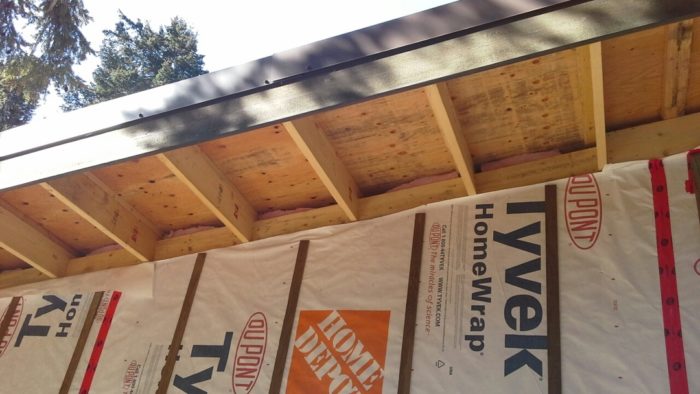
Image Credit: Photo courtesy Carolyn Wood
Carolyn Wood is building a house 80 miles north of Vancouver, British Columbia, and if nothing else she’d like to get all the details in the roof assembly right. The question is whether the house is too far along to let her reach that goal.
The roof, with a 2-in-12 pitch, is framed with I-joists, strapped with 2x4s, and sheathed with 1/2-in. plywood. Above the roof sheathing, the roofers plan to install NovaSeal roofing underlayment and standing-seam metal roofing.
Below the sheathing are two layers of Roxul mineral wood insulation, providing a total of R-36. Wood plans to finish the ceiling with 1×6 tongue-and-groove boards. Against her builder’s advice, there will be no polyethylene vapor barrier in the ceilings or in the walls, but Wood would like to know whether, as she has recently heard, there should be a layer of drywall between the T&G ceiling boards and the insulation.
As currently built, the roof assembly has 1-inch-high ventilation gap between the top of the insulation and the underside of the roof sheathing, Wood writes in Q&A post at GreenBuildingAdvisor, but the question is whether 1 inch will be adequate. That’s the topic for this Q&A Spotlight.
Yes, the ceiling needs an air barrier
There’s no question that an air barrier should be installed between the ceiling boards and the mineral wool insulation, write both GBA senior editor Martin Holladay and Dana Dorsett.
“Unless measures were taken to fully vent the 1 1/2-inch air space between the 2×4 purlins to the exterior in a manner compliant with [the International Residential Code], using poly would be a BAD idea,” Dorsett writes. “But you can use a ‘smart’ vapor retarder such as Certainteed MemBrain or Intello Plus, detailed as an air barrier.”
Either 1/2-inch plywood or…
Weekly Newsletter
Get building science and energy efficiency advice, plus special offers, in your inbox.
This article is only available to GBA Prime Members
Sign up for a free trial and get instant access to this article as well as GBA’s complete library of premium articles and construction details.
Start Free TrialAlready a member? Log in
30 Comments
Mystified by the drywall suggestion
Why would you choose gypsum, a heavy water sensitive product that can support mold, to install on a ceiling as an air barrier instead of a smart vapor retarder? The smart vapor retarder is lightweight, unlikely to support mold, not destroyed by water, and runs (current intello pricing on 475) $0.43/sf for the material. Gympsum is heavy, easily damaged by water, supports mold, and runs ~$0.30/sf (US prices). Yes, you'll want some spendy tape for the intello but the gypsum likely has much higher labor costs. It seems like a no brainer to me.
Response to Keith H
Keith,
Either drywall or a smart vapor retarder can be used as an air barrier. Each material has certain advantages; you should use the material that makes sense for you.
As you point out, drywall is less expensive and uses much cheaper tape. It is readily available locally, and builders are completely familiar with it. Many builders prefer rigid air barriers because they are likely to be more durable than flexible air barriers.
If you purchase a roll of Intello, you may have to buy many more square feet than you need.
