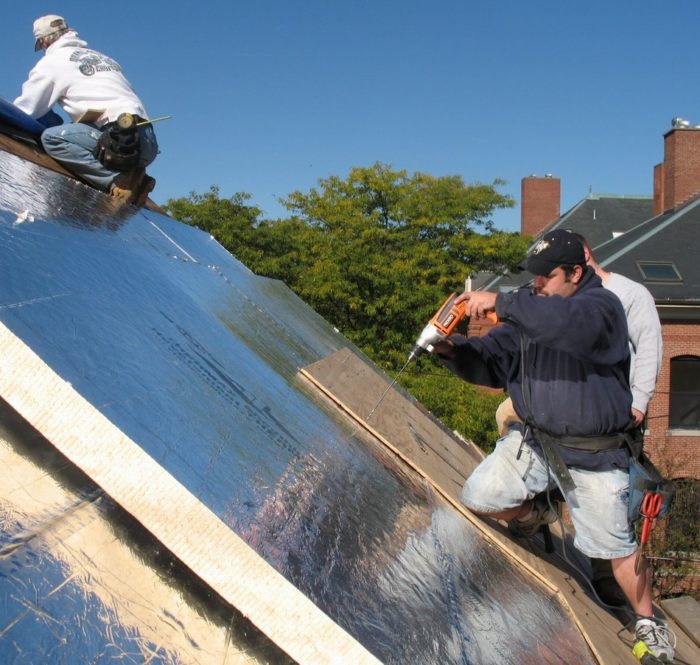
Image Credit: Image #1: Green Building Advisor - Alex Cheimets job
UPDATED on December 15, 2017 with information on the U-factor alternative.
A roof over a vented, unconditioned attic does not need to include any insulation. However, most cathedral ceilings and low-slope (flat) roofs are insulated roof assemblies: with this kind of roof, the insulation follows the slope of the roof.
Insulated roof assemblies can be vented or unvented. There are lots of different ways to insulate this type of roof, but one of the best methods calls for the installation of rigid foam insulation above the roof sheathing.
There are at least two good reasons why this approach makes more sense than installing the insulation under the roof sheathing:
- Rigid foam above the roof sheathing interrupts thermal bridging through the rafters.
- Rigid foam above the roof sheathing keeps the sheathing warmer and drier than it would be if all the insulation were on the interior side of the roof sheathing.
How much foam do I need?
If you plan to install rigid foam above your roof sheathing, you have two choices:
- Option 1: You can install all of the insulation above the roof sheathing (in which case the rigid foam has to meet minimum code requirements for ceiling R-value); or
- Option 2: You can install some of the insulation above the roof sheathing, and the rest of the insulation underneath the roof sheathing (and in direct contact with the roof sheathing).
If you choose Option 1, your rigid foam will be fairly thick:
Weekly Newsletter
Get building science and energy efficiency advice, plus special offers, in your inbox.
This article is only available to GBA Prime Members
Sign up for a free trial and get instant access to this article as well as GBA’s complete library of premium articles and construction details.
Start Free TrialAlready a member? Log in
272 Comments
Great article, thanks Martin.
Great article, thanks Martin. Will be using the un-"vented-over" method when we build our addition, probably with the EPS buffered polyiso option for the foam.
Have you ever heard of someone installing 2x4s over the first half of the foam, parallel to the rafters, with 1.5" foamboard between the 2x4s to fill the gap, then installing the rest of the foam over top? Seems like you could avoid a lot of the frustration associated with using 10" screws. Plus, the tiny thermal penalty would be more than overcome by avoiding metal fasteners traveling directly through the assembly.
Do you see any drawbacks wiyh this method? Does it seem impractical?
Response to Peter Rogers
Peter,
Yes, I've heard of the method you describe. You'll end up with a roof assembly that isn't quite as well insulated as it would have been without the 2x4s in the middle of the sandwich. But in some cases, ease of installation may trump performance. The decision is yours.
A couple of comments...
The amount of exterior-R needs to rise above the IRC prescripitive minimums if the total-R is going to be above code min. The whole point of the prescriptive minimum is to keep the average temperature of the roof deck sufficiently above the average wintertime dew point of the conditioned space air that it doesn't accumulate too much moisture. If you increase the interior-side R value such that the total R goes higher than code min, you MUST raise the exterior-side R proportionally or the roof deck will run colder.
For example, in climate zone 5 the code minimum is R49, and the minimum exterior-R prescription for splitting that R is R20, or about 41% of the total. To reach code min you would then have to install R29 on the interior side. But if R38 is installed between the rafters, the total R would then be R58, which is great, but the exterior-R is now only about 34% of the total- the roof deck will run substantially colder. To hit the same average roof deck temp as the code-min prescriptive with R38s on the interior would require R26 for the exterior foam bringing the total center-cavity R to R64. (R26 / R64= 41%)
On another note, regarding the derating of polyiso for temperature it's the average temperature through the foam, and not the exterior temperature that is the relevant parameter. At an average temp through the foam of 25F the performance drops below R4, true. But if polyiso is the only insulation and the interior is kept at 70F and the exterior temp is 25F, the average temp through the foam is 47.5, or about +9C. Looking at Karagiozis' curve (https://www.greenbuildingadvisor.com/sites/default/files/Karagiozis%20-%20thermal%20conductivity%20of%20a%20variety%20of%20insulations%20as%20a%20function%20of%20mean%20temperature.jpg ), at +9C the performance of polyiso at a mean temp of +9C is comparable to that of XPS at +9C. The performance of XPS at a mean temperature of +9C/47.5F is substantially above it's R5/inch labeled performance, which is tested at a mean foam temp of 75F, with the cold side at 60F, the hot side at 90F.
So, in the all-polyiso insulation stackup when the outdoor temp is +25F, the performance is still well above R5/inch, which is still pretty good.
But in the climate zone 5 prescriptive-mininum situation with R29 on the interior, R20 polyiso on the exterior, the warm side of the polyiso is colder than 70F. At an interior temp of 70F and an outdoor temp of 25F, the roof deck is colder, about 40% of the temperature difference above the outdoor temp, or about 43F. With an outdoor temp of 25F and roof deck temp of ~43F the mean temp through the foam is now about 34F/1C. Looking at Karagiosis' derating curve the performance of polyiso at a mean temp of 1C is about half that of XPS at 1C, which.
The performance of XPS at +1C is no better than R5.5/inch, which means that in a 40% of labeled R on the exterior stackup the performance of the polyiso is LESS THAN R2.8 / inch, not R4.0inch (!).
What this means for the average roof deck temp is complex, since during the warmer part of an average winter day in climate zone 5 the performance is substantially higher than during the coldest part of the day, but still performing at less than the labeled-R. But during the shoulder seasons it will perform substantially BETTER than it's labeled R as the mean-temp through the foam crosses through the +15C knee in Karagiozis' curve, which means the roof deck can dry faster.
To compensate for the plummeting performance of polyiso in those stackups it's useful to split the thickness using equal thickness of EPS to polyiso, maintaining the prescriptive minimums. EPS performance rises in performance at low temps, and with EPS on the exterior it keeps the polyiso layer wamer, warm enough to improve it's average performance. In the zone 5/R20 case, 2" of EPS (R8) and 2" of polyiso (R12) would meet the prescriptive minimum. But now rather than having a mean temp of 34F through the polyiso when it's +25F out it will be running about 38F/+3C through that layer, and would be performing at about R4/inch, or R8 @ 2" , while the EPS would be running about R9, for a net performance of R17.
A mean daily temp of +25F is pretty typical for a climate zone 5 location in January, but it's (usually) substantially higher in December & February, and the performance of polyiso will rise rapidly at those higher temperatures, reaching the peak performance knee in the curve in March in the 2" + 2" stackup. So even though the roof deck moisture accumulates faster in January than anticipated based on just the labeled R values, the drying season begins sooner, so it's still a moisture-safe and decent thermal performance stackup, a stackup that really will indeed average about R20 over the entire heating season.
Of course going a bit higher than the prescriptive minimums gives you more moisture margin, but it's still worth splitting the thickness 50/50 with EPS to compensate for the derating curves. For an all-foam code-min solution that can be reduced to about 35 / 65 in climate zone 5 (4" of EPS + 5.5" polyiso) and it would meet or beat R49 throughout the season.
Response to Dana Dorsett
Dana,
Thanks for your very helpful comments. I have edited my article to reflect your points.
Martin,
Great article. If you
Martin,
Great article. If you refer to this article in QA answers will non-GBA prime members be able to read it? It's really good information.
First time in 14 years I did not have ice dams!
Live in zone 5 NH. 200 year colonial.
1.screwed old boards down, had to replace some, skinned with plywood
2. Ice and water as air barrier
3. 3 inches of polyiso, 1 inch sheets staggered and taped
4. 3 inch thick layer of Eps on top of polyiso , taped seams
5.screwed 2x4 on flat every 16, screwed plywood through 2x4 to deck and beams
6. Second layer ice and water over that.
Had 4 feet of snow on roof and did not sniff an ice dam. First time in 14 years. Great way to go if anyone is interested. Even with all this believe it or not the roof is lighter because I started by stripping 4 layers of shingles. Got to love old houses.
Hi Terry, I'm getting ready to do exactly what you've done. I'm curious, have you had any concerns with using Ice and water as the air barrier? I'm curious if the smell will be noticeable and if any of the adhesive will eventually soften and "run" or drip between the T&G cedar boards.
I had same concerns and found out there is butyl based peel and stick roof underlayments such as Grace Ultra. It does not use the rubberized asphalt that the "ice and water" does. I'm guessing it is not used as much since it is 3x the price of the regular asphalt based version.
wow, bomber roof assembly!
Question:
Since you are replacing bad board sheathing, is it still necessary to skin it with plywood?
Charlie,
Whether or not to add plywood above old board sheathing is a judgment call. If the boards are tight and coplanar, the plywood is unnecessary (assuming, of course, that there is a good air barrier like Ice & Water Shield, which was the case on Terry Grube's roof). If the boards have wide gaps and varying thickness, however, many roofers would prefer a new plywood surface.
I looked at the links in
I looked at the links in Lucy's comment (good links Lucy!) and was taken by an idea in the third one using SIPs on a roof. SIPs really are a good idea here because of the thickness and the nailer being included. The big disadvantage is that you don't need more than 1 layer and then it wouldn't be staggered, like two individual layers of foam would be.
Here's an idea for the enterprising types. (Not me) Shouldn't there be a standardized type of SIP that is T&Ged on all 4 sides just like hardwood flooring? I'm not talking T&G on the nailers only but on the whole thickness of the SIP. If SIPs could be made like that in a standardized way it would eliminate all the fussiness in using 2 individual layers of foam. You have all the advantages of staggered seams by using that method, perhaps with some canned spray at the joints.
Attaching Metal Roofing
If I am planning to install a standing seam metal roof, is it possible to attach it directly through the rigid foam? Or, if a top layer of plywood is necessary, what's the thinnest plywood that you'd recommend?
Response to Lucy Foxworth (Comment #5)
Lucy,
Taunton Press has decided to put all my blogs (those written after late January 2015) behind the new paywall. These blogs can only be read by GBA Prime members. However, Taunton is still offering a 10-day free trial membership.
Response to Terry Grube (Comment #6)
Terry,
Thanks for sharing your story. I'm glad that following this approach solved your ice dam problem.
Response to Eric Habegger (Comment #7)
Eric,
I'm confused by your reference to links in Lucy's comment -- which comment? which links? -- but my article does discuss the use of SIPs as one approach to adding rigid foam above the roof sheathing of an existing house.
Respose to Matt Brewster (Comment #8)
Matt,
As far as I know, standing-seam metal roofing can't be installed on rigid foam; it has to be installed on plywood, OSB, or (possibly) purlins. If you want to be sure, talk to your roofer or the manufacturer of the roofing panels.
I imagine that you could install it on 5/8" plywood, but of course 3/4" would be better.
This is a similar situation which brought me to this chat. I currently am building an unvented roof assembly 5:12 pitch. I am in CZ5 and will be installing ZIPS 1/2" over the rafters, taped. Over that I plan to install 2 layers of Neopor GPS insulation boards (R20). I will stick to the ratio for the interior insulation. I will be installing metal roof panels on furring strips over the Neopor.
I would prefer not to add the expense of another layer of plywood over the Neopor. I do see the need though for a waterproof membrane possibly over the Neopor.
The ZIPs under the Neopor is a water tight barrier but is under the Neopor, but according to this I also need an air barrier over the ZIPs. So is using ZIPs under a waist? At least it is a backup
If a second layer of plywood is used, then I assume it would be best to put OSB/Ply on the rafters, then the Neopor, than the ZIPS on the outer layer, over the Neopor?
Any tips on this layering would help. It gets to a point with too much layering and complications, that just doing spray foam on the interior starts to make more sense.
The attached shows what I am talking about.
User 7927072,
If your primary roof sheathing is taped Zip sheathing, it's not "a waste." It provide an air barrier (which is important) and a secondary water barrier in case your roofing is destroyed by a hurricane or tornado.
Building codes require the installation of roofing underlayment (i.e., asphalt felt or synthetic roofing underlayment). Although you may be able to argue that taped Zip sheathing is equivalent to underlayment, it would make sense to me to install roofing underlayment between the rigid foam and the purlins.
Whether or not you install a second continuous layer of roof sheathing (OSB or plywood) above the rigid foam is up to you (and up to the manufacturer of your brand of metal roofing, since the manufacturer sets the rules on installation requirements). Note that building codes require materials to be installed in accordance with manufacturers' instructions.
Got it, thank you. One last question. I read in the article that an "air barrier" is needed over the sheathing. Is that still correct with ZIPS because it is not actually an air barrier.
When properly taped as required by the manufacturer (Huber), Zip sheathing is an air barrier. Assuming that the installers of the Zip sheathing do a good job (which means using a roller to press down the tape properly), no additional air barrier is required at the sheathing level.
Links for roofing over foam
Martin,
I wrote a response to Dirk Gently's question about installing foam on a roof. It's this post. That's where the links are.
https://www.greenbuildingadvisor.com/community/forum/gba-pro-help/40117/r-25-rigid-insulated-roof-deck-cold-metal-roof-above-question
Response to Lucy foxworth
Lucy,
Thanks for clearing up the confusion. If other GBA readers are interested, here are the links that Lucy shared:
Insulating the roof with polyiso foam boards
Retrofitting an Insulated Cold Roof
Ventilated Cold Roof
Washer-head extra long screws - up to 18 in. long
FastenMaster's HeadLok screws work great for screwing down 2xs or sheathing over thick foam. The washer-head style has good holding power and planes out flush without the need to overdrive and bury the hex head on many other screws.
Best part is they're available up to 18 in. long
http://www.fastenmaster.com/details/product/headlok-heavy-duty-flathead-fastener.html
Response to Mike Guertin
Mike,
Thanks. I have edited the article to include your FastenMaster link, and the information on maximum length.
Great information, Martin, as
Great information, Martin, as always! I am so happy to have found your advice through this website.
Just confirming that I understand correctly: Through-fastened metal roofing can be attached through 1x3 purlins over foam sheathing, correct? I am about to start building an 8x20 "tiny house" and am sold on this method of roof insulation, but I'm struggling to keep my build weight low enough for my trailer. So if possible, it seems best to use purlins on my house, rather than another layer of (heavy) sheathing. (I plan on using 2" of polyiso on top of my structural sheathing.)
What do you think? Any concerns? Thanks in advance!
Response to Michaela Riley
Michaela,
Yes, you can install through-fastened metal roofing to purlins. I would suggest 1x4s rather than 1x3s. You can install them 24 inches o.c., screwed through the foam to the rafters below.
Of course, you still need solid sheathing (usually OSB or plywood) between the rafters and the rigid foam.
Interior Air Barrier Question
First, this article (and commentary) are incredibly thorough and very helpful as I am working with a customer interested in just such a roof retro-fit. If I can still get a question answered it is whether an interior air barrier is necessary on the inside of fibrous insulation under the roof deck when using the "Option 2" roof. It seems like it should be. Assuming it is, do you think dense-packing cellulose behind something like Mento-Plus would work. The house has vaulted and attic portions. Roof deck insulation is being chosen for continuity, the attic areas have limited accessibility, and cellulose will already be on site. To avoid getting into spray foam or having to get rigid material into the attic, I'm wondering if this is a possibility?
Response to Andy Kosick
Andy,
It is always important to make sure that you know where your air barrier is, and to seal all leaks in your building envelope.
Many builders establish the air barrier at the sheathing level. It is also possible to use well-taped rigid foam (above the roof sheathing) as your air barrier. Any air leaks at the eaves or ridge must be located and sealed.
Once you've done this, a second air barrier under your fluffy insulation isn't strictly necessary -- but it certainly can't hurt. If you want to establish your primary air barrier on the interior side of the fluffy insulation rather than at the roof sheathing layer or rigid foam layer, that's certainly possible.
Q. "Do you think dense-packing cellulose behind something like Mento-Plus would work?"
A. I assume that Mento-Plus is an air barrier. Most installers of dense-packed cellulose use an air-permeable membrane like InsulWeb for dense-pack jobs. Because InsulWeb is air-permeable, it allows air to escape during the installation process. For more information, see How to Install Cellulose Insulation.
Thanks for the quick response.
I see your point about installation issues, duly noted. Although it still makes me nervous, I feel reasonably reassured that if an air barrier is established at the roof deck and an adequate percentage of R-value is outside of that, some air permeability of the fluffy stuff is acceptable. Besides it seems that an open cell foam installation wouldn't be much different than net and blown cellulose under these conditions.
Percentage of rigid above plywood at unvented cathedral ceiling
Climate Zone 4C Portland Oregon: I want to ensure that I have the right percentage of r-value above the roof deck relative to below the roof deck for dealing with condensation at the roof deck. In comments, Dana Dorsett commented particularly on this subject. She talks about the exterior side needing a minimum of 41% of the total r-value. What/where does this comes from and backup for this?
Response to Daniel LaJoie
Daniel,
The relevant code requirements are explained in the article on this page, as well as in How to Build an Insulated Cathedral Ceiling.
In Climate Zone 4, the code requires at least R-10 of rigid foam above the roof sheathing for the type of roof assembly that you are contemplating.
Estimate for foam over rafters
Hi folks,
First, an heartfelt "thank you" to all the professionals on this site for the building science education I'm getting!
I have a typical American Foursquare in zone 5. I just got a quote from a roofing company to tear-off the original cedar shake plus two layers of asphalt, install nailbase over the rafters, and then re-install the fascia and gutters, new asphalt shingles. The quote was $26k. Is that reasonable?
My neighbor has the identical home next to me. Last year, he paid $7500 for the tear-off and new asphalt shingles. I was hoping I could get the nailbase done for a total of around $13k, but that's just speaking with my wallet and the practicality of my spending.
Regards,
Tom
Response to Tom Woodman
Tom,
There is no way for us to determine if the quote is reasonable. We don't know the size of the roof; how many feet off the ground it is; whether the roof has good access for ladders or difficult access; the clearance to adjacent houses; and whether there is room to set a dumpster or to stage materials and equipment.
We don't even know the R-value of the nailbase.
If you don't like the estimate, call up a few more roofing contractors and get a few more estimates.
SIP vs. Rigid Foam in Z2 Hot-Humid
I have a small uninsulated concrete block home in Clearwater, Florida. (Added stucco and elastomeric paint to exterior, would have added rigid foam if I knew then what I know now.) There also is no insulation in the wall between the attached garage and the house. Now the simple gable roof needs replacing. I can see it buckling in a couple small areas and there has been leaking, which has been fixed. AC handler and ducting are in the attic and probably leaky. Also, I'd like to use the attic for storage and possibly cathedralize the living room (which is the center of the rectangle). I read your other article, "Creating a Conditioned Attic-Five questions to consider before insulating a sloped roof" and this. I have seriously thought about using SIPs. Innova Eco is in Miami, not too far, and their roof SIPs are 10", with EPS and MgO panel on top side. They spray a coating on top of that. I have requested a quote. However, it sounds like your rigid foam concept might be preferable.
Keep in mind that it rains a LOT here. It has rained heavily almost every day for the past 2 months. The temperature never gets below 32-F and I'm not worried about heating the house. I do not set the AC below 80 in the summer, and let it get up to 86 during the day, running it mainly to reduce humidity. (It is undersized for the current condition of the house, so it will always run long enough to remove humidity.)
If this were your house, what would you do? Is there a specific formulation that would be preferable in Zone 2 hot-humid-rainy?
EDIT: I was thinking about removing the sheathing, at least in the small damaged areas, but I just saw the photo of the installation over existing roof. Would this work?
Thank you for your always-excellent articles.
Response to Andrea W.
Andrea,
Q. "If this were your house, what would you do?"
A. If I could afford to do the work, I would install roof insulation that meets minimum code requirements. In your climate zone (Zone 2), that means R-38. Since your air handler and ductwork are in your attic, this insulation should be installed above your roof sheathing, so that you create an unvented conditioned attic. In other words, you should follow the advice given in the article posted on this page.
You shouldn't do any of this work without first exposing enough of your roof sheathing to make sure that the sheathing and rafters are sound. Repair as necessary before proceeding.
If you can't afford the work -- welcome to the club. Do the best you can with the money you have. Good luck.
Response to Robert Johnson III
Robert,
Q. "For such an unconditioned house, would one or two inches of above-deck insulation help somewhat reduce the transfer of the tropical sun's heat into the living area?"
A. Yes, although you can't expect to be cool and dry when the windows are open all day, and the weather is hot and humid. Your expectations need to be low enough to be satisfied with the approach you have chosen. If the humidity is beginning to get to you, you should install window glass and an air conditioner.
Q. "If so, should we resort to XPS?"
A. To insulate above your roof sheathing, the usual approach is rigid foam. However, XPS is the least environmentally friendly option (because it is manufactured with a blowing agent with a high global warming potential). Either EPS or polyiso would be more environmentally friendly.
Q. "Does this look approach to the above-deck insulation look functional?"
A. Yes, your stack-up will work.
Q. "Can we get away without venting in the above-deck roof, given our unconditioned house?"
A. There is no need to vent the roof you describe (especially in a hot, humid climate, where venting is counterproductive).
Q. "I don't know how the roofers will be able to attach the standing seam once the roof is built up in this way--the screws must somehow artfully pass through the above layers to stop within the old 1.5" brushed cedar T&G deck without being visible from below in the open beam ceilings."
A. First of all, a little bit of math should help with roofers choose a good screw length. (I think that 2 3/4 inch screws would work fine.) That said, I think that standing-seam roofs are routinely fastened to 1/2 inch plywood, without being attached to rafters or roof framing. Talk to your roofer.
Q. "I've read in a couple of places that "whirlybird" attic fans (we're about to install a solar one to cool our attic) can cause attic wood rot--is this a concern under our unconditioned scenario?"
