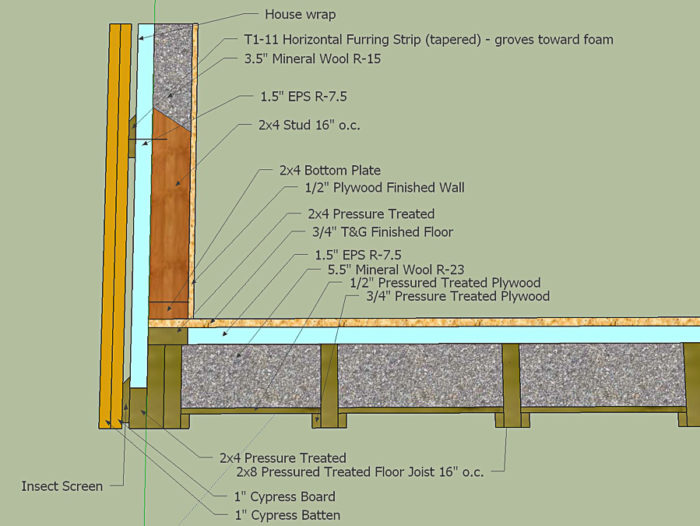
Peter Danube is planning to build a detached workshop in northern Delaware, a Climate Zone 4 locale. The 20-by-32-foot building will be constructed on concrete piers, rather than on a slab or over a crawlspace, and therein lies the dilemma. How should he insulate the floor?
“It is important that the shop have a warm wood floor and the project has to be something I can build myself,” Danube writes in a Q&A post. “I would like the building’s heating and cooling to be as efficient as possible and would like to apply best practices in building efficiency given this situation. ”
Danube explains that the bottom of the floor assembly will be too close to the sloping ground underneath the shop to allow him to insulate from below. Instead, as the drawing at the top of this column shows, he wants to do the job from above, after the floor has been framed. First, he would install pieces of 1/2-inch pressure-treated plywood between the joists. Next, mineral wool between the joists; and finally, a continuous layer of 1 1/2-inch-thick foam on top of the joists to slow down thermal bridging. The shop floor will be made from tongue-and-groove OSB 3/4 inch thick.
An alternative would be to add 2×4 sleepers across the tops of the joists on 24-inch centers and fill the voids in between with extruded polystyrene (XPS) foam. The floor could be laid over the 2x4s.
“The above plan (and even the alternative) will allow me to set my joists and build everything from the top as I do not have access to the underside of the joists for attaching foam or plywood directly,” he says. “Over what little space there is available under the building, I intend to put down a permeable fabric on the ground…
Weekly Newsletter
Get building science and energy efficiency advice, plus special offers, in your inbox.
This article is only available to GBA Prime Members
Sign up for a free trial and get instant access to this article as well as GBA’s complete library of premium articles and construction details.
Start Free TrialAlready a member? Log in
43 Comments
I'm not that keen on membrane as a capillary break under posts. A bit like the pond liner discussed above, it can hold moisture rather than repel it. A better choice are squares of UHDP. You can bed them in caulking and screw them to the bottom of the post. For jobs with minimal loading, dollar store plastic cutting boards are an inexpensive source.
Many building codes require a mechanical connection at the base of the post that can resist uplift. That hardware usually creates its own capillary break.
Most of the discussion above centered on moisture. However I do have a question relating to the compression of the foam. I believe that Mr Taylor indicated that the compression was too great for the foam and Mr Yost thought that, though higher compressive strengths of EPS are available, standard 25psi EPS would be sufficient. But that's not my question.....which is: The point of diagram 2 was to reduce the compression of the foam in diagram 1, but, Is not the compression of the foam in diagrams 1 and 2 the same? I'm just trying to understand concepts.
Ted,
In diagram one, the weight bears on the top of the joists, which dig into the soft foam.
In diagram two, the joists are supported by joist hangers, so the foam bears no weight.
I like this idea but, I can't understand what happens if there is another pier under the internal joists. For instance, in diagram two, imagine there is another pier under the joist all the way to the right side of that picture. Wouldn't there be a compression issue there?
K,
The foam does have to be interrupted at the piers at interior beams, but that incurs a very minor energy penalty
I have not decided how I'm going to do this yet. But ...
May I also ask about insulating between the joists?
I have some 4.5" ISO with a paper face. If I put that between my floor joists, should it be touching the subfloor? Or is it best to leave a small air gap between the ISO and the subfloor?
I plan to build my 16 by 16 floor in two sections so that I can put plywood on the bottom, then flip it over in order to complete it.
