventilation, all should be good,
I plan on having the thermal mass needed for passive homes in the floors (concrete slabs)
I would appreciate your wisdom. Can you also contact me off list as I would love to get an article from you for a newsletter I publish for home inspectors in BC
Cheers
Sean
http://www.theBCInspector.ca
Response to Sean
Sean,
I think your planned assembly will work.
Planned Wall Assembly
Martin - can the proposed wall system be realistically/practically improved in any way?
Peter - you sometimes differ with Martin in your opinion. Can I have your take on my proposed wall system?
Much appreciated!
Retrofitting a summer cabin
I just purchased a summer cabin--2 x 4 construction, crawl spaces, drywall, old redwood siding, no insulation--near San Francisco (Marin) to use as a year-round home. I can't have anything in the house that off-gasses. I intended to use cotton insulation but have just discovered that there are rats nests in all the walls. I am pretty scared by the dialog on this page. If I end up with mold, I may be dead.
My designer recommends Air-Crete. The insulation guy who is coming to do an estimate recommends formaldehyde-free fiberglass. My builder wants to use something like Thermo-Ply (I think) and I'm not sure he knows what a rainscreen is.. I would really appreciate another level of advice. Thank you.
Response to Sean Wiens
Sean Wiens,
Any wall can be improved. The limit is set by your budget.
I'm a big fan of putting insulation on the outside of your framing and sheathing. That's why I like the PERSIST method. If you can afford the investment, you can install much thicker exterior foam and leave your stud bays empty.
Response to Lisa
Lisa,
Your question is too complicated to answer with the information you have provided.
1. Two of your statements -- "I can't have anything in the house that off-gasses" and "If I end up with mold, I may be dead" -- imply that you have special medical problems. If my guess is correct, only a physician can make medical recommendations. (Don't depend on builders for medical advice.) We don't know what your condition is or what you are trying to avoid. So get your doctor to make a specific list of recommendations, and give that list to your builder.
2. There are lots of ways to keep a wall dry and mold-free, but we don't know your budget or what parts of your house to save. Obviously, you don't have to change the house. Just live in it the way it is, and keep pumping energy through the walls. If you want insulation, though, you'll have to change it. You may have to remove the siding -- perhaps carefully, for reuse, or perhaps in a way that doesn't allow it to be salvaged -- so that you can install sheathing and exterior insulation. But we can't recommend that path if you have your heart set on saving the siding.
Thanks Martin, you're right
Thanks Martin, you're right and the sheathing is dry now.
On another note, you say that if there's enough outsulation you can leave your stud bays empty. But why leave them empty? Why not use the space to achieve the desired R-value and mitigate the complicated detailing around openings that comes with using thick outsulation?
Response to MJB
MJB,
Either way will work if you get the details right. Here are the advantages of empty stud bays:
1. Life is easier for electricians (and, in some cases, plumbers).
2. There is no risk of condensation against the wall sheathing -- something that can happen if your stud bays are too well insulated and the foam is too thin.
3. In the unlikely case of water intrusion, the sheathing and framing dry much faster.
More for Martin
Thanks, Martin. But your reply confused me.
Like a lot of women I know, I have moderate chemical sensitivity and allergies to mold and dust mites. My only doctor is a gynecologist.
I am going on the "pail theory"--my pail is obviously not as big as a lot of people's, since I already have problems, and I don't want to get really sick by moving into a newly-renovated building that off-gasses.
I have read books on green building, but I can't become an expert. I can only do the best I can. What I am reading says to super-insulate, but not to add to your "pail" in the process. Are you saying I shouldn't insulate at all?
And are you saying I should remove all of the siding? The siding isn't moldy. I just don't want to *create* mold by e.g. putting in a vapor barrier that will do more harm than good.
I have my heart set on saving my health. I have a "budget" (actually a cap, there is no budget--an entirely different subject) of $100,000 for the entire renovation--the cabin is a 32 x 20 box, and my agent said that was enough to do it right. i want to do it right. I thought I knew what that meant. Then I discovered 'building science."
Response to Lisa's second post
Lisa,
If you have allergies, I assume that at some point you consulted a physician who diagnosed your problems. I don't know what "moderate chemical sensitivity" means. Have you ever been sick because of exposure to certain chemicals? If so, did you see a doctor? Which chemicals made you sick?
I agree that you don't want mold. The best ways to avoid mold are:
1. Design your wall assembly to handle wind-driven rain; I suggest good flashing details and a rainscreen siding installation.
2. Design your ceiling and wall assemblies to avoid condensation problems. There are a wide variety of insulation products that can accomplish this.