A. In a hot, humid climate, you definitely don't want to install a powered attic ventilator. For more information on this topic, see Fans in the Attic: Do They Help or Do They Hurt?
Above-deck insulation under aluminum, on an unconditioned house
Aloha--relieved to just find this site, and impressed with the level of expertise in evidence here! I've not yet found a treatment of our particular simple unconditioned building scenario--forgive if I missed it. Excellent article, and dialogue, here.
We live in a screen-windowed 1965 tract house (no AC or heat year-round), in Kane'ohe on the island of O'ahu, which is rather humid and warm, and rainy for much of the year. The house is unsealed and unconditioned. About a third of the 2,500 sf low-pitch roof is over a crawl-space attic; the rest is cathedral-style with 3.5" x 7" beams (only about 12' at peak), and nothing but about 1.5" x 8" brushed cedar T&G and Ice & Water Guard between us and the sky post-tear-off. (We did the tear-off just in time for flash flood rains today--but that's a different issue.)
I've not yet been able to find building science addressing above-deck insulation for such an open house. What we just tore off was the original pitch and gravel and two layers of modified bitumen; what we'll lay down is aluminum standing seam. Here's what I (know I) don't know.
Q1: For such an unconditioned house, would one or two inches of above-deck insulation help somewhat reduce the transfer of the tropical sun's heat into the living area?
Q2: If so, should we resort to XPS? Does this look approach to the above-deck insulation look functional--
g. aluminum standing seam
f. tar paper
e. plywood (1/2"?)
d. XPS (1"?)
c. tar paper
b. ice and water guard
a. wood deck
Q3: Can we get away without venting in the above-deck roof, given our unconditioned house?
Q4: I don't know how the roofers will be able to attach the standing seam once the roof is built up in this way--the screws must somehow artfully pass through the above layers to stop within the old 1.5" brushed cedar T&G deck without being visible from below in the open beam ceilings. Probably can't just anchor to the beams, which are spaced about 4' apart. (Hurricanes rarely actually hit us, but every once in a while, they will. We're somewhat inland, close to the Ko'olau mountains, but storms are possible.)
Q5: I've read in a couple of places that "whirlybird" attic fans (we're about to install a solar one to cool our attic) can cause attic wood rot--is this a concern under our unconditioned scenario?
Mahalo Nui in advance for your help as we take this path to a "permanent" and cooler roof!
Above-deck radiant barrier and aluminum, on unconditioned house
Thank you again very much for your help! May I ask what you think might be the relative effectiveness at slowing heat transfer using a radiant barrier (TechShield) board under aluminum standing seam as follows (instead of ~1.5" of polyiso), on a year-round unconditioned, unsealed house in hot/wet climate?
e. aluminum standing seam
d. high temp underlayment
c. TechShield (1/2")
b. water & ice peel & stick
a. wood deck
Mahalo!
Response to Robert Johnson III
Robert,
A radiant barrier won't be effective if you sandwich it between roofing underlayment and Ice & Water Shield. The radiant barrier only works if it faces an air space.
If you are willing to build your stack-up this way:
f. aluminum standing seam roofing
e. high temp underlayment
d. 1/2-inch-thick radiant barrier roof sheathing, shiny side down
c. 1x4 furring strips, 16 inches on center, installed from soffit to ridge (parallel to the rakes)
b. water & ice peel & stick
a. wood deck
...then you would get a benefit from the radiant barrier.
According to ASHRAE Fundamentals, a 3/4-inch-thick air space bounded by such a radiant barrier will have an R-value (resistance to downward heat flow) of between R-2.1 and R-2.3. That is less effective than 1.5 inch of polyiso, which has an R-value of about R-8. So the polyiso wins.
A few comments for Robert Johnson III
On a low-pitched roof in the tropics you may actually exceed the ~160F operating temp limit for polystyrene (EPS or XPS). I've measured roof temps about that high on dark membrane flat roofs even at 42 degrees north latitude, on a 70F early afternoon under a clear sky(!). Polyisocyanurate would be a much better choice, since it's good to 300F. For reference:
http://www.engineeringtoolbox.com/insulation-temperatures-d_922.html
The solar reflective index(SRI) of the finish coat of your aluminium roof also matters- it makes as much or greater difference than a radiant barrier under the roof. The aged SRI of various roofing materials can be searched on the CRRC site:
http://coolroofs.org/products/results
White finishes tend to have higher infra-red emittance compared to bare metals, and a somewhat higher SRI lower solar spectrum reflectivity compared to bare metal. Take a look at this vendors' published SRIs:
http://www.americanbuildings.com/upload/Literature/Solar%20Reflectant%20ratings.pdf
Note that the zinc plated aluminum SRI is only 72, due to the ultra- low 0.08 emittance. The white (probably titanium oxide) finishes from that vendor are comparable or better than the much shinier bare zinc. This is pretty typical.
Mounting metal roofing on 2x purlins giving 1.5" of air between the roof and foil-faced polyiso gives you the thermal benefit of the radiant-barrier facer on the polyiso, as well as the full R-value of the polyiso. The exact R of the polyiso isn't constant with temperature and it falls off with rising temp, so it depends on just how hot that purlin-cavity gets. Any convective cooling you can get through that purlin gap is going to help, but it will vary with location on the roof, the greatest benefit being near where the convection air is entering.
(edited to add)
In that climate, the thermal mass of an inch or two of concrete on top of the roof deck plus an inch of polyiso on top of that does quite a bit for thermal performance, if the structure can take the load. (Reinforcing thin concrete with steel wire would be important to keep it from breaking up and becoming a hazard in an earthquake. Presumably local building codes cover concrete roofs.)
Preexisting rafter-mates and vapour barrier in retrofit planning
We have a vaulted ceiling in our old cabin-like home. it is a storey and a half. upstairs we have knee walls and a front porch overhang with no insulation. straight forward roof - moderate to highly sloped. we have the usual intrusions plus a wood stove chimney and 2 light tubes. We need a better roof as we currently have both ice damming with some water making its way inside and likely not enough insulation.
The vaulted ceiling profile from the interior to the exterior has the following layers: drywall, vapour barrier, extended rafters with 5.5" of Roxul (R22?), rafter-mate baffles, original T&G roof deck, roofing paper/felt, shingles.
I am interested in adding insulation to the roof. EPS overtop the existing shingles & 2x4's for air channels, 1x3 strapping across the channels for a vented cold metal roof overtop the added foam.
1. Are the rafter-mates problematic? If so, would their effect be negated if I filled the gap with spray foam from above the deck down into the void? I would need to drill access holes down through the shingles and decking - what distance between holes would be needed?
2. Is the vapour barrier problematic? need to be removed? (if so then I would forgo the approach in question 1.)
3. Should the porch overhang be insulated from underneath? (has a t&g Ceiling).
4. What happens at the peak? Currently there is a ridge vent - does it just get ripped off? along with careful mating of rooftop foam to follow?
5. We live in Sudbury, ON. What zone are we in??
Answers here can help me wrap my around around the best course of action moving forward and will help determine whether there is work to be done on top of the existing roof or both beneath and on top of the existing roof.
Many thanks! Great and helpful articles on this subject that I wish existed but 16 years ago. Time to get it done right.
Zone 3 Roof Plan
Thank you in advance for providing your expertise here!
I am building a 4/12 roof in Zone 3 (Charlotte area North Carolina). I'm planning on open cell spray foam on the underside of the roof deck.
Given that it seems that the ideal roof deck build-up would consist of:
1. OSB sheathing
2. 1/2" rigid foam board
3. OSB sheathing
4. Moisture barrier
5. Asphalt shingles.
I am curious as to whether the first layer of OSB could be omitted if the foam board did not react to the spray foam?
And considering my climatic zone, what would be the optimal roof and wall construction method?
Thank you again,
Pat
Response to Patrick Cronin
Patrick,
If you want to install rigid foam above your roof sheathing in Climate Zone 3, then 1/2 inch of rigid foam board is not "ideal." This rigid foam layer needs a minimum R-value of R-5, and that's impossible with 1/2 inch of foam. As my article states, you need a minimum of about 1.5 inch of EPS, 1 inch of XPS, or 1 inch of polyiso.
In your question, there's another issue: the difference between a minimum standard and an ideal roof. It's hard to design the ideal roof, but in general, thicker rigid foam is better than thinner rigid foam.
When building a sandwich as you propose -- OSB, rigid foam, and OSB -- you can't omit the lower layer of OSB, because roof sheathing is structural. It has to be fastened directly to your roof trusses or rafters to obtain the strength that engineers insist on.
Fire considerations of air gap under shingled roof deck?
Given that:
1) roof shingles are normally nailed into 5/8" plywood or OSB roof decking, and
2) a sloped ventilation channel is often needed directly under this wooden decking (and above the exterior foam) to prevent moisture accumulation,
what happens in the case of a fire? Seems to me that fire would spread rapidly through such a roof (much quicker than though a roof that had mineral wool in direct contact with the underside of the topmost roof decking).
Is there a less flammable roof decking material/stack up that you'd recommend?
I'm in Zone 4 Coastal.
Thanks!
Response to John Charlesworth
John,
The vast majority of roof shingles are fastened to roof sheathing that has an air gap underneath. (Most sloped roofs are uninsulated -- these roofs cover a vented unconditioned attic.)
This type of roof (a vented roof) meets building codes and the expectations of the insurance industry.
It's possible that unvented insulated roof assemblies are somewhat safer in a fire than conventional vented roof assemblies -- but if that's true, I've never seen any data that shows that it's true. Perhaps some researchers have studied the issue and published a paper reporting on their findings -- but if they have, I haven't seen it.
In the absence of data, I hesitate to speculate.
Second response to John Charlesworth
John,
Q. "Is there a less flammable roof decking material/stack up that you'd recommend?"
A. I wouldn't recommend it (because of the high expense), but you could adopt commercial construction techniques if you wanted to. It's possible to use steel framing and to install steel decking (or concrete decking) if you want. You can even install steel roofing on top of your steel or concrete decking.
The firefighters I know talk
The firefighters I know talk about that, when flames enter the soffit vents and set the decking on fire, it's game over in a hurry.
Thinking of doing a "chainsaw retrofit" which (unfortunately) would connect the rainscreen gap on the walls to the roof's ventilation channel.
I can reduce the flame spread up the rainscreen gap by using mineral wool exterior insulation and fiber-cement siding (leaving the wooden furring strips as the only flammable item on the exterior walls) but wasn't sure how to do a similar risk reduction on the roof ventilation channel.
Is there a non-flammable sheathing material for roof decking that's suitable for attaching shingles to? (Thinking something like DensGlass)?
Third response to John Charlesworth
John,
It sounds like you are talking about a small subset of structure fires -- namely structure fires that are caused by wildfires. These are buildings that burn down after being ignited by burning vegetation near the house.
Structure fires caused by wildfires probably represent a small percentage of structure fires in the U.S. -- (and I welcome statistics on this issue from knowledgeable GBA readers).
The percentage of structure fires caused by wildfires ranges widely by location. Here in New England, this type of fire represents something close to 0% of all structure fires. In dry areas of California, the percentage is of course higher.
Rigid insulation under a Cool Roof in Zone 3?
Appreciate this extremely helpful blog. I live in Charleston, SC, in an old (1858) 3-story wooden house. Plan to replace asphalt shingle roof with standing seam metal. Currently there is no insulation anywhere, and the third floor, basically an enclosed attic, gets crushed by heat in the summer.
Proposed project: strip off the asphalt shingles, apply 1" polyiso and then "cool roof" metal over that. Would then add cellulose in rafters, and on top of of the third floor ceiling (the third floor ceiling is low, leaving an A-frame of unfinished and partially vented attic above it).
My question is whether the polyiso is worth it if we are going with a very reflective/emissive metal roof, if heat gain on the third floor is the big energy issue.
Thanks for your thoughts!
Response to Blan Holman
Blan,
Q. "My question is whether the polyiso is worth it."
A. If you are planning an unvented insulated roof assembly -- one in which the insulation follows the roof slope -- the polyiso is not only "worth it," it is required. The polyiso performs an essential function: it keeps the roof sheathing above the dew point during the winter, preventing moisture accumulation in the sheathing.
If, instead, you are considering a vented roof assembly, then the polyiso would be unnecessary.
Rigid insulation under a Cool Roof in Zone 3?
Thank you! Wondering if this is not an "insulated roof assembly" -- cellulose would go on top of the conditioned third floor living space's ceiling, which is a good four feet below the rafters that will support the new metal roof. The space above the ceiling could be thought of as uninsulated attic; if so, would answer be the same? Charleston SC is very warm and humid.
Response to Blan Holman
Blan,
If you have a vented unconditioned attic, then installing polyiso above your roof sheathing is a waste of polyiso. If you want to install a thicker layer of insulation, then all of the insulation belongs together -- in your case, on the attic floor. Take the money that you would have spent on the polyiso and use it for a thicker layer of cellulose.
Of course, I hope you don't have any ducts up there. Installing ducts in an unconditioned attic is always a mistake.
For more information on these issues, see:
All About Attic Venting
Creating a Conditioned Attic
Keeping Ducts Indoors
Rigid insulation under a Cool Roof in Zone 3?
Thanks! Last followup I promise: house was built in 1858 -- attic space above the third floor ceiling is not intentionally "vented" (so gable vent, no soffit vents) but it is leaky, w gable ends constructed out of lapped siding with no sheathing.
Also, to complicate things, because the third floor living space is mostly an enclosed attic, the third floor walls follow the roofline. So while it has a flat ceiling (creating an 5 ft wide by 4 ft tall A-frame "attic" above it), the 4 ft of sloped walls follow the roof line, then terminate into a knee wall.
I could *probably* get cellulose in the rafters between the sloped wall and roofline. Did I mention there are five dormers? Nothing easy with this house. My concern from the thread was having cellulose in those rafters without insulation above roof decking. Then again it is very warm here so maybe water concerns are lessened. We get about 20 freezing nights a year total.
Charleston is a lovely town w beautiful old houses. But they are very strict about changes to rooflines and features...
Rigid insulation under a Cool Roof in Zone 3?
*no* gable vents, and no soffit vents
Response to Blan Holman
Blan,
If you have a section of your sloped roof assembly that is insulated (or needs to be insulated), then of course you have to follow the usual rules for these types of insulated assemblies. You still have the usual choices: you can create a vented insulated roof assembly or an unvented insulated roof assembly. If the assembly is an unvented insulated assembly, it would need at least some rigid foam on the exterior side of the roof sheathing in your climate zone.
If these concepts are new to you, you can read more about them in these two articles:
How to Build an Insulated Cathedral Ceiling
Insulating a Cape Cod House
novice: want to insulate over asphalt shingle cottage roof
Any help gratefully received: 1953: northern Michigan near Traverse City, my parents had a 900 s f tongue and groove cottage built. Asphalt shingle roof. The underside of the roof, the supporting beams, all are visible and beautiful to me. So I want to insulate, but on top of the roof. No insulation at all now. I am trying to learn from this site. Would anyone advise me further? I have subscribed to GBA and have begun to read articles. Don't know what "zone" I'm in, there. Thank you
Response to Amy D'Ancona
Amy,
Traverse City, Michigan is in Climate Zone 6. Here is a link to GBA's Q&A page -- the Climate Zone map is on that page. (If you click the map, it will get bigger):
https://www.greenbuildingadvisor.com/qa
For information on installing rigid foam above roof sheathing, read the article on this page (the page where you posted this question). If you have further questions, you may want to post them on GBA's Q&A page.
question for Martin on air barriers
Martin,
You wrote, "Before installing the rigid foam, make sure that the roof sheathing is airtight (or that you install an air barrier immediately above the roof sheathing)." Is it acceptable to use a layer of taped foil-faced polyiso foam immediately above untaped sheathing as the air barrier?
[Editor's note: To read the answer to this question, as well as other comments, advance to Page 2 by clicking on the 2 below.]
Response to David Hicks
David,
There are two schools of thought on this question.
1. Joe Lstiburek's take is that you need an air barrier at the sheathing level, or else you risk the possibility that warm interior air will get into the cracks between the rigid foam panels, creating convective loops that melt the frost on your roof in stripes. It happened to Joe, so he now insists on a tight air barrier at the sheathing level.
2. Other builders say that taped rigid foam can be the air barrier, especially if you have at least two layers of rigid foam with staggered seams (to prevent those embarrassing frost-melt stripes). If you go this route, it's best to tape each layer of rigid foam.
Thanks for the response
I had in mind that plain vanilla osb with polyiso taped with inexpensive foil tape was more cost-effective than either trying to tape untreated OSB with Siga or using Zip panels and tape. But if two layers of polyiso and taping are needed, that defeats some of the cost benefit. Zip system and EPS is probably more effective since there is no ambiguity in the air barrier (it's all at the sheathing layer) as long as you don't mind the frustration of fastening many inches of EPS to the roof.
Flat reroof in Albuquerque
Dear Martin and GBA,
Great article. Thanks for in detailed reviews on this topic.
I am currently planning to reroof my flat roof home here in Albuquerque, NM. My roof construction is as follows (interior to exterior): gypsum board, polyethylene, R-29 fiberglass batts in 2x12 joists, half-inch plywood decking, and finally a tar and gravel roof. There is no dead airspace between the fiberglass and the plywood decking. This setup may be similar to that of the Arizona houses that Bill Rose investigated. The roof is currently un-vented.
At this point I plan to do a complete tear-off of the existing roof in order to inspect the plywood. Then the new roof will consist of tapered (1/4” over 1 ft pitch) polyiso foam, 75 lb. paper followed by 3 layers of 15 lb fiberglass paper with hot mopped tar in between each layer, and then gravel. Strips of modified bitamen will be applied to the parapet walls.
The question is whether or not we should install roof vents. The roofer is talking about installing one-way vents will “let the hot air out.” Should this roof be vented in this way?
A separate issue is the thickness of the polyiso foam. The minimum thickness of the foam will be 0.5”. If I understand your articles correctly, for my climate zone (4B), I am required by code to insulate the roof deck with R-15 so that condensate does not form on the plywood. However, to increase the minimum thickness of the polyiso foam to 2” would put parts of the roof above the parapet wall, and not to mention greatly increase the cost of this project.
Thanks for your help.
Response to Eric Harding
Eric,
Q. "The question is whether or not we should install roof vents. The roofer is talking about installing one-way vents will 'let the hot air out.' Should this roof be vented in this way?"
No. If you are installing rigid foam above the roof sheathing, you certainly don't want to ventilate under the roof sheathing. Your roofer is wrong.
Q. "The minimum thickness of the foam will be 0.5 inch. If I understand your articles correctly, for my climate zone (4B), I am required by code to insulate the roof deck with R-15 so that condensate does not form on the plywood. However, to increase the minimum thickness of the polyiso foam to 2 inches would put parts of the roof above the parapet wall, and not to mention greatly increase the cost of this project."
A. If you are using polyiso, 2.5 inches of polyiso would be the minimum thickness for your climate zone. Where the roof extends above the parapet, simply trim the exposed edges with metal flashing. Parapets are useless (and in fact often inhibit the proper installation of insulation and also often inhibit proper drainage).
Here is a link to an article with more information on the type of roof you are describing: Insulating Low-Slope Residential Roofs.
Metal roofing attached to battens on EPS
Martin,
I'd like to attach 5V metal roofing to battens laid atop 10" of EPS, which would be on top of the OSB sheathing. My concern is, for V5, structurally, I don't think that I can just lay the battens atop the EPS. 10" tall battens also seems like a bad idea. To add more complication, I was thinking about encasing the EPS in 2" of closed cell foam to serve as the vapor barrier and the last bit of required insulation.
What's the best way to approach this? Will battens laid atop the Closed cell foam and bolted to the sheathing with 10" lag screws with rubber washers be sufficient? Would that compromise the vapr barrier?
Response to Justin Husted
Justin,
Ten inches is a lot of foam, so it's time for you to consult an engineer.
One simple approach is simply to buy 10-inch-thick SIPs. (Here is a link to one of many SIP manufacturers that sells 10-inch-thick SIPs: http://sipsteamusa.com/packages/.)
The SIP manufacturer can provide advice on fastening -- they have in-house engineers.
Hi Martin,
I've looked at
Hi Martin,
I've looked at all the drawings on GBA, but I can't find one that details this approach when using purlins over the foam, rather than another layer of roof sheathing. Can you please confirm that I've got the stackup right? From the bottom up:
* Rafters filled with Roxul
* ZIP system with taped seams as the air barrier
* Asphalt felt
* Two layers of polyiso with staggered, taped seams
* 1x4 purlins fastened to the rafters with long screws
* Aluminum roofing fastened to the purlins
My main questions here are:
* I want to confirm that the roof underlayment goes *beneath* the foam in this scenario.
* Do I need to worry about the purlins having any moisture problems, or (as I assume from the article) is that a non-issue?
Also, I have opted for applied overhangs, per the details in this article: https://www.greenbuildingadvisor.com/blogs/dept/musings/getting-insulation-out-your-walls-and-ceilings. Their drawing does not show the use of exterior foam on the roof, though, so I have a couple more questions related to how this all fits together:
* Do I need to run sheathing over the top of the applied rafter tails to give the polyiso a continuous surface to rest on? I would love to avoid the extra weight (since I'm building a tiny house on a trailer), but I also don't want the polyiso to end up getting crushed into the rafter tails if we step on that area of the roof, so I'm assuming it's best to have sheathing there to distribute the weight.
* I will be attaching our fascia boards to the applied rafter tails, and I've ordered our roof drip edge long enough to extend from the top of the roof, down over the polyiso, and over the top of the fascia boards. To protect the edges of the polyiso from moisture, I am planning to run Grace Ice & Water around the edges of the polyiso and down to overlap the fascia boards, similar to the detail for the "Thick Roof" drawing shown on this article. Does that sound reasonable?
Thanks again for all your excellent advice! I don't know what I'd do without this website.
Michaela
Response to Michaela Riley
Michaela,
Q. "Can you please confirm that I've got the stackup right?"
A. You haven't given us enough information for an answer. In order to provide an answer, we need to know (a) your climate zone; (b) the thickness of the mineral wool insulation; and (c) the thickness of the polyiso.
Q. "I want to confirm that the roof underlayment goes beneath the foam in this scenario."
A. Roofing underlayment is required by most roofing manufacturers and building codes, and these manufacturers and most code enforcement officers would probably recommend that the roofing underlayment be installed above the polyiso.
You don't need roofing underlayment above the taped Zip sheathing, because taped Zip sheathing is waterproof. However, if you want to install asphalt felt between the Zip sheathing and the polyiso, the asphalt felt will do no harm.
Q. "Do I need to worry about the purlins having any moisture problems, or (as I assume from the article) is that a non-issue?"
A. Your purlins will be fine, until the day your roofing starts leaking.
Q. "I have opted for applied overhangs, per the details in this article: https://www.greenbuildingadvisor.com/blogs/dept/musings/getting-insulatio.... Their drawing does not show the use of exterior foam on the roof, though."
