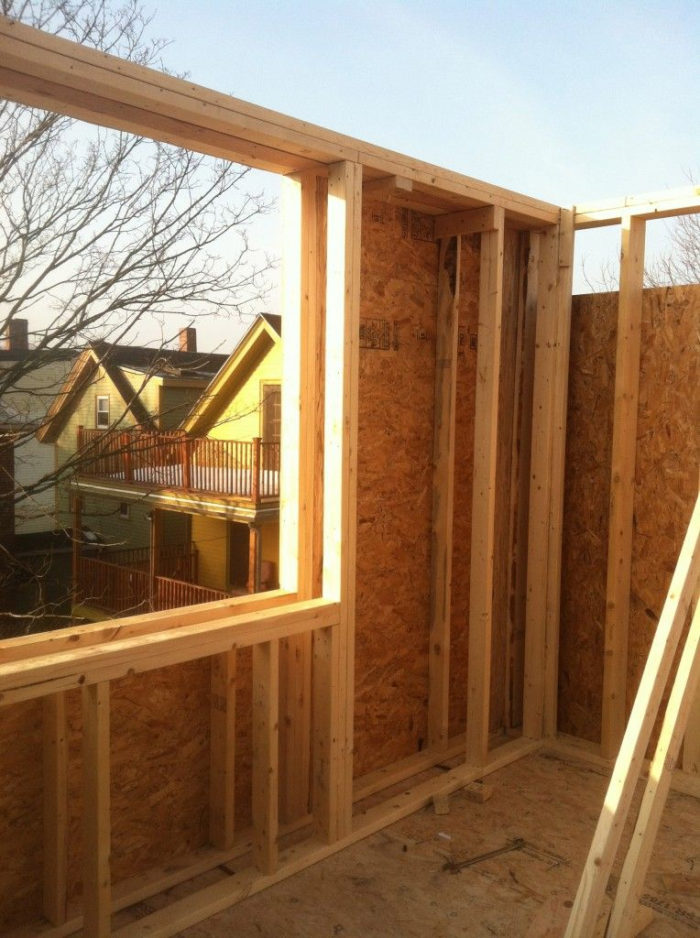
Image Credit: Urbanica
Southwest Nebraska sounds like the kind of place that gets all kinds of weather: hot and occasionally humid summers, cold winters, and by many accounts lots of wind. This is where Nicholas C will be building his house, and the question is, how?
He’s done so much reading on the subject that he’s now confused by the number of options he has. Getting it right is important because Nicholas plans on living in the house for a long time.
His best thinking so far? A 2×8 stud wall framed on 16-inch centers and insulated with blown-in cellulose, then wrapped in 2 inches of rigid foam insulation.
Spacing studs farther apart would mean a savings in lumber, and less thermal bridging through the framing. But for purposes of hanging drywall and cabinets, 24-inch on-center framing doesn’t interest him.
“How does my method sound?” he asks in a Q&A post at GreenBuildingAdvisor. “I am aware spray foam offers better insulation, but I believe it may be too costly.”
Other possibilities he’s considering include using more rigid foam inside the stud bays, or sealing walls with a thin coat of spray foam and then filling the remainder of the stud bays with cellulose (what’s called the “flash and fillt” method).
“Is my method flawed?” Nicholas asks. “Have I combined too many methods into one big mess?”
That’s the focus for this Q&A Spotlight.
Walls framed with 2x8s are really heavy
For one thing, warns Maine builder Dan Kolbert, those 2×8 walls will be very heavy, and more expensive than building a double 2×4 wall.
“I think you’ll find your idea is perhaps the least cost-effective method,” he writes.
Kolbert can buy an 8-foot 2×4 for $3.25, and a 2×8 of the same length for $7.45,…
Weekly Newsletter
Get building science and energy efficiency advice, plus special offers, in your inbox.
This article is only available to GBA Prime Members
Sign up for a free trial and get instant access to this article as well as GBA’s complete library of premium articles and construction details.
Start Free TrialAlready a member? Log in
6 Comments
Double Stud Wall
I am very curious as to how double stud wall assemblies will hold up in the future. The high moisture content in exterior sheathing layers has deterred me from jumping on the cheaper wall assembly band wagon.
Time will tell....and it may get expensive...with repairs....
More rigid installation!
Why not EIFS?
I often wonder why EIFS seems excluded from the discussion on this website. It has many advantages:
4" of foam instead of 1" adds very little to the bid; it eliminates one trip around the house for the rain screen furring; drainage details are worked out, including drip edges above windows; one subcontractor does it all; it is cheaper than most other sidings. Making the sheathing serve as both air and moisture barrier, and locating the windows and doors there, seems like an efficient choice. Filling a 2x4 wall with cellulose adds up to about R-25.
My suggeston for a future blog post
I too am wrestling with double stud wall issues, in particular how to resolve the cold sheathing issue when combined with a masonry layer resting on a brick ledge - the foundation wall now needs to get thicker.
One possible solution I referenced in this thread https://www.greenbuildingadvisor.com/community/forum/green-building-techniques/39021/can-brickstone-veneer-coexist-double-wall-construct is moving the sheathing layer to the inner surface of the external wall. I found this http://www.ecohome.net/guide/interior-sheathing-better-air-vapour-barrier" linl to a project which is doing this form of construction.
The problem I'm having is finding more discussion of this voodoo-art. In my opinion this is a topic that should be discussed in detail, the pros and cons and particularly the nitty gritty methods of framing and a blog post gives you lots of room to pull together information from many sources.
Moving the sheathing into the middle of the wall nicely solves the wet wall problem but at what trade-off.
Response to Alex House
Alex,
Good suggestion. While it doesn't address all of the issues that you bring up, the following article may be useful: The Klingenberg Wall.
I still like the sheathing on
I still like the sheathing on the outboard face of the inner (load bearing) wall. You can insulate it, or keep it clear as a service cavity. Then, rather than adding foam, add an outer wall (studs/TJIs) and fill with DPC/mineral wool.
Been done many times, here is one example. http://www.cchrc.org/sites/default/files/docs/Thorsten_walls_report.pdf
cheers
Response to David McNeely (Comment #2)
David,
I agree with you that EIFS often makes sense. It is the best way by far to insulate an old brick building, for example.
However, when it comes to new construction, I don't agree that "EIFS is cheaper than most other sidings," nor that "4 inches of foam instead of 1 inch adds very little to the bid." In fact, many areas of the U.S. have few EIFS contractors, and prices can be high.
There's another problem with EIFS: the wet-wall fiascos in North Carolina made many home buyers leery of EIFS homes. That fact makes it difficult to sell an EIFS home in some parts of the country.
Log in or become a member to post a comment.
Sign up Log in