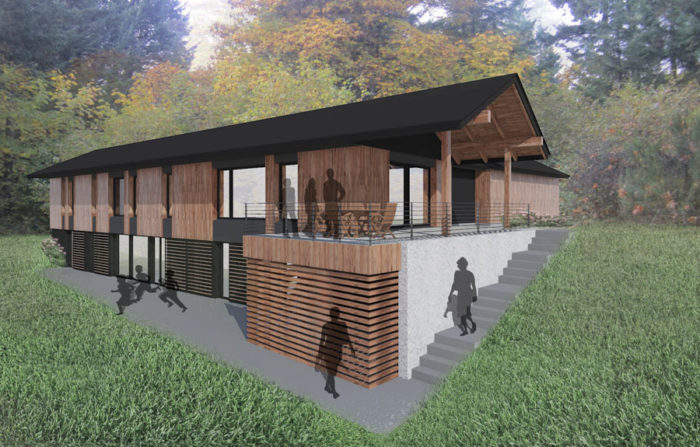
Image Credit: Hammer and Hand
In three new videos produced by Oregon builder Hammer & Hand, lead carpenter Val Darrah explains how he keeps air sealing in mind as he frames the walls for his current project, the Pumpkin Ridge Passive House.
Val explains why he prefers to use a router rather than a saw when he cuts out window openings in the OSB sheathing. He also shares his method of building window bucks out of 3/4-inch plywood.
The OSB sheathing seams are treated with Prosoco R-Guard products: Joint and Seam Filler for the seams, and FastFlash for the inside of the window rough openings. Val explains that in damp weather, it’s easier and more effective to seal sheathing seams with Joint and Seam Filler, a moisture-cured sealing product, than with air-sealing tape.
The concrete foundation will be insulated on the exterior with 6 inches of expanded polystyrene (EPS) foam.
For more information on the Pumpkin Ridge Passive House project, visit this page on the Hammer and Hand website.
Weekly Newsletter
Get building science and energy efficiency advice, plus special offers, in your inbox.
16 Comments
Liquid Applied Air Barriers
Nice videos. Thanks for sharing.
Having installed both tape and liquid applied products, I had a couple of comments.
1) I found that installing a permanently flexible caulk between the window buck and framing member provides a great air seal. Even if you are installing an additional layer on the inside corner surface (as shown in the video), sandwiching the sealant is fast, cheap, and effective. In my mind, anyway, it is less prone to joint movement failure than surface applied sealants.
2) I'm curious how the Prosoco product performs on the sheathing joints. Unlike comparable LA air barriers, the Prosoco system doesn't use a joint reinforcement tape. If the Prosoco sealant is strong enough and flexible enough to withstand the expansion / contraction of the sheathing during the dry-in period, then it eliminates a significant material and labor step.
Tape vs goo...
Anyone have an idea what the difference in material cost is to airseal an assembly like this using something like "Fast Flash" vs. a "high performance" tape?
Since they're just treating the seams, it seems like the "goo" would be more affordable...
I wonder which ("goo" or tape) will prove more durable once these houses start to get old?
Response To Daniel Ernst
Daniel,
The Prosoco R Guard system has two components for this application: 1, Joint and Seam filler. 2, Fast Flash. They work extremely well. They maintain a testing lab in Portland. I've been in the Lab during performance tests and the system performs extremely well. The ability to handle EXTREME building movement is impressive and gaps can increase or decrease by +/- 5mm (3/16") (Thats my opinion, not the factory line).
It's important to note that this level of performance is based on using joint and seam filler on gaps and then top coating with Fast Flash! It's not a case where you can cheat and just top coat with Fast Flash and call it good.
Response to Lucas
Lucas,
We sell both Prosoco R Guard, and Siga and so we get this question a lot. In general terms Taping sheathing joints will cost less than R Guard.
However... that's not the whole story. Having a tool box full of options is a good thing. Being able to apply R Guard onto a wall, or floor system in the rain is a pretty nifty thing. R Guard makes a "kiiler" flashing for window bucks. It'll also does a great job when you have wiring or plumbing popping up through the slab. But... you can do all that with tape too...
The thing I like about Hammer and Hand is their total commitment to quality. We've discussed both options and H&H management continues to base their decision on their "perception" of quality rather than cost. A trait I'd like to see more of.
