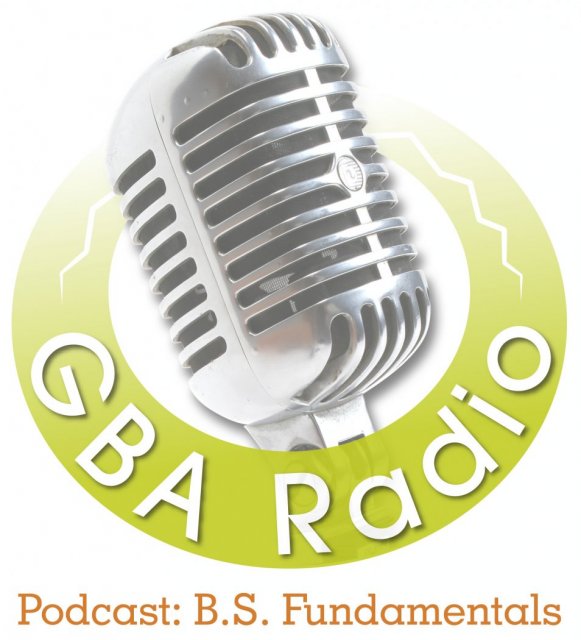
This podcast series is from a two-day class called "Building Science Fundamentals" taught by Dr. Joe Lstiburek and Dr. John Straube of Building Science Corporation.
For information on attending a live class, go to BuildingScienceSeminars.com
In our last episode, Dr. John talked about How Heat Moves Through Homes
and why radiant barriers work better in outer space than on earth.
In this episode, Dr. John talks about the history of insulation, how different materials work, and where they make sense.
TRANSCRIPT
The history of insulation comes about because of the history of structural engineering. Now, I’m a recovering structural engineer, which is probably why I like to think of it that way.
But in the old days, when we didn’t have good structural engineers, to be able to build a building you had to use a lot of material—and it had to be solid. You couldn’t put a lot of windows in there, and it needed to be pretty thick. So, you got decent R-value, just because…yeah, you used a lot. As we got smarter structural engineers, they were able to thin the layer of material down, until the point where a concrete wall 4 inches thick of 3000-psi concrete—you could build a 10-story building with that. But what’s the R-value of 4 inches of concrete? Bupkus. And then we go one step further: We were able to concentrate that 4 inches of concrete into a steel column every 20 feet. If you look at the R-value of concrete, it’s 0.07 per inch, so 4 inches of it gives you a quarter of an R. Woo!
Logs and adobe have pretty good R-value
But if you have a chunk of steel…let’s say you have a 1-inch steel flange on your I-beam; the R-value is about 0.004. When you start saying point zero anything in R-values, you know you’re a loser. So, none of these materials actually has a hope of working. It’s only when you get up into this range—you know, that 10-inch-thick log cabin with 12-inch-diameter logs—R-10. That’s not that bad. It actually meets the comfort requirements [and] avoids surface condensation. People say, “Oh, you can’t live in a log cabin. That’s got no R-value.” Well, that’s three times better than your standard curtain wall, and it doesn’t have any solar gain problems.
But we’ve gotten so brainwashed by the propaganda that insulation is something you buy in a bag from the Home Despot, that we forgot 10 inches of wood or 12 inches of adobe—not a bad product actually, because it’s continuous and it’s solid. That’s why it works. This wall—pretty crappy R-value, having that much rock. But this wall, made out of aluminum, which has an R-value of 0.001 per inch, well, is it any surprise that we have problems with thermal performance in these buildings? Or that the energy consumption numbers don’t go down?
Insulation affects our fashion choices, too
Now, what we obviously need—we’re coming to crunch time, the oil price before this session was at $133.69 a barrel—we’re going to need more in-flow control. People are going to want to do something smarter about insulation. (They’re also going to want to change these unbelievably stupid bulbs, but I’m sure they’ll get around to that shortly.) There are also more environmental concerns, climate change, more demanding comfort standards. People used to put up with cold places in the winter and hot places in the summer. And we’ve gotten spoiled into saying, “No, I want a more comfortable environment.” So, the temperature ranges that are tolerable have narrowed quite considerably. In fact, the Europeans make quite a bit of fun of the North Americans on that basis. They’re saying, “What the big deal? Why don’t you just wear short-sleeve shirts in the summer and wear a cardigan in the winter?” We actually do the opposite. I don’t know about you, but in my office I actually have to wear thin shirts in the wintertime, because otherwise I sweat. And in the summertime I have to take a fleece to school, because if I wear my shorts and a T-shirt, well, I’ll freeze to death in my air-conditioned office. So, we actually flip it around completely. That might come to an end soon.
