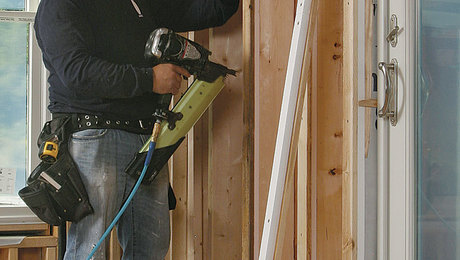
Writing from Long Island, New York, Joe C describes repairs that he’s been making to his house to correct water and insect damage. Two of the four walls of the room are exterior walls, and Joe is concerned that thermal bridging through the new framing he’s adding significantly degrade energy performance.
“With all the extra studs, I’m concerned there will be a lot of thermal bridging,” he says in a Q&A post. “To counteract this I’m considering installing rigid foam [insulation] on the interior side of the wall framing.”
For reference, on the outside of the studs is a layer of exterior gypsum board, followed by a small air gap, and then brick veneer.
His plan is to insulate the stud cavities with fiberglass, then add 1/2-inch thick extruded polystyrene (XPS) on the interior side of the wall before installing drywall over the rigid foam. The only 1/2-inch foam available from Home Depot is Owens Corning Foamular, which he says has an R-value of 3.
“Is this a reasonable plan of attack?” Joe C asks. “There shouldn’t be any issues drying to the outside. Would condensation on the outside face of the foam board in the summer (AC on in the house) be an issue?”
That’s where we start this Q&A Spotlight.
The foam isn’t thick enough
Martin Holladay doesn’t try to steer Joe C away from his interior insulation approach, but he does suggest the layer of foam Joe wants to use isn’t thick enough. For starters, a realistic R-value for 1/2-inch rigid foam is R2.5, not R-3.
“I don’t think it’s worth doing with less than 1 inch of rigid foam,” Holladay says. “Of course, 1 1/2-inch foam would be even better.” For more details, Holladay…
Weekly Newsletter
Get building science and energy efficiency advice, plus special offers, in your inbox.
This article is only available to GBA Prime Members
Sign up for a free trial and get instant access to this article as well as GBA’s complete library of premium articles and construction details.
Start Free TrialAlready a member? Log in
3 Comments
Thank you for a very interesting article. I am strongly considering to follow the interior rigid foam approach for much of my insulation upgrade - I have a mostly brick veneer exterior in zone 6. I do have a lingering question.
In the expert opinion section, Peter Yost states that interior rigid foam : "makes the entire assembly exterior to the rigid insulation colder in the winter..."
What is the problem with making the sheating colder?
I believe it would make the dew point higher, but given sufficient attention is placed to air sealing, is it a theoretical issue or an actual concern?
Thank you for helping me understand.
Hi Sofiane -
When insulation makes any type of wood sheathing colder, it just means that it is experiencing less drying over time. Since colder means wetter it means higher potential for degradation of moisture-sensitive materials.
It's not that materials can't get wet and then dry with little to no problem. It's more of a problem when they stay wet for longer periods of time.
Peter
Thanks so much for this article because I have been thinking about this for a while. We are about to do a kitchen remodel, and want to add R value to about 150 sf of a south-facing wall that has perfectly good stucco on the exterior. We are in a hot-dry climate (45F year-round) in Los Angeles.
I have more questions about using rigid foam on the interior. I was thinking of using 2 layers of 1" or 1.5" rigid foam, staggered to reduce any water vapor issues when it does get cold. If there are any holes that escaped air sealing, such as screw holes to mount cabinetry, do we need to worry about indoor water vapor escaping into the framing cavity that would cause condensation issues (per Peter Yost's comment)? Or does stucco dry out well enough to avoid that? Or is the wall cavity warm enough with 3.5" of batt insulation? Is it overkill to do 2 layers of rigid or fine to do 1 thick layer with tape?
Would it be better to use rigid mineral wool (to allow better drying and be more environmentally friendly than foam) or maybe even just furr out the wall to add more batt insulation? We were thinking rigid board would be easier, but it looks like getting rigid board mineral wool is a lead-time issue these days (6 months or more?!). Because of this we are even considering the more expensive furring out of the wall, too. And if we furred out the wall, then the studs would be staggered to solve thermal bridging, correct?
Thanks for your help!
Log in or become a member to post a comment.
Sign up Log in