A. Look again. The PERSIST approach shown in that article includes rigid foam above the roof sheathing. Then 2x4s (usually installed on the flat) are installed above the rigid foam; these 2x4s are extended at the eaves and rakes to create a roof overhang.
Q. "Do I need to run sheathing over the top of the applied rafter tails to give the polyiso a continuous surface to rest on?"
A. You don't need polyiso on the roof overhangs.
Q. "I will be attaching our fascia boards to the applied rafter tails, and I've ordered our roof drip edge long enough to extend from the top of the roof, down over the polyiso, and over the top of the fascia boards. To protect the edges of the polyiso from moisture, I am planning to run Grace Ice & Water around the edges of the polyiso and down to overlap the fascia boards, similar to the detail for the "Thick Roof" drawing shown on this article. Does that sound reasonable?"
A. I don't think so. In most cases, a PERSIST roof has no rigid foam on the applied overhangs. See the detail drawing below.
.
Response to Timothy Robinson
Timothy,
Q. "What type of roof underlayment between the roof deck and first layer of polyiso is necessary with the taped OSB seams and foil facing of the staggered foam panels?"
A. If the OSB seams are taped with a high-quality tape, and you are also taping the rigid foam seams, you have good air barriers. Strictly speaking, you don't need roofing underlayment on the lowest level of OSB -- but because the work on the roof might take a while (during the construction phase), some ordinary asphalt felt might be a good idea to help keep the OSB dry.
Q. "I can't figure out what type of tape is used for the OSB joints. Is it one of the aluminum tapes?"
A. The three best tapes for taping OSB are Siga Wigluv, Huber Zip System tape, and 3M All Weather Flashing Tape. Here are links to two articles with more information on tape performance:
Return to the Backyard Tape Test
Two Wingnuts Describe Their Backyard Tape Tests
Insulation stack Zone 5 question
The attached file shows a roof detail for an ICF house planned for Omaha, Nebraska. You'll see that the top chord of the 30" roof trusses rests on the ICF wall. Between the trusses and sill pieces, I intended to use sill sealer and spray foam to keep the joint between the top of the wall and roof deck airtight.
I've tried to follow the guidance across multiple articles and, not counting the nominal R-value of the non-foam layers, estimate the insulation above the roof deck to approach R-55, but, in any event, exceed the R-49 required.
In case the attachment doesn't open/display correctly, the assembly stack from top to bottom is:
a. steel roofing screwed to osb sheathing
b. 5/8" T&G OSB sheathing
c. 4" XPS
d. 5.5" Polyiso
e. synthetic roof underlayment
f. 3/4" T&G OSB with seams taped.
Other than the general question about whether I've misunderstood something in the articles designing the insulated roof this way and you see serious red flags:
1) What type of roof underlayment between the roof deck and first layer of polyiso is necessary with the taped OSB seams and foil facing of the staggered foam panels?
2) I can't figure out what type of tape is used for the OSB joints. Is it one of the aluminum tapes?
Many thanks for this valuable resource.
Insulation stack
Perfect! Really appreciate it, Martin. This greatly helped me avoid some bad/more expensive ideas from contractor and architect.
hip roof in zone 6
We are renovating a mid-1800's carriage house in mid-coast Maine (zone 6). The building was completely gutted prior to purchase and the exposed beams and roof structure sold us on the place. What we didn't factor in was the difficulties and expense of insulating the unvented hipped roof with two skylights on opposing sides of the "peak". We decided it would be worth covering up the exposed roof decking and rafters to insulate at a reasonable cost. Not as reasonable as we had hoped. Three quotes all came in over $10k, so we're now considering insulating exclusively with rigid foam above even though the roof is still in fairly good condition. If this option proves expensive at least we'll save by not having to finish the interior ceiling and we get to keep the feature that sold us on the building in the first place.
I'm not getting comparable information from roofers so turned to this site for some knowledge. All fully understood that I planned to keep the ceiling exposed and only insulate from above. The first roofer wouldn't touch the job, it just isn't in his wheelhouse. The second (a fairly sizable company) thinks 6"+ inches of foam is too much and came back with a recommendation of using a 3.5" of polyiso nailbase panel faced on one side with MDF, followed by asphalt shingles which they said this would give us R20 on the roof, no mention of ventilation. When I balked at R20 and repeated there would be no insulation on the interior, they responded with R20 is pretty good considering it has nothing now. (FYI, the town I live in only follows state code for plumbing and electric so no one is going to insist I get to R49.) Roofer #3 has no problem stacking up 6"+ of foam on the roof, but insisted he would only do the job if he installs prefabricated metal roof vents in every other rafter bay. I had a hard time grasping that one and his explanation didn't do much to help my understanding.
My questions – First, can you tell me if the 3rd roofers insistence on vents in every other rafter bay is appropriate for this situation? And if so, can you explain how all my heated interior air in the winter won't just escape through those vents?
In regards to this article and my situation, assuming Option 1, all insulation above the roof sheathing, and being able to skimp a little on R value and code, would installing less than R49 above (but hopefully more than R20) cause any issues and if so what sort?
I'm a little confused regarding the section on ventilation channels. Does an air gap, in and of itself, between the foam and the upper layer of sheathing make a difference or must there be a path for air to travel from soffit to ridge and if so, is there some way to create this above what is currently an unvented hipped roof? Basically, does this paragraph apply with a hip roof?
Thank you so much for this column and the opportunity to learn.
Reply to Kim
Kim, I'm sorry you are having so much trouble finding someone do do this. You could certainly survive with R20, but there's no good reason to stop with that little. But then the suggestion of venting every other rafter by is very hard to make sense of. The only things I can think of that he might mean are either putting some venting above the foam between it and the new roofing, which is a good idea. Or maybe he think you are going to put drywall over the rafters, and have uninsulated closed cavities there, and he wants them vented to the indoors.
There might be builders who are generalists and do some roofing who understand insulation better than the roofers you are talking to.
You could also try talking to EcoCor, which is a very innovative green building company at least somewhat near you. They have a system of cellulose insulated wall and roof panels that are primarily for new construction, but they also do retrofits, and might be able to offer something good for your situation. And if they can't, they might know a builder to refer you to.
Kim,
I agree with Charlie.
If
Kim,
I agree with Charlie.
If you want to negotiate with the roofers:
1. You can tell the roofer who likes nailbase that "Nailbase is available in a variety of thicknesses from several manufacturers. For example, ABT Foam sells 9-inch-thick nailbase panels rated at R-33, while Atlas EPS sells 11Âľ-inch-thick nailbase panels rated at R-48."
2. You can point out to the roofer who wants to install ventilation channels underneath the roof insulation that ventilation channels always belong on the exterior side of the insulation, not on the interior side of the insulation. After all, why would you want to introduce cold exterior air into a channel on the interior side of the insulation?
to Martin and Charlie
Martin, I certainly agree that beefing up on the R20 is good, should I assume from your response that being shy of R49 with no added interior insulation will not cause problems?
Nice to know my reasoning is sound on the through the ceiling vents. If I can convince him to vent above the insulation, can that be a simple air gap or must it be vented for air flow from soffit to ridge? And is that feasible with my hip roof?
Charlie, thanks for the lead. I'll seek them out for another opinion and quote. The roofer who suggested the vents is a general builder who does a lot of roofs and he stood inside with me and agreed how cool it would be to keep the ceiling exposed. Maybe he had an off day.
sunroom roof
I'm planning a south side sunroom addition with a simple metal shed roof. I'm in rural southwest NM at 6300 ft - it will get up to 90 in the summer and down to the 20's in the winter (and some snow). I have limited height against the existing brick wall, so the slope will be about 1/12. I am buying 1x6 t&g blue pine (beetle kill) and want to expose between the rafters - as follows: rafters, t&g, underlayment, 2" foam (polyiso?), 2x4 purlins, then metal roof.
My concerns: 1) having enough ventilation to avoid overheating in the summer, 2) will 2" polyiso be enough and is polyiso the right choice, 3) does this make sense?
Thanks for your great articles! So much to think about!
Response to Kim Dolce (Comment #65)
Kim,
Assuming that you don't have to meet any minimum code requirements for R-value -- and it sounds like you don't -- then you can install below-code insulation levels without worrying about moisture problems. If you end up with R-20 foam or R-24 foam instead of R-49 foam, your roof won't rot. You'll just have higher energy bills than a house with code-minimum insulation.
On a hip roof, there isn't much point in spend extra for ventilation channels above the rigid foam, since soffit-to-ridge venting is impossible on a hip roof.
Response to Sherry Litasi (Comment #66)
Sherry,
I urge you to read this article: How to Build an Insulated Cathedral Ceiling.
It sounds like you are located in Climate Zone 4 or 5. In your climate zone, building codes require a minimum of R-49 roof insulation.
You are planning to install only R-12 insulation; that's woefully inadequate. It's fine to use polyiso insulation if you want; but you'll need to install at least 9 inches of polyiso, not 2 inches of polyiso.
Does this method Totally preclude no insulation under sheathing
I am assuming that this article almost exclusively applies to a conditioned and unvented attic, right?
My attic, in a Zone 5 dry arid climate at 5000 feet, is currently passively vented and unconditioned. I favor installing air wash channels under the sheathing but I also want to reduce daytime temps. When the outside air is in the 90's or 100's the temps in the attic can reach 150. For this reason I am leaning towards some form of polyiso or a combination of polyiso and EPS on top of the sheathing. Am I going the wrong direction with this plan?
Response to Roger Smith
Roger,
There are two types of attics: vented unconditioned attics and unvented conditioned attics. You have to decide what type of attic you want.
If you have a vented attic, it makes no sense to install rigid foam above the roof sheathing. A vented attic is basically outdoors -- so installing rigid foam above your roof sheathing is a waste of money and a waste of rigid foam. You might as well put the rigid foam in the branches of a tree in your back yard.
If you want to install rigid foam above your roof sheathing, it means that you are committed to creating an unvented conditioned attic. For more information on this type of attic, see Creating a Conditioned Attic.
If you don't have any HVAC equipment or ducts in your attic, it makes sense to have a vented unconditioned attic. This type of attic is less expensive to insulate, and it usually performs better in all respects than an unvented conditioned attic.
If your attic has HVAC equipment or ducts, you may want to create an unvented conditioned attic.
So how do you reduce daytime attic temps...
or do you just live with it and [over]compensate with a ton of insulation on the attic floor?
Response to Roger Smith
Roger,
As long as your attic doesn't contain any HVAC equipment or ducts, the temperature of your attic is irrelevant. The reason that building codes require R-38 or R-49 insulation on the attic floor is that analysis shows that this level of insulation is cost-effective. It's not only cost-effective -- it's enough insulation that you don't have to worry whether your attic temperature is 110°F or 150°F. In either case, the insulation is enough.
That said, some GBA readers install R-60 attic insulation, and you're free to do that if you want. But putting insulation above the roof sheathing is misguided if you have a vented attic. Instead of adding insulation above your roof sheathing, put it on the attic floor where it belongs.
If you intend to use your attic for storage, and if you are worried that the attic will get so hot that your wax candles (or whatever vulnerable items you are storing) will melt, that's another story. In that case, you probably want to design an unvented conditioned attic.
Much much thanks Martin...
Thanks for clearing that up and steering me in the right direction. This site is awesome made all the better by contributors like you.
Cheers
to vent or not to vent my cathedral ceiling
Hey all,
I’ve read many articles on GBA on this topic and really appreciate the dialog. I’ve learned a lot.
I’m in climate zone 3 and am building a new home and am to the point where I need to make a decision on how to finish the roof structure. The roof is a 12/12 pitch. Simple gable style.
I’ve got a cathedral ceiling throughout consisting of 2x12 TJIs running along a ridge beam. I’ve thrown out the idea of using spray foam on the underside of my sheating due to the fact it's too expensive. As I see it I have these two options and I’m interested in opinions.
Option 1. Create a vent channel underneath the sheathing using cut and cobble method. foam battens created from 2” polyiso glued in place on the top cord of the TJI. That gives me 1.5” of ventilation space. 8 1/2” is left for fiberglass batts. high density R-30 batts are 8 1/4” high so that just fits. The rigid battens are R-10 so that gets me to where I need to be for code. I will have wiring and sprinklers in that ceiling.
Option 2. Create an unvented roof putting foam on top of the sheathing. My roofing is steel and is designed to be mounted on battens/purlins. From what I’ve learned here, seal the seams of the OSB roof sheathing with zip system tape to create an air tight barrier. Put down roof felt. Put full sheets of 2” foam on top of the sheathing and felt tacked in place. I know two layers of 1” foam would be ideal but that’s more expensive per R. Finally, lay down 1x4s parallel to the ridge at 24” spacing and screw those through the foam, felt and sheathing into the rafters. Roofer mounts his roofing clips to the 1x4s and installed the roofing panels. The roof is vented at the ridge and soffit. Inside we have an unvented rafter bay we can fill with standard R30 batts. It would give me extra room for wiring and sprinkler plumbing.
In looking at both options, it appears that they cost about the same in materials. There’s the same square footage of rigid foam required. Option 1 requires glue/caulk/tape to seal the rigid foam and Option 2 requires zip system and housewrap tape and 1x4s.
For labor, it seems that option 2 would be faster given there’s no cut and cobble of rigid foam. Foam is going down in full sheets on the roof and 1x4s are getting tacked in after.
My inspector seems to be ok with either option.
I know the bonus is I get a thermal break with the insulation on the outside. It gets hot here during the Summers so I’m looking to keep a 130 degree metal roof from transferring heat into my loft.
Any thoughts or advice appreciated.
Response to Ehren Maedge
Ehren,
Either approach will work, so the decision is up to you.
If your roof has a skylight or chimney, these features would argue against the vented option (since the features would interrupt the continuity of the ventilation channels).
If you choose Option 2, it would be best if you could fill the entire rafter bays with fluffy insulation (fiberglass, cellulose, or mineral wool) rather than only filling a portion of the cavity depth. If your batts don't fill the full depth, you have two problems: (1) how to make sure that the batts stay in contact with the roof sheathing, and don't slump down, and (2) what material to use as an interior air barrier (which, ideally, needs to be installed in contact with the interior side of the fluffy insulation).
I suppose that you could try to staple up strips of a European air barrier material on the interior side of the batts, but that's fussy work. It's much easier to let your drywall be the interior air barrier -- and if you decide to do that, you need to fill the full depth of the rafter bays with insulation.
Martin,
Thanks for your words
Martin,
Thanks for your words of encouragement and advice. I really appreciate it. Understood on the need to keep fiberglass batts in contact with sheathing.
One other thing came to mind. You mentioned in another article on GBA that venting the top side of sheathing with a cold roof (steel roof fastened on battens allowing air flow directly underneath the roofing but on top of the sheathing) while at the same time venting underneath the sheathing is incompatible. Why is that? I ask because of the intense sun we get here, even if I chose option 1, I like the idea of raising the roof off the sheathing 3/4" and letting some air flow underneath creating a "sombrero" of sorts. It seems like this would keep my roof cooler rather than having heat from the steel roofing get transferred directIy to the sheathing. Why is doing a cold roof a bad idea if I choose option 1?
Response to Ehren Maedge
Ehren,
You must have misunderstood what I wrote. I probably wrote that if a roof has rigid foam above the roof sheathing, you don't want to have a ventilation channel underneath the roof sheathing (because it makes no sense to install insulation on the exterior side of a ventilation channel).
If you want two ventilation channels -- one above the roof sheathing, and one below the roof sheathing -- that's perfectly OK, as long as all of the insulation is on the interior side of the ventilation channels.
got it
Thanks Martin. Makes sense now.
ventilation channels metal roof
Hi Martin,
Thank you for another great article.
I wanted to make sure that there isn't any significant problem with 2x4s being perpendicular to the rafters over the foam rather that parallel, as you recommended in the article for reducing ice dams? This would be to avoid adding additional 1x4 purlins or plywood over the 2x4s for attaching a metal roof. Also, if a channel is only open on one side, will it significantly increase risk of ice dams?
Also, is there any structural concern about adding solar panels to a standing seam metal roof that is attached to 2x4s 24" o.c. rather than plywood base?
Thank you for your advise!
no venting for hip roofs?
In comment 67, you said not to put in ventilation channels with a hip roof. If no ventilation channels, how does one vent a hip roof? Thank you.
Hipped roofs
Typically you build hipped roofs as un-vented assemblies. If you are using metal on the roof you can vent the hips the same way you vent a ridge. There are also some manufactured vents for hipped roofs with asphalt shingles, but I have no idea whether they work.
More on hipped roofs
It's possible (sort of) to vent a hipped roof over an unconditioned attic, with a combination of mushroom vents and (in some cases) a short ridge vent.
If the house has cathedral ceilings, though, I don't recommend a vented approach for a hipped roof.
The only way you might succeed would be with two layers of strapping (probably 2x4 strapping) above the rafters -- one layer perpendicular to the rafters, and another layer parallel to the rafters). Each layer of strapping would be installed at either 16 inches o.c. or 24 inches o.c. You'd still need to be creative when it comes to installing vent outlets (again, probably a combination of mushroom vents and a short ridge vent).
-- Martin Holladay
Also consider DCI SmartVents
Also consider DCI SmartVents or similar.
Best setup for my remodel with 2x6" rafters
Hi Martin,
I have started a remodel of my home in Woodside, CA (I believe climate zone 3). The house has cathedral ceilings and is framed with 2x6".
My plan is to use normal fiberglass between rafters (5.5") which will give me R-19, correct?
And then add polyiso on top following your instructions above. Looks like 2 layers of 1" will give we another R-13 taking me to R-32 which is above the min R-30.
But going for 2" (R-13) + 1" (R-6.5) poly-iso (Rmax Thermasheat 3) would get me to R-38.5 which I guess is a better idea?
Additional questions:
1. You suggest air barrier for the first layer of plywood/OSB (on top of my 2x6") rafter and use "Siga wigluv tape" which sounds good but for the final layer of Rmax Thermaheet (where we also want it airtight) can I use HVAC foil tape (I assume cheaper)?
2. For the new insulation I place between the 2x6 should I use kraft faced fiberglass with the kraft paper down towards the inner ceiling? House has on the interior side drywall and then cedar planks and I am doing all the insulation from the top as I am also re-roofing.
3. If I use OSB board is there any value to add OSB Techshield radiant barrier version? I guess not since the 2 layers of OSB (On top of rafters and on top of polyiso) will both face an insulated area?
Thanks,
/Mats
Response to N/A N/A
Q. "My plan is to use normal fiberglass between rafters (5.5 inches) which will give me R-19, correct?"
A. Correct.
Q. "But going for 2 inches (R-13) + 1 inch (R-6.5) polyiso (Rmax Thermasheet 3) would get me to R-38.5, which I guess is a better idea?"
A. Correct.
Q. "You suggest air barrier for the first layer of plywood/OSB (on top of my 2x6) rafter and use "Siga Wigluv tape," which sounds good, but for the final layer of Rmax Thermaheet (where we also want it airtight) can I use HVAC foil tape (I assume cheaper)?"
A. Yes.
Q. "For the new insulation I place between the 2x6 should I use kraft-faced fiberglass with the kraft paper down towards the inner ceiling?"
A. You could. Unfaced batts would also work.
Q. "If I use OSB board is there any value to add OSB Techshield radiant barrier version? I guess not since the 2 layers of OSB (On top of rafters and on top of polyiso) will both face an insulated area?"
A. You're right: the radiant barrier wouldn't help, because a radiant barrier is only effective if it faces an air space.
-- Martin Holladay
Follow-up question
Hi again Martin.
We intend to install recessed lights (Airtight Title 24 approved cans) in the cathedral ceiling. Since we are using LED lights we can use shorter cans (Halo H25ICAT) that will fit between 5.5" joists for most of the areas but were we have the great room we have 20 feet ceiling and need deeper cans that can adjust for the roof slope and provide 1200 lumens (like Halo HL612ICAT). These cans are typically inside an internal metal box to handle the tilt function. With a depth of 7" they will go through the first plywood layer but I should still be able to cover them with 1 layer of 1" polyiso (R6) plus 1" square cut piece for the rectangular piece. I believe this is enough?
For ceiling between the can and the plywood on top of the rafters can I use Siga wigluv or should it be sealed with some spray foam or silicon?
Also If can fit it flush with 1" polyiso on top of the first plywood layer I can put the 2" on top? I guess there is no issue with putting first 1" polyiso and then 2" polyiso on top vs. start with 2" and then add 1"?
Thanks,
/Mats
Response to N/A N/A
First of all, I advise you to change your user profile so that your screen name isn't "N/A N/A." Here is a link to an article that explains what you need to do: How the GBA Site Displays Readers’ Names.
Second: You are making a big mistake by installing recessed lights in your insulated ceiling. These lights (a) introduce air leaks even when carefully installed, (b) take up volume that should be devoted to insulation, thereby lowering the R-value of your assembly, and (c) create hot thermal chimneys that accelerate the stack effect and lead to hot spots on your roof.
For more information on this issue, see these articles:
How to Build an Insulated Cathedral Ceiling
Ban the Can
Q. "With a depth of 7 inches, the recessed lights will go through the first plywood layer but I should still be able to cover them with 1 layer of 1 inch polyiso (R6) plus 1 inch square cut piece for the rectangular piece. I believe this is enough?"
A. It's not. You're wrong.
lights
The good news is that you have lots of options for other types of lights to install. Not only are there now low-profile LED lights that look the same as recessed lights, but in a high-ceiling room, you don't need them to be low profile anyway.
Climate Zone 3
R30 Insulation not R38 required......
Response to Sarah Deeds
Sarah,
Your comment is cryptic. I'm not sure if it's an observation or a question.
If it's an observation, you're right: many Zone 3 locations in the U.S. have not yet adopted the 2012 IECC, or have adopted a modified (watered-down) version of the 2012 IECC. That means that some Zone 3 homes can get away with R-30 roof insulation instead of the R-38 insulation mandated by the 2012 IECC. (GBA often advises builders to check with their local code authority concerning code questions like these.)
If it's a question, here is the answer: If you are installing R-30 insulation in Zone 3 (following the method discussed in this article), at least 13% of the total R-value of the roof assembly must come from the rigid foam layer. That means that you'll need a minimum of R-3.9 of rigid foam (1 inch of EPS).
For more information on this topic, see Combining Exterior Rigid Foam With Fluffy Insulation.
1930's commercial building update
Hi Martin,
I've just read every word of this article, almost every comment, and joined the website too... Great information here.
I've got two complex issues that have me concerned and we have already hired the roofer and have product on the roof waiting to be installed. Scheduled work to start in two to three weeks, but I fear they will start sooner.
General project, 'restore' and update a 1930's building purpose built for a newspaper, offices & printing plant, plus a 1970's addition. The 1930's building is a steel 'superstructure', wood truss building with brick walls and limestone façade.