Another thing people don’t realize is that when we used to have condensation on our steel single-glazed windows, it dripped onto brick—and so, big whoop. Now, when we have condensation, it drips onto paper-faced gypsum, and we have mold. Mold kills babies. And so people pull the fire alarm and run screaming from the building because they have mold on their drywall. That’s changed owners’ concerns about condensation. It used to be, “Ah, suck it up.” Now it’s like, “Uh-oh, this is a problem.” Right or wrong, that’s how they’re reacting.
Fiberglass and insulation from the future
So, let’s look at some of the insulation materials we have to help us control heat flow. First of all, accept that density of the insulation material matters; moisture content, airspace content, temperature difference—all these things matter. The combination of the insulation and the air in it is actually what gives us the R-value. Still air is about R-6 per inch. The trick is how do I keep the air still? Fiberglass is a triumph because think of what they’ve done. They’ve taken a material…glass is a horrible insulator. But if you make it really fluffy so it’s not actually glass anymore, it’s just the thing that stops air from convecting, you actually get decent R-values out of it—R-3.5 per inch, R-4 per inch —even though still air is R-6… eh, fiberglass isn’t perfect. The only way to improve that R-value of R-6 per inch is to use gas fills, like HCFCs and pentenes, and in the good old days, CFCs, Freon, and so on. That would give us slightly higher R-values.
There are some future products I’ll talk about…. Vacuum panels: This is a product from Germany—Porextherm, I think it’s called—two layers of 3/8-inch polystyrene on either side of a vacuum panel. So, it basically makes a Thermos. And you get about R-20 to -30 per inch, depending on the product. Not bad. Now, it costs you per R-value about 10 to 50 times more than using spray polyurethane foam insulation. But at least you could do it. If you really had Frank Gehry’s budget, you could spend it all on ridiculous insulation. Not all of us have that option. Nanogels and aerogels are also products that are commercially available now at horrific prices that will get you R-12 to -20 per inch. So, we can do it, but it’s unlikely we’re going to do it.
The applications of these things are quite interesting, actually. You want to ship some frozen seafood from Singapore to London, and it’s a 14-hour flight. The normal way was to put a refrigeration unit in a container, put the fish in there, and send it to London. But that refrigeration unit weighs 1,000 pounds. Flying 1,000 pounds from Singapore to London costs $10,000. So, instead what you do is use 100 pounds of superinsulation, throw 20 pounds of dry ice into a 40-foot container, and you fly it to London and save yourself 900 pounds in shipping and 9,000 dollars in cost on the first flight. So, those guys really care about volume-constrained insulation products. In buildings, you just make your walls thicker. Get over it. People like deep windowsills; they like that happy, comfortable feeling.
How much insulation is enough?
Inside most of our insulations we have conduction, convection and radiation going on. Ideally, if we have closed cell foam insulation—actually, most open cell as well—we have suppressed all convection; no air movement goes through it. That’s one reason why all foam insulation gets higher R-value; it’s pretty easy. But we do still have to deal with conduction and radiation. At very low densities, you can’t get good R-value. Because there’s so little stuff there, you get lots of radiation, and convection loops start forming. As you add more fibers, more blockers to air flow and radiation, the density of the material goes up. Most fiberglass insulations are in the 0.7 to 1.1 pound a cubic foot range, and that’s an economic optimum. But you can get higher-density fiberglass; rockwool is typically a higher-density product, and with that you can get R-4.1, 4.2, 4.3 per inch.
