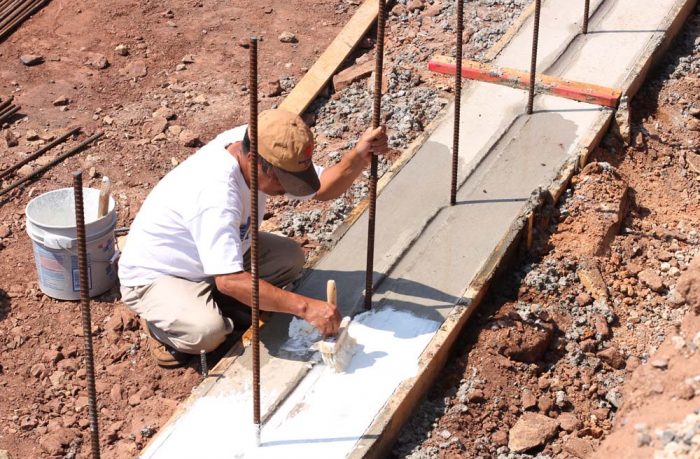
Q: Should the top of a concrete footing be treated to prevent moisture from wicking up from the soil into the foundation walls? Aren’t the perimeter drains enough?
The practice of adding a capillary break to the top of a concrete footing before forming and placing the foundation walls is apparently not universal and is not required by code. But building scientists, researchers, and well-informed builders all recommend it.
Capillary action, a more elegant way of saying wicking, is the movement of a liquid through gaps in a solid material. Water can, in fact, rise to some amazing heights as it moves through materials such as concrete and wood. In an article titled “Capillarity—Small Sacrifices,” building scientist Joe Lstiburek says the theoretical limit of capillary rise in concrete is 10 km., or about 6 mi. Capillary action explains how water gets to the top of very tall trees and keeps them alive.
Footings often sit in wet soil, even when perimeter drains have been installed. The perforated pipe that drains water away from the base of a foundation wall is higher than the bottom of the footing. As a result, even when the drains are working perfectly, the base of the footings could be soaking wet.
A capillary break is typically applied to the outside of the foundation wall in the form of damp-proofing or water-proofing (either in membrane or liquid-applied forms). Underneath the basement slab, assuming there is one, a layer of crushed rock and a polyethylene vapor barrier provides a capillary break. And at the top of the foundation wall, sill seal prevents moisture from wicking from the top of the foundation wall into the mud sill.
That leaves the intersection of the footing and the foundation wall vulnerable. Without some kind of barrier there, moisture certainly will have no trouble making it up a few feet and into the basement.
In a paper for the Building Science Corporation, Lstiburek says that capillary breaks over footings were not common at one time—and they were not all that important when basement walls were uninsulated and unfinished on the inside. Water that migrated upward could dry to the inside. The lack of a capillary break did no harm. “For finished basements,” he adds, “[capillary breaks] are an important control mechanism. Without them, moisture constantly migrates through the foundation, and then into the interior insulation layer and interior gypsum board lining.” That has got trouble written all over it.
For these reasons, Lstiburek and others recommend a capillary break be installed over the top of the footing to control what the British call “rising damp,” (also the title of a British sitcom), as shown in the illustration below.
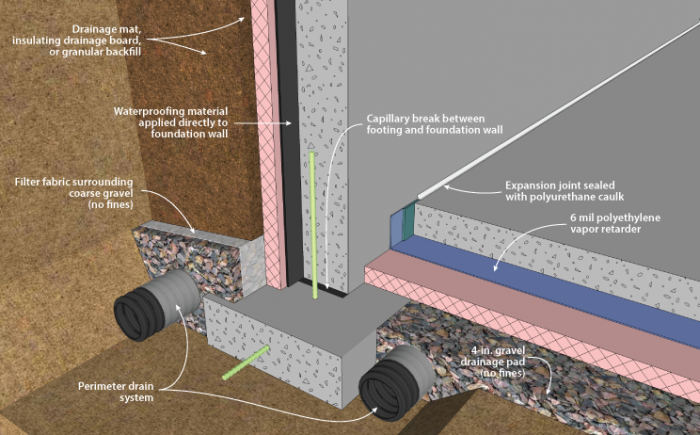
Worries about a weakened foundation
Some builders and building inspectors are apparently concerned that applying a moisture barrier between the footing and the foundation wall might weaken that connection, and lower the shear resistance between wall and footing—that is, make it easier for the foundation to be pushed off the footing.