3. Keep your indoor humidity low; this may require the use of an air conditioner or dehumidifier, depending on your climate.
4. Install a whole-house ventilation system.
Vapor retarders
I have been building with visquene on the interior and 1" styrofoam on the exterior no sheeting for 25 years with no problems and people love the insulated values. But I continue to see problems without it when opening walls with OSB with mold and early rot from moisture from inside condensation cold corner mold and wetness into the carpet. House wrap stopped at corners uncovered walls rain driven and moisture condensation on the exterior OSB swelling mold and rusting nails. I'll stick with my 1" styro exterior 2 x6 2' on center walls cellulose insulation and visquene wrap. Tyvek where needed.
Vapor barrier
I have read through the full thread and Im still confused! Ok I have a 35 yo ranch style home that has steel siding then 1/2 black (Buffalo?) board. Looks like a thicker type of tar paper board. The inner wall board is OSB. Walls are framed with 2X6 studs then standard pink insulation with plastic vapor barrier and drywall.
Because the house leaks air like a sieve we want to remove the outside wall drywall and seal the sheeting to the studs with closed cell spray foam then re-install the pink fiberglass insulation and dry wall.
The question is if I need to replace the vapor barrier?
In central Montana we have COLD winters low humidity.
I want to use a roto zip and leave a strip of drywall above the floor trim and below the ceiling.
Thanks!
Response to Mike Hoyt
Mike Hoyt,
1. House number one: I would put the plywood against the studs, on the interior side of the foam, to provide bracing for the wall studs.You don't have to worry about "reflection" from the foil facing onto the siding, because the polyiso will always be in the shade. It would be best to install 1x4 vertical strapping over the foam, however, to make it easier to attach the siding.
2. House #2 will work, as long as you use closed-cell (not open-cell) spray polyurethane foam. The R-value is OK, but nothing to write home about -- only R-20 to R-26.
Pole barn Insulation
I have a 72by64 pole barn built this last August. It has 12 inches of blown in cellulose in the ceiling with vented ridge and eves. We put 1 inch closed cellulose spray foam directly on the exterior steel sheets to seal it up. There is also 6 inches of fiberglass bats with no backing, then the inside is lined with steel sheets, no vapor barrier on the inside. We have condensation between the foam insulation and the fiberglass, enough to make some puddles on the floor. The fiberglass is actually froze to the foam in spots. I have been told that I need to tear off the inside steel sheets, take the wet fiberglass out and put in new (dry) fiberglass back in and put up a plastic vapor barrier. Will this solve my problem? What should I do now?
Vapor barriers in new home in North Okanagan, BC Canada
We built a home with 2 X 6 stud walls, fibreglas insulation and polyiso spray foam around vents and critical areas. We have housewrap outside the exterior plywood sheathing and will install 1" rigid foam prior to a rain-screen and then Hardie siding. The frame got very wet prior to the roof completion, and I made sure that interior poly vapor barrier was not installed after insulation as we began heating (infloor radiant heat) right after lockup was complete. The stud walls have now dried significantly (after removal of sections of fibreglas to allow drying of the sheathing and stud walls while using a dehumidifier). Should I leave out interior poly vapor barrier step?
We have a walk-out basement on our south side (conventional 2 X 6 stud walls), with a full-height concrete wall along north and east sides of the basement. How should insulated areas of concrete wall in the basement be treated? Vapor barrier was installed during insulation in those areas.
Response to Cherilyn
Cherilyn,
First of all, your need to comply with existing BC building codes. I'm not familiar with the code in your area.
You don't want any interior polyethylene on your above-grade walls. Since these walls have exterior foam, they won't be able to dry to the exterior -- only to the interior. That means no interior poly.
You don't explain how your below-grade concrete walls were insulated. I hope they weren't insulated with fiberglass batts. These walls should be insulated with rigid foam or closed-cell spray polyurethane foam. They should not have any interior poly.
Response to Martin
The BC building code specifies the use of 6mil interior poly....although my home is being built outside of any areas where building inspectors have jurisdiction.
The below-grade walls were insulated with fiberglass batts, although the sill areas used polyiso insulation (1' area where the floor trusses sit on top of the concrete walls). Should I pull the interior poly off the below-grade walls? I don't really want to change the insulation there as that is fairly standard treatment here and I have paid for the materials and labor already....but am willing to listen...!
Fiberglass batts for below-grade walls?
Cherilyn,
I wouldn't leave any fiberglass batts in my basement. But only you can make the decision for your house.
You might want to research the issue further on the GBA Web site and the Web site of the Building Science Corporation (http://www.buildingscience.com).
Good luck.
Log in or become a member to post a comment.
Sign up Log in