So, how much insulation does it take to get to R-20? R-20 is kind of a touchstone. Four inches of extruded polystyrene—the blue stuff, pink, the color doesn’t affect heat transfer much—4 inches will do it, no matter what the product. Bad insulation, about 6 inches. Sawdust, about 8 inches. Sawdust used to be a pretty popular insulation product, but it no longer had a standard because nobody was actually producing it on purpose. And if it doesn’t have a standard, it can’t be accepted into a code, and therefore, it pretty quickly fell out of use. So in the ’50s and ’60s, people stopped using sawdust, even though 8 inches will get you about R-8; it’s a pretty good system. But since no one is making money on it, of course we can’t buy it anymore. Softwood, you’d need about 18 inches or so to get to R-20. It’s pretty hard these days to get buildings made out of 18 inches of solid wood, so that’s not a popular solution. Adobe, 2 feet. There are a lot of older buildings in Santa Fe, New Mexico, which have walls that are this thick of adobe, and they are getting about R-20. And they perform really well.
Dirt is not a great insulation
Then we have the loose dry sand, which I include in this plot to remind people that green roofs—where they put the goats on them—you don’t get any insulation value out of the dirt. If dirt were good insulation, they would probably sell dirt in the insulation aisle at the Home Depot. But they don’t. They sell it in the gardening section, because the R-value of dirt really sucks. This is about the best I could get: 4 feet of dry sand. If you make it actually potting soil and keep it moist enough to grow plants, you need about 6 feet. So, you wouldn’t put the dirt on there for insulation; you’d put the dirt on there to grow plants. That’s why you put it there.
Weekly Newsletter
Get building science and energy efficiency advice, plus special offers, in your inbox.
21 Comments
Insulation
Any comments about Cellulose - Blown Dry or Sprayed Wet? There is a lot of different cellulose installations out there. Also the trendy treated denim in some places?
Cellulose
Cellulose insulation is a tried and true product. Like all, you can screw it up, and we learned about the many ways to screw up, and how to avoid problems, around the time I was learned how to do fractions in grade school. Dense pack in walls works great to fill all the voids and its high density (over 3.5 pcf) helps slow air leaks. It is not an air barrier by any stretch, but it certainly slows airflow. Damp spray is less dense and can be sprayed into open cavities to fill all the voids and around obstacles. You have to beware of the weather and construction cycle and dont over wet the product to manage moisture. Not hard for smaller projects and custom homes. Our experience with the denim insulation has been pretty disappointing: poor loft (does not fluff up) and poor quality. I am sure it can be made to work reliably, although I am not sure why someone would try that hard to use jeans for this purpose with all the good insulation products out there. Did I mention that cellulose is fully recycled? Does not burn? Has a long track record of success? I am afraid most people specifying denim insulation are more worried about looking like they are being green rather than being green.
Open Cell Foam
Thanks for the article John.
You wrote about closed cell foam (and most open cell foam as well) do a great job at convection suppression. When and what open cell foams do not suppress air flow? I have read that open cell foam is not mechanically designed to be an air barrier, but does an effective job at it, so it is an accepted application as such. Could you go a little further in talking about this topic, as I find it relevant in the fact that open cell foam is gaining lots of momentum these days and is more cost-effective than closed cell foam.
Thanks,
Jamie Kaye
Elm Energy Group
Insulation......polystyrene/blueboard etc
Brick build home 1934, cavity walls, no insulation when built, cavity wall insulation added later, and 2 inches of fiberglass in the roof.
I am in the process of adding 8 inches of polystyrene board insulation to a flat roof, the room below positively eats power, it is impossible to hold 22 degrees C during the winter, when this insulation is in place I expect to reduce my heat loss by above 80%.
Remove poly sheet vapor retarder under drywall?
We live in a home built in the 1970's in Omaha, NE. Existing construction consists of cedar siding, particle board sheathing, 2x4 studs, batt insulation and a poly sheet vapor retarder under the drywall.
We will be having the siding, sheathing and batt insulation removed soon.
We are looking at having the following installed: Hardie Fiber Cement Lap Siding (backprimed), Home Slicker (vertically channeled nylon matrix, creating a vented rainscreen), Tyvek, Huberwood AdvanTech Exterior Wall Sheathing and Johns Manville Formaldehyde Free Fiberglass Unfaced Batt Insulation.
We have two questions:
1. Should we have the poly sheet vapor retarder cut out between the studs while the wall cavity is exposed?
2. Will these proposed wall assembly components work together successfully?
Our biggest concern is mold and mildew. We are allergic to both. We'd like to have this done once and have it done correctly.