In the Pacific Northwest, air and water management are critical components of the building envelope. In my opinion, both R Guard and GOOD tape (SIGA Wigluv, 3M 8067 & Pro Clima) are good quality materials for durable applications. Caulking is for counter tops...
Response to Albert Rooks
Thanks for the additional information on the Prosoco products.
I wasn't thinking of cheating the system. Other liquid applied barriers use a combination of fill and coat products, but they have an additional component that is not found in the Prosoco line---joint reinforcement tape. As an example, the Sto Guard system requires this tape on all joints---flats and angles. Prosoco doesn't.
I've included a picture of a plywood joint treated with Sto Gold Fill, before the Gold Coat has been applied. Notice the 4 1/2" fiberglass mesh tape underneath.
Hopefully this clarifies my observation and query.
Joint Reinforcement Tape
Daniel,
The following post is from Tom Schneider, he is the chemist behind the formulation of the R-Guard products. His GBA account is having issues so he asked me to post on his behalf:
PROSOCO product Joint and Seam Filler was developed to address the joints and seams within the framing and sheathing conditions. It has adhesion, expansion, and contraction capacity to account for the movement caused by drying, settling and windloads the structure will likely be subjected to.
Expecting that reinforcement tapes will be properly installed on 5th floor scaffolding on a windy Friday afternoon, that they will not protrude through the membrane and act as a conduit for water intrusion or that thousands of feet of horizontal gaps in the sheathing will be treated perfectly is unrealistic at best.
The Joint and Seam material from PROSOCO is part of a Flashing/Waterproofing/Air-Barrier system designed to perform repeatedly under Category 5 Hurricane conditions for extended periods or up to structural failure. A very sophisticated test chamber and racking device were developed to help define product requirements and demonstrate performance.
The system is visually inspectable and eliminates steps and materials in addition to being able to apply the products under less than ideal conditions.
Thanks,
Tom Schneider
Building Envelope Innovations, LLC
Office: 503 560 5452
Wet-Flash Products
Skylar --- Nice post.
Quoting the coverage of one tube (J & SF) at .35/LF sounds about right to me.
The equivalent SIGA product (Wigluv 60) is 0.39 to 0.42/LF depending on quantity. (but has the handy dispenser!). I'll leave the labor valuation to those that have more experience with it.
Daniel,
What I was going to say about the mesh is what Tom Schneider said in too many words for me... (Too much education can often do that... Sadly, thats never been a problem for me! :) In my mind, adding an inflexible mesh is bad. It limits the joints ability to stretch. The reason a mesh is added is to compensate for the materials lack of ability to remain in one piece under stress. Ie: Not crack and tear in action.
The flexibility characteristics is exactly what I like about the R guard system.
EPS glue/foam?
What is that foam product used to glue the EPS to the foundation (in the 3rd video) that allows you do run without fasteners?
EPS Glue/Foam
Dana,
We used DOW ENERFOAM one-component spray foam adhesive to glue the EPS to the foundation wall. Of course other types of one-component foam will work, but the Enerfoam is the best thing we have tried. Another option is to drill out a hole in the EPS and countersink a mechanical fastener deep inside the EPS. The hole can then be filled with an EPS plug and glued in with Enerfoam. It only takes a couple fasteners to keep the foam in place until the foundation is backfilled.
Response to Dana
Dana,
Your question might have been specific to the foam adhesive being used in the video...
But I have found that OSI QB300 adhesive works very well in this application - even when bonding to the poly surface of "Blueskin" type materials.
Response to Albert and Skylar
Thanks for the information guys.
I am actually a bit surprised at how closely the two materials compare in terms of material cost for the same application.
Another question:
How does the "fast flash" work on the "rough side" of OSB?
Good Posts
Thanks, Skylar, for the informative posts and links. That's just the kind of information that makes this forum a valuable tool.
Joint and Seam Filler
Daniel,
Thank you for your comments. I work with Val at H+H and I am the Passive House Consultant on the project shown in this post. We have utilized FastFlash (red) and Joint & Seam Filler (pink) on dozens of projects over the past several years. I've grown very confident in the Joint & Seam Filler's ability to handle structural movement when applied to the surface of a building joint. This is exactly what the product was developed and designed to accomplish. We are fortunate to be located in the same city as the chemist that developed this system and on many occasions we have been able to see the R-Guard system, prototype materials, and competing systems pushed to their limits in a "Design Verification Testing Chamber". I've seen the Joint & Seam perform leak free during a structural racking test under 150mph wind driven rain conditions. Very convincing stuff. Under the same conditions a similar system that utilized the embedded mesh at joints failed.