Ted,
Another way of doing this (which really only makes sense if the foam is going to be the only floor insulation) would be to have two layers of subfloor, with the foam sandwiched between them. That way the live-loads of the structure that bear on the foam are distributed by the plywood, instead of digging into the joists. I did that when I built my own much smaller outbuildings, where the additional cost wasn't as substantial.
Funny but sad at the same time. Basically, everyone here is wrong or totally confused by the properties of Modern Materials and Techniques. You could correct many of your conceptions bu assembling a Simple Test Section and put weight on it. On the water absorption, XPS is a Sponge, check the research before printing Fake News. on the facts on lifetime R values.
Of Course! Thanks,
Thanks for writing this article Martin and Malcolm. I asked for your advice for some similar additions I am designing in Ontario. I may have some additional questions after reading the article in greater detail now.
Lowell,
I'm glad to provide advice. But just to be clear: The article on this page was written by Scott Gibson.
Sorry Martin and Hi Scott,
If the addition is too big to do the raised floor in sections. Would you still not recommend putting the rigid foam on top of the joists even if it were sandwiched by 2 layers of plywood above and below it as Malcolm I think was suggesting in the reply section?
Also, do you think if we add a few vertical weeping tiles (just like they do for basement window wells I think) below the several inches river-rock or gravel bed with landscape cloth under the floor assembly would help to drain water under the floor?
Hi Lowell,
Aren't you in Toronto? I'm not sure how you would incorporate enough rigid insulation into the floor to satisfy the code. Is there something that precludes excavation to provide a typical foundation, or at least adequate work space below the addition?
Thanks Malcolm for your reply again.
I was instructed by the client and contractor not to design a continuous foundation to save on construction cost.
In Toronto we need R-31 for exposed floors. With 2" of XPS (sorry for not using EPS! Can I also get confirmation both XPS & Polyiso will decrease in R-value in cold temperatures?) and 2"x8" filled entirely with "Eco"-fibreglass I can get R-33.
There is only around 1'-0" joist space below the addition!
Thanks for your reply in advance again.
Lowell,
It sounds like you are a designer, working with a homeowner and a contractor.
Even when the client and contractor "instruct" you "to save on construction cost," you are under no obligation, as a designer, to go along with their plan for a foundation that (a) may not comply with building codes, and (b) may have long-term durability issues.
Hi Martin,
Yes. I tend to attract contractors that may be 'new' to the country as my 'clients' in Toronto.
This is a one storey addition. Helical piles are used as commonplace by 'old-stock' seasoned contractors here if I may say it like that!
I think my design is to code, I am trying to design buildings that will be durable as well but with an economy of means which is I think in keeping with all green movements.
My take as a green architect today is to critic and 'improve' on designs that are over-engineered and can be once again considered as 'over-kill' structures!
Lowell Lo (OAA Architect)
On a related topic, I am trying to promote a Rain-barrel and Sub-irrigated Planter Bed Initiative for Sub-urban Yards. Here is the link to the wooden demountable and stackable rain-barrel stand!
http://www.lowelllodesign.com/things-permaculture/#THE%20DEMOUNTABLE%20AND%20STACK-ABLE%20WOODEN%20RAIN-BARREL%20STAND
Lowell:
"Can I also get confirmation both XPS & Polyiso will decrease in R-value in cold temperatures?"
Nope!
XPS loses some R value over TIME, but over TEMPERATURE the performance INCREASES monotonically with falling temperatures.
Polyiso has a more complicated curve with temperature, and that curve is different across different vendors. All polyiso increase in performance from the labeled R value as temperatures begin to fall, but when the average temperature through the foam layer drops to ~45F it begins to drop off with temperature.
Dow Chemical claims to have beaten that derating issue with their Thermax branded product. See the comparative derating curves of different insulation products in Figure 2 of this document:
http://msdssearch.dow.com/PublishedLiteratureDOWCOM/dh_09b4/0901b803809b49c0.pdf?filepath=styrofoam/pdfs/noreg/179-00263.pdf&fromPage=GetDoc
The oddball curved polyiso was a sample of 2lb density roofing polyiso only rated R5.2/inch @ 75F (the labeled R value), and should be considered a worst-case. Most 2lb roofing polyiso is rated abotu R5.7-R5.8/inch, and while it may have a similar, parallel curve it will be higher than that. Most 1.0-1.5lb foil faced polyiso is rated R6- R6.5/inch, and would be better still. The knee in the curve where it drops below it's labeled performance varies a bit too.
And mind you this is the average temperature from the warm side to the cold side of the foam layer, not the outdoor/cold-side temperature.