Response to Laura Kunkle
Laura Kunkle,
It's a shame that you are planning an extensive (and expensive) remodeling project to upgrade your walls, but you aren't planning to significantly improve the insulation. That's a wasted opportunity that only comes around every 50 years.
Whether or not you slit the polyethylene really doesn't matter. Your home will perform adequately either way. But your walls are going to leak a lot of heat. You should seriously consider installing 2 to 6 inches of rigid foam board on the exterior side of your studs or sheathing; that will cut the thermal bridging through your studs and significantly improve the thermal performance of your walls.
slitting poly
Slitting the poly will do almost nothing to increase inward vapor drive but can increase the air leakage of the assembly. Leave it in place unless you insulate the walls with additional foam sheathing. Replacing the siding with a 75 yr+ product like Hardie and NOT adding even just 1.5" of foam is a true wasted opportunity. The additional cost of 1.5 polyiso is around $1/sf but reduces heatflow through you wall by about half, while increasing durability (remove the poly if you can).
blown in batts and rock wool
Hi John (and Martin),
I have a design/build company out in the San Juan Islands of Washington. I was actually wanting to take John's building science class in Seattle this past summer, but ended up being in Massachusetts visiting family that week. I hope you offer a course out here again next year.
I have few insulation material questions:
1) How do you like blown-in-batts. All of the installers in my area seem to prefer them to cellulose. And no one will do wet spray cellulose due to drying concerns. In your mind are they pretty comparable products in terms of performance and longevity?
2) I am working on a project right now with 2x6 framing and a timber floor system for the second floor. There is a fair amount of wood in the walls around windows and under the timber joists even though the framing is 2 ft on center. Having become very interested in improving the performance of my projects and having made a study of building science this past year, I wanted to try to improve the performance of my already designed building, while I still could. What I came up with was applying a layer of 2x2s to fur out my walls primarily run horizontally except at corners and windows etc, then using the blown-in-batt system. In my mind this would significantly reduce thermal bridging and yet wouldn't cost wildly more. Does this seem like a reasonable method to improve a 2x6 framed wall? To me it made sense.
One of my concerns was whether or not my already installed Jeld-Wen metal clad wood windows with double pane, low e, and argon filled, which are generously placed in the building for views an light, would make this added insulation pointless. Is there still significant value in improving wall performance if the windows are not improved with them? Triple paned windows of this sort would indeed be a fair bit more expensive though I would push people to consider them if they made a world of difference.
3) I do not like using foam. I do not like cutting it. I do not like how much carpenter ants like nesting in it. And I do not like that it off-gasses and has seemingly heavy manufacturing costs. I do understand that it performs well, and have certainly used it many times in unvented roofs, under slabs and in remodels. John, what is your opinion of rigid rockwool as an alternative to foam especially for exterior wall applications and unvented roofs? Do you think it might be an effective substitute for foam? And do you ever wonder about the longevity or negative manufacturing impacts of foam despite its ease of availability and high r-value?
Thanks for your thoughts. Please do return to the Pacific Northwest next year.
furring-in walls
I meant fur-in my walls with 2x2's, not out. (My building is actually sheathed and sided at this point.)
foam airtightness
All currently available spray foams are airtight enough to be used as part of an air barrier system. Open cell and closed cell are both fantastic in this regard. Minimum thickness is the issue, and is one of practicality. I aim for 1.5" closed cell in specs but 1" would work, and open cell I spec 3" but 2" would be fine.
Response to Chris Morris
Chris,
Many builders install interior horizontal strapping on their walls as you suggest. It has many benefits.
To get the highest benefit, you want to be sure that the interior horizontal strapping is installed before you install the partition walls -- so you catch the thermal bridging at the intersection between partition walls and exterior walls.
Disadvantages:
1. You lose interior space.
2. The system doesn't address thermal bridging at rim joists.
I haven't heard the term "blown-in batts," but I assume you are talking about blown-in fiberglass. (This system doesn't have any batts.) I think that blown-in fiberglass is a big step up from fiberglass batts, and is a perfectly acceptable method of wall insulation. Michael Chandler uses the system frequently.
chris morris
1. I love blow in or sprayed in insulation of all types: it fills all the gaps and voids and around wire etc. Cellulose is one such type, but if you use the damp spray variety, it may be hard to dry it out in your climates fall winter weather. It would dry in a day or two in your summer. Cellulose could be used if you netted it and then blow into that. But there is now spray fiberglass, and netted fiberglass. Both work well, and I am very impressed with the spray fiberglass I have seen.
