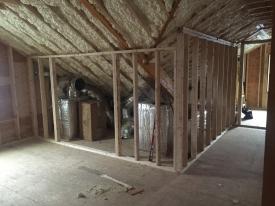
Image Credit: David Amenhauser
David Amenhauser is buying a home near Boston, Massachusetts, that’s apparently still under construction, but far enough along to have the roof framed and insulated.
“When I decided to purchase the home, it was already framed and the roof deck/rafter bays were sprayed with open-cell spray foam,” Amenhauser writes in a post at Q&A post at GreenBuildingAdvisor. “I do not know what was used for the roof underlayment, but I know there are asphalt shingles. The rafter bays are made out of 2x12s and are completely filled with foam.”
Because the roof is insulated with open-cell foam, which is vapor-permeable, Amenhauser had been planning to ask the builder to prime the ceiling drywall with a vapor-retarding primer/sealer. Then, he came across an article by building scientist Joseph Lstiburek entitled “Cool Hand Luke Meets Attics.”
Now, Amenhauser isn’t so sure he needs a vapor retarder after all. The article implies that may not be necessary as long as the attic has supply and return air ducts. Amenhauser, however, is still concerned about the area behind the kneewalls where the HVAC equipment and ducts will be housed.
“So my question is,” he writes, “what do the experts here recommend to make sure I don’t have moisture problems in the attic?”
For starters, there’s not enough insulation up there
The photo of the attic that Amenhauser posted along with his question suggests to Dana Dorsett that the roof is under-insulated and probably doesn’t meet code requirements for this Climate Zone 5 location.
“The pictures don’t look anything like a complete fill with foam,” Dorsett writes. “It looks (being generous) closer to an ~8-10-inch average depth which, by the way, does not meet code minimum in Massachusetts, with some spots as thin as 6 inches.”
Weekly Newsletter
Get building science and energy efficiency advice, plus special offers, in your inbox.
This article is only available to GBA Prime Members
Sign up for a free trial and get instant access to this article as well as GBA’s complete library of premium articles and construction details.
Start Free TrialAlready a member? Log in
5 Comments
Vapor Retarders and Open Cell Foam
Just to give folks a reference point--a key point of the IRC section on unvented roof is:
IRC FAQ: Conditioned Attics
http://www.buildingscience.com/documents/guides-and-manuals/irc-faqs/irc-faq-conditioned-attics
That being said: are there probably plenty of roofs in Climate Zone 5 without any vapor control that are operating just fine? Yes, that is very likely true--there are not endemic failures of that assembly. But there are enough risks that this code provision is on the more conservative side.
For an excellent case study of what can go wrong with open cell foam in Zone 6 (near Toronto), and bypassing of a sheet good vapor barrier (polyethylene), see this presentation by John Straube:
2015-03-24 LAB Event SPF SprayFoam
https://drive.google.com/folderview?id=0Bzj5mJeuPvYzelgxS2R1ZE8xNk0&usp=drive_web
He stated that there were not exceptional humidity loads in that house. However, there was... wait for it... a white roof membrane. This reduced how much the roof was "baked down" during the summer--thus, the OSB sheathing that you can step through.
Wish I could find someone to help. We are looking at reshingling a cathedral ceiling but incthe 70’s using only 2x6 rafters. It is poorly sealed on the interior as ceiling is old t&g barneood though i believe palced against 1/4” ply. Not enough money to do this right so the plan is to reinsulate with rockwool during re-shingle. I know sealing air gaps is 1st priority but do I use a vapor retarded before putting incthe rockwool then baffle then new decking. Spent many hours trying to find the answer but my problem seems very specific.
Moopy,
1. No one can help you with specific advice unless you share your geographical location or climate zone. Here is a link to the climate zone map: Climate Zone map
2. "Not enough money do to this right" is an unpromising way to start. Bad details can cause roof rot, especially in a cold climate. If you need a bank loan, you need to get a bank loan -- that's preferable to rotting your roof.
3. Here is a link to an article that explains your options: "How to Build an Insulated Cathedral Ceiling."
Thanks. Im in zone 4a. I did read the article (and many others) I read enough to know I cannot afford to do it right. I did get several qoutes to sister the rafters to essentially raise the roof and create enough insulation space. $20k- just cannot do that. The cost to just reinsulate from above about $8k.
Anyway I would have the same question regarding using a smart vapor retarder between the interior ceiling and the rock wool and after using (can foam?, etc) to fill any air gaps
Suggestions are very welcome
Moopy,
A smart vapor retarder can be installed on the interior if you want, but a smart vapor retarder is only one component of a functioning insulation system. You will also need soffit vents, ventilation baffles that create a continuous air gap between the top of the insulation layer and the roof sheathing (from soffit to ridge), a ridge vent, and an interior air barrier -- just to name some of the necessary components of a safe system.
Log in or become a member to post a comment.
Sign up Log in