Also note: The manufacturers will only warrantee XPS to hit 90% of the labeled R value. So at 2" from a design point of view you can only reasonably count on R9, not the labeled R10. In fact the fully depleted end of life R-value will probably be around R8.4, warrantee notwithstanding. If you're being conservative, assume R8.4, not R9, and definitely not R10.
Thanks for your reply and info Dana. Embarrassed to say, I will need to reread your message to get all the technical points.
Lowell,
Q. "Can I also get confirmation both XPS & Polyiso will decrease in R-value in cold temperatures?"
A. I think you are confusing two issues: the issue of so-called "thermal drift" and the issue of cold-weather performance.
To learn more about thermal drift in rigid foam products, see this article: "Thermal Drift of Polyiso and XPS."
To learn more about the cold weather performance of polyiso, EPS, and XPS, see these two articles:
"In Cold Climates, R-5 Foam Beats R-6"
"Cold-Weather Performance of Polyisocyanurate"
Thanks for your point n links, Martin
Lowell,
You wrote, "There is only around 1'-0" joist space below the addition!" I'm not sure what this means. Does this mean that there is 1 foot from the bottom of the joists to the soil? Or does this mean that there is 1 foot from the top of the joists to the soil? Or something else?
I don't believe in crawlspaces that are too tight for human entry. Some building codes forbid that type of crawlspace -- but maybe such a crawlspace is legal in Ontario. If it is, you'll have to figure out how to build it. Most ways are problematic.
Whenever someone writes a question to GBA asking how to build a crawlspace that is too tight for human entry, I answer, "Don't. Either pour a slab, or excavate for a proper crawlspace."
Martin,
Sorry. I meant 1'-0" clearance under the bottom of the pressure-treated ply.
A lot of these new-comer clients won't appear to have big budgets may I also say.
Lowell,
A couple of related questions:
- If you can't flip the floor sections, how are you going to get the pressure treated plywood on the underside of the floor joists?
- If you can somehow get the pressure treated plywood soffit attached, why can't you put the foam on the underside of the joists too?
As background, here are BSC's recommendations for building a framed floor over earth (i.e., piers or open crawl space): the most relevant is to use a sheet of foam across the bottom of the joists (Figure 6 & Figure 7), as sketched and discussed previously.
BSI-009: New Light In Crawlspaces
https://buildingscience.com/documents/insights/bsi-009-new-light-in-crawlspaces
I might have a marginal solution based on these bad constraints.
I'm borrowing a page from Henri Fennell (a wizard of SPF and a good friend). He helped us on a project in Climate Zone 6 where a vented attic was ice damming like crazy--massive heat loss from mechanicals in a vented attic. An unvented attic would be a good solution, but access was terrible (mechanicals installed, tall attic, and occupied conditions below). The solution he came up with: demolish the top side of the roof, hold THERMAX polyisocyanurate board on the underside of the rafters, and "tack" it in place with spray foam. Add more SPF to secure it, and fill the cavity with insulation. See pictures below.
So using this idea: if you can slide polyisocyanurate sheets laterally across the ground, and pull them up against the bottom of the floor framing, you could "tack" them in place with ccSPF in a similar manner. Of course, you need a clever way to pull the polyiso sheets up--you could attach "handles" (e.g., glued-on polyiso blocks) to pull the sheet up from above. Then fill the remainder of the cavity with loose fill insulation.
Not a great solutions by any means: there's no good way to install physical protection (critter barrier) on the underside of the rigid foam. Using a THERMAX product with a thicker foil facer provides some more protection, but I would bet that critters would get through eventually. Also, air barrier continuity is dependent on ccSPF spray on foam seams and at penetrations.. probably reasonable, but nowhere as good as taping from below with full access.
One possible way to reduce critter entry is using an XPS board with a cement facer laminated to it (http://www.tclear.com/products/wallguard/). But with this solution, you're hanging an awful lot of weight from your spray foam attachment.
So.... all this being said... wouldn't you rather build a slab on grade?
[Photo credits HC Fennell Consulting http://polyurethanefoamconsulting.com/%5D
Its a pile of research while also all being a pile of BAD information, we're going off the deep end here.
George,
What we are doing here is having a discussion. If you don't agree, then make your case. Just saying we are all idiots and invoking "Fake News" doesn't help in a the political or building science context.
So what are your concerns about the things that have been said about the load-bearing capacity of foam? What are your concerns with the research Building Science does?
Malcolm- is it troll feeding season?
If you click on his profile and review his relatively short list of (mostly content-free) posts you'll find that in his world if it's not EPS & concrete it's not worth owning. But it's also (apparently) not worth engaging on the particulars.
I see that you failed to see the truth, so listen closely.
EPS is capable fo doing the job without additional assistance, fact.