2. for your climate those windows are good. Too many of them will always be bad. Adding to the walls does definitely help, but remember: airtightness is at least as important as insulation
3. Rockwool can be used as a sheathing, but does not have the strength that foams do for supporting cladding. We are working on testing it and coming up with details to allow its use, but for now you will need to experiment yourself.
Furring on the inside is a way to improve a wall. The challenge is that it cools the exterior sheathing and thus increases the risk of condensation and reduces the rate of drying. It is hard to give universal answers beyond that. Insulation on the exterior makes you safer and on the interior less so. Air seal and improve exterior rain control.
blown in fiberglass and Roxul dual density board insulation
Thanks for the responses. Indeed "blown in batts" is blown in fiberglass. I do not know why it is called that around here but it is.
The rock wool board insulation that I am interested in as an alternative to foam is ROXUL TopRock® DD and ROXUL TopRock® DD Plus. Roxul sells it as a commercial roof insulation to go below membrane roofs. It is described as a rigid, dual density mineral wool board insulation with a rigid top layer for durability and enhanced strength. The link to it is http://www.roxul.com/roofing/products/roxul+toprock%C2%AE+dd+plus
I am interested in a product like this because it could be used to insulate from the exterior while being water vapor permeable to the outside. My hunch is that it is both more inert and more durable than foam, especially poly iso and expanded polystyrene. Finally it does it have blowing agent issues. I have heard that there may be a small amount of urea formaldehyde used as a binder in rock wool insulation which might trouble some, but at least it would be on the outside.
There is also a product called Roxul DrainBoard which I think could be quite an interesting alternative to extruded poly for foundation walls. http://www.roxul.com/commercial/products/roxul+drainboard%C2%AE Do you have any experience with this either?
The trick is that these product appear to be significantly harder to get a hold of than foam boards. To me they seem potentially superior and perhaps worth the effort to get a hold of and try. I am curious as to whether these are the products the you have seen and are working on testing.
Thanks.
Second response to Chris Morris
Chris Morris,
If you do a search on the GBA Web site for "Roxul" you'll receive lots of information. Here are some of our mentions of Roxul mineral wool:
https://www.greenbuildingadvisor.com/product-guide/prod/drainboard
https://www.greenbuildingadvisor.com/product-guide/prod/roxul-mineral-wool-insulation-batts
https://www.greenbuildingadvisor.com/product-guide/prod/cavityrock
https://www.greenbuildingadvisor.com/product-guide/prod/mineral-wool-insulation
https://www.greenbuildingadvisor.com/community/forum/green-products-and-materials/15419/material-resource-listings-or-sharing-green-produ
How Moisture Content Effects Open Cell Foam R-Value
Doing an insulation upgrade to our 1975 home . First planned project is to insulate the under side of our roof w/open cell foam. Looking for information on how increases in moisture content effect the performance/R-value before making final decision on project. What will real world R-value be inplace for midwest area.
Also, studying the recommended thickness for a roof, finding that using open cell foam is around 5 inches max for midwest (zone 6), however, this does not corespond to buiding codes which have a much higher total R value.
The contractor report that 5 inches of open cell provides about 92 to 96 % reduction in energy transfer. Is 5 inches a good cost/benefit number?
Also, plan to spray the roof rafters to minimize thermal bridging.
Contractor will only spray open cell foam on roof, to allow any future roof leakage to be detected and corrected quickly. Versus closed cell which reportedly could hide leakage for several years, allowing major deteration.
Thank you for your comments, their is so much more kowledge that needs tobe made available on how insulation/energy transfer works for a whole house.
Looking forward to your comments.
Les Otte
Retired Engineer
Response to Les Otte
Les,
Many spray-foam manufacturers have not obtained code approval or fire-testing approval for their foams beyond a certain thickness. In the case of the foam you are investigating, that appears to be 5 inches. Five inches of open-cell foam has an R-value of about R-18.
