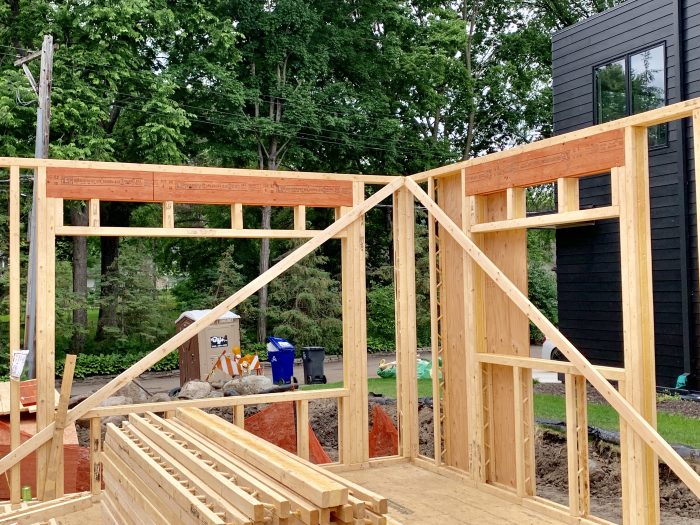
High-performance exterior walls typically handle thermal bridging at framing members in one of two ways—either the building is wrapped in some thickness of continuous rigid insulation outside of the sheathing or the home is framed with staggered, double-stud walls. Each of these two approaches has drawbacks. Window installation is more complicated. There are new details for carpenters to master in terms of managing structural and hygrothermal loads. And these options are also more expensive than conventionally built and insulated walls.
Enter inventor Brian Iverson and the Tstud. Tstuds are an alternative to solid 2×6 framing lumber. Tstuds can be used for pretty much any framing element in exterior walls: studs, jacks, cripples, plates, and headers. They are designed for advanced framing—24-inch on center, with single top plates, and two-stud corners. Tstud are designed to break the thermal bridge within the stud itself.
How Tstuds work
Each Tstud has two 2x3s on the flat connected by angled wood dowels. The empty space between the 2x3s is filled with closed-cell spray foam. The dowels are installed at compound-angles to provide greater structural stability to the 2x3s. On one face of the Tstud, the dowel dead-ends into middle of the 2×3 for added structural strength. The 2x3s are all No. 2 grade lumber with up to a 30% wane. “We just turn any wane to the inside so we get nice exterior faces to each Tstud,” Iverson said.
With this design, Tstuds act like engineered trusses, not solid sawn lumber. So, Tstuds need full bearing across the truss. This means, for example, that when used as bottom plates, j-bolt anchors are connected to the Tstud with a metal plate that spans the truss. When building with Tstuds, care must be taken to cut no more than one consecutive dowel in order to maintain structural integrity. Fortunately, Tstud has an excellent installation guide that addresses many of these installation and configuration considerations. You can find it here: Tstud Installation Guide.
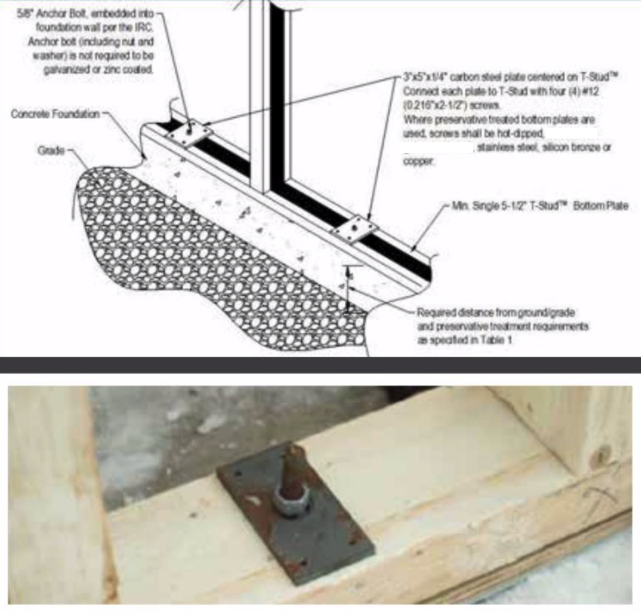
The BASF Spraytite 158 HFO-blown closed-cell spray foam fills the open web space with R-6.6 per inch airtight insulation creating a reported R-20 TStud. I asked Iverson of the report’s assignment of the full initial R-6.6 per inch rather than the industry-accepted aged value. “The HFO blowing agent used is new enough that there really is no aged R-value per inch,” he told me. The reported value in BASF’s Evaluation Service Report (ESR 2642) is indeed R-6.6.
