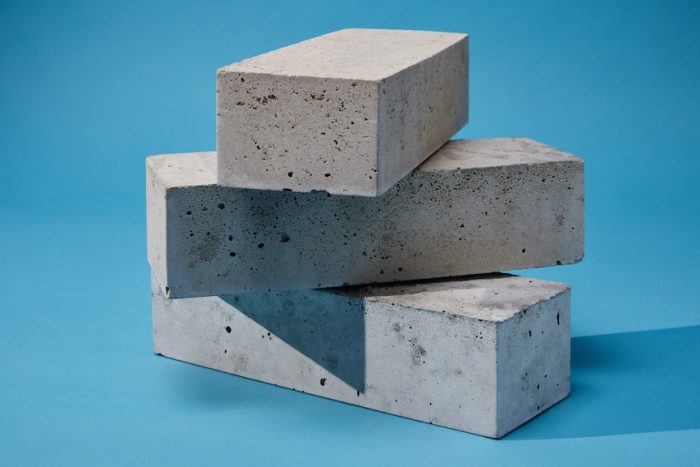
The global portland cement market is huge. There’s simply no other way to characterize the carbon impacts and production scope of an industry that is responsible for 8% of global CO2e emissions and is projected to reach 5.8 billion tons by 2027. The residential market alone is expected to account for roughly one-third of that tonnage by the same year, thanks to a compound annual growth rate of 5% from 2020–2027. In layman’s terms, it’s a damn juggernaut.
And here’s another troubling statistic: the U.S. alone currently accounts for nearly 29% of total market share (or 1.2 billion tons), according to 2020 numbers. Measure for measure, that’s a lot of kilns burning up a lot of limestone and emitting a lot of toxins. Yet somehow, with all the carbon output we track and all the hazardous air pollutants we account for, the standard manufacturing processes and supply chains for ordinary portland cement production continue to grow. So, what gives?
“Industry doesn’t like change, and this particular industry is pretty conservative,” says Greg Williams, head of product at Sublime Systems. Sublime is a three-year-old manufacturing startup, co-founded by Leah Ellis, PhD, a former Banting Postdoctoral Fellow at MIT, and Yet-Ming Chiang, serial entrepreneur and professor of materials sciences and engineering at MIT, and based in Somerville, Massachusetts. In an industry that’s already pretty crowded with bit- and mid-size players adept at producing low-carbon concrete options, often at considerable cost (for now), Sublime is intent on standing out.
Different process, similar chemistry
Sublime Systems’s product employs a proprietary electrochemical process that claims to eliminate both phases of CO2 emissions that are typically associated with cement production. The first phase is the burning of fossil fuels (mostly coal) in a kiln to break down limestone (calcium carbonate) and other feedstock materials like clay and sand; the second is the CO2 that’s released once the limestone is decomposed at approximately 2700°F (about 1450°C). “Since the beginning, [we] realized that to reach our goal of zero carbon, we have to eliminate both sources of emissions,” says Jesse Benck, Sublime’s vice president of R&D. “There are some valuable strategies out there that maybe only eliminate one part, or reduce one part, but we’re really trying to tackle both.”
Sublime’s technology is founded on the premise of being “true” zero carbon, as opposed to “net.” In other words, carbon is a non-factor from the outset. While ancillary processes of crushing, grinding, and transporting raw materials (i.e., all the scope 3 stuff) do come with associated emissions, the company has keyed in on honing that rare breed of industrial manufacturing that produces no emissions up front and foregoes the need for carbon capture and storage, or offsets of any kind.
According to Benck, “We start with calcium silicates, or non-carbonate feedstocks. Unlike limestone, there is no CO2 bonded to the rock, but they still contain [the key materials] needed to make cement. These feedstocks include a variety of abundant rocks and minerals, as well as some industrial waste like coal, ashes, slags … things of that nature. So, our process is actually flexible and can work with a lot of common materials.” Sublime’s electrolyzer (electrochemical reactor) is all electric and requires temperatures only up to 100°C to achieve the necessary chemical reaction, which produces an aqueous solution. “We don’t need to burn fossil fuels at all!”
The end product is a calcium silicate cement. The key ingredients are hydrated lime, calcium hydroxide, and a reactive silica “which is kind of like a portland or supplementary cementitious material that’s used today, although we make it in a different way,” Benck says. “The process is different, but the chemistry is actually related to portland cement.” The reactor’s ability to process and upcycle waste streams to produce the calcium silicate is analogous to “a chef using the whole animal,” he says. Nothing goes to waste.
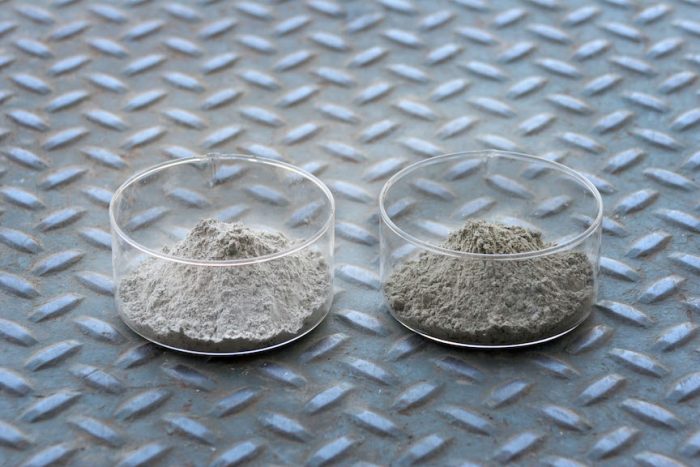
Scaling up and third-party validation
Sublime Systems announced in September that its product has obtained industry approval in the form of ASTM C1157 designation, meaning that it meets baseline performance and safety requirements (note: it exceeds them) and now has the proverbial green light–via third-party verifiers–to go to market. That said, don’t expect your local Ready-Mix supplier to have low-carbon calcium silicate cement on hand any time soon. Getting to that point will require scalability, and the company still has an uphill climb ahead to become commercially viable.