Intello will almost undoubtedly be faster to install.
As I said, use whatever product your prefer. And remember: if you install all of the insulation above the roof sheathing, or if you install spray foam insulation under the roof sheathing, you probably won't need an air barrier directly above the tongue-and-groove boards.
Some thoughts
I agree that an air barrier is needed, and the 1 X 6 T&G boards will not be an effective air barrier. Drywall, plywood, or a smart vapor retarder would work as an air barrier. So would polyethylene, unless there is a significant convergence of summertime air conditioning and outdoor dewpoint temperatures. I think that would be unlikely. I don’t worry about it in Minnesota.
I do not understand the reasoning of Dana Doresett when he says this:
Unless measures were taken to fully vent the 1 1/2-inch air space between the 2x4 purlins to the exterior in a manner compliant with [the International Residential Code], using poly would be a BAD idea,"
Some might think poly is a BAD idea under any circumstance, but why would it be a bad idea if the venting is insufficient, as Dana seems to be saying? I would think that with insufficient venting, the air/vapor barrier would be more necessary rather than less necessary.
The following are my preferences as I would apply them to the questions and decisions Carolyn is facing with her house at this point. I would not switch to an unvented roof at this point in the construction. My preference for a house that I would build would be for a much deeper air space which would be possible because I would use scissors trusses, and have as much depth as I needed for insulation and air space. However, in the case of Carolyn’s house, I am not convinced that a 1-inch air space is insufficient, or that it will cause any problems-- if it can be set up with continuous eave inlets and a continuous ridge outlet. However, as Peter Yost mentioned, we don’t know what this roof design looks like. My points assume a relatively simple roof.
I like cupolas for the ridge outlet because they are out of the snow. However, there must be a way for the venting air to converge on the cupola locations. If I understand it, the insulation bays are isolated from each other, so there can be no cross flow of air needed to converge on the cupolas.
I would not use plywood or sheetrock for an air barrier. Although they can work fine, my perception is that they require too much effort in proper fitting and sealing, and these seals can fail over time. I would use polyethylene sheet because it can be a perfect air and diffusion barrier. I understand that it is commonly believed that diffusion will not be enough to make an effort to prevent. I do not assume that to be true, although it might be.
I would not use a smart vapor retarder because I am not sure how long they will keep working. They are, after all, vapor retarders with “moving parts.” And again, without the reverse vapor drive dewpoint crossover during air conditioning in the summer, I don’t see the need for a smart membrane.
I like the Carolyn’s idea of dropping the ceiling by adding 2 X 2 furring, which would enable lowering the insulation in order to increase the ventilation space. But I do not understand why she says it would result in a 4-inch vent space. I would think that if it is 1 inch now, and you add a 2 X 2 (1.5” nom.), you would have 2-1/2 inches of vent space. Actually, this question may relate to the 2 X 4 strapping and its relationship to the air space, with I do not understand from the various descriptions of it.
I should mention that the poly vapor barrier I would install would be way above average material and workmanship used in average construction. Carolyn’s builder may agree with the use of a poly vapor barrier, but he might not agree with my approach to quality control. But that same issue might be the case with the builder installing airtight drywall or any type of air barrier.
I would add 2 X 2 furring after attaching the poly to the bottoms of the joists. I would also try to obtain poly as thick as possible up to 15 mil. This arrangement would have the poly fully secured in place before the boards are added. The nailing of the boards would only penetrate the 2 X 2s and not pierce the poly. Nails piercing the poly are not normally an issue, but with the boards, there will be a lot of them, and they might be run in at a diagonal to hide them. And they are less decisive in clamping down on the poly than say sandwiching the poly under 2 X 2’s secured by sinker nails. In general, there is a variety of small reasons to secure the poly under the battens before adding the finish boards.