In a Q&A Spotlight devoted to this topic, Peter Yost recalled a building inspector making this argument on a Building America project. At the time, Yost was working at Lstiburek’s company, the Building Science Corporation, and says Lstiburek was adamant that this concern was unfounded. The only time when there was reason to be concerned about shear forces across this connection was where high winds and earthquakes were likely, or where expansive soils are found.
Otherwise, it’s not a problem.
Footings are often connected to foundation walls with vertical reinforcement, such as steel rebar, or by forming a keyway in the top of the footing while the concrete is still wet. When the walls are poured, concrete fills the depression and the interlocking connection resists inward pressure.
Yost cites this reference from the Department of Housing and Urban Development. It says, in part, “Friction is sufficient for low, unbalanced backfill heights, whereas the basement slab can resist slippage for higher backfill heights on basement walls.” While there are many locations across the country where no physical connection might be required, the document goes on to say, it’s always a good idea to provide one.
So, the best practice is to use either rebar or a key at this connection, and provide a capillary break between footing and wall.
What products to use
A capillary break can either be a membrane, such as Vycor or EPDM, or a coating that’s applied as a liquid and allowed to dry. Choosing between the two approaches may depend on whether or not vertical rebar has been placed in the footing. In cases where there is no rebar, a membrane capillary break is relatively simple to install. When there is rebar, a liquid-applied barrier is probably less of a hassle.
There are many such products on the market. In this article from Fine Homebuilding magazine, Mike Guertin discusses his product of choice from Protecto Wrap called LWM200. Although intended for use as a waterproofing membrane in window and door openings in concrete-block walls, Guertin found it worked well in this application. He and a coworker treated 130 ft. of 18-in.-wide footing in about an hour.
There are many more liquid-applied products from which to choose. In this article posted at GBA in 2016, Martin Holladay lists seven possibilities, including LWM200. Prices vary considerably, and so do cure times. Further, some of the products are to be applied only when the concrete has reached 80% of its design strength, which takes 28 days, according to one of the manufacturers. Waiting a couple of weeks for the coating to cure, or waiting a month for the concrete to cure, is not very practical, so some of these instructions are no doubt ignored.
There also are products that don’t have these drawbacks, as Holladay discovered. Some of them, such as the LWM200 that Guertin used, can be applied to fresh concrete and cure in 24 hr. or less. Several products fall into this category.
Adding a capillary break at the top of the footing is neither expensive nor time consuming, and there are lots of products that will do the job. If this is not part of your routine now, it should be.
-Scott Gibson is a contributing writer at Green Building Advisor and Fine Homebuilding magazine.
Weekly Newsletter
Get building science and energy efficiency advice, plus special offers, in your inbox.
22 Comments
In the center of the drawing, I would extend the polyethylene upwards such that is can be lapped inside any foam that is applied to the interior side of the wall. As drawn, any water coming through the wall will end up on the floor.
Some discussion of "gravel under footing" would be helpful.
Curious that the entire upper surface of the footing is being painted (vs the partial coverage in the drawing).
I wish this blog has been written a hundred years ago and published in Britain. I lived there for several years, and rising damp was almost ubiquitous in every house I visited.
Capillary breaks represent a bit of a problem for areas (like here) where builders usually pour the footing and foundation walls monolithically.
I'm wondering a couple of things.
- Joe L. says it is primarily a problem if the interior basement walls are finished. Is it still a problem worth addressing in a crawlspace with interior foam?
- The water can easily move up through the concrete, but what is the volume of water that does?