The 1970's addition is a steel building, steel decking with cinderblock walls.
We are doing our best to fix years of bad conversions and neglect and bring the building into the modern age. After the newspaper left, it was a school, a boxing gym, artist lofts, and warehouse....
There are two very different roofs to contend with:
Roof 1> 1930's building, 2nd floor office space.
Original roof (still intact) is hot tar over 7/8" tongue & groove deck. We believe according to a roof core that there is only one layer of torch down over the hot tar. At most two layers. Engineers have certified that we do not have to tare the existing roof off. Since the original plaster ceilings were not salvageable, we have exposed the roof trusses and wood roof deck. The intent is to leave them exposed along with the brick walls. There are some small intermittent leaks that appear during heavy rain, but not light rain.
We are Zone 4, which I understand is R38. The roof is a flat roof.
The current stackup is:
>Solar System with racking & ballast - Minimal screws into the OSB layer TBD.
>PVC SlipSheet
>Durolast PVC White Roof
>Densdeck 1/2" (or equal) (Screwed to the OSB Layer)
>4" Polyiso (2"/2")
>1/2" OSB (Screwed thru the polyiso into wood roof trusses)
>4" Polyiso (2"/2")
>Existing Torch Down & Hot Tar
>Tongue & Groove
>Roof Truss
One other item of note is that because the interior tongue & groove ceiling is fully exposed, the contractor has agreed to align the screws from the OSB into the roof trusses so we don't have a ceiling riddled with screws. And in order to ensure enough pull out resistance, the screws have to land in the roof trusses, not just the wood deck.
I don't believe that there is a vapor barrier in the current stackup. Is this a concern?
I read comment #3 several times and I understand the concern, my question is, because we are basically exposed to the ceiling, how much should we worry about not having EPS on the top layer? (We are on the very northern edge of Zone 4, as in the next town is Zone 5).
Roof 2> 1970's building, steel deck
Again, the original roof is intact. The building was purpose built for a high speed web-offset press with huge ink drying ovens & motors generating heat, so the idea was to get the heat OUT of the building, not trap it inside. There is also a 10 foot x 30 foot skylight in the middle of the room, and the ceiling height is 18 feet. The skylight is single pane glass, a whole separate issue I'm sure!
Existing building construction is a heavy gauge steel deck, fully exposed on the inside. There are NO screws holding the roof on. It is beautiful to look at and we are doing our best to keep it free from screws. Again, the structural engineer has determined we do not have to remove the existing roof.
This space will be used as a residence, again with a fully exposed roof structure.
Current Stackup:
>Solar System with racking & ballast - Minimal screws into the OSB layer TBD.
>PVC SlipSheet
>Durolast PVC White Roof
>Densdeck 1/2" (or equal) Screwed into the 1/2 OSB.
>1-1/2" Polyiso (new)
>1/2" OSB (new)
>Existing roll roofing layer - possibly a torch down, (original roof)
>1-1/2" Polyiso - Glued directly to the steel deck. - (original)
>Steel Deck. - (original)
>Screws up into OSB. (new) Rather than screw down into the steel deck, the contractor has agreed to drill holes in the steel deck and screw up INTO the OSB so that we can have a fixed pattern of screw heads on the exposed ceiling so that it doesn't look like a warehouse with screws sticking out into the space.
Concerns are many here. Because of the huge skylight and the structural setup, we can not add more than 2" of additional height to the roof or Durolast will not permit the design because the curb heights become too small.
Also, the Steel deck is a commercial 'deep channel' heavy gauge deck. The channel 'pockets' are open air with only the 1-1/2" polyiso above it.
With the low total R Value and these air-channels, I'm worried in the winter that the roof deck will be cold enough to literally condense moisture on the inside.
Note, we have had the building for two years, but it has only been heated to 55° with a scorched air blower heater, to keep the sprinkler pipes from freezing, and we have NOT seen a problem, but the space was vacant and I assume ambient moisture levels were not high enough.
We considered doing a tareoff but the consensus is that the Polyiso in place now is still effective and removing it won't allow us to increase the overall R value, so it was not worth removing it.
I have also thought that perhaps we should figure out a way to fill the steel channels. One idea is to drill holes from the roof down into the channels and fill them with foam and then cover them with the OSB. (Any recommendations on the foam to do this?)
Any thoughts or other advice?
I hope I made it as clear as possible!
If you're interested, we started a facebook page to collect the history of the building and there are many photos showing it over the years, two of them show the 1970's roof as it overhangs the car park. It was built for the Peekskill Evening Star newspaper.
http://www.facebook.com/peekskilleveningstar/
I hope my post isn't too long winded for you!
Regards,
Sepp.
Response to Sepp (Comment #92)
Sepp,
Q. "I don't believe that there is a vapor barrier in the current stackup. Is this a concern?"
A. The old hot tar (asphalt roof) is a vapor barrier. Relax.
That said, you need an excellent air barrier at the bottom of this stack-up. If any exploratory holes have been drilled in the old roofing, or there are obvious seams or air leaks, these need to be carefully repaired and sealed before the first layer of polyiso goes down. Alternatively, the first layer of polyiso needs taped seams. Even better: tape the seams of the OSB layer in the middle of the sandwich. Use a high-quality tape like Siga Wigluv.
Q. "I read comment #3 several times and I understand the concern, my question is, because we are basically exposed to the ceiling, how much should we worry about not having EPS on the top layer? (We are on the very northern edge of Zone 4, as in the next town is Zone 5)."
A. Well, your 8 inches of polyiso will have an R-value that is at least R-40, and probably more. I wouldn't worry.
Q. "I'm worried in the winter that the roof deck will be cold enough to literally condense moisture on the inside."
A. For the roof with steel decking that has deep channels, the two biggest areas of concern are: (1) The interior perimeter of the roof, where the ceiling meets the wall -- you need to seal the air leaks where the steel channels meet the wall. (2) The exterior perimeter of the roof, there the steel channels may be covered by flashing that allows air penetration to the steel channels between the decking and the lowermost layer of rigid insulation. These channel openings need to be exposed and sealed with spray foam.
I'm not as familiar with commercial roofs as I am with residential roofs. If I were you, I would hire a consultant from Building Science Corp. in Westford, Mass. The consulting fee will be worth every penny you spend. They are experts at air leaks and corrugated steel decks like the one you describe.
Much thanks!
Martin,
Thank you for the quick answers and help.
I will reach out to the company you recommended.
We have had a real hard time getting good advice in all areas of the building. From recommendations to spray foam historic brickwork (HUGE NO NO!) to putting vents in the historic limestone façade!
HVAC requirements has also been a big problem for mix-ed use, conversion of a purpose built historic structure.
And I look forward to reading more on the site in next few weeks. (Indeed I was up for two more hours after I wrote this email last night)
I hope you had a chance to see the photos on facebook, we are very excited to bring this building back to life.
Regards,
Sepp.
How long has this insulation system been used?
I live in the San Francisco Bay Area in the east bay which is climate zone 3. I'm planning an addition and remodel. The roof structure will be 2x8 rafter and I have 2" I can add on top of the sheathing due to zoning height constraints. I'd like to install r30 mineral wool battsbetween the rafters and 1.5" of polyiso above the sheathing. My architect is unfamiliar with this and thinks closed cell spray foam between the rafters is a more proven approach. How long has this sandwich insulation approach been used? I'd rather use it but am concerned if it doesn't have a long track record.
Permeable or Unpermeable membrane under Metal Roof
Martin,
I am building an unvented roof in Marine 4 zone and following your excellent article above, including JL,s suggestion to put an impermeable peel n stick on the bottom layer of roof sheeting which I just completed. My quandary is I am putting down plywood above 7 inches of EPS for my SS metal roof and elswhere on GBA there has been a variety of opinion on whether a permeable membrane would have the ability to breathe out through metal. I am using a snap lock panel tha does have a few slightly raised flanges. Mr. RIversong suggests breathable in all cases, which was my original thought given the bottom impermeable layer. Most of the new synthetics are very low perms .06 or so unless I go to a polyolefin or similar breathable such as GAF deck armour....but these seem to be geared towards shingles. Both these high and low perm synthetics all indicate they pass the D4869 water shower test in Canada so I assume they stop some water penetration equally. HOwever am unsure which way to go as if the metal prevents any realistic breathability I am wondering if the impermeablemembranes would be better protection for the plywood as they may prevent trapped moisture between the metal and the membrane from coming back through the membrane into the deck.... thanks in advance.
Response to Rick Milne
Rick Milne,
There is no outward drying through a standing-seam metal roofing. The metal roofing is a vapor barrier.
If you build an unvented roof assembly -- a common approach -- the vapor permeance of the roofing underlayment is irrelevant.
If you want ventilation channels between the top of the insulation layer and the underside of the upper layer of plywood roof sheathing -- an unnecessary step in most cases, but useful in some climates to reduce the chance of ice dams (a problem that does not generally affect standing-seam roofs) -- the usual method would be to create a ventilation channel by installing 2x4s on the flat, 16 inches or 24 inches on center, from soffit to ridge (in other words, the 2x4s are perpendicular to the ridge). These 2x4s are installed above the top layer of rigid foam, and are fastened to the rafters below with long screws. The result is a ventilation channel that is 1 1/2 inch deep.
The top layer of plywood is fastened to the 2x4s.
What about snow loads?
What about snow loading for these type of assemblies? I'm working on a plan for a mountain lodge that gets drifts up to about 15 feet deep on the roof (and has seen 25 feet deep, though at that point it get shoveled). Does the foam hold up?
Response to Bryce Nesbitt
Bryce,
The rigid foam will hold up just fine. As I'm sure you know, though, you'll need to talk to an engineer about sizing the rafters or trusses.
A few additional questions
Thank you for the informative article and comments. I have a few additional clarificating questions for my situation.
Current situation:
Climate zone 4 Marine. I have a low-slope roof (1:12 on one half, 2:12 on the other) with torchdown, which I am replacing with standing seam metal. The house has vaulted ceilings throughout, with 2x6 rafters, currently filled with 55-year old rockwool insulation (~R-11, definitely well below code). The ceilings are vaulted throughout, which means the insulation is sitting directly on the ceilings, with ventilation space between the insulation and the sheathing. Water leaks and likely condensation from poor insulation have led to some sheathing and rafter damage, which I plan to replace as needed.
Plan:
Current plan is to only replace sheathing where damaged, convert to an unvented roof, and then add 6 inches of polyiso. This implies that I would simply keep the existing rockwool resting on the ceiling. Reason for keeping the rockwool is because I don't want to take down inside ceiling (cedar T&G) and don't want to remove the good sheathing just to remove the old rockwool.
Questions:
Q1: The article states that if some insulation is above sheathing (foam board) and some insulation is below (something breathable), then the insulation underneath should be attached directly to the roof sheathing. Will there be an issue if I keep the existing batts in place, resting on the ceiling instead of attached to the sheathing?
Q2: Between the sheathing and the first layer of polyiso, do I need any type of barrier, such as ice/water shield, or can the polyiso go directly on the sheathing?
Q3. Right now, 2x8 cedar fascia (needs replacement) cover the rafter tails (2x8 fascia is also on the gable ends). I still need the same coverage the fascia is providing today but with the added 6" of polyiso, need to cover that as well. Any ideas on how to cover everything in a way that looks good? I've never seen 2x14 fascia, but maybe I'm not looking hard enough :)
Thanks in advance for your advice.
Response to User 7097488
User 7097488,
First of all, can you tell us your name? (I'm Martin.) It makes this type of online dialogue a lot easier.
Second, you probably should read this article: "Insulating Low-Slope Residential Roofs."
Third, are you sure that the manufacturer of your standing-seam metal roofing allows its roofing to be installed on a roof with a 1-in-12 pitch?
Q. "The article states that if some insulation is above sheathing (foam board) and some insulation is below (something breathable), then the insulation underneath should be attached directly to the roof sheathing. Will there be an issue if I keep the existing batts in place, resting on the ceiling instead of attached to the sheathing?"
A. Probably not, as long as you install 6 inches of polyiso above the roof sheathing as planned. (That will give you about R-37 or R-38 -- not quite code minimum, but good for a retrofit. Good enough, in other words, that you can more or less ignore the contribution of the old insulation.)
Q. "Between the sheathing and the first layer of polyiso, do I need any type of barrier, such as ice/water shield, or can the polyiso go directly on the sheathing?"
A. As is stated in the article on the page where you posted this question, you need an air barrier at this layer. Read the article again. I'll quote:
"Before installing the rigid foam, make sure that the roof sheathing is airtight (or that you install an air barrier immediately above the roof sheathing). There are at least two ways to do this:
• If your roof has board sheathing, install an airtight membrane (for example, Solitex Mento, a product available from 475 High Performance Building Supply), a layer of synthetic roofing underlayment, or a peel-and-stick membrane.
• If your roof has OSB or plywood sheathing, the panel seams can be taped (for example, with Zip System tape or Siga Wigluv tape); after taping the panel seams, install the roofing underlayment of your choice (for example, asphalt felt)."
Q. "Right now, 2x8 cedar fascia (needs replacement) cover the rafter tails (2x8 fascia is also on the gable ends). I still need the same coverage the fascia is providing today but with the added 6" of polyiso, need to cover that as well. Any ideas on how to cover everything in a way that looks good? I've never seen 2x14 fascia, but maybe I'm not looking hard enough :)."
A. You can use metal flashing (coil stock), which comes in a variety of colors. Or you can get creative (see image below).
.
A few additional questions (part 3)
Thanks, Martin. I'll go back and read again for those details I missed.
Regarding the metal roof, yes, manufacturer allows installation on 1:12. Thanks for checking.
Regarding the fascia, for your coil stock idea, would that be a single large piece that covers both fascia boards, which would be stacked one on top of the other? Currently, the rafters extend a few feet past the wall; the fascia basically cover the tails. Added drawings to illustrate current and potential solutions.
A few additional questions (part 4)
One more question:
Reading your article "How to Build an Insulated Cathedral Ceiling", I want to clarify that my understanding is correct. I believe the article is saying that the assembly should not have a vapor barrier; however, there should be a form of air barrier, but not necessarily in the assembly itself (e.g., gypsum board with tape).
I'm pretty sure the builders committed the "biggest air-barrier blunder" in that my T&G was not attached to taped gypsum drywall. At best, they might have first put up some thin plywood and attached the T&G to that. If I find there is no air barrier, is there any way for me to add an air barrier without pulling down the T&G and adding drywall? I will have access to the top of the T&G when I remove the sheathing, but I'm not sure if there's a legitimate way to add an air barrier between the rafters.
Evan
If you decide to use coil stock as the fascia, it would be a good idea to form it as a drip-edge for the metal roofing. Be really careful how you detail the lower edge of your metal roof panels. At 1/12 the water will want to move back into the roof on the underside of the metal (by friction and capillary action), rather than falling into the gutter or off onto the ground.
You might also think of using one piece of lumber for your fascia. From your drawing it's unclear what the upper-one would be fastened to.
Malcolm
Thanks, Malcolm. Good point about fastening the top fascia; it probably won't fasten very well to polyiso! For a single piece fascia, will it hold well enough if only the lower half of the board is attached (to the rafters)?
Also, thanks for your advice on the drip edge.
Evan
Sure. The top is nailed to the plywood roof sheathing too isn't it?
Response to Evan Lewis
Evan,
I'm sorry that I didn't see your Comments #102 and #103 when you posted them.
Q. "Regarding the fascia, for your coil stock idea, would that be a single large piece that covers both fascia boards, which would be stacked one on top of the other?"
A. Yes, a single piece of coil stock, with appropriate drip-edge details as mentioned by Malcolm. And you need a single fascia -- 3/4-inch plywood will work if you can't find solid lumber.
Q. "Reading your article "How to Build an Insulated Cathedral Ceiling", I want to clarify that my understanding is correct. I believe the article is saying that the assembly should not have a vapor barrier; however, there should be a form of air barrier, but not necessarily in the assembly itself (e.g., gypsum board with tape). I'm pretty sure the builders committed the 'biggest air-barrier blunder' in that my T&G was not attached to taped gypsum drywall. At best, they might have first put up some thin plywood and attached the T&G to that. If I find there is no air barrier, is there any way for me to add an air barrier without pulling down the T&G and adding drywall? I will have access to the top of the T&G when I remove the sheathing."
A. Correct: No need for an interior vapor barrier, but you will need an interior air barrier. Working from above, you can install 1 inch of closed-cell spray foam on the top side of the T&G boards as an air barrier. If the gaps between boards are large, or there are knot-holes, you'll need to put down rectangles of cardboard or some type of membrane first, to avoid spray foam bulges squeezing between the cracks.
That said, it may be easier to establish the air barrier at the sheathing level -- either by taping the plywood or OSB seams (if you have that type of sheathing), or by installing a peel-and-stick material like Grace Ice & Water Shield above the sheathing as an air barrier.
Response to Malcolm
Malcolm, I wasn't aware that the fascia connected to the sheathing. I'll check with my contractor.
Response to Martin Holladay
Very helpful. To summarize, my plan is to install the following layers (top to bottom):
(1) Standing seam metal roof
(2) Ice and water shield
(3) Plywood sheathing (not sure if tape required for this sheathing layer)
(4) Polyiso (6")
(5) Asphalt felt (moisture barrier)
(6) Plywood sheathing + tape (air barrier)
Underneath the plywood sheathing, the assembly will be fully sealed to create an unvented assembly (with either no insulation or the existing rockwool simply resting on the ceiling). Currently not planning on including 2x4 above the polyiso due to my being in climate zone 4C.
Please let me know if there's anything wrong with my plan above, and thanks for all your help.
Response to Evan Lewis
Evan,
Your plan sounds fine to me. I don't think that the asphalt felt layer is necessary, unless it is intended to protect the lower level of plywood during construction (in case of rain).
Thanks again, Martin (no message)
N/A
Insulation Question
Hi Martin,
Construction is underway! I've attached pictures of my rafter bays (2x6), which will be filled completely with mineral wool batts, and then of course I'll a layer of sheathing and then 6" of polyiso on top of that.
My question for you relates to the vertical foam board, shown in the picture to be between the rafter ways. Using the pictures I attached as reference, if I don't include any polyiso, will I get condensation on the pressure blocks and gable-end trusses?
If so, should I put the polyiso against the pressure blocks and gable-end trusses on the interior or exterior?
Please try not to cringe when you see the T&G nailed directly to truss without an air barrier!
Regards,
Evan
Response to Evan Lewis
Evan,
My understanding is that this is an existing house with a board ceiling, and that the original builder forgot to install an air barrier above the ceiling boards. Is that correct?
If so, the most important task for you to work on is air sealing the perimeter of these 2x6 rafter bays. The polyiso you propose isn't important. What you need to do is stop air leaks -- with lots of caulk or canned spray foam.
Response to Martin
Martin,
Correct. This is 1962 construction with T&G nailed directly to trusses and no air barrier. As I turn this into an unvented assembly, I plan to use lots of caulk and spray foam to make it airtight around the perimeter. My air barrier will be achieved with ice and water shield above the first layer of sheathing. I also have 3M flashing tape available. Not sure if the tape or the I/W shield is preferred, or if it doesn't really matter.
Thanks again for your guidance.
Question for Martin
Martin,
Above you stated that polyiso on the exterior of the 2x6 blocks is not important. For my learning, could you help me understand why this polyiso is not important. More specifically, if I were to exclude the polyiso above the sheathing, I would get condensation on the sheathing due to the sheathing surface reaching the dew point. What is preventing the same thing from happening to the sides of the 2x6 blocks if I don't include some foam insulation vertically on the outside of the 2x6 blocks? Is there something about the blocks being vertical that makes condensation less of an issue than it would be for sheathing?
Response to Evan Lewis
Evan,
You guessed correctly: the rules for vertical surfaces (let's call them "walls") are different than the rules for sloped or horizontal surfaces (let's call them "roofs").
Roof sheathing is at much greater risk of moisture accumulation, due to two factors that don't apply as strongly to walls as to roofs: 1. The stack effect (which carries moist interior air upward) and night sky radiation (which cools roof sheathing below the outdoor air temperature in some weather conditions).
All of that said, it's perfectly OK to install polyiso against the blocking if you want to. I'd probably do it myself, even though it isn't strictly necessary (as long as you do a good job of air sealing).
Response to Martin
Martin,
Exactly what I needed to know. Thanks again!
Regards,
Evan
Quick project update and a question...
The installation is complete, including IW shield and fascia. Next step is to put down the standing seam metal roof. Overall, I'm extremely pleased with the insulating performance of the assembly. One issue I'm facing is that when installing a section of the fascia, the contractor got the angle cut slightly off. This caused a gap to open up between the top CDX and the fascia, eventually reaching a size of 1.25". The contractor was able to subsequently close the gap over another sloped run. Luckily, the creation and removal of the gap both happened on slopes of the gable side, and so visually, you can't really notice. On the other hand, once I put soffits up, I think it will be more noticable from underneath, but in reality, I'm probably one of the few people in the world that will notice. I'm not sure there will be any performance issues since the gap will be covered by a metal drip edge. Regardless, I'm going to always know it's there (and it will bug me), and since I paid a lot for this contractor to do the work, I've asked them to pull off the fascia (~25') and reattach it. I'm getting significant push back from the contractor: they are saying it's not an issue, and that I should just fill with spray foam spray foam. This isn't an easy fix because it's massive massive 2'x14' cedar fascia, already attached with SS ring shank nails (risk of damaging the boards if we pull them). But, this was clearly a miss on their end that the should have caught as they were installing them and fixed immediately.
Am I being too finicky and making this into a bigger issue than it is?
(photos attached)
Evan,
If this crack will be covered by your dripedge flashing, you are being too fussy.
I'm not sure of your construction details. Are the fascia and the roof sheathing both part of your air barrier? (That would be unusual.) If the fascia and the roof sheathing are both part of your air barrier, then the use of canned spray foam to seal this gap sounds OK to me (although not ideal -- not as good as planning a different detail for your air barrier).
Martin,
Neither the fascia nor the top layer of roof sheathing are part of the air barrier. The air barrier is the lower layer of IW shield that is on the lower layer of CDX, directly underneath the polyiso.
Sounds like I am being way too fussy. I'll simply fill with Great Stuff Pro Gaps & Cracks foam. I don't need the foam for air barrier reasons; the void just bothers me. Please let me know if I you have any further advice, and thanks again for your prompt reply and helpful advice.
I'm looking to do a re-roof on my home and want to improve the insulation at the same time. Based on this article, I am leaning towards option 1. Here are the details:
-Home located in climate zone 3, southern California.