No doubt, the Tstud is an elegant design in terms of strength and thermal performance.
An internet sensation
Iverson and Tstuds have taken the internet by storm, at least the parts of the internet that cover the building industry. This is in no small part because of a Tstud-sponsored video posted by Matt Risinger on his Build Youtube channel. According to Iverson, the video led to more than 978,000 views in the first three weeks after its release, more than 8,000 unique potential customers, and 22 new customers from Kentucky alone.
“Our initial business model was to go after local and regional lumber retailers/distributors, essentially pushing Tstuds into the supply chain. But their uptake on innovative lumber products is generally pretty slow,” Iverson told me. “Between Risinger’s video and social media activity, we have ended up marketing and selling quite a bit to builders directly, reversing the way that new building products get into projects, pulling supply to lumber retailers and distributors.”
At a recent event for the Greater Grand Rapids Home Builders Association—a longtime progressive and innovative local HBA—125 builders came to see Iverson and the Tstud.
Thoughts from an early adopter
Jesse Hartung of Modern Construction built his first Tstud home in 2016 and has been using them ever since. He’s built nearly 20 homes in the last three years using the new framing system (Jesse is the featured builder in the Risinger video).
“Our standard exterior wall was 2×6, 16-inch on-center, with R-19 fiberglass batt and 6-mil poly,” Hartung told me, “The studs were simply getting too cold, generating lots of callbacks for nail pops. The switch to Tstud’s advanced framing package has virtually eliminated those callbacks.”
This makes Jesse’s switch a great cost case study. Tstuds are not cheap—about $2.50 per board foot vs. around $.50 per board foot for 2x6s. But Tstud’s advanced framing approach means 24-inch on-center, single top plates, and virtually no deep-member headers at doors and windows. “It’s not an apples-to-apples framing member comparison between 2x6s and Tstuds,” said Jesse, “There is definitely a premium, but for my company, the builder premium on a typical home is around $1800 – $2000, with our largest home running about a $7500 Tstud premium. More than worth the cost,” concludes Hartung.
When I asked Hartung about any disadvantages to TStuds he was quite straightforward.
“As with anything new, no one likes the changes. But our crews, from framers to electricians, have learned how to be as fast with Tstud exterior walls, if not faster, than our former standard walls. One Tstud quirk is electrical boxes on exterior walls. The nails for most boxes are located too deep to catch the 1.5-inch deep Tstud (from the side). Turns out that for some strange reason, electrical boxes from The Home Depot in our area have the nails more toward the front, so we just pick up enough for the exterior walls. Or, one guy discovered that if you take the nails out and flip the box, that works too!”