In your climate zone, the International Residential Code requires a minimum ceiling R-value of R-49. That would require about 13 1/2 inches of open cell foam -- not 5 inches.
If a ceiling has only R-18 insulation, then heat flows through that assembly at a rate that is 2.7 times higher than heat flow through an assembly with R-49 insulation. If you double the insulation thickness, you cut the heat flow in half. With 5 inches of foam, you are only getting about 1/3 of the insulation your ceiling needs.
Martins Responces Leads to a Follow-up Question
Martin, thank you for your response and leads me to a follow-up question.
I may be incorrect, but I think of the energy needed to heat/cool a home in the following way, leading to the following question. Reducing the energy needed to heat/cool a home by adding additional thickness of insulation is not a linear condition. More specically , for example in a heat box test, 10 inches of insulation reduces energy usage by X, and doubling the insuation to 20 inches does not reduce energy usage by 2X. Rather it will be reduced by less then 2x. Is the reduction in energy usage as insulation thickness increases an exponential function, meaning that each additional inch of insulation provides less benefit to reducing energy usage?
If this is correct is their a formula for it?
Thanks,
Les Otte
Response to Les Otte
Les Otte,
The relationship between insulation R-value and heat flow is linear, not geometric or exponential. If you double the R-value, you cut the heat loss in half.
However, as you continue doubling the insulation, the amount of energy being saved with each doubling obviously decreases, while the cost of the insulation increases. Therefore the question, "how much insulation should I install?", is basically a question of economics, not physics.
I see code requirements for insulation as the bare minimum of thermal performance for any house. If you double the amount of insulation compared to minimum code requirements, you will cut your heat loss in half. Only you can decide whether that economic investment is a wise one. It depends on how long you will live in the house, the current price of energy, and your expectations concerning future energy prices.
Whole Home R-value
Martin thank you again for your response.
Still working on the decisions for retrofitting our 1970's brick home. Will do a infared analysis and door blower test soon. Again our planned first part of this upgrade is the roof area. New home to us and the upstairs/2nd floor air handler is in an uninsulated part of 3rd floor attic . Need for it to be in condition area. Also ceiling of 2nd floor has very little insulation, a couple of iches of rock wool currently We see four opions: 1) move air handler into conditioned part of attic along with significant additional insulation added in attic floor; 2). box in air handler w/ ridgid foam insulation along with significant additional insulation to attic floor: 3.) Try to air seal and insulate bottom of roof rafters w/ ridgid foam insulation: and 4.) spray open cell foam insulation on rafters and underside of roof deck. Any thoughts?
We are currently looking at the spray foam option. Aware of several factors to be considered: air infiltratin- reduce to minimum practical; thermal bridging-control where we currently have access to; moisture content control-home seems fairly dry and will use humidity control mechanisms to keep it low; and lastly R-value of added insulation. How all these factors combine and relate to total/overall home R-value is what I am trying to evaluate. Your site is excellent and has provided me some estimates for thermal bridging effects.
Still trying to evaluate how about five inches of open cell spray foam compares to options available, when all factors are considered. Here in Louisville area contractor is using this methodology in new home with good results, e.g.low energy bills. We realize new construction, is more wholistic then what we can do w/inside only retrofit. I will talk to them again to confirm the total roof R-value they are using.
Our goal is for the roof area retofit to be a foundation for our other future home energy improvments(e.g. windows, doors, walls, and basement).
Again thanks again for your suggestions.
Les Otte
Latest response to Les Otte
Les,
It's impossible to come up with a project scope for your energy retrofit job without a site visit.
If you are unsure of how to proceed, I strongly suggest that you hire a home performance contractor or home rater -- ideally one certified by RESNET or BPI -- to perform a home energy audit. The result of the audit will be a prioritized list of recommended energy retrofit measures.
Also, I hope you can afford install more than R-18 roof insulation (5 inches of open-cell foam). That's not much.
subslab thermal regime
Is there any literature for the steady state thermal regime that sets up under "floating slab" construction? I would especially like to understand what are optimal insulation thicknesses at various points. Is it correct to assume that center of slab, at least technically could be much thinner without compromising heat loss targets? I notice that passivhaus standards use something like 14" of rigid foam, continuous!
Log in or create an account to post a comment.
Sign up Log in