Lucas,
Albert hit the nail on the head regarding cost. When it comes to air and moisture management our focus is on performance first. Our second focus is installation efficiency. Labor and installation costs can quickly outweigh material cost, so comparing the cost of a liquid applied system vs a tape can get challenging. Under many conditions the liquid system is faster and more effective while in other cases a tape is the perfect tool for the job.
To give you a rough idea of material cost, a 20oz sausage of Joint & Seam Filler applied 2" wide over a sheathing seam will cover at least 50LF. This comes out to less than $0.35 LF.
The million dollar questions is how all these tapes and sealants will perform in 25, 50, or 100+ years. I'm confident that with proper substrate preparation, application, and design the top of the line high performance tapes and sealants that we are using today will fair very well in the long term. Regardless they will perform FAR better than almost nothing, which sadly is the current industry standard.
I've attached a photo of a few H+H carpenters hanging around one of the racking devices that are used in the Design Verification Testing Chamber. More info here: http://greenpiece1.wordpress.com/2011/03/01/if-were-not-testing-were-guessing/
"rough side" OSB
Lucas,
To date we have not had any problems applying FastFlash to the "rough side" of OSB without a primer, but to be honest 9 out of 10 times we use plywood as our exterior sheathing. On this project the structural sheathing will be covered with a Larsen Truss system (9.5" I-Joists+Agepan DWD+Rainscreen), so we were less concerned with using OSB. To be on the safe side we always try to put the "smooth side" of the OSB to the air-sealing side. Luckily the building inspectors in our area don't seem to be too concerned with us facing the "smooth side" or grade stamp to the exterior.
As you probably know OSB varies depending on the manufacturer and region, so I would always recommend testing FastFlash or tape for adhesion. If the "rough side" of the OSB is so rough and fibrous that there is structural or substrate failure with the FastFlash/tape (see attached pic:source), then applying a primer might not remedy the problem. In a perfect world I would prefer to use a "premium grade" OSB (when not using plywood) from manufacturers like Weyerhaeuser or Huber (Advantech/ZIP) rather than "commodity grade" OSB. These higher quality OSB products primarily use a formaldehyde-free MDI resin instead of a phenolic resin binder; as a result, they are harder and smoother (great for air-sealing) and are far more moisture resistance that standard OSB.
If I had to guess I'd say the OSB with MDI is also less air-permeable than commodity grade OSB. The same goes for vapor permanence, so it is important to account for this when designing the wall assembly.
From what I've seen on my limited travels to Europe, the OSB over there has a distinct look to it. A quick google search told me that some European OSB manufacturers have completely ditched phenolic resin and utilize 100% MDI resin in the core and face layers of the OSB. Perhaps this is the reason behind the foreign look of Euro OSB.
Response to Skylar
Skylar,
Thanks again for the thoughtful reply.
Caulk is for countertops
It's not just the product, but how it's installed. A great product installed poorly is a poor product. An average product installed with attention to detail can outperform poorly installed great products.
We have used caulks and achieved fantastic air sealing results because of being nitpicky with details. We use Sika 1A or 15LM depending on the situation and caulk all open stud walls before the wall sheating is applied. This means studs, top and bottom plates and around any penetrations. Then when the sheating is pressed into the studs, we have a full 1.5 inch strip of sealant. This way when we drive our fasteners, they are driving through the sealant, eliminating penetration holes. We then caulk the edges and squish the edges together. Everything closes up nicely.
Inside, we caulk all the joist 'bays' with caulking as well and that way everything is sealed up on the inside and the outside. Finally, we use a roll on sealant to seal the joints on the outside. In our practical experience tapes in our climate (Ontario) fail if the exterior cladding isn't put up immediately. In a cold Canadian fall or winter, not dissimilar to the US west coast, cold rain can make all but the heartiest products fail. Labour intensive? Yes. In our practice, worth it. And caulk isn't just for countertops. Key is you have to have the right product and know how to use it the right way.
Log in or create an account to post a comment.
Sign up Log in