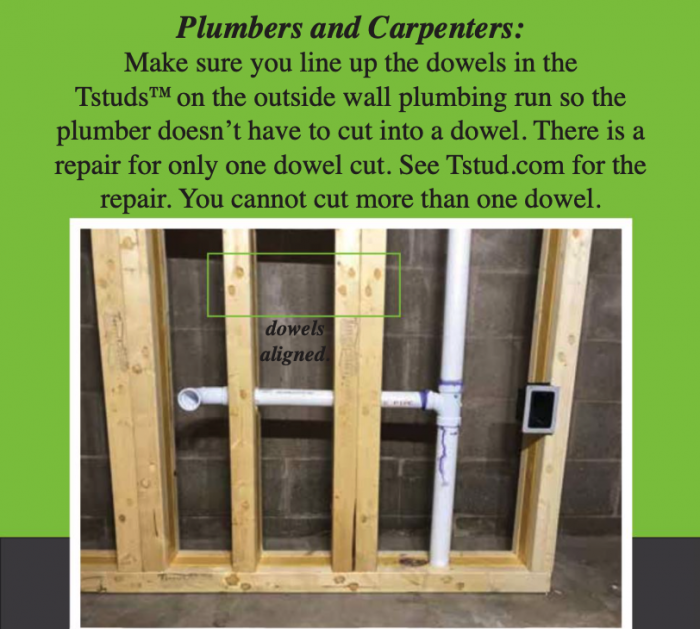
In my interview with Jesse Hartung he surprised me with his new exterior wall configuration: “Our new exterior wall is Tstud framing, ZIP wall sheathing (as an exterior air barrier), using the same R19 fiberglass batts, and poly as the vapor retarder. I bought a $100k closed-cell spray foam rig a ways back, but for me the spray foam works great for rim joists and eaves but I like the fiberglass batt and poly just fine.”
Tstud is agnostic about what a builder chooses for cavity fill insulation.
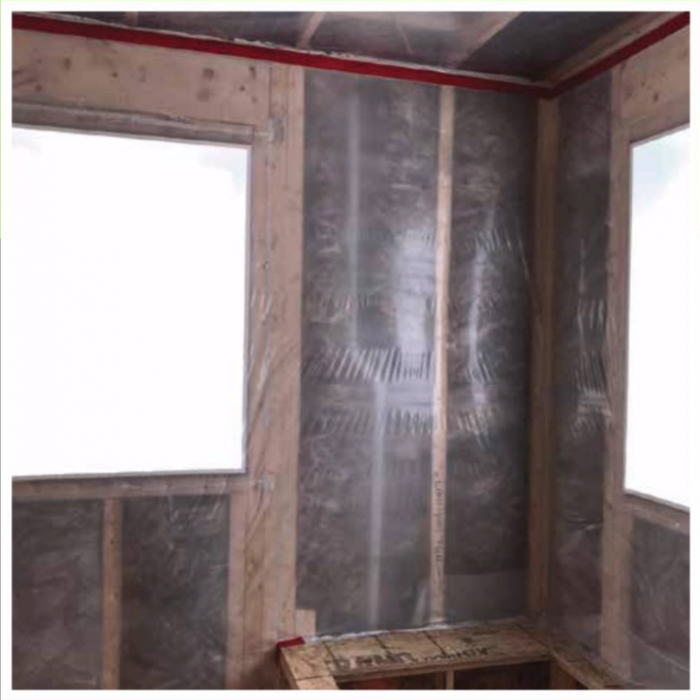
More innovations to come
Tstuds are a specialty product and they need to be configured by the manufacturer to satisfy different needs. The company plans to continue to innovate around the first-generation Tstud including the following:
- After attending a Passive House event in New York City, Iverson is committed to developing a 2×8, R-30 Tstud.
- For certain locations and for Tstuds as bottom plates, at least one 2×3 chord needs to be treated. The plate treatment Iverson has selected is NexGen, which has great fire performance as well. Treated Tstuds are reported to achieve a Class A fire rating (flame spread using ASTM E84 of less than 25).
- Wouldn’t it be cool to use some sort of Tstud in roofs and floors? Those Tstud products are under development.
- Iverson is now heavily promoting the Bare Naked Tstud, which has no insulation and allows builders to fill the thermal break with whatever type of insulation they would prefer. This new product has proven to be of real interest to modular and manufactured home builders.
For a full slate of currently available Tstud and new products under development, see Iverson’s Roosevelt Energy Technologies website.
The bottom line
Like many of us—last time I checked, the video had well over 1M views—I watched the Matt Risinger Tstud video with intrigue and excitement: a new and innovative approach to exterior walls—yowza! And there are a lot of advantages to the Tstud framing solution. Here are my reservations now that the video buzz has worn off:
- Cost: Compared to double-stud walls and continuous exterior insulation, I am just not convinced that Tstud’s are superior, or superior enough, given their cost. Having said that, I don’t like most cost comparisons, and this is even more true for Tstuds, since they are not a 1:1 functional substitution for 2x6s. I think in the next 6 months to a year, as more builders in more markets use the TSud system and Iverson gets the economies of scale with larger production facilities, the cost issue will be more clearly sorted out.