The gap created by the battens can also be used for wiring cavity if lighting is installed in the ceiling. That way the vapor barrier will not be penetrated with wires or boxes that must be sealed to it. It is also further insurance against any reverse vapor drive dewpoint issue of summertime air conditioning.
Actually the option to fur down from the bottoms of the rafters offers some other variations such as lowering the insulation to increase the ventilation space above; and providing an electrical cavity. Although I am not sure how easy it will be to lower the mineral wool batts. Can they easily be pulled out for removal?
Replying about your thoughts on the cupolas because we have the exact same situation. If each of the rafters is separated from one another then the cupolas will only vent the bays that lead to it… is my understanding correct? With a low slope roof (1-12) will that be adequate ventilation? In an area with very little to no snow (zone 2a) is there a concern regarding ventilation through ridge vent? Is there a way to maximize air flow in and out through that 6” gap while preventing water from getting in ridge vent? Also, if you put rock wool 10” of insulation between each rafter bay then how do you insulate under the actual 2x8? Will the ceiling sheet rock be sufficient for vapor barrier between the interior and the insulation?
Unvented roof caveat
Would you still use closed cell spray foam if she is planning to use the Nova-Seal roof underlayment? Depending on if that product is impervious, which I don't know, you need the roof to "breathe" to one side so you don't create a "moisture sandwich" with the wood roof sheathing in the middle.
This situation is all too common.... lots of research, lots of talking to contractors, roofers, building scientists, insulation contractors, mold remediators and they all have a different way, opinion or contradiction. Been there on quite a few projects!
Response to Shannon Maris
Shannon,
Many unvented roof assemblies have been insulated with closed-cell spray foam. The vast majority of these roof assemblies can't dry to the exterior.
As you have discovered with your research, there is no consensus on whether these roofs will have problems. If this type of assembly bothers you, there is a fairly simply solution: include ventilation baffles to create a ventilation gap between the underside of the roof sheathing and the upper side of the insulation. The spray foam can be installed on the ventilation baffles (as long as these are stiff enough).
In my opinion, as long as the roof sheathing is dry on the day that the insulation contractor installs the spray foam, these roofs will be fine. In fact, there is a fair amount of evidence showing that roof sheathing is more likely to stay dry when closed-cell foam (not open-cell foam) is installed in this location.
Yup, 2 major issues exposed!
This discussion illustrates two of the most maddening issues of green building practice:
Issue No. 1, Conflicting advice & theories -.
Quoting: Although Wood hadn't overlooked the twin issues of ventilation and insulation, guidance was anything but clear-cut. "We had considered the insulation and roofing construction before and throughout the construction process ... "Unfortunately, it now turns out our builder and others in the industry where we live were not well informed about building science. "We have tried to educate ourselves on the topic, but a lot of it is confusing....."
EXACTLY!! For those of us non-experts out in the field, these kinds of debates among experts, as well as the hours of reading up via long, technical building science articles simply add up to increasing confusion and the risk of making a bad choice of materials or technique in spite of extensive research. Somewhere, some day, I hope we non-experts can find a source for clear, definitive information.
Then maybe we would be better equipped to deal with Issue No. 2 when we advocate for ourselves in the face of ignorance --
Quoting: Sal Lombardo writes, is that local tradespeople may not be receptive to doing things in a way that doesn't conform to what they know.
"I find its not uncommon to garner information from good building science sources, such as this site or Building Science Corporation, and when you refer to this information or relay the same in conversation to the contractor, craftsman, or mechanic in the field, they have little to any idea what your talking about," Lombardo says.
"Much of this 'theory' seems to be lost on the day-to-day contractor doing the work in the field. In my area, if you stray from the 'accepted' standards, you're suddenly in uncharted waters, getting looks of confusion and skepticism."
Response to Janell Cole
Janell,
I understand your frustration. GBA does its best to provide good advice based on the most up-to-date data and building science research. If you are frustrated and confused, it might be worth researching topics on this web site, or posting questions on our Q&A page.
