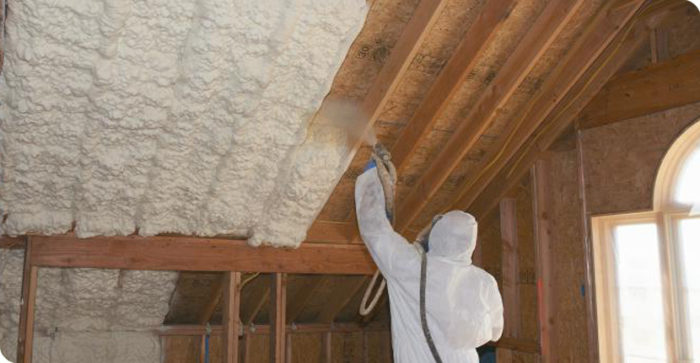
Image Credit: dunktanktechnician/ CC BY 2.0 / Flickr
Planning a new house in Climate Zone 6, Chad Kotlarz is reviewing his architect’s plans for the roof — and discovers he has a few misgivings.
The unvented roof will be framed with 2×12 rafters, sheathed with plywood and capped with standing-seam metal roofing. Closed-cell spray foam will insulate the rafter bays, and the interior of the cathedral ceiling will be finished with gypsum drywall. An exposed truss with a collar tie provides structural support.
“The main concern is with the thermal bridging from the 2x12s,” Kotlarz writes in Q&A post at Green Building Advisor. “The roof is a 10/12 pitch, with a dormer and two valleys. I was told that the thermal bridging created from the 2x12s would cause hot/cold spots in the roof and would lead to problems with the metal roof. I’m assuming this is from expansion/contraction or condensation, but I’m not certain.”
For reasons he doesn’t explain, Kotlarz doesn’t want to use rigid foam on top of the roof sheathing or on the interior, so those approaches to thermal bridge reduction won’t work.
Will thermal bridging through the rafters cause problems over time, such as rippling in the metal roofing or condensation in the roof framing?
Those are the questions for this Q&A Spotlight.
Consider using scissor trusses
Stephen Sheehy, who built a well-insulated house with a standing-seam roof in Maine, suggests that Kotlarz look at a different way of framing the roof. Sheehy used raised-heel scissor trusses that were deep enough to allow about 20 inches of cellulose plus a ventilation space.
Raised-heel, or energy, trusses are extra deep at the building perimeter to provide more room for insulation than a conventional truss. “A nice benefit to trusses,” Sheehy adds, “is the ability to put…
Weekly Newsletter
Get building science and energy efficiency advice, plus special offers, in your inbox.
This article is only available to GBA Prime Members
Sign up for a free trial and get instant access to this article as well as GBA’s complete library of premium articles and construction details.
Start Free TrialAlready a member? Log in
5 Comments
Solutions for "Lack of drying potential"
How about using:
http://www.cosella-dorken.com/bvf-ca-en/products/roof/underlayments_metal/products/trela.php
or:
http://www.roofaquaguard.com/synthetic-underlayments/dry-tech/
between the roof sheathing and the standing-seam metal roofing?
These will provide an airspace under the standing seam roofing for ventilation and drying.
Peter's venting space is critical
Peter stressed the important point: allow the roof to dry. Venting under the metal roof is needed. You can get condensation on the underside of the metal roof further slowing the summer drying (night sky effect). And don't muck up the deal by sealing the whole roof deck with ice & water shield.
Recommend you research solutions applied to SIP roofs in Alaska at the roof peak. You're constructing a site-built SIP. Consider the venting solutions that came out of those studies.
I recently had a local metal roofer offer something like C.B
We have a roof that has closed cell foam insulation applied to the underside of the roof deck and need to replace the old concrete roof shingles. The roofer had a styrofoam product about 1.5" thick with ~1/2" channels on both sides that he combines with a ridge cap to achieve soffit to ridge ventilation above the roof deck and a thermal break. Not sure anyone has experience with this or something similar. We are still considering options including just adding 2" of rigid foam to the roof deck and installing standing seam over top without ventilation.
BSC Resources
As discussed above, the main issue with spray foam in the rafter cavities without continuous insulation is the thermal bridging through the wood rafters. The consequence of it is mostly embarrassment due to differential frost lines forming on your roof:
BSI-063: Over-roofing—Don't Do Stupid Things
http://buildingscience.com/documents/insights/bsi-063-over-roofing
I concur with Peter Yost that metal panels buckling due to thermal bridging sounds highly unlikely--these systems are designed to handle movement.
As for drying potentials and spray foams, one excerpt:
PA-1401: Are You Doing Something Stupid?
http://buildingscience.com/documents/published-articles/pa-are-you-doing-somethig-stupid/view
As further background, a research report from 2013 on a field survey of spray foam roofs:
BA-1312: Application of Spray Foam Insulation Under Plywood and OSB Roof Sheathing
http://buildingscience.com/documents/bareports/ba-1312-application-of-spray-foam-insulation-under-plywood-and-osb-roof-sheathing/view
Risk
The excerpt kohta posted:
"There is no greater risk of roof damage with SPF, regardless of type, under a roof deck when exposed to a leak than the risk compared to structural insulated panels (SIPs) or typical commercial compact flat roofs."
Somehow seems like cold comfort to me. I've always though of SIPS and commercial flat roofs as fairly risky assemblies and not ones I'd look to emulate in terms of durability or resilience.
Log in or become a member to post a comment.
Sign up Log in