- Strength: Iverson is really convincing in showing how much more compressive strength the Tstud has compared to a 2×6. But for many, if not most single-family homes, 2×6 advanced frame walls are perfectly adequate structurally. I do think that there may be convincing advantages to Tstuds in larger wood buildings where superior compressive framing member strength is a real fit for Tstud. Iverson is going after that market aggressively.
- Business models based on social media and page views: Both builders and manufacturers can jump to action based on web buzz. I am not saying that is true for Iverson or builders initially attracted to Tstud, but I am going to wait and see on this one. I am just not sure that the advantages of a fixed product will prove a clear cost and performance winner over the more malleable double-stud and exterior insulation wall systems.
Maybe I am just getting old. My aversion to social media and particularly Instagram could be age-based instead of both being truly glitzy and distracting pastimes.
Peter Yost is GBA’s technical director. He is also the founder of a consulting company in Brattleboro, Vermont, called Building-Wright. He routinely consults on the design and construction of both new homes and retrofit projects. He has been building, researching, teaching, writing, and consulting on high-performance homes for more than twenty years, and he’s been recognized as NAHB Educator of the Year. Do you have a building science puzzle? Contact Pete here.
All photos and graphics were provided by Tstud.
Weekly Newsletter
Get building science and energy efficiency advice, plus special offers, in your inbox.
33 Comments
Neat product.
One of the benefits of a conventional lumber (especially a 2x6 (16" oc) and 2x8) is that you can cantilever the stud some over the slab edge and/or rim joist edge. This allows for a couple of inches of exterior rigid insulation to be added at those areas. Continuous exterior rigid insulation on walls allows for the same.
This doesn't seem feasible with t studs and may constitute a weakness from a design perspective.
Have Tstuds been tested for use in seismic zone construction?
I think is great to be able to have a near continuous R20, R23 or R25 exterior walls. The issue with lining up the dowels for plumbing, I would assume if the Tstuds come in standard stud precut lengths, it should no be a problem, till you need 12'-22' studs in large homes. I do have a concern with cost increases of $2K+ for an average house. That's $1/sf on just framing, where I think taped outsulation will easily cover that, plus it gives me a chance to have an additional air seal and moisture barriers for the same or less money. Finally, if the cost of Tstuds were not an issue, I think its worth taking a second look.
Hi RIck -
You are correct; as a truss you can't load unevenly across the truss. You would need to get a structural engineer, or maybe someone from TStud to engineer any cantilever of the Tstud.
Peter
HI John -
In this TER for TStud (https://www.drjcertification.org/system/files/drj/ter/node/1567/ter1603-06tstud.pdf), it states:
"9.5 TstudTM is not currently permitted to be used in areas where the Seismic Design Category is D, E, or F"
But you should check with Brian Iverson at TStud because he has been working on getting approvals for hurricane- and earthquake-prone areas of the US.
From the Roosevelt Energy Technologies website you gave: "The Tstud™ has been tested and passed for all Hurricane and Seismic Zones in North America, up to 16’ tall in exterior walls."
Exciting product, but it's unfortunate that after decades of know how production builders and a majority of custom builders simply have had no reason to deviate from 16" OC stud spacing.
The path for widespread adoption by builders of engineered products really depends on one thing: Whether they are taken up and available in local lumberyards. T-studs are just like LVLs and I-joists. They were specialty products you rarely saw until you could pick-them up without having to order them. Being able to get more or return excess is critical. If they remain, like engineered roof trusses, something you need to order exact amounts of in advance, I don't see them succeeding.
I had always wondered about this concept - not specific to this particular product, but more along the lines of I-joists. For exterior walls you only need the equivalent of a 2x4. Then you could connect that with just about anything to an interior stud; even a 2x2 is sufficient to hang drywall from on most walls.