The MIT spinout has raised $50 million in capital funding to date from various climate tech investors, and its current operation consists of a “pilot plant” that’s capable of producing “a few hundred tons per year,” according to Williams. The plan is to get product “on the ground” and into a few construction projects by year’s end, he says. “We are fully out of the lab!”
Of course, when considering the sheer breadth of the industry in which Sublime is looking to compete, a few hundred tons of anything–low carbon or otherwise–won’t raise any eyebrows. Sublime’s road to scale is being paved. “We are in the process of bringing online our first commercial-size plant,” Williams says, which is estimated to become operational by 2026 and have the capacity to produce up to 25,000 tons per year. But as Williams notes, “any kind of cement plant operating at full scale today is [making] a million tons a year. That’s what you need to achieve economies of scale.” It’s a long road indeed, and to that end, Sublime’s team is eyeing 2028 when they can attain that “megaton scale.”
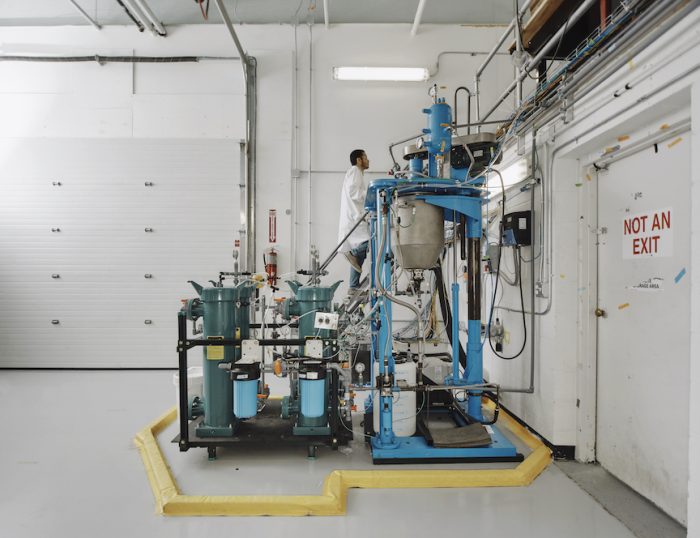
In addition to its ASTM designation, the company announced only days ago that Climate Earth, the industry’s leading provider of environmental product declarations (EPDs), has conducted a cradle-to-gate screening life cycle assessment (LCA) and validated that Sublime’s proprietary process can eliminate more than 90% of the global warming potential (GWP) of its cement manufacturing, relative to the standard portland cement.
The screening constitutes a preliminary EPD (actual EPDs cannot be obtained without a full 12 months of operations and data), which is based not on Sublime Systems’s “pilot” status but rather estimates of its full-scale manufacturing process. According to the press release, the screening LCA determined a GWP of 72 kg CO2/ton for a 100% Sublime cement blend, compared to the 922 kg CO2/ton, the industry-wide average for portland cement in U.S. The remaining emissions are mostly attributable to the “mining and transportation of feedstocks and waste and wastewater treatment, processes that are primarily upstream and downstream of Sublime’s core manufacturing innovations.”
All the same, with a green light to go to market already in hand, why go to the extra trouble? “We’re doing this because we realize how important EPDs are,” says Leah Ellis. “The cement industry isn’t anticipating startups; the rules are not really in our favor. That’s why we’re working towards an EPD, to show how we will stock up when we’re at full scale.”
Getting partners on board
“The cement industry is massive and very capital intensive,” Ellis says. “They’re all about turning the crank on the status quo, which is why it’s been so hard for them to decarbonize. But what they’re doing is important and the material is important. They know they have to change, but they don’t know how.”
The road to decarbonization isn’t a straight line. Put another way, to overcome “the inertia of a conservative industry” and “achieve cost parity with current products,” according to Williams, multiple factors need to align just right. Advancements in grid integration technology and mass scale availability and delivery of low-impact electricity are two such examples. This would lead, theoretically, to incumbent manufacturers of ordinary portland cement (those already operating at megaton scale) to transition their operations to more renewable and regenerative models. The hope, at least, is that ‘adapt or die’ will become mantra across the industry.
Sublime’s leadership has indicated that their company is open to licensing opportunities and similar partnerships. (Patent applications for Sublime’s electrolysis process were submitted years ago but remain in limbo.) There is clearly enthusiastic support for such a disruptive product, and Sublime has the support of some notable industry players, among them Senior Fellow of the Design Futures Council Don Davies, who sits on the company’s advisory board. But as Benck astutely points out, “not everyone has the ability to pay a green premium.”
Getting close to cost parity will require widescale adoption from concrete contractors, engineers, construction firms, developers, and pretty much every stakeholder in between. Fortunately, thanks to recent approval from ASTM International and formal validation from Climate Earth, we know that Sublime’s low-carbon product exceeds industry standards and that its claims about GHG reductions aren’t greenwashing.
Compliance and validation are both welcome news, not just to Sublime but to the building industry writ large. Going forward, the scalability challenge will be compounded by an education challenge. According to Williams, “In working with partners, [we need] to help them understand how to write specs that are tailored to this kind of product and make sure they know that [our cement] meets all the right standards and thresholds.”
________________________________________________________________________
Justin R. Wolf is a Maine-based writer who covers green building trends and energy policy.
Weekly Newsletter
Get building science and energy efficiency advice, plus special offers, in your inbox.
0 Comments
Log in or create an account to post a comment.
Sign up Log in