-Saltbox style roof, but the front is 1 story, rear is 2 story
-Mostly vaulted ceilings with no attic, two small sections have attic space (details below)
-Soffit vents to ridge vent. There is a 4'x8' skylight in one section of a vaulted ceiling
-2x6 rafters spaced @ 24"
-Very poor insulation (3" batting labeled as R11 from Rockwool. Most appears detached from sheathing)
-1x6 solid board sheathing with small (1/4") gaps - appears to be in good condition
-Front roof pitch is 7:12
-Back roof pitch is 3:12 or 4:12
Current roof layering (inside-out):
-1/2" drywall
-Ancient 3" Rockwool R-11 batting in a 2x6" rafter cavity, mostly detached
-1x6" solid board sheathing
-Underlayment
-2 or 3 layers of fiberglass composite shingles
Attics:
One section of roofing has an attic underneath. This attic space does has soffit venting but doesn't appear to connect to the ridge vent, nor does it have a gable vent.
Another small section of roofing has a tiny attic underneath. This attic space is not accessible, but has a gable vent and a whirly bird.
What I plan to do:
-Remove all shingles and underlayment
-Remove whirly bird and seal gable vent over small attic space
-Repair any damaged 1x6" sheathing, but largely keep as-is
-Leave existing rafter insulation alone
-New airtight membrane
-7" polyiso rigid foam with staggered and taped seams
-OSB or plywood sheathing (no ventilation gap)
-Underlayment & new composite shingles
I would treat the roofing over the small attic areas the same as the rest of the house. Basically following what is in this video:
https://www.youtube.com/watch?v=rn0c4WDOlMQ
Questions:
-Does the above plan seem reasonable given the information?
-How does the foam connect at the ridge? I assume there is no ridge vent in this configuration
-Do I need to close off the existing soffit vents in the rafters? If so, what is the recommended way to do this?
-Are 8+" screws sufficient to hold this much foam and roof sheathing in place, particularly on a such a high pitch roof?
-What material goes at the side edges of the roof to contain the foam?
-The exterior of my home is stucco, can soffit boxes be built without having to go through stucco?
Travis,
I recently discovered your comment here, and felt a little guilty for not answering -- and than I remembered that you posted it again on our Q&A page ("Vaulted ceiling insulation advice?").
So it looks like you got the advice you needed.
I have a home (zone 4 marine) with "vented" cathedral ceilings, I believe there are R-28 fiberglass bats in-between 2x12 rafters. There is a soffit vent and a ridge vent on two sections of the roof with lower slope 6/12. There is no soffit vent on the 12/12 portion of our roof as only the gable ends have soffits, there is a ridge vent. We are having a standing seam metal roof installed. I am planning on installing 2" of xps ridge foam or Gutex Multitherm 60 (R-8.7) on the exterior of the sheathing, then a vapor perm WRB, then furring strips at 45 degrees to attach the metal roof to and allow for drainage of any condensation. The interior of the ceiling is sheetrock, then an air gap, then 2x T&G. There is no air barrier in the stack other then the sheetrock and plywood or OSB sheathing. My question is, since the roof is "vented" although poorly, and the bats are likely not in direct contact with the sheathing, will I have any issues with the exterior foam and condensation on the interior of the sheathing? Also should I seal the soffit vents or ridge vents? We would really like to upgrade the R-value of the roof, but want it to last a long time. We have a limited budget. Any advice is appreciated.
Josh,
If you plan to install rigid foam on the exterior side of your roof sheathing, you certainly don't want a channel of ventilation air underneath your roof sheathing. (Inviting exterior air into the center of your roof assembly, between two layers of insulation, has the effect of making your rigid foam worthless.)
If you go this route, you'll have to spend a lot of time conscientiously sealing up the air intake openings and air outlets for each ventilation channel -- whether at the soffit vents or at the ridge vent. You need an airtight assembly -- and if this roof assembly used to be vented, that can be tricky.
Hello Martin,
My roofers put plywood, peel and stick, 2" iso board with some kind of brown paper or cardboard face with no tape and then a standing seam roof on top of that. They did 2 sections and I'm already seeing really bad oil canning.
We are paying them 50,000 dollars for a 2,100 sq ft home in South Florida bordering zone 1 and 2 does this seem right to you?
David
David,
Your question is unclear, but I'll respond to three issues.
1. As my article explains, it's better to tape the seams of rigid foam than to leave the seams untaped.
2. I can't comment on costs, which vary regionally and depend, in part, on issues that can only be determined by a site visit.
3. For more information on oil canning in metal roofing, see this article: "Oil Canning Controls."
We would like to use this method on our 59 year old home as a retrofit. We live near Chicago, Illinois. I have not been able to find any contractor in our area who has used this method before. Please help me get in touch with a contractor from any area who has successfully used this method and would be willing to do the job for us or help us make sure we do the job correctly. Thanks.
Rebekah,
I suggest you read this article: "I Can’t Find a Contractor to Do That."
Hello Martin,
We have a mostly seasonal NH cabin (use wood stove occasionally in cold season... for an occasional winter break to the cabin) that we are going apply 4 inches of rigid foam on top of the otherwise uninsulated cathedral roof. The roof is ten years old asphalt shingles. Can we save time and apply the rigid foam on top of the shingles?
Also, I recently (before reading all the issues with polyethylene) insulated the 2x4 cabin walls with fiberglass insulation, applied plastic to the warm side, and then ship lapped the interior. We use the lake cabin mostly in the summer (much less in October thru April). Because we use limited ac and heat, I am hoping polyethylene issues won't present. My second question relates to when I apply cedar shakes to the existing painted exterior ship lap siding. I don't want to limit breathing but feel I should use a housewrap. How does Ben Obdyke hydro gap sound (seems expensive ....) for my application?
Many thanks for the reply. Bill
Bill,
Q. "The roof is ten years old asphalt shingles. Can we save time and apply the rigid foam on top of the shingles?"
A. You can, but I wouldn't. Stripping shingles is fast -- use a flat-bottomed spade. Clean up all the nails. Then you can (a) inspect the sheathing, making repairs if necessary, and (b) use air sealing tape at the seams, or install a proper air barrier (a peel-and-stick product or a European air sealing membrane).
Q. "I applied plastic to the warm side, and then shiplapped the interior. We use the lake cabin mostly in the summer (much less in October thru April). Because we use limited AC and heat, I am hoping polyethylene issues won't present."
A. Everything should be OK, but polyethylene makes a lousy air barrier -- easy to rip, and too many holes -- and your shiplap boards leak air like a sieve. Your method won't get you into trouble, but it isn't airtight, so other GBA readers shouldn't imitate your approach (especially if they care about energy costs).
Q. "When I apply cedar shakes to the existing painted exterior shiplap siding. I don't want to limit breathing, but feel I should use a housewrap. How does Benjamin Obdyke HydroGap sound (seems expensive ....) for my application?"
A. A water-resistive barrier (WRB) -- usually housewrap -- is a code requirement and recommended by everybody. It is not optional. Benjamin Obdyke HydroGap is a good choice under cedar shingles.
We live in Zone 5 (suburb of Chicago) and are (hopefully) about to put rigid foam above the roof sheathing on just the "Northeast Roof" portion of our roof: 4" of polyiso under 4" of EPS, all above the original roof sheathing; then a second layer of plywood sheathing and asphalt shingles, following the steps explained in this article. (Roof pitch is 4 everywhere.) We do get ice damming as shown in diagram. (Our attic is not sufficiently insulated at this time.)
1. Is it impossible to vent the west part of the Northeast Roof because of the way the Addition Roof ties in to it? (Would two layers of strapping, as you mention in comment #82 with maybe some mushroom vents and a ridge vent, possible work?)
2. If we just skip the ventilation gap and install the second layer of plywood roof sheathing directly to the top surface of the EPS rigid foam, are we risking getting a lot of ice damming? Are there some other drawbacks we should be aware of? We don't think white asphalt shingles would look right, and so if we don't ventilate we will probably lose our shingles warranty.
3. If we skip the ventilation gap, would this be called a "hot roof"?
I don't want to call off the project, but we may have to if the risks associated with not having a ventilation gap are too great. I am very grateful to be able to ask you for advice.
Rebekah
Rebekah,
Q. "Is it impossible to vent the west part of the Northeast Roof because of the way the Addition Roof ties in to it?"
A. It looks impossible to me, since the bottoms of the rafter bays all begin in valleys.
Q. "If we just skip the ventilation gap and install the second layer of plywood roof sheathing directly to the top surface of the EPS rigid foam, are we risking getting a lot of ice damming?"
A. No. If your rigid foam is thick enough (and yours will be), the thick foam will reduce the chance of ice damming by 90% or 95%, even without any ventilation channel above the foam.
Q. "If we skip the ventilation gap, would this be called a 'hot roof'?"
A. Some people use that term, but I don't like the term "hot roof." The technically accurate way to refer to it is as an "unvented roof assembly." Properly designed, you'll end up with a cold roof -- whether vented or unvented.
Are there any articles on techniques that explain how to guide a long screw into 2 inch wide rafter through thick foam? or does anybody have techniques that they have used? It seems like it would be really difficult to do. I feel like I would miss it each time.
Erik,
Yes, there is such an article. Here is the link: "A Timber-Frame House for a Cold Climate — Part 3."
In the article, author Rob Myers explains how he created a jig to help make sure that his screw holes were established at a 90 degree angle to the roof plane.
The simple answer to your question (in my opinion) is that 50% of all human beings are born with the ability to understand "plumb" and "90 degrees," while the other 50% of human beings just don't seem to have an intuitive grasp of "plumb" or "90 degrees."
If you are struggling with this issue, I'll give you the same answer as the traditional response to the question, "How do I get to Carnegie Hall?" -- namely, "Practice, practice, practice."
If you can cut a fresh loaf of bread into consistent slices, you might be one of those lucky people born with an intuitive understanding of "plumb" and "90 degrees."
Thank you for helping me several times before this with our proposed project of converting our north attic into storage space. (We are near Chicago, Zone 5, 2x6 rafters 16" on center. A diagram is attached. It is ONLY THE "NORTH ROOF" that we want to insulate so the space under it can be used for storage. The "Addition Roof" is cathedralized. The "South Roof" is over a conventional, vented attic with insulation on the floor of it.)
My husband and I met with our contractors yesterday and everyone decided not to add 8" of foam above our roof sheathing as I had hoped for because it would be costly AND it would cause such a thick fascia that it might decrease the value of our home, since it wouldn't blend in with the rest of the house.
The roofing foreman proposed two options:
1. He said he could add 3.5 - 4" of polyiso rigid foam above the roof sheathing and that would be sufficient - no need for also putting fluffy insulation between the rafters - I guess maybe our city doesn't require R49 since it is a retrofit - and the fascia, while being thicker, would look fine because it would not be all that noticeably different from the rest of the house. This would be the more costly of the two options.
2. He could put zero rigid foam above the roof sheathing and just put fiberglass between the 2x6 rafters. He recommended this option because it costs less. I said, "Wouldn't we would have to furr down the rafters to reach a high enough R value, and so wouldn't this option cause us to lose headroom?" He said no, we wouldn't lose any headroom.
My goals are storage in our attic, preferably without losing any headroom; a tight building envelope with sufficient insulation; and the prevention of ice dams. Ever since our addition ~8 years ago, we have been getting ice dams every year at the location shown in the attached diagram. Our house is always cold in winter, hot in summer, and has drafts and frequently fluctuating temperatures.
My husband would like to choose option 2 w/ no rigid foam above sheathing, just fiberglass between rafters, because it would cost less. I am concerned that this would be a big mistake.
***Could you give me and my husband a rundown of the pros and cons of options 1 & 2?
***I would like to put 4" of rigid foam above the roof sheathing for now, and then later when money and time allow add fluffy insulation between the rafters as described in this article, to reach R49. (I could add the fluffy stuff myself, doing a little at a time.) If I can convince my husband and the contractors to go this route, would 2" of polyiso topped with 2" of EPS be our best option? We would use reclaimed foam. How critical is it that the EPS be Type II? (The man selling me the reclaimed EPS says its density measures about 1.4 lbs/cu ft which puts it nearest Type II EPS.)
***The roofing foreman said that he would vent the roof. (I couldn't understand his words exactly, but I think he would use the 2x4's on the flat as described in this article - I plan to check on that.) You at GBA had told me before that it looks like it might be impossible where the "Northeast Roof" attaches to the "Addition Roof". He felt confident that he could have one of his little guys get in there, and they could install vents. The roofing foreman did not seem interested at all in installing a "hot roof". He definitely wants to vent the roof, and I like the idea of venting the roof if it's possible. Should I be concerned that you thought it was likely impossible but he thinks it's possible?
***What is the best & least expensive way to seal around the perimeter of the attic? My contractor says to stuff fiberglass insulation batts around the edges - would this be fine?
***Our neighbors had carpenter ants, and we might have them. Does this make it really risky to install the rigid foam above the sheathing? ( I read the GBA's Q&A Spotlight "If Ants Like Rigid Foam, Should We Stop Using It?")
Thank you for helping us. This method is extremely unusual in our area, and so advice is hard to find.
Rebekah,
Q. "My husband would like to choose option 2 (with no rigid foam above sheathing, just fiberglass between rafters), because it would cost less. I am concerned that this would be a big mistake. Could you give me and my husband a rundown of the pros and cons of options 1 & 2?"
A. The option with rigid foam is clearly better. Going with fiberglass insulation only is risky unless your air intake openings and ridge vent openings are robust in every single rafter bay.
Q. "Would 2 inches of polyiso topped with 2 inches of EPS be our best option?"
A. That option is fine, but any combination of polyiso and/or EPS would work.
Q. "We would use reclaimed foam. How critical is it that the EPS be Type II?"
A. Not critical.
Q. "The builder felt confident that he could have one of his little guys get in there, and they could install vents."
A. I don't understand this plan. In the absence more more information, I'm skeptical.
Q. "What is the best & least expensive way to seal around the perimeter of the attic? My contractor says to stuff fiberglass insulation batts around the edges - would this be fine?"
A. No. Fiberglasss batts are not an air barrier. To seal air leaks, you need caulk, tape, or sheets of rigid foam with air-sealed edges, depending on the side of the opening -- or you can use canned spray foam (or two-component spray foam).
Q. "Our neighbors had carpenter ants, and we might have them. Does this make it really risky to install the rigid foam above the sheathing?"
A. In my mind, no -- as long as everything is detailed well. Most experts say that carpenter ants follow the moisture -- so that if everything stays dry, your roof assembly should be ant-free.
One more question - If I can't find 2" EPS, (and/or if doing two layers would cost a lot more in labor), would a single layer of 4" polyiso be just as fine?
Rebekah,
Four inches of polyiso will work. Just assume that the polyiso will perform at about R-5 per inch.
I took some time to carefully study through many articles on GBA and your answers to other questions of mine over the years and have found answers to most of my own questions. I'm hoping our roofer is willing to install at least 2" of EPS over at least 2" of polyiso on top of the roof sheathing before the new shingles go on. If you get a chance, any advice on the best & least expensive ways to seal around the perimeter of the attic would be very helpful.
Rebekah,
See my comment above (Comment #135). For more information, see "Air Sealing an Attic."
Hoping for help - fear I'm stuck. In Zone 6 in Toronto, years ago had my cathedral ceiling closed-cell spray-foamed and made a hot roof, hoping it would be enough to make it comfortable but didn't fur inward as there's no space to do so. R-27 later and it's not enough for comfort. I was thinking of adding rigid exterior but your guidance says no, not if you have closed-cell. If I stack rigid on the exterior when I go to re-shingle, I'll get condensation. I can't picture and could not find any guidance of an assembly that works (R-49+) and is safe in the long-run if you have closed-cell foam existing. Of note: 12/12 roof. Any ideas that work here from the experts? Appreciate it!
Ideally I would have this assembly (from inside to out):
1. Drywall (done)
2. In-rafter Closed-cell spray-foam (~R-27. Done)
3. Original roof deck (Done)
4. Ice and Water shield
5. 6" EPS
6. 2x4's on flat for vent channel
7. 3/4" ply
8. Ice and water shield
9. Asphalt shingles
Kurt,
If you are planning from the start to install rigid foam above your roof sheathing, it makes sense to leave vapor-permeable layers on the interior (to allow any moisture that may get into your roof assembly to dry inward).
But your situation is different -- you've already chosen to install closed-cell spray foam against the underside of your roof sheathing.
You wrote, "If I stack rigid [foam] on the exterior when I go to re-shingle, I'll get condensation." Says who? Not me. Where is the cold surface where condensation will accumulate? What are you worried about?
If you now have asphalt shingle roofing, it's not as if your roof sheathing can dry to the exterior in any case. It can't. So adding rigid foam won't make the existing situation worse -- it will make it better, by warming up the roof sheathing.
Thank-you, Martin! Glad I clarified my incorrect interpretation. This guidance below on what is recommended or not, is what threw me off. Appreciate the clarity and will proceed then. Thanks again.
"If you follow Option 2, a wide variety of insulation materials can be installed under the roof sheathing. Among the possibilities: fiberglass batts, mineral wool, cellulose, or open-cell spray foam. (Closed-cell spray foam is not recommended for this purpose, since closed-cell spray foam prevents the roof sheathing from drying toward the interior if it ever gets damp. "
Kurt,
As I said in Comment #139, I stand by the advice given in the article. If you are creating a roof assembly with exterior rigid foam on a new house, it's better to use open-cell spray foam, not closed-cell spray foam, between the rafters.
Your case is different, because you have already installed the closed-cell spray foam. I'm not sure why you concluded that this type of insulation will lead to condensation; I certainly never wrote that. In any case, it sounds like your incorrect interpretation has been clarified.
My wife and I bought our first house last year in July. It is located in NH climate zone 6. At that time we did not know much about houses. Our house has maybe 60% cathedral ceilings and 40% where there is an attic you can go up into that is over a couple bedrooms and a bathroom. The house was built by somebody who built it themselves (aka not a typical contractor) and never lived in it. Within our price range we figured we would go with this house as it was not as dated as some of the other houses that were in our price range. We thought this would be better but we were wrong... Over the winter we had really high heating bills and by the time February came we had severe ice dams. These ice dams caused significant water damage requiring the removal of drywall and wet insulation in the ceilings and exterior walls. What we learned is the builder put blocking at the eaves between the rafter bays completely blocking any soffit to ridge ventilation. We also found that there is R30 fiberglass insulation in the rafter bays of the cathedral ceiling.
After spending a lot of time on GBA I believe the best approach is to put exterior foam on the roof sheathing as we are looking to replace the shingles this summer due to the damage that was caused to the shingles to remove the ice dams and the fact that the builder never applied any ice/water guard.
My tentative plans are this:
1) strip the shingles off to the roof sheathing
2) Apply rubber membrane over sheathing- This is to act as an air barrier
3) Add r31 of foam to roof to create the correct inside to outside ratio of insulation as currently there are faced r30 fiberglass batts on the interior of the rafter bays.
4) strap with 2x4s and then I was considering cross strapping with 1x4s to help create better cross ventilation as on the back of the roof there are skylights and then the front has two valleys (see attached pic)
5) Then I would put sheathing on top of that and have the typical roof placed over that.
The only things that I am not exactly sure about in the details are:
1) How does a wood stove pipe going through the roof function in this kind of set up?
2) How do skylights work in this set up? (Yes we would like to keep them, My wife works at home and loves them)
3) I know that the fiberglass under the sheathing does not contact the sheathing on the underside, is that going to cause problems?
The contractors in our area that I have talked to seam to think the exterior rigid foam idea is ridiculous. Most think it is better to just rip down all the drywall in the ceilings and spray closed cell spray foam to reach an r value of r49 which is code in this area. So finding a willing contractor has also been a barrier.
Erik,
Q. "How does a wood stove pipe going through the roof function in this kind of set up?"
A. Hopefully, what you have going through is roof is not a stove pipe. If it is, that would be very dangerous. Probably, what you have is a metal chimney -- which is quite different from a stovepipe. At the roof penetration, you need to install a penetration kit from the metal chimney manufacturer, and you need to follow the manufacturer's installation instructions to ensure a safe installation.
Q. "How do skylights work in this set up?"
A. Each skylight needs proper flashing at the roof penetration; different skylight manufacturers make different flashing kits. You can either remove each skylight and reinstall it in a new (carefully flashed) curb, or you can buy new skylights. In either case, each skylight needs a carefully constructed well. The well needs to be air sealed and carefully insulated.
Q. "I know that the fiberglass under the sheathing does not contact the sheathing on the underside. Is that going to cause problems?"
A. That's not ideal (and is one reason you've had all those ice dams). But once you install the new rigid foam, everything will be so much better that you shouldn't worry about the air gap. Just pay attention to air sealing at the ceiling plane.
Thanks for the reply Martin, and yes it is a metal chimney I didn't realize there was different terminology.
Martin, I am trying to figure out how to best insulate a small unvented roof above a bay window. Can mineral wool be substituted for rigid foam to insulate the exterior of a roof?
Zone 5 project: replace rotting roof deck and shingles, add insulation above and below the roof deck to a non-vented roof above a bay window.
Propose to do the following:
1. Add rockwool R29 (or 59% of total) insulation above drywall ceiling, in between rafters
2. Cover with 5/8 in plywood or OSB, tape seams; use FastenMaster's HeadLok screws to fasten sheathing to rafters
3. Cover deck with ice and water shield
4. Cross layer deck with 2 layers of rockwool = R20 or 41% of total insulation
5. Cover with 5/8 in plywood or OSB, tape seams; fasten to rafters
6. Cover deck with ice and water shield
7. Install drip edge around roof perimeter with 5 or 6 inch roof leg
8. Finish with asphalt shingles and flashing along brick veneer wall
Any thoughts/recommendations would be appreciated.
Randy,
You have the correct minimum R-value targets for your ratio. Here's the thing: installing mineral wool on the exterior side of roof sheathing is technically possible but rarely done. The hardest part of your plan will be finding semi-rigid panels of mineral wool that are dense enough to work. You can't just use batts. The type of dense mineral wool you need is hard to buy in small quantities.
For more information on the different densities of mineral wool -- especially semi-rigid mineral wool panels -- see "Installing Mineral Wool Insulation Over Exterior Wall Sheathing."
You'll find that it's much easier to buy rigid foam in small quantities than to buy dense semi-rigid panels of mineral wool in small quantities. I suggest that you install rigid foam with a minimum R-value of R-20 in this location, and use any handy type of fluffy insulation (fiberglass or mineral wool) between the rafters.
Martin, I have a cathedral ceiling roof on a home build in 1978 and located on the Olympic Peninsula in Washington state that started with a cedar shake roof which was replaced with composite shingles. In this remodel, we want to replace the shingles with a standing seam steel roof.
The existing roof structure below the composite shingles is the following:
7/16" OSB
1x4 skip sheeting (from its cedar shingle life phase)
2" closed cell foam (R-10)
T&G car decking (bottom of which is exposed to the house interior)
Since we want to also beef up the roof R-value, we have installed 2x4 purlins onto the bottom of the existing exposed house beams upon which 1/2" sheetrock will be attached. In the "new cavity" between the sheetrock and the car decking, between the 4x8 exposed beams, denim insulation will be installed. The depth of that insulation space is be 7-1/4". With that addition of insulation between the sheetrock and the car decking, we want to be certain any moisture that seeps between the sheetrock and the steel roof has an opportunity to dry or escape while minimizing moisture getting to the car decking from the exterior.