The interior web could be inexpensive OSB with large holes cut in it to both accommodate wiring and to reduce thermal transfer, and blown-in insulation would fill in the web holes and the differing thickness of the assembly. The straight line edges of the web material would ensure straight interior and exterior walls, and would at the same time stiffen the assembly. This seems like a no-brainer to me, but am I missing something?
Wall thickness could be adjusted simply with different width OSB webs between the interior 2x2 and exterior 2x4. Again, why would this be difficult to work out?
I'm aware of the use of Larsen trusses that hang off the exterior of a home. But using an I-joist-like stud that would sit on the floor deck conventionally would, seemingly, simplify building a double-stud wall, as pointed out in the article on T-studs ; conventional exterior detailing without the use of exterior foam probably being the primary issue.
Zolton Cohen
> “Our new exterior wall is Tstud framing, ZIP wall sheathing (as an exterior air barrier), using the same R19 fiberglass batts, and poly as the vapor retarder {Minnesota}.
Would be interesting to see a cost and performance comparison of T-studs vs 1.5" of exterior EPS.
We don't use 1.5" in DFW, but our prices are for 7/16 OSB $8 + 1/2" R3.2 polyiso $10 + $.25/sf tape install vs. ZipR3 $30 plus tape install. For 7/16 OSB $8 + 1" R6 polyiso for $21 + $.25/sf tape install vs. ZipR5 $39, plus tape install. For us, is not even close.
I just updated a better price for ZipR.
The only time ZIP-R seems to make financial sense is in very high labor price markets or where there is a serious CALENDAR TIME = MONEY aspect to a particular project.
ZIP-R might be easier to deal with in markets where crews are completely unfamiliar with how to properly detail a separate layer of foam (not that it takes a major education program to get people up to speed.)
If I may digress a little -- what's the story behind putting the cripple studs UNDERNEATH the header in that first photo? I've never seen a window framed that way.
Structurally, there is no problem doing that, however, I rather have the header on top of the R.O. so there is stronger support and backing to install windows, trim/casing and curtain rods, usually 3'-6" above trim/casing.
There are benefits both ways. As Armando said it's nice to have the lintel as solid backing, although most curtain rods still need additional blocking to extend past the window. On the other hand, if you have ever had to change the head height of a window for any reason you will know the virtues of having the lintel as high as possible. A third option if there is an additional floor above, is to double-up the rim joist, eliminating a dropped lintel altogether. This allows uninterrupted insulation, much as you get above windows on a non-load bearing wall.
Kurt - We may be seeing more windows and doors framed with the headers tight to the top plate with cripples beneath as states begin adopting the 2015 IRC.
One of the new requirements for dimensional lumber headers is that they must be laterally braced [Table 602.7(1) footnote f] or if not braced there's a 30% span reduction. Though the code only addresses dimensional lumber headers the lateral bracing practice will likely be applied to engineered lumber headers.
Lateral bracing a header can be done two ways - it can be installed tight to the top plate (as the photo shows) or you can diagonally brace the header back up to the floor / ceiling framing (and I doubt many will like that option).
Exterior insulation is not just about preventing thermal bridging but decreasing sheating condensation risks. Tstuds don't address this concern. Of course, you could always use metal strapping instead of sheating your house but then you have to figure out where to put your air barrier. There is no free lunch.
True, but sheathing condensation can be managed many different ways (see Martin's article "How Risky Is Cold OSB Wall Sheathing?" https://www.greenbuildingadvisor.com/article/how-risky-is-cold-osb-wall-sheathing).
But the main reason I may choose exterior rigid foam (and I think this goes for most people who choose it), is to break thermal bridging across the whole wall assembly--including rim joists.
Tstuds were discussed on this week's Fine Homebuilding Podcast (#186). at about 38:00 minutes into it. The opinions of the podcast crew were not all that favorable for Tstuds. Issues they cited are (1) instead of 1.5 inch thickness, Tstuds are a non-standard 2.5 inch. (2) Running pipes could be a problem without planning ahead. (3) If you break a dowel, it needs to be repaired. (4) If you break 2 dowels, the Tstud needs to be replaced. (5) Tstuds require 4" nails. A nail gun that handles 4" nails is super spendy. (6) corners must be strapped.