I don't have a good solution to the second frustration -- the fact that local contractors and code inspectors often provide bad advice. The long-term solution is education; GBA is doing the best we can in that department, but it's likely that the problem will always be with us.
It sounds to me like the only
It sounds to me like the only issues here are the depth of the ventilation gap between the top the insulation and the bottom of the sheathing; and whether an air barrier is needed below the insulation.
Everybody agrees that an air barrier is needed there because the 1 X 6 ceiling boards will leak like a sieve. As I understand it, the 1 X 6 ceiling has not been installed yet, so it does not seem like there is any problem with having done something the wrong way.
As to the air gap, I understand that there is no code that applies in Carolyn’s location. Where did the choice of the gap being 1” come from? What is supposed to happen if the space is 1” instead of 6”?
If open cell foam on the underside of the sheathing will not get wet from outward moisture drive if there is an air barrier/vapor retarder, why wouldn’t the inclusion of an air barrier/vapor retarder in Carolyn’s house eliminate the need for any vent gap to vent out moisture?
Response to Ron Keagle
Ron,
Q. "Why wouldn’t the inclusion of an air barrier/vapor retarder in Carolyn’s house eliminate the need for any vent gap to vent out moisture?"
A. Because it is really, really hard to totally eliminate air leakage from the interior to a vent space above the insulation layer. The vapor retarder will address vapor diffusion -- but a bulletproof air barrier is rarely seen in the real world, especially if the insulation is air-permeable.
Reply to Martin Holladay
Martin,
Why then is an air barrier/vapor retarder deemed to be a successful way to prevent moisture from condensing on the underside of roof decking after passing through open cell foam?
How much condensation is too much condensation?
Simple question, no simple answer, right? Isn't this question what WUFI is supposed to tell us?
Reponse to Ron Keagle
Ron,
Q. "Why then is an air barrier/vapor retarder deemed to be a successful way to prevent moisture from condensing on the underside of roof decking after passing through open cell foam?"
A. Because spray foam does an excellent job of stopping air flow.
Reply to Martin Holladay
Martin,
If you have an air barrier that is not perfect enough to stop all the airflow, the breaching airflow will carry water vapor into the attic an onward to the layer of closed cell foam. The foam will stop the airflow so it will not carry the vapor into the foam and into contact with the sheathing.
Yet the water vapor that came into the attic with the airflow will be carried right to the foam by that airflow. And while the airflow will not be able to carry it into the foam, won’t diffusion carry it right into the foam and into contact with the sheathing?
Response to Ron Keagle
Ron,
You're right, of course, that there are two ways that moisture can move from a warm interior to cold sheathing: by piggybacking on exfiltrating air, or by diffusion. If there are a few cracks that permit air movement, the first mechanism is by far the most worrisome, because it allows for the transport of far more moisture than can move by diffusion.
While the amount of moisture that moves by diffusion can be measured and calculated, and while that moisture flow is sometimes problematic, the problem pales in comparison to moisture carried by moving air. If you can stop air movement, you are most of the way to your goal.
That's why air-permeable insulation materials (fiberglass, cellulose, and mineral wool) require entirely different air sealing and venting strategies than spray polyurethane foam. The need for different strategies is fully reflected in U.S. building codes.
advantage of new construction versus retrofits
. . . is that you can to find the best configuration to suit the local environment and built to last. However, in older Eichler's and similarly designed homes from the 50s, like the one I own near San Francisco, a roof retrofit can be a monumental challenge. I have interviewed a large number of roofing contractors and to date I'm not convinced that any one of them have a firm grip on the best approach to re-roofing with design considerations to satisfy insulation requirements, which would include mold prevention down the road.
my roof has a 2.1/2 in 12 pitch, the gentle slope does not qualify for conventional roofing materials and my options are limited to sheet-metal, torch down, or self adhering membranes, FINE!