The plan calls for a breathable peel-and-stick membrane such as VaproShield Slopeshield Plus (https://vaproshield.com/products/roof/slopeshield-plus-self-adhered) and perhaps adding vertical strips like VaproShim SA self-adhered furring strips to create air ventilation channels between the VaproShield membrane and the steel roofing sheets.
Our questions are:
1. Is the presence of the 1x4 skip sheeting a fatal issue in the design of an unvented roof given the inherent air space it creates?
2. Can the VaproShims above the membrane create sufficient air ventilation/movement to keep the roof sufficiently dry with venting access from the roof edge to peak? That product comes in only 1/4" and 1/8" thicknesses, so those options seem insufficiently thick to allow for enough air movement. You suggested flat 2x4s in your article. Could that option work in this situation even with the skip sheeting remaining?
3. Given the existing structural layers, can you suggest a plan to achieve the desired result of an unvented roof....or even a vented roof design that wouldn't require major roof changes? We realize the steel roof option comes with moisture/condensation issues that need addressing... and that getting this design right is essential.
Thanks. Tom
Tom,
If you are going to install new roofing, you have an opportunity to do all the work on the exterior -- thereby avoiding the disruption incurred by your plan to install denim insulation on the interior, and with the added bonus of getting a better result.
If you take my advice, you'll strip the existing asphalt shingles, OSB, and skip sheathing. Then you can install an additional layer of rigid foam above the existing rigid foam. The new rigid foam can be installed with staggered seams, and attention to airtightness. Above this new rigid foam, you would then install a layer of OSB and new roofing. Vent channels between the new OSB and the steel roofing are optional but possible.
There really shouldn't be any moisture to vent if you do a good job of air sealing. Your plan to include a peel-and-stick membrane should be adequate as an air barrier.
Does anyone have any ideas/suggestions for safety harness anchors for a roof with exterior rigid foam?
I will likely not be doing the installation of the standing seam metal roof, but will likely be on the roof eventually for maintenance, new vents, and possible solar panels. Any ideas/products that could be left as permanent anchor points?
Steve,
I don't know what product would be best, but I suggest you call up a company like Simplified Safety (telephone: 866-527-2275) to ask about available products.
We live near Chicago, climate zone 5. Last month, a roofing crew installed rigid foam (2 layers of 2.25" thick polyiso sheets, staggered) above the roof sheathing of one attic of our 60 year old split level home. It was a traditional, vented attic, and we wanted to bring it inside the building envelope by constructing an unvented roof assembly. No one in my area had ever installed rigid foam above the roof sheathing on a sloped residential roof, but after many months of searching I found a contractor and an architect willing to try something new. I directed them to this article, and the architect firm measured our home and drew up plans following the steps described in this article. The planning and installation were frantically rushed because of an insurance deadline and frequent precipitation including a heavy snowfall in April.
The general contractor and I did not realize it until after they were done, but significant errors occurred due to being so rushed. They got some things right - they did tape the seams of the original roof sheathing, and then used synthetic underlayment. They did space the screws correctly, as the architect instructed. But I don't think they filled the gaps between the sheets with minimal expanding spray foam. And, a couple days ago, I discovered a vent that they installed near the ridge, cutting through both layers of foam and OSB. I plan to attach a picture of this vent plus some other obvious voids in what should be an airtight building envelope. The picture with a long screw and drooping underlayment showing is the hole where a power fan used to be. The crew did not follow the instructions in the architect drawings.
Am I right to think that the crew will have to remove everything down to the original roof sheathing and start again, in order to achieve an unvented roof assembly that will meet code and protect our home from rot? If so, do they need to change all of this before winter?
My general contractor came by today to check on these errors. He is confident that they will be able to correct these mistakes from the inside of the attic, using leftover sheets of polyiso, canned spray foam, and leftover shingles. Do you agree that correcting these mistakes from the inside could be sufficient? Any advice you can give us is greatly appreciated.
Thanks,
Rebekah
Rebekah,
Q. "Am I right to think that the crew will have to remove everything down to the original roof sheathing and start again, in order to achieve an unvented roof assembly that will meet code and protect our home from rot?"
A. There is no way to answer your question without a site visit -- or, at a minimum, more information. For example: you haven't even told us what type of roofing was installed.
Here's what I know: This type of insulation job needs to be installed in an airtight manner, and it appears that your contractor didn't know this basic fact, or chose to ignore it. Some of the defects shown in your photos can be remedied from below, without removing anything. But the extent of the defects is impossible to judge from the information you have provided.
Whether or not you have any remedies available (for example, by raising these issues with the contractor) depends entirely on the construction documents, if any, that were prepared and signed before the job began.
Martin,
Thanks so much for your reply. They installed 35 year architectural asphalt shingles. I plan to keep trying to find someone who is as knowledgeable as you all are at Green Building Advisor, and who can visit our site.
I greatly appreciate this website and the good advice you and others have given me over the years concerning this project.
Thanks again,
Rebekah
Thanks again for a great article Martin.
Do you know if it would be possible to use low density EPS on top of the roof sheathing?
I suppose the critical thing here is the EPS being able to support either the plywood, OSB or 2x4’s that lie over it.
I would bet that with plywood or OSB you would not have any problem using any low density EPS, because the force exerted by the roofing weight is spread through all of the plywood/OSB board’s area, but if you use 2x4’s to hold the rigid foam and nail, for example, a metal roofing over it, I’m not sure that a low density EPS will hold withouth being squeezed by the 2x4’s holding the weight of the roof
I think the lowest density you guys get in the US is Type I, which is 1 pcf. But here in Chile the cheapest and most commonly used EPS is 0.62 pcf.
Do you think a 0.62 pcf EPS would be ok using 2x4”s on a light metal roof? Would you recommend a higher density EPS?
Thanks
Jose
I’ve really been wanting to do this for my roof but every time I talk to a contractor about this and show them the article along with the article “over-roofing—don’t do stupid things” by Joseph Lstiburek they think I’m insane... if there are any contractors in New England area especially near North Conway, NH that do this ide love to hear from you! Has anyone else had my same issue of finding somebody capable of doing this?
I had a pretty tough time. The same issue you are having. All the roofing companies only wanted to put on a roof, nothing more.I live in southeastern Virginia. It has taken almost a year from starting the process to finding a contractor that will do it. In the end I hired a consultant that found a contractor, and insulator, and a commercial roofing company to do the job. The contractor is actually coming in from about 2 hours away. Only one roofing contractor would even bid on the project. As it stands the project should be started in about 2 months, just waiting on availability of the contractor. I would suggest googling “rigid foam roof contractor” and then reaching out to companies that advertise commercial rigid foam roofs.
Hi Erik,
If you are calling roofing contractors, you may not get anywhere. Try to find a contractor or builder who specializes in building high performance homes or energy retrofits. They'll likely either have subs that can do the work or they'll know how to do it themselves.
Erik,
Reach out to Bob Irving (RH Irving home builders) or Starr Construction in Bethlehem.
“[Deleted]”
Thanks for the helpful article, Martin! I'm updating the never-occupied second story of my 1880s balloon frame house, which was never insulated. The rafters are exposed and 5-3/4" deep. It's a cathedral ceiling and I'm hoping not to drop the ceiling lower than I have to, which makes above-deck rigid foam insulation attractive. I'm in Zone 5. I have a few questions:
1. Is use of above-sheathing rigid foam well suited to houses with many valleys and dormers. I've attached a PDF showing the roof line in blue. As you can see, there are several dormers and valleys.
2. Original wood planks comprise my roof sheathing (see attached image), with a small patch of OSB from a repair where a chimney used to be (not visible in image). I believe I will need to make an air barrier. Any recommendations on how to do that?
3. If all of our insulation is above-sheathing rigid foam (i.e., no insulation below the deck), does that mean we would make our roof un-vented?
> To achieve the R-49 required in our jurisdiction we're considering (i) 12-1/2" of EPS or (ii) 2" EPS + 5-1/2" polyiso + 2" EPS.
4. Am I correct in recalling that we do not have to vent for batting or cellulose insulation if we do a combination of above- and below-sheathing insulation?
> For example we achieve R-29 with rigid foam above-sheath by either (a.i) 7.5" of EPS or (a.ii) 1" EPS + 3" polyiso + 2" EPS. Then, we achieve R-21 below-sheath with either (b.i) 7-3/4" of open cell spray foam, (b.ii) 5-1/2" of mineral wool, or (b.iii) 5-1/2" of high-density fiberglass batt. Obviously, the spray foam in option b.i would be un-vented, and I assume I would similarly want the mineral wool and fiberglass from b.ii and b.iii right up against the roof sheathing.
5. I've also considered forgoing above-sheath rigid insulation and using a combination of closed-cell and open-cell spray foam. Using all closed-cell spray foam would allow me to maximize R value and minimize the amount I have to drop my ceiling, but spraying closed-cell is too environmentally costly. (Or am I mistaken about this?!) Using all open-cell would be more environmentally friendly, but would open me to moisture problems. If I go the spray foam route, I would like to use the minimum amount of closed-cell needed.
Any suggestions on how I can achieve R-49 without sacrificing too much ceiling space would be much appreciated. Options b.ii and b.iii seem the most promising, but I'm sure there are cleverer solutions. Thanks!
Jacob,
Q. " Is use of above-sheathing rigid foam well suited to houses with many valleys and dormers?"
A. Yes.
Q. "Original wood planks comprise my roof sheathing (see attached image), with a small patch of OSB from a repair where a chimney used to be (not visible in image). I believe I will need to make an air barrier. Any recommendations on how to do that?"
A. Read the article on this page. In the article, I wrote, "You need an air barrier at the bottom of the assembly. Before installing the rigid foam, make sure that the roof sheathing is airtight (or that you install an air barrier immediately above the roof sheathing). ... If your roof has board sheathing, install an airtight membrane (for example, Solitex Mento, a product available from 475 High Performance Building Supply), a layer of synthetic roofing underlayment, or a peel-and-stick membrane."
Q. "If all of our insulation is above-sheathing rigid foam (i.e., no insulation below the deck), does that mean we would make our roof unvented?"
A. Yes.
Q. "Am I correct in recalling that we do not have to vent for batting or cellulose insulation if we do a combination of above- and below-sheathing insulation?"
A. Correct. For more information, see my article, "How to Build an Insulated Cathedral Ceiling." In that article, I wrote, "There are four ways to build an unvented roof assembly ... [One way is to] Install rigid foam insulation above the roof sheathing and air-permeable insulation between the rafters. This type of assembly is designed to dry to the interior, so the assembly should never include an interior polyethylene vapor barrier."
Note also the information in the article on this page: "If you plan to install rigid foam above your roof sheathing, you have two choices. ... [One choice:] You can install some of the insulation above the roof sheathing, and the rest of the insulation underneath the roof sheathing (and in direct contact with the roof sheathing)."
Am I correct in assuming that installing above-deck rigid insulation will necessitate that you either (1) extend your eaves or (2) make your fascia taller? If so, does anyone know of any clever ways to handle the latter option? Extending my eaves is difficult given my house's proximity to the property line. This is perhaps more of an architectural, aesthetic question than one of design and construction efficiency.
Jacob,
Q. "Am I correct in assuming that installing above-deck rigid insulation will necessitate that you either (1) extend your eaves or (2) make your fascia taller?"
A. Yes.
Q. "Does anyone know of any clever ways to handle the latter option?"
A. A tall fascia can be disguised by applying decorative trim (something like cornice moulding) or by applying boards to give the fascia a stepped-back look. Multiple vertical planes will disguise the fascia's height.
If you decide after all that it's possible to extend the eaves, you can use a detail similar to the one shown in the Building Science Corporation drawing reproduced below.
Thanks for your thoughtful replies to my earlier questions, Martin. A few follow-up questions, this time regarding the interior of my unvented cathedral ceiling with above-deck insulation (a combination of EPS and polyiso).
1) Will I need a thermal barrier on the underside of my roof?
> From what I understand, many residential codes allow rigid foam boards like EPS and polyiso to be left exposed, or separated by a non-fire-rated barrier (i.e., a roof deck). See, for example, . I assume that is because EPS and polyiso do not count as "foam plastic insulation" , or have been specifically tested to show that they meet the requirements for 15-minute fire rating. Regardless, I am hoping to avoid installing 1/2" drywall on the underside of my rafters, and probably can't afford a 15/32" hardwood ceiling
2) Supposing I do need a thermal barrier on my ceiling, are there any promising alternatives to 1/2" drywall and 15/32" tongue-and-groove. I've come across a partial list of materials and thicknesses for which I might be able to make a case to my local code enforcement office . Do you know of any other such lists, or any other interesting and affordable materials that might satisfy code?
> I'm specifically interested in the industrial cardboard used, for example, as structural materials by Japanese architects . Or, perhaps more reasonably, some of the new wood paneling options that are cheaper and lighter than tongue-and-groove, and more appealing than their cheap-looking predecessors . I've been unable to find reliable information for fire-ratings of any but a few common building materials.
3) If I decide to add 5-1/2" of high-density fiberglass batt between my rafters, will that affect whether or not I need a thermal barrier on my cathedral ceiling?
I understand that I will need to consult with local code and enforcement officials, but as you frequently point out, the code is not entirely clear on when and where thermal barriers are necessary. Your responses to my questions will, therefore, serve as useful starting points for further investigation and help me in my conversation with local code and enforcement. Thanks!
Jacob,
EPS and polyiso are types of "foam plastic insulation" under the code, and usually require a thermal barrier. But when the EPS or polyiso is installed on the exterior side of your roof sheathing, no additional thermal barrier is required on the interior, to the best of my knowledge. That said, your local code enforcement official always has the last word on code interpretation -- so you'll need to make a local inquiry on the issue.
Exposed fiberglass batts are usually permitted in an attic, but exposed kraft paper is not. (Kraft facing is flammable.) That said, you'll need to come up with a way to keep the fiberglass batts in place and snugged up tightly to the roof sheathing -- so interior drywall often makes sense.
Martin,
What's the best way to handle dormer walls(with exterior rigid foam) to roof with foam above the deck transition?
a- Rigid foam on the dormer wall spray foamed and sealed to the roof foam?
b- Wall foam spray foamed and sealed to the sheathing above the roof foam?
c- Rainscnreen behind the wall foam with gap between the bottom of it and the sheathing above the roof foam?
Asim,
Either (a) or (b) is better than (c). You don't want a rainscreen gap to be behind the wall foam. The rainscreen gap (which allows outdoor air to move through the wall assembly) always belongs on the exterior side of the insulation layer.
For details on dormer-to-roof connections when the dormer has exterior rigid foam, I urge you to study the details provided by Mike Guertin in his recent presentation, "Keep Water Out or Nothing Else Matters." Start at Slide 51 or Slide 52. You're looking for the slides with a heading that reads, "Exterior Insulation / Rainscreen."
Thanks for your thoughtful replies to my earlier questions, Martin. A few follow-up questions, this time regarding the interior of my unvented cathedral ceiling with above-deck insulation (a combination of EPS and polyiso).
1) Will I need a thermal barrier on the underside of my roof?
> From what I understand, many residential codes allow rigid foam boards like EPS and polyiso to be left exposed, or separated by a non-fire-rated barrier (i.e., a roof deck). See, for example, . I assume that is because EPS and polyiso do not count as "foam plastic insulation" , or have been specifically tested to show that they meet the requirements for 15-minute fire rating. Regardless, I am hoping to avoid installing 1/2" drywall on the underside of my rafters, and probably can't afford a 15/32" hardwood ceiling
2) Supposing I do need a thermal barrier on my ceiling, are there any promising alternatives to 1/2" drywall and 15/32" tongue-and-groove. I've come across a partial list of materials and thicknesses for which I might be able to make a case to my local code enforcement office . Do you know of any other such lists, or any other interesting and affordable materials that might satisfy code?
> I'm specifically interested in the industrial cardboard used, for example, as structural materials by Japanese architects . Or, perhaps more reasonably, some of the new wood paneling options that are cheaper and lighter than tongue-and-groove, and more appealing than their cheap-looking predecessors . I've been unable to find reliable information for fire-ratings of any but a few common building materials.
3) If I decide to add 5-1/2" of high-density fiberglass batt between my rafters, will that affect whether or not I need a thermal barrier on my cathedral ceiling?
I understand that I will need to consult with local code and enforcement officials, but as you frequently point out, the code is not entirely clear on when and where thermal barriers are necessary. Any responses to my questions will, therefore, serve as useful starting points for further investigation and help me in my conversation with local code and enforcement.
See my response above, in Comment #168.
I apologize if I've missed this clarification, but I noticed from the FHB article on sealing SIPS:
"Most asphalt-shingle manufacturers void their warranties when shingles are installed on an unventilated roof."
I was also told this by a builder as well; mentioned something about 'not good for the shingles' (it didn't seem they were referring to ice dams, the issue that makes sense to me, but perhaps they were—I wasn't able to talk long with them)
I'm just curious why this hasn't been discussed or clarified here given that the advice seems to be that ventilation is unnecessary save for areas with high likelihood of ice dams. Is it that science/experience doesn't back whatever reason the manufacturers came up with for voiding?
https://www.jlconline.com/how-to/roofing/unvented-roofs-and-shingle-warranties_o
Thanks Malcolm. Seems like a case of 'not an issue if you actually build a proper assembly according to code, but... we (manufacturers) don't trust that to happen.' haha
Tyler,
That sounds like fair summary to me.
It must be difficult for them to separate out the warranty claims rightly based on issues related to defective products, and those originating in poor roof assemblies.
Tyler,
This topic comes up regularly on GBA. For example, the issue was discussed in an article called "Rescuing a Problem Cathedral Ceiling."
In that article, Scott Gibson wrote:
"One key question about the unvented assembly, he [David Sheard] adds, is whether it affects the life expectancy of asphalt shingles on the roof, and whether manufacturers will honor warranties when shingles are installed over an unvented roof.
“ 'Either way will work,' Holladay replies. 'If you want to have a ventilation gap between the top of the cured spray foam and the underside of the roof sheathing, you’ll need to install very rigid insulation baffles before the foam is installed.'
"As to the warranty issue, he says, it varies by manufacturer. Many won’t provide a warranty if there is no ventilation channel beneath the sheathing. 'There is little logic to justify their position, however,' Holladay says. 'Fortunately for contractors, the roofing warranties are almost worthless, so this issue doesn’t matter too much.' ”
Hello,
I am about to install my roof assembly. Its a low slope metal roof. With exterior rigid foam above the roof sheathing. Its for a tiny house which has a fascia board that covers the sides of the rigid foam and attaches to the wall sheathing. Hoping to make the whole thing very air tight.
My question is about underlayment. The house will likely spend time in hot Arizona summers, I would like to install a high temp peal and stick underlayment. Wondering which is best. Underlayment bellow or above the rigid foam. ?
The issue is because of the way the fascia is assembled. I think I need to have an underlayment on top of the rigid foam so it can extend over the fascia board, and not get trapped behind it.
Also considering doing both above and below? Unless this would trap excessive moisture. Its a very low slope and will likely see some moisture. I guess if it needs to be bellow the rigid foam I could vent the fascia board so water can escape. Would like to avoid this though.
Any recommendations between the peel and stick underlayment being above or bellow the rigid foam ? Or possibly doing both, which would be my preference.
Thanks ,
Alex
Alex,
My recommendation would be to install the peel-and-stick membrane directly above the roof sheathing as an air barrier. Then the rigid foam goes on top of the peel-and-stick. Between the rigid foam and the roofing, you need roofing underlayment (it's a code requirement) -- but you can use any type of roofing underlayment you want. It doesn't have to be a peel-and-stick product.
Ok thank you,
Yeah, I will install the peel and stick membrane directly above the roof sheathing.
And then find another underlayment to go under the metal roofing.
Thanks
Alex
Martin,
Do you see any issues with installing a peel and stick membrane to the sheathing as well as another peel and stick on top of the rigid foam as the roofing underlayment. Just worried I may create some issue trapping the foam from being able to dry out if it gets wet.
Appreciate all your advice, this website has been tremendously helpful.
Thanks
Alex
Alex,
I would use a simple underlayment, not a peel-and-stick underlayment, between the rigid foam and the roofing. Ordinary asphalt felt would work, or (if you are worried about hot-temperature performance) a high-temperature synthetic underlayment.
Needless to say, you need very dry weather for this phase of construction -- any dew or light rain during the work would make me nervous.
Ok, what about your thoughts on using Mento 1000 air barrier on the roof sheathing to air seal. Then rigid foam, then a high temp peel and stick as my roofing underlayment.
Or do you still think the above option is preferable ? Peel-and-stick, foam , then felt.
I will also have battens and an air gap bellow the metal roof.
Thanks!
Alex
Alex,
The layers you suggest will work.
Martin,
I have another question regarding my roofing installation on the tiny house. It has R23 wool between rafters, then sheathing, Mento 1000 air barrier then R20 rigid foam and then a high temp peel and stick. With all this bellow the metal roof do I need to be very concerned with condensation under the metal?
I am needing to install structural members to attach the standing seam too. I was planning to attach battens which would also provide an air gap under the metal roof. However its a low slope so the ventilation aspect will likely not be very functional, I mostly need it to structurally attach roofing. With all these layers bellow and a high level of air tightness do you think condensation under the metal will be an issue? I am mostly concerned that my battens will eventually rot out. I've considered coating them for water protection, but wondering if you even think they will be exposed to much condensation from underneath the panels?
Thanks for the help,
Alex
Alex,
Condensation under metal roofing has nothing to do with how much insulation is below the metal roofing, nor with the airtightness of the roof assembly. The source of the moisture is outdoor air. Moisture in the outdoor air will condense on the underside of the metal roofing whenever weather conditions are favorable for condensation -- generally in the spring, when outdoor air warms up and holds more humidity, and when the metal roofing is cooled by a layer of snow or by night-sky radiation.
So, yes, your metal roofing will get condensation on the underside.
Your roof assembly will be fine. The condensation will sit for a while on the peel-and-stick membrane, and will eventually evaporate.
Ok thank you! the climates I am are prone to a lot of condensation.
Do you think I should primer the battens to protect them?
Or they should be fine ? Just thought a little added protection for the wood battens on the low slope might be a good idea.
You've really helped me out on this project Martin.
Thanks,
Alex
Alex,
Untreated battens should be fine.
Martin!
I made a mistake. Ive been moving quickly to get this done. I Installed Polyiso, which after re-reading this article was not the move I wanted to make.
I've been planning to have this house in Zone 5. I have R24 wool under sheathing. then mento 1000 wrb. Then 4 inches of polyiso . Im concerned that the regular bellow 20 temp winters in eastern Oregon is going to significantly decrease my upper R value and compromise the unvented roof assembly. I saw Dana's post above and If the house is kept warm the polyiso R value may only drop to R5 or R4.5.