So the Fine Homebuilding podcast team raises some issues to think about.
That podcast was the first I heard about T-Studs and I found the concept very intriguing and wrote a letter to the podcast gang about my situation. They said there will be a follow-up discussion in the near future. Stay tuned...
I like their point that the Bonfiglioli approach solves the thermal bridging at the studs issue with less cost and none of the drawbacks listed above.
Bonfiglioli walls are a good alternative for owner/builders. For developers and production builders looking for higher efficiency walls T-Studs, even at their current price, probably still make more sense. They don't have the time or money to pay someone to rip and install foam strips on all the exterior framing.
Probably worth remembering though that T-Studs are the latest in a line of engineered thermally-broken wall studs going back more than a decade. As far as I can see, none of the rest are still in business.
All the techniques for breaking thermal bridging that add foam on the interior or exterior (including the "Bonfig" wall) assume you can afford the extra 2+" of wall thickness. Sometimes interior and exterior limitations and boundaries make this extremely difficult, or even impossible.
There's always a solution that makes the wall thicker, but if you reframe the question as "How do I make the most efficient 6" wall possible?" then your options are reduced dramatically. In my case, my next-best option is a 2x4 wall with 2" of XPS which can achieve a whole-wall R value of R20+. Regardless of how you do it, if you can build an efficient 6" wall, you save on space (inches add up), and you save on all the jam extensions and other modifications required for thicker assemblies.
Thanks for pointing this out. Not everyone has a large lot or accommodating zoning. The relevant question is given a 6 inch wall. On a related note, these discussions never address stucco-they always assume you’re putting on standard board/fiber cement sheathing. You can just hang 2 plus inches of exterior insulation and then apply a traditional three coat stucco without giving a lot of structural thought to nail size, nail number and shear issues, ie you need to get it engineered. Huber does not go out on a limb and provide that data/backup for stucco over insulation over zip.
Are there moisture/condensation concerns for the exterior part of the T-stud and the sheathing, which will both be outside all the insulation?
If you want to use engineered products, just use SIPs. They have to be as good as these complex, labor intensive system.
If I get it right, cost separated, it’s still an efficient solution for thermal bridging for walls that cannot put too much external insulation. Which is what I looking for my remodel duplex in heart of Montreal., where I cannot have a double wall or put too much exterior insulation
Exactly. If exterior (or interior) foam won't work due to extra wall thickness, hitting minimum foam thickness ratios, or other reasons--this is an intriguing option.
Any updates after 1 year since posting?
Risinger just had an Instagram story (not a post, alas, so it is gone) where he received an order of T-Studs. He mentioned how they had to find a new manufacturing facility for them but that they finally have that all set and are ready to ramp up to full production. Seems pretty early one (even one year one) considering that the owner and lead engineer(?) came along with the order...
I appreciate, then, that you're watching Instagram, because I don't have an account of my own. :) If that's the case, then I'm sure he'll have another video up documenting his experience in another 6 months or so. I'm still four or five years from building a house (if we build at all, vs buy), so I'm not in any rush, but this is definitely an interesting technology, and I'm curious enough to keep an eye on it (minimally :) ). I set a reminder to check back at the one-year mark because I thought there was a remark in the article, above, to update the story at around one year. Thanks!
All I know as they got a lot of interest after the Matt Risinger video and had to scale up production to meet demand. I received an email several months ago soliciting investors for a new facility but don't know the outcome. I suggest contacting them directly for more info. Please update here if you find out anything new! 😊
It's great to see that T-studs are doing such a good job of marketing. The product deserves it. I was aware of them from the first day Risinger's video came out.
That said, until there are multiple competing manufacturers and these are available in Big Box stores, I can't specify them in my work, as much as I would like to.
Also, seismic shear wall testing for Zone D needs to be done. My hunch is they will perform fine. But hunches don't satisfy building officials.
Log in or create an account to post a comment.
Sign up Log in