The problem is the overall depth from 1x6 D.fir T&G planks, to the top of the sheet metal is limited by what would be practical to assemble and secure over the top of these planks. Planks which are nailed across 3x5 rafters, spaced 30" o.c. and tied at the ridge, sitting on outer loadbearing walls, all this beautiful old growth Doug fir exposed to the living area.
The easy way out would be to have a closed cell foam contractor spray the entire bottom side of all the rafters and 1x6 planks, and finishe this ceiling with dry wall. That would satisfy both vapor barrier, insulation, and simplify the re-roofing project, at the expense of destroying all the charm & character of this 50's architecture. I would did used to it but still with hate myself for covering up all that beautiful quarter sawn old-growth Doug-fir.
My next option is to peel off everything that's the above the planks now, R&R any dry rot, then focus on implementing a solution on the exterior and leave the inside wood ceiling intact.
1. cover the entire roof deck with 10mil poly ethylene, then
2. Stack two layers of 2" Polyso foil-backed rigid sheets of foam, staggered and taped at the seams, secured to the rafters with 5 inch screws.
3. then a layer of Tyvek-roofing membrane or self adhering GRACE, or GAF against water penetration.
4. Then 2x2 or 2x4 straps screwed down, which will accommodate sheet-metal snaplock brackets,
5. Lastly finish off with 16" panels of steel roofing.
(Alternatively, a layer of 1/2-inch OSB atop the wood straps, covered with adequate underlayment, and topped off with roles of self adhering or torch down roofing).
Seems like a good plan, but the need for adding adequate cavity for venting the roof further complicates this scenario.
Additionally, many articles on the subject warn against using more than one layer of vapor barrier. So that polyethylene-based layer, covered with impervious sheets of Polyso, topped off with water barrier underlayment has been flagged by some writers as inadvisable approach.
So in the long run I don't really know what is the best way to re-roof, I only know that by doing get myself I have as good a chance of getting it right as paying a so-called professional roofer too screwed up for me for thousands of dollars more, has he is faced with the same see of conflicting information, has construction methodology and building science appear to be riding along separate parallel paths that are yet to converge.
Sincerely,
-F-
Response to Farrokh Khodadadi
Farrokh,
Talk to a roofer familiar with commercial roofing jobs. Installing thick rigid foam and new roofing on top of a low-slope roof is a routine job for a commercial roofer.
By the way, polyethylene is a poor choice for an interior air barrier. Either use the rigid foam as your air barrier, or install a layer of OSB with taped seams above your 1x6 ceiling as an air barrier.
Finally, your roof might be a good candidate for the use of SIPs or nailbase.
Lots of complaints. Look
Lots of complaints. Look folks, there are home designs that are very easy to build in a way that is safe to moisture problems. And then there are the odd balls. Low pitches, situations where someone wants insulation but not the cost, or not the loss of head room, or not the loss of seeing some nice beams or whatever.
Yes, if a budget is tight, there will be very few if any easy options.
aj
One other point. There are suggestions on sites like this that may have no basis in actual builder experience. Good luck with that info.
What about using spray foam roofing
I'm building a home with a similar roof design, our original thought was to use closed cell under the roof sheeting, but now we are leaning towards sprayed polyurethane roofing with a elastomeric coating.
It seems to make sense to do this to for a few reasons, first to have more room for conventional insulation between I-joists, and save the cost of adding either membrane or metal roofing.
The pitch of the roof is 1" to 12" so we are not so concerned about the appearance.
Is there something wrong with this approach?
Response to Paul Lennon
Paul,
Installing spray polyurethane foam roofing is an excellent approach, as long as you make sure that (a) there are no vent channels in the roof (or, at a minimum, the vent channel openings and outlets have been carefully sealed), and (b) you have ensured that there is air barrier continuity and insulation continuity between the walls and the roof.