However if it drops to R4 or lower and I get less than R16 should I be worried about condensation? Consider changing my design?
-Alex
Alex,
I suggest you read this article: "Cold-Weather Performance of Polyisocyanurate."
Here's the advice from building scientist John Straube: "One option is to stick with polyiso and just make it thicker. If we do that, let’s call polyiso R-5 per inch."
Following Straube's recommendation, you have a layer of polyiso that performs at R-20, and you have fluffy insulation between the rafters that performs at R-24, so the total R-value of your roof assembly is R-44. In Climate Zone 5, you want a minimum of 41% of the total R-value of your roof assembly to come from the rigid foam layer. (For more on this topic, see "Combining Exterior Rigid Foam With Fluffy Insulation.")
In your case, 45% of your total insulation is provided by the polyiso, even if you de-rate the polyiso's performance down to R-5 per inch. So you're fine.
Hi Martin,
I am trying to determine if adding a layer of rigid foam board will help resolve a problem we have had with a leaking flat roof deck (tiled) over living space. The deck has leaked on and off since it was installed in 2014. It leaks in the summer when storms are in full force (Tampa Florida (climate 2) waterfront). The deck faces south and does not have a roof over it so it gets a lot of sun and a lot of driving rain. The tile and waterproofing layer have now been removed, and the deck is ready to be rebuilt. However, the problem is that there was no clear evidence of the source of any leaks. The walls, windows, doors, and the single post-to-deck penetration show no evidence of being the leak source. The waterproofing company believes their product failed because the ceiling of the living space below is insulated with open cell insulation (Icynene). They believe the open cell foam needs to be removed from below, OR an air gap needs to be installed on top of the existing deck prior to their new installation. I believe the “gap” concept fails here because there is nowhere for the hot air to escape from a gap in this assembly, and the drainage from this gap on the low side of the deck also does not work the same way it would if it were a wall assembly. It is also unclear to me how the open cell spray foam could be causing the waterproofing layer to fail. However, based upon your article, it appears there may be merit in adding a layer of XPS foam and another sheathing layer before we put on the new waterproofing layer.
ORIGINAL CONSTRUCTION OF DECK - EXTERIOR ASSEMBLY
- Trusses 12” on center with 1/4” pitch designed into the top chord
- 3/4” Advantech subfloor glued and screwed
- Second layer of Advantech subfloor staggered and then glued and screwed
- Waterproofing System = Cement based system installed over wire lathe and flashing (.60 Perms) (demo is complete and this is now removed)
- Porcelain Floor Tile (demo is complete and this is now removed, and tile will not be reinstalled on the new deck)
ORIGINAL CONSTRUCTION OF DECK - INTERIOR ASSEMBLY
- The living space ceiling below the deck is insulated with Icynene open cell foam. In addition, upon inspection of the original foam installation it was discovered to be a little thin, so we added a layer of R-13 (or R-19 I can’t remember which) below all of the icynene.
- Ceiling is 1/2” drywall
- There are three A/C units in this home. The one that controls this space is dedicated almost exclusively to this space. The unit has a thermostat with a dehumidification function that is always set at 50% RH.
POSSIBLE SOLUTION -
- Install 1” of XPS foam on top of the existing two layers of Advantech subfloor.
- Install 3/4” Subfloor sheathing on top of foam board so waterproof system can bond to the new subfloor (will not bond to foam)
- Install new waterproof system (.60 Perms) on top of new subfloor.
CONCERNS:
- Will the addition of this new vapor barrier (the 1” of XPS) create any new problems with condensation, trapping moisture, etc?
- How effective is the 1” of XPS as a vapor barrier when it is full of nail and screw holes from the sheathing install, and then from the staples from the lathe system of the waterproofing layer?
- Should there be a gap at the foam board? If so, how does it vent and drain in a roof deck assembly?
- It seems to me that in this assembly the 1” XPS may be unnecessary. With a .60 Perm waterproof system the entire assembly should just dry to the inside as it is currently constructed, should it not? It is not clear to me in this application what the foam board actually accomplishes.
- Alternatively, If the goal is to install a vapor barrier between the living space and the waterproofing system would it not work to just install a peel-and-stick roof membrane directly onto the existing sheathing, and then install 3/4” sheathing on top?
Thank you for any help you may be able to offer.
Eric
Eric,
I'm not sure whether the diagnosis you describe makes any sense. If the diagnosis was made by someone other than you -- by a contractor, for example, or a consultant -- then it's possible that you aren't clearly communicating certain factors.
This is either a roofing leak or some type of condensation issue, and all evidence seems to point to the fact that this is a roofing leak. I'm not there, however, and I haven't inspected the roof assembly, nor do I know all the details. So perhaps I'm wrong.
If this is indeed a roofing leak, you need an impeccable job of flashing and a new watertight roof. The insulation details are irrelevant.
Needless to say, a low-slope roof covered by patio tiles is often problematic. I'm not enamored of the detail -- I like roofs to have a significant slope. I'm not sure what you mean by "Waterproofing System = Cement based system." In general, I think like a roofer. First you need roofing. Once you have watertight roofing installed, you can then install a drainage membrane or some type of dimple mat, followed by a substrate for patio tiles and the actual tiles.
Make sure that you have a roofing consultant on your team -- not just a tile guy. Good luck.
I would also question the "waterproofing system." I do a fair amount of work with flat roof decks, and I have yet to run into a cement-based waterproofing system that works. You generally need some sort of organic-based (think rubber) membrane layer to do the waterproofing. Add a drainage layer on top of that, and then your cement-based bedding layer for the tile.
Dex-o-Tex is one cementitious system that works OK, but it incorporates a slip sheet and a latex waterproofing layer under the cement-based traffic surface. You've just got to have a waterproofing layer below the cement.
You could also take a look at Schluter systems. They're just one of the available systems, but they make all of the different layers necessary for a successful tile roof deck, and they've got pretty consumer-friendly information on their website.
There's nothing wrong with the construction you mention. The Icynene foam should not cause any particular problems with condensation in your climate, and the two layers of Advantech should be plenty stiff to support any sort of deck system. Another layer of foam on top of the Advantech probably won't help and it could hurt because it's a lot softer than the Advantech - less support for the surface.
My house is 150 years old; the rafters are not uniformly 16" on-center though they are close, and the decking is 3/4" hardwood boards with some gaps in between. The roof line is fairly complicated, with several hips and valleys, and it is fairly steep at a 12/12 pitch. I have a stamped structural engineer letter saying my rafters, walls, and foundation can handle the additional load of my proposed 4" of EPS + 5.5" polyiso, plus additional OSB et al.
I'm having a hard time convincing roofers in the Midwest to consider installing rigid foam on top of my existing roof. Most residential roofers are totally unfamiliar with the concept, but even many commercial roofers are confused, and keep asking for "plans and specs for the entire roof system". This, after I've also linked them to this website and the USDE brief on the topic, and shared with them the details therein.
As such, two questions:
1) Is there some other resource I can point them towards that would show in greater detail how all of this goes together? Among other things, they seem nervous about flashing, and about extending the eaves.
1.a) Regarding flashing, I have not been able to find much information on how to install and flash Velux skylights (which I'll need for egress) with the thickness of rigid foam I'm proposing.
1.b) Regarding soffit and fascia, you've already provided helpful illustrations showing that eaves can be extended or stepped, and that fascia can be made taller. Are there more complete details showing how such treatments are built? The only one I've found is here , but it uses 2x4"s atop the rigid foam to extend the overhand AND create a vented roof, while GBA seems to promote an un-vented roof assembly.
3) Is there something about my roof in particular that makes this assembly questionable and/or especially difficult? In addition to the description above, I've included images of the roofline and the rafters and decking.* Are there specific air membranes, underlayments, nails/screws, etc I should specify in my roof assembly detail?
* In the exterior roof renderings, please note that the hole to the south will house a new, flat-roofed dormer. In the interior images, please note that the rafters are being sistered with engineer-specified steel plate, and hip and valley beams are being reinforced with engineer-specified LVL.
Hi Martin,
Thanks for providing this help for all of us needing to retrofit our leaky old houses. My questions are: 1) if rigid can be installed on top of some asphalt shingle without a full tear down, plus 2) if the ice and water at the base of the job needs to be high temp if under a metal roof.
We are in climate zone 7 and our contractor and I agreed on the following layers: (mix of R11/R19 fiberglass underneath the board sheathing currently, and it looks like we meet the minimum rigid requirements)
1. Mix of standing seam metal roof for 2:12 slope areas (two dormers) and asphalt shingle for the 8:12
2. Synthetic vapor barrier
3. OSB
4. 2x4's flat on the foam creating air channel and 2x10's around the sides forming a box
5. 4" EPS+4" PolyIso staggered with top layer taped
6. Ice and water
7. original board sheathing
Today the job started in earnest, but three of his tear-off crew didn't show up to work and there is supposed to be rain tonight. Because of the rain, he is now proposing to leave the current asphalt shingles in place over the 8:12 sloping areas and just tear the asphalt off of the dormers completely, plus a small bit off the rest of the roof where the 2x10's are going. The dormers would be ice and watered, but nothing else would be. Then install the rigid layers directly on top of the existing shingle for all the 8:12 sloping areas.
I've told him I want to stick with the existing plan, but I am getting a lot of push back. What do you think?
I would like to know, instead of guess, that the original board sheathing is in good condition. The current shingles were a previous homeowner and I think there is only felt under there. We've had leaks on the dormers, but not on the rest of the roof.
An update after the first day.
The contractor removed the existing shingles from the low slope area and exposed quite a bit of rot. He replaced some boards, OSB over the whole thing, and then ice and water. He still insists that doing this to the rest of the 8:12 sloped roof will be unnecessary and cost prohibitive. I need to have an answer for him today about this.
I'm concerned about the interior of the house being not particularly air tight, and humid air migrating into the sheathing underneath the asphalt shingles and foam and causing more rot or compromising the roof above. Is that a valid concern?
In a comment from 2013, I see you (Martin) mentioning vapor barrier paint. Does this advice still hold? Can I repaint the upstairs and sleep easily while doing what the contractor wants and leaving the existing shingles in place? Or do I tell him to tear it all off, replace as necessary, and ice and water regardless of his labor problems and his warning about potentially high costs (he is charging $75/sheet installed for OSB).
Thank you.
Cyrus,
Q. "I'm concerned about the interior of the house being not particularly air tight, and humid air migrating into the sheathing underneath the asphalt shingles and foam and causing more rot or compromising the roof above. Is that a valid concern."
A. No. If you are installing 8 inches of rigid foam above the roof sheathing, then the roof sheathing will be warm. (Remember, condensation or moisture accumulation happens on cold sheathing, not warm sheathing.)
If you decide to skip the Ice & Water Shield, then you need to make up for its lack by having a very tight air barrier somewhere in the roof assembly. In theory, you can create an air barrier with your plan, since you plan to tape one of the rigid foam layers. But without the Ice & Water Shield, the tape details matter -- so you need high quality tape, and the tape needs to be wide rather than narrow, and it needs to be impeccably installed.
All that said, even with an impeccable air barrier at the top of the foam, you can have problems. The most famous case is the case of Joe Lstiburek's barn. Read about the problems here: Complex Three Dimensional Airflow Networks. If you're worried about recreating Lstiburek's mistake, you need the Ice & Water Shield above the lowest level of roof sheathing.
Thanks for the reply Martin, and especially your reminder that moisture accumulation happens on cold sheathing. More of an education than a reminder, and I appreciate it.
I will pass this information on to the contractor. Our panels will be offset, unlike Joe's which will hopefully help, and I'll have the contractor tape multiple courses of foam with thick, high-quality tape and attention to detail.
In attaching a peel and stick membrane to existing board sheathing (100 year old house) to act primarily as an air barrier (short-term water barrier until the cold roof is completed), is any one brand/product better than another? The gaps between the board sheathing are generally around 1/4" to 1/2", with some up to 1". Some products suggest that the boards need to be butted together and thus the question.
B Allison,
I don't have any product recommendations, but I'd be interested to hear any suggestions from other GBA readers.
I looked at the installation instructions for a few products, and I couldn't find any information from manufacturers on the maximum sheathing gap width. You may want to call one of the manufacturer's technical help phone lines to ask about any limitations related to gap width.
Thanks Martin for looking into installation instructions for some products and the follow-up. I'll reach out to a few manufacturers and circle back if I acquire any information on specific products re: max gap widths. I too would be interested to hear what other GBA readers have used for such an application. Not having to install a skim sheet of 3/8" plywood over the existing board sheathing would save both time and funds.
Please do share your findings - we also have skip-sheathing, and are considering Intello (with taped seams, obviously) instead of peel-and-stick. The Intello is rated for dense-packing, so I presume that little gaps should be no trouble. Throwing a bunch of rigid foam on top (instead of dense-packing cellulose between above-deck TJIs) would be even less stressful, I imagine.
Why not Grace Ice & Water Shield? I'm embarking on a similar project and it seems to me that any quality peel-and-stick roofing underlayment would provide a robust air barrier while also protecting the house from rain during roof re-construction. I also prefer materials that are locally available, familiar to my contractor, and can provide good traction on our 10/12 roof.
Climate zone six requires R-49
Roof is a 2/12 pitch unvented assembly stacked as follows
1.Metal Roof
2. ice and water shield
3. osb or plywood
4. 2X4s for vent channels
5. 5 inches of xps taped Will give R-25
6. osb or plywood taped
7. underside of roof sheathing R-24 air permeable insulation.(6 1/2")
8. Drywall
Will this roof assembly work any thoughts or concerns?
Will I get ice dams if I eliminate the 2x4's for vent channels on a metal roof?
Brandon,
Since your roof has a pitch of 2 in 12, it's a low-slope roof. For advice on insulating a low-slope roof, see this article: "Insulating Low-Slope Residential Roofs."
In general, you won't get much air flow through 1.5-inch-high vent channels in a low-slope roof -- the slope is too low for air flow. So I wouldn't bother with the 2x4s for vent channels.
While it's impossible to totally eliminate the chance of ice dams -- some ice dams occur simply from the effects of the sun -- your roof won't allow any ice dam problems, because (a) it's well insulated, (b) it sounds like it will be airtight, and (c) you plan to include Ice & Water Shield under the metal roofing.
Ok. Sounds good Martin. Thanks for the reply
For option 1 in zone 6, is there a minimum r-value that will keep the roof deck safe from condensation (code requirement aside). I will be removing a roof down to 2x t&g deck, zero insulation on the interior and dont want to add any as there's no room to come down from the existing ceiling, and planning on doing a solitex peel and stick, build up with rigid foam, 2x4 on side to screw to and create air gap, metal roofing on the top. I am hoping to not tear down existing 2x6 fascia, which only has 4" between the top of it and the roof deck top. Some possibilities to build the foam up higher that have been suggested to me is to do a double fascia (keep existing fascia on, nail another one to its face but higher so that the top of it ends where I would put my foam). The inspector is ok with me me not hitting code for insulation since its a replacement but i'd like to up the insulation from what it is obviously. I'm on a pretty tight budget and don't want this to spiral out of control with having to replace all fascia, use ultra long screws, and so on.
For a roof-replacement project on a 90+ year old Slate roof of a Zone 5 brick house, I am planning on metal shingles that resemble the existing Slate. The existing roof is a simple tent: 45 deg pitch, two gables. I estimate it is good for about R-1.
As insulating the inside of the attic is not practical, I am planning exterior insulation per option 2 of the above article: tear-off down to existing board deck, air barrier, polysio + EPS, and flat-laying 2x4s for a vent space.
So, a new substrate for the shingles is needed. There seem to be at least two configurations: a new layer of sheathing on top of the 2x4 vent guides, or purlins over the 2x4s.
My questions:
What are the pros/cons of sheathing or purlins in this configuration?
With purlins, would the second underlayment go on top of the EPS layer and the rest of the sticks over that?
With sheathing, would the second underlayment go on top of the sheathing?
Are there any pros/cons for OSB or CDX for the sheathing in this situation?
New taller fascia boards will be needed at the edges. How should the edges of the insulation sheets meet them? Flush? Air gap? Sealed? Should the top layer of underlayment wrap down to cover the edges of the insulation sheets?
Thanks in advance ...
Robert,
You need to have a conversation with the roofer who will be installing the new metal shingles. There are many brands of metal shingles, and I imagine that each manufacturer has its own requirements for the substrate. Some metal shingle manufacturers may allow the use of skip sheathing (purlins), while other metal shingle manufacturers may require solid plywood or OSB sheathing as the substrate for the shingles. Your roofer should know these requirements -- and in addition, your roofer almost certainly has strong opinions on the best approach.
Of course, the contractor and supplier's requirements will have to be accommodated. Are you suggesting that, other things being equal, the purlin or solid substrate on top of the option 2 stack will not have a significant effect on overall thermal performance?
Robert,
Q. "Are you suggesting that, other things being equal, the purlin or solid substrate on top of the option 2 stack will not have a significant effect on overall thermal performance?"
A. Yes.
I recently had slate like metal "shingles" manufactured by Edco installed to replace old asphalt shingles. You'll want to consider carefully replacing real slate with these steel look a likes. What they don't tell you is that there will be considerably more noise when it rains since there is an inherit air gap under the shingles to form the protruded slate profile. You will also notice creaking noises from day to night from thermal expansion. I would suggest getting a sample of whatever product you will use to see if it is acceptable especially considering you have real slate now. The shingles are surprisingly thin. If you still want to use them you may want to ask if there is some way to deaden the noise if you think that may be an issue for you.
Edit: the noise I am referring to is from outside since the insulation you would be adding under the shingles should deaden noise propagating into the building itself.
Thanks for the info - Edco is one of the suppliers I'm considering. I'd prefer real slate, but the prices I gotten indicate it would be about 3x over metal shingles (not including the thermal layer), which would put the total cost at 20%+ of the house's market value.
A solid top layer (OSB + underlayment) would probably mitigate noise propagation to the inside a little more than purlins. As there are no living spaces directly under the roof deck, I'd guess the interior noise would be de minimus. I'm considering adding mineral wool batts to the existing rafters (where possible), which would further reduce noise transmission.
What is your take on the visual effect? How well do they resemble real slate when viewed from street level? The samples I've seen have a slight sheen that is not present in (old) slate.
An interesting approach for sheet Polyiso exterior insulation of flat commercial roofs is presented at
https://www.gaf.com/en-us/blog/designing-with-polyiso-281474980064941
The strategy is to use a thin first layer of Polyiso attached with fasters. A second thicker layer with overlapping edges is glued on top of this without using fasteners. This reduces thermal bridging that results when fasters exposed to the exterior penetrate both layers, because the metal fastener heads are covered under the second layer. Making the first layer thinner also allows for the use of shorter fasteners.
Could this configuration (or elements of it) be usefully adapted for pitched residential roofs as discussed above? How so?
Publications on cold roof design by J. Lstiburek suggest using a 2” air channel, while others have suggested that 1 1/2” is sufficient (2”x4” laid flat on its side). I’d appreciate hearing what folks real world experience has been (i.e., Climate Zone 7 - ) relative to air channel depth?
Below is the cold roof assembly being considered for existing 11/12 pitch roof (upper section of gambrel roof - Dutch Colonial house):
-3 1/2” closed cell foam below existing roof boards (currently in place - LTTR ~ R20)
repair (as necessary) existing 1” roof boards
-3/8” plywood skin
-Siga Majvest 500 SA (air barrier)
-6 1/2” GPS Chrome insulation (LTTR ~ R32 - R35 temperature dependent - J. Straube) 3 layers w/ taped seams
-1 1/2” (2”x4” on side) OR 2” (2”x4” on side + 1/2” plywood) air channel
-1/2” plywood deck
-Siga Majvest 500 SA (eaves, rakes, valleys) / Siga Majcoat underlay (elsewhere)
-metal shingles
B. Allison,
You have a lot of redundancy in this assembly. For example, 3.5 inches of closed-cell spray foam is already an air barrier, so you don't need to invest in the layer of Siga Majvest 500 SA (although this unnecessary layer won't cause any harm).
Moreover, your insulation layers -- R-20 of closed-cell spray foam under the roof sheathing, and R-32 of graphite-enhanced EPS rigid foam above the roof sheathing -- don't require a vent channel. This is a perfectly acceptable unvented assembly.
So there won't be any moisture that your vent channel needs to handle. Perhaps the vent channel is there to address potential ice dam concerns? If I were you, I would be happy with a 1.5-inch-high vent channel (using 2x4s), and I wouldn't worry.
Thanks Martin for your quick response. A couple follow-up comments below.
- Ice dams have been an issue on this house for several winters, even with the 3.5 inches of current (closed cell) spray foam in place. Given the roof shingles need to be replaced, it seems reasoned to work towards addressing the ice dam issue via added external insulation et cetera at this time.
- Good to hear your thoughts on redundancy in the proposed assembly (e.g., Siga Majvest air barrier layer). With the work likely to take some time to complete, my thinking was that this layer could also act as a water barrier through the construction phase.
- Given I'm in a high snow load area (past issues with ice dams), Lstiburek (BSI-046: Dam Ice Dam) seems to suggest the need for a vent channel to reduce ice dam potential. Do you believe that ground snow load (i.e., > 60 lb./ sq. ft.) does not matter and thus no need for an air channel or at least not one of 2" depth in such locales?
Thanks much for your insights.
Hi Martin,
In a retrofit situation, how much of a concern is thermal bridging through rafter tails if foam extends over the tail (as in your drawing for "Insulating a Cathedral Ceiling FHB #228, options 1 or 3, screen grab attached). Should the soffit be insulated to limit energy transfer through the rafter into the building or does the foam on top keep the rafter warm enough to prevent it from becoming a condensing surface? Thanks! - Oliver
Oliver,
Is this the image you intended to post (but forgot to post)?
If so, the image doesn't really show the whole story. While it shows a section of the assembly at one of the rafters, it doesn't show what's going on between the rafters.
You need a careful air barrier above the exterior wall top plate -- some type of blocking between the rafters, with the perimeter of each piece of blocking carefully sealed with caulk or spray foam. That blocking needs to be insulated (with insulation adjacent to the blocking). The R-value of that insulation should at least match the R-value of your wall insulation.
Assuming that you have air barrier continuity from the interior wall finish material all the way to the roof sheathing, and assuming that you have insulation adjacent to the blocking, I wouldn't worry too much about thermal losses through the rafter tails.
Hi Martin,
That is indeed the image. I edited my comment to add my name and neglected to re-attach. Thanks for digging it up.
As for the blocking, I do remember now seeing that detail referenced in another of your articles using rigid foam sealed with canned foam. For a good seal, perhaps detail that with a bead of sealant? And I'm guessing that foam blocking should end up in same plane as exterior and interior insulation so the wall is consistent.