- As Jon asked: Can gravel under the footing be relied on over time to provide a capillary break?
> worth addressing in a crawlspace with interior foam
Recent recommendations from Joe L. here. Also note, interior foam should be vapor permeable. But "should" isn't "must".
https://www.buildingscience.com/documents/information-sheets/crawlspace-insulation
“[Deleted]”
Very small holes can wick large amounts of water. So how delicate is the painted on coating (vs say thicker and more durable EPDM)? Does it self seal holes and scrapes?
“[Deleted]”
This is a little off topic but does anyone have an issue with putting a round drain tile next to the foundation? I know this what everyone does, but would something like Certainteed Form a Drain be a better choice?
Steve,
We install the perforated pipe several inches away from the footing to allow for some drain-rock in-between the two. I'm not sure the shape of the pipe makes much difference.
Concrete plants like Hanson have special concrete mixes that are "hydrophobic" that are used in footings, slabs and septic tanks. It naturally resists water permeation once cured.
Can one just buy something like Sika WT-200 and have it added to the mix when it arrives? How does cost/performance compare to a capillary break?
Jon,
I asked about using Xypex admixtures in Martin's original blog on capillary breaks. Xypex replied to Martin the it wasn't approved for that use - which still begs the question as to whether is might work just fine?
This includes "foundations/basements". Of course my next thought is "show me the comparison data".
https://usa.sika.com/content/dam/dms/us01/v/integral-solutions-for-watertight-concrete-brochure.pdf
General info (admixtures help, but see response #14 for even better):
https://www.concrete.org/portals/0/files/pdf/webinars/Yuers.pdf
Sounds like a good test for Wingnut or a building science student.
Low water content + some-fly-ash concrete (around 5000+ psi / .4 w/c) is surprisingly and exponentially non-permeable (confirmed by numerous sources). But > .6 w/c and even "make it soupy, it's easier to work with" is standard. No wonder wicking/rising damp is sometimes a problem.
Here is another option (lower the drain, put a membrane under the footing). But note that their test wasn't performed with rebar poking through the bottom of the membrane.
https://www.youtube.com/watch?v=w6iiwvi1tx4
Back in 2016 Martin wrote this in response to a c0mment:
"You have proposed the use of another additive, Hycrete, for this purpose. Hycrete is sold as a waterproofing additive, and I can see why some people might assume that the product limits capillary rise. But in the absence of data, I'm not going to make any claims about capillary rise in concrete with Hycrete."
I don't understand the distinction between an admixture as waterproofing, and as a capillary break. Sika's link says it " reduces the size of capillary pores", which sounds a lot like a capillary break to me. But Xypex's reluctance to endorse their similar product for that use makes me think there maybe something more to these mechanisms than I understand.
Just order a low water-cement mix and add a superplasticizer if you need workability and you can resolve the issue. Fooling with dubious membranes and coatings is mind boggling.
"Remnants of the original mixing
water form a network of capillary
voids in the hardened cement paste.
These voids are initially interconnect-
ed, but if the water-cement ratio is less
than 0.70 they become discontinuous
during the curing process. If the origi-
nal water-cement ratio is low enough
(about 0.42) and the cement paste
cures long enough, hydration products
fill all of the space and there are no
capillary voids. The only water re-
maining in the concrete is combined
chemically with the cement or held
within the calcium silicate hydrate
structure. Concrete with no capillary
voids has a high strength and low per-
meability."
https://www.google.com/url?sa=t&source=web&rct=j&url=https://www.concreteconstruction.net/_view-object%3Fid%3D00000153-8bb3-dbf3-a177-9fbba3b40000&ved=2ahUKEwjdurjs7J_uAhW7FTQIHbz7AmsQFjABegQIARAB&usg=AOvVaw23JlI5Re6ipLEuzXc5qPo_
Granular,
I've mixed, poured, vibrated, and cured concrete with that w/cm ratio and lower. When I say cured, I mean full on wet cured for a full 28 days. To say that it wouldn't pass water is 'mind boggling'. It will wick water all the same, and often, hold it longer once it has become saturated. Without some type of additional waterproofing agent, it will not perform any differently than 'regular' concrete.
I used Xypex additive for both footing pour and wall pour. The two were separately formed and rebar verticals cast into the footing tied to rebar specced for the walls. I don't think I have seen anyone do a footing key in many years. I am quite happy with the performance even though Xypex at the time told me they did not consider the application within their recommendations. Just the same, I have no fear of putting my expensive multiply sheet goods against my shop walls, nor do I worry about cardboard boxes being in contact.
I believe the point they made was the sealing properties related to bulk water intrusion via small cracks and the general pore structure. To my thinking, this would greatly reduce transport of water sitting around the footing and further reduce transport up the wall. The rep made sure I understood that even treated concrete would give up moisture to the open air side if the concrete was sitting in water or faced high water tables on the exterior side. It would not leak water, but I could face high humidity. I believe one of the main applications for the liquid version of Xypex is for parking decks, dock aprons and the like. The material penetrates into the above mentioned curing pores to seal that avenue, with the added benefit of being able to span cracks up to 1/32". The less salt/pollution laden water that gets into the concrete the longer the life of the rebar and concrete will be.
The epoxy coated rebar more frequently seen in commercial or highway contexts also helps to keep structural integrity as designed by reducing corrosion failure if salts do manage to get into the concrete. A very long report I came across discussed test boxes of epoxy coated rebar set in concrete to see how well corrosion inhibition worked with various sealants and additives. Xypex seemed to be one of the more effective, but the report tried to blind which product was represented by which chart, so I am inferring from text statements that slipped through the editor. The freeze thaw spalling issues were also reduced by using additive treatments over surface treatments. This would all be expected if salt laden water is being excluded from the concrete and cracks were filled to prevent ice wedges. While some soils do carry salts, the long term exposure for a foundation is likely lower than a highway bridge, so one might ignore long term corrosion risks. Garage floor slabs would perhaps benefit most depending on where one lives, though the top coat I have used seems sufficient.
I would note, while super plastic high density concrete might minimize the pore structure issues, it still can't control water intrusion should it crack. I suspect that like Xypex treated concrete it would still pass moisture (though slowly) if it was holding back a high water table. Low permeability does not mean no moisture transfer, just what the rep warned me about. "Hydrophobic concrete" might be a local companies way of selling an additive treated concrete without specifying which of the three or four additive brands it uses.
The notion of using "gravel" ("washed rock" in my mind) underneath a footing to provide a capillary break might be at odds with code in some areas. I am use to seeing the term "undisturbed soil" as a requirement for footings, which in fairness is a vague and somewhat pointless characterization given the wide range of soil types that may be encountered. However, as soon as you introduce new material as fill, I believe most inspectors will want to see soil engineers stamp of approval.
There is also the added issue of where the drain line goes relative to the footing if you do attempt to introduce the washed rock under a footing. Certainly, laying the drain line along side the footing as diagrammed above would render the whole idea moot. I will leave it up to others on how one pours a footing over an open stone bed given the often soupy mixes being delivered. How much concrete would filter down into the rock bed to make contact with the water you are trying to avoid is an interesting question.
Why not just wrap the footing in polyethylene as well?
I had the same question. I live in an earthquake prone area, so if the polyethylene sheet solves the capillary problem, is their any need to apply one between footer and retaining wall?
Henry's Blue Seal is available at most "big box stores" and their technical department told me that it can be used as a capillary break when I asked them.
Are you in Canada? I can only find this in Canada. Can't find a Henry product in the US that isn't asphaltic.
How important is it for this barrier to be vapor permeable as opposed to waterproof? The Protecto LMW200 is vapor permeable (not super high but 10'ish.) My architect can't figure out why vapor permeability would matter, but others insist it be a vapor barrier.
Also, should the capillary break cover the whole top of the footing or just where the stemwall is? BSI's article shows the whole thing.
Log in or create an account to post a comment.
Sign up Log in