For more information on this approach, see:
Spraying Polyurethane Foam Over an Existing Roof
Roofing With Foam
`Roofing with foam' didn't want to reveal its secrets. Error no. 403. Since I'm here I'll ask this; would 15 inch screws through 12 inches of foam on a roof deck constitute a thermal bridge of consequence? I'm planning a 2x6 tongue and groove roof deck which is also the finished ceiling, covered with peel and stick roofing membrane, a foot of polyiso, then either 2x4's or OSB to screw the metal roofing to. If a screw missed the rafter and came through the decking or almost through, would it be covered with a little ball of frost when the temperature dips below the minus 20C's?
Nils,
I have corrected the broken link. You should be able to read the "Roofing With Foam" article if you click it again.
Question for aj builder
aj,
What would you advise Carolyn Wood to do about the issues regarding the air vent space and air barrier for her house project?
Ron, Vancouver... is a
Ron, Vancouver... is a completely different climate than I build in. Mild wet area if coastal. Whistler is a great place to ski though. And the city is so green with landscaping even mid winter which I liked.
I am not a fan of low slope roofs. I would have a qualified local engineer draw up the assembly Ron not me or you or any internet poster.
Aj,
Well even though you
Aj,
Well even though you would hire an engineer, you must have some design ideas of your own. Do you think that if Carolyn sought advice of an engineer for the remedy to her concerns, that engineer would advise her just as ten other engineers would? Or would she get ten different opinions?
I don’t like low slope roofs either. I want 7:12 minimum pitch. But that preference is influenced by the fact that I am in snow country.
7/12 and steeper roofs will shed the snow so you can build them flimsier but you end up with a greater area to cover and a bigger structure to frame. If you beef up the structure to support the snow burden, will it cost more? Recent footage of tornado damage in Gatineau, Quebec showed steep roofs sustained the most damage and flat roofed buildings came through almost intact. Also a low slope roof is much easier to work on.
Nils,
Your comments contain several fallacies.
1. It is untrue that a roof that is 7/12 or steeper will shed snow. I have a 12/12 roof that retains snow, so I know. Whether a roof sheds snow depends on temperature and the roofing material -- not just the slope.
2. "Beefing up the structure to support the snow burden" is not optional -- it is code-mandated, as any engineer knows.
I have a house with a 12/12 roof which retains the snow and my bakery roof is 6/12 and also retains snow. The 6/12 roof is covered with steel roofing which allows a significant quantity of snow and ice to build up before creeping off and crushing whatever I have been foolish enough to leave beneath. Also gutters are impractical as they will just be ripped off by snow and ice. The 12/12 roof is covered with asphalt shingles (which are due for replacing) but which don't let the minimal amount of snow which does accumulate slide off. I don't want to be redoing my roof when I'm in my eighties, so no asphalt shingles. I want to avoid the damage of snow and ice sliding off the roof, I would like to recuperate water shed by the roof, and I want something sturdy and maintenance free. Also I think that the snowload will add to the insulation value of a roof. Also, as the timber I plan to use is still standing it makes sense to mill bigger timbers and use less of them. My quandary is more, what length of roof span is possible with the pines we have? Also is it feasible with the skills and energy and time frame and budget I have to build low slope timberframe vs ordering premade trusses. I really appreciate all the information available on GBA, and the more I learn the more questions I have.
Nils,
Q. "What length of roof span is possible with the pines we have?"
A. You have two choices: You can depend on span tables -- easily discoverable on the internet -- or you can hire an engineer to help you. (As I'm sure you know, if you cut down your own pine, the lumber will not be graded -- calling into question the use of span tables.)
Q. "Is it feasible with the skills and energy and time frame and budget I have to build low-slope timber frame vs. ordering pre-made trusses?"
A. I'm assuming that's a rhetorical question. Good luck with your project.
Ron, repeat, I do not design
Ron, repeat, I do not design wet humid Vancouver low slope roofs. If I move to such a climate then I will get with the program.
Log in or become a member to post a comment.
Sign up Log in