Would it harm much to further insulated the rest of the rafter tail in the soffit with something permeable like mineral wool?
Thanks a lot!
-O
Oliver,
Q. "Would it harm much to further insulate the rest of the rafter tail in the soffit with something permeable like mineral wool?"
A. Since this roof assembly is unvented, adding insulation on the exterior side of the blocking (above the soffit) is fine.
Apologies if most of my question is redundant with the rest of this Q&A, but i want to make sure my exact scenario and details are considered.
I'm building a new A-frame where R38 roof insulation is required. I'm in zone 4A, but my state's requirements amend the IRC to only require R38 (Virginia). VA experiences extremes of both hot and cold, but neither for extended periods, and we have very modest amounts of snowfall. My roof pitch is 21/12, IE extremely steep, in case that matters. I'm hoping the steep pitch allows me some leeway in a few areas. Here is current plan, bottom to top:
1. T&G ceiling
2. Blown in wool insulation between 2x12 rafters at R31-R33.
3. Traditional plank roof deck (thinking full dimension 1x8's unless swayed otherwise)
4. Rigid foam at R5-R7
5. 1x4 purlins
6. 5V metal roofing
What this system is currently lacking is a moisture or air barrier beyond what is provided by the rigid foam. If at all possible, I would like to keep the system just like this, but my questions are:
1a. Does best practice dictate I add an additional WRB and/or ARB to this system?
1b. Regardless of best practice, is an additional WRB/ARB required by code?
2a. If the answers to 1a/1b are both "no", do I need an underlayment between the foam/purlins and the metal roofing?
2b. If the answer to any/all of the above is "yes", can I accomplish both or all 3 (ARB, WRB, underlay) with a single layer directly above the rigid foam and under the purlins/metal?
3. Would a 2x4 grid under the metal be preferred (versus 1x4 purlins) for venting purposes in an otherwise un-vented assembly?
Thanks in advance for the help!
Free Hollow,
I suggest that you read this article: "Combining Exterior Rigid Foam With Fluffy Insulation."
Your current plan does not include enough rigid foam to keep you out of trouble. As the article I linked to explains, in Climate Zone 4A, your type of roof assembly must have a minimum of 31% of the total roof R-value in the form of exterior rigid foam. Your current plan (R-5 exterior rigid foam plus R-31 of fluffy insulation) provides only 13% or 14% of the total R-value in the form of exterior rigid foam. That's not enough. So you need thicker exterior rigid foam.
If you added a minimum of R-14 of rigid foam above your roof sheathing, along with R-31 of fluffy insulation, you would be OK, since 14 divided by 45 is 31%.
The other big problem with your proposed assembly is that you have no interior air barrier. All you have is a tongue-and-groove board ceiling, which is as leaky as a sieve. If there are any small air leaks near the ridge of your roof assembly -- and trust me, such leaks are common -- you have created an air highway for interior air to flow at a high rate through your assembly. So you need an interior air barrier (I recommend drywall) behind your tongue-and-groove board ceiling.
Martin,
Thanks for the input. I've thought about it until my head hurts, and I think, as an amateur builder doing my own home, my most forgiving method will be to cut out the rigid foam and do a vented system with baffles and rely fully on the interior fluffy insulation. I'm going with Havelock Wool, so I can easily achieve the needed insulation depth in my full dimension 2x12 rafters.
It seems that having that ventilation is a nice crutch in case I missed any details associated with air sealing. Ventilated spaces like this may not be the most cutting edge, but I think they are tried and true.
In lieu of drywall, which I hate with a burning passion, I am considering an Intello Plus or similar membrane for interior air barrier. With attention to taping detail, I assume this is a reasonable solution, right?
My next question related to this new assembly is air tightness on my 1x8 planked roof deck. Are there airtight products that would also serve as my roofing underlayment so I just need one layer between my metal roof and the roof deck? The Havelock Wool is exceedingly expensive, so anywhere else I can simplify and save cost would be great.
Free Hollow,
There are lots of roofing underlayments that are relatively airtight. Some, like Grace Ice & Water Shield, are vapor barriers. Others, like SlopeShield Plus Self-Adhered, are vapor-permeable. Google "roofing underlayment +airtight" or "roofing underlayment +air barrier".
Note that if you are installing a type of roofing that is vapor-impermeable, there is no need for your roofing underlayment to be vapor-permeable.
Hello,
I have a 1970’s house with a family room with an unvented cathedral ceiling. Zone 6. Rafters are partially exposed inside. I haven’t cut into the drywall between the rafters. But from measuring outside and in, my best guess is a cavity of about 3-1/2” thick. We would like to add rigid foam to the exterior. We don’t have room to meet current code minimum because of 2nd story windows. We have room for 2” of rigid insulation. Maybe a little more after I research how close windows can be to roof. Can we follow recommendations for exterior insulation on stud walls to determine a thickness that won’t cause moisture problems?
Thanks for the great website.
70,
Here is a link to an article that explains the ratio rules when rigid foam is installed on the exterior side of roof sheathing: "Combining Exterior Rigid Foam With Fluffy Insulation."
The article includes a table (reproduced below) that summarizes the ratio rules. (Click on the thumbnail to enlarge the image.) Read the article for full details.
Thanks for the link. Does the minimum percentage of exterior insulation apply when the roof assembly doesn’t meet code? Or are the first two columns the only way to do exterior insulation? Meeting code is just not feasible for our house. But we’d like to do better than the 2 to 3” we have.
70,
If you read the article, you'll find the answer. In your case, you need to pay attention to the last column on the right -- the one with the heading, "Minimum percentage of the roof's total R-value that needs to come from the rigid foam layer." This percentage applies to all houses, whether or not the house meets code.
Thanks. I was confused about whether the minimum percentage was only for interior insulation going beyond code minimum.
You should be fine. The danger is when there is too little exterior insulation compared to interior. I've read some articles where they even advocate for virtually all insulation to be exterior with little or no interior insulation.
I'm doing something similar to you. We're renovating a Cape Cod with 3.5" insulation in the slanted wall/ceiling sections. We didn't want to destroy the interior or fur down the rafters, but we were able to add 4" of EPS on the roof. (Like you, we couldn't do more because we'd run into the bottom of the dormer windows. Plus, detailing the eaves and rakes becomes more challenging the thicker you go). It's all less than code, but the incremental reduction in heat loss in those first few inches of insulation is dramatic--especially if everything is sealed. See this graph about the diminishing returns of additional insulation. People talk about the "pretty good house" as a more realistic option for those of us with constraints (whether it's budget, design, existing obstacles, etc.) I think that goes for "pretty good insulation", too--as long as you observe the ratios and other best practices.
“[Deleted]”
Is an air barrier needed at the top of the sheathing if it is a flat roof so the exterior foam is covered with EPDM, making the air barrier at the top of the foam?
If you are applying the foam over existing sheathing, the barrier would be at the membrane applied on top of the existing sheathing under the foam. Furthermore, if the foam is properly sealed when installed, that would be an additional air barrier. By the time you get to the top sheathing, you should already be well-sealed. If it isn't, you might get frost accumulating under the EPDM from air leaks below that layer (depending on your climate zone). You want your air seal on the warm side of the foam.
I have 7/16 OSB sheathing on a hip roof that butts up to a wall. It seems easier to do the foam on top unvented assembly vs. trying to vent such a roof. I did not tape the osb, but I have grace tri-flex XT on top of that. Does that count as an air barrier, or do I need to take it off, and tape the seems? or will adding foil taped polyiso serve as an air barrier?
thanks!
User ...308,
Grace tri-flex is a roofing underlayment, so if you are adding exterior insulation it's going to end up in the wrong spot, and you will need another layer under whatever roofing you are using.
The problem with air-barriers over the sheathing is getting them continuous with the air-barriers on your walls, and dealing with penetrations. A better location is at your ceiling - or the sheathing itself, although you still have the same problems with continuity.
Is it a cathedral ceiling hipped roof, or is there an attic? If the latter you can effectively vent it with a combination of soffit and spot vents near the peak.
my sheathing terminates at the end of my rafters, and is not connected to my wall sheathing. Is it not possible to have the roof sheathing air sealed, separate from the walls? as long as you block off the spaces in between the wall top plate and the underside of the sheathing, between rafters?
Why do we need an air barrier at the roof sheathing, if we are going to be providing another air barrier with the taped polyiso?
how much trouble would I be asking for If I left the tri-flex and continued with polyiso?
I was hoping to leave it open inside, as a cathedral hipped roof.
thanks,
forrest
Forrest, the most important consideration is continuity. It's often difficult to make the transition from the air control layer at the walls to the rooftop, especially if there is a roof overhang. It can be done, but it's usually easier to do what Malcolm suggested. If you have a way to seal the rafter tails, you should be able to use the roof sheathing layer as your air control layer.
I can imagine overall performance of the building envelope will suffer if the wall is NOT continuous with the roof, but is it possible to treat them as separate entities? I mainly just want a well insulated roof that won't incur moisture problems. I think I would rather seal it up, than cut holes for vents. I've read that the tri-flex xt is a vapor barrier, but will it not serve as an air control layer in combination with the OSB? Just trying to figure if I need to tear it off, and use something different, or if it will work.
user-7601308, have you read these articles? I would start there, as I think they will answer most of your questions.
https://www.greenbuildingadvisor.com/article/how-to-build-an-insulated-cathedral-ceiling
https://www.greenbuildingadvisor.com/article/five-cathedral-ceilings-that-work
https://www.greenbuildingadvisor.com/article/installing-rigid-foam-above-roof-sheathing
Forrest, I think you're fine as long as you wrap the barrier around the rafter tails and there is adequate insulation outboard of that to keep the air barrier warm. I believe your Grace triflex plus taped polyiso is a solid air barrier. Not sure why it wouldn't be. I know Joe Lstiburek had an experience with warm spots along the seams of the foam on his home because he didn't seal them adequately (despite having an air barrier on the sheathing and the foam being overlapped). But the only casualty (other than his pride as he tells it) was that when there was a layer of frost on the roof, he could see lines in the frost where it melted along the seams. This makes an interesting point about how air can potentially navigate cracks and crevices, or even just move around via convection currents. But in the real world, it doesn't necessarily mean the assembly is failing--it's just a slight variation in performance. In Joe's case it wasn't inside air getting through to the roof sheathing (which would be bad), it was just a slight temperature difference at the seams. My biggest concern in cold climates (like Minnesota where I am) is moist air hitting cold condensing surfaces and freezing. I don't see how that could happen with your proposed roof assembly. Just make sure you know where the air barrier is at each part of the assembly and that it is insulated adequately such that it doesn't provide any condensing surfaces.
Forrest,
Sorry I was unclear. There is no downside to leaving the underlay and adding layers on top.
Air-barriers are only as good as their weakest point. If you can seal the perimeter of the rigid foam, and figure out a way to make the problem areas between the walls and the roof a air-tight as you can, you should be good to go.
thank you! should I tape the seams of the first layer of triflex? or should I just rely on the taped polyiso?
Forrest,
I wouldn't do any harm, but is probably not necessary.
I am planning to insulate the roof of a small timberframe (12x16) with an exposed decking roof. Above the toungue and groove decking, I have synthetic roofing felt, followed by 6" of xps foam. On top of the foam, im planning to do vertical 1x4 purlins, with horizontal purlins on top of that to make it easy to attach the exposed fastener metal roof. I have a few questions:
1) will this be adequate fro such a small building (30r value in zone 5b)
2) Will it be helpful to add peel and stick on top of the foam as extra water barrier, or is it a waste? Im thinking if the foam is taped well, it can be exposed for a short time before the metal roof gets installed?
3) What would the details look like in allowing airflow under the metal roof to flow? Would I just leave the space at the end of the metal roof open (bugs rodents and issue?) or install a sort of air permeable version of the gaskets they make for putting under the metal roof at the top and bottom?
User 6884146,
Q. "Will this [R-30 roof insulation] be adequate fro such a small building?"
A. In Zone 5, the 2015 International codes (under the prescriptive table) call for a minimum of R-49 for ceilings or roofs. In the 2021 version of the code, this minimum R-value has been increased to R-60. There are exceptions to these prescriptive minimums, of course -- check with your local code authority -- but R-30 isn't much.
Q. "Will it be helpful to add peel and stick on top of the foam as extra water barrier, or is it a waste?"
A. If the rigid foam gets wet during roof assembly, that's not an issue -- the moisture will escape via the air gaps provided by the purlins. But you need a bulletproof air barrier for this type of assembly (ideally close to the ceiling). If you forgot to tape the synthetic roofing underlayment seams and punctures, or you forgot to tape the rigid foam seams with high-quality tape, you certainly need to do something about air sealing.
Q. "What would the details look like in allowing airflow under the metal roof to flow?"
A. Sealing these openings to prevent the entry of insects or rodents is important. High-quality insect screening is one option.
Does it make any difference how you get 3" of polyiso on top of the roof sheathing? say either 2" sheet with a 1" sheet, or two 1-1/2" sheets? or three 1" sheets? currently you can buy two 1.5" sheets for less than 2" + 1" sheets. just curious if it makes a difference either way. Also, from what I've read on this site, polyiso - though its performance goes down with the cold, having 3" means you will likely always have two full rated inches that are insulated by the outermost inch? so you can meet the minimums for zone 4 in Virginia with 3" even if it gets really cold every once in a while? thanks!
User 7601308,
Q. "Does it make any difference how you get 3" of polyiso on top of the roof sheathing? say either 2" sheet with a 1" sheet, or two 1-1/2" sheets?"
A. No, it doesn't make any difference.
Q. "Polyiso - though its performance goes down with the cold, having 3" means you will likely always have two full rated inches that are insulated by the outermost inch? so you can meet the minimums for zone 4 in Virginia with 3" even if it gets really cold every once in a while?"
A. Here's the advice given by building scientist John Straube on this issue: "One option is to stick with polyiso and just make it thicker. If we do that, let’s call polyiso R-5 per inch [instead of the R-6.5 or R-6.7 per inch claimed by some polyiso manufacturers]."
So, if you take Straube's advice, 3 inches of polyiso can be considered to provide R-15, which (as you correctly suggest) works in Zone 4.
More information here: "Cold-Weather Performance of Polyisocyanurate."
I think I posted this question in the wrong place. Hopefully this is the right spot. Thanks.
I live in a story and a half home in zone 6. I have been planning to add rigid foam insulation to my roof with 1x trips for venting and metal roofing. Since the hvac systems has been renovated to properly heat the whole home we consistently have ice dams. My roof rafters are 2x4's and though there were roof vents installed during an older re-roofing (before I purchased), there is no soffit venting on this home, so I am not certain their purpose. After reading several articles on this helpful site, I am still had questions about my situation.
Before having a full understanding of the lack of venting and ice dam issues, I had more cellulose insulation added into both attic spaces already containing cellulose insulation. One space behind a knee wall overtop of a conditioned bedroom and the other space is a 3/12 roof covering a 28ft dormer section of the home. Hopefully my poorly drawn photo will help shed light on my description.
Based on my understanding, the knee wall area could be a candidate for rigid foam on the roof sheathing if I removed the roof vents and adding batt insulation in its their place. Then I would remove the cellulose leaving r15 batts in the cavity in direct contact with the sheathing and R34 of rigid foam on the roof sheathing. However, the larger roof area has no batt and all cellulose in direct contact with the sheathing excluding about 9 inches off depth. I presume I could fill the attic with cellulose to fulfill insulation in direct contact with the sheathing and apply the same R34 worth of rigid foam there as well, however, as I’ve come to understand the amount of cellulose may create a moisture problem for me and change the requirement for rigid foam on te exterior.
Could you recommend how I might move forward considering the loose fill insulation?
What are my options if the loose fill stays?
Because my home stays warm throughout the winter do I forgo the rigid foam all together and simply create external vents under new roof base or under metal roofing?
Thanks for any insight.
Vic
Old Cold,
Installing an adequately thick layer of rigid foam insulation over your entire roof, along with new sheathing above the rigid foam and new roofing, is an excellent way to address ice dams. You are on the right track.
Ideally, you will supplement the rigid foam insulation with additional fluffy insulation between the rafters (in direct contact with the underside of the roof sheathing), following the ratio rules outlined in this article. If you do that, you shouldn't have any vent channels (except optional vent channels above the rigid foam layer).
If it takes you a few years to get around to installing the fluffy insulation between your rafters, a thick layer of rigid foam will still prevent ice dams. Do the best you can at achieving the goal of moving the fluffy insulation where it belongs -- between the rafters and in direct contact with the underside of the roof sheathing.
Is there a thing as "too much" fluffy insulation? Meaning, if I remove my side gable vent and filled my entire actic with fluffy insulation to gauarentee it is touching the roof sheathing and then covered the top side of the deck with 6-8" of rigid foam. Would something like this work? Accessing the attic to install batt insulation is nearly impossible as it is approximately 2 ft high because of the 2/12 pitch of the dormer.
The only way I could see this happening is stripping the roof of the original gapped planks at which time it might be easier to sister new 2x12's to give better insulation depth and vented chanels. A job I am not looking froward to attmeping.
And if I had to, *not monetarily ideal*, place R49 of rigid on the roof deck then I am curious if anyone has done a 2x4 perimeter as tall as the sheathing so they can continue the wall sheathing and then detail the eaves and gables sides. *maybe asking this incorrectly*
Old Cold,
Q. "Is there such a thing as 'too much' fluffy insulation?"
A. Yes, as my article explains: "If you are planning to thicken the insulation installed under the sheathing in order to achieve a total R-value that exceeds code-minimum requirements, you’ll need to also thicken your above-sheathing foam layer to keep the ratio of above-sheathing insulation to below-sheathing insulation in the proper proportion."
The table below summarizes the ratio rules. The last column shows percentages; in each case, the R-value listed for the rigid foam is a minimum R-value.
Why is the ratio of above-sheathing to below-sheathing important?
Several Types,
Q. "Why is the ratio of above-sheathing to below-sheathing important?"
A. If there is too little exterior rigid foam, or too much interior fluffy insulation, the sheathing can be cold enough in winter to permit condensation (or moisture accumulation) in the sheathing. The exterior rigid foam limits outward drying, so mold and rot are possible.
Martin,
I'm curious how having too much fluffy insulation and not enough rigid foam is any different conditions than my current situation of an unvented roof filled with fluffy insulation aginst most of th e sheathing yet not enough insulation depth near the eaves?
Considering that the majority of my roof pitch is low (2/12) making insulating the bottom side of the roofing deck extermely difficult if not impossible without demoing every ceiling, what might you reccommend? Is the "answer" leave the blow in as is and place 10in of rigid foam on the roof deck? Do I consult my engineer about using 2x12 i-joist and building a deeper roof over my existing roof? Or simply cover the enitre roof deck with ice and water shield and invest in a good roof rake.
My apologies for the barage of questions. Just trying to get a better grasp of it all.
Old Cold,
Q. "My current situation [is that I have] an unvented roof filled with fluffy insulation against most of the sheathing yet not enough insulation depth near the eaves. ... My roof pitch is low (2/12)."
A. Your roof is poorly insulated and at risk of moisture accumulation. How bad the moisture situation is depends on (a) your climate (colder climates come with more risk that hot climates) and (b) the number of air leaks in your ceiling (more air leaks are worse than few or no air leaks). Regardless of the urgency of the moisture situation, you describe a roof that is wasting energy.
Low-slope roofs are very difficult, or in some cases impossible, to vent, so my recommendation to you is to choose an unvented solution. The best solution in your case is probably to install a thick layer (0r layers) of rigid foam above the existing sheathing (after repairing any rotten sheathing, of course), followed by a second layer of sheathing and new roofing.
For more information, see "Insulating Low-Slope Residential Roofs."
As far as having an air Barrier on the ceiling side - am I correct in understanding that is just extra precaution to make sure you don't get hot humid indoor air in contact with the roof sheathing?
Is this more of a concern if you only have insulation below the roof sheathing?
If you have taped poly-iso that satisfies the rooftop insulation requirements, won't your sheathing always - in theory - be warm enough to prevent condensation from indoor air, even without an interior air barrier? SO if you have adequate rooftop insulation, an interior air barrier is redundant, though helpful?
thanks!
User 7601308,
An air barrier on the inside of you ceiling assembly is always desirable. Air leaks are never good. Even if you have an adequate thickness of exterior rigid foam, air can leak out of your house through cracks between sheathing sheets and cracks between pieces of rigid foam. When this warm, humid interior air contacts the underside of your cold roofing, you can get condensation and a wet ceiling.
I've come to the conclusion that internal air barriers are close to useless unless you build a service cavity. There's too many penetrations and they are going to leak. An exterior air barrier is superior if you can do it.
qofmiwok,
A perfectly legitimate preference, but not half as clear cut as you suggest. Both perform well if done diligently, as blower door testing confirms.
I am working on project that has ZIP sheathing on the roof deck with an unvented cathedral ceiling at 8:12 pitch. I plan to do 4" of GPS on top of the sheathing to get R20 (I am in CZ5), and R19 of the fluffy stuff inside the rafter cavity. I am doing metal roofing on top of furring strips over this.
For the ease of construction, I would like to do one 2" layer of the GPS on top of the sheathing, and the other layer 2" directly below the sheathing. I would fit that tight between the rafters and spray foam edges. This would sandwich the ZIP in between the two layers. Would this possibly put the plywood too close to the exterior and then be a point where condensation develops?
Only having the 2" on the top the roof deck would help with the ease of construction and other roof line and siding details. But I don't want to risk issues.
Any advice would be appreciated.
User 7927072,
I'm not sure what "GPS" stands for, but I'm guessing that you are referring to some type of rigid foam -- perhaps EPS, or perhaps XPS -- with an R-value of about R-5 per inch. That sounds like XPS.
I don't recommend installing rigid foam between the top of the rafters and the sheathing layer, because the sheathing layer needs to be directly nailed to the rafters for structural reasons. If you are convinced that you want to pursue your plan, talk to a structural engineer.
GPS is Graphite Polystyrene ridged insulation (Neopor https://neopor.basf.us/) . The insulation would actually be cut to fit in between the rafters on the underside of the sheathing.
See the attached: From top down. 2" GPS (R10), 1/2" ZIP, 2" GPS (R10), Fiberglass (R19)
User 792,
Thanks for explaining that you were referring to Neopor. (As you might have guessed, I'm not a fan of abbreviations.) The technique you are suggesting is called cut-and-cobble. When it comes to unvented cathedral ceilings, installing rigid foam using the cut-and-cobble method has been associated with failures, so I don't recommend this approach. All of your rigid insulation should be on the exterior side of the roof sheathing.
For more information on cut-and-cobble failures in unvented roof assemblies, see "Cut-and-Cobble Insulation." (Check out the third bullet point in the section on cut-and-cobble disadvantages.)
Thanks again for the information, it has likely saved me from making a potential big mistake.
Log in or become a member to post a comment.
Sign up Log in