PolySprays and today's engineered wood are TOXIC to health and R-Values, fact.
I'm getting some "Riversong" vibes all over again, Burrr!. I guess some folks think "their way" is the only way. :-O
Geeez Armando, your starting to sound like my wife:-/
Sorry just caught up with the messages again. Had to visit the hospital for reoccurring panic attacks from stress I think, embarrassed to say!)
I may have to email you Malcolm to get your advice without having to group message everyone here!
I live on a piece of land without a single flat spot, and rock ledge throughout,so excavation is out of the question. So in building my shop I've been debating all these issues. Naturally I have to side with Malcolm and Martin (thanks to Scott for assembling the article, which seems to be an edited version of the discussion). I'm using the foam sandwich approach which Malcolm suggested, on top of the joists. This to leave more room around the joists for air and access for inspection - I do not enclose anything where Carpenter ants can find easy access.
I intend to have an R 20 floor -by no means adequate for a house, but warm enough for a shop that sees intermittent use.
Brian,
You don't mention your climate zone or your foundation plans. But if "excavation is out of the question," I hope that you have come up with a plan for a structurally sound foundation that is impervious to frost heaves.
Vancouver Island is one big rock. it isn't unusual to have an entire foundation built on a sloped ledge. Typically what we do is to excavate the area where the walls will go. On the uphill side fill any low voids with concrete so that water will not pool against the foundation. If the void is too deep, we use that as the low spot for the perimeter drain, and run solid pipe (switching to schedule 40) under the foundation and out the lower side. Not needing footings to distribute loads, rods epoxied into the rock pin the walls. Before pouring the foundation, it's important to power-wash the rock so you get good adhesion with no voids.
Edit: And on the lower side we place a small pit of drain-rock inside the foundation with performed pipe running out through the wall to drain any water that accumulates under the slab.
I'm just north of you , Martin, in the Champlain Valley of Vermont, so zone 6, or 5 depending on the year. My shop is on piers that sit on ledge so I'm not worried about drainage around a foundation. I built it with the idea it would have 4inches of foam on top of the sub-floor, then another layer of plywood (likely the finished floor). The foam on the floor will be continuous with wall insulation.
Thanks for the interest and advise guys
Still a spotlight article I see. I need to keep up with more comments here!
Would be interesting to see discussion of putting foam strips inter-spaced with wood blocks over the top of the joists. The blocks to take the compression force and the foam to reduce thermal bridging over most of the joist area.
OSB, foam, then more OSB is another option to address thermal bridging/cold spots.
Wouldn't strapping the joists with 2"x4"s achieve the same result?
Somewhat more thermal bridging and wood, but a similar result.
Would adding a layer of 1/2" plywood (would 1/4" or 7/32" be viable in this situation?) between the joists and the EPS solve the issue of the joists pressing on the EPS? It would extend out between the 2x4 and 2x8s on the edge. The EPS would still be bearing weight, but I imagine it would be much more spread out.
There doesn't seem to be a definitive answer to the vapor barrier under the gravel pad. What's the best way to keep mosquitoes from getting pools of water to breed underneath as well as minimizing the vapor under the floor?
What if it's just a shed, don't want a crawlspace under it, and can't really pour a slab?
Edit: changed rafters to joists. I'm talking about the same topic as this entire post and somehow I used the wrong term.
Pepper,
I'm guessing that you need to start a new Q&A thread for these questions.
Since your first question talks about both "rafters" and "joists," I don't know if you are talking about a floor assembly or a roof assembly. But in general, you need to install an OSB or plywood subfloor (generally at least 1/2 inch thick, although the thickness of the subfloor depends on the joist spacing) before you can install a continuous horizontal layer of rigid foam.
The best way to keep mosquitoes from breeding in puddles under your house is to make sure that the dirt floor of your crawl space is higher than the exterior grade, so that liquids drain away from the house.
Q. "What if it's just a shed, don't want a crawlspace under it, and can't really pour a slab?"
A. There are only so many ways to build a foundation. The technical answer to your question is, "You could build a basement foundation," but you are unlikely to do that. For more information, see "Crawl Spaces vs. Skirts."
Based on the context of this post, being floor-centric, I meant joists (I fixed my post for clarity). I'm very new to framing, insulation, and general building so I'm still getting some terms mixed up.
I was only able to read the first few paragraphs of that article (since I'm not a GBA prime member).
I'm looking to build an insulated shed. I think I'll make a new post.
Thanks for the Spotlight, and for all the good advice. Would SIP floor panels work? Seems like this would help with keeping the critters out, but it doesn't address the problem with thermal bridging.
Log in or become a member to post a